One such alloy that is widely used in manufacturing and casting industries is the zinc-based Zamak 5 alloy, which has some unique features. This is because of the great strength, excellent durability and great corrosion resistance, which Zamak 5 offers, making it an ideal material for use in die casting operations. After extraction, Zamak 5 is extremely low-melting and has excellent casting characteristics, thus making Zamak 5 an ideal material for automotive manufacturing and consumer products and hardware industries. Industry participants will have the certainty about Zamak 5 alloy properties, such as composition and various concrete usages, to make production decisions and optimize the process of operational effectiveness.
The article discusses Zamak 5 alloy through its chemical makeup and the manufacturing methods alongside temperature control and pressure maintenance, and mechanical substance attributes on the industrial performance.
Zamak 5 Alloy Overview
Zamak 5 functions as a leading zinc-based alloy that industry refers to as zinc-aluminum alloy. Zamak 5 is chemically composed of 3.5 to 4.3 percent aluminum along 0.03 to 0.08 percent magnesium, and 0.75 to 1.25 percent copper. It also gets its superior strength due to the elements that the manufacturer can use to create high-strength components for use in the automotive and aerospace, and consumer goods industries. The tensile strength, as well as 6.7 g/cm³ density and a relatively wide melting point range of 380-385°C, are present in this alloy because of its good durability and good precision.
Composition and Properties of Zamak 5

Chemical Composition of Zamak 5
Mechanical properties of Zamak 5 are improved by mixing in a zinc-based alloy in controlled percentages of zinc and aluminum and copper, and magnesium.
This property of easy melting is one of the qualities that makes Zamak 5 an excellent die casting alloy in comparison with 96–98% of the alloy that is ZINC. For the achievement of superior results, it is critical to use zinc material with 99.99% purity in order to avoid contaminants that would impair the alloy strength and structural integrity.
The solidification of Zamak 5 material is improved by the addition of Aluminum (3.5 to 4.3%) as it improves the alloy’s microstructure. The regions have e composition forming them that combines ductility and hardness features in the material structure. Zamak needed to be measured for the exact aluminum content to prevent material defects like cracking as well as brittleness problems.
The presence of magnesium between 0.03% to 0.08% in zamak 5 is because with this element, the corrosion of micro cracks in grain boundaries is blocked by impurities. Because this addition makes the alloy more fluid, the mold benefits by obtaining better filling features. Leaving out magnesium will make the Zamak 5 surface defective, as well as being very hard to machine.
Zamak 5 is graphite casted and has good wear resistance and heat treating capability when the amount of copper is added at 0.75 to 1.25 percent, which has enhanced creep resistance, which is appropriate for thermal variation applications. Because Zamak 5 becomes brittle when the correct limits are exceeded, the ratio of copper is important.
Physical Properties of Zamak 5

The weight of a Zamak 5 material is 6.7 g/cm³ with a density between steel and greater than the aluminum alloys. Its favorable weight-to-strength relation makes Zamak 5 suitable for many structures involving strong materials with low weights.
Zamak 5 melts between 380 and 385 degrees Celsius, which makes the exact casting of zamak 5 cost-effective compared to aluminum.
At a mean temperature of 120 °C, the tensile strength of Zamak 5 was 330 MPa with 220 MPa yield strength and elongation potential of 7-10%, which meets the requirements of industrial use. Zamak 5 is strong and adaptable as it has high yield strength at 220 MPa and the maximum elongation before almost failure of 7-10%.
Mechanical Properties of Zamak 5
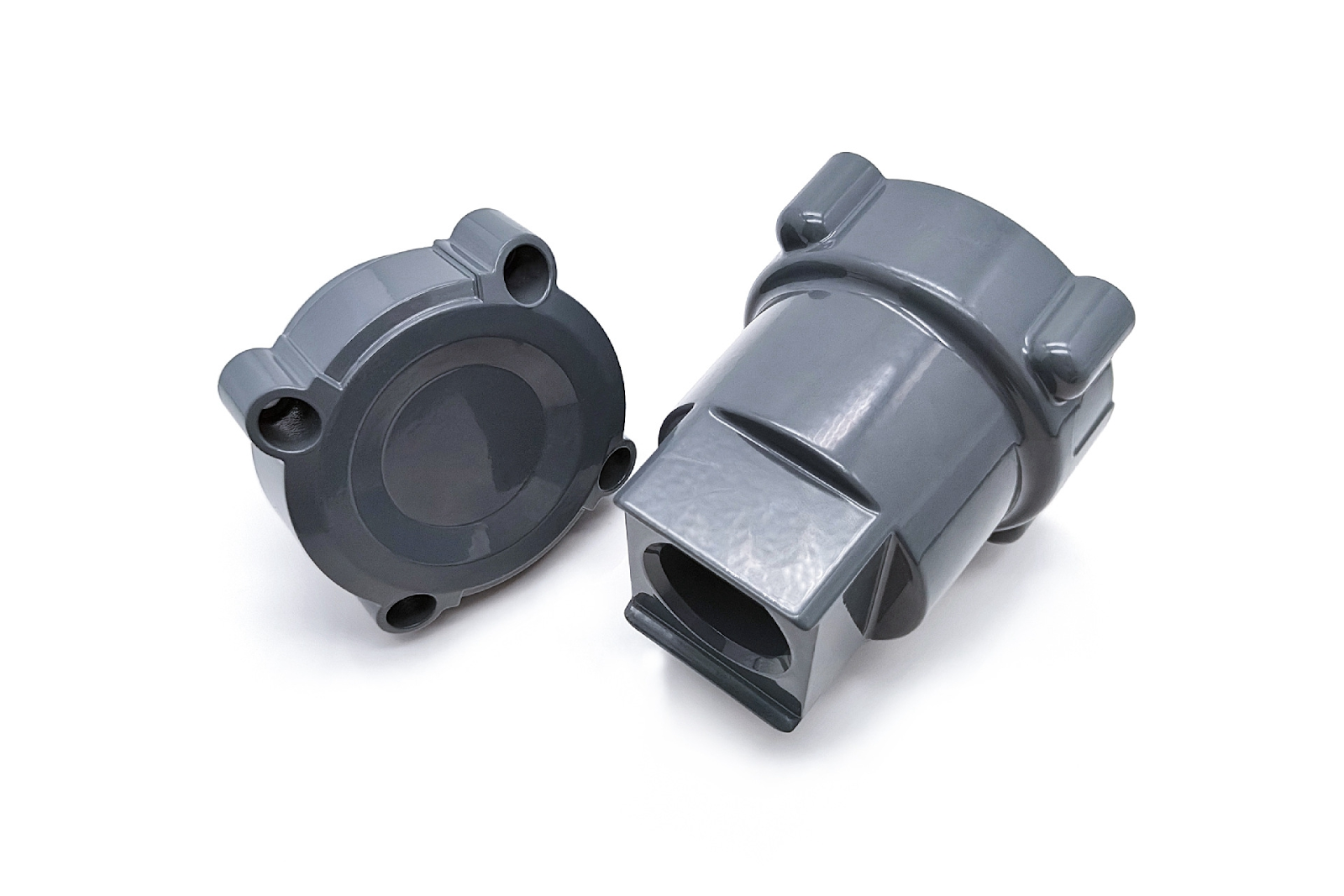
Zamak 5 has 91 HB Brinell hardness levels perfectly struck in between strength and surface hardness, making it an excellent combination for decorative handles or other parts demanding wear protection.
Impact Resistance:
The measure of room temperature Charpy impact strength of the material is 53 J, while at -20°C it reduces to 35 J. The alloy has high impact resistance so that it can protect itself against mechanical stresses and vibrations in dynamic force conditions.
Zamak 5 can stand up to cyclic stress of 100 MPa and survive without failure up to 1 million cycles. Zamak 5 performs in practice with reliable stability under continuous loading, thus being suitable for the machine components and the washing machine part.
Mechanical Properties of Zamak 5 Alloy
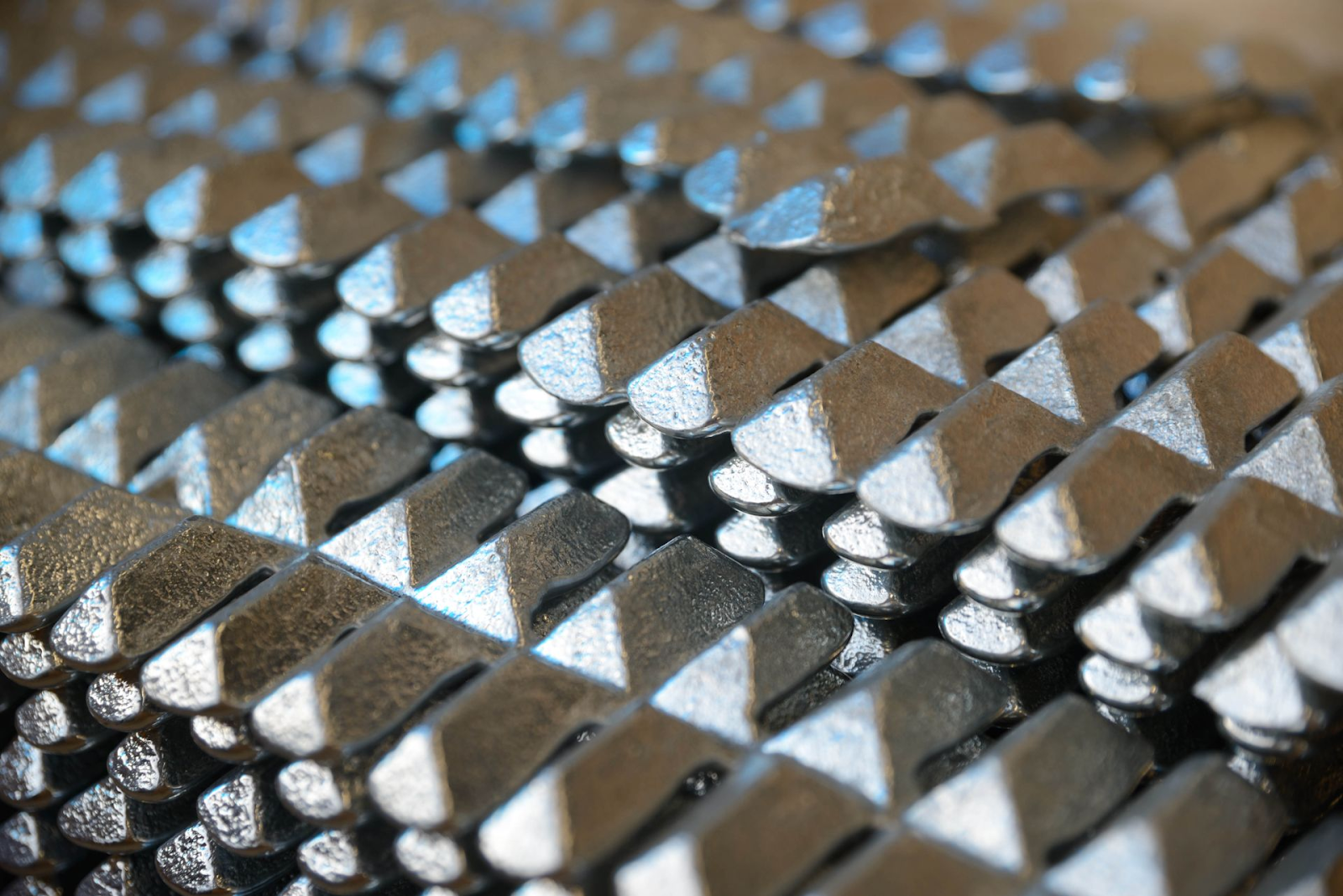
A table below displays essential mechanical characteristics of Zamak 5 aluminum alloy.
Property | Value |
Brinell Hardness | 91 HB |
Ultimate Tensile Strength | 328 MPa |
Yield Strength (0.2%) | 269 MPa |
Shear Strength | 262 MPa |
Compressive Strength | 600 MPa |
Fatigue Strength | 56.5 MPa |
Impact Strength | 65 J |
Modulus of Elasticity | 96 GPa |
Elongation | 7% in 50mm |
Zamak alloy’s strength values show how it can withstand stress and place it within other materials where it can be used in demanding applications. Zamak 5 provides superior resistance to fatigue loads and impacts, thus suitable for parts subjected to repeated force loadings.
Physical Properties of Zamak 5 Alloy
Through its full set of characteristics, Zamak 5’s behavior is controlled by the physical properties.
Property | Value |
Melting Range | 380-386°C |
Density | 6.60 g/cm³ |
Electrical Conductivity | 26% IACS |
Thermal Conductivity | 109 W/mK |
Specific Heat Capacity | 419 J/kg-°C |
Coefficient of Thermal Expansion | 27.4 µm/m°K |
Poisson’s Ratio | 0.30 |
The combination of properties in Zamak 5 makes it perform well in different settings and for application conditions that are suitable for thermal as well as electrical conductivity. Appropriate density characteristics and thermal ability make Zamak 5 to must for warm sensitive systems and also possesses good electrical properties, which provide a variety in an use form of an electrical part.
Advantages of Zamak 5 Alloy
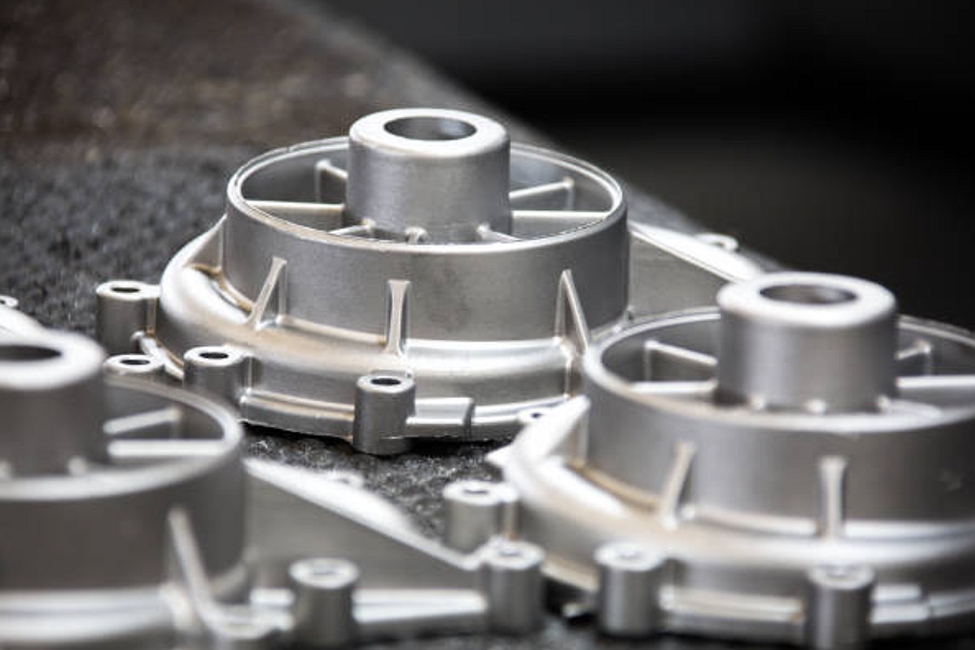
In comparison, the superior strength properties that Zamak 5 exhibits at the same time with lower weight are because its strength-to-weight ratio is 49 MPa, which exceeds A380 aluminum. Due to its dominant characteristic of high strength level with high weight efficiency, Zamak 5 can be used successfully in various industrial applications that are related to the automobile and aerospace sectors.
Good Corrosion Resistance: Its alloy makes Zamak 5 superior to corrosion under other salty and humid conditions, where its alloy offers perfect benefits for marine hardware and exposed applications. Zamak 5 has been tested in the laboratory, and exposure to salt spray for more than 500 hours on the material does not damage the surface.
Excellent Castability: Zamak 5 is especially good for die casting because the metal is sufficiently fluid to easily flow into complex casting shapes. Zamak 5’s castability is used by manufacturers with its fast and easy easypost-production, requiring minimal and particularly where variations in geometrical dimensions will not affect a function.
High Ductility: Zamak 5 can be cold formed using processes that succeed because of its ductility, ranging between 7% and 10%. Zamak 5 allows bending and throating, and drilling operations, which enables making Zamak 5 better due to increasing its manufacturing versatility.
Manufacturing Process of Zamak 5
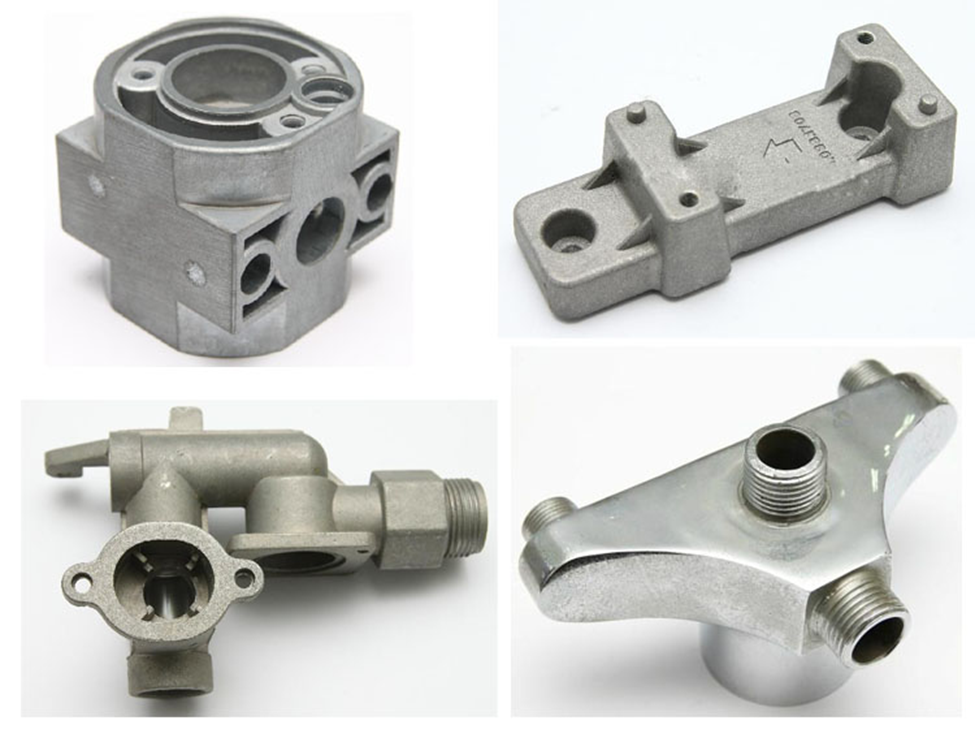
Die Casting Process
Zamak 5 material has a low melting point, which means the material cannot be produced on a macro injection die, but is feasible from the hot chamber die. The molten metal is received under high pressure into the steel mold for making pieces with close tolerance and a fine surface. However, the method achieves efficiency rates that are outstanding, especially when high quantities of products are to be manufactured.
Process Parameters
In fact, the three crucial process parameters are: injection pressure ranging from 700 to 1000 bar in conjunction with die temperature from 150 to 200 °C and cooling rates of 50 °C / s. Mechanical quality, excellent, has to be controlled very precisely before achieving the product defects at the lowest level.
Machining and Finishing
Zamak 5 is readily available for finishing processes after the casting stage by means of its characteristics. High ductility of the product allows for exact threading and precise grooving protocols as well as precise electroplating procedures and powder coating methods to enhance corrosion protection and aesthetic features.
Differences between Zamak 5 and Zamak 3
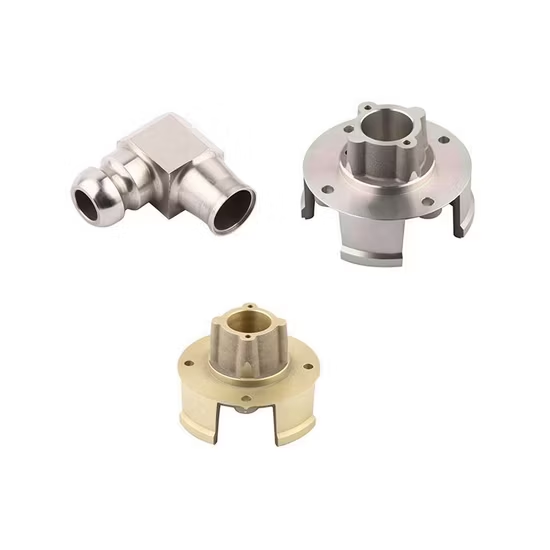
Chemical Composition: Zamak 5 is not Zamak 3 because it has heat tolerance due to the inclusion of copper element and Zamak 3 has no copper because it provides the best casting and moisture-resistant protection capabilities.
Mechanical Properties: Zamak 5 has greater strength and hardness, thus has better mechanical properties and is more useful in parts which have load requirements than Zamak 3.
Comparison Between Zamak 5 and Zamak 3
Property | Zamak 5 | Zamak 3 |
Chemical Composition | Zinc (96-98%), Aluminum (3.5-4.3%), Magnesium (0.03-0.08%), Copper (0.75-1.25%) | Zinc (95-97%), Aluminum (3.5-4.3%), Magnesium (0.02-0.06%), Copper (<0.1%) |
Tensile Strength | 330 MPa | 240 MPa |
Yield Strength | 220 MPa | 160 MPa |
Elongation | 7-10% | 10-15% |
Hardness | 91 HB (Brinell) | 80 HB (Brinell) |
Density | 6.7 g/cm³ | 6.6 g/cm³ |
Melting Point | 380-385°C | 380-385°C |
Applications | Automotive, aerospace, consumer goods, high-strength applications | Toys, decorative items, low-stress applications |
Key Advantage | High-temperature resistance, wear resistance, improved strength and durability | Excellent castability, corrosion resistance in humid environments |
Disadvantage | Less ductile, more susceptible to brittleness at higher temperatures | Lower temperature and stress resistance |
Zamak 5 and Zamak 3 possess parallel chemical structures, mechanical characteristics and common utilization cases, and this table shows it in one place.
Zamak 5 (ASTM AC41A, Z35531, Mazak 5) Zinc Alloy
Zamak 5 is a zinc-aluminum alloy that shows numerous applications because of its excellent strength properties and versatility. This alloy in the industry is widely known to be Zamak 5, though under the AC41A under ASTM standards, and Z35531 under the UNS classification system. Zamak 5 is composed based on primary zinc alloyed with aluminum and copper to boost its mechanical features, similar to strength, corrosion resistance and hardness. As stated, the fabrication properties apply to Zamak 5 in its condition before any tempering processes or other treatment. Because it can produce both intricate, detailed parts and high-quality parts, Zamak 5 alloy is used for die casting. Since it provides both economical and dependable operable capability, Zamak 5 has established its position in automotive and electronics products as well as decorative items.
Melting Point of Zamak 5
The values of the melting of Zamak 5 alloy are between 380°C and 386°C (716°F to 727°F), which are lower than other metallic materials. The use of Zamak,5 as it has a lower than average melting temperature, has an important role in the die casting operations due to ease of moldability in lower process temperatures. The low melting range of the alloy helps in easier working on precision manufacturing due to its requirement for rapid melting and solidification in making intricate components. Zamak 5 has a low melting point, which makes it easy for the Finishing manufacturer to choose it in numerous automotive production plus furniture and consumer goods manufacturing.
Young’s Modulus of Zamak 5
Zamak 5 alloy has certain technical characteristics. Young’s Modulus is ~96 Giga pascals (GPa). This value gives the material stiffness since it reflects how much the material resists deformation under the applied stress. The average stiffness of Zamak 5 is because of Young’s Modulus of 96 GPa, close enough to reach both strength and flexibility requirements. The material has the strength it is designed for, and it is still flexible since its stiffness on the moderate scale of 96 GPa (Giga pascals) allows the alloy to keep structural integrity during mechanical applications.
Equivalent Materials to Zamak 5
Different applications require different substances, with the specific zinc alloy Zamak 5 having particular properties, but any number of equivalent materials together with additional substances exist. Three primary alternative materials to use instead of Zamak 5 are Zamak 3 (ZnAl4Cu1), Zamak 2 and Zamak 13.
Zamak 3 (ZnAl4Cu1)
Among the Zamak family alloys, Zamak 3 ranks among the most popular types due to its similar features with Zamak 5. The zinc, aluminum and copper substances from which these alloys derive their crystalline structures. Zamak 3 is being used as a substitute for Zamak 5 because it contains less copper, which is responsible for weaker strength and corrosion resistance.
Zinc Die Castings
Additionally, Zamak 2 and Zamak 7 have a good cast ability that makes them suitable for use in production requiring high precision and high finish quality, both with zinc die casting alloys. Even though these alloys have different mechanical properties, the same manufacturing processes are used for these alloys.
ALSi12
When requiring slightly elevated strength at higher temperatures, users may be able to replace the ALSi12 aluminum silicon alloy with some alternative supplies for procurement. The same chemical makeup does not have to be matched between Zamak 5 and ALSi12, as they are both used in casting and die-casting production.
ADC 12 (Aluminum Alloy)
When requiring good corrosion resistance and castability, ADC 12 aluminum alloy can be used as an equivalent material to replace some manufacturing applications. Since Zamak 5 may be slightly harder, performance criteria would be the basis for selection.
According to the individual mechanical properties balance acquired of tensile strength and corrosion resistance, as well as hardness, such an equivalent is chosen by production teams.
Zamak 5 Casting Process
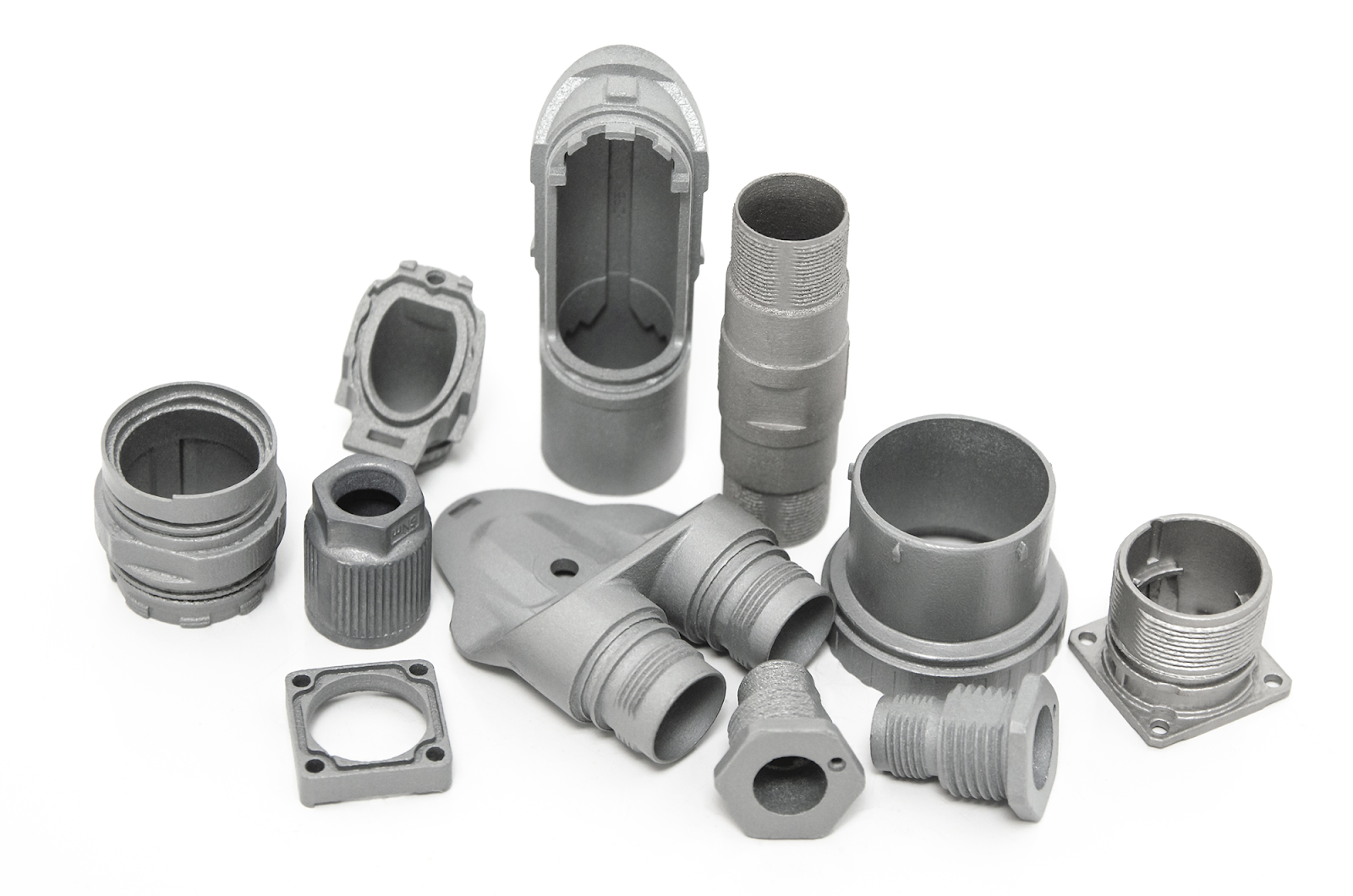
Zamak 5 cast can be preserved and optimized in the end product by different stages of the Zamak 5 casting procedure. The major Zamak 5 production method is die casting,g where Zamak 5 molten metal is injected under high pressure into metal molds. The Zamak 5 casting operation is composed of several successive operations.
Preparation of the Mold:
The die needs to be heated above a certain temperature so that during the injection process, thermal shock to the specimen is prevented. Then we allow the current to be used outside to make sure the casting surface and output production are always defect-free.
Melting of Zamak 5 Alloy:
Zamak 5 has to reach a heat between 380-390°C (716-734°F) before it becomes fully liquid. The alloy is heated in the furnace up to this specified temperature, and the state of the alloy becomes liquid, which is susceptible to injection.
Injection of the Molten Alloy:
The Zamak 5 alloy moves from the liquid form to the properly prepared mold cavity under high pressure after melting. Injection pressures for different parts complexities and their magnitude are 30–60 MPa, which are applied by manufacturers to form.
Cooling and Ejection:
Then, as the mold receives the molten alloy material, it starts to cool down and become solid. It is cast from the mold when it ceases to remain at an adequate cooling temperature. Mold cooling duration and its temperature may be controlled to ensure the quality of the final casting (avoid deformation).
Finishing Operations:
The ejection of Zamak 5 parts necessitates their processing through various finishing procedures whereby the parts are trimmed and also deburred, and polished, and finally coated in order to meet end requirements.
The Zamak 5 casting process is efficient for a high-volume production, as it can create complex objects with precise tolerance requirements. An alloy with exceptional fluidity corrects filling of complex mold cavity areas, so the alloy is suitable for the production of fine detail components in automotive and hardware sectors as well as consumer electronic devices.
Different Standards for Zamak 5 Alloy: A Global Perspective
Zamak 5, the somewhat versatile zinc alloy, is known generally by different names; however, these identifications originate from the particular standard as well as the country of origin. Different specifications related to Zamak 5 have different tendencies specific to regions under the production method and previous designation. These designations are very important to Zamak 5 users because they define protocols for the company as per the alloy specifications in various market sectors and regional standards. All worldwide standards and alternative names of Zamak 5 alloy are presented in one considerable overview.
Global Names and Standards for Zamak 5 Alloy
The following table provides different country standards and the ways its Zamak 5 alloy is named.
Traditional Name | Zamak 5 |
Short Composition Name | ZnAl4Cu1 |
ASTM | AC 41A |
Common Name | Alloy 5 |
China | ZX03 |
JIS (Japan) | Ingot Type 1 (Ingot) ZDC1 (Alloy) |
Short European Designation | ZL0410 (Ingot) ZP0410 (Alloy) |
Germany DIN 1743-2 | Z420 |
France NFA 55-010 | Z-A4UI |
UK BS 1004 | Alloy B |
UNS (Unified Numbering System) | Z35530 (Ingot) Z35531 (Alloy) |
Why Do These Standards Matter?
Different Zamak 5 alloy standards were adopted due to the global adoption of a combination of regional influenced industrial practices and international communication requirements. It (Zamak 5) means that companies which produce Zamak 5 materials as well, and their engineers, need to know about regional standards and designations of that material in particular to select the proper material for their application. The standards are imperative details of Zamak 5 alloy’s chemical composition, performance standards, to choose suitable materials for casting and machining operations.
Benefits of Zamak 5 Alloy
Zamak 5 is employed for quite a few applications in industry as a versatile, robust alloy of zinc, providing plenty of useful attributes to diverse manufacturing efforts. Zamak 5 boasts threefold improvement over the characteristics of superior strength as well as great toughness and protective properties that make it suitable for abundant material applications in consumer devices and industrial equipment. These are the fundamental advantages that Zamak 5 alloy offers to the manufacturers.
1. Strength, Durability, and Safety
The outstanding performance qualities in terms of strength and also in terms of hardness levels are retained by the zinc alloy Zamak 5. The alloy is a strong source of force resistance, which is why it remains a strong solution for demanding applications that need very high percentages of stress. Zamak 5 is important to industries because it is very physically resistant, and at the same time, it meets absolute safety measures for contact events.
Zamak 5 provides a safety benefit over some metals, such as magnesium, escaping the fire-related issues. Zamak 5 has a rare quality which distinguishes it from the other common materials because it never takes in moisture, thus leading to no plastic-like water absorption problems. Due to the feature of safety for human contact, Zamak 5 is used in the manufacture of cosmetic packaging.
As a result of its reliability-related attributes,, which secure manufacturers as well as the end users, Zamak 5 is being chosen by new technological applications.
2. Superior Quality in Die-Casting
Zamak 5 is used for die casting applications owing to this alloy’s ability to produce high-quality parts free of defects. Because of its capability to create smooth, finished products with minimal defects, Zamak 5 alloy produces high-quality die castings which resulting in a minimal post-production process needed.
Zamak 5 has the properties of naturally zam, which makes exact molding techniques be used to manufacture products that are found to have high levels of perfection in the production process. As Zamak 5 possess the characteristics of no formal finishing stages, the fabrication process can save time as well as cost of manufacturing operations. The Zamak 5 parts have a nice appearance because the designers can paint or chrome them according to their tastes.
The simple finishing capability of Zamak 5 has made it ideally suited for product applications in those products of home decoration items, home furniture detailing and decorative lighting components. Zamak 5 parts will resist the tarnishing effects due to its enduring effect.
3. Transformed into different final products
Zamak 5 has a superior nature for the production work. The fact that the alloy is pliable by nature, because zinc is ductile, allows for it to be shaped easily for different working operations during production. Zamak 5 can easily work with different methods of production, such as casting and bending and machining, and riveting, to satisfy the requirements of manufacturing.
Zamak 5 possesses easy processing characteristics, making it a vital accessory to different industries that have benefited from the lowering of manufacturing expense, and maintaining an easy production process. With this being the preferred choice for assembling locked products and handle components that have been cast, the assembly process of Zamak 5 parts becomes less effortful.
4. Cost-Effective Manufacturing
Zamak 5 is a material that makes exceptional price affordability available to manufacturers. Zamak 5 is so inexpensive it is cheaper than other alloys and very cost-efficient when it is cast. Its reasonable cost structure, however, invites manufacturers to reach superior cost efficiency standards, and its superior properties bring in the manufacturers.
Zamak 5 has a great potential to be recycled, and that puts the ability to recycle it as an important factor in reducing long-term manufacturing costs. Zamak 5 items are reusable and lead to the production of scrap metal that will be recovered, based on saving cost and minimizing waste due to it.
5. Environmentally Friendly Production Cycle
Zamak 5 production matches much of the environmental friendliness. Zamak 5 doesn’t raise much environmental threat as it uses a different procedure for manufacturing compared to hazardous procedures for some metals. Manufacturing of the alloy exhibits no harmful pollution because no by-products are formed. About environmental legislation, Zamak 5 is a good choice, and it also provides a company with an environmentally friendly method of complying with its own regulations.
Limitations of Zamak 5
Although Zamak 5 has many beneficial points, it should first be selected based on its fixed limitations in the selection process.
Poor Resistance to Humidity
Contact of Zamak 5 with wet conditions will form oxidation on its surface because it demonstrates weak resistance to moisture. Manufacturers of Zamak 5 products should provide protection measures against excessive moisture, and if not, then extra protective coatings should be provided against its breakdown.
Limited Resistance to High Temperatures
The thermal resistance capability of Zamak 5 stands at a moderate level. Zamak 5 should not be used for applications where temperature exposure exceeds 80°C due to a very high drop in tensile strength, which will increase the risk of breakage or bending.
Not Ideal for Lightweight Applications
The part obtained using Zamak 5 is heavier as it has greater density than the competing non-ferrous alloys. The lightweight element for such applications is then required to have other alloy materials considered, as they determine the requirements.
Corrosion Resistance Issues with Other Metals
When zinc or tin is combined with lead to make this material, the durability of Zamak 5 is compromised because of the reduced corrosion resistance of the resulting alloy. In particular usage, special attention needs to be paid to material combination when Zamak 5 is used.
Impact Properties at Low Temperatures
In cold environments, the effect strength of Zamak 5 is affected at points where the temperature dips to extremely low levels, hence it is not functional in cold conditions.
Where to Use Zamak 5?
Zamak 5 is extensively used by many sectors, including the die casting industry. Zamak 5 excels between the two ends of the production spectrum in the manufacturing of automotive elements and decorative items. Some common uses include:
Bathroom Fixtures: Zamak 5 has the ability to protect itself against corrosion, wherein it is widely used in the production of bathroom accessories such as faucets and handles.
Firearm Components: The alloy is very durable and strong, and therefore functions very well in the manufacture of firearm parts.
Toys and Collectibles: However, because of its simple molding process and top-notch surface finish, Zamak 5 is a popular choice for die casting toys and miniature items as well as collectible products.
Lock and Hardware Manufacturing: Zamak 5 is predominant in the manufacturing industry to produce locks with handles, locks’ knobs and other hardware parts thanks to the good strength properties and easy machinability for such alloy
Electronics and Appliances: Zamak 5 has durability aspects and attractive qualities, and household items such as blenders and staplers and ceiling fans as well as other appliances, appreciate Zamak 5.
Mechanical Properties of Zamak 5 Alloy
Zamak 5 alloy is determined by its structural qualities to work well or poorly in various industrial operations. Zamak 5 alloy has tensile strength, along with elongation and hardness and corrosion resistance. The values are changed quantitatively when the casting process is different and the metal alloy composition and cooling rate are changed.
Tensile Strength: Zamak 5 alloy retains tensile strength of 280-300 MPa, which is higher than other zinc-based alloy materials.
Yield Strength: Zamak 5 alloy has excellent stress deformation resistance because the yield strength is approximately 230 MPa.
Elongation: The Zamak 5 alloy has a medium ductility circle (between 3 and 6%) in its elongation rate. Its properties allow for small amounts of deformation that are not accompanied by cracking, and hence it is suitable for use in flexible systems.
Hardness: Zamak 5 hardness value is 90-120 HB (Brinell hardness), which makes the material applicable for applications requiring a relatively low wear resistance.
Corrosion Resistance: Even at the expense of average moisture content and standard chemical substances, Zamak 5 alloy will resist corrosion very well. Zamak 5 works well as a material for outdoor and automotive components.
Applications of Zamak 5 Alloy
Zamak 5 is chosen for the wide range of industries because it combines its good casting characteristics with strong mechanical properties. Its applications include:
Automotive Industry: As an essential material for making fine functional components for automotive engines and vehicle trim housings, electronic device housings, Zamak 5 is a key material.
Hardware and Fittings: Such materials, as Zamak 5, have been serving the automotive sector since it maintain high strength and durability together and are finished with pleasing products.
Consumer Goods: Zamak 5 alloy is the material producers use because of its favorable strength and corrosion resistance, and for shapeability to produce toys and electrical connectors, as well as household appliances.
Electronics: Zamak 5 conducts electricity well, makes good molds into complex forms, and is used to make electronic device casings and housings.
Advantages of Zamak 5 Alloy
Zamak 5 delivers several important benefits which can make it the preferred alloy of choice for manufacturers.
Cost-Effectiveness: The cost of Zamak 5 is an excellent option as it provides good durability and easy casting at a simpler and cheaper rate than other metal alternatives.
Versatility: The reason why Zamak 5 is chosen to make complex, precise parts is easy to produce complicated shapes, with no accommodation.
Finish quality: As Zamak 5 produces excellent smooth surfaces, there is a need for high-quality finishing work, so manufacturers can get a better finish quality.
High Strength-to-Weight Ratio: Zamak 5 alloy is good for the automotive industry along with other such sectors, as this alloy offers high strength and lightweight independence.
Challenges and Considerations in Using Zamak 5
Despite the fact that Zamak 5 alloy boasts a number of advantages, there are several critical points when it comes to its usage.
Temperature Sensitivity: However, Zamak 5 has thermally sensitive behavior because it lacks property degradation in the presence of increased temperature under 250°C (482°F). Zamak 5 parts have to be constrained in a useful lifetime to environments where the temperature is low enough, so s not to exceed this threshold.
Machining Limitations: Although the casting process for Zamak 5 is simple, the material creates problems with machinery operations that involve aggressive methods, as the material tends to involve galling as well as wear mechanisms. To reach successful results very well technicians need proper tools and the right techniques.
Environmental Impact: Evaluation of The good resistance to corrosion in Zamak 5 should also be taken into account in the environmental impact that Zamak 5 causes in the production and cycle processes. Zamak 5 can be further improved through recycling and waste reduction in casting emissions, and the industry is doing so both to increase zinc alloy sustainability.
Zamak 5 Die Casting Services at CNM TECH
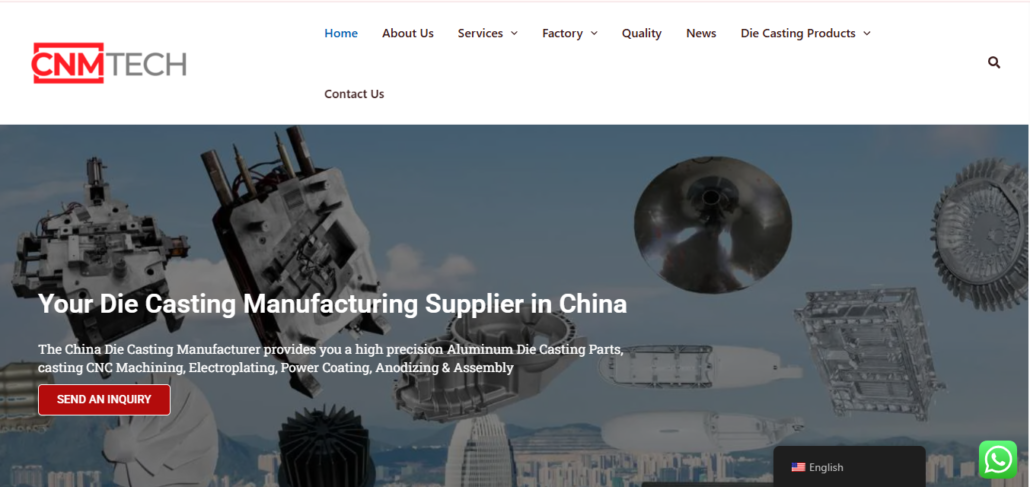
We offer outstanding Zamak 5 die casting solutions under the portfolio of CNM TECH for various industry needs, from automobile, aerospace, to consumer products production. We are an organization specializing in deep experience and modern die casting systems that allow us to develop parts that give excellent performance, ability and maintenance.
Applying our modern die casting method, Zamak 5 products with good dimensions, excellent surface quality, and systematic manufacturing time for economical production quantity will be provided. Simply stated, with CNM TECH, clients can dictate their specifications to the die casting material precisely and get tight turnaround periods.
Take a look at all our Zamak 5 offerings that provide prototyping and large-scale manufacturing capabilities. At www.thediecasting.com, you can find out how Zamak 5 solutions from our company increase product lifetime performance.
You must choose Zamak 5 die casting services from CNM TECH as they are precise.
Conclusion
Zamak 5 is the commonly used alloy casting in the industries for manufacturing parts which require precision, especially in automotive, hardware, and electronics, which have the capability of low production costs and effectiveness. The zinc, aluminum, copper magnesium mix of Zinc Alloy 5 makes for a strong material with great mechanical characteristics, strength and corrosion defense, and castability. The manufacturing techniques using Zamak 5 casting, if approached properly, with the controls on temperature and pressure, produce highly quality components with very minimal imperfections whenever they are performed. However, Zamak 5 has a low melting point and fluidity characteristics that make it suitable for highly sophisticated designs, which is why for is widespread industrial applications.
FAQs
1. What are the essential characteristics of the die casting process at CNM TECH that lead towards Zamak 5?
A: High-performance zinc alloy has descriptions like: excellent strength and dimensional stability, and outstanding corrosion protection. One of them is Zamak 5. Zamak 5 exhibits exceptional cast ability, due to which extremely detailed, intricate components may be manufactured with minimum machining. CNM TECH uses Zamak 5 to manufacture reliable cost cost-effective components which can work as a utility in automotive applications and consumer electronics, and hardware industries.
2. Can CNM TECH produce certain Zamak 5 parts to my project requirements?
A: Absolutely. As a specialized company, CNM TECH provides an individual Zamak 5 die casting solution. The company makes molds with clients, those companies who need low-volume prototyping as well as high-volume parts that are required to be exactly as specified. The dedicated work of our employees in the processes of production results in our delivering accurate results and dependable performance.
3. What are the possible types of treatments to complete Zamak 5 casting products?
A: At CNM TECH, the multiple finishes available for Zamak 5 parts include electroplating in combination with powder coating and chroming and painting and polishing. By using the finishing techniques, the appearance and wear resistance and corrosion protection of parts that can be functional or decorative can be improved.