İmalat ve döküm endüstrilerinde yaygın olarak kullanılan bu alaşımlardan biri, bazı benzersiz özelliklere sahip olan çinko bazlı Zamak 5 alaşımıdır. Bunun nedeni, Zamak 5'in sunduğu yüksek mukavemet, mükemmel dayanıklılık ve mükemmel korozyon direncidir, bu da onu basınçlı döküm işlemlerinde kullanım için ideal bir malzeme haline getirir. Ekstraksiyondan sonra Zamak 5 son derece düşük erime ve mükemmel döküm özelliklerine sahiptir, bu da Zamak 5'i otomotiv üretimi, tüketici ürünleri ve donanım endüstrileri için ideal bir malzeme haline getirmektedir. Sektör katılımcıları, üretim kararları almak ve operasyonel etkinlik sürecini optimize etmek için bileşim ve çeşitli beton kullanımları gibi Zamak 5 alaşım özellikleri hakkında kesin bilgiye sahip olacaklar.
Makalede, Zamak 5 alaşımı, kimyasal yapısı ve imalat yöntemlerinin yanı sıra sıcaklık kontrolü ve basınç bakımı ve endüstriyel performans üzerindeki mekanik madde özellikleri.
Zamak 5 Alaşımına Genel Bakış
Zamak 5, endüstrinin çinko-alüminyum alaşımı olarak adlandırdığı önde gelen çinko bazlı bir alaşım olarak işlev görmektedir. Zamak 5 kimyasal olarak yüzde 3,5 ila 4,3 alüminyum, yüzde 0,03 ila 0,08 magnezyum ve yüzde 0,75 ila 1,25 bakırdan oluşur. Ayrıca, üreticinin otomotiv, havacılık ve tüketim malları endüstrilerinde kullanılmak üzere yüksek mukavemetli bileşenler oluşturmak için kullanabileceği unsurlar nedeniyle üstün mukavemetini elde eder. Çekme mukavemetinin yanı sıra 6,7 g/cm³ yoğunluk ve 380-385°C'lik nispeten geniş bir erime noktası aralığı, iyi dayanıklılığı ve iyi hassasiyeti nedeniyle bu alaşımda mevcuttur.
Zamak'ın Bileşimi ve Özellikleri 5

Zamak'ın Kimyasal Bileşimi 5
Zamak 5'in mekanik özellikleri, kontrollü oranlarda çinko, alüminyum, bakır ve magnezyum içeren çinko bazlı bir alaşımla karıştırılarak geliştirilmiştir.
Bu kolay erime özelliği, ÇİNKO alaşımının 96-98%'si ile karşılaştırıldığında Zamak 5'i mükemmel bir basınçlı döküm alaşımı yapan niteliklerden biridir. Üstün sonuçlar elde etmek için, alaşımın mukavemetini ve yapısal bütünlüğünü bozacak kirleticilerden kaçınmak amacıyla 99.99% saflıkta çinko malzeme kullanmak çok önemlidir.
Zamak 5 malzemesinin katılaşması, alaşımın mikro yapısını iyileştirdiği için Alüminyum (3.5 ila 4.3%) ilavesiyle geliştirilmiştir. Bölgeler, malzeme yapısında süneklik ve sertlik özelliklerini birleştiren e bileşimine sahiptir. Zamak, çatlama gibi malzeme kusurlarının yanı sıra kırılganlık sorunlarını önlemek için tam alüminyum içeriği için ölçülmelidir.
Zamak 5'te 0.03% ile 0.08% arasında magnezyum bulunması, bu element ile tane sınırlarındaki mikro çatlakların korozyonunun safsızlıklar tarafından engellenmesinden kaynaklanmaktadır. Bu ilave alaşımı daha akışkan hale getirdiğinden, kalıp daha iyi dolgu özellikleri elde ederek fayda sağlar. Magnezyumun dışarıda bırakılması, Zamak 5 yüzeyini kusurlu hale getirecek ve işlenmesi çok zor olacaktır.
Zamak 5 grafit dökümdür ve yüzde 0,75 ila 1,25 oranında bakır eklendiğinde iyi aşınma direncine ve ısıl işlem kapasitesine sahiptir, bu da termal değişim uygulamaları için uygun olan gelişmiş sürünme direncine sahiptir. Doğru sınırlar aşıldığında Zamak 5 kırılgan hale geldiğinden, bakır oranı önemlidir.
Zamak 5'in Fiziksel Özellikleri

Zamak 5 malzemesinin ağırlığı 6,7 g/cm³'tür ve yoğunluğu çelik ile alüminyum alaşımları arasındadır. Uygun ağırlık-mukavemet ilişkisi, Zamak 5'i düşük ağırlığa sahip güçlü malzemeler içeren birçok yapı için uygun hale getirir.
Zamak 5 380 ila 385 santigrat derece arasında erir, bu da zamak 5'in tam dökümünü alüminyuma kıyasla uygun maliyetli hale getirir.
Ortalama 120 °C sıcaklıkta Zamak 5'in çekme dayanımı 330 MPa, akma dayanımı 220 MPa ve uzama potansiyeli 7-10% olup endüstriyel kullanım gereksinimlerini karşılamaktadır. Zamak 5, 220 MPa'da yüksek akma dayanımına ve 7-10%'nin neredeyse bozulmadan önceki maksimum uzamasına sahip olduğu için güçlü ve uyarlanabilirdir.
Zamak'ın Mekanik Özellikleri 5
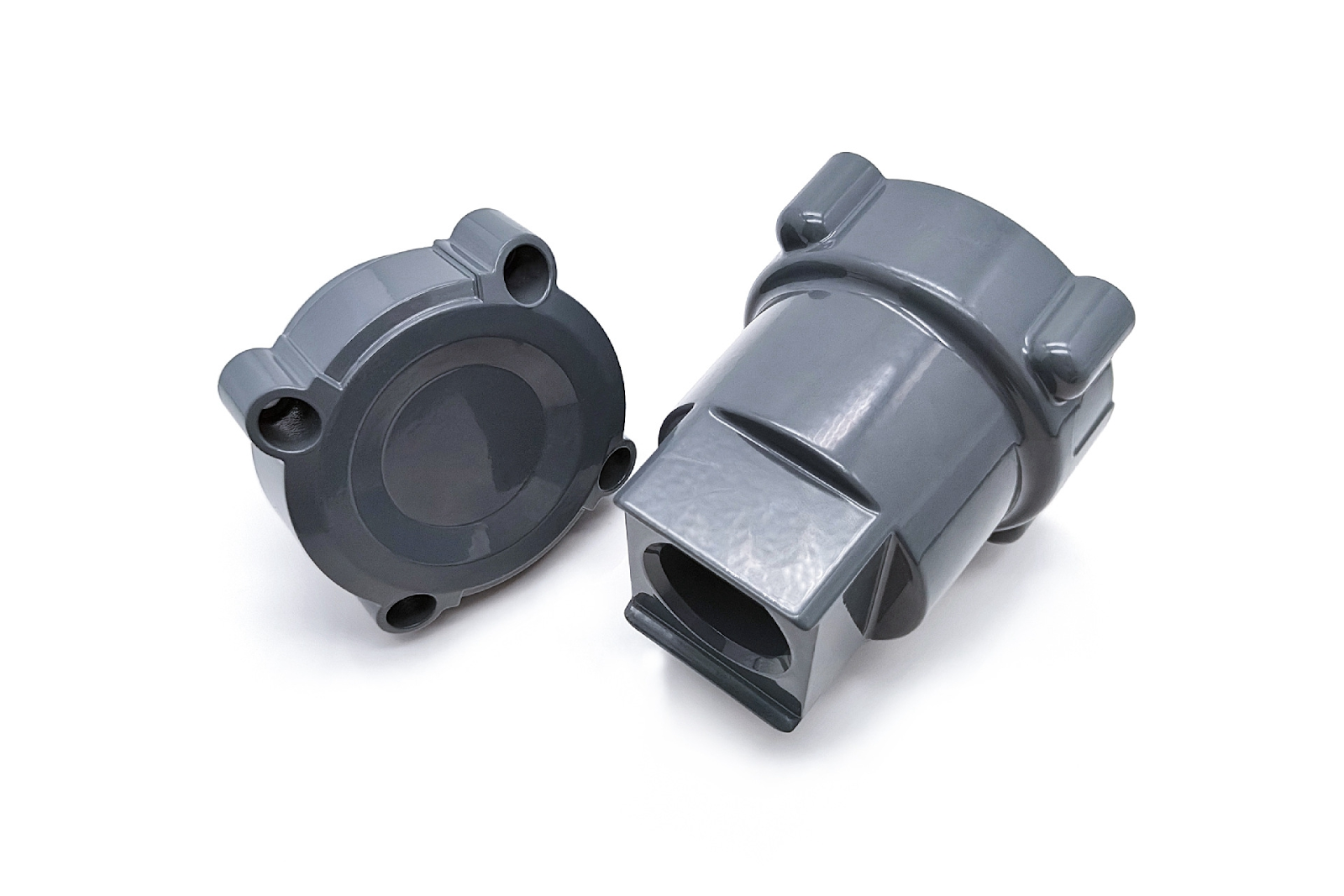
Zamak 5'in 91 HB Brinell sertlik seviyesi, mukavemet ve yüzey sertliği arasında mükemmel bir denge kurarak dekoratif tutamaklar veya aşınmaya karşı koruma gerektiren diğer parçalar için mükemmel bir kombinasyon oluşturur.
Darbe Dayanımı:
Malzemenin oda sıcaklığı Charpy darbe dayanımı ölçüsü 53 J iken, -20°C'de 35 J'ye düşmektedir. Alaşım, dinamik kuvvet koşullarında mekanik gerilimlere ve titreşimlere karşı kendini koruyabilmesi için yüksek darbe direncine sahiptir.
Zamak 5, 100 MPa'lık döngüsel gerilime dayanabilir ve 1 milyon döngüye kadar arıza olmadan hayatta kalabilir. Zamak 5, sürekli yükleme altında güvenilir bir stabilite ile pratikte performans gösterir, bu nedenle makine bileşenleri ve çamaşır makinesi parçası için uygundur.
Zamak 5 Alaşımının Mekanik Özellikleri
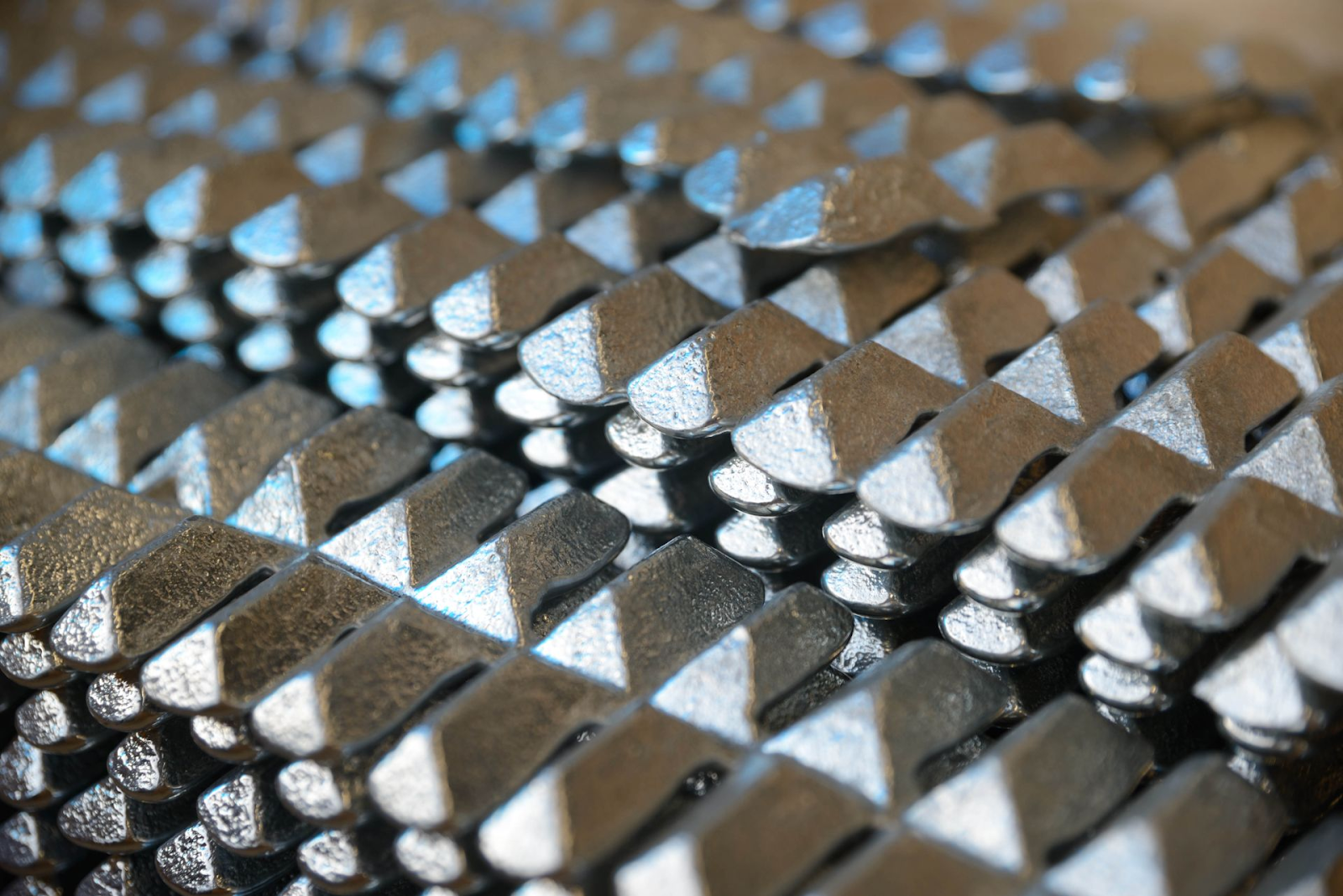
Aşağıdaki tablo Zamak 5 alüminyum alaşımının temel mekanik özelliklerini göstermektedir.
Mülkiyet | Değer |
Brinell Sertlik | 91 HB |
Nihai Çekme Dayanımı | 328 MPa |
Akma Dayanımı (0,2%) | 269 MPa |
Kesme Dayanımı | 262 MPa |
Basınç Dayanımı | 600 MPa |
Yorulma Dayanımı | 56,5 MPa |
Darbe Dayanımı | 65 J |
Elastisite Modülü | 96 GPa |
Uzama | 50 mm'de 7% |
Zamak alaşımının mukavemet değerleri, strese nasıl dayanabileceğini gösterir ve onu zorlu uygulamalarda kullanılabileceği diğer malzemeler arasına yerleştirir. Zamak 5, yorulma yüklerine ve darbelere karşı üstün direnç sağlar, bu nedenle tekrarlanan kuvvet yüklerine maruz kalan parçalar için uygundur.
Zamak 5 Alaşımının Fiziksel Özellikleri
Tüm özellikleri sayesinde Zamak 5'in davranışı fiziksel özellikler tarafından kontrol edilir.
Mülkiyet | Değer |
Erime Aralığı | 380-386°C |
Yoğunluk | 6,60 g/cm³ |
Elektriksel İletkenlik | 26% IACS |
Termal İletkenlik | 109 W/mK |
Özgül Isı Kapasitesi | 419 J/kg-°C |
Termal Genleşme Katsayısı | 27,4 µm/m°K |
Poisson Oranı | 0.30 |
Zamak 5'teki özelliklerin kombinasyonu, farklı ortamlarda ve hem termal hem de elektrik iletkenliği için uygun uygulama koşullarında iyi performans göstermesini sağlar. Uygun yoğunluk özellikleri ve termal kabiliyeti, Zamak 5'i sıcaklığa duyarlı sistemler için bir zorunluluk haline getirir ve aynı zamanda elektrikli bir parçanın kullanım biçiminde çeşitlilik sağlayan iyi elektriksel özelliklere sahiptir.
Zamak 5 Alaşımının Avantajları
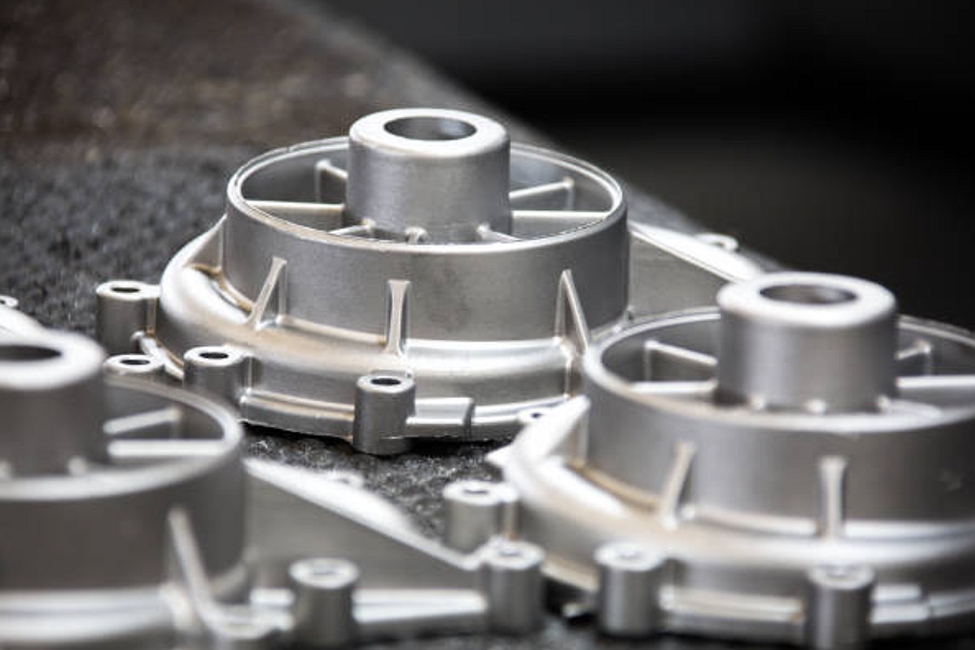
Buna karşılık, Zamak 5'in daha düşük ağırlıkla aynı anda sergilediği üstün mukavemet özellikleri, mukavemet/ağırlık oranının A380 alüminyumunu aşan 49 MPa değerinde olmasından kaynaklanmaktadır. Zamak 5, yüksek ağırlık verimliliği ile yüksek mukavemet seviyesinin baskın karakteristiği nedeniyle, otomobil ve havacılık sektörleriyle ilgili çeşitli endüstriyel uygulamalarda başarıyla kullanılabilir.
İyi Korozyon Direnci: Zamak 5'i diğer tuzlu ve nemli koşullar altında korozyona karşı üstün kılan alaşımı, deniz donanımı ve açıkta kalan uygulamalar için mükemmel avantajlar sunar. Zamak 5 laboratuvarda test edilmiş ve malzeme üzerinde 500 saatten fazla tuz spreyine maruz kalmanın yüzeye zarar vermediği görülmüştür.
Mükemmel Dökülebilirlik: Zamak 5 özellikle basınçlı döküm için uygundur, çünkü metal karmaşık döküm şekillerine kolayca akacak kadar akışkandır. Zamak 5'in dökülebilirliği, üreticiler tarafından hızlı ve kolay kolay üretim sonrası, minimum gerektiren ve özellikle geometrik boyutlardaki varyasyonların bir işlevi etkilemeyeceği durumlarda kullanılır.
Yüksek Süneklik: Zamak 5, 7% ile 10% arasında değişen sünekliği nedeniyle başarılı olan prosesler kullanılarak soğuk şekillendirilebilir. Zamak 5 bükme, boğaz açma ve delme işlemlerine izin verir, bu da Zamak 5'in üretim çok yönlülüğünü artırarak daha iyi hale getirilmesini sağlar.
Zamak Üretim Süreci 5
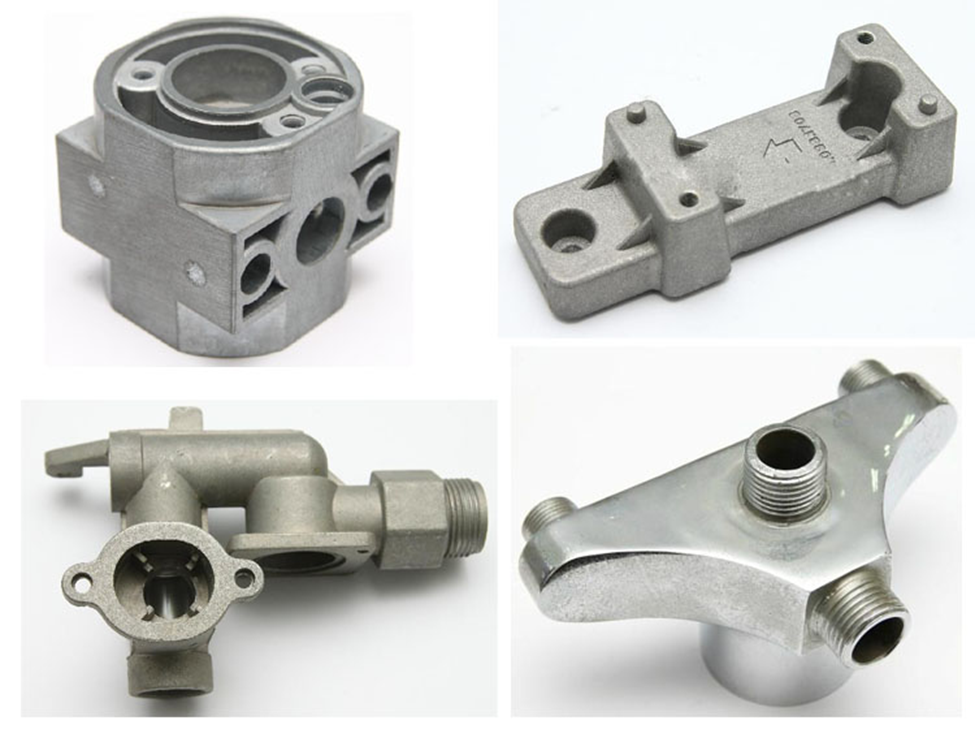
Basınçlı Döküm Süreci
Zamak 5 malzemesi düşük erime noktasına sahiptir, bu da malzemenin makro enjeksiyon kalıbında üretilemeyeceği, ancak sıcak kamara kalıbından üretilebileceği anlamına gelir. Erimiş metal, yakın toleranslı ve ince yüzeyli parçalar yapmak için yüksek basınç altında çelik kalıba alınır. Bununla birlikte, yöntem özellikle yüksek miktarlarda ürün üretileceği zaman olağanüstü verimlilik oranlarına ulaşmaktadır.
Süreç Parametreleri
Aslında, üç önemli süreç parametresi şunlardır: 150 ila 200 °C kalıp sıcaklığı ve 50 °C / s soğutma hızları ile birlikte 700 ila 1000 bar arasında değişen enjeksiyon basıncı. Mekanik kalite, mükemmel, ürün kusurlarını en düşük seviyede elde etmeden önce çok hassas bir şekilde kontrol edilmelidir.
Talaşlı İmalat ve Son İşlem
Zamak 5, özellikleri sayesinde döküm aşamasından sonra bitirme işlemleri için hazırdır. Ürünün yüksek sünekliği, hassas diş açma ve hassas kanal açma protokollerinin yanı sıra korozyon korumasını ve estetik özellikleri geliştirmek için hassas elektrokaplama prosedürlerine ve toz kaplama yöntemlerine izin verir.
Zamak 5 ve Zamak 3 arasındaki farklar
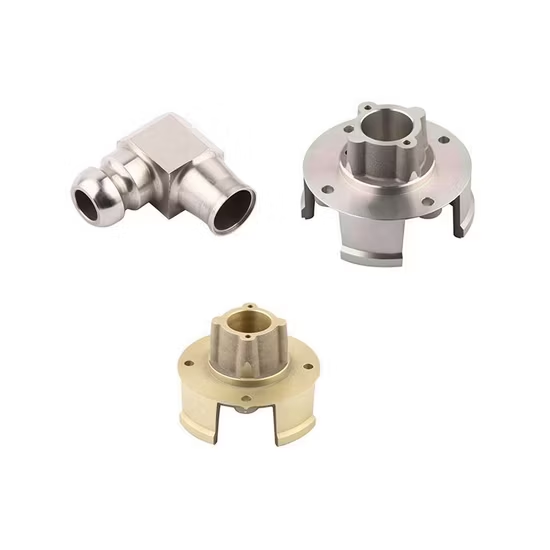
Kimyasal Bileşim: Zamak 5, bakır elementi içermesi nedeniyle ısı toleransına sahip olduğu için Zamak 3 değildir ve en iyi döküm ve neme dayanıklı koruma yeteneklerini sağladığı için Zamak 3 bakır içermez.
Mekanik Özellikler: Zamak 5 daha yüksek mukavemet ve sertliğe sahiptir, bu nedenle daha iyi mekanik özelliklere sahiptir ve yük gereksinimleri olan parçalarda Zamak 3'e göre daha kullanışlıdır.
Zamak 5 ve Zamak 3 Karşılaştırması
Mülkiyet | Zamak 5 | Zamak 3 |
Kimyasal Bileşim | Çinko (96-98%), Alüminyum (3,5-4,3%), Magnezyum (0,03-0,08%), Bakır (0,75-1,25%) | Çinko (95-97%), Alüminyum (3,5-4,3%), Magnezyum (0,02-0,06%), Bakır (<0,1%) |
Çekme Dayanımı | 330 MPa | 240 MPa |
Akma Dayanımı | 220 MPa | 160 MPa |
Uzama | 7-10% | 10-15% |
Sertlik | 91 HB (Brinell) | 80 HB (Brinell) |
Yoğunluk | 6,7 g/cm³ | 6,6 g/cm³ |
Erime Noktası | 380-385°C | 380-385°C |
Uygulamalar | Otomotiv, havacılık, tüketim malları, yüksek mukavemetli uygulamalar | Oyuncaklar, süs eşyaları, düşük stresli uygulamalar |
Anahtar Avantaj | Yüksek sıcaklık direnci, aşınma direnci, gelişmiş güç ve dayanıklılık | Mükemmel dökülebilirlik, nemli ortamlarda korozyon direnci |
Dezavantaj | Daha az sünektir, yüksek sıcaklıklarda kırılganlığa daha yatkındır | Düşük sıcaklık ve stres direnci |
Zamak 5 ve Zamak 3 paralel kimyasal yapılara, mekanik özelliklere ve ortak kullanım durumlarına sahiptir ve bu tablo bunu tek bir yerde göstermektedir.
Zamak 5 (ASTM AC41A, Z35531, Mazak 5) Çinko Alaşım
Zamak 5, mükemmel mukavemet özellikleri ve çok yönlülüğü nedeniyle çok sayıda uygulama gösteren bir çinko-alüminyum alaşımıdır. Sektörde yaygın olarak Zamak 5 olarak bilinen bu alaşım, ASTM standartlarına göre AC41A ve UNS sınıflandırma sistemine göre Z35531 olarak adlandırılmaktadır. Zamak 5, mukavemet, korozyon direnci ve sertlik gibi mekanik özelliklerini artırmak için alüminyum ve bakır ile alaşımlandırılmış birincil çinko esas alınarak oluşturulmuştur. Belirtildiği gibi, imalat özellikleri Zamak 5'in herhangi bir temperleme işlemi veya diğer işlemlerden önceki durumu için geçerlidir. Hem karmaşık, ayrıntılı parçalar hem de yüksek kaliteli parçalar üretebildiğinden, Zamak 5 alaşımı basınçlı döküm için kullanılır. Hem ekonomik hem de güvenilir çalışma kabiliyeti sağladığından, Zamak 5 otomotiv ve elektronik ürünlerin yanı sıra dekoratif eşyalarda da yerini almıştır.
Zamak'ın Erime Noktası 5
Zamak 5 alaşımının ergime değerleri 380°C ile 386°C (716°F ile 727°F) arasında olup, diğer metalik malzemelere göre daha düşüktür. Ortalama erime sıcaklığından daha düşük bir sıcaklığa sahip olan Zamak,5'in kullanımı, düşük proses sıcaklıklarında kalıplanabilirlik kolaylığı nedeniyle basınçlı döküm operasyonlarında önemli bir role sahiptir. Alaşımın düşük erime aralığı, karmaşık bileşenlerin yapımında hızlı erime ve katılaşma gereksinimi nedeniyle hassas üretimde daha kolay çalışmaya yardımcı olur. Zamak 5 düşük erime noktasına sahiptir, bu da finisaj üreticisinin çok sayıda otomotiv üretiminin yanı sıra mobilya ve tüketim malları üretiminde tercih etmesini kolaylaştırır.
Zamak Young's Modülü 5
Zamak 5 alaşımı belirli teknik özelliklere sahiptir. Young Modülü ~96 Giga paskaldır (GPa). Bu değer, malzemenin uygulanan stres altında deformasyona ne kadar direnç gösterdiğini yansıttığı için malzeme sertliğini verir. Zamak 5'in ortalama sertliği, hem mukavemet hem de esneklik gereksinimlerini karşılamaya yetecek kadar yakın olan 96 GPa'lık Young's Modülünden kaynaklanmaktadır. Malzeme tasarlandığı mukavemete sahiptir ve 96 GPa'lık (Giga paskal) orta ölçekteki sertliği alaşımın mekanik uygulamalar sırasında yapısal bütünlüğünü korumasına izin verdiği için hala esnektir.
Zamak 5'e Eşdeğer Malzemeler
Farklı uygulamalar farklı maddeler gerektirir, spesifik çinko alaşımı Zamak 5 belirli özelliklere sahiptir, ancak ek maddelerle birlikte herhangi bir sayıda eşdeğer malzeme mevcuttur. Zamak 5 yerine kullanılabilecek üç temel alternatif malzeme Zamak 3 (ZnAl4Cu1), Zamak 2 ve Zamak 13'tür.
Zamak 3 (ZnAl4Cu1)
Zamak ailesi alaşımları arasında, Zamak 3 Zamak 5 ile benzer özellikleri nedeniyle en popüler türler arasında yer almaktadır. Bu alaşımların kristal yapılarını elde ettikleri çinko, alüminyum ve bakır maddelerdir. Zamak 3, daha zayıf mukavemet ve korozyon direncinden sorumlu olan daha az bakır içerdiği için Zamak 5'in yerine kullanılmaktadır.
Çinko Basınçlı Dökümler
Ayrıca, Zamak 2 ve Zamak 7 iyi bir döküm kabiliyetine sahiptir, bu da onları hem çinko basınçlı döküm alaşımları ile yüksek hassasiyet ve yüksek finiş kalitesi gerektiren üretimde kullanıma uygun hale getirir. Bu alaşımlar farklı mekanik özelliklere sahip olsa da, bu alaşımlar için aynı üretim süreçleri kullanılır.
ALSi12
Daha yüksek sıcaklıklarda biraz daha yüksek mukavemet gerektiğinde, kullanıcılar ALSi12 alüminyum silikon alaşımını tedarik için bazı alternatif malzemelerle değiştirebilirler. Her ikisi de döküm ve kalıp döküm üretiminde kullanıldığından, Zamak 5 ve ALSi12 arasında aynı kimyasal yapının eşleşmesi gerekmez.
ADC 12 (Alüminyum Alaşım)
İyi korozyon direnci ve dökülebilirlik gerektiğinde, ADC 12 alüminyum alaşımı bazı imalat uygulamalarının yerini almak için eşdeğer bir malzeme olarak kullanılabilir. Zamak 5 biraz daha sert olabileceğinden, performans kriterleri seçim için temel oluşturacaktır.
Çekme mukavemeti ve korozyon direncinin yanı sıra sertlikten elde edilen bireysel mekanik özellik dengesine göre, böyle bir eşdeğer üretim ekipleri tarafından seçilir.
Zamak 5 Döküm Süreci
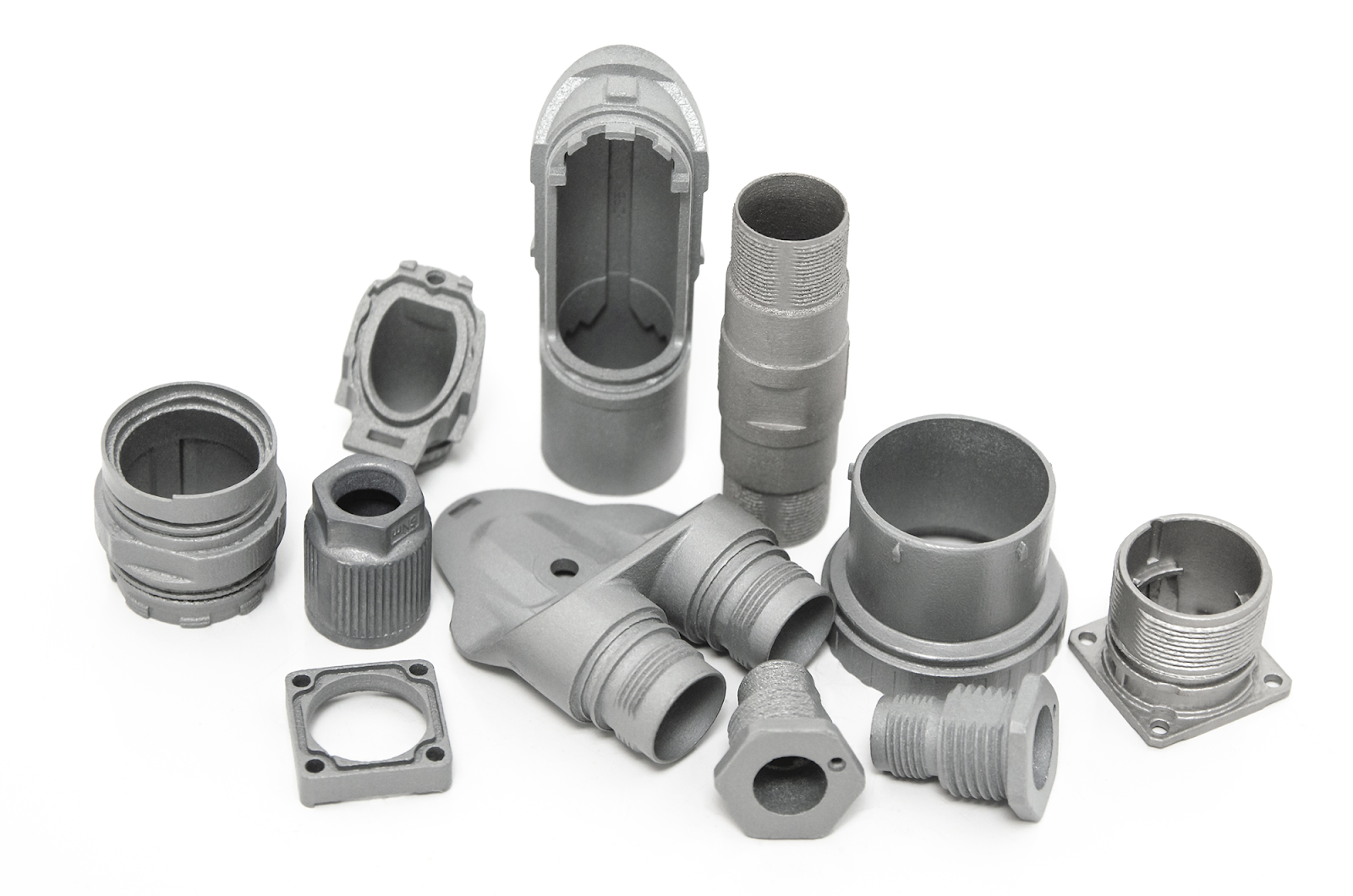
Zamak 5 dökümü, Zamak 5 döküm prosedürünün farklı aşamaları ile son üründe korunabilir ve optimize edilebilir. Başlıca Zamak 5 üretim yöntemi, Zamak 5 erimiş metalin yüksek basınç altında metal kalıplara enjekte edildiği basınçlı dökümdür. Zamak 5 döküm işlemi birbirini takip eden birkaç işlemden oluşur.
Kalıbın Hazırlanması:
Kalıbın belirli bir sıcaklığın üzerinde ısıtılması gerekir, böylece enjeksiyon işlemi sırasında numuneye termal şok verilmesi önlenir. Ardından, döküm yüzeyinin ve çıktı üretiminin her zaman hatasız olduğundan emin olmak için akımın dışarıda kullanılmasına izin veriyoruz.
Zamak 5 Alaşımının Eritilmesi:
Zamak 5 tamamen sıvı hale gelmeden önce 380-390°C (716-734°F) arasında bir ısıya ulaşmalıdır. Alaşım fırında belirtilen bu sıcaklığa kadar ısıtılır ve alaşımın durumu enjeksiyona duyarlı sıvı hale gelir.
Erimiş Alaşımın Enjeksiyonu:
Zamak 5 alaşımı eritildikten sonra yüksek basınç altında sıvı formdan uygun şekilde hazırlanmış kalıp boşluğuna doğru hareket eder. Farklı parça karmaşıklıkları ve büyüklükleri için enjeksiyon basınçları, üreticiler tarafından form vermek için uygulanan 30-60 MPa'dır.
Soğutma ve Fırlatma:
Daha sonra, kalıp erimiş alaşım malzemesini aldıkça soğumaya ve katı hale gelmeye başlar. Yeterli soğutma sıcaklığında kalmayı bıraktığında kalıptan dökülür. Kalıbın soğuma süresi ve sıcaklığı, nihai dökümün kalitesini sağlamak (deformasyonu önlemek) için kontrol edilebilir.
Son İşlem Operasyonları:
Zamak 5 parçalarının fırlatılması, parçaların kırpıldığı, çapaklarının alındığı, cilalandığı ve son olarak nihai gereksinimleri karşılamak üzere kaplandığı çeşitli son işlem prosedürlerinden geçirilmesini gerektirir.
Zamak 5 döküm prosesi, hassas tolerans gereksinimleri olan karmaşık nesneler yaratabildiği için yüksek hacimli üretim için verimlidir. Olağanüstü akışkanlığa sahip bir alaşım, karmaşık kalıp boşluğu alanlarının doldurulmasını düzeltir, bu nedenle alaşım, otomotiv ve donanım sektörlerinin yanı sıra tüketici elektroniği cihazlarında ince detay bileşenlerinin üretimi için uygundur.
Zamak 5 Alaşımı için Farklı Standartlar: Küresel Bir Perspektif
Çok yönlü bir çinko alaşımı olan Zamak 5, genel olarak farklı isimlerle bilinmektedir; ancak bu tanımlamalar, belirli bir standardın yanı sıra menşe ülkeden de kaynaklanmaktadır. Zamak 5 ile ilgili farklı spesifikasyonlar, üretim yöntemi ve önceki tanımlama altında bölgelere özgü farklı eğilimlere sahiptir. Bu tanımlamalar Zamak 5 kullanıcıları için çok önemlidir, çünkü çeşitli pazar sektörlerindeki alaşım spesifikasyonlarına ve bölgesel standartlara göre şirket için protokolleri tanımlarlar. Zamak 5 alaşımının dünya çapındaki tüm standartları ve alternatif isimleri önemli bir genel bakışta sunulmaktadır.
Zamak 5 Alaşımı için Global İsimler ve Standartlar
Aşağıdaki tabloda farklı ülke standartları ve Zamak 5 alaşımının adlandırılma şekilleri verilmiştir.
Geleneksel İsim | Zamak 5 |
Kısa Kompozisyon Adı | ZnAl4Cu1 |
ASTM | AC 41A |
Ortak İsim | Alaşım 5 |
Çin | ZX03 |
JIS (Japonya) | Külçe Tip 1 (Külçe) ZDC1 (Alaşım) |
Kısa Avrupa Tanımlaması | ZL0410 (Külçe) ZP0410 (Alaşım) |
Almanya DIN 1743-2 | Z420 |
Fransa NFA 55-010 | Z-A4UI |
BIRLEŞIK KRALLIK BS 1004 | Alaşım B |
UNS (Birleşik Numaralandırma Sistemi) | Z35530 (Külçe) Z35531 (Alaşım) |
Bu Standartlar Neden Önemli?
Farklı Zamak 5 alaşım standartları, bölgesel olarak etkilenen endüstriyel uygulamaların ve uluslararası iletişim gereksinimlerinin bir kombinasyonunun küresel olarak benimsenmesi nedeniyle kabul edilmiştir. Bu (Zamak 5), Zamak 5 malzemelerini üreten şirketlerin ve mühendislerinin, uygulamaları için uygun malzemeyi seçmek için özellikle bu malzemenin bölgesel standartlarını ve tanımlarını bilmeleri gerektiği anlamına gelir. Standartlar, Zamak 5 alaşımının kimyasal bileşimi, performans standartları, döküm ve işleme operasyonları için uygun malzemeleri seçmek için zorunlu detaylardır.
Zamak 5 Alaşımının Faydaları
Zamak 5, çok yönlü, sağlam bir çinko alaşımı olarak endüstride pek çok uygulamada kullanılmakta ve çeşitli üretim çabalarına pek çok yararlı özellik sağlamaktadır. Zamak 5, tüketici cihazlarında ve endüstriyel ekipmanlarda bol miktarda malzeme uygulaması için uygun hale getiren üstün mukavemet özelliklerinin yanı sıra büyük tokluk ve koruyucu özellikler üzerinde üç kat iyileştirmeye sahiptir. Bunlar, Zamak 5 alaşımının üreticilere sunduğu temel avantajlardır.
1. Güç, Dayanıklılık ve Güvenlik
Zamak 5 çinko alaşımı, mukavemet ve sertlik seviyeleri açısından üstün performans niteliklerini korumaktadır. Alaşım güçlü bir kuvvet direnci kaynağıdır, bu nedenle çok yüksek stres yüzdelerine ihtiyaç duyan zorlu uygulamalar için güçlü bir çözüm olmaya devam etmektedir. Zamak 5, fiziksel olarak çok dayanıklı olması ve aynı zamanda temas olayları için mutlak güvenlik önlemlerini karşılaması nedeniyle endüstriler için önemlidir.
Zamak 5, yangınla ilgili sorunlardan kaçınarak magnezyum gibi bazı metallere göre güvenlik avantajı sağlar. Zamak 5'i diğer yaygın malzemelerden ayıran nadir bir özelliği vardır, çünkü asla nem almaz, böylece plastik benzeri su emme sorunları yaşanmaz. İnsan teması için güvenli olma özelliği nedeniyle Zamak 5 kozmetik ambalaj üretiminde kullanılmaktadır.
Üreticilerin yanı sıra son kullanıcıları da güvence altına alan güvenilirlikle ilgili özelliklerinin bir sonucu olarak, Zamak 5 yeni teknolojik uygulamalar tarafından tercih edilmektedir.
2. Basınçlı Dökümde Üstün Kalite
Zamak 5, bu alaşımın hatasız yüksek kaliteli parçalar üretme kabiliyeti sayesinde basınçlı döküm uygulamaları için kullanılır. Zamak 5 alaşımı, minimum kusurlu pürüzsüz, bitmiş ürünler yaratma kabiliyeti nedeniyle, yüksek kaliteli basınçlı dökümler üretir ve bu da minimum üretim sonrası işleme ihtiyaç duyulmasına neden olur.
Zamak 5 doğal zam özelliklerine sahiptir, bu da üretim sürecinde yüksek mükemmellik seviyelerine sahip olduğu tespit edilen ürünleri üretmek için tam kalıplama tekniklerinin kullanılmasını sağlar. Zamak 5 resmi bitirme aşamalarının olmaması özelliğine sahip olduğundan, imalat süreci zamandan ve imalat işlemlerinin maliyetinden tasarruf sağlayabilir. Zamak 5 parçaları hoş bir görünüme sahiptir çünkü tasarımcılar bunları kendi zevklerine göre boyayabilir veya kromlayabilir.
Zamak 5'in basit bitirme kabiliyeti, onu ev dekorasyon ürünleri, ev mobilyası detaylandırma ve dekoratif aydınlatma bileşenleri gibi ürün uygulamaları için ideal hale getirmiştir. Zamak 5 parçaları, kalıcı etkisi sayesinde kararma etkilerine karşı direnç gösterecektir.
3. Farklı nihai ürünlere dönüştürülür
Zamak 5, üretim çalışmaları için üstün bir yapıya sahiptir. Alaşımın doğası gereği esnek olması, çünkü çinkonun sünek olması, üretim sırasında farklı çalışma operasyonları için kolayca şekillendirilmesine olanak tanır. Zamak 5, döküm, bükme, talaşlı imalat ve perçinleme gibi farklı üretim yöntemleriyle kolayca çalışarak üretimin gerekliliklerini karşılayabilir.
Zamak 5 kolay işleme özelliklerine sahiptir, bu da onu üretim maliyetinin düşürülmesinden ve kolay bir üretim sürecinin sürdürülmesinden yararlanan farklı endüstriler için hayati bir aksesuar haline getirmektedir. Kilitli ürünlerin montajı ve dökülmüş tutamak bileşenleri için tercih edilen bu ürün sayesinde, Zamak 5 parçalarının montaj süreci daha az zahmetli hale gelmektedir.
4. Uygun Maliyetli Üretim
Zamak 5, üreticiler için olağanüstü fiyat uygunluğu sağlayan bir malzemedir. Zamak 5 o kadar ucuzdur ki, diğer alaşımlardan daha ucuzdur ve döküldüğünde çok uygun maliyetlidir. Bununla birlikte, makul maliyet yapısı, üreticileri üstün maliyet verimliliği standartlarına ulaşmaya davet eder ve üstün özellikleri üreticilere kazandırır.
Zamak 5 büyük bir geri dönüşüm potansiyeline sahiptir ve bu da geri dönüşüm kabiliyetini uzun vadeli üretim maliyetlerini azaltmada önemli bir faktör olarak ortaya koymaktadır. Zamak 5 ürünleri yeniden kullanılabilir ve maliyet tasarrufu ve buna bağlı atıkların en aza indirilmesi temelinde geri kazanılacak hurda metal üretimine yol açar.
5. Çevre Dostu Üretim Döngüsü
Zamak 5 üretimi çevre dostu olma özelliğinin büyük bir kısmını karşılamaktadır. Zamak 5, bazı metaller için tehlikeli prosedürlere kıyasla üretim için farklı bir prosedür kullandığından çok fazla çevresel tehdit oluşturmaz. Alaşımın üretiminde hiçbir yan ürün oluşmadığı için zararlı kirlilik görülmez. Çevre mevzuatı konusunda Zamak 5 iyi bir seçimdir ve aynı zamanda bir şirkete kendi yönetmeliklerine uymak için çevre dostu bir yöntem sağlar.
Zamak 5'in Sınırlamaları
Zamak 5 birçok faydalı noktaya sahip olsa da, seçim sürecinde öncelikle sabit sınırlamalarına göre seçilmelidir.
Neme Karşı Zayıf Direnç
Zamak 5'in neme karşı zayıf direnç göstermesi nedeniyle ıslak koşullarla teması yüzeyinde oksidasyon oluşturacaktır. Zamak 5 ürünleri üreticileri aşırı neme karşı koruma önlemleri sağlamalı, sağlamıyorsa bozulmasına karşı ekstra koruyucu kaplamalar sağlanmalıdır.
Yüksek Sıcaklıklara Karşı Sınırlı Direnç
Zamak 5'in termal direnç kabiliyeti orta düzeydedir. Zamak 5, kopma veya bükülme riskini artıracak gerilme mukavemetindeki çok yüksek düşüş nedeniyle sıcaklığa maruz kalmanın 80°C'yi aştığı uygulamalarda kullanılmamalıdır.
Hafif Uygulamalar için İdeal Değil
Zamak 5 kullanılarak elde edilen parça, rakip demir dışı alaşımlardan daha yüksek yoğunluğa sahip olduğu için daha ağırdır. Bu tür uygulamalar için hafif element, gereksinimleri belirlediği için diğer alaşım malzemelerinin de dikkate alınması gerekir.
Diğer Metallerle Korozyon Direnci Sorunları
Bu malzemeyi yapmak için çinko veya kalay kurşunla birleştirildiğinde, ortaya çıkan alaşımın korozyon direncinin azalması nedeniyle Zamak 5'in dayanıklılığı tehlikeye girer. Özellikle kullanımda, Zamak 5 kullanılırken malzeme kombinasyonuna özel dikkat gösterilmesi gerekir.
Düşük Sıcaklıklarda Darbe Özellikleri
Soğuk ortamlarda, sıcaklığın aşırı düşük seviyelere indiği noktalarda Zamak 5'in etki gücü etkilenir, bu nedenle soğuk koşullarda işlevsel değildir.
Zamak 5 Nerede Kullanılır?
Zamak 5, basınçlı döküm endüstrisi de dahil olmak üzere birçok sektör tarafından yaygın olarak kullanılmaktadır. Zamak 5, otomotiv elemanları ve dekoratif eşyaların üretiminde üretim spektrumunun iki ucu arasında üstünlük sağlar. Bazı yaygın kullanım alanları şunlardır:
Banyo Armatürleri: Zamak 5 korozyona karşı kendini koruma özelliğine sahiptir, bu nedenle musluk ve kulp gibi banyo aksesuarlarının üretiminde yaygın olarak kullanılır.
Ateşli Silah Bileşenleri: Alaşım çok dayanıklı ve güçlüdür ve bu nedenle ateşli silah parçalarının üretiminde çok iyi işlev görür.
Oyuncaklar ve Koleksiyon Ürünleri: Bununla birlikte, basit kalıplama süreci ve birinci sınıf yüzey kalitesi nedeniyle Zamak 5, oyuncak ve minyatür eşyaların yanı sıra koleksiyon ürünleri için de popüler bir seçimdir.
Kilit ve Hırdavat İmalatı: Zamak 5, bu alaşım için iyi mukavemet özellikleri ve kolay işlenebilirlik sayesinde imalat endüstrisinde kulplu kilitler, kilit topuzları ve diğer donanım parçalarının üretiminde baskındır.
Elektronik ve Beyaz Eşya: Zamak 5 dayanıklılık özelliklerinin yanı sıra çekici niteliklere de sahiptir ve blender, zımba, tavan vantilatörü gibi ev eşyalarının yanı sıra diğer aletler de Zamak 5'i tercih etmektedir.
Zamak 5 Alaşımının Mekanik Özellikleri
Zamak 5 alaşımı, çeşitli endüstriyel işlemlerde iyi veya kötü çalışmak için yapısal nitelikleri ile belirlenir. Zamak 5 alaşımı, uzama ve sertlik ve korozyon direnci ile birlikte gerilme mukavemetine sahiptir. Döküm işlemi farklı olduğunda ve metal alaşım bileşimi ve soğutma hızı değiştiğinde değerler niceliksel olarak değişir.
Çekme Dayanımı: Zamak 5 alaşımı, diğer çinko bazlı alaşım malzemelerden daha yüksek olan 280-300 MPa gerilme mukavemetini korur.
Akma Dayanımı: Zamak 5 alaşımı, akma dayanımı yaklaşık 230 MPa olduğu için mükemmel gerilme deformasyon direncine sahiptir.
Uzama: Zamak 5 alaşımı, uzama oranında orta süneklik dairesine (3 ile 6% arasında) sahiptir. Özellikleri, çatlamanın eşlik etmediği küçük miktarlarda deformasyona izin verir ve bu nedenle esnek sistemlerde kullanım için uygundur.
Sertlik: Zamak 5 sertlik değeri 90-120 HB'dir (Brinell sertliği), bu da malzemeyi nispeten düşük aşınma direnci gerektiren uygulamalar için uygun hale getirir.
Korozyon Direnci: Ortalama nem içeriği ve standart kimyasal maddeler pahasına bile, Zamak 5 alaşımı korozyona çok iyi direnç gösterecektir. Zamak 5, dış mekan ve otomotiv bileşenleri için bir malzeme olarak iyi çalışır.
Zamak 5 Alaşımının Uygulamaları
Zamak 5, iyi döküm özelliklerini güçlü mekanik özelliklerle birleştirdiği için çok çeşitli endüstriler için tercih edilmektedir. Uygulamaları şunları içerir:
Otomotiv Endüstrisi: Otomotiv motorları ve araç trim muhafazaları, elektronik cihaz muhafazaları için ince fonksiyonel bileşenlerin yapımında temel bir malzeme olan Zamak 5, kilit bir malzemedir.
Donanım ve Ek Parçalar: Zamak 5 gibi bu tür malzemeler, yüksek mukavemet ve dayanıklılığı bir arada tuttuğu ve göze hoş gelen ürünlerle tamamlandığı için otomotiv sektörüne hizmet etmektedir.
Tüketim Malları: Zamak 5 alaşımı, üreticilerin uygun mukavemeti ve korozyon direnci nedeniyle ve oyuncak ve elektrik konektörlerinin yanı sıra ev aletleri üretmek için şekillendirilebilirlik için kullandıkları malzemedir.
Elektronik: Zamak 5 elektriği iyi iletir, karmaşık formlarda iyi kalıplar oluşturur ve elektronik cihaz muhafazaları ve gövdeleri yapmak için kullanılır.
Zamak 5 Alaşımının Avantajları
Zamak 5, üreticiler için tercih edilen alaşım olmasını sağlayabilecek birkaç önemli avantaj sunar.
Maliyet-Etkinlik: Zamak 5'in maliyeti, diğer metal alternatiflerine göre daha basit ve daha ucuz bir oranda iyi dayanıklılık ve kolay döküm sağladığından mükemmel bir seçenektir.
Çok yönlülük: Zamak 5'in karmaşık, hassas parçaların yapımında tercih edilmesinin nedeni, karmaşık şekillerin kolaylıkla üretilebilmesidir.
Bitiş kalitesi: Zamak 5 mükemmel pürüzsüz yüzeyler ürettiğinden, üreticilerin daha iyi bir finisaj kalitesi elde edebilmeleri için yüksek kaliteli finisaj işlerine ihtiyaç vardır.
Yüksek Mukavemet-Ağırlık Oranı: Zamak 5 alaşımı, yüksek mukavemet ve hafiflik bağımsızlığı sunduğundan, bu tür diğer sektörlerin yanı sıra otomotiv endüstrisi için de iyidir.
Zamak 5 Kullanımında Karşılaşılan Zorluklar ve Dikkat Edilmesi Gereken Hususlar
Zamak 5 alaşımının çok sayıda avantajı olmasına rağmen, kullanımı söz konusu olduğunda birkaç kritik nokta vardır.
Sıcaklık Hassasiyeti: Bununla birlikte Zamak 5, 250°C (482°F) altında artan sıcaklık varlığında özellik bozulmasına uğramadığı için termal olarak hassas bir davranışa sahiptir. Zamak 5 parçaları, bu eşiği aşmamak için faydalı bir kullanım ömründe sıcaklığın yeterince düşük olduğu ortamlarla sınırlandırılmalıdır.
İşleme Sınırlamaları: Zamak 5 için döküm süreci basit olmasına rağmen, malzeme aşınma mekanizmalarının yanı sıra safralaşma eğilimi gösterdiğinden, agresif yöntemler içeren makine operasyonlarında sorun yaratır. Başarılı sonuçlara ulaşmak için çok iyi teknisyenlerin uygun araçlara ve doğru tekniklere ihtiyacı vardır.
Çevresel Etki: Zamak 5'in korozyona karşı iyi direncinin değerlendirilmesi, Zamak 5'in üretim ve çevrim süreçlerinde neden olduğu çevresel etkide de dikkate alınmalıdır. Zamak 5, döküm emisyonlarında geri dönüşüm ve atık azaltma yoluyla daha da geliştirilebilir ve endüstri, çinko alaşımının sürdürülebilirliğini artırmak için her ikisini de yapmaktadır.
CNM TECH'de Zamak 5 Basınçlı Döküm Hizmetleri
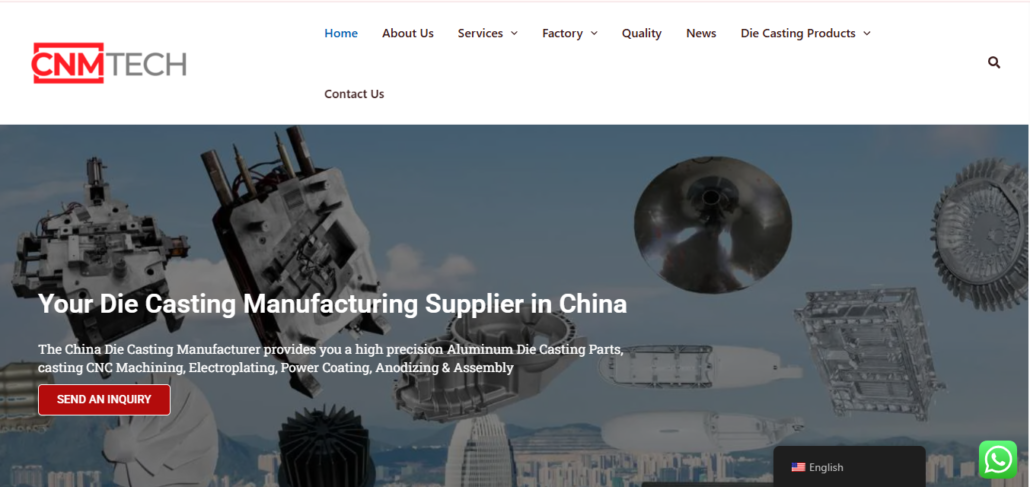
Otomobil, havacılık ve uzaydan tüketici ürünleri üretimine kadar çeşitli endüstri ihtiyaçları için CNM TECH portföyü altında olağanüstü Zamak 5 basınçlı döküm çözümleri sunuyoruz. Mükemmel performans, yetenek ve bakım sağlayan parçalar geliştirmemize olanak tanıyan derin deneyim ve modern basınçlı döküm sistemleri konusunda uzmanlaşmış bir kuruluşuz.
Modern basınçlı döküm yöntemimizi uygulayarak, iyi boyutlara, mükemmel yüzey kalitesine ve ekonomik üretim miktarı için sistematik üretim süresine sahip Zamak 5 ürünleri sağlanacaktır. Basitçe ifade etmek gerekirse, CNM TECH ile müşteriler spesifikasyonlarını basınçlı döküm malzemesine tam olarak dikte edebilir ve sıkı geri dönüş süreleri elde edebilirler.
Prototipleme ve büyük ölçekli üretim yetenekleri sağlayan tüm Zamak 5 tekliflerimize bir göz atın. www.thediecasting.com adresinden, şirketimizin Zamak 5 çözümlerinin ürün kullanım ömrü performansını nasıl artırdığını öğrenebilirsiniz.
Hassas oldukları için CNM TECH'den Zamak 5 basınçlı döküm hizmetlerini seçmelisiniz.
Sonuç
Zamak 5, özellikle otomotiv, hırdavat ve elektronik sektörlerinde hassasiyet gerektiren parçaların üretiminde yaygın olarak kullanılan, düşük üretim maliyeti ve etkinliğe sahip bir alaşım dökümdür. Çinko Alaşım 5'in çinko, alüminyum, bakır magnezyum karışımı, mükemmel mekanik özelliklere, mukavemete ve korozyona karşı savunmaya ve dökülebilirliğe sahip güçlü bir malzeme oluşturur. Zamak 5 dökümünü kullanan üretim teknikleri, sıcaklık ve basınç kontrolleri ile doğru bir şekilde ele alındığında, gerçekleştirildiklerinde çok az kusurlu yüksek kaliteli bileşenler üretir. Bununla birlikte, Zamak 5 düşük erime noktasına ve akışkanlık özelliklerine sahiptir, bu da onu son derece sofistike tasarımlar için uygun hale getirir, bu nedenle yaygın endüstriyel uygulamalar içindir.
SSS
1. CNM TECH'deki basınçlı döküm sürecinin Zamak 5'e yol açan temel özellikleri nelerdir?
A: Yüksek performanslı çinko alaşımı şu özelliklere sahiptir: mükemmel mukavemet ve boyutsal kararlılık ve olağanüstü korozyon koruması. Bunlardan biri de Zamak 5'tir. Zamak 5, son derece ayrıntılı, karmaşık bileşenlerin minimum işleme ile üretilebilmesi sayesinde olağanüstü döküm kabiliyeti sergiler. CNM TECH, otomotiv uygulamalarında, tüketici elektroniği ve donanım endüstrilerinde yardımcı olarak çalışabilen güvenilir, uygun maliyetli bileşenler üretmek için Zamak 5 kullanır.
2. CNM TECH, proje gereksinimlerime göre belirli Zamak 5 parçalarını üretebilir mi?
A: Kesinlikle. Uzman bir şirket olarak CNM TECH, bireysel bir Zamak 5 basınçlı döküm çözümü sunmaktadır. Şirket, düşük hacimli prototiplemenin yanı sıra tam olarak belirtildiği gibi olması gereken yüksek hacimli parçalara ihtiyaç duyan müşterilerle kalıplar yapar. Çalışanlarımızın üretim süreçlerindeki özverili çalışmaları, doğru sonuçlar ve güvenilir performans sunmamızla sonuçlanır.
3. Zamak 5 döküm ürünlerini tamamlamak için olası işlem türleri nelerdir?
A: CNM TECH'de, Zamak 5 parçaları için mevcut olan çoklu yüzey işlemleri arasında toz kaplama ve kromlama ile birlikte elektrokaplama, boyama ve cilalama bulunmaktadır. Son işlem teknikleri kullanılarak, işlevsel veya dekoratif olabilen parçaların görünümü, aşınma direnci ve korozyon koruması iyileştirilebilir.