
ZAMAK is the name given to a zinc-based alloy that is used with aluminum, copper (Kupfer), and magnesium. ZAMAK was named in German from these words. This alloy usually contains 94% to 96% zinc, the other material being added to foil or sheet. Several remarkable qualities make ZAMAK alloys good for die casting applications. The fact that these alloys have a low melting point, high fluidity, and high strength per weight makes them extraordinarily useful for making hard, tough and accurate parts. In addition to these key features, ZAMAK alloys offer other features that qualify them for several industrial applications.
Zamak die casting has established itself in the world of metal casting as a highly cost-effective and cozy method of metal casting. Zamak is a zinc family of alloys used widely to build complex high quality parts in many industries. The process involves injecting molten Zamak alloy into a metal mold or die under high pressure. The process is capable of making intricate parts to very close tolerances with very good surface finishes, which makes it suitable for manufacturing precision parts. The more critical role of Zamak die casting is here because, as industries evolve with the increased need for durable, lightweight and strong materials. In this article, we analyze the significance of Zamak die casting and why a person should prefer Zamak die casting over other casting methods.
ZAMAK alloys are used in die casting foundries for casting parts, and their cast parts comprise many industries such as automotive, electronics and hardware. This also adds an extra edge because these alloys are fully recyclable, as per the sustainability goals. However, ZAMAK die-cast parts have additional surface options, which will be of help to manufacturers to have aesthetically appealing products with a premium look, especially these decorative parts.
What Is ZAMAK Die Casting?
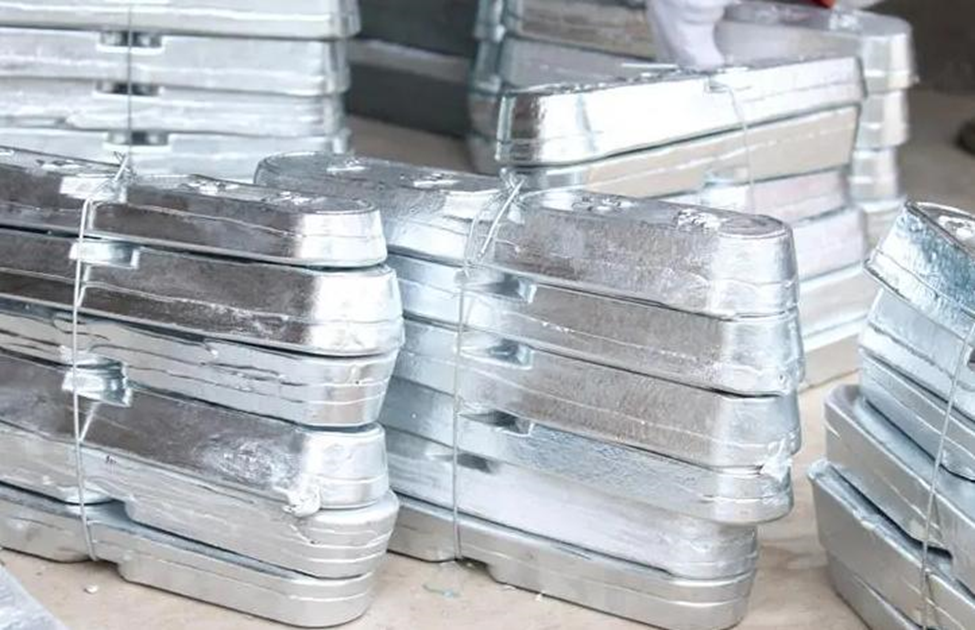
ZAMAK die casting is a metal casting technique widely used in which molten ZAMAK alloy is injected under high pressure into a mold. Typical in this process is the die or mold made from durable tool steel. Various molds are needed for each shape, and the ZAMAK die casting process just requires a hot chamber die casting machine.
A two-halve hot chamber die casting machine is arranged with one stationary half and one movable half. These halves are then closed, and molten metal is injected into the mold by an injection chamber. When the metal is solidified, the cast part is removed from the mold by ejector pins. ZAMAK die casting uses this method on ZAMAK alloys.
Hot Chamber Die Casting (HPDC), Low Pressure Die Casting (LPDC), and Gravity Die Casting (GDC) are possible types of ZAMAK alloys suitable for die casting processes with their respective advantages for different applications.
1. The ZAMAK Die Casting Process
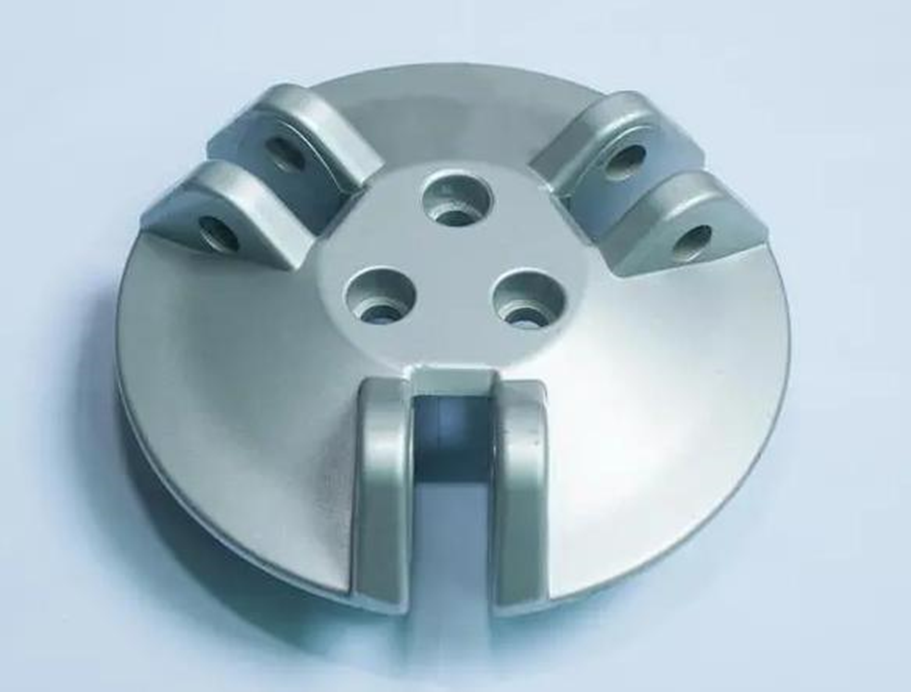
Like other types of aluminum or magnesium die casting, the ZAMAK die casting method needs attention to be paid wherever possible because the results are only as good as the ZAMAK casting process. The typical ZAMAK die casting process is written below in a breakdown:
Step#1: Designing and Creating the Die
The process starts with mold or die design and the final part design in the ZAMAK die casting process. It is important as it determines the final result of the casting as such. The first is that engineers first design a 3D model of the part to be cast using specialized CAD software. Typically, a prototype is made and tested, the design is improved until approval of the final version. Secondly, once there is a final part design, the mold is created, which means:
The injection type: The melting point of the ZAMAK is low enough that it has to be hot enough to be injected into the mold.
- Engineers decide the number of cavities: These are arranged for maximum efficiency.
- Determining the parting system: This is how the two halves of the mold meet.
- This ensures smooth removal of the cast part without damage and a precise ejector system design.
- Cooling system planning: Without cooling, defects would occur, and part quality could not be consistent.
- Choosing the mold material: Metal like H13, SKD61 or other tool steels is good for durability and heat resistance.
Step #2: Preparing the ZAMAK Alloy
After that, prepare ZAMAK alloy. The ZAMAK alloy is purified with several refining methods such as thermal refining, chemical reaction, electrolytic refining and zone refining.
The alloy is melted in a furnace at strictly controlled temperatures to prevent the alloy from coming to a liquid state with impurities. After the final refining, the molten metal is kept in an injection chamber to control temperature to prevent contamination.
Step #3: Injecting the Molten ZAMAK into the Die.
One of the critical phases of die casting is the injection of molten ZAMAK into the mold. After preparation and storage of the molten metal in the injection chamber, it is then injected under high pressure into the die with a plunger or piston. The molten alloy undergoes pressure, forcing it into every corner of the mold since all the space of the cavity is filled.
In this way, one can have the part’s surface even and smooth, and produce good quality results through proper injection techniques. Also, the design of the mold’s injection channels is a key determinant of accomplishing this.
Step 4: Cooling and Solidifying the Part
However, as soon as the molten metal enters the mold, cooling begins. They quickly cycle the high-quality tool steel mold to draw the heat of the molten metal quickly enough for it to solidify. The cooling system is also used by many molds to accelerate the solidification process.
Simply, to achieve the desired part quality and prevent defects, a consistent cooling rate is required, and are most commonly used are water and air cooling systems.
Step #5: Solidified ZAMAK Casting Ejection
The next step from the ZAMAK alloy to solidify is to eject the casting from the die. Care is taken in this to retain the quality of the part. To expel the solidified part out of the mold, ejector pins are used. The mold breaks open into two halves, the ejector pin is actuated, and the casting is released. There is a nice degree of precision to do this step, because too much force on the casting cay damage it. Proper alignment of the ejector pin will also ensure no surface imperfections or dents.
Step #6: Finishing and Trimming
The casting is usually ejected with excess material on it, known as flashing that has to be removed. These can also affect the functioning of the part, and they must be carefully trimmed. Cleaning of the part is accomplished with various trimming tools – grinding, polishing machines. Some foundries may trim manually. Trimmed parts may be surface-treated further to improve a part’s finish.
Step #7: Surface Treatment
Surface treatment is the final step of the ZAMAK die casting. Improving the part’s appearance as well as protecting it from corrosion and wear, surface treatments are also not simply for decorative reasons. ZAMAK is one of the most commercially used surfaces finishes most often through the method of zinc plating, where the surface to be zinc plated e.g. ZAMAK part, is coated with a layer of zinc or any other material, i.e. zinc or black nickel, chrome or other. Another high-profile industry that is very popular involves painting, which includes spray painting and powder coating. The advantage of the powder coating process is that it is usually less susceptible to chipping and wear.
Thus, anodizing, although less commonly used, is applicable in increasing surface hardness, while also adding corrosion resistance, mainly for the highest quality applications such as in the automotive or furniture industry and others.
2. Types of Die Casting ZAMAK Alloys
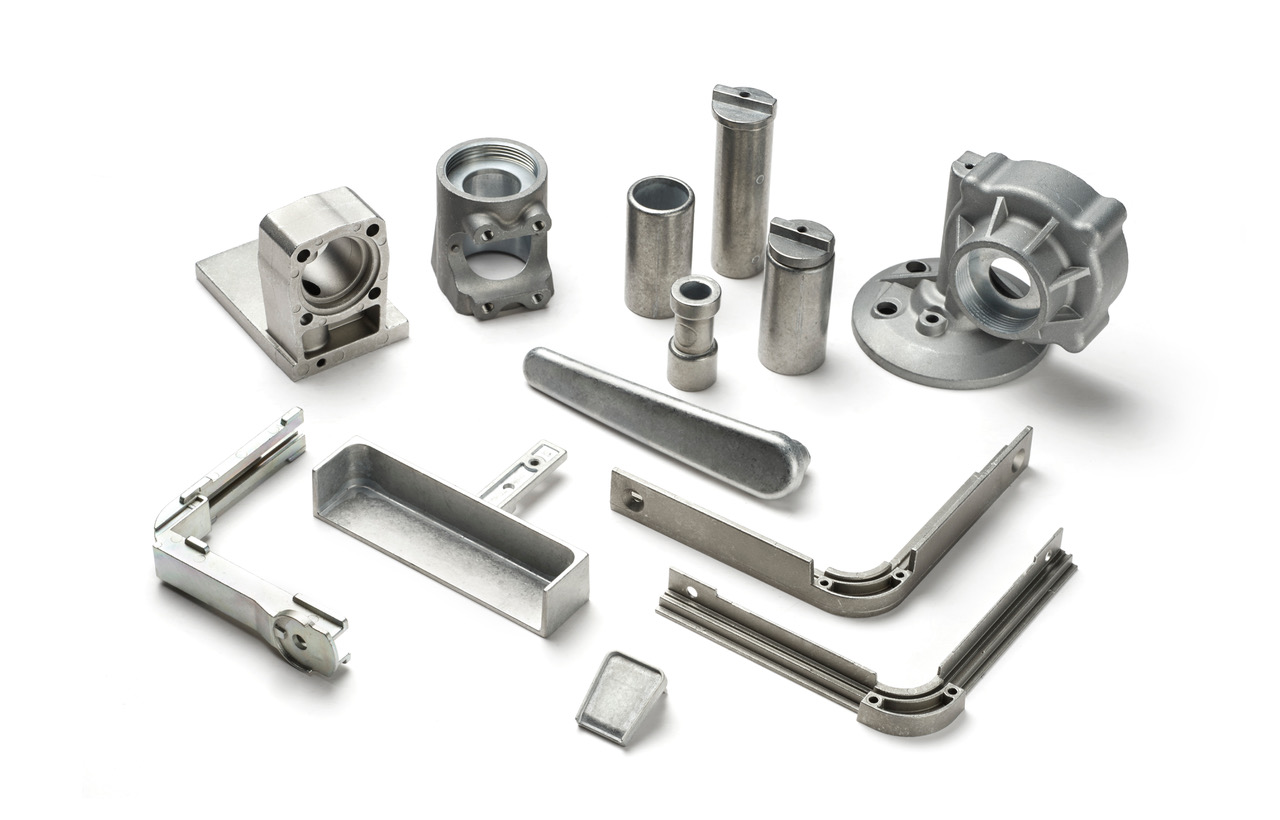
They are available as die-cast ZAMAK alloys of different grades, depending on the particular requirement. The grades available on these ranges are a variety of characteristics, higher strength or greater flexibility, based on how the component is used.
ZAMAK 3 and ZAMAK 5 are among the most used ZAMAK grades. ZAMAK 3 is a good strength, flexibility balance for many applications. In comparison with ZAMAK 5, this material has an excellent hardness and strength, which makes it ideal for structurally strong components.
ZAMAK is also available in additional grades. The following tables list the composition, benefits, and application of these alloys in the following order.
Table 1: Composition of ZAMAK Die Casting Alloys
ZAMAK Alloy Grade | Zinc (%) | Aluminum (%) | Magnesium (%) | Copper (%) | Other Elements |
ZAMAK Grade 2 | Balance | 4% | 0.035% | 1% | – |
ZAMAK Grade 3 | Balance | 3.5 to 4.3% | 0.02 to 0.05% | 0.25% | Fe <0.1%, Pb <0.005%, Cd <0.004%, Sn <0.003% |
ZAMAK Grade 5 | Balance | 3.5 to 4.3% | 0.03 to 0.06% | 0.75 to 1.25% | Fe 0.75%, Pb 0.004%, Cd 0.003%, Sn 0.002% |
ZAMAK Grade 7 | Balance | 3.5 to 4.3% | 0.005 to 0.02% | 0.25% | Fe 0.075%, Pb 0.003%, Cd 0.002%, Sn 0.001% |
Table 2: ZAMAK Die Casting Alloy Features & Applications
ZAMAK Alloy Grade | Features | Applications |
ZAMAK Grade 2 | Strongest and hardest ZAMAK alloy | Heavy-duty tools, machine parts |
ZAMAK Grade 3 | Balanced strength, flexibility, and castability | Automotive components, hardware, and electrical housings |
ZAMAK Grade 5 | Greater strength and hardness, excellent creep resistance | Gears, levers, small machine parts |
ZAMAK Grade 7 | Excellent flexibility and fluidity | Electrical terminals, connectors |
3. Benefits of ZAMAK Alloys in Die-Casting
The main reasons why ZAMAK alloys are used in the die casting process are as follows:
Low melting point: ZAMAK alloys have a low Melting Point and, in general, they melt at relatively low temperatures (typically around 380°C to 420°C), thus saving energy and increasing production speed.
Ease in Molding: ZAMAK alloys have easy flow characteristics that allow molten metal to easily fill the die cavity, thus making it conducive to the production of intricate and highly dimensional parts with close tolerances.
Strength-to-Weight Ratio: The mix that ZAMAK alloys provide between strength and weight is excellent, and they’re a good choice for lightweight, mechanical stress-resistant components.
Surface finish: Surface finish of the ZAMAK alloys is excellent, which makes them suitable for applications where aesthetics are a supreme factor. However, these alloys can undergo different surface treatments such as plating, anodizing, or painting that not only enhance their appearance but also the endurance of these alloys.
Recycling: ZAMAK alloys are fully recyclable and hence materials costs and waste are reduced. Recycling not only conserves resources but also increases a manufacturing cycle’s sustainability.
4. Common Applications of ZAMAK Alloys
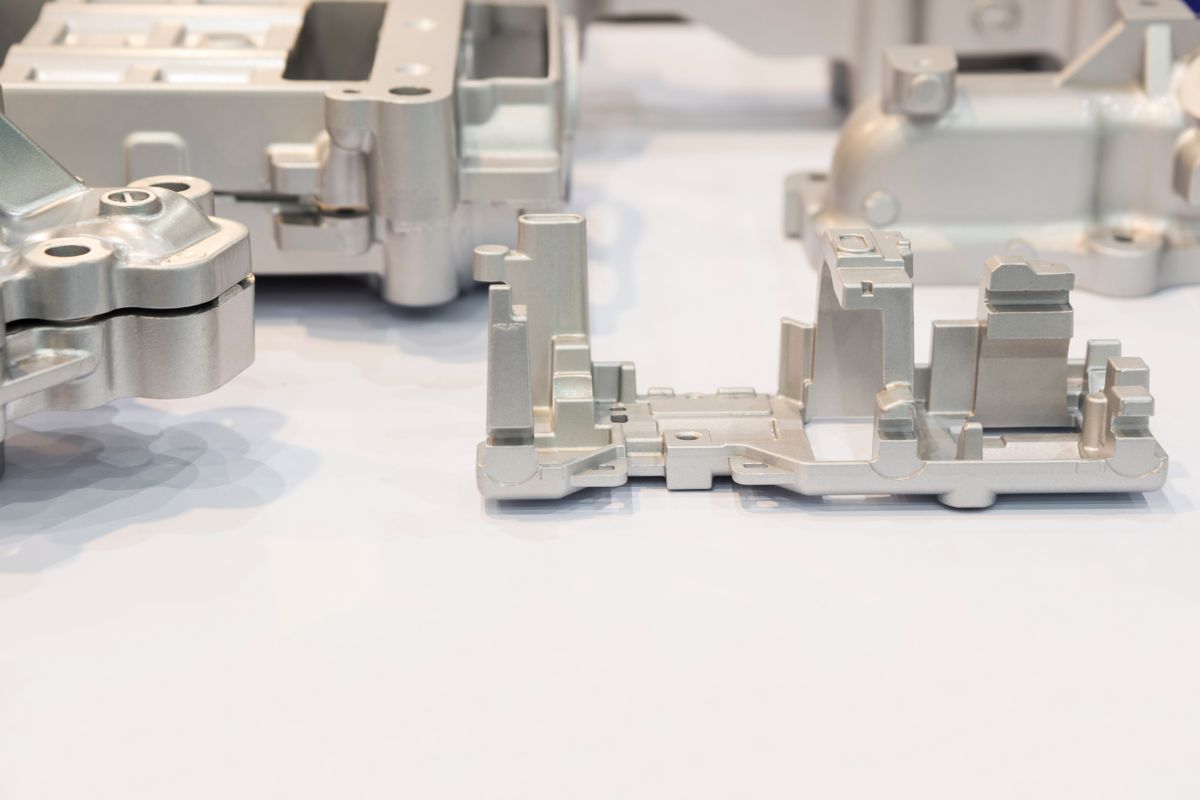
ZAMAK alloys are applied in a large range of industries:
- Carbon Foam Equivalent Die-cast ZAMAK is used for parts such as door handles, engine parts, and electrical housings because of the die-cast ZAMAK material’s strength, lightweight properties, and temperature integrity.
- ZAMAK alloys are the perfect choice for electronics such as those in mobile phone cases or circuit boards, or connector, and they provide good EMI shielding and durability.
- Common materials used for hardware which are also both strong and corrosion resistant are ZAMAK alloys, which are used in the production of faucets, door hardware, locks and knobs.
- Surface Finish Applications: ZAMAK lends itself well to decorative applications where many surface finishes can be applied, ranging from artistic applications as jewelry, collectible items, and ornaments.
Below is the table describing the application of ZAMAK die casting parts from various areas, and then paragraphs dedicated to each category mentioned in that table.
Applications of ZAMAK Die Casting Parts
Industry | Use Examples |
Automotive Industry | Door handles, knobs, clusters, AC ventilators, sound systems, seat belt adjusting parts, engine components, starters, car electronic gadgets. |
Electronics Industry | Laptop castings and parts, mobile phones, headphones, TV remote controls. |
Hardware and Furniture | Grips, levers, pulls, joints, drawer tracks, decorative furniture parts. |
Plumbing and Appliances | Tap handles, showerheads, appliance dials, switches, ornamental edging. |
Toys and Sporting Goods | Die-cast toy vehicles, mini trains, toy firearm parts, and sports gear parts. |
1. Automotive Industry
The automotive industry is one of the most extensive users of ZAMAK die casting parts because of its strength, precision and light weight. ZAMAK parts are lightweight, which is very beneficial concerning improved Fuel efficiency while maintaining the performance of various automotive components. The intricate parts manufactured like door handles, knobs and control clusters are durable and quite aesthetic and hence again ZAMAK alloys become the perfect choice. Moreover, ZAMAK is utilized in vital parts of air conditioning (AC) ventilators, sound system parts, seat belt adjusters, and engine parts so that the vehicle works properly even under tough conditions.
2. Electronics Industry
Die casting ZAMAK is of utmost importance for the electronics industry because of its effectiveness for shielding against electromagnetic interference (EMI). Due to the unique properties of ZAMAK, the potential disruptions of the signal that are common in electronic gadgets are prevented. Various products such as laptop castings, mobile phone parts, TV remote controls and headphones make use of ZAMAK parts. ZAMAK alloys offer a high level of precision and durability and are therefore a good choice for electronic components that have to show both structural integrity and resistance against the influence of electromagnetic fields.
3. Hardware and Furniture
This fact makes ZAMAK die casting parts widely used in the hardware and furniture industries due to their ability to produce excellent adhesion qualities and to attain a high-quality surface finish. As such, ZAMAK alloys are suitable for decorative applications. It is also commonly used in this field in grips and levers, pulls and joints, as well as drawer tracks and decorative furniture components. ZAMAK alloys can be coated with a variety of coatings – chrome or powder coatings, for example – to provide a top-quality finish that is still functional and durable.
4. Plumbing and Appliances
The corrosion resistance also makes ZAMAK die casting parts common in the plumbing and appliances industries, where parts are required to be strong. The main cause for the highly malleable nature of ZAMAK alloys is that they can be shaped into complex forms required in plumbing applications. Examples of ZAMAK parts in this field are tap handles, showerheads, appliance dials, and switches. ZAMAK can stand up to the harsh conditions of water and steam and still maintain structural integrity, and this makes it a good material for such applications.
5. Toys and Sporting Goods
ZAMAK die casting is generally used by the toy and sports equipment industries due to its strength, precision, and light weight characteristics. The ZAMAK alloys permit the making of specified and complex parts such as die-cast toy vehicles, mini trains or toy firearm components. Besides, ZAMAK is also durable and capable of withstanding wear and tear in sports gear parts. ZAMAK makes sure that the final product, like a toy car or sports item, is such that the aforementioned features are present in it.
5. ZAMAK alloys are used in die casting for a variety of reasons.
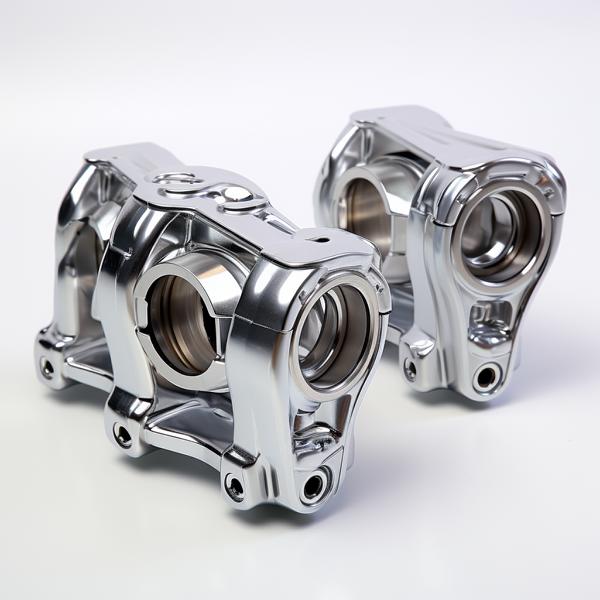
ZAMAK alloys, with their spectrum being mainly zinc, aluminum, magnesium, and copper, are becoming widely used in die casting because of their specific properties. In general, they provide benefits that surpass those of other metals in specific applications. Therefore, below are some key reasons why ZAMAK alloys are the most preferred in die casting:
Reason #1: High Fluidity
ZAMAK alloys, however, comprise one of the exceptional features, high fluidity. The ease with which molten metal flows into the die cavity during casting is referred to as fluidity. Since ZAMAK has this property, it is more easily filled into intricate mold designs with complex shapes. As the molten metal is free to flow to all parts of the die cavity, the finished die cast parts have smooth, consistent, and uniform surfaces. In particular, this quality is helpful for functional parts such as parts with complicated geometries that demand very fine details.
Reason #2: Toughness and High Rigidity
ZAMAK alloys have good toughness and easy deformation. These alloys are quite durable and can be used in continuous operation or high stress conditions. One of the main advantages of ZAMAK 2 and 5 is the high rigidity and toughness of these alloys, which are suitable for products which undergo heavy use. ZAMAK die casting alloys are reliable for components used in frequent stress and wear, as the alloy is durable.
Reason #3: High Strength-To-Weight Ratio
While the tensile strength of Aluminum alloys is slightly higher, ZAMAK alloys still compare very well on a strength-to-weight basis. ZAMAK die casting parts are lightweight yet have a tensile strength ranging from 280 MPa, which makes them suitable for many applications in varied industries where strength as well as weight reduction are the characteristics desired. The balance enjoyed by ZAMAKs refers to them as an ideal substitute for aluminum in case of parts that have to be both tough and light.
Reason #4: Low Melting Point
ZAMAK alloys have the advantage of a relatively low melting point that varies in the range of 380°C to 420°C (except ZAMAK 2). Several key benefits are provided by this characteristic:
- As a result, it is less expensive in energy, since it requires less energy to melt the metal at lower temperatures.
- Lower melting point: The result is faster solidification of the castings and thus faster production.
- Fewer casting defects: After solidifying a part very fast, it is harder to be affected by casting defects.
Reason #5: Excellent Adhesion
ZAMAK alloys are regarded as good bonders with different coating materials. This feature allows a wide variety (as contrasted to high precision) of conducting materials within the surface treatment (i.e., electroplating or painting) for a final product with a particular appearance. The strong adhesion ensures that coatings will stay in place over time, which contributes to the scope of improving both the aesthetics and durability of die-cast parts. The availability of this property works well with products demanding both the functionality and a premium finish.
Reason #6 Excellent Wearing and Bearing Properties
ZAMAK alloys have good resistance to wear and are resistant to the friction encountered in moving parts. ZAMAK components retain their functionality under continuous stress. Because of its resistance to wear, zamak die casting alloys can be used for applications specific to moving parts like gears, levers and other mechanical components. This leads to a minimization of the need for their frequent replacement, and offers long-term reliability with a minimized maintenance cost.
Reason #7: 100% Recyclable and Environmentally Friendly
ZAMAK alloys are recyclable and, therefore, an ecologically sound material. The quality of the final product does not suffer from re-melting and reusing scrap ZAMAK material. Also, it makes the product recyclable, reducing waste and decreasing raw material costs. ZAMAK alloys can be reused in many industries now that sustainability has become important, and using ZAMAK alloys helps improve the eco-friendly manufacturing process.
Reason #8: Cost-Effective
On the other hand, ZAMAK die-casting alloys cost a little more than aluminum alloys, yet the cost is affordable as it is lower than that of other metals. ZAMAK alloys are less expensive (and are thus economical) compared to high-performance alloys like brass and copper. ZAMAK alloys show excellent casting properties and are highly durable, and yet they are economical, all of which are appealing to manufacturers to strike the right balance between performance and budget.
6. How to Choose the Right Zamak Die Casting Manufacturer?
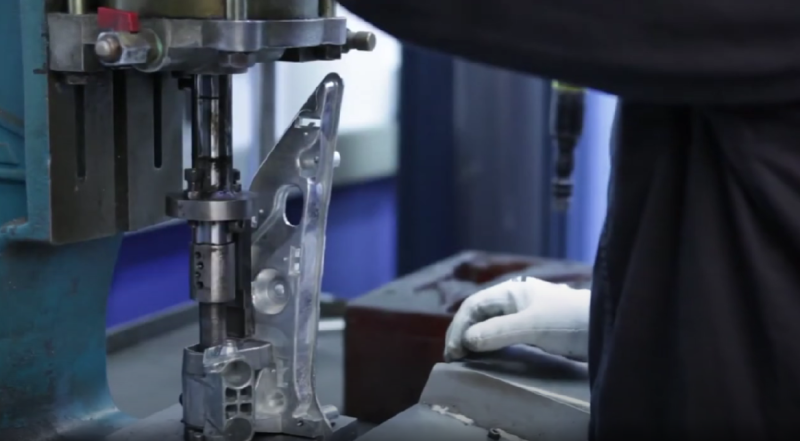
There are a few things to take into account when evaluating a Zamak die casting manufacturer or supplier to ensure optimal results for your project:
- The manufacturer should have experience in Zamak die casting as well as good experience with this alloy and the casting procedure. Thus, they can produce your high-quality part as you specify.
- Capabilities and Equipment – Search out a manufacturer with advanced equipment to carry out large production runs with precision and quality, capable of handling large production runs.
- A trustworthy producer should boast certifications like ISO 9001, indicating that they follow strict quality control procedures in bringing consistency and meeting high standards in every part.
- Every project should be unique, and a good Zamak die casting manufacturer should provide options to customize per your requirements, like custom finishes, special coatings, or special alloys like Die Cast Zamak 3.
- A strong relationship with the manufacturer is key – Customer Support. Check the suppliers who provide good customer support service throughout the process from design, production and post-delivery.
7. Why is Die Cast Zamak 3 such a popular choice for spotlights?
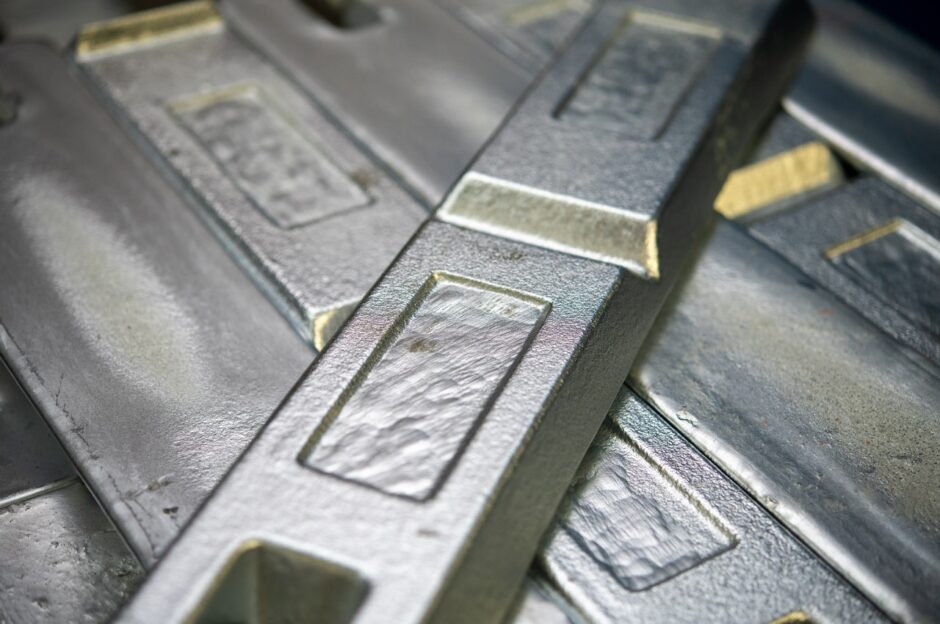
One of the most used Zamak alloys in the die casting industry is Die Cast Zamak 3. Zamak 3 is known for its good mechanical properties with good strength, durability, and ease of casting. Because of its high zinc content, it has come to have a good capacity to resist corrosion, which makes it suitable for parts exposed to outdoor environments and in the automotive industry. Also, Zamak 3 can be easily cast into complex shapes to help make it easier for both large and small-scale projects.
A result of these advantages is that Zamak 3 Die Cast remains the solution for many applications where strength, weight and corrosion resistance are vital.
We are CNM TECH – one of the leading ZAMAK die casting manufacturers.
We, at CNM TECH, are experts in delivering high-quality ZAMAK die casting. As a professional in the industry for years, we take pride in producing durable, precise and relatively cheap ZAMAK die-cast parts in a variety of industries. We use state-of-the-art manufacturing processes to make sure that we come out with quality and reliable parts.
Thus, we know what materials you need to use. That’s why we concentrate on ZAMAK alloys with excellent fluidity, high strength and weight ratios, low melting point and recyclability. Our ZAMAK die-cast components are suitable for automotive, electronics or hardware applications and will operate in the most extreme conditions.
We at thediecasting.com work with our clients to understand the exact needs and provide them solutions specially designed for their needs. As a testament to our expertise in innovation and having a team of skilled engineers, we promise to deliver precision-engineered products that have excellent surface finishes.
If you need top-quality ZAMAK die casting, CNM TECH is the right partner to turn your design into reality. If you’re interested in more on how we can help with your next project, check it out at thediecasting.com!
8. Conclusion
Finally, it is concluded that zamak die casting has unmatched advantages on the aspects of cost, efficiency and versatility. Regardless of whether you need parts for the automotive, electronics or consumer goods industries, die casting Zamak is a process which can give you high-quality quality durable parts. Die Casting Zamak 3 offers unique benefits and, coupled with utilizing a proper Zamak die casting manufacturer, can ensure your job fulfills all the mandates while keeping your production costs down. Using this strength, the precision and efficiency of Zamak die casting, companies are still able to create high-performance parts to continue meeting the changing needs of modern industries.
FAQs
1. What is Zamak die casting?
It is also known as the process of creating precise, durable parts by injecting molten Zamak alloy into a mold. It is popular because it is cost-effective, strong and can be used to produce complex shapes with little need for finishing.
2. What is the difference between the Zamak 3 and other Zamak alloys?
Zamak 3 is the most common Zamak alloy because of the balance of strength and ease of casting. Other alloys, such as Zamak 5 provide higher strength or hardness depending on the need, but Zamak 3 is extremely versatile.
3. The Zamak die casting is used in?
Among the automotive, electronics, consumer goods, and industrial equipment industries, the durable and accurate components it produces with Zamak die casting have a lot of popularity.
4. What is the process to select a Zamak die casting manufacturer?
Select a Zamak Die Casting manufacturer with experience, equipment capability, quality certification, customization, and solid customer service.