
Çinko döküm, birçok farklı endüstride kullanılmak üzere yüksek kaliteli hassas parçalar oluşturmak için kullanılan popüler ve etkili bir üretim sürecidir. Özel çinko döküm, tasarım özgüllüğünün kendine özgü ihtiyaçlarını karşılamak isteyen imalat işletmeleri için paha biçilmez bir dönüm noktası oluşturmuştur. Otomotiv Parçaları, Elektronik muhafazalar, sertlik, Özelleştirilmiş ekstremite kolaylığı, En Yüksek Standart ve diğer birçok kullanımda çinko döküm uygulaması gösterilmiştir.
Zamak 2, Zamak 3, Zamak 5 ve ZA 8, mekanik ve termal gereksinimlerine göre seçilen ve yaygın olarak kullanılan Çinko döküm alaşımlarıdır. Zamak 2 yaklaşık yüzde 4 alüminyum, yaklaşık yüzde 3 bakır ve bir miktar magnezyum içerir ve 330 MPa'ya çok yakın bir gerilme mukavemeti ile büyük bir güç ve sertlik sağlar. Zamak 3 açık ara en çok kullanılanıdır ve neredeyse bakır içermez (yaklaşık 4 % alüminyum ve benzer magnezyum içeriği) ve bu nedenle yaklaşık 280 MPa gerilme mukavemeti ile sert ve dökümü kolaydır. Mukavemet ve sertliği 310 MPa çekme mukavemetine kadar biraz artıran 1% bakır içeren çinko bazlı bir alaşım, iyi dökülebilirliğe sahip olan Zamak 5 olarak bilinir. ZA-8, yaklaşık 8.5% alüminyum ve yaklaşık 1% bakır alaşımı olup, yaklaşık 390 MPa çekme mukavemetine ve yüksek sıcaklık koşulları altında iyi aşınma direncine ve performansa sahiptir.
Özel çi̇nko dökümBu makalede, bu süreç ve Çin'in özel çinko alaşımlı basınçlı döküm hizmetlerinin iş kullanımı araştırılacaktır.
Çinko Basınçlı Döküm Nedir?

Çinko döküm, erimiş çinkonun yüksek basınçta çelik bir kalıba enjekte edilmesi yöntemidir. Metal katılaştığında, kalıbın şeklini alarak belirli ve kalıcı bir parça oluşturur. Diğer metallerle karşılaştırıldığında, çinko büyük bir akışkanlığa, mükemmel mukavemete ve ince detaylara sahip kalıp döküm bileşenlerine sahiptir.
Dayanıklılığı çinkoyu performans açısından cazip bir seçenek haline getirir, ancak aynı zamanda nispeten düşük maliyetli bir malzemedir ve performansı üretim maliyetleriyle dengelemek isteyen şirketler için cazip bir seçenektir. Bu durum özellikle her tür özel çinko basınçlı döküm için geçerlidir, çünkü bu süreç işletmelerin bireysel ihtiyaçları için özelleştirilmiş bileşenler tasarlamasına olanak tanır.
Özel Çinko Basınçlı Dökümün Avantajları
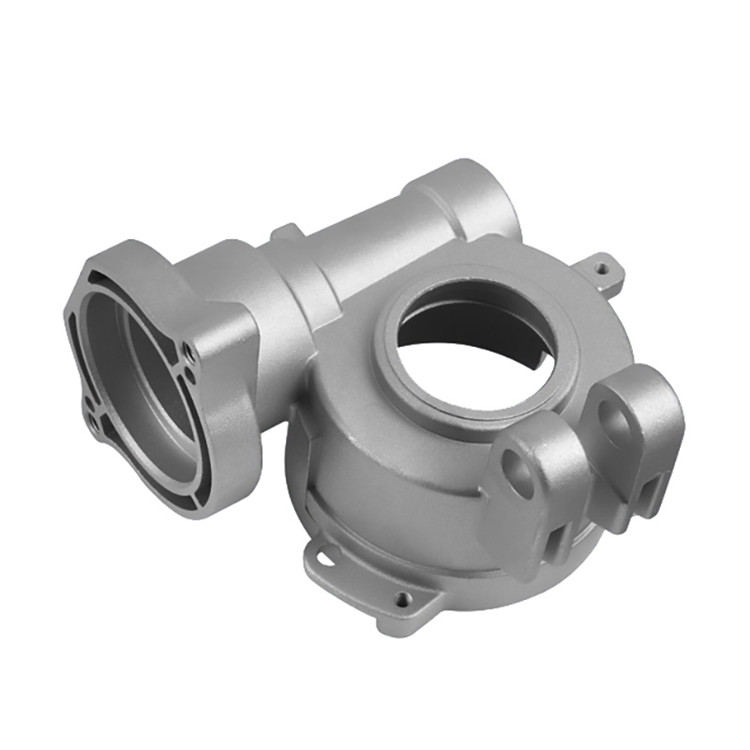
1. Hassasiyet ve Doğruluk
Çinko basınçlı dökümün özelleştirilmesinin en önemli avantajlarından biri, son derece doğru ve hassas parçalar yapabilmesidir. Bu basınçlı döküm süreci, karmaşık tasarımlar için bile bileşenlerin boyutlarda ve yüzey kaplamasında tutarlı kalmasını sağlar. Tolerans ve uyum ihtiyacının olduğu elektronik, otomotiv ve havacılık alanlarında bu hassasiyet çok önemli hale gelmektedir.
Başka yollarla oluşturulamayan ince detaylı parçalar ve karmaşık heykel detaylı geometrilere sahip parçalar özel çinko döküm kullanılarak üretilebilir. Diğer üretim yöntemleri, minimum varyasyonla yüksek hacimli aynı parçalara sahip bazı parçaları üretebilirken, basınçlı döküm, yüksek düzeyde tutarlılık gerektiren parçalar için gerçekten gidilecek yoldur.
2. Dayanıklılık ve Güç
Sağlam bir metaldir ve çok dayanıklı ve korozyona dirençlidir. Bu nedenle, aşındırıcı koşullara maruz kalacak parçaların yapımı için mükemmeldir. Çinko basınçlı döküm, kullanım süreleri boyunca etkili bir şekilde kullanılmak üzere tasarlanmış özel parçalar üretmek için özel yetenek sunar.
Çinko alaşımlı basınçlı dökümler olağanüstü mukavemet / ağırlık oranları sağlar, böylece ürünler güçlü olur ancak çok ağır olmaz. Çoğu endüstride olduğu gibi, sistemin kütlesini azaltmanın performans, yakıt verimliliği vb. açısından kritik önem taşıdığı otomotiv üretiminde de bu çok önemlidir.
3. Maliyet Etkinliği
Birçok işletme için uygun maliyet çok önemli bir husustur. Bu zorluk, nispeten daha düşük bir maliyetle yüksek kaliteli parçalar yaratma kabiliyeti nedeniyle özel çinko döküm işlemi kullanılarak oldukça iyi bir şekilde çözülebilir. Çinkonun nispeten düşük malzeme maliyeti ve basınçlı döküm işleminin verimliliği nedeniyle, Çinkonun üreticiler için çok uygun maliyetli bir seçim olduğu konusunda çok az tartışma vardır.
Basınçlı döküm aynı zamanda çok hassas bir şekilde yüksek seviyede hassas olduğundan üretim sonrası maliyetleri veya ikincil makine çalışmalarını azaltabilir. Ayrıca tek bir üretim çalışmasında yüksek düzeyde aynı parça üretimine izin verir ve bu nedenle maliyetleri daha da düşürür, bu da onu seri üretim için mükemmel bir çözüm haline getirir.
4. Tasarım Esnekliği
Özel tasarım kullanan çinko basınçlı dökümün ana avantajı, tasarım açısından esneklik olmasıdır. Bu, üreticilerin karmaşık şekillere, ince duvarlara ve aksi takdirde üretilmesi pratik olmayan karmaşık özelliklere sahip parçalar oluşturmasına olanak tanır. Bu tür bir esneklik, işletmelerin belirli işlevler ve belirli bir görünüm sağlayan farklı parçalar icat etmelerine ve yaratmalarına olanak tanır.
Ayrıca, bu özel çinko alaşımlı basınçlı döküm kullanılarak pürüzsüz ve cilalı, dokulu veya mat gibi çeşitli yüzey kaplamalarına sahip parçalar oluşturulabilir. Tasarımdaki çok yönlülük, çinko dökümünü tüketici elektroniği dışında daha birçok uygulama için uygun hale getirir - endüstriyel makineler, araç parçaları vb.
5. Kısa Teslim Süreleri
Günümüzde yüksek hızlı, yüksek hacimli üretim ortamında zaman çok önemlidir. Özel çinko döküm, işletmelerin ürünlerini pazara hızlı bir şekilde sunarken, hızlı üretim teslim süreleriyle hedefe ulaşmalarına yardımcı olur. Kalıplar yapıldıktan sonra döküm süreci oldukça hızlıdır, bu nedenle aslında tüm süreç oldukça hızlıdır ve minimum sürede büyük miktarda parçanın hızlı bir şekilde üretilmesine olanak tanır.
Ayrıca, pazara sunma süresinin kritik olduğu sektörlerde de kullanışlıdır. Çinko dökümün doğru kullanımı, şirketlerin gecikmelerden ve envanter sıkıntısından kaçınmasına yardımcı olur ve yüksek kaliteli parçalarla sonuçlanır.
Özel Çinko Basınçlı Döküm Süreci
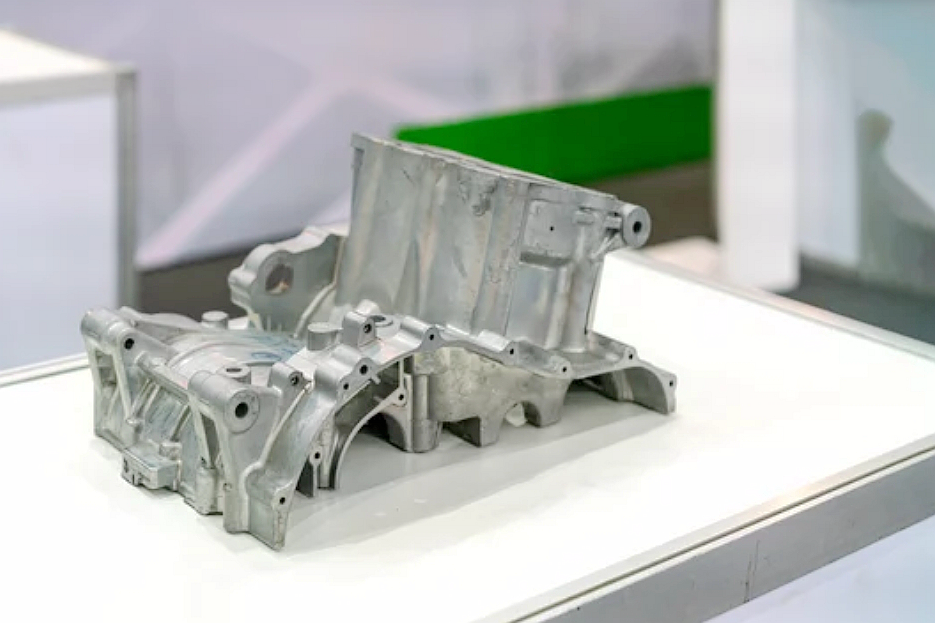
Bu, gerekli olanı başarmak için gerçekleştirilmesi gereken birçok önemli adıma sahip olan seri özel çinko döküm işlemi için geçerlidir. Bu adımlar şunlardır:
1. Kalıp Tasarımı ve Oluşturulması
Bir kalıp yapmak için yapılan ilk şey, kalıbı çelik kullanarak tasarlamaktır. Üretilen parça, kalıbı oluşturmak için kalıpta üretilecek olanla şekil ve özellik olarak eşleştirilir. Bu durumda müşteri ne tür bir kalıba ihtiyacı olduğunu tanımlayabilir. Özel basınçlı döküm kalıpları, müşterinin benzersiz isteklerini ve modifikasyonlarını karşılamak üzere tasarlanır.
2. Erimiş Çinko Enjeksiyonu
Kalıp hazırlandıktan sonra, erimiş çinko yüksek basınç altında içine doldurulur. Bu şekilde basınç, hassas bir parça için kalıbın her detayının çinko ile doldurulmasını sağlar. Hızlı bir şekilde soğur ve kalıbın şeklinde katılaşır.
3. Fırlatma ve Son İşlem
Çinko donduktan sonra parça kalıptan çıkarılır. Bununla birlikte, basınçlı döküm işlemi bitmemiş olsa bile, bitmiş parça, fazla malzemenin kırpılması veya pürüzlü kenarların düzeltilmesi gibi başka son işlemlerden geçebilir ve hatta basınçlı döküm işleminden sonra bile parça üzerinde yüksek kaliteli bir yüzey kalitesi üretir.
4. Kalite Kontrol
Parçalar daha sonra, belirlenen güç, doğruluk ve performans standartlarını karşıladıklarını garanti etmek için kalite kontrollerinde kapsamlı bir şekilde test edilir. Bu testler boyutsal kontroller, görsel denetim ve stres testlerini içerebilir.
Çinko Alaşım Karşılaştırma Tablosu
Mülkiyet | Zamak 2 | Zamak 3 | Zamak 5 | ZA-8 | Superloy | AcuZinc 5 |
Alüminyum (%) | 3.8 - 4.3 | 3.8 - 4.3 | 3.8 - 4.3 | 8.2 - 8.8 | 3.5 - 4.0 | 3.5 - 4.3 |
Bakır (%) | 2.7 - 3.3 | <0.03 | 0.7 - 1.1 | 0.9 - 1.3 | 2.2 - 2.7 | 0.5 - 1.2 |
Magnezyum (%) | 0.035 - 0.06 | 0.035 - 0.06 | 0.035 - 0.06 | 0.02 - 0.035 | 0.02 - 0.05 | 0.02 - 0.05 |
Çekme Dayanımı (MPa) | ~328 | ~283 | ~310 | ~386 | ~410 | ~410 |
Akma Dayanımı (MPa) | ~270 | ~210 | ~230 | ~315 | ~360 | ~370 |
Uzama (%) | 3 | 7 | 6 | 1 | 2.5 | 3 |
Sertlik (Brinell) | 120 | 82 | 85 | 92 | 110 | 105 |
Dökülebilirlik | Adil | Mükemmel | İyi | İyi | Adil | İyi |
Korozyon Direnci | Orta düzeyde | İyi | Zamak 3'ten daha iyi | İyi | Yüksek | Yüksek |
Kayda Değer Özellik | Yüksek mukavemet ve sertlik | Genel amaçlı alaşım | Geliştirilmiş güç ve aşınma | Yüksek sıcaklık performansı | Mükemmel dayanıklılık ve aşınma | Yüksek süneklik ve mukavemet |
Çin'in Özel Çinko Alaşımlı Basınçlı Döküm Hizmetlerinin Rolü
Çin'in özel çinko alaşımlı basınçlı döküm hizmetleri, son yıllarda üretim holdinginde lider bir oyuncu olarak kendini göstermiştir. Çin, basınçlı döküm endüstrisi için ileri teknoloji, kalifiye işgücü ve düşük maliyetli üretim avantajlarına sahiptir. Bu nedenle, birçok şirket yüksek kaliteyi korurken üretim maliyetlerini düşürmek amacıyla Çin'den özel çinko döküm hizmetleri almaktadır.
Çinli üreticiler ölçekte hassas parçalar üretmek için son teknoloji döküm ekipmanlarına para akıtmıştır. Ayrıca, Çin'in üretim temeli ve tedarik zinciri ağları, işletmelerin rekabetçi bir temelde hammadde ve yapı malzemeleri tedarik etmesine daha elverişlidir.
Çinli üreticilerle çinko alaşımlı basınçlı döküm, yüksek kaliteli özel çinko alaşımlı basınçlı döküm sağlamak isteyen şirketler için iyi bir fırsat sunuyor. Üretim süreçlerini basitleştirmek isteyen şirketler için son derece faydalı bir kaynak olan Çin basınçlı döküm hizmetleri, büyük hacimli parçaları hızlı ve makul fiyatlı bir şekilde üretebilmektedir.
Çinko döküm malzemeleri.
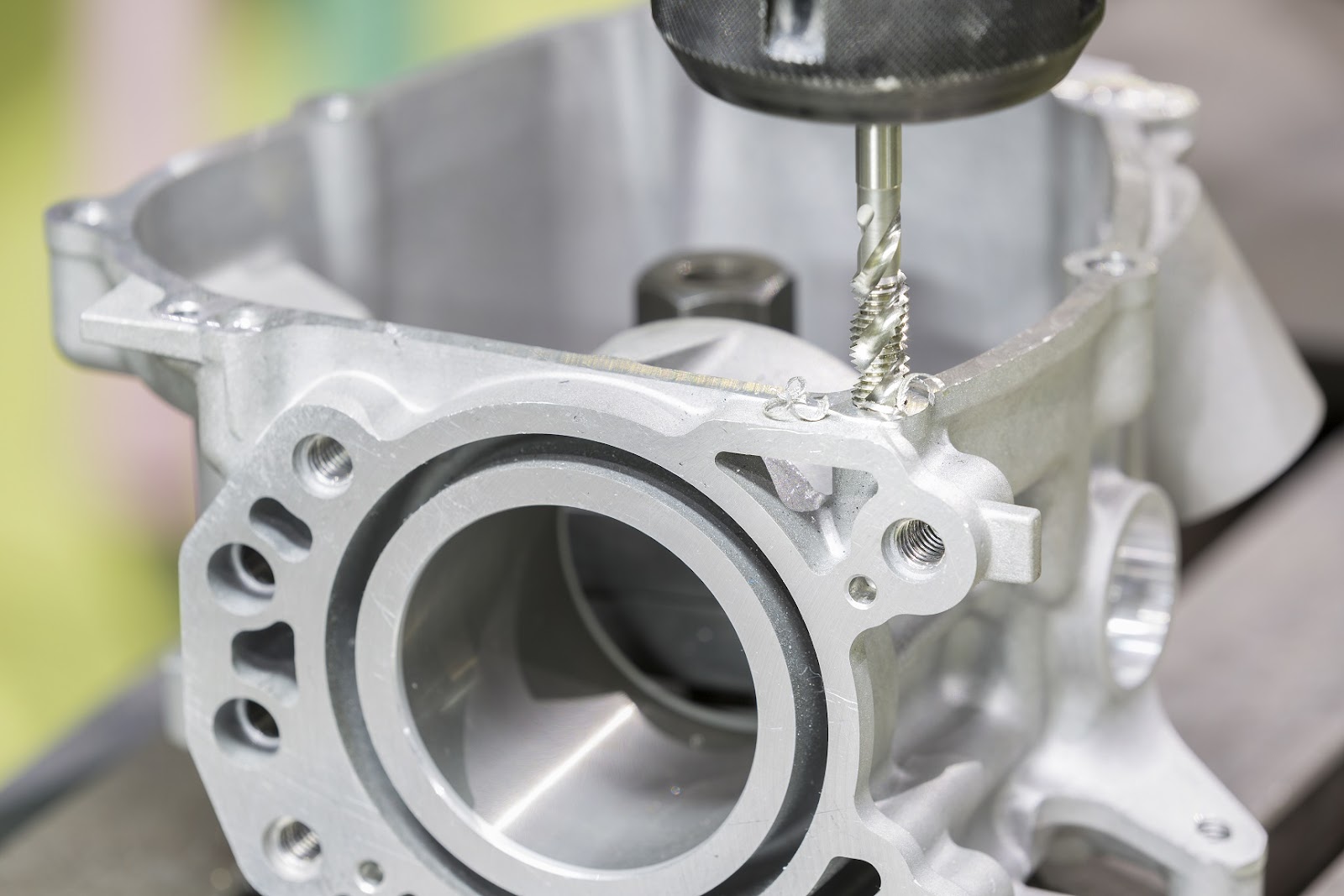
Çinko basınçlı döküm, çok yönlülüğü, dayanıklılığı ve maliyet etkinliği nedeniyle yüksek hassasiyetli bileşenlerin üretiminde kullanılan cazip bir yöntemdir. Döküm sürecindeki malzeme, bu yöntemin başarısına katkıda bulunan kilit unsurlardan biridir. Çinko basınçlı döküm, alaşımların mukavemet, korozyona karşı direnç ve akışkanlık gibi özellikleri nedeniyle ana malzeme kaynağı olarak çinko alaşımlarını kullanır. Bununla birlikte, çinko basınçlı dökümde yer alan ana malzemeleri öğrenelim.
1. Çinko (Zn)
Karmaşık, kompleks, detaylı parçaların üretimi, çinkonun basınçlı döküm işlemi için temel malzeme olarak kullanılmasının arkasındaki en önemli nedenlerden biridir, çünkü çinko eritildiğinde mükemmel bir akışkan olarak kabul edilir ve karmaşık kalıpları doldurma kabiliyetine sahiptir. Genel olarak, otomotiv, elektronik ve tüketici ürünleri de dahil olmak üzere çeşitli endüstriler için hassas şekilli parçalara kalıpla dökülebilen bir metaldir.
- Çinko özellikleri, basınçlı döküm için iyi bir malzeme olduğu anlamına gelir.
- İyi akışkanlığa sahiptir: Kalıpları kolayca doldurabilir ve doldurabilir, bu nedenle karmaşık kalıplarda kullanılabilir.
- Konjenital erime noktası: Çinko düşük bir sıcaklıkta (yaklaşık 419°C veya 786°F) eriyerek döküm işlemi için daha az enerji gerektirir.
- Korozyon direnci: Çinko korozyona karşı dayanıklıdır, bu da zorlu ortamlarda veya dışarıda kullanılan parçalarda kullanım için mükemmeldir.
- Mukavemet: Çinkodan elde edilen ürünün mukavemeti de özellikle diğer metallerle birleştirildiğinde güçlü ve dayanıklıdır.
2. Çinko Alaşımları
Basınçlı dökümde saf çinko kullanılır; ancak belirli özellikleri iyileştirmek için genellikle çinko alaşımları kullanılır. Basınçlı döküm için kullanılan en yaygın çinko alaşımları aşağıdaki gibidir:
A. ZA-8 (Çinko-Alüminyum Alaşımı)
Çinko alaşımı, yaklaşık 92% çinko ve 8% alüminyum (ZA8) çok yüksek bir patlama gücüne sahiptir ve metal parçaların delinmesinde ve gerilmesinde oldukça etkilidir. Daha iyi mekanik özellikleri ve iyi döküm özelliği ile yaygın olarak karakterize edilir. ZA-8 yüksek mukavemet ve sertliğe ve iyi korozyon direncine sahiptir. ZA-8 alaşımlı parçalar, otomotiv ve elektrik bileşenlerinde kullanım gibi son derece hassas uygulamalarda yaygın olarak kullanılmaktadır.
B. ZA-12 (Çinko-Alüminyum Alaşımı)
ZA-12 yaklaşık 88% çinko ve 12% alüminyum içerir. Çinkodan daha yüksek mukavemet ve sertlik sağlayan bir alaşımdır; ve büyük dökümlerde daha iyi boyutsal kararlılık sağlar. Bu alaşımın kullanıldığı ağır hizmet uygulamaları, örneğin endüstriyel makineler veya tüketici elektroniği ve donanımlarıdır.
C. ZAMAK Alaşımları (Çinko-Alüminyum-Magnezyum)
ZAMAK alaşımları, farklı alüminyum, magnezyum ve bakırdan oluşan çinko bazlı alaşımlardır. Çinko, Alüminyum, Magnezyum ve Bakırdan oluştuğu için bu alaşıma ZAMAK adı verilmiştir. ZAMAK 3, ZAMAK 5 ve ZAMAK 7 en yaygın kullanılan ZAMAK alaşımlarıdır. Bu alaşımların avantajları aşağıdaki gibidir.
ZAMAK 3 - güçlü, sert ve boyutsal olarak kararlı - en yaygın kullanılan basınçlı döküm çinko alaşımlarından biridir. Otomotiv parçaları, elektrikli bileşenler ve benzerlerinin üretimi için en iyisidir.
ZAMAK 5: Korozyon direnci ZAMAK 3'ten biraz daha iyidir ancak döküm biraz daha kötüdür; bu alaşım, denizcilik veya dış mekan bileşenleri gibi zorlu ortamlar için daha iyi bir seçimdir.
ZAMAK 7: Geliştirilmiş korozyon direnci söz konusu olduğunda, ZAMAK 7 esas olarak detaylar ve güzel yüzey için yüksek talepleri olan parçalar için basınçlı dökümde kullanılır.
D. ZL-2 (Çinko-Bakır Alaşımı)
ZL-2 olarak bilinen çinko bakır alaşımı ağırlıklı olarak çinko ve bakırdan yapılır. Mukavemet ile aşınma ve korozyon direnci arasında iyi bir uzlaşma sunar. ZL 2, makine parçaları ve bazı otomotiv parçaları gibi büyük strese dayanması gereken parçaları imal etmek için kullanılır.
3. Bakır (Cu)
Çinko dökümlerde genellikle birincil malzeme olarak bakır kullanılmaz, ancak mukavemetini ve termal iletkenliğini artırmak için çinko alaşımlarına bakır eklenir. Çinkoya eklenen 0.25% kadar küçük miktarlardaki bakır, alaşımın mekanik özelliklerini iyileştirir.
Güçlü: Çinko alaşımı doğası gereği güçlüdür ve özellikle yüksek sıcaklıklarda bakır ilavesiyle güçlendirilir.
Aşınma Direnci: Alaşımın aşınma direnci bakır ile arttırılmıştır.
Korozyon Direnci: Bakır ilavesi, özellikle denizcilik gibi zorlu ortamlarda çinko alaşımının korozyon direnci özelliklerini artırır.
4. Alüminyum (Al)
- Çinko alaşımlarındaki bir diğer yaygın element, örneğin ZA-8 ve ZAMAK alaşımlarında olduğu gibi alüminyumdur. Ayrıca çinkoya alüminyum ekleyerek birkaç önemli özelliği geliştirir.
- Mukavemet: Alaşımın gerilme mukavemeti alüminyumun varlığıyla artar, bu da alaşımı ağır iş uygulamaları için kullanışlı hale getirir.
- Boyutsal stabilite - boyutsal stabilite değerlerini koruyan alüminyum sayesinde dökümler eğilmez.
- Korozyon Direnci: Korozyon direnci açısından alüminyum, çinko alaşımının korozyon direncini artırarak onu nem veya diğer çevresel etkilere karşı daha dayanıklı hale getirir.
5. Magnezyum (Mg)
ZAMAK alaşımları, alaşımın özelliklerini bir miktar geliştirmek için magnezyum da ekler. Magnezyum aşağıdakileri geliştirir:
- Magnezyumun mukavemet avantajları vardır: alaşımın mukavemet/ağırlık oranını ağırlık oranına göre artırır, bu nedenle hafif parçalar için önerilir.
- Magnezyum Metal, alaşımın sünek olmasına yardımcı olur, böylece kırılmadan strese ve deformasyona dayanmasını sağlar.
- Magnezyum, deniz veya dış mekan uygulamalarında kullanım için tercih edilen alaşımın korozyon direncini artırır.
6. Diğer Katkı Maddeleri ve Alaşım Elementleri
Uygulamanın ihtiyaçlarına bağlı olarak bazı küçük miktarlarda diğer metaller ve elementler bazı çinko döküm alaşımlarına dahil edilebilir. Bu elementlerden bazıları şunlardır:
- Kurşun (Pb): Bazen işlenebilirliği artırmak için çinko alaşımlarında bulunur.
- Kalay (Sn): Alaşımın korozyona karşı direncini ve yüksek sıcaklıklardaki mukavemetini arttırmak için eklenir.
- Mukavemeti, sertliği ve aşınma direncini artırmak için az miktarda demir eklenebilir.
Basınçlı Döküm için Neden Çinko Alaşımları Tercih Edilir?
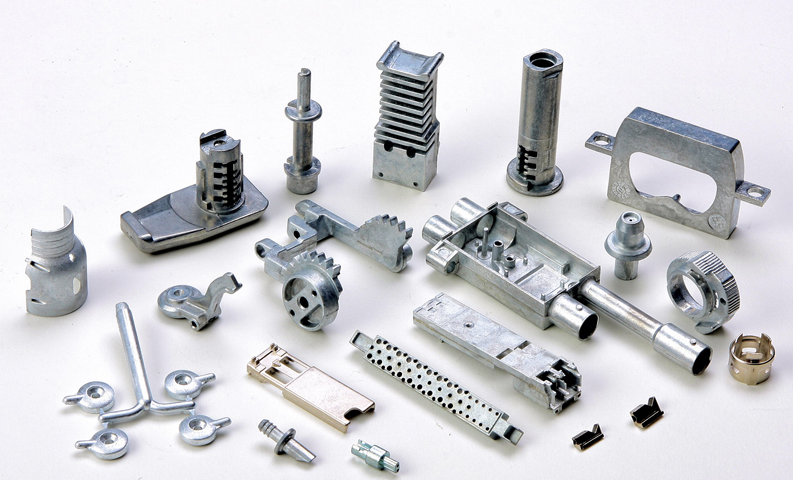
Çinkonun diğer alaşım elementleriyle kombinasyonu, tüm bu özellikler üzerinde ayrıntılı bir kontrol sağladığında bir malzeme üretilir:
- Eritildiğinde Mükemmel Akışkanlık: Çinko alaşımları yüksek döküm akışkanlığına sahiptir ve erimiş metal karmaşık kalıp boşlukları içinde kolayca akar. Bu nedenle ince detaylı ve pürüzsüz yüzeyli parçalar üretir.
- Çinko Alaşımları yüksek mukavemet ve sertliği mükemmel darbe direnciyle birleştirir, özellikle otomotiv parçalarında ve son zamanlarda tüketici elektroniğinde kullanım için idealdir.
- Çinko alaşımları genellikle diğer metallerden daha ucuz olduğu için uygun maliyetlidir ve basınçlı döküm işleminin kendisi onu çok verimli kılar.
- Çinko ve alaşımları doğal olarak korozyona dayanıklıdır; bu nedenle elementlere maruz kalan parçalar için uygundurlar.
Çinko Basınçlı Döküm Alternatifleri
Alüminyum basınçlı döküm, karmaşık parçaların oluşturulmasını kolaylaştıran hassas bir bileşen üretim sürecidir ve yalnızca birkaç kusur meydana gelebilir. Ancak bu tek çözüm değildir ve belirli bir projenin ağırlık, mukavemet, maliyet veya çevresel faktörlere olan ihtiyacına bağlı olarak başka seçenekler de mevcuttur. Açıklanan yöntemlerin her biri bir dereceye kadar yararlıdır ve bazıları belirli bir bağlamda diğerlerinden daha az etkili olabilir, bu nedenle seçenekleri tartmak son derece önemlidir.
1. Alüminyum Basınçlı Döküm
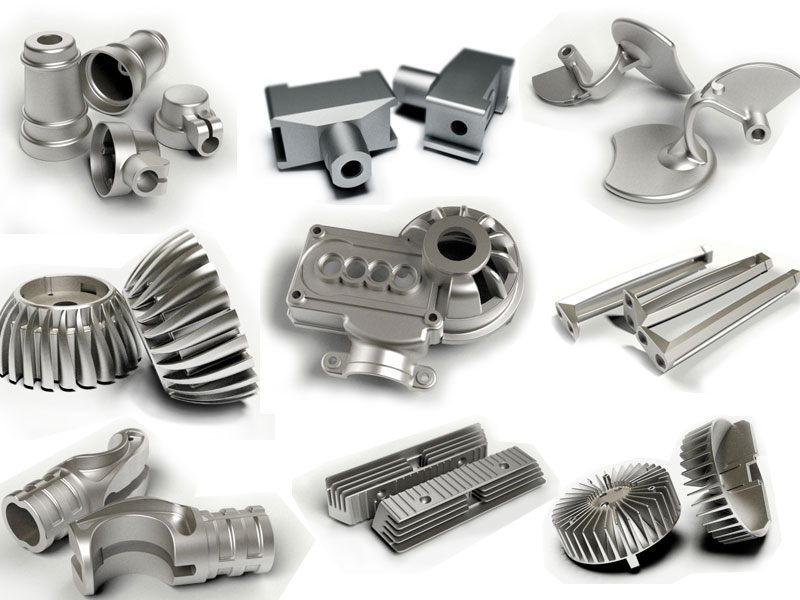
Alüminyum döküm, çinkonun yerini almak üzere üretim sürecinde kullanılan malzemeler arasındadır. Bu paslanmaz çeliğin doğası, otomobil imalat endüstrilerinde ve uçak yapımında yaygın olarak kullanılmasını sağlayan makul ağırlığın yanı sıra büyük bir güç sağlar. Alüminyum parçalar nispeten hafif olmakla birlikte yüksek mukavemete sahiptir ve yüksek sıcaklık uygulamalarına uygundur.
Ayrıca, süreç mükemmel termal ve elektriksel iletim özelliklerine sahip parçaların üretimine izin verir. Bununla birlikte, alüminyumun çinkoya kıyasla nispeten düşük akışkanlığa sahip olması, ince duvarlı karmaşık yapı için dezavantaj oluşturmaktadır. Ayrıca, alüminyum kullanımıyla ilgili kalıplama ve döküm masraflarının çinkodan biraz daha yüksek olduğu bilinmektedir.
2. Magnezyum Basınçlı Döküm
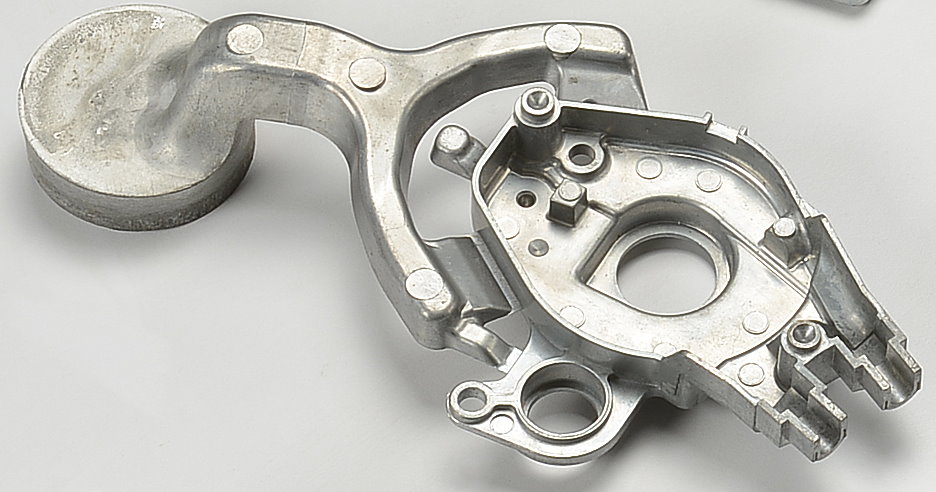
Magnezyum, piyasada bulunan basınçlı döküm amaçlı en hafif yapısal metaldir. Bu tür bir uygulama, elektronik, otomobil endüstrileri vb. gibi ürün ağırlığının azaltılmasının büyük önem taşıdığı alanlar için çok uygundur. Magnezyum iyi bir mukavemet ve sertliğe sahiptir ve bu malzemenin dökümleri çok ince duvarlı ve karmaşık şekillerde olabilir.
Öte yandan, çinkodan daha maliyetlidir ve erimiş magnezyum kolayca alev aldığından kullanımı yüksek güvenlik önlemleri gerektirir. Ayrıca östenitik çeliklere göre biraz daha düşük korozyon direncine sahiptir, bu da bazı ortamlarda kaplama tabakası eklenmeden kullanılmasını engelleyebilir.
3. Plastik Enjeksiyon Kalıplama
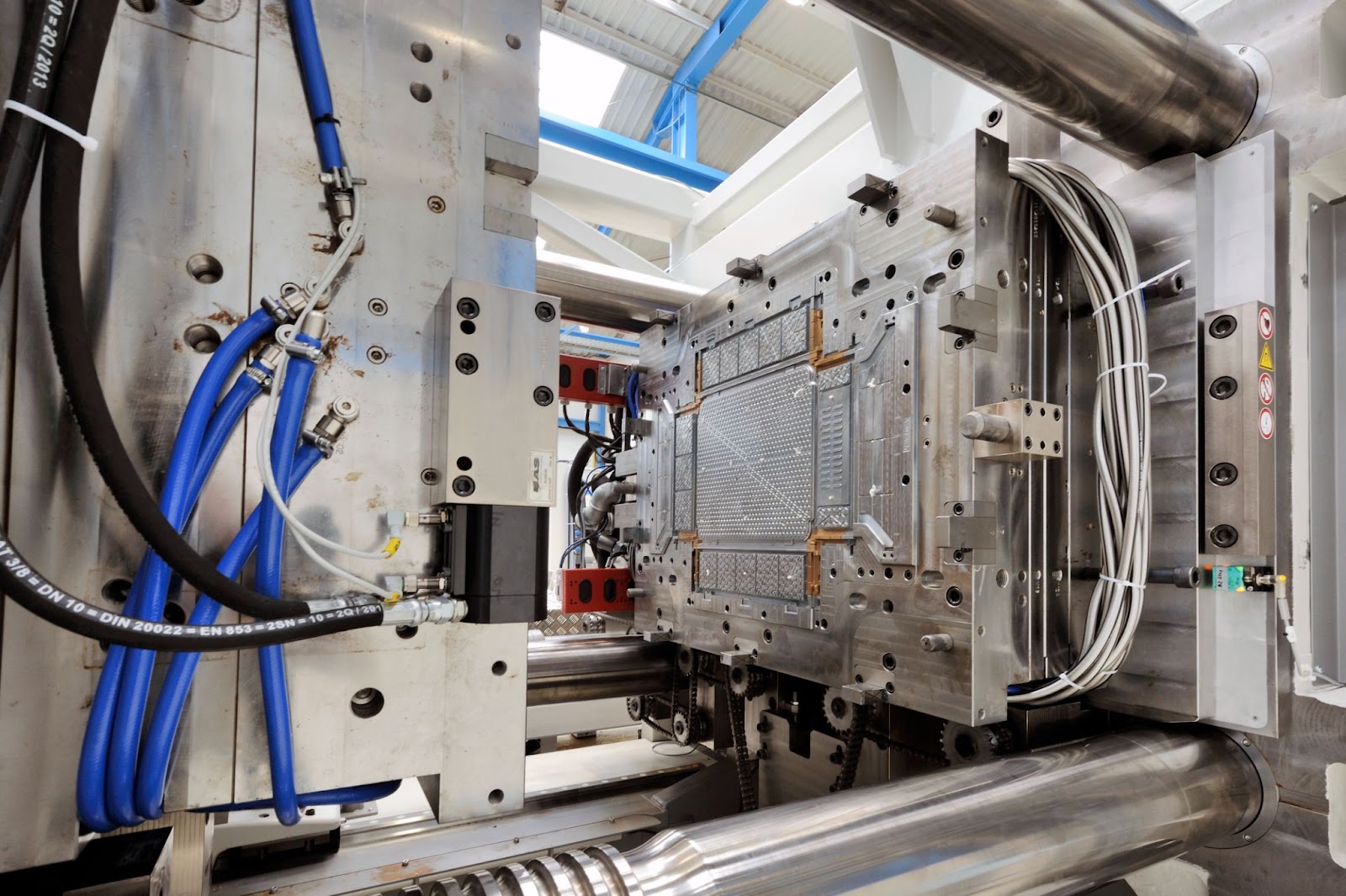
Yapısal olmayan bileşenlerin en faydalı teknolojik gelişmelerinden biri plastik enjeksiyon kalıplamadır. Polipropilen, tüketim malları, ilaç cihazları ve elektrik muhafazaları gibi projelerde yaygın olarak uygulanmaktadır.
Bu teknoloji sayesinde, renk spektrumunun en iyisi, ince ürünler ve hızlı döngü süresi elde edildi. Ancak, metaller kadar güçlü değillerdi ve sıcaklık değişimlerine de dayanıklı değillerdi. Bununla birlikte, daha dayanıklı olması, ısıya dayanıklı olması veya yükleri kaldırabilmesi gereken uygulamalar için metal döküm daha iyi olacaktır.
4. Çelik veya Demir Döküm
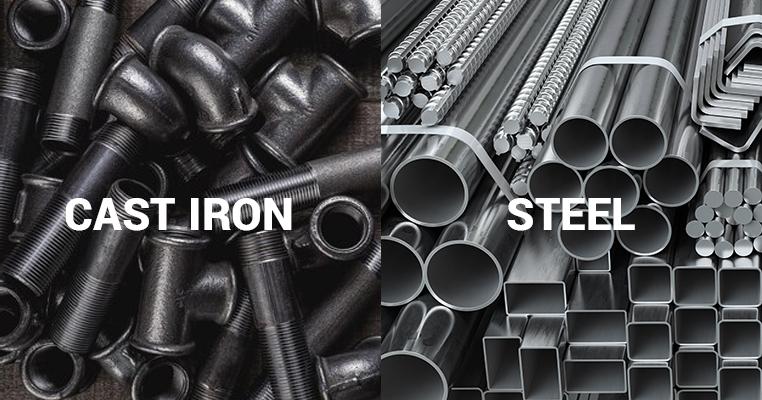
Aşırı güç ve dayanıklılık kişinin ödün verebileceği şeyler olmadığında, çelik ve demir döküm dikkate alınması gereken en iyi malzemeler arasındadır. Bu tür malzemeler, makineler, aletler veya yapılar gibi yoğun aşınma ve yıpranmaya maruz kalacakları durumlarda kullanım için uygundur.
Genel olarak, çelik ve demir dökümler yüksek gerilme, aşınma ve termal direnç kapasitelerine sahiptir. Yine de, çinko veya alüminyumdan çok daha yoğundurlar ve daha yüksek erime noktasına sahip olmaları nedeniyle döküm sadece enerji tüketmekle kalmaz, aynı zamanda maliyetlidir. Bu nedenle, bu metallerin hem işlenmesi hem de taşınması diğer türlere kıyasla daha karmaşık hale gelmektedir.
5. 3D Baskı (Metal Katmanlı Üretim)
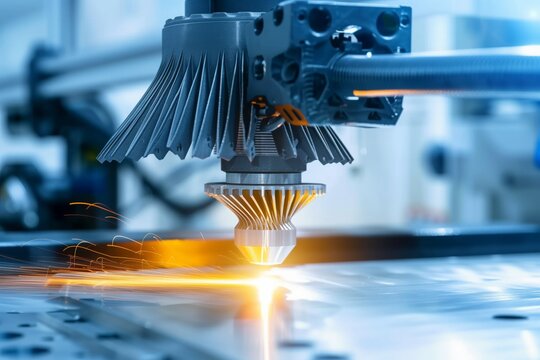
Katmanlı üretim olarak da bilinen Metal 3D, düşük hacimli ancak karmaşık küçük parçaların üretimi dünyasını yeniden şekillendiren yeni çağ üretim teknolojilerinden biridir. Artık döküm yoluyla üretmenin pahalı ve zaman alıcı olacağı özel bileşenlerin veya prototiplerin gerekli olduğu birçok sektör için büyük bir fırsat olarak kullanılıyor.
Ayrıca parçaları üretmek için kalıp kullanılmasını gerektirmez, bu nedenle hızlıdır ve tasarım çeşitliliği sunar. Bununla birlikte, parça başına maliyet çok daha yüksektir ve genel olarak teknoloji, kullanılan malzeme yelpazesi açısından henüz maksimum ilerleme oranlarına ulaşmamıştır. Son ayarlamaların işlem sonrası yapılması için genellikle bazı değişikliklere ihtiyaç duyulmaktadır.
6. Yatırım Döküm
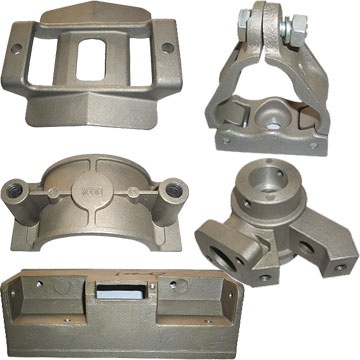
Hassas döküm veya kayıp mum dökümü, hassas ürün ve ince yüzey kalitesi sağlayan bir tekniktir. Paslanmaz çelik, titanyum ve bronz gibi çeşitli metal türlerinden karmaşık parçalar geliştirmek için idealdir.
Bununla birlikte, geometriler ve çok ince detaylar üretebilir ve bu, basınçlı dökümden daha yavaş ve daha maliyetli olma dezavantajına sahiptir. En çok yüzey kalitesi ve yüksek doğrulukta parça üretimi gerektiren küçük ölçekli üretim için uygundur.
Doğru Alternatifin Seçilmesi
Çinko döküm için uygun yedek parçanın seçilmesinde uygulama, maliyet, malzeme özellikleri ve kapasite gibi bazı faktörlerin göz önünde bulundurulması tavsiye edilir. Küçük boyutlu parçalar için alüminyum veya magnezyum kullanılması tavsiye edilebilir. Çok sayıda plastik parça olması durumunda, enjeksiyon kalıplama etkili bir mod olabilir. Ayrıca, döküm parça için mukavemet kilit faktör haline geldiğinde, çelik veya yatırım seçeneği kullanılabilir.
Böyle bir anlayış, üreticinin performans özellikleri, maliyet ve üretim kolaylığı açısından en uygun süreci seçmesini sağlar.
Sonuç
Son olarak, özel çinko dökümün hassasiyet, dayanıklılık, maliyet etkinliği ve tasarım esnekliği ile çok değerli bir süreç olduğu sonucuna varılmıştır. Bu yöntem kullanılarak, yüksek kaliteli bileşenlere sahip işletmeler, tarifelerin kısıtlanmasıyla geliştirilebilir ve bu da üretim maliyetini düşük tutar. Çin'in özel çinko alaşımlı basınçlı döküm hizmetleri, gelişmiş basınçlı döküm teknolojisini kullanmak isteyebilecek işletmeler için daha da yüksek olanaklara katkıda bulunur.
Özel çinko döküm, otomotiv, elektronik ve endüstriyel sektörlerde parça üretimi için en yüksek kalite standartlarını karşılayan bir parça üretiyor olsanız da çok yönlü ve güvenilir bir çözümdür. Teknoloji hala gelişmekte olduğundan, çinko basınçlı döküm teknolojisi sadece daha da yükselecek, temel klanger olarak sadece modern üretimde etkili olacaktır.
Sıkça Sorulan Sorular (SSS)
1. Özel çinko döküm ve nasıl çalıştığı açıklanmaktadır.
Çinko basınçlı döküm, son derece hassas özel tasarım çinko metal parçalar oluşturmak için erimiş çinko alaşımlarının yüksek basınç altında kalıp boşluğuna enjekte edildiği bir üretim sürecidir. Yüksek boyutsal doğruluk ve minimum işleme ile karmaşık şekiller üretmek için yaygın olarak kullanılır.
2. Basınçlı döküm için neden çinko alaşımları kullanmalıyım?
Çinko alaşımlarını kullanmanın bazı avantajları iyi mukavemetleri, düşük erime noktaları, daha iyi finisaj ve ince duvarlı, karmaşık parçalar üretme olasılığıdır. Ayrıca, iyi korozyon direncine sahiptirler ve yüksek üretim hacmi için çok uygun maliyetlidirler.
3. Zamak 3, ZA-8 veya AcuZinc 5 hangi çinko alaşımları projem için en iyisidir?
En iyi alaşım uygulamanıza bağlıdır.
- Zamak 3 için genel amaçlı parçalar idealdir.
- Yüksek mukavemetli ve ısıya dayanıklı uygulamalar için daha uygun olan ZA-8'dir.
- AcuZinc 5, süneklik ve tokluk gerektiğinde tercih edilen malzemedir.
- Alaşımı tedarikçinizle birlikte özel ihtiyaçlarınıza göre eşleştirin.
4. Çin'den kaliteli çinko döküm bulmak mümkün mü?
Evet. Çin'in birçok özel çinko alaşımlı döküm üreticisi düşük fiyatlar, en son ekipman ve nitelikli mühendislik desteği ile. Prototip ve özel parçaların seri üretimi için iyidirler.
5. Çinko basınçlı dökümün faydaları neler olabilir?
Hafif uygulamalar alüminyum veya magnezyum basınçlı döküm, metal olmayan parçalar için plastik enjeksiyon kalıplama, yüksek mukavemet için çelik döküm veya hassas parçalar için hassas döküm ile yapılabilir. Tasarım, güç, bütçe ve üretim hacmine göre bir seçim yapılır.