Modern üretim dünyası basınçlı döküm kalıplarla çevrili olduğundan, basınçlı döküm kalıpların hassas ve güvenilir metal bileşenlerin üretiminde kritik bir adım haline gelmesi şaşırtıcı değildir. İster otomotiv parçaları ister tüketici elektroniği olsun, amaç ürünlerin dayanıklılık, işlev ve görünüm açısından en yüksek kalite standartlarına sahip olmasıdır. Döküm kalıpçılığının türlerinden avantaj ve dezavantajlarına ve uygulamalarına kadar her bölümünü ele alan bu kapsamlı kılavuzu, üretimle tamamen ilgileniyorsanız son derece yararlı bulacaksınız.
Döküm kalıptan parça üretmenin maliyeti başlangıçta daha yüksek olsa da, diğer yandan size daha az malzeme israfı, daha hızlı üretim döngüsü süresi ve varsa çok az işlem sonrası işlemle karmaşık tasarımlar yapma yeteneği sağlar. Soğutma sistemlerindeki ilerlemeler ve yedek uçlar, yüzey kaplamaları ve benzerleri gibi daha verimli ikame parçalar verimliliği ve dayanıklılığı artırmakla kalmadı, aynı zamanda daha az aşınmış ızgaralar ve elektrik sistemi için daha iyi temizleme de yardımcı oldu.
Basınçlı Döküm Kalıplama Nedir?
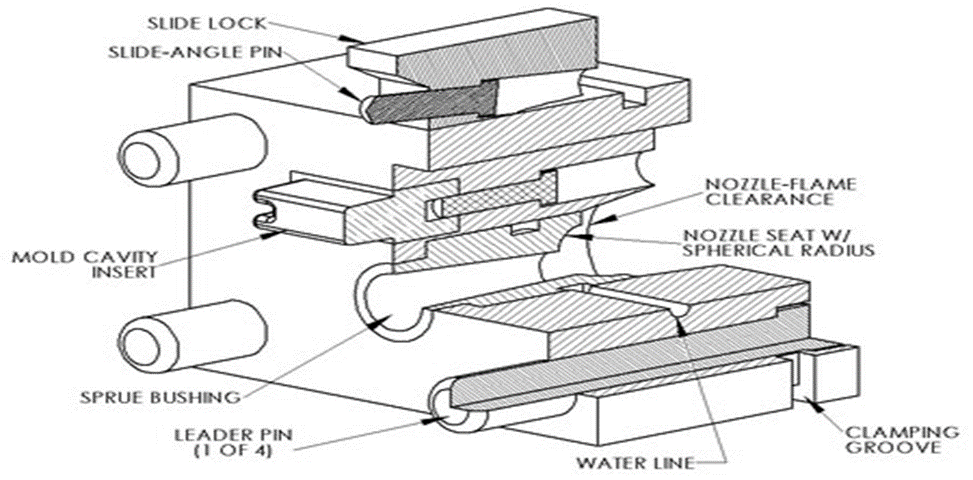
Basınçlı döküm kalıpları, basınçlı döküm kalıpları için kullanılan araçlar ve süreçler anlamına gelir. Bu kalıplar aynı zamanda erimiş metali yüksek basınç altında karmaşık ve hassas bileşenlere dönüştürür. Gelişmiş basınçlı döküm kalıplarının mühendisliği, malzeme ve titiz tasarım uygulamalarının yanı sıra tutarlı bir şekilde üretilen hatasız parçaların üretimini kolaylaştırmak için ileri mühendislik becerileri gerektirir.
İlk olarak, metal (genellikle alüminyum, çinko veya magnezyum) eritilir ve yüksek basınç altında kalıba geçirilir. Nihai ürünün kalitesi kalıpların hassasiyetine bağlıdır ve bu nedenle döküm kalıpları endüstriyel üretim için hayati önem taşır.
Basınçlı Döküm Kalıp Bileşenleri
Basınçlı döküm süreci, yüksek kaliteli metal parçalar üretmek için gereken bir dizi alete büyük ölçüde dayanan hassas bir üretim sürecidir. Bu aletlerin kombinasyonu doğru, dayanıklı ve verimli olacak şekildedir. Basınçlı dökümde kullanılan en yaygın aletler aşağıda listelenmiştir.
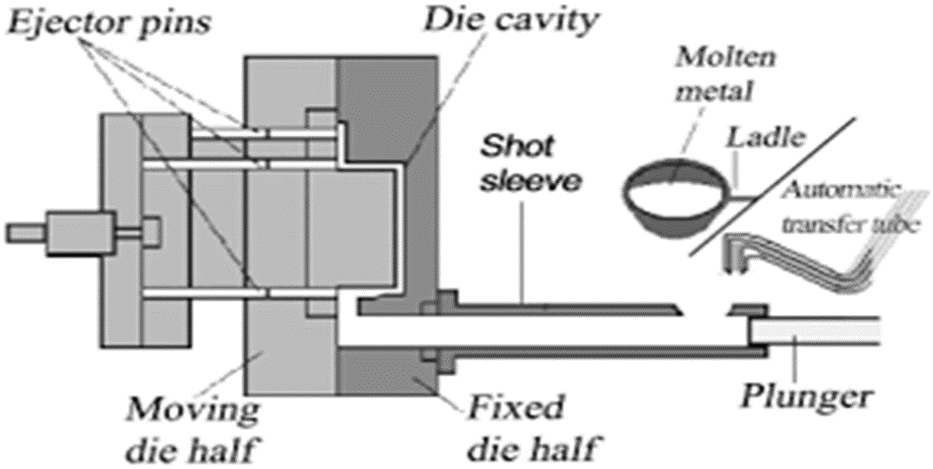
1. Kalıplar (Molds)
Süreçteki en kritik araç, kalıp olarak da adlandırılan kalıptır. İki yarıdan oluşur:
- Kapak kalıbı; sabit kalır ve enjeksiyon sistemine hizalanır.
- Eğer bir ejektör kalıbı ise, katılaşmış dökümü serbest bırakmak için hareket eder. Aşırı basınçlara ve yüksek sıcaklıklara dayanacak kalıplar yapmak için sertleştirilmiş çelik kullanılır. Hangi boyutları inşa edeceklerini, nihai ürünün karmaşıklığını ve ne kadar hassas olacağını belirlerler.
2. Boşluk Uçları
Kalıbın iç şekli, karmaşık olanları oluşturmak için boşluk ekleri tarafından oluşturulur. Bu nedenle, bu uçlar değiştirilebilir ve yeni bir takım imal etmek zorunda kalmadan farklı bileşenler için kalıbın değiştirilmesini kolaylaştırır.
3. Çekirdek Pimleri
İç delikler, yuvalar veya karmaşık girintiler üretmek için bir göbek pimi ile bir iç özellik oluşturulur. Bitmiş ürünü veya ürünü mümkün olan en iyi kalitede elde etmek için bunlar gereklidir.
4. İtici Pimler
Tamamlanan döküm, ejektör pimleri ile zarar görmeden kalıp boşluğundan çıkarılır. Bu pimler, pürüzsüz ve kolay parça çıkarma için verilen fırlatma sistemi için kullanılır.
5. Soğutma Kanalları
Kalıp, döküm sırasında ilgili sıcaklığın ayarlanmasını sağlamak için soğutma kanalları içerir. Düzgün soğutma eğilme, çatlama veya büzülme gibi kusurları önlediğinden, aynı zamanda sabit kalite sağlar.
6. Havalandırma Delikleri ve Taşma Kuyuları
Erimiş metal kalıba enjekte edildiğinde sıkışan hava deliklerden serbest bırakılır ve fazla malzemeyi toplamak için taşma kuyuları kullanılır. Nihai üründe boşluk veya hava cepleri bulunmaz ve her iki alet de bunu sağlar.
7. Trim Kalıpları
Trim kalıpları, dökümlerdeki fazla malzemeyi, yani parlamayı gidermek için kullanılan özel aletlerdir. Nihai ürün için temiz kenarlar ve doğru boyutlar garanti edilir çünkü bunu vaat ederler.
8. Yağlama Sistemleri
Kalıp, aşınmayı en aza indirmek, sürtünmeyi azaltmak ve ayrıca parçanın çıkarılmasını kolaylaştırmak için bazı sulu yağlayıcılarla yağlanır. Uygun biçimde yağlama, kalıp ömrünü uzatır, kalıbın kapanmasını önler ve sorunsuz döküm işlemleri sağlar.
9. Atış Kolları
Enjeksiyon sisteminin kılavuzları, erimiş metali kalıp boşluğuna yönlendiren atış manşonlarıdır. Aşırı ısı ve basınçla başa çıkacak şekilde tasarlanmaları, metal akışını yumuşatmak için çalıştıkları anlamına gelir.
10. Püskürtücüler
Erimiş metalin kalıba yapışmasını önlemek ve parçanın çıkarılmasını kolaylaştırmak için püskürtücüler kullanılarak kalıp içine ayırıcı maddeler kaplanır.
Diğer bir deyişle, bu araçlar otomotiv, havacılık, elektronik vb. endüstriler için vazgeçilmez olan tutarlı, yüksek kaliteli ve hatasız parçalar sunmak için birlikte çalışır.
Basınçlı Döküm Kalıp Çeşitleri
Basınçlı döküm kalıplar arasında tek beden herkese uymaz. Üretim gereksinimlerine bağlı olarak çeşitli kalıp türleri tasarlanır.
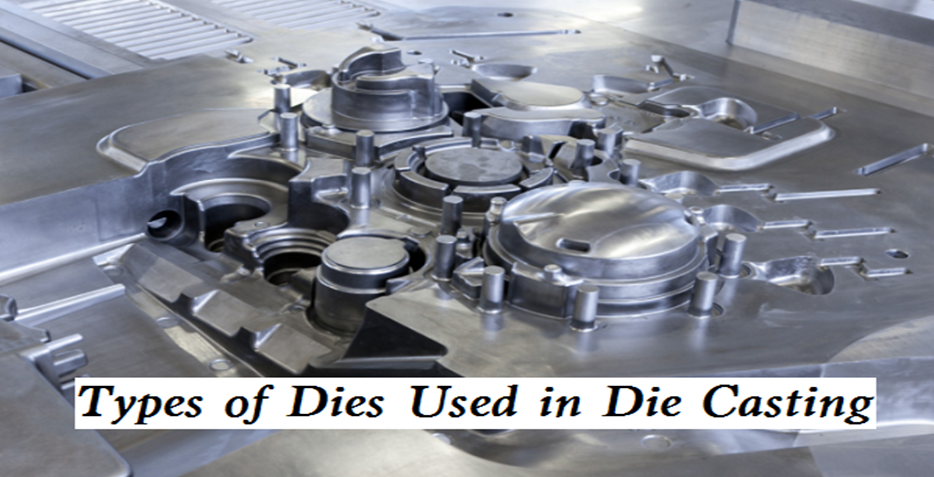
Tek Boşluklu Takımlama: Bu tip takımlar döngü başına bir parça üretir. Düşük hacimli bir üretim veya prototipleme sistemi uygun olacaktır.
Çok Kaviteli Takımlar: Çok oyuklu takımlar, üretim verimliliğini artıran birden fazla özdeş parçanın aynı anda üretilmesini sağlar. Yüksek hacimli üretim için çok yaygın olarak kullanılır.
Aile Takımları: Tüm takımlama yöntemi yenilikçidir, tek bir döngüde birçok farklı parça üretir. Özellikle birlikte üretilecek bileşenlerin montajı için uygundur.
Birim Kalıplama: Modüler birim kalıplar, tüm kalıbı yeniden çizmeden kesici uç tiplerini veya kalıp kısımlarını değiştirebilir. Bu da maliyetleri ve duruş sürelerini azaltır.
Süs Kalıpları: Bitmiş parçadaki fazla malzemeden (flaş) kurtulmak için kullanılırlar ve bitmiş parçanın tam spesifikasyonları karşıladığından emin olurlar.
Döküm Kalıplamanın Faydaları

Günümüzde basınçlı döküm kalıplar birçok avantajı nedeniyle vazgeçilmezdir:
Hassasiyet ve Doğruluk: Yüksek boyutsal doğruluk elbette basınçlı döküm, nispeten dar toleranslara sahip parça üretimi ve karmaşık tasarımlarla elde edilir.
Dayanıklılık: Bu aletler sert çelikten üretilmiştir ve yüksek basınçlı dökümün ve artan kullanımın zorluklarına dayanabilecek kapasitededir.
Verimlilik: Süreç, çok fazla hurda olmadan aynı parçaları üretmek için hızlı ve ekonomik bir yol sağlar ve bu nedenle büyük ölçekli üretim için ekonomiktir.
Tasarım Esnekliği: Basınçlı döküm kalıplarda, diğer imalat yöntemlerinde mümkün olmayan karmaşık şekiller, ince duvarlar ve karmaşık detaylar vardır.
Malzeme Tasarrufu: Minimum atık ve hurdaya olanak tanıyan ve daha sürdürülebilir bir üretim süreci sağlayan takımlar benzersizdir.
Yüzey İşlemi: En yaygın olarak, döküm parçalar, işlem sonrası çok az işlem gerektiren veya hiç gerektirmeyen ve zamandan tasarruf sağlayan nispeten pürüzsüz yüzeylere sahiptir.
Basınçlı Döküm Kalıplamada Karşılaşılan Zorluklar
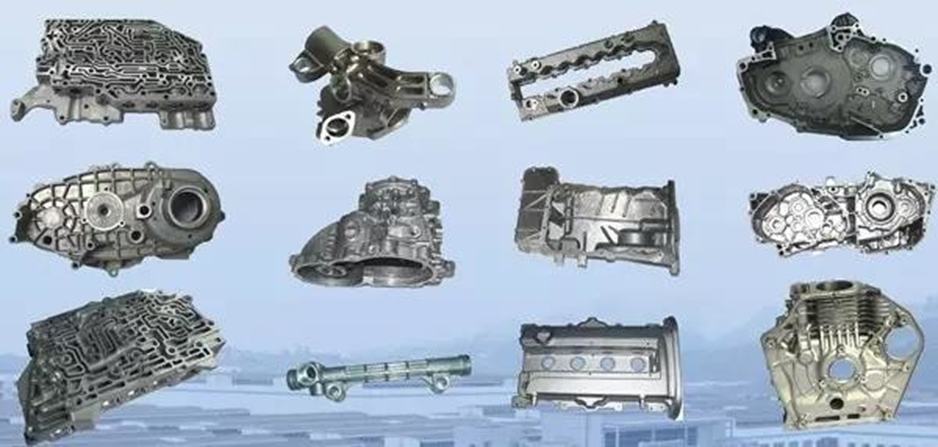
Döküm kalıplamanın avantajları olmasına rağmen, döküm kalıplamanın zorlukları çoktur:
1. Yüksek Başlangıç Maliyetleri
Kalıp imalatı ve tasarımı maliyetli olabilir (bu ölçeğe bağlı olsa da) ve küçük ölçekli üreticiler için kalıplar için büyük sermaye yatırımı gerekir.
2. Bakım Gereklilikleri
Aletlerin ve ürünün kalitesini korumak için düzenli olarak bakım yapılması gerekir. Bakım yapılmaması üretimde kusurlara ve gecikmelere yol açacaktır.
3. Tasarım Sınırlamaları
Acil durum tasarımı bazı durumlarda önemli, hatta kritiktir. Son derece karmaşık tasarımlar, üretim maliyetlerinin karmaşıklığını artıran gelişmiş teknikler veya çok adımlı süreçler de gerektirebilir.
4. Termal Yorgunluk
Tekrarlanan yüksek sıcaklıklar kalıbı yıpratabilir ve yıpranmış kalıp zamanla çatlar veya deforme olur.
Basınçlı Döküm Kalıp Tasarımında Dikkate Alınması Gereken Faktörler
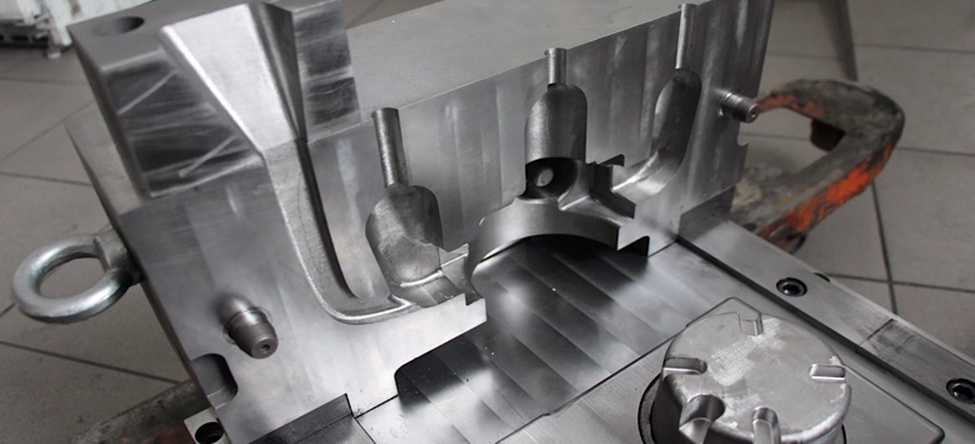
Aşağıda, verimli ve güvenilir basınçlı döküm kalıplarının oluşturulmasında yer alan faktörlerin ayrıntılı planlaması ve değerlendirilmesi sunulmaktadır.
1. Malzeme Seçimi
Kalıp tasarımı metal seçimine dayanır. Yaygın olarak hafiflik, mukavemet ve korozyon direnci özelliklerine sahip alüminyum, çinko ve magnezyum kullanılır.
2. Termal Yönetim
Öte yandan, dökümde kusurlara yol açabilecek aşırı ısınmayı önlemek için uygun soğutma sistemleri gereklidir.
3. Alet Uzun Ömürlülüğü
Kalıbı oluştururken daha kaliteli malzemeler seçmek, ömrünü uzatacak ve değiştirme sıklığını azaltacaktır.
4. Maliyet Verimliliği
İlk takım maliyetleri yüksektir, ancak büyük hacimli üretimler için birim bazında çok düşüktür.
5. Ürün Karmaşıklığı
Parça tasarımı ne kadar karmaşıksa, takımlama da o kadar karmaşıktır. İkinci bir etki de teslim süresi ve maliyet üzerinde olabilir.
Basınçlı Döküm Kalıplama Uygulamaları
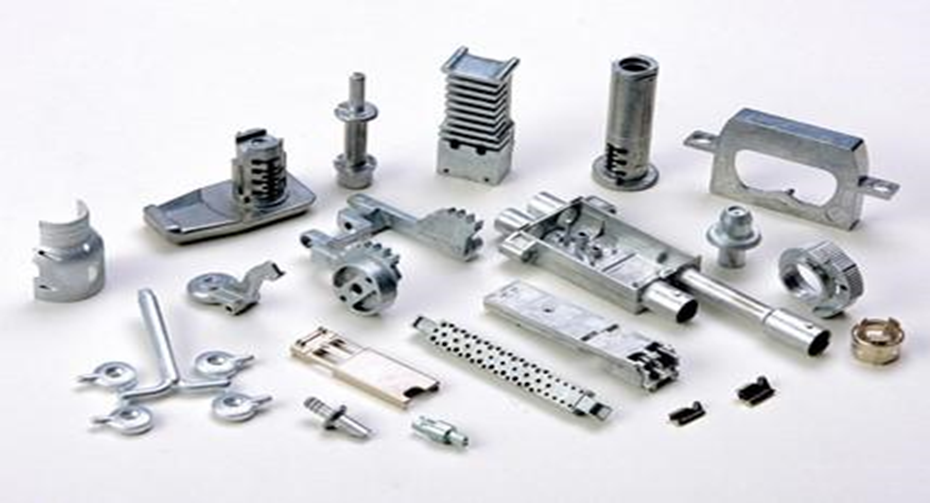
Bununla birlikte, basınçlı döküm kalıplama, birçok endüstride karmaşık ve yüksek kaliteli metal parçaların üretimi için kritik bir uygulamadır. Dayanıklı, hafif ve hassas parçalar üretme kabiliyeti nedeniyle çok çeşitli uygulamalar için vazgeçilmezdir. Basınçlı döküm kalıpları yoğun olarak kullanan başlıca sektörlerden bazıları şunlardır:
1. Otomotiv
Otomotiv sektöründe, basınçlı döküm kalıpları çok önemlidir. Çok sıkı hassasiyet, tokluk ve mukavemet standartlarına göre dökülmesi gereken motor blokları, şanzıman kutuları, braketler, direksiyon bileşenleri vb. gibi basınçlı döküm bileşenler kullanılır. Elbette bu süreç, modern araçlarda daha fazla yakıt verimliliği için önemli olan hafif parçaların üretilmesi için de faydalıdır.
2. Tüketici Elektroniği
Elektronik üretiminde basınçlı döküm, akıllı telefonların çerçevelerini, dizüstü bilgisayarların kasalarını, konektörleri ve ısı alıcılarını üretmek için yaygın olarak kullanılmaktadır. Parçalar hafif ve güçlü olduğu için sürecin karmaşık tasarımlar yapma kabiliyeti de bu parçalara fayda sağlar.
3. Havacılık ve Uzay
Gövdeler, braketler ve yapısal parçalar gibi bileşenlerin hafif ancak sağlam bileşenler yapmak için kullanıldığı havacılıkta basınçlı döküm kalıp uygulamaları mevcuttur. Bu modern endüstri için, bu bileşenler sıkı performans ve güvenlik gereksinimlerini karşılamalıdır ve bu, basınçlı dökümün ihtiyaç duyduğu şeyi verdiği yerdir.
4. Endüstriyel Ekipmanlar
Endüstriyel Makine Parçaları için Basınçlı Döküm Pompalar, Dişliler, Vanalar ve Muhafazalar sunuyoruz. Basınçlı döküm, bu tür bileşenlerin sıkı çalışma standartlarını karşılamasını garanti eder.
5. Tıbbi Cihazlar
Tıbbi alanda kalıp dökümler, görüntüleme cihazları, teşhis araçları ve cerrahi aletler gibi cihazlar için güvenilir ve hassas parçalar yapmak için çok önemlidir. Bu cihazların sıkı toleranslara sahip olacak şekilde üretilebilmesi son derece önemlidir, çünkü bunlar parçanın güvenliği ve etkinliği için çok önemlidir.
6. Yenilenebilir Enerji
Yenilenebilir enerji yaygınlaştıkça, basınçlı döküm kalıplama, hem dayanıklılık hem de verimlilik elde etmek için rüzgar türbinleri, güneş paneli montajları veya elektrikli araçlar için bileşenler oluşturmanın bir yöntemi haline geliyor.
Döküm kalıpları, bu uygulamalarda gösterildiği gibi birçok farklı sektörde inovasyonu ve üretimi desteklemektedir.
Basınçlı Döküm Kalıplamada Yenilikler
Teknolojideki gelişmeler basınçlı döküm kalıpçılığını dönüştürüyor: süreç daha mümkün, verimli ve hassas hale geliyor. Bu da israfı azaltarak, kaliteyi artırarak ve kalıpların kullanım ömrünü uzatarak sektörü dönüştürüyor. KAYDA DEĞER GELIŞMELERDEN BAZILARI AŞAĞIDA YAZILMIŞTIR:
Katmanlı Üretim: Katmanlı üretim veya 3D baskı nedeniyle döküm kalıplarının yapacağı çok şey var. Dizinler, üreticilerin tasarımları hızlı ve düşük maliyetle test etmek ve iyileştirmek için kullandıkları prototip takımları oluşturmak için kullanılıyor. Geliştirme döngüsünü hızlandırıyor ve büyük üretimde meydana gelen hata riskini azaltıyor. 3D baskı ayrıca geleneksel üretim teknikleri kullanılarak yapılamayan karmaşık geometrilerin üretilmesini de mümkün kılıyor.
Gelişmiş Kaplamalar: Döküm Kalıp döküm ürünlerinde daha iyi aşınma direnci, termal stabilite ve yüzey sertliği ihtiyacı nedeniyle takımlar, Fiziksel Buhar Biriktirme (PVD) ve nitrürleme gibi yüzey kaplamalarına tabi tutulmaktadır. Bu kaplamaların eklenmesi, kalıpların yüksek basınçlı dökümün zorlu koşullarından korunmasına yardımcı olur, böylece her bir kalıbın ömrünü uzatır ve bakım maliyetlerini azaltır. Kaplamalar ayrıca sürtünmeyi azaltarak ve erimiş metalin kalıba yapışmasını önleyerek nihai ürün kalitesini de artırır.
Simülasyon Yazılımı: Mühendisler, herhangi bir üretim başlamadan önce kalıpları en iyi şekilde tasarlamak için gelişmiş simülasyon araçları kullanıyor. Sonuç olarak bu araçlar erimiş metalin akışını, soğutma hızlarını ve olası kusurları simüle ederek üreticilerin kusurları tasarım aşamasında ortaya çıkmadan önce bulmasını ve düzeltmesini sağlıyor. Bunu başarıyor: Deneme-yanılma azalıyor, teslim süreleri kısalıyor ve üretimde başarı artıyor.
Otomatik Sistemler: Basınçlı döküm prosesi, otomasyon ve gelişmiş verimlilik ve tutarlılığın getirdiği bir değişim geçiriyor. Erimiş metal enjekte edilirken, parçalar işlenirken ve bitmiş bileşenler denetlenirken robotik sistemler kullanılmaktadır. Otomatik sistemler insan hatalarını ortadan kaldırmakta, daha yüksek üretim hızı sağlamakta ve tüm partileri aynı kalitede üretmektedir.
Akıllı İzleme ve IoT Entegrasyonu: Nesnelerin İnterneti (IoT) teknolojisinin entegrasyonu, döküm kalıplarının gerçek zamanlı olarak izlenmesini sağlayacaktır. Takımlara yerleştirilen sıcaklık, basınç ve aşınma sensörleri, verileri kestirimci bakıma besler ve bakımın genel verimliliğini artırır.
Uzun süre göz ardı edilemeyecek bir sektör olmaya devam eden basınçlı döküm endüstrisinin giderek daha hassas, sürdürülebilir ve esnek hale gelmesine yardımcı oluyorlar.
Basınçlı Döküm Kalıplamada Gelecek Trendler

Döküm kalıpları, endüstriler daha rekabetçi hale geldikçe daha hafif, daha güçlü ve daha sürdürülebilir yeni ürün taleplerini karşılamak için değişiyor. Gelecekteki bazı trendler şunlardır:
1. Sürdürülebilirlik Odağı
Çevre dostu uygulamaların benimsenmesi, atıkların azaltılması ve basınçlı dökümde enerji tüketiminin azaltılmasına yönelik çabalarla teşvik edilmektedir.
2. Hafif Malzemeler
Magnezyum ve diğer hafif alaşımlar otomotiv ve havacılık endüstrilerinde giderek daha fazla kullanılmaktadır.
3. Dijital İkiz Teknolojisi
Takım sistemlerinin dijital ikizleri aracılığıyla gerçek zamanlı izleme ve kestirimci bakım sağlanabilir ve takım sistemlerinin verimliliğinde daha fazla artış ve arıza sürelerinde azalma elde edilebilir.
Sonuç
Modern üretim ortamında, döküm kalıpları yüksek kaliteli metal parçaların doğruluk ve tutarlılıkla üretilmesi için kullanılan zorunlu bir parçadır. Ancak çok sıkı toleranslara ve karmaşık geometrilere sahip parçalar üretmek için bir araya gelen kalıplar, boşluk ekleri, maça pimleri ve fırlatma sistemleri kullanan çok karmaşık bir zincirdir. Dayanıklı ve hafif bileşenlerin üretilmesini sağladığı için otomotiv, havacılık ve elektronik endüstrilerinde yaygın olarak kullanılmaktadır. Daha önce bahsedilen sertleştirilmiş çelik malzemeden yapılmış olgun, yüksek kaliteli kalıp döküm takımları, aşırı sıcaklıklar ve basınçlar altında uzun ömürlü iyi bir performans elde edebileceğiniz anlamına gelir. Değiştirilebilir kesici uçlar, gelişmiş soğutma sistemleri, PVD kaplamalar ve yukarıdakileri sağlayan yenilikler, atıkları en aza indirirken ve dayanıklılıklarını artırırken takımlama verimliliğini geliştirmiştir. Takımlama için büyük bir başlangıç yatırımı gerektirse de, daha hızlı üretim döngüleri, daha az kusur ve yüksek hacimde daha düşük üretim maliyeti sağlar.
Basınçlı döküm kalıpları her ne kadar gönülsüzler için olmasa da, hassas üretimin ayrılmaz bir parçasıdır, bakım ve yüksek maliyetleri vardır. Teknolojinin artan varlığı sayesinde, 3D baskılı prototipler ve dijital ikiz sistemleri kesinlikle süreci daha da verimli ve esnek hale getirecektir. Özetle, basınçlı döküm kalıpları, endüstrilerin mevcut üretim gereksinimlerini doğruluk ve hızla karşılamasını sağlamak için dayanıklı, ayrıntılı bileşenler oluşturmak açısından kritik öneme sahiptir.
Sıkça Sorulan Sorular: Basınçlı Döküm Kalıplama Hakkında
1. Döküm kalıplama nedir?
Basınçlı döküm işlemi, erimiş metali istenen bileşenlere şekillendirmek için kalıplar, kalıp (kalıplar) ve çeşitli boşluk ekleri, göbek pimleri ve fırlatma sistemleri olarak adlandırılan özel aletler içerir; basınçlı döküm takımları bu özel aletler olarak adlandırılır. Bunlar, imalatta yüksek kaliteli, tutarlı sonuçlar elde etmenin çok önemli bir parçasıdır.
2. Basınçlı döküm kalıplarında hangi çelikler kullanılır?
Basınçlı döküm kalıpları bu kadar yüksek basınç ve aşırı sıcaklıklarda çalıştığından, basınçlı döküm kalıpları genellikle H13 takım çeliği, 8407, H13, DIN 1.2344 vb. gibi sertleştirilmiş çelikten yapılır. Genellikle, dayanıklılığı ve aşınma direncini artırmak için yüzey kaplamalarına PVD ve nitrürleme eklenir.
3. Döküm kalıplama maliyeti nedir?
Kalıp maliyeti tasarımın çeşitli yönlerine, kalıp boyutuna ve kullanılan malzemeye bağlıdır. Parça başına maliyet önemli ölçüde daha düşüktür, ancak üretimin ilk aşamasında ilk yatırım yüksektir (örneğin, binlerce ila on binlerce dolar).
4. Döküm kalıpların kullanım ömrü ne kadardır?
Döküm kalıplarının ömrü büyük ölçüde döküm malzemesi, bakım prosedürleri ve döküm süreci gibi faktörler tarafından belirlenir. Sertleştirilmiş çelikten yapılan yüksek kaliteli kalıplar, bakımları düzgün bir şekilde yapılırsa yüz binlerce çevrime dayanabilir.