Yüksek basınçlı döküm (HPDC), mevcut üretimde en sık kullanılan metal döküm proseslerinden biridir. Üreticiler HPDC'yi, hem yüksek hassasiyet ve hızlı üretim oranları hem de üstün boyutsal doğruluk ve pürüzsüz yüzeyler elde eden karmaşık metal parçaların üretimini mümkün kıldığı için tercih etmektedir. HPDC, otomotiv ve havacılık endüstrileri ile elektronik bileşenler ve tüketim malları üretiminin motorlar ve muhafazalar, yapısal elemanlar ve mekanik montajlar gibi uygulamalar için hafif ve dayanıklı parçalar üretmesini sağlar. Yüksek basınçlı döküm üretim süreci, kullanım ömrünü kısaltırken ve performanstan ödün verirken ürün kalitesini düşüren önemli kusurlar yaratan çok sayıda riskle karşı karşıyadır. Üretim sürecinde yanlış kalıp tasarımı, türbülanslı erimiş metal akışı, sıkışan gazlar, tutarsız soğutma oranları ve termal stres nedeniyle çeşitli kusurlar oluşur. HPDC teknolojisi gözeneklilik, soğuk kapanma, büzülme kusurları, parlama oluşumu, yüzey kusurları, yanlış çalışma, kalıp erozyonu ve lehimleme gibi yedi temel kusurla karşılaşır. Bu tür üretim hataları, malzeme mukavemetinin bozulmasına neden olurken, düzensiz boyutlar ve bileşen bozulmasını tetikleyebilecek istenmeyen görsel efektler üretir. Üreticiler, kontrollü sıcaklık sistemleri ve vakum destekli döküm prosedürlerinin yanı sıra işleme parametrelerinin optimizasyonu ve daha iyi talaş kaldırma yöntemleri aracılığıyla üretim sorunlarıyla mücadele etmektedir. Gerçek zamanlı izleme ve simülasyon yazılımları, basınçlı döküm sürecinde daha fazla verimlilik ve güvenilirlik sağlayan gelişmiş kalite kontrol yöntemleridir.
Bu makale, yüksek basınçlı hava koşullarında standart üretim sorunlarının kapsamlı bir analizini sunmaktadır. kalıp döküm Bu kusurları azaltmak için temel nedenlerin ve çözüm stratejilerinin açıklamaları ile teknoloji. Üreticiler ancak bu zorlukları anlayarak ve en iyi uygulamaları uygulayarak basınçlı döküm bileşenlerinin kalitesini, uzun ömürlülüğünü ve tabii ki performansını artırabilir ve aynı zamanda israfı ve üretim maliyetlerini azaltabilir. Bu üretim hataları konusunda yetkinlik, basınçlı döküm mühendislerine, üretim müdürlerine ve kalite kontrol uzmanlarına süreçlerini en iyi basınçlı döküm sonuçları için optimize etmelerinde yardımcı olacaktır.
1. Gözeneklilik
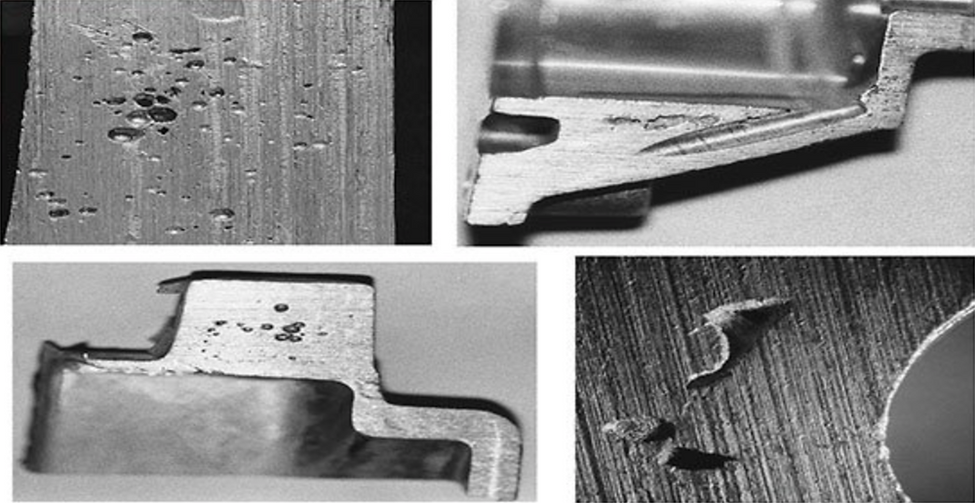
Gözeneklilik, metal matris içinde bulunan küçük delikler veya gaz kalıntıları ile tanımlanır ve sonuç olarak mekanik özellikleri etkiler, mukavemeti azaltır, hava ve gazların yapıdan geçmesine izin verir ve kalıp döküm ürünlerde görünür yüzey kusurlarına yol açar.
Sebepler:
- Dökümden önce malzemelerde bulunan gaz içerikler.
- Erimiş metal akışında aşırı türbülans.
- Kötü havalandırma ve yanlış kalıp tasarımı.
- Büzülme gözenekliliğine neden olan hızlı katılaşma.
- Erimiş metalin kirlenmesi.
- Düzgün metal akışına neden olmayan yetersiz basınç.
Önleme ve Çözümler:
- Geçit ve havalandırma tasarımı yoluyla uygun gaz atımının sağlandığından emin olun.
- Boşluğa giren metalin pürüzsüzlüğünü artırmak için enjeksiyon hızını yavaşlatın.
- Hava hapsetme sorunu vakum destekli kalıp döküm tekniği ile çözülmelidir.
- Erimiş metalin enjekte edilmeden önce yeterince gazdan arındırıldığından emin olun.
- Çatlak sorununun ve diğer katılaşma kusurlarının oluşumunun üstesinden gelmek için soğutma hızını kontrol edin.
- Kirleticilerden kaynaklanan gözeneklilik olasılığını azaltmak için kalıp yüzeylerini sık sık kontrol edin ve temizleyin.
2. Soğuk Kapatma
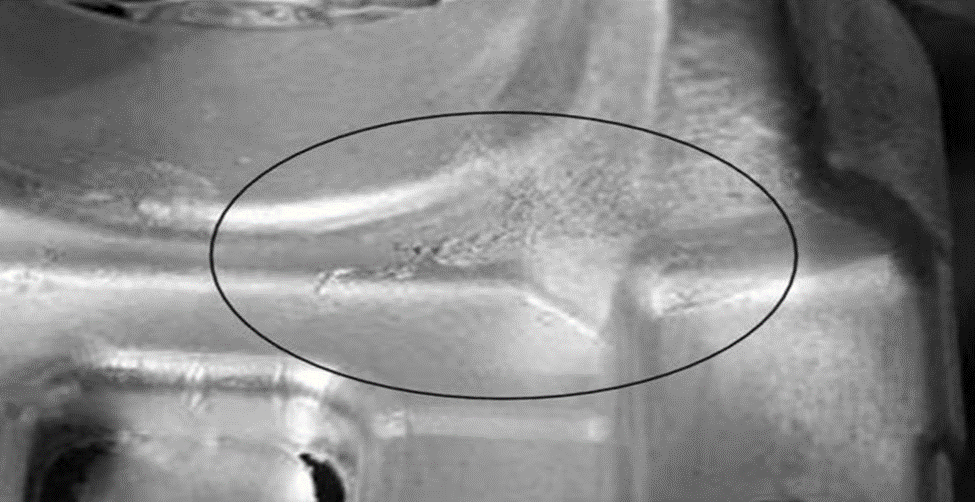
İki erimiş metal akımı düzgün bir şekilde kaynaşmadığında ve dökümde zayıf bağlanma alanları veya görünür dikişler oluşturduğunda bir soğuk kapanma meydana gelir. Bu kusur sadece mekanik mukavemeti azaltmakla kalmaz, aynı zamanda kırılma riskini de artırır ve bileşenin dayanıklılığını ve görünümünü olumsuz etkiler.
Sebepler:
- Düşük erimiş metal sıcaklığı.
- Genellikle erken katılaşmaya yol açan yavaş enjeksiyon hızı için işaretlenmiştir.
- Yetersiz akış kanallarına sahip kötü kalıp tasarımı.
- Düzgün füzyonu engelleyen yüzey filmleri oluşturan aşırı oksidasyona neden olabilir.
- Kötü yolluk sistemi tasarımı nedeniyle tutarsız metal akışı.
Önleme ve Çözümler:
- Ayrıca, uygun akışkanlığı sağlamak için en uygun metal dökme sıcaklığı korunmalıdır.
- Dolumu tamamlamak ve tek parça haline getirmek için enjeksiyon hızını artırın.
- Metalin zorlanmadan hareket edebilmesi için kalıp tasarımında gereksiz akış engellerini ortadan kaldırın.
- Termal analiz araçlarını kullanarak üretimden önce akış sorunlarının tespiti ve çözümü.
- Genellikle soğuk kapatma kusurlarını artıran hava sıkışmasını önlemek için uygun havalandırma teknikleri uygulanmalıdır.
3. Büzülme Kusurları
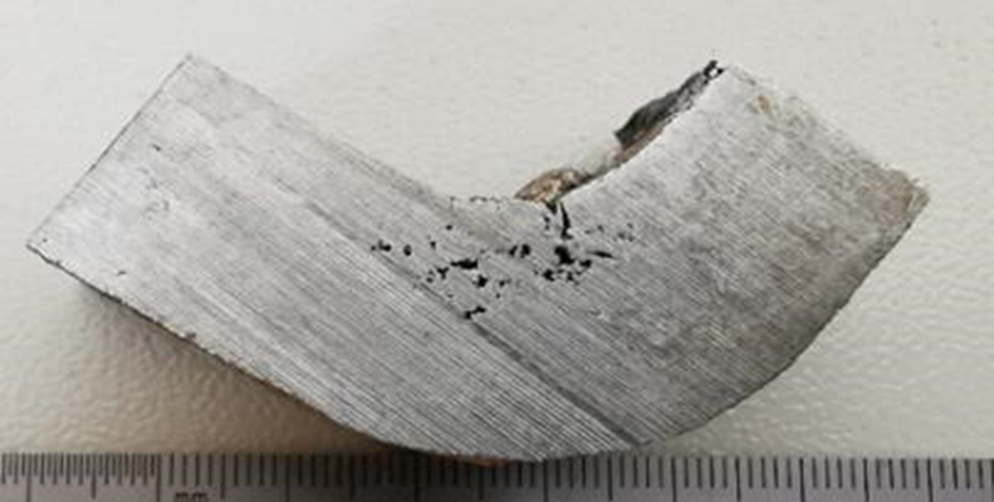
Büzülme kusurları, soğutma sırasında metalin büzülmesi nedeniyle meydana gelir ve dökümün yapısal bütünlüğünü bozan iç boşluklara veya oyuklara yol açar. Sonuç olarak, bu kusurlar nihai ürünün mekanik mukavemetini azaltır, stres altında potansiyel arızaya neden olur ve düşük yüzey kalitesine neden olur, böylece nihai ürünlerin hem işlevselliğini hem de estetiğini etkiler.
Sebepler:
- Katılaşma sırasında yetersiz metal besleme
- Uygun olmayan kalıp tasarımı nedeniyle soğutma hızları eşit değildir
- Alaşım bileşimi nedeniyle yüksek metal büzülmesi
- Lokalize kasılmaya neden olan hızlı soğutma
- Katılaşma aşamasında yetersiz basınç
Önleme ve Çözümler:
- Kalıbı, homojen soğutma ve erimiş metalin uygun şekilde beslenmesini sağlayacak şekilde modifiye edin.
- Daha düşük büzülme eğilimine ve daha iyi katılaşma özelliklerine sahip alaşımlar kullanın.
- Büzülme boşluklarını doldurmak ve en aza indirmek için katılaşma sırasında basınç ayarlarını optimize etmek için kullanılır.
- Katılaşma oranlarını dengelemek ve termal gerilimi azaltmak için kontrollü soğutma yöntemleri kullanın.
- Büzülme kusurlarını tahmin etmek ve önlemek için gerçek zamanlı izleme ve simülasyon araçları uygulayın.
4. Flaş Oluşumu

Yüksek basınçlı metal kaçışı nedeniyle ayırma hattında veya kalıp boşluğunda oluşan fazla ince metal katmanlar flaş olarak adlandırılır. Parlama döküm sonrasında kesilebilse de, aşırı parlama malzeme israfının, takım aşınmasının ve ilgili üretim maliyetlerinin artmasına neden olur ve böylece kalıp döküm işleminin genel verimliliğini azaltır.
Sebepler:
- Aşırı enjeksiyon basıncı, erimiş metalin kalıp boşluklarına zorlanmasına neden olur.
- Aşınmış kalıp veya sızıntılara izin verecek şekilde yanlış kalıp kilitleme nedeniyle.
- Enjeksiyon sırasında kalıp ayrılmasına neden olan yetersiz bir sıkıştırma kuvvetinin olduğu durumlarda.
- Metalin dışarı sızması için boşluklarla kötü bir şekilde uzanacaklardır.
- Kalıp yağlama ile net olmayan metal akış kontrolü
Önleme ve Çözümler:
- Kalıp ayrılmasını ve parlama oluşumunu önlemek için uygun sıkıştırma kuvveti korunmalıdır.
- Doğru sızdırmazlık sağlamak için aşınmış kalıpları düzenli olarak inceleyin ve değiştirin.
- Dolumun en az parlama ile dolması ve doldurulması için basınç için en uygun ayarları sağlayın.
- İstenmeyen boşlukları ve metal sızıntısını önlemek için kalıp yeniden hizalaması iyileştirilmelidir.
- Metal akışını kontrol etmek ve aşırı metal kaçışını azaltmak için hassas kalıp yağlama teknikleri uygulayın.
5. Yüzey Kusurlarının Kontrolü (Kabarcıklar, Çatlaklar ve Kırışıklıklar)

Çeşitli yüzey kusurları, kabarcıklar, çatlaklar ve kırışıklıklar, dökümün görsel görünümünü ve mekanik mukavemetini bozar ve önlenmesi ve ortadan kaldırılması gerekir. Ürünün dayanıklılığını azaltan, reddetme oranını artıran ve boyama veya kaplama gibi döküm sonrası işlemlerden sonra ürünün kötü yapışmasına neden olan kaynak kusurlarına neden olur.
Sebepler:
- Dökme sırasında sıvı plastik içinde sıkışan hava.
- Ayrıca, üniform olmayan soğutma hızları nedeniyle termal stres ve yüzey düzensizlikleri vardır.
- Katılaşma sırasında aşırı ısınma veya kötü kontrol edilen sıcaklık.
- Veya döküm yüzeyini etkileyebilecek metal safsızlıkları veya kalıntıları
- Kötü kalıp yağlaması düzensiz metal akışına ve yüzey kusurlarına neden olmuştur.
Önleme ve Çözümler:
- Dökümden önce sıkışan gazları önlemek için erimiş metalin uygun şekilde gazdan arındırılması.
- Düzgün soğutma teknikleri kullanarak katılaşmayı kontrol edin ve termal stresi önleyin.
- Kalıp sıcaklık kontrolü, aşırı ısınmayı ve eşit olmayan soğutmayı önlemek için optimize edilmelidir.
- Dökümden önce tüm safsızlıkların tespit edilmesini sağlayacak şekilde kalitesinin sıkı bir şekilde kontrol edilmesi.
- Yüzey kalitesine ve kusurları azaltmaya dayalı olarak kalıp için kaplamalar ve yağlayıcılar uygulayın.
6. Kapanımlar ve Kirlenme
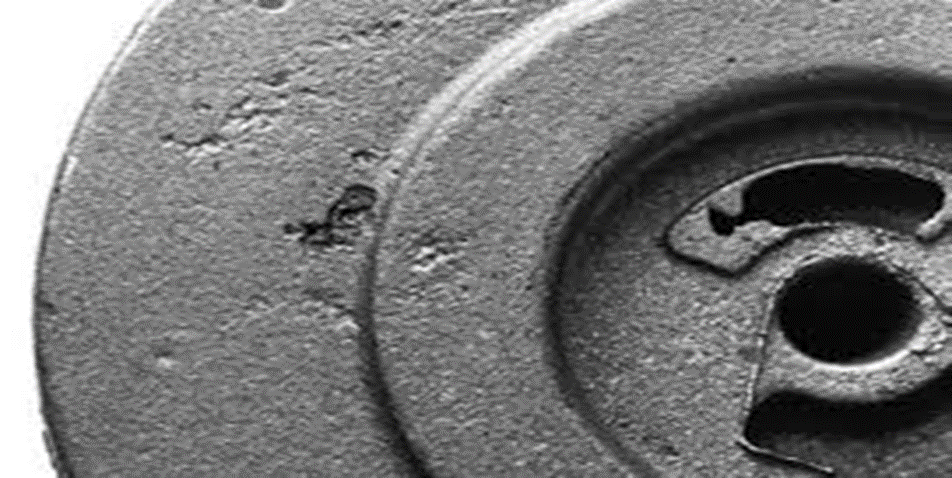
Nihai dökümde sıkışan cüruf, oksit filmleri, kir veya diğer yabancı maddeler gibi istenmeyen yabancı partiküller zayıf mekanik özellikler, zayıf yapısal bütünlük ve yüzey kusurları yaratır ve inklüzyon olarak adlandırılır. Bu kirleticilerin varlığı, basınçlı döküm bileşen performansını ve dayanıklılığını azaltabilir, böylece yüksek hassasiyetli uygulamalar için uygun olmazlar.
Sebepler:
- Örneğin, kontamine hammaddeler istenmeyen safsızlıklardan oluşur.
- Erimiş metal içindeki yabancı partiküller sonuç olarak iyi filtrelenemez
- Metal eritme veya dökme sırasında uzun süre havaya maruz kalma nedeniyle
- Daha yüksek cüruf oluşumuna neden olan verimsiz metal işleme uygulamalarını içerir
- Yetersiz kalıp yağlaması, erimiş metale yabancı bir maddenin girmesini içerir.
Önleme ve Çözümler:
- Yüksek kaliteli hammaddeler uygun şekilde ve kirletici maddeler olmadan rafine edilmelidir.
- Enjeksiyondan önce erimiş metalden cürufu, oksitleri ve diğer safsızlıkları gidermek için etkili filtreleme sistemleri kurun.
- Kontrollü erimiş metal kullanımını sürdürün ve uygun olan yerlerde oksidasyonu sınırlamak için inert gaz koruması kullanın.
- Artık malzemeden kaynaklanan kontaminasyonu önlemek için döküm ekipmanını düzenli olarak temizleyin ve bakımını yapın.
- Kalıp boşluğunda yabancı madde birikmemesini sağlamak için uygun kalıp yağlaması kullanın.
7. Yanlış Çalışmalar ve Eksik Doldurma
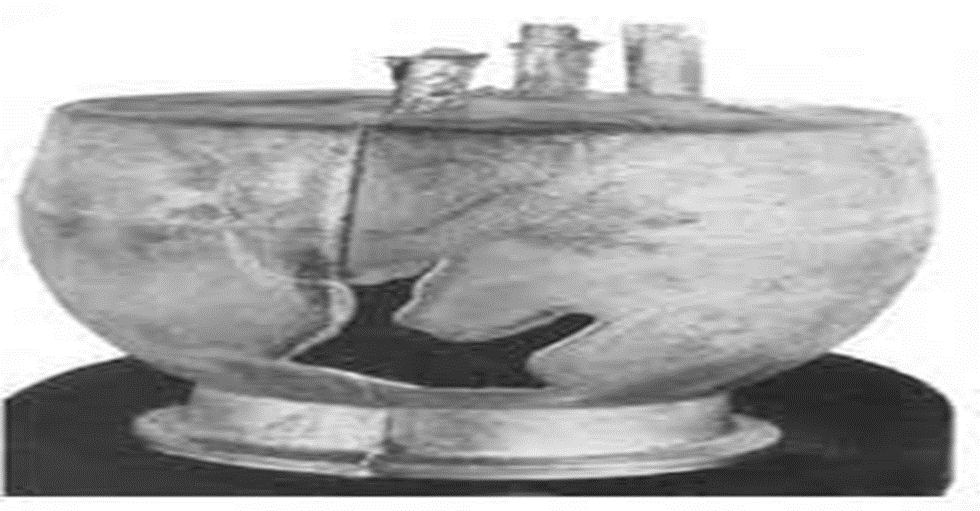
Yanlış çalışma, kalıp boşluğunun kısa sürede doldurulduğu durumlarda meydana gelir ve bu da nihai bileşende eksik bölümlere, ince duvarlara ve zayıf noktalara neden olur. Parçanın yapısal bütünlüğü ve işlevselliği üzerinde olumsuz etkiler ve bu şekilde performans uygulamaları için uygun değildir.
Sebepler:
- Düşük enjeksiyon hızı veya basıncında, kalıbı tamamen kaplamayan
- Metal akışını ve erken katılaşmayı önleyen soğuk kalıp yüzeyleri
- Yetersiz erimiş metal hacmine neden olarak yetersiz kavite dolumuna yol açar
- Erimiş metalin eşit olmayan dağılımına neden olan zayıf yolluk ve yolluk tasarımından
- Aşırı türbülans metal akışını engelleyen hava cepleri oluşturur
Önleme ve Çözümler:
- Akışkan hale getirmek ve erken katılaşmayı önlemek için metal sıcaklığını artırın.
- Ayrıca, enjeksiyon basıncı ve hızı doğru ayarlanarak boşluk doldurma optimize edilmelidir.
- Kalıpların uygun çalışma sıcaklıklarını koruyun ve zamanından önce soğumalarını önleyin.
- Düzgün ve eşit metal dağılımını desteklemek için geçit ve yolluk tasarımını iyileştirin.
- Üretimden önce simülasyon yazılımı ile metal akışını ve hatalı çalışma potansiyelini simüle edin.
8. Kalıp Erozyonu ve Aşınması
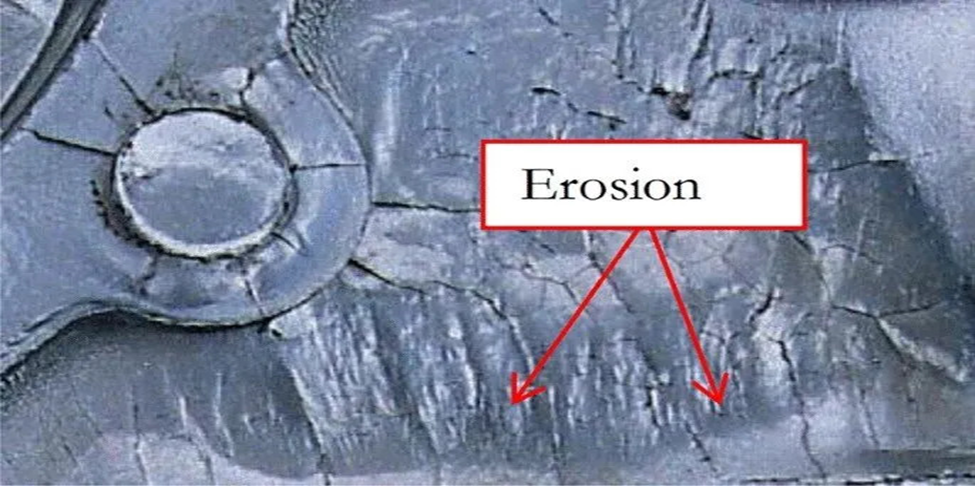
Ergimiş erozyon kalıp aşınması, yüksek hızlı metalin kalıp parçası yüzeylerini gerekli boyutlar elde edilene kadar sürekli olarak aşındırması nedeniyle kalıp yüzeylerinin kaybedilmesidir, bu da kötü yüzey kalitesi ve kısa kalıp takım ömrü ile sonuçlanır. Bu kusur meydana gelirse, kalıp değişimi yaygındır ve sonuç olarak, döküm kalitesi değişirken üretim maliyetleri artar.
Sebepler:
- Ayrıca, kademeli aşınmaya neden olan yüksek sıcaklıkta erimiş metale tekrar tekrar maruz kalır.
- Hem termal hem de mekanik strese karşı zayıf direnç gösteren nispeten düşük kaliteli kalıp malzemeleri
- Aşırı termal döngü, yorulma nedeniyle malzemenin çatlamasına neden olabilir.
- Yüksek enjeksiyon altında kalıp malzemesinin bozulmasına yol açar.
- Az yağlama mı? Daha fazla sürtünme ve daha fazla aşınma sonucu.
Önleme ve Çözümler:
- Bunlardan biri, daha dayanıklı olan yüksek kaliteli ısıya dayanıklı kalıp malzemeleri kullanmaktır.
- Kalıp ömrünü uzatmak için nitrürleme veya seramik kaplamalar gibi koruyucu yüzey kaplamaları uygulanabilir.
- Termal stresi azaltmak ve erken aşınmaya neden olmak için kontrollü soğutma yöntemleri uygulanmalıdır.
- Kalıp üzerinde minimum zorlanma ile hız ve basınç arasında bir denge kurmak.
- Erozyonu mümkün olan en kısa sürede tespit etmek ve gidermek için kalıpları düzenli olarak inceleyin ve bakımlarını yapın.
9. Sıcak Çatlama
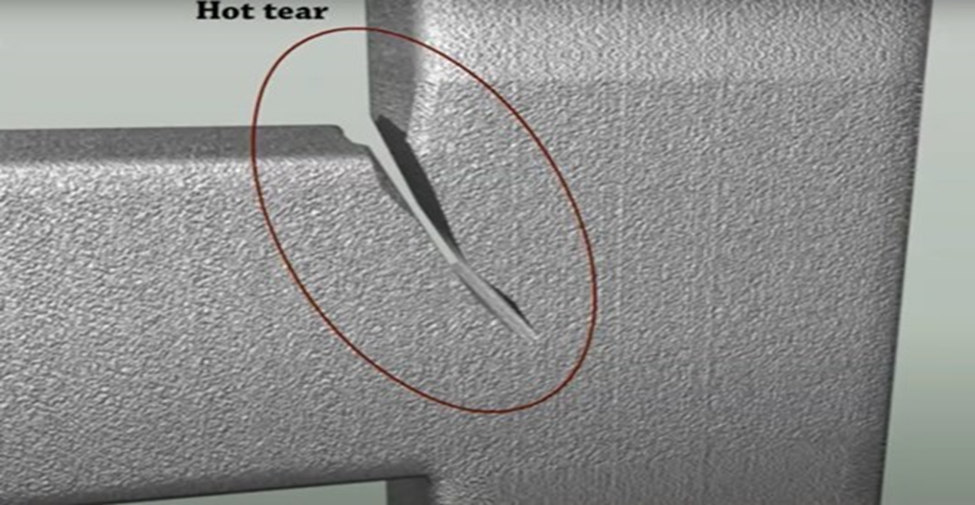
Metalin yarı katı hali sırasında, yüksek termal stres ve aşırı büzülme nedeniyle meydana gelen çatlaklar sıcak çatlama olarak bilinir. Bu çatlaklar dökümün mekanik bütünlüğünü bozar, yani stres veya yük altında çatlakların bulunduğu yerde dökümün bozulma olasılığını artırır.
Sebepler:
- Kalıpta güvenilir olmayan soğutma hızları, belirli bölgelerde stres noktalarına neden olur
- Alaşım bileşiminde termal strese ve çatlamaya karşı yüksek bir duyarlılığa sahiptir.
- Ayrıca hızlı katılaşma sırasında oluşan aşırı artık gerilime neden olur metal büzülmesinde bir kısıtlama
- Kalıp tasarımı zayıfsa, döküm boyunca sıcaklık değişimleri olacaktır.
- Katılaşma sırasındaki basınç, çatlakların yayılmasını önlemek için çok küçüktü.
Önleme ve Çözümler:
- Aynı zamanda homojen katılaşma için soğutma hızlarının optimize edilmesini ve termal stresin en aza indirilmesini de içerecektir.
- Daha iyi tane yapısına sahip alaşımların uygun şekilde kullanılmasıyla alaşımların çatlama direncinin artırılması.
- Dökümden sonra gerilim giderme tekniklerinin kullanılması, yani kontrollü ısıl işlem.
- Daha az sıcaklık farkı olan kalıplar tasarlayın.
- Metalin katılaşması sırasında akması ve çatlakların oluşmaması için uygun basıncı sağlayın.
10. Lehimleme
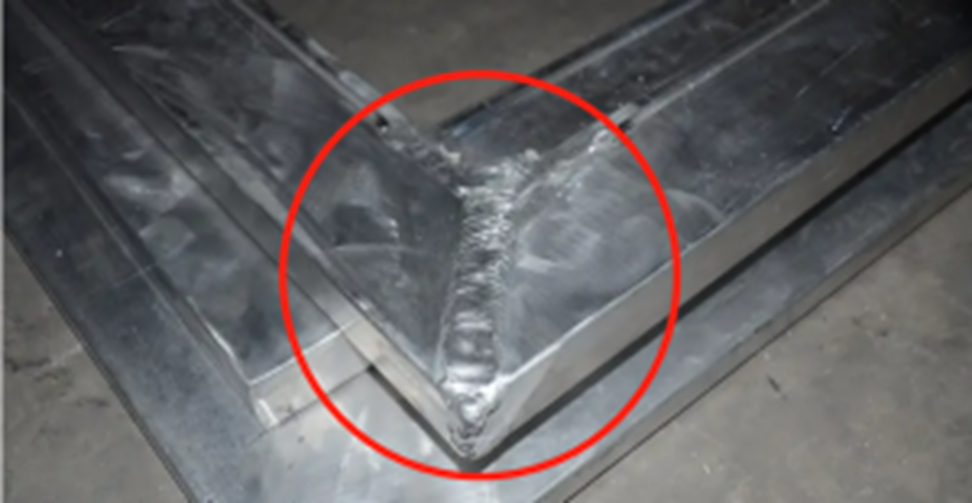
Erimiş metal, dökümle çıkarılması zor olan kalıp yüzeyine yapışarak yüzey kusurlarına, kalıp aşınmasına ve uzun süreli üretim kesintilerine neden olur. Boyutsal hatalar ve kötü yüzey kalitesi de bu kusurdan kaynaklanır ve nihai ürünün kalitesinin genel olarak düşmesine neden olur.
Sebepler:
- Yüksek alüminyum içeriği nedeniyle alaşımdaki metal yapışma olgusunda artış
- Metalin kalıp yüzeyine yapışması için kalıp sıcaklıklarının aşırı yüksek olması
- Zayıf kalıp yağlaması nedeniyle yapışmaya karşı yetersiz koruma
- Yetersiz soğutma, erimiş metalin kalıpla çok uzun süre temas halinde kalmasına neden olur - Metal yapışmasını teşvik eden kalıp üst yüzeylerinde kireçlenme veya hasar.
Önleme ve Çözümler:
- Metal yapışmasını önlemek için her zaman yüksek kaliteli kalıp yağlayıcıları uygulanır.
- Sıcak yapışma çok güçlüyse kalıp sıcaklığının optimum aralıkta kontrol edilmesini sağlar.
- Seramik veya nitrür tabakaları gibi uygun kalıp kaplamaları kullanarak metal yapışmasını azaltın.
- Metal-kalıp temas süresini azaltmak ve soğutma sistemi verimliliğini artırmak için.
- Yapışkan olmayan pürüzsüz bir yüzey elde etmek için kalıp yüzeylerini düzenli olarak inceleyin ve parlatın.
Sonuç
Yüksek basınç kalıp döküm karmaşık metal parçaları maksimum verimlilikle yüksek doğrulukta oluşturan güçlü bir üretim sürecidir. Bununla birlikte, uygun olmayan proses parametreleri, malzeme sorunları ve/veya kalıp tasarımı kusurları kullanılarak farklı türde hatalar ortaya çıkar. Üreticiler bu olağan imalat hatalarını anladıktan sonra optimum proses kontrol kalıbı, doğru seçilmiş malzeme vb. gibi önleyici tedbirler alabilirler.
Bir şirket, sürekli süreç iyileştirmenin yanı sıra hata önleme stratejilerini vurgulayarak ürün kalitesini artırabilir, üretim maliyetlerini düşürebilir ve kalıp döküm operasyonlarında daha yüksek üretim verimliliği elde edebilir.
Sıkça Sorulan Sorular (SSS)
1. Yüksek basınçlı dökümdeki kusurların başlıca nedenleri nelerdir?
Yüksek basınçlı dökümdeki kusurların ana nedenleri arasında yanlış kalıp tasarımı, zayıf metal akışı, sıkışmış gaz, yüksek termal stres, eşit olmayan soğutma ve kontamine hammaddeler yer alır. Bu kusurlar, proses parametrelerinin optimizasyonu ve kalite kontrol önlemlerinin kullanılmasıyla azaltılabilir.
2. Döküm parça performansında gözeneklilik nasıl bir rol oynar?
Gözenekliliğin varlığı, basınçlı döküm bileşenlerinin yapısal bütünlüğünü zayıflatarak mukavemeti azaltır ve basınç geçirmez bileşenlerde hava sızıntılarına ve anestezik kusurlara neden olur. Uygun gaz giderme, optimize edilmiş yolluk sistemleri ve vakum destekli döküm kullanılarak gözeneklilik en aza indirilebilir.
3. Basınçlı dökümde soğuk kapanmalar nasıl önlenebilir?
Doğru metal dökme sıcaklığı, daha yüksek enjeksiyon hızları, metal akışını yumuşatmak için optimize edilmiş kalıp tasarımı ve olası akış sorunlarını belirlemek için termal analiz araçlarının uygulanması soğuk kapanmaların önlenmesine yardımcı olabilir.
4. Kalıp erozyonu yüksek basınçlı dökümde önemli bir sorundur çünkü?
Yüksek sıcaklıktaki erimiş metalin kalıplara tekrar tekrar maruz kalması, kalıpların ömrünü kısaltan ve döküm parçaların hassasiyetini azaltan kalıp erozyonuna neden olur. Kalıp ömrü, yüksek kaliteli kalıp malzemelerinin kullanımı, koruyucu kaplamaların kullanılması ve kontrollü kalıp soğutması ile uzatılabilir.
5. Basınçlı döküm ürün kalitesini ve tutarlılığını daha iyi yapan nedir?
Sıkı kalite kontrolü, proses parametrelerinin optimizasyonu, kalıp sıcaklığı kontrolü, yüksek kaliteli alaşımların kullanımı ve kalıp ve makine denetimi, döküm ürün kalitesinin olağan iyileştirilmesi için periyodik olarak yapılır.