
ZAMAK, alüminyum, bakır (Kupfer) ve magnezyum ile birlikte kullanılan çinko bazlı bir alaşıma verilen isimdir. ZAMAK adını bu kelimelerden Almanca olarak almıştır. Bu alaşım genellikle 94% ila 96% çinko içerir, diğer malzemeler folyo veya levhaya eklenir. Birkaç dikkat çekici özellik ZAMAK alaşımlarını basınçlı döküm uygulamaları için iyi hale getirir. Bu alaşımların düşük erime noktasına, yüksek akışkanlığa ve ağırlık başına yüksek mukavemete sahip olması, onları sert, sağlam ve doğru parçalar yapmak için olağanüstü derecede kullanışlı hale getirir. Bu temel özelliklere ek olarak, ZAMAK alaşımları onları çeşitli endüstriyel uygulamalar için nitelendiren başka özellikler de sunar.
Zamak basınçlı döküm, metal döküm dünyasında son derece uygun maliyetli ve rahat bir metal döküm yöntemi olarak kendini kanıtlamıştır. Zamak, birçok endüstride karmaşık yüksek kaliteli parçalar üretmek için yaygın olarak kullanılan bir çinko alaşım ailesidir. Süreç, erimiş Zamak alaşımının yüksek basınç altında bir metal kalıba veya kalıba enjekte edilmesini içerir. Süreç, hassas parçaların üretimi için uygun hale getiren çok iyi yüzey kaplamaları ile çok yakın toleranslarda karmaşık parçalar yapabilir. Zamak basınçlı dökümün daha kritik bir rolü vardır, çünkü endüstriler geliştikçe dayanıklı, hafif ve güçlü malzemelere olan ihtiyaç artmaktadır. Bu makalede, Zamak basınçlı dökümün önemini ve bir kişinin neden diğer döküm yöntemlerine göre Zamak basınçlı dökümü tercih etmesi gerektiğini analiz ediyoruz.
ZAMAK alaşımları dökümhanelerde parça dökümü için kullanılmakta ve döküm parçaları otomotiv, elektronik ve donanım gibi birçok endüstriyi kapsamaktadır. Bu alaşımların sürdürülebilirlik hedeflerine uygun olarak tamamen geri dönüştürülebilir olması da ekstra bir avantaj sağlamaktadır. Bununla birlikte, ZAMAK basınçlı döküm parçaları, özellikle bu dekoratif parçalar olmak üzere, birinci sınıf bir görünüme sahip estetik açıdan çekici ürünlere sahip olmak için üreticilere yardımcı olacak ek yüzey seçeneklerine sahiptir.
ZAMAK Basınçlı Döküm Nedir?
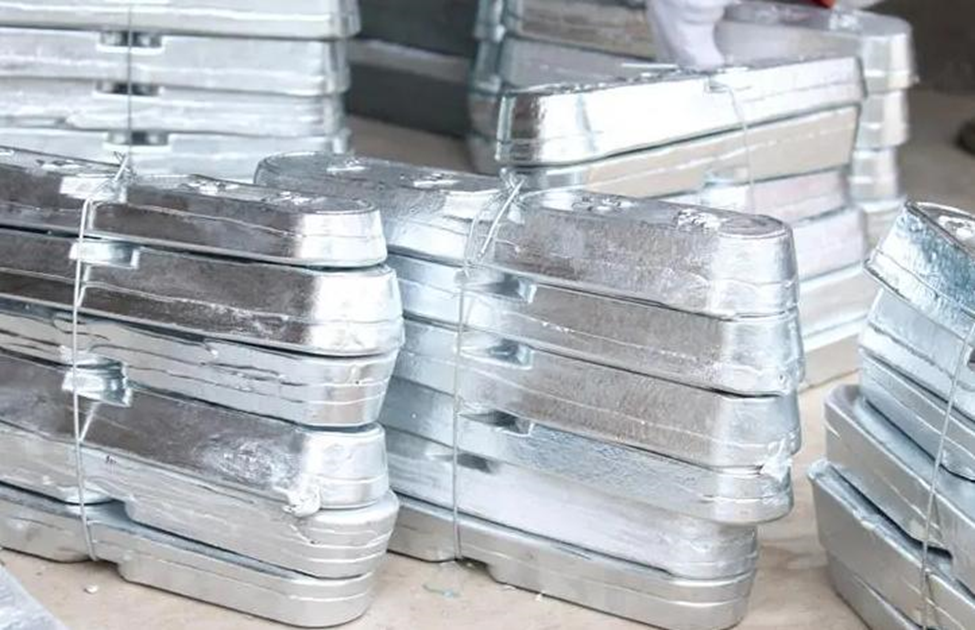
ZAMAK basınçlı döküm, erimiş ZAMAK alaşımının yüksek basınç altında bir kalıba enjekte edildiği yaygın olarak kullanılan bir metal döküm tekniğidir. Bu işlemde tipik olan, dayanıklı takım çeliğinden yapılmış kalıp veya kalıptır. Her şekil için çeşitli kalıplara ihtiyaç vardır ve ZAMAK basınçlı döküm işlemi sadece sıcak kamaralı bir basınçlı döküm makinesi gerektirir.
İki kovanlı bir sıcak kamaralı döküm makinesi, bir sabit yarı ve bir hareketli yarı ile düzenlenmiştir. Bu yarımlar daha sonra kapatılır ve erimiş metal bir enjeksiyon odası tarafından kalıba enjekte edilir. Metal katılaştığında, döküm parça ejektör pimleri ile kalıptan çıkarılır. ZAMAK basınçlı döküm, ZAMAK alaşımlarında bu yöntemi kullanır.
Sıcak Kamaralı Basınçlı Döküm (HPDC), Düşük Basınçlı Basınçlı Döküm (LPDC) ve Kokil Basınçlı Döküm (GDC), ZAMAK alaşımlarının farklı uygulamalar için kendi avantajları ile basınçlı döküm proseslerine uygun olası tipleridir.
1. ZAMAK Basınçlı Döküm Süreci
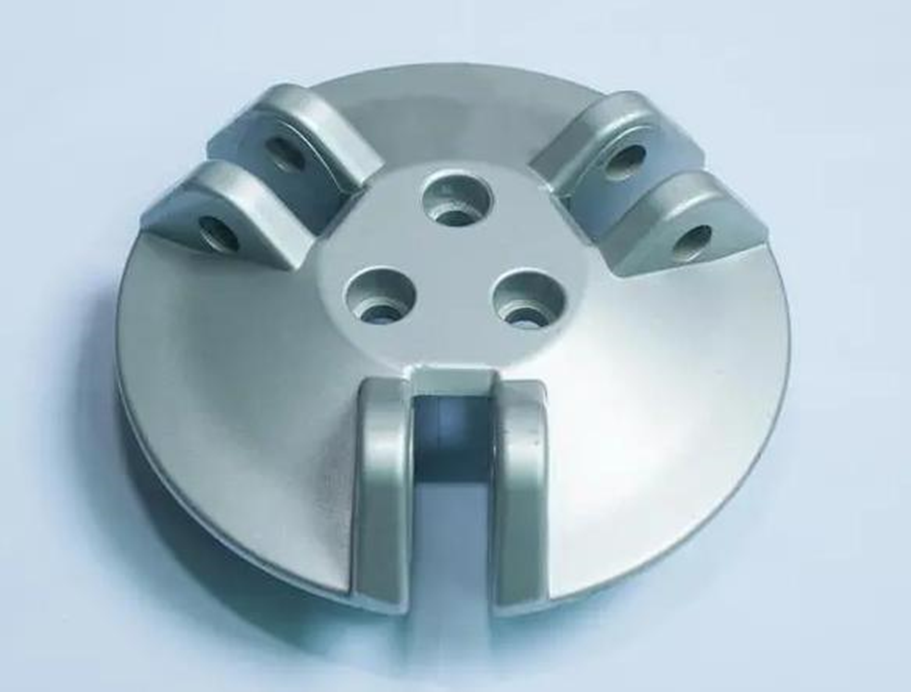
Diğer alüminyum veya magnezyum basınçlı döküm türleri gibi, ZAMAK basınçlı döküm yöntemine de mümkün olan her yerde dikkat edilmesi gerekir, çünkü sonuçlar yalnızca ZAMAK döküm işlemi kadar iyidir. Tipik ZAMAK basınçlı döküm süreci aşağıda bir döküm halinde yazılmıştır:
Adım#1: Kalıbın Tasarlanması ve Oluşturulması
ZAMAK basınçlı döküm prosesinde süreç kalıp veya kalıp tasarımı ve nihai parça tasarımı ile başlar. Bu, dökümün nihai sonucunu belirlediği için önemlidir. İlk olarak mühendisler özel CAD yazılımı kullanarak dökülecek parçanın 3D modelini tasarlar. Tipik olarak, bir prototip yapılır ve test edilir, tasarım son versiyonun onaylanmasına kadar geliştirilir. İkinci olarak, nihai bir parça tasarımı olduğunda, kalıp oluşturulur, bu da şu anlama gelir:
Enjeksiyon tipi: ZAMAK'ın erime noktası, kalıba enjekte edilebilmesi için yeterince sıcak olması gerekecek kadar düşüktür.
- Boşlukların sayısına mühendisler karar verir: Bunlar maksimum verimlilik için düzenlenmiştir.
- Ayırma sisteminin belirlenmesi: Bu, kalıbın iki yarısının nasıl birleştiğidir.
- Bu, döküm parçanın hasar görmeden sorunsuz bir şekilde çıkarılmasını ve hassas bir ejektör sistemi tasarımını sağlar.
- Soğutma sistemi planlaması: Soğutma olmadan hatalar meydana gelir ve parça kalitesi tutarlı olamaz.
- Kalıp malzemesinin seçilmesi: H13, SKD61 veya diğer takım çelikleri gibi metaller dayanıklılık ve ısı direnci açısından iyidir.
Adım #2: ZAMAK Alaşımının Hazırlanması
Bundan sonra ZAMAK alaşımı hazırlanır. ZAMAK alaşımı, termal arıtma, kimyasal reaksiyon, elektrolitik arıtma ve bölgesel arıtma gibi çeşitli arıtma yöntemleriyle saflaştırılır.
Alaşım, safsızlıklarla sıvı hale gelmesini önlemek için sıkı bir şekilde kontrol edilen sıcaklıklarda bir fırında eritilir. Son arıtma işleminden sonra erimiş metal, kirlenmeyi önlemek amacıyla sıcaklığı kontrol etmek için bir enjeksiyon odasında tutulur.
Adım #3: Erimiş ZAMAK'ın Kalıba Enjekte Edilmesi.
Basınçlı dökümün kritik aşamalarından biri erimiş ZAMAK'ın kalıba enjekte edilmesidir. Erimiş metal, enjeksiyon odasında hazırlanıp depolandıktan sonra yüksek basınç altında bir pistonla kalıba enjekte edilir. Erimiş alaşım basınca maruz kalır ve boşluğun tüm alanı doldurulduğundan kalıbın her köşesine zorlanır.
Bu şekilde, parçanın yüzeyi düzgün ve pürüzsüz hale getirilebilir ve uygun enjeksiyon teknikleriyle kaliteli sonuçlar elde edilebilir. Ayrıca, kalıbın enjeksiyon kanallarının tasarımı da bunu başarmanın önemli bir belirleyicisidir.
Adım 4: Parçanın Soğutulması ve Katılaştırılması
Ancak, erimiş metal kalıba girer girmez soğutma başlar. Erimiş metalin ısısını katılaşmasına yetecek kadar hızlı bir şekilde çekmek için yüksek kaliteli takım çeliği kalıbını hızlı bir şekilde döndürürler. Soğutma sistemi, katılaşma sürecini hızlandırmak için birçok kalıp tarafından da kullanılır.
Basitçe, istenen parça kalitesini elde etmek ve kusurları önlemek için tutarlı bir soğutma hızı gereklidir ve en yaygın olarak kullanılanlar su ve hava soğutma sistemleridir.
Adım #5: Katılaşmış ZAMAK Döküm Ejeksiyonu
ZAMAK alaşımının katılaşmasından sonraki adım, dökümün kalıptan çıkarılmasıdır. Parçanın kalitesini korumak için buna dikkat edilir. Katılaşan parçayı kalıptan dışarı atmak için ejektör pimleri kullanılır. Kalıp ikiye ayrılır, itici pim harekete geçirilir ve döküm serbest bırakılır. Bu adımı gerçekleştirmek için iyi bir hassasiyet derecesi vardır, çünkü döküm üzerindeki çok fazla kuvvet ona zarar verebilir. İtici pimin doğru hizalanması da yüzey kusurları veya çukurlar olmamasını sağlayacaktır.
Adım #6: Son İşlem ve Düzeltme
Döküm genellikle üzerinde flashing olarak bilinen ve çıkarılması gereken fazla malzeme ile çıkarılır. Bunlar da parçanın çalışmasını etkileyebilir ve dikkatlice düzeltilmeleri gerekir. Parçanın temizlenmesi çeşitli düzeltme aletleri ile gerçekleştirilir - taşlama, parlatma makineleri. Bazı dökümhaneler manuel olarak düzeltme yapabilir. Kırpılan parçalar, parçanın finisajını iyileştirmek için daha fazla yüzey işlemine tabi tutulabilir.
Adım #7: Yüzey İşlemi
Yüzey işlemi, ZAMAK basınçlı dökümün son aşamasıdır. Parçanın görünümünü iyileştirmenin yanı sıra korozyon ve aşınmadan da koruyan yüzey işlemleri sadece dekoratif nedenlerle yapılmaz. ZAMAK, ticari olarak en çok kullanılan yüzey işlemlerinden biridir ve çoğunlukla çinko kaplama yöntemiyle yapılır; burada çinko kaplanacak yüzey, örneğin ZAMAK parçası, bir çinko veya siyah nikel, krom veya başka bir malzeme tabakasıyla kaplanır. Çok popüler olan bir diğer yüksek profilli sektör de sprey boyama ve toz boyamayı içeren boyamadır. Toz kaplama işleminin avantajı, genellikle ufalanmaya ve aşınmaya karşı daha az duyarlı olmasıdır.
Bu nedenle, daha az yaygın olarak kullanılmasına rağmen eloksal, yüzey sertliğini artırırken, özellikle otomotiv veya mobilya endüstrisi ve diğerleri gibi en yüksek kaliteli uygulamalar için korozyon direnci de ekler.
2. Basınçlı Döküm Çeşitleri ZAMAK Alaşımları
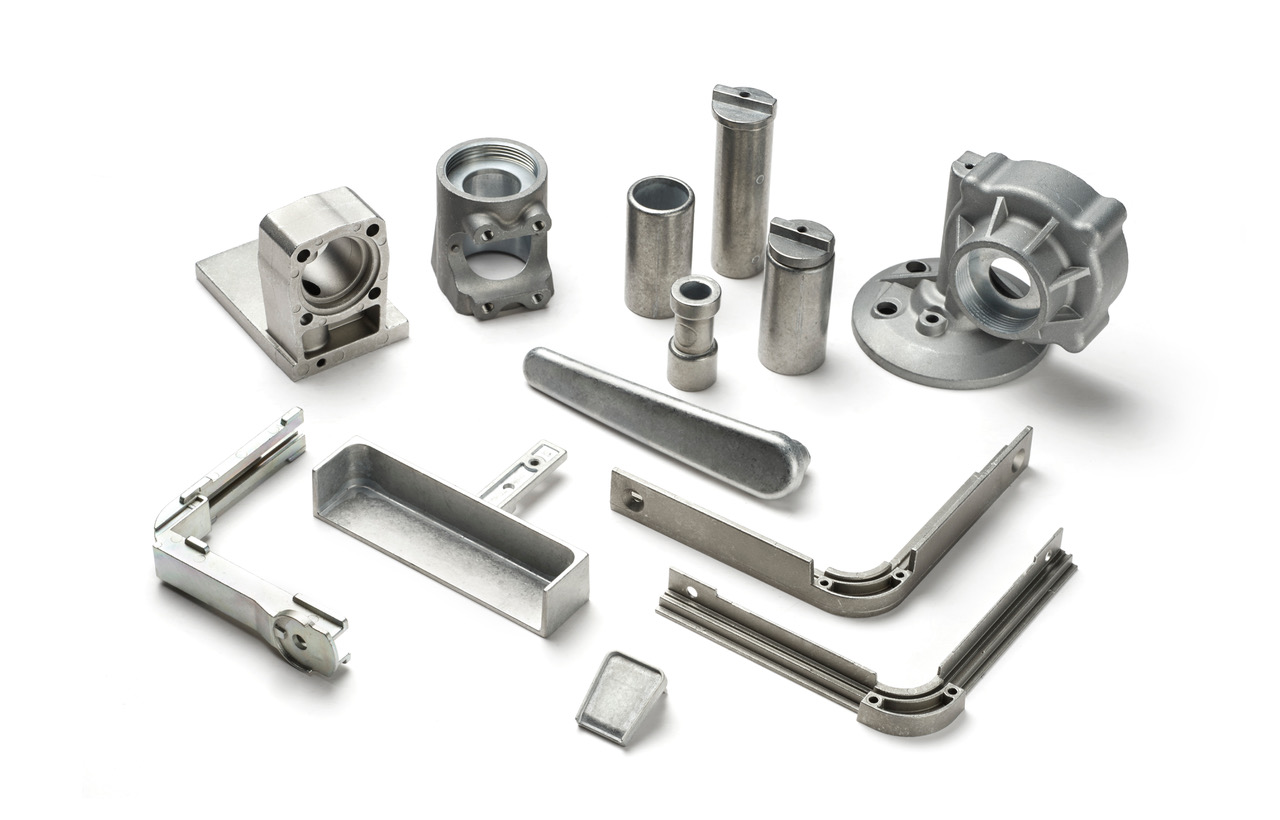
Bunlar, özel gereksinime bağlı olarak farklı derecelerde döküm ZAMAK alaşımları olarak mevcuttur. Bu serilerde mevcut olan kaliteler, bileşenin nasıl kullanıldığına bağlı olarak çeşitli özelliklere, daha yüksek mukavemete veya daha fazla esnekliğe sahiptir.
ZAMAK 3 ve ZAMAK 5 en çok kullanılan ZAMAK kaliteleri arasındadır. ZAMAK 3 birçok uygulama için iyi bir mukavemet, esneklik dengesidir. ZAMAK 5 ile karşılaştırıldığında, bu malzeme mükemmel bir sertliğe ve mukavemete sahiptir, bu da onu yapısal olarak güçlü bileşenler için ideal kılar.
ZAMAK'ın ek kaliteleri de mevcuttur. Aşağıdaki tablolar bu alaşımların bileşimini, faydalarını ve uygulamalarını aşağıdaki sırayla listelemektedir.
Tablo 1: ZAMAK Basınçlı Döküm Alaşımlarının Bileşimi
ZAMAK Alaşım Sınıfı | Çinko (%) | Alüminyum (%) | Magnezyum (%) | Bakır (%) | Diğer Unsurlar |
ZAMAK 2. Sınıf | Denge | 4% | 0.035% | 1% | - |
ZAMAK 3. Sınıf | Denge | 3,5 ila 4,3% | 0,02 ila 0,05% | 0.25% | Fe <0,1%, Pb <0,005%, Cd <0,004%, Sn <0,003% |
ZAMAK 5. Sınıf | Denge | 3,5 ila 4,3% | 0,03 ila 0,06% | 0,75 ila 1,25% | Fe 0.75%, Pb 0.004%, Cd 0.003%, Sn 0.002% |
ZAMAK 7. Sınıf | Denge | 3,5 ila 4,3% | 0,005 ila 0,02% | 0.25% | Fe 0.075%, Pb 0.003%, Cd 0.002%, Sn 0.001% |
Tablo 2: ZAMAK Basınçlı Döküm Alaşım Özellikleri ve Uygulamaları
ZAMAK Alaşım Sınıfı | Özellikler | Uygulamalar |
ZAMAK 2. Sınıf | En güçlü ve en sert ZAMAK alaşımı | Ağır hizmet aletleri, makine parçaları |
ZAMAK 3. Sınıf | Dengeli güç, esneklik ve dökülebilirlik | Otomotiv bileşenleri, donanım ve elektrik muhafazaları |
ZAMAK 5. Sınıf | Daha yüksek mukavemet ve sertlik, mükemmel sürünme direnci | Dişliler, kollar, küçük makine parçaları |
ZAMAK 7. Sınıf | Mükemmel esneklik ve akışkanlık | Elektrik terminalleri, konektörler |
3. Basınçlı Dökümde ZAMAK Alaşımlarının Faydaları
ZAMAK alaşımlarının basınçlı döküm prosesinde kullanılmasının başlıca nedenleri aşağıdaki gibidir:
Düşük erime noktası: ZAMAK alaşımları düşük Erime Noktasına sahiptir ve genel olarak nispeten düşük sıcaklıklarda (tipik olarak 380°C ila 420°C civarında) erir, böylece enerji tasarrufu sağlar ve üretim hızını artırır.
Kalıplama Kolaylığı: ZAMAK alaşımları, erimiş metalin kalıp boşluğunu kolayca doldurmasını sağlayan kolay akış özelliklerine sahiptir, bu nedenle yakın toleranslara sahip karmaşık ve yüksek boyutlu parçaların üretimine elverişlidir.
Güç-Ağırlık Oranı: ZAMAK alaşımlarının mukavemet ve ağırlık arasında sağladığı karışım mükemmeldir ve hafif, mekanik gerilime dayanıklı bileşenler için iyi bir seçimdir.
Yüzey kaplaması: ZAMAK alaşımlarının yüzey kalitesi mükemmeldir, bu da onları estetiğin üstün bir faktör olduğu uygulamalar için uygun hale getirir. Bununla birlikte, bu alaşımlar kaplama, eloksal veya boyama gibi farklı yüzey işlemlerine tabi tutulabilir, bu da sadece görünümlerini değil, aynı zamanda bu alaşımların dayanıklılığını da arttırır.
Geri dönüşüm: ZAMAK alaşımları tamamen geri dönüştürülebilir ve böylece malzeme maliyetleri ve atıklar azaltılır. Geri dönüşüm sadece kaynakları korumakla kalmaz, aynı zamanda bir üretim döngüsünün sürdürülebilirliğini de artırır.
4. ZAMAK Alaşımlarının Yaygın Uygulamaları
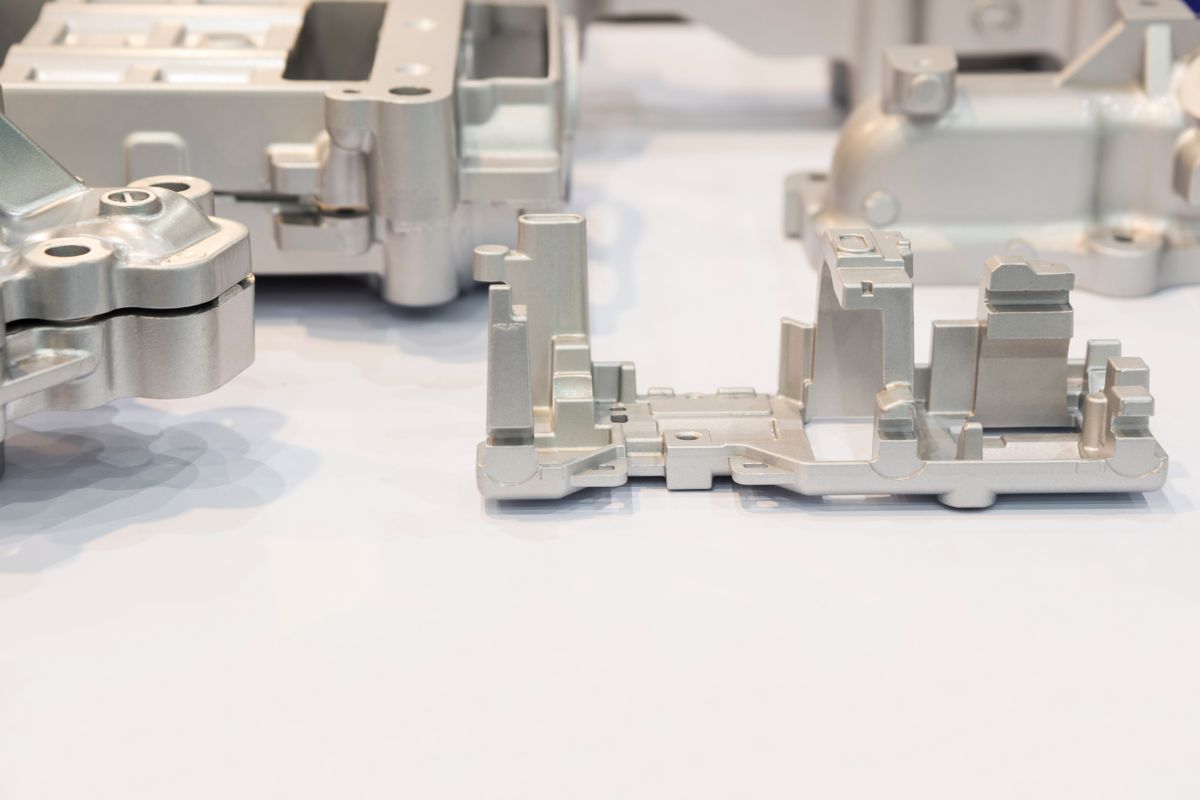
ZAMAK alaşımları çok çeşitli endüstrilerde uygulanmaktadır:
- Karbon Köpük Eşdeğeri Döküm ZAMAK, döküm ZAMAK malzemesinin mukavemeti, hafif özellikleri ve sıcaklık bütünlüğü nedeniyle kapı kolları, motor parçaları ve elektrik muhafazaları gibi parçalar için kullanılır.
- ZAMAK alaşımları, cep telefonu kasaları veya devre kartları veya konektörler gibi elektronik cihazlar için mükemmel bir seçimdir ve iyi EMI koruması ve dayanıklılık sağlarlar.
- Hem güçlü hem de korozyona dayanıklı olan donanımlar için kullanılan yaygın malzemeler, musluk, kapı donanımı, kilit ve topuz üretiminde kullanılan ZAMAK alaşımlarıdır.
- Yüzey İşlem Uygulamaları: ZAMAK, takı, koleksiyon ürünleri ve süs eşyaları gibi sanatsal uygulamalara kadar birçok yüzey kaplamasının uygulanabileceği dekoratif uygulamalara uygundur.
Aşağıda, ZAMAK basınçlı döküm parçalarının çeşitli alanlardaki uygulamalarını açıklayan tablo ve ardından bu tabloda belirtilen her kategoriye ayrılmış paragraflar bulunmaktadır.
ZAMAK Basınçlı Döküm Parça Uygulamaları
Endüstri | Örnekleri Kullanın |
Otomotiv Endüstrisi | Kapı kolları, düğmeler, kümeler, klima vantilatörleri, ses sistemleri, emniyet kemeri ayar parçaları, motor bileşenleri, marş motorları, araç elektronik aygıtları. |
Elektronik Endüstrisi | Dizüstü bilgisayar dökümleri ve parçaları, cep telefonları, kulaklıklar, TV uzaktan kumandaları. |
Donanım ve Mobilya | Kulplar, kollar, çekmeler, bağlantılar, çekmece rayları, dekoratif mobilya parçaları. |
Sıhhi Tesisat ve Aletler | Musluk kulpları, duş başlıkları, cihaz kadranları, anahtarlar, süs kenarları. |
Oyuncaklar ve Spor Malzemeleri | Die-cast oyuncak araçlar, mini trenler, oyuncak ateşli silah parçaları ve spor dişli parçaları. |
1. Otomotiv Endüstrisi
Otomotiv endüstrisi, mukavemeti, hassasiyeti ve hafifliği nedeniyle ZAMAK basınçlı döküm parçalarının en kapsamlı kullanıcılarından biridir. ZAMAK parçaları hafiftir, bu da çeşitli otomotiv bileşenlerinin performansını korurken yakıt verimliliğinin artırılması açısından çok faydalıdır. Kapı kolları, düğmeler ve kontrol kümeleri gibi üretilen karmaşık parçalar dayanıklı ve oldukça estetiktir ve bu nedenle yine ZAMAK alaşımları mükemmel bir seçim haline gelir. Ayrıca ZAMAK, klima (AC) vantilatörleri, ses sistemi parçaları, emniyet kemeri ayarlayıcıları ve motor parçaları gibi hayati parçalarda kullanılarak aracın zorlu koşullar altında bile düzgün çalışmasını sağlamaktadır.
2. Elektronik Endüstrisi
Basınçlı döküm ZAMAK, elektromanyetik parazitlere (EMI) karşı koruma etkinliği nedeniyle elektronik endüstrisi için büyük önem taşımaktadır. ZAMAK'ın benzersiz özellikleri sayesinde, elektronik cihazlarda yaygın olan potansiyel sinyal kesintileri önlenir. Dizüstü bilgisayar dökümleri, cep telefonu parçaları, TV uzaktan kumandaları ve kulaklıklar gibi çeşitli ürünlerde ZAMAK parçaları kullanılmaktadır. ZAMAK alaşımları yüksek düzeyde hassasiyet ve dayanıklılık sunar ve bu nedenle hem yapısal bütünlük hem de elektromanyetik alanların etkisine karşı direnç göstermesi gereken elektronik bileşenler için iyi bir seçimdir.
3. Donanım ve Mobilya
Bu gerçek, ZAMAK basınçlı döküm parçalarının mükemmel yapışma kaliteleri üretme ve yüksek kaliteli bir yüzey kalitesi elde etme yetenekleri nedeniyle donanım ve mobilya endüstrilerinde yaygın olarak kullanılmasını sağlar. Bu nedenle, ZAMAK alaşımları dekoratif uygulamalar için uygundur. Bu alanda kulplar ve kollar, çekmeler ve bağlantıların yanı sıra çekmece rayları ve dekoratif mobilya bileşenlerinde de yaygın olarak kullanılır. ZAMAK alaşımları çeşitli kaplamalarla (örneğin krom veya toz kaplamalarla) kaplanarak işlevselliğini ve dayanıklılığını koruyan üstün kaliteli bir yüzey elde edilebilir.
4. Sıhhi Tesisat ve Aletler
Korozyon direnci, ZAMAK basınçlı döküm parçalarını, parçaların güçlü olması gereken sıhhi tesisat ve beyaz eşya endüstrilerinde de yaygın hale getirmektedir. ZAMAK alaşımlarının son derece dövülebilir doğasının ana nedeni, sıhhi tesisat uygulamalarında gerekli olan karmaşık formlara şekillendirilebilmeleridir. Bu alandaki ZAMAK parçalarına örnek olarak musluk kolları, duş başlıkları, cihaz kadranları ve anahtarlar verilebilir. ZAMAK, su ve buharın zorlu koşullarına dayanabilir ve yine de yapısal bütünlüğünü koruyabilir ve bu da onu bu tür uygulamalar için iyi bir malzeme yapar.
5. Oyuncaklar ve Spor Malzemeleri
ZAMAK basınçlı döküm, mukavemet, hassasiyet ve hafiflik özellikleri nedeniyle genellikle oyuncak ve spor malzemeleri endüstrileri tarafından kullanılmaktadır. ZAMAK alaşımları, basınçlı döküm oyuncak araçlar, mini trenler veya oyuncak ateşli silah bileşenleri gibi belirli ve karmaşık parçaların yapılmasına izin verir. Ayrıca, ZAMAK dayanıklıdır ve spor dişli parçalarında aşınma ve yıpranmaya dayanabilir. ZAMAK, bir oyuncak araba veya spor eşyası gibi nihai ürünün yukarıda belirtilen özelliklere sahip olmasını sağlar.
5. ZAMAK alaşımları basınçlı dökümde çeşitli nedenlerle kullanılır.
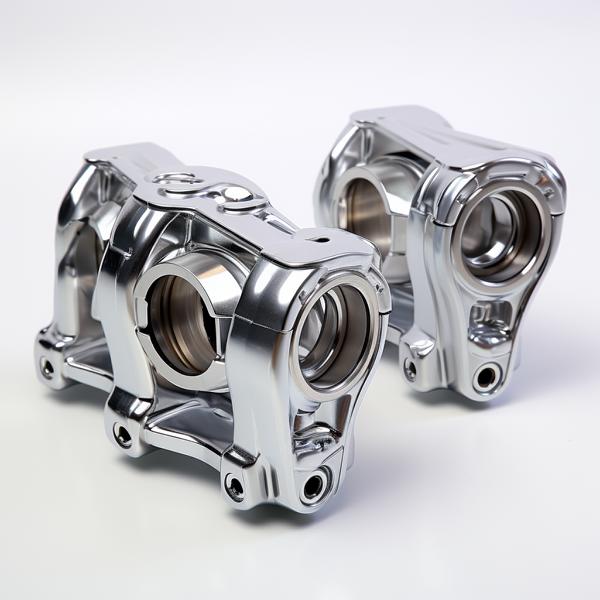
Spektrumları ağırlıklı olarak çinko, alüminyum, magnezyum ve bakır olan ZAMAK alaşımları, spesifik özellikleri nedeniyle basınçlı dökümde yaygın olarak kullanılmaktadır. Genel olarak, belirli uygulamalarda diğer metallerinkini aşan faydalar sağlarlar. Bu nedenle, aşağıda ZAMAK alaşımlarının basınçlı dökümde en çok tercih edilmesinin bazı temel nedenleri yer almaktadır:
Sebep #1: Yüksek Akışkanlık
Ancak ZAMAK alaşımları istisnai özelliklerden biri olan yüksek akışkanlığa sahiptir. Döküm sırasında erimiş metalin kalıp boşluğuna akma kolaylığı akışkanlık olarak adlandırılır. ZAMAK bu özelliğe sahip olduğundan, karmaşık şekillere sahip girift kalıp tasarımlarına daha kolay doldurulur. Erimiş metal kalıp boşluğunun tüm kısımlarına serbestçe akabildiğinden, bitmiş basınçlı döküm parçalar pürüzsüz, tutarlı ve tek tip yüzeylere sahiptir. Bu kalite özellikle, çok ince detaylar gerektiren karmaşık geometrilere sahip parçalar gibi işlevsel parçalar için faydalıdır.
Neden #2: Tokluk ve Yüksek Sertlik
ZAMAK alaşımları iyi tokluğa ve kolay deformasyona sahiptir. Bu alaşımlar oldukça dayanıklıdır ve sürekli çalışma veya yüksek stres koşullarında kullanılabilir. ZAMAK 2 ve 5'in ana avantajlarından biri, ağır kullanıma maruz kalan ürünler için uygun olan bu alaşımların yüksek sertliği ve tokluğudur. ZAMAK basınçlı döküm alaşımları, alaşım dayanıklı olduğu için sık stres ve aşınmada kullanılan bileşenler için güvenilirdir.
Neden #3: Yüksek Mukavemet-Ağırlık Oranı
Alüminyum alaşımlarının çekme mukavemeti biraz daha yüksek olsa da, ZAMAK alaşımları yine de mukavemet-ağırlık bazında çok iyi karşılaştırılır. ZAMAK basınçlı döküm parçaları hafiftir ancak 280 MPa arasında değişen bir çekme mukavemetine sahiptir, bu da onları mukavemetin yanı sıra ağırlık azaltmanın da istenen özellikler olduğu çeşitli endüstrilerdeki birçok uygulama için uygun hale getirir. ZAMAK'ların sahip olduğu denge, hem sağlam hem de hafif olması gereken parçalar söz konusu olduğunda alüminyum için ideal bir ikame olduğunu ifade eder.
Sebep #4: Düşük Erime Noktası
ZAMAK alaşımları 380°C ila 420°C aralığında değişen nispeten düşük erime noktası avantajına sahiptir (ZAMAK 2 hariç). Bu özellik birkaç önemli fayda sağlamaktadır:
- Sonuç olarak, metali daha düşük sıcaklıklarda eritmek için daha az enerji gerektirdiğinden enerji açısından daha ucuzdur.
- Daha düşük erime noktası: Sonuç, dökümlerin daha hızlı katılaşması ve dolayısıyla daha hızlı üretimdir.
- Daha az döküm hatası: Bir parça çok hızlı katılaştıktan sonra, döküm hatalarından etkilenmesi daha zordur.
Sebep #5: Mükemmel Yapışma
ZAMAK alaşımları farklı kaplama malzemeleri ile iyi bağlayıcılar olarak kabul edilir. Bu özellik, belirli bir görünüme sahip nihai bir ürün için yüzey işleminde (örn. elektrokaplama veya boyama) çok çeşitli (yüksek hassasiyetin aksine) iletken malzemelere izin verir. Güçlü yapışma, kaplamaların zaman içinde yerinde kalmasını sağlayarak döküm parçaların hem estetiğini hem de dayanıklılığını geliştirme kapsamına katkıda bulunur. Bu özelliğin kullanılabilirliği, hem işlevsellik hem de birinci sınıf bir yüzey talep eden ürünlerde işe yarar.
Sebep #6 Mükemmel Aşınma ve Yatak Özellikleri
ZAMAK alaşımları aşınmaya karşı iyi bir dirence sahiptir ve hareketli parçalarda karşılaşılan sürtünmeye karşı dayanıklıdır. ZAMAK bileşenleri sürekli stres altında işlevselliklerini korurlar. Aşınmaya karşı direnci nedeniyle, zamak döküm alaşımları dişliler, kollar ve diğer mekanik bileşenler gibi hareketli parçalara özgü uygulamalar için kullanılabilir. Bu, sık değiştirme ihtiyacının en aza indirilmesine yol açar ve en aza indirilmiş bakım maliyeti ile uzun vadeli güvenilirlik sunar.
Sebep #7: 100% Geri Dönüştürülebilir ve Çevre Dostu
ZAMAK alaşımları geri dönüştürülebilir ve bu nedenle ekolojik olarak sağlam bir malzemedir. Nihai ürünün kalitesi, hurda ZAMAK malzemesinin yeniden eritilmesi ve yeniden kullanılmasından zarar görmez. Ayrıca, ürünü geri dönüştürülebilir hale getirerek atıkları azaltır ve hammadde maliyetlerini düşürür. Sürdürülebilirliğin önem kazandığı günümüzde ZAMAK alaşımları birçok endüstride yeniden kullanılabilir ve ZAMAK alaşımlarının kullanılması çevre dostu üretim sürecinin iyileştirilmesine yardımcı olur.
Gerekçe #8: Uygun Maliyetli
Öte yandan, ZAMAK kalıp döküm alaşımları alüminyum alaşımlarından biraz daha pahalıdır, ancak maliyeti diğer metallerden daha düşük olduğu için ekonomiktir. ZAMAK alaşımları, pirinç ve bakır gibi yüksek performanslı alaşımlara kıyasla daha ucuzdur (ve bu nedenle ekonomiktir). ZAMAK alaşımları mükemmel döküm özellikleri gösterir ve son derece dayanıklıdır, ancak yine de ekonomiktir, tüm bunlar performans ve bütçe arasında doğru dengeyi kurmak için üreticilere hitap eder.
6. Doğru Zamak Basınçlı Döküm Üreticisi Nasıl Seçilir?
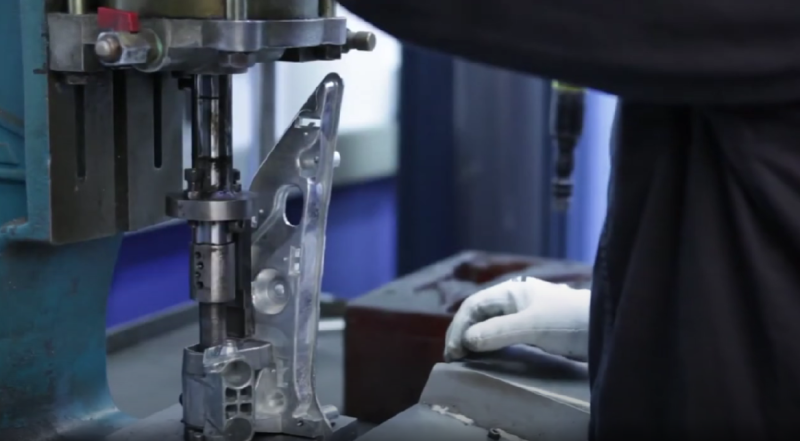
Projeniz için en iyi sonuçları elde etmek amacıyla bir Zamak basınçlı döküm üreticisi veya tedarikçisini değerlendirirken göz önünde bulundurmanız gereken birkaç husus vardır:
- Üretici, Zamak basınçlı döküm konusunda deneyim sahibi olmalı ve bu alaşım ve döküm prosedürü konusunda iyi bir deneyime sahip olmalıdır. Böylece, yüksek kaliteli parçanızı belirttiğiniz şekilde üretebilirler.
- Yetenekler ve Ekipman - Büyük üretim çalışmalarını hassasiyet ve kaliteyle yürütmek için gelişmiş ekipmana sahip, büyük üretim çalışmalarını idare edebilen bir üretici arayın.
- Güvenilir bir üretici ISO 9001 gibi sertifikalara sahip olmalıdır, bu da her parçada tutarlılık sağlamak ve yüksek standartları karşılamak için sıkı kalite kontrol prosedürlerini takip ettiklerini gösterir.
- Her proje benzersiz olmalıdır ve iyi bir Zamak basınçlı döküm üreticisi, özel yüzeyler, özel kaplamalar veya Die Cast Zamak 3 gibi özel alaşımlar gibi gereksinimlerinize göre özelleştirme seçenekleri sunmalıdır.
- Üretici ile güçlü bir ilişki anahtardır - Müşteri Desteği. Tasarım, üretim ve teslimat sonrası süreç boyunca iyi müşteri destek hizmeti sağlayan tedarikçileri kontrol edin.
7. Döküm Zamak 3 neden spot lambalar için bu kadar popüler bir seçimdir?
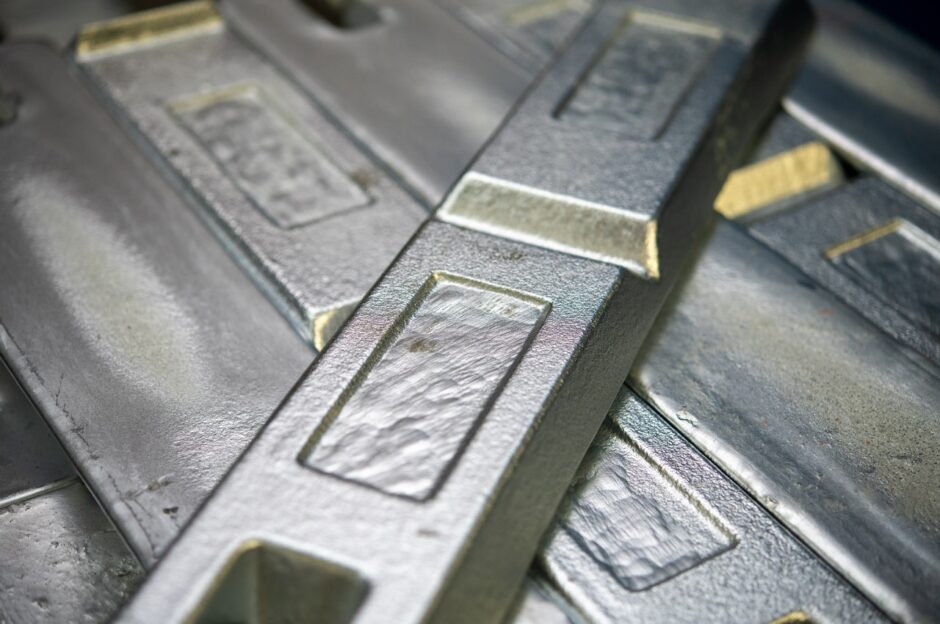
Basınçlı döküm endüstrisinde en çok kullanılan Zamak alaşımlarından biri Die Cast Zamak 3'tür. Zamak 3, iyi mukavemet, dayanıklılık ve döküm kolaylığı ile iyi mekanik özellikleriyle bilinir. Yüksek çinko içeriği nedeniyle, korozyona karşı iyi bir direnç kapasitesine sahiptir, bu da onu dış ortamlara maruz kalan parçalar ve otomotiv endüstrisi için uygun hale getirir. Ayrıca, Zamak 3 hem büyük hem de küçük ölçekli projelerin gerçekleştirilmesini kolaylaştırmak için karmaşık şekillere kolayca dökülebilir.
Bu avantajların bir sonucu olarak Zamak 3 Basınçlı Döküm, mukavemet, ağırlık ve korozyon direncinin hayati önem taşıdığı birçok uygulama için çözüm olmaya devam etmektedir.
Biz CNM TECH - önde gelen ZAMAK basınçlı döküm üreticilerinden biriyiz.
CNM TECH olarak, yüksek kaliteli ZAMAK basınçlı döküm sağlama konusunda uzmanız. Yıllardır sektörde bir profesyonel olarak, çeşitli endüstrilerde dayanıklı, hassas ve nispeten ucuz ZAMAK basınçlı döküm parçaları üretmekten gurur duyuyoruz. Kaliteli ve güvenilir parçalar ortaya çıkardığımızdan emin olmak için son teknoloji üretim süreçlerini kullanıyoruz.
Bu nedenle, hangi malzemeleri kullanmanız gerektiğini biliyoruz. Bu nedenle mükemmel akışkanlığa, yüksek mukavemet ve ağırlık oranlarına, düşük erime noktasına ve geri dönüştürülebilirliğe sahip ZAMAK alaşımlarına odaklanıyoruz. ZAMAK döküm bileşenlerimiz otomotiv, elektronik veya donanım uygulamaları için uygundur ve en zorlu koşullarda çalışacaktır.
thediecasting.com olarak müşterilerimizin ihtiyaçlarını tam olarak anlamak ve onlara ihtiyaçları için özel olarak tasarlanmış çözümler sunmak için onlarla birlikte çalışıyoruz. İnovasyon konusundaki uzmanlığımızın ve yetenekli mühendislerden oluşan bir ekibe sahip olmamızın bir kanıtı olarak, mükemmel yüzey kaplamalarına sahip hassas mühendislik ürünleri sunmayı vaat ediyoruz.
En yüksek kaliteye ihtiyacınız varsa ZAMAK basınçlı dökümCNM TECH, tasarımınızı gerçeğe dönüştürmek için doğru ortaktır. Bir sonraki projenize nasıl yardımcı olabileceğimiz hakkında daha fazla bilgi edinmek istiyorsanız, thediecasting.com adresini ziyaret edin!
8. Sonuç
Son olarak, zamak basınçlı dökümün maliyet, verimlilik ve çok yönlülük açısından eşsiz avantajlara sahip olduğu sonucuna varılmıştır. Otomotiv, elektronik veya tüketim malları endüstrileri için parçalara ihtiyacınız olup olmadığına bakılmaksızın, Zamak basınçlı döküm size yüksek kaliteli dayanıklı parçalar sağlayabilecek bir süreçtir. Zamak 3 Basınçlı Döküm benzersiz avantajlar sunar ve uygun bir Zamak basınçlı döküm üreticisinin kullanılmasıyla birleştiğinde, üretim maliyetlerinizi düşük tutarken işinizin tüm gereklilikleri yerine getirmesini sağlayabilir. Bu gücü, Zamak basınçlı dökümün hassasiyetini ve verimliliğini kullanan şirketler, modern endüstrilerin değişen ihtiyaçlarını karşılamaya devam etmek için hala yüksek performanslı parçalar yaratabilmektedir.
SSS
1. Zamak basınçlı döküm nedir?
Erimiş Zamak alaşımını bir kalıba enjekte ederek hassas, dayanıklı parçalar oluşturma süreci olarak da bilinir. Uygun maliyetli, güçlü olması ve çok az son işlem gerektirerek karmaşık şekiller üretmek için kullanılabilmesi nedeniyle popülerdir.
2. Zamak 3 ile diğer Zamak alaşımları arasındaki fark nedir?
Zamak 3, mukavemet dengesi ve döküm kolaylığı nedeniyle en yaygın Zamak alaşımıdır. Zamak 5 gibi diğer alaşımlar ihtiyaca bağlı olarak daha yüksek mukavemet veya sertlik sağlar, ancak Zamak 3 son derece çok yönlüdür.
3. Zamak basınçlı döküm hangi alanlarda kullanılır?
Otomotiv, elektronik, tüketim malları ve endüstriyel ekipman endüstrileri arasında, Zamak basınçlı döküm ile ürettiği dayanıklı ve hassas bileşenler çok popülerdir.
4. Bir Zamak basınçlı döküm üreticisini seçme süreci nedir?
Deneyim, ekipman kapasitesi, kalite sertifikası, özelleştirme ve sağlam müşteri hizmetleri ile bir Zamak Basınçlı Döküm üreticisi seçin.