
Döküm ve basınçlı döküm, metal bileşenlerin istenen hassasiyet, dayanıklılık ve verimlilikle üretilmesi için hayati önem taşıyan iki önemli üretim sürecidir. Döküm, erimiş malzemenin bir kalıba dökülüp soğumaya ve katılaşmaya bırakılmasını içerir. Kum döküm, hassas döküm ve kalıcı kalıp dökümü bazı döküm türleridir. Bununla birlikte, basınçlı döküm, erimiş metali yüksek hassasiyet ve iyi bir yüzey kalitesi ile bir kalıp boşluğuna enjekte etmek için yüksek basınç kullanan özel bir dökümdür. Hafif, güçlü, korozyona dirençli parçalara ihtiyaç duyulan otomotiv, havacılık, elektronik ve ilgili endüstri uygulamaları için basınçlı döküm yaygın olarak kullanılmaktadır. Zaman içinde farklı varyantların basınçlı dökümü, endüstrilerin farklı ihtiyaçlarına uyacak şekilde geliştirilmiştir. Yerçekimli Basınçlı Döküm (GDC) kalıbı doldurmak için yerçekimine bağlıdır ve Düşük Basınçlı Basınçlı Döküm (LPDC) daha yüksek kalitede malzeme bütünlüğü elde etmek için türbülansı ortadan kaldırır. Sıkıştırmalı Basınçlı Döküm ile uygulanan aşırı basınç, yüksek mukavemetli, gözeneksiz parçalar yaratır ve Vakumlu Basınçlı Dökümde sıkışan hava, hatasız bir bileşen elde etmek için ortadan kaldırılır. Ayrıca, Yarı Katı Basınçlı Döküm (Reocasting), mekanik özellikleri ve hassasiyeti iyileştirmek için kısmen katılaşmış metal kullanılarak elde edilir. İmalatta genel döküm terimi, metali bir kalıba doldurarak ve katılaşmasına izin vererek şekillendirme biçimini ifade etmek için kullanılır. Bu yöntem yaygın olarak kum döküm, hassas döküm ve kalıcı kalıp dökümünde kullanılır. Basınçlı dökümde kalıp, yüksek basınçlı döküm işleminde kullanılan metal kalıp iken, basınçlı döküm işleminde kalıp, kalıp yüzeyine takılan metal kalıp anlamına gelir. Genellikle seri üretim için tasarlanmış sertleştirilmiş çelik kalıplar yapılır.
Bu makale, döküm ve basınçlı dökümün arkasındaki kavramları, bu iki kavram arasındaki farkları ve ayrıca her birinin türlerini, yukarıdakilerin olası uygulamalarını ve bu işlemle ilgili artıları ve eksileri ele alacaktır.
1. Döküm Nedir?
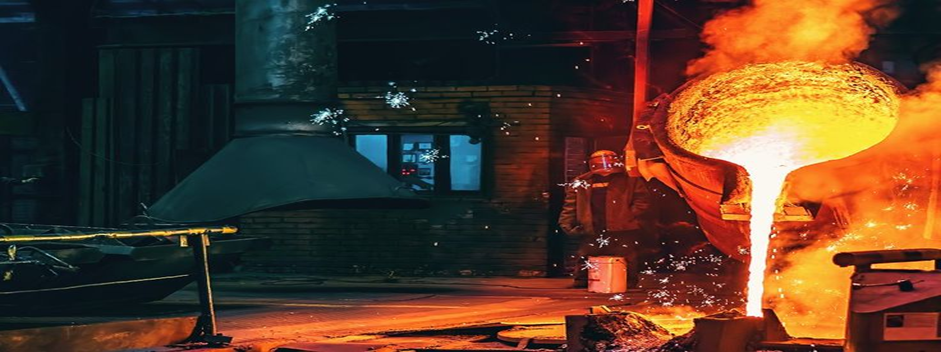
Döküm, sıvı bir malzemenin katılaştığı bir kalıba zorlandığı endüstriyel bir süreçtir. Sıvı, temel olarak herhangi bir metal veya plastik ya da diğer eritilebilir malzemeler olabilir. Sertleştikten sonra, malzeme kalıbın boşluğuna karşılık gelen bir şekil alır. Geçtiğimiz birkaç bin yıl boyunca, bu teknik kullanılarak aletler, silahlar ve karmaşık heykeller yaratılmıştır.
Döküm Süreci
Bu adımlardan birkaçı, metal veya plastik bir bileşen için döküm sürecinin doğasında önemli bir rol oynar.
- 1. Nihai ürünün ahşap, plastik veya metalden bir modeli yapılır. Kalıp boşluğunun şekli ve boyutları bu modele göre belirlenir.
- 2. Kalıp Hazırlamada, Kalıp boşluğu kalıba göre tasarlanır. Döküm yöntemi, kum, metal veya seramikten yapılıp yapılmayacağını belirleyecektir. Erimiş malzemenin düzgün akışını sağlamak için havalandırma ve yolluk sistemleri uygun şekilde dahil edilir.
- 3. Bu, ham maddenin genellikle metal veya plastiğin bir fırında yüksek sıcaklıkta eritilmesidir. Kullanılan malzemenin türüne özgü sıcaklık farklıdır.
- 4. Erimiş malzeme, dökme işlemi eşit olduğu için kusurları önlemek amacıyla kalıp boşluğuna doğru miktarda dikkatlice dökülür. Bunun için manuel dökme veya otomatik dökme sistemleri kullanılabilir.
- 5. Katılaşma - Malzeme soğur ve kalıp içinde katılaşarak boşluğun şeklini oluşturur. Döküm ürünün nihai özelliklerini etkileyen şeyin soğuma hızı olduğu bilinmektedir.
- 6. Katılaşmadan sonra döküm kalıptan çıkarılır, kapılar, yolluklar veya flaş gibi fazla malzeme kesilir ve ardından montaj sökme ve son işlemden geçirilir. Daha sonra, nihai ürünün görünümünde ve mekanik özelliklerinde bir iyileşme sağlamak için taşlama, parlatma veya ısıl işlem gibi ek bitirme işlemlerine tabi tutulabilirler.
Bu yapılandırılmış yaklaşım ile döküm daha güvenilir ve kaliteli bir şekilde yapılır.
2. Basınçlı Döküm Nedir?
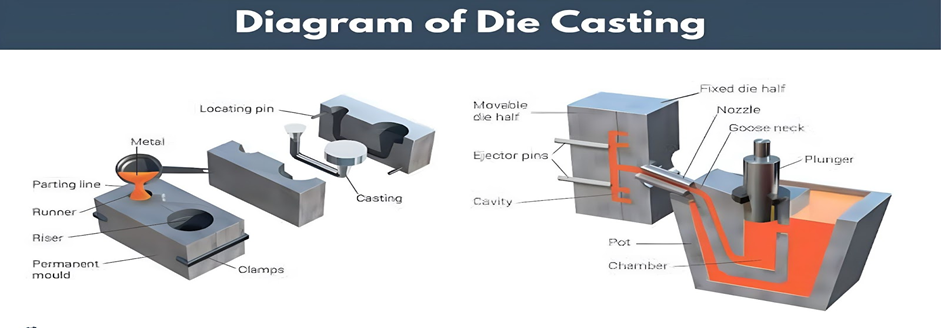
Kalıplar, kalıplar anlamına gelir, dolayısıyla erimiş bir metalin bir kalıp boşluğunu doldurmak için yüksek basınç altında zorlandığı basınçlı döküm işleminin adıdır. Yüksek hacimli, karmaşık ve boyutsal olarak doğru parçalar yapmak için en uygun yöntemdir.
Basınçlı Döküm Süreci
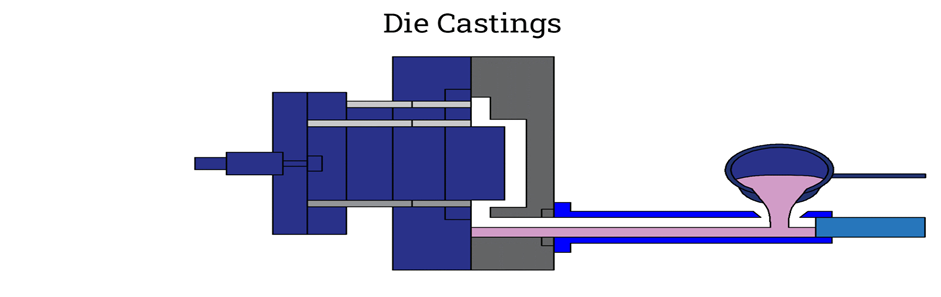
Basınçlı döküm, metal bileşenlerin yüksek basınç altında bir kalıbın boşluğu şeklinde oluşturulduğu ve aynı zamanda yüksek hassasiyet ve doğru boyutsal doğruluk ve yüzey kalitesi gerektiren bir üretim sürecidir. Bu, aşağıdaki adımların bir takibidir:
- 1. Erimiş Metal Enjeksiyonu - Erimiş metali (alüminyum, çinko veya magnezyum gibi) çelik bir kalıba (kalıp) enjekte etmek için 1.500 ila 25.000 psi arasında değişen yüksek basınç uygulanır ve seçilen metal bir fırında eritilir. Bu, kalıbın her ayrıntısını erimiş metalle dolduracaktır.
- 2. Kalıp veya Kalıp - Erimiş metal gerçekten soğur ve kalıp içinde katılaşır, böylece güçlü ve hassas bir parça elde edilir. Nihai ürünün mekanik özellikleri soğuma hızına bağlıdır.
- 3. Çıkarma ve düzeltme - Katılaştığında, döküm parça çıkarma pimleri tarafından kalıptan çıkarılır. Flaş, yolluklar ve kapılar dahil olmak üzere fazla malzeme istenen şekle göre kesilir.
- 4. Yüzey bitirme - Uygulamaya bağlı olarak, dökümün görünümünü, dayanıklılığını ve korozyon direncini artırmak için daha fazla bitirilmesi gerekebilir Nice taşlama, parlatma boyama, eloksal veya toz kaplama.
Bu süreç, yüksek mukavemetli, düşük ağırlıklı, az işlem sonrası karmaşık parçalarla sonuçlanacaktır. Basınçlı dökümün en yaygın kullanıldığı malzemeler arasında alüminyum, çinko ve magnezyum gibi demir içermeyen metaller yer alır.
Döküm Prosesleri Türleri
Kullanılan yöntemin türüne bağlı olarak çeşitli döküm türleri vardır
1 Kum Döküm

- Kum kalıpların kullanıldığı en çok yönlü ve ekonomik döküm yöntemlerinden biridir.
- Otomobil, havacılık ve sanat endüstrilerinde yaygındır.
2 Hassas Döküm
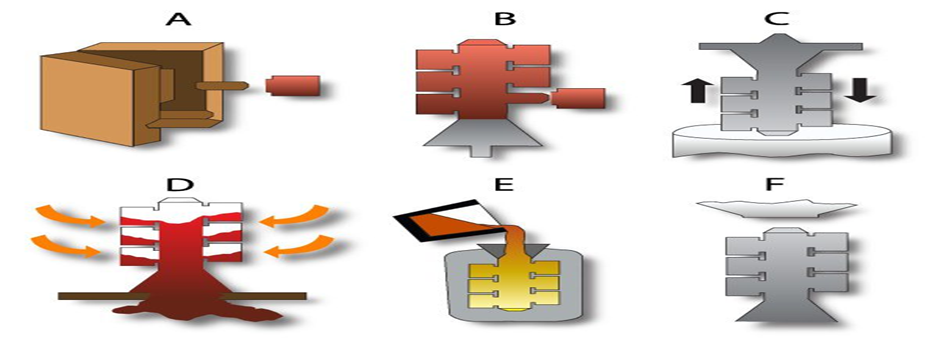
- Kayıp balmumu dökümü olarak da bilinen bu yöntemle son derece detaylı ve karmaşık parçalar üretilir.
- Mücevherat, tıbbi implantlar ve havacılık bileşenleri olarak kullanım için.
3 Santrifüj Döküm

- Erimiş metali iyice entegre etmek için bir kalıbın döndürülmesini içerir.
- Genellikle boru, silindir ve halka yapımında kullanılır.
4 Kalıcı Kalıp Döküm
- Atıkları azaltır ve yeniden kullanım yoluyla kalıp kullanımını azaltır.
- Tekrarlanan, yüksek kaliteli metal parça üretimi için idealdir.
Kalıp döküm çeşitleri
Basınçlı döküm için başlıca iki yol vardır:
1. Sıcak Kamara Basınçlı Döküm
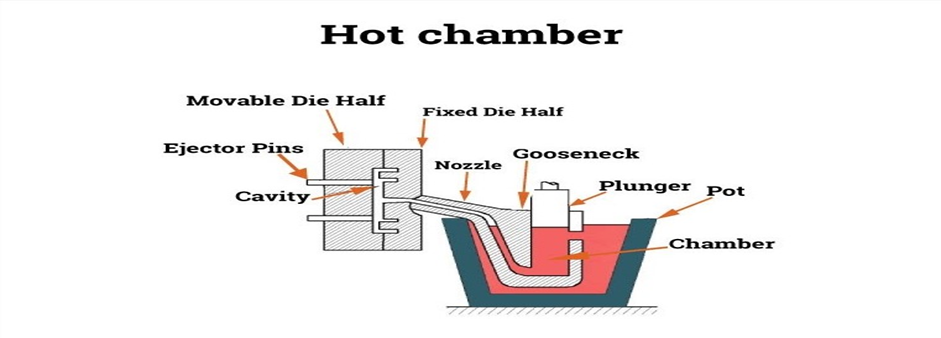
- Çinko ve magnezyum gibi düşük erime noktalı metaller için kullanılır.
- Daha yüksek üretim oranları ile daha hızlı süreç.
2. Soğuk Kamara Basınçlı Döküm

- Alüminyum ve pirinç gibi yüksek erime noktalı metaller için kullanılır.
- Dayanıklı parçalar için uygun olmakla birlikte eritme ve enjeksiyon adımlarını yavaşlatır.
5. Döküm ve Basınçlı Döküm Arasındaki Farklar
Özellik | Döküm | Basınçlı Döküm |
süreç | İçine metal dökülmüş kalıp | Erimiş metal yüksek basınç altında enjekte edilir |
Malzemeler | Çeşitli metaller ve plastikler | Çoğunlukla alüminyum ve çinko gibi demir dışı metaller |
Hassasiyet | Orta düzeyde | Yüksek hassasiyet |
maliyet | Düşük maliyetli başlangıç maliyeti | Yüksek ilk takım maliyeti |
Uygulamalar | Büyük ve basit parçalar | Küçük, karmaşık, yüksek hacimli parçalar |
Döküm ve Basınçlı Döküm Uygulamaları

Döküm ve basınçlı döküm, kendi yöntemleriyle, farklı endüstrilerde muazzam rollere sahiptir ve karmaşık metal bileşenlerin mükemmel hassasiyetle üretilmesini kolaylaştırdıkları için uygun maliyetlidir.
- Otomotiv Endüstrisinde motor blokları, şanzıman gövdesi, tekerlek göbekleri, fren parçaları ve süspansiyon parçaları üretilmektedir. Hafif alüminyum parçalara gelince, basınçlı döküm, daha yüksek yakıt verimliliği seviyelerini karşıladığı için bu amaç için özellikle tercih edilmektedir.
- Havacılık ve Uzay: Türbin kanatları, yapısal uçak gövdesi bileşenleri, muhafazalar ve iniş takımı bileşenleri gibi havacılık ve uzay bileşenleri, dayanıklı, güçlü ve hafif olacak şekilde dökülür.
- Elektronikte, ısıyı dışarı atmak ve kırılgan elektronik devrelere güvenlik zihniyeti sağlamak için ısı alıcıları, konektörler ve ekranlama cihazları gibi muhafazalar ve kalıp döküm bileşenleri gerektiğinden, döküm ve kalıp döküm çok önemlidir.
- İnşaat - Binaların, köprülerin vb. inşası için yapısal stabilite ve uzun ömür sağlayan borular, bağlantı parçaları, braketler, vanalar ve korkuluklar.
- Tıbbi Ekipman - Hassas döküm bileşenler, cerrahi aletler, görüntüleme ekipmanlarının muhafazaları, ortopedik implantlar vb. için tıp alanında geniş kullanım alanı bulmaktadır.
- Endüstriyel Makineler - Dişli kutularında, pompalarda ve zorlu koşullarda çalışan diğer ağır iş makine parçalarında mukavemet ve aşınma direnci sağlamak için döküm gereklidir.
Döküm ve basınçlı döküm uygulamaları yaygındır ve bu nedenle modern imalat endüstrilerinin vazgeçilmez bileşenleridir.
Kalıp döküm çeşitleri
En popüler üretim süreçlerinden biri, karmaşık ve öngörülen özelliklere sahip bileşenler yapmak için erimiş metalin kalıba girdiği basınçlı dökümdür. Malzemelere, üretim gereksinimlerine ve kalite standartlarına uymak için zaman içinde farklı basınçlı döküm çeşitleri geliştirilmiştir. Her yöntemin avantajları vardır ve farklı uygulama türleri için az ya da çok uygun olacaktır. Aşağıda, ilgili süreçleri ve faydaları ile birlikte başlıca basınçlı döküm çeşitleri yer almaktadır.
Yerçekimli Basınçlı Döküm (GDC)
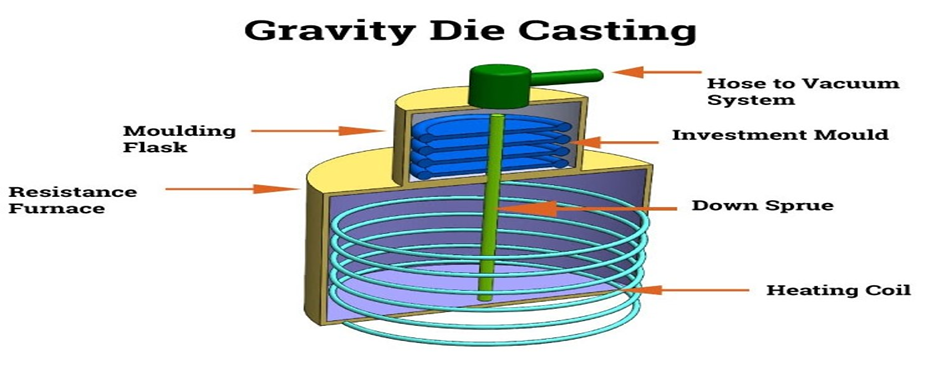
Genel Bakış
Yerçekimli Basınçlı Döküm (GDC), erimiş metalin yüksek basınç kullanılmadan bir kalıba dökülmesi uygulamasına sahiptir. Bunun yerine, yerçekimi metali boşluğu doldurmaya ve sanki kendi kendine organize olmaya yönlendirmeye yardımcı olur. Bu işlem daha düşük erime noktalı alaşımlar için tercih edilir ve daha kontrollü katılaşma süreci istendiğinde yaygın olarak kullanılır.
Temel Özellikler
- Yeniden kullanılabilir kalıplar kullandığı için kum dökümden daha verimlidir.
- Basınçlı dökümden daha yavaştır, ancak daha yoğun moda bağlı olarak parça daha güçlüdür.
- Alüminyum ve magnezyum gibi belirli alaşımlarla sınırlıdır.
Yaygın Uygulamalar
- Otomobil bileşenleri (silindir kapakları, motor parçaları).
- Boru bağlantı parçaları ve vana gövdeleri.
- Endüstriyel makineler ve yapısal parçalar.
Düşük Basınçlı Basınçlı Döküm (LPDC)

Genel Bakış
Düşük basınçlı basınçlı döküm (LPDC), erimiş metalin 0,1 ila 1 MPa mertebesinde düşük basınç altında kalıp içine basınçlandırılmasıdır. Bu kontrollü dolum ile türbülans en aza indirilir ve akış daha düzgün hale getirilir, böylece hava cepleri ve inklüzyonlar gibi bu kusurlar minimumda tutulur.
Temel Özellikler
- Azaltılmış türbülans sayesinde daha iyi malzeme bütünlüğü.
- Opsiyon, yüksek yapısal mukavemete ihtiyaç duyan büyük, karmaşık parçalar için uygundur.
- Seri üretim durumunda güvenilirdir (tutarlı kalite).
Yaygın Uygulamalar
- Otomobiller için alüminyum jantlar.
- Uçak yapısal parçaları.
- Endüstriyel makinelerde ısıya dayanıklı bileşenler.
Sıkıştırmalı Basınçlı Döküm

Genel Bakış
Squeezedie-döküm işleminde, kalıp boşluğu içindeki erimiş metale yüksek basınç uygulanır. Uygulanan kuvvet 20.000 psi'den (inç kare başına pound) fazla olduğundan, metal kalıbın en ince detayını bile doldurur ve gözenekliliği giderir.
Temel Özellikler
- Son derece yoğun ve güçlü parçalar oluşturur.
- Gözenekliliği azaltır ve daha iyi mekanik özellikler sağlar.
- Dayanıklılığın önemli olduğu yüksek mukavemetli uygulamalara uygulanabilir.
Yaygın Uygulamalar
- Otomobiller için süspansiyon bileşenleri.
- Yüksek performanslı havacılık parçaları.
- Ağır hizmet tipi endüstriyel alet ve ekipmanlar.
Vakumlu Basınçlı Döküm

Genel Bakış
Vakumlu Basınçlı Döküm, döküm işlemi öncesinde ve sırasında sıkışan hava ve gazları kalıp boşluğundan tahliye etmek için tasarımını kullanır. Bu yöntem bir vakum yaratarak uygulanır ve standart basınçlı dökümde yaygın bir kusur olan gözeneklilikte önemli bir azalma sağlar. Sonuç olarak daha hassas, daha güçlü ve hatasız bir döküm elde edilir.
Temel Özellikler
- Nihai ürünün mekanik özelliklerini geliştirir.
- Hava sıkışmasını en aza indirir, bu da onu dört duvarlı ve yüksek hassasiyetli parçalar için uygun hale getirir.
- Genel döküm kalitesini artırır, işlem sonrası işlemleri azaltır.
Yaygın Uygulamalar
- Hafif dayanıklılığı karşılamak için otomotiv yapısal parçalarının kaynaklanması.
- Yüksek hassasiyete sahip tıbbi ekipman bileşenleri.
- Havacılık ve uzay parçalarının bütünlüğü.
Yarı katı basınçlı döküm (Reocasting)

Genel Bakış
Reokasting veya Yarı Katı Basınçlı Dökümde tamamen sıvı metal yerine kısmen katılaşmış metal kullanılır. Bu, metali yarı sıvı veya bulamaç halinde tutarak kalıbın içine düzgün bir şekilde akmasını sağlar ve türbülansı ve gözenekliliği azaltır.
Temel Özellikler
- Üstün mekanik özelliklere sahip bileşenler üretir.
- Büzülme kusurlarını ve gözenekliliği azaltır.
- Karmaşık, yüksek hassasiyetli parçalar için idealdir.
Yaygın Uygulamalar
- Yüksek mukavemet ve hafiflik özellikleri gerektiren tüm otomobil parçaları.
- İnce detaylara sahip elektronik muhafazalar.
- Aşınmaya dayanması gereken bileşenlere sahip endüstriyel makineler için.
Basınçlı Dökümde Kullanılan Yaygın Metaller
Erimiş metalin yüksek basınç altında bir kalıba enjekte edilmesi için kullanılan üretim süreci basınçlı dökümdür. Bu süreçte seçilen metal, nihai ürünün mukavemeti, dayanıklılığı ve uygulamasında da önemlidir. Bu tür döküm için çeşitli metaller kullanılabilir, ancak demir içermeyen metaller (veya demir içermeyen metaller) daha düşük erime noktalarına sahip oldukları ve daha dökülebilir oldukları için en çok kullanılanlardır.
Basınçlı dökümde en çok kullanılan metaller, özellikleri ve kullanım alanları ile birlikte aşağıda belirtilmiştir.
1. Alüminyum
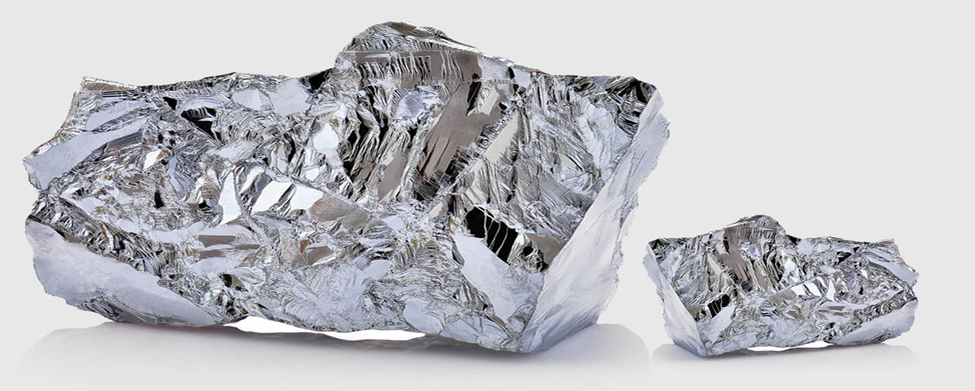
Kullanılan metaller arasında kalıp döküm, Bununla birlikte, alüminyum en yaygın kullanılanıdır ve iyi mukavemet, düşük ağırlık ve korozyon direncinin ideal kombinasyonuna sahiptir. Nispeten düşük yoğunluğuyla, yüksek mukavemete sahip düşük yoğunluklu bileşenlere ihtiyaç duyulan endüstrilerde kullanılmak için iyi bir adaydır.
Basınçlı Dökümde Alüminyumun Avantajları
- Otomotiv ve havacılık endüstrilerinde ağırlığı azaltmak için kullanıldığı için hafif ve güçlüdür.
- Korozyona dayanıklı - Dış mekan ve deniz uygulamaları için uygundur.
- İyi termal ve elektriksel iletkenlik - Elektronik muhafazalarda ve ısı alıcılarında kullanılır.
Alüminyum Basınçlı Dökümlerin Yaygın Uygulamaları
- Motor blokları, şanzıman gövdeleri, tekerlekler, vb. (otomotiv parçaları).
- Havacılık ve uzay bileşenleri (uçak çerçeveleri, braketler).
- Tüketici elektroniği (akıllı telefon gövdeleri, dizüstü bilgisayar kasaları).
Alüminyum, yüksek erime noktası nedeniyle normalde soğuk kamaralı kalıp döküm ile dökülür.
2. Çinko
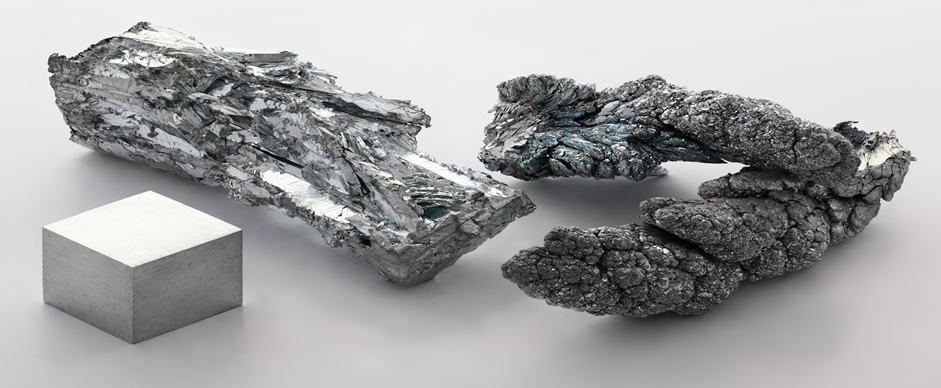
Bir diğer popüler basınçlı döküm metali de yüksek hassasiyeti, mukavemeti ve döküm kolaylığı ile bilinen çinkodur. Bununla birlikte, çinkonun alüminyuma kıyasla daha düşük erime noktası, onu sıcak kamaralı basınçlı döküm için çok uygun hale getirir ve daha hızlı üretim döngüleri üretir.
Basınçlı Dökümde Çinkonun Avantajları
- Yüksek mukavemet ve dayanıklılık - Mekanik bileşenler için idealdir.
- Düşük erime noktası - Daha hızlı üretim ve daha uzun kalıp ömrü sağlar.
- İyi yüzey kalitesi - Kapsamlı son işlem ihtiyacını azaltır.
Çinko Basınçlı Dökümlerin Yaygın Uygulamaları
- Küçük mekanik bileşenler (dişliler, bağlantı elemanları, menteşeler).
- Elektrik ve elektronik konektörler.
- Aşağıdakiler gibi ek bileşenler içerir otomoti̇v parçalari (braketler, tutamaklar, kapı kilitleri).
Ayrıca, çinko alüminyumdan daha ucuzdur ve bu nedenle küçük parçaların üretiminde tercih edilen malzemedir.
3. Magnezyum
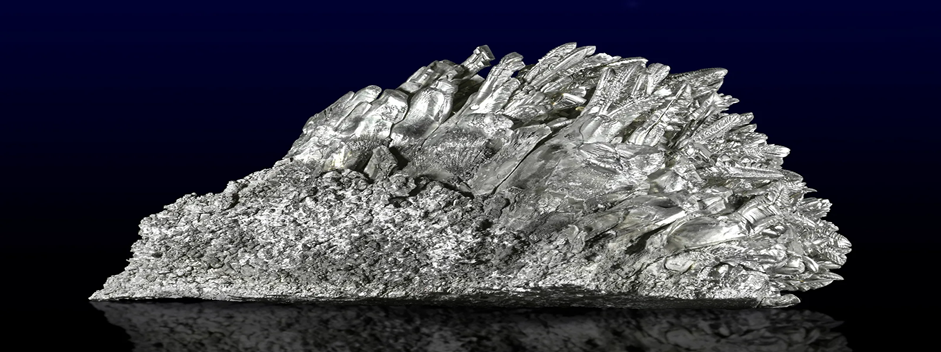
Basınçlı döküm için yapısal bir metal olarak magnezyum, kullanılan en hafif metaldir ve olağanüstü bir mukavemet / ağırlık oranı sağlar. Alüminyuma kıyasla yaklaşık 30% daha hafiftir, bu da onu ağırlık azaltma gerektiren uygulamalar için iyi bir seçenek haline getirir.
Basınçlı Dökümde Magnezyumun Avantajları
- Son derece hafif - Havacılık ve otomotiv uygulamaları için ideal.
- İyi mukavemet ve darbe direnci - Mekanik strese dayanabilir.
- Diğer metallere göre işlenmesi (işlenebilirliği) çok kolaydır.
Magnezyum Basınçlı Dökümlerin Yaygın Uygulamaları
- Otomotiv endüstrisinde (direksiyonlar, gösterge paneli çerçeveleri) kullanılır.
- Havacılık ve uzay endüstrisi (drone ve uçak parçaları).
- Tüketici elektroniği (dizüstü bilgisayar ve kamera gövdeleri).
Toz halindeki magnezyum oldukça yanıcı olmasına rağmen, döküm parçalar endüstriyel kullanım için yeterince sağlam ve güvenlidir.
4. Bakır ve Bakır Alaşımları (Pirinç ve Bronz)

Yüksek termal ve elektriksel iletkenliğe sahiptir ve bu nedenle bakır ve alaşımları (pirinç, bronz) elektrik ve sıhhi tesisat uygulamaları için kullanılır. Hem çinko hem de alüminyumdan daha yüksek fiyatlı ve daha ağır olmalarına rağmen, daha yüksek korozyon direnci ve aşınma direncine sahiptirler.
Basınçlı Dökümde Bakır ve Alaşımlarının Avantajları
- Mükemmel elektrik iletkenliği - Elektronik ve elektrikli bileşenlerde kullanılır.
- Korozyona dayanıklıdır ve sıhhi tesisat ve denizcilik uygulamaları için çok uygundur.
- Üstün aşınma direnci - Daha uzun ömürlü parçalar sağlar.
Bakır ve Bakır Alaşımlı Basınçlı Dökümlerin Yaygın Uygulamaları
- Elektrik konnektörleri ve terminalleri.
- Sıhhi tesisat armatürleri ve vanalar.
- Endüstriyel makine bileşenleri.
Bakır, basınçlı dökümde genellikle alüminyum veya çinko kadar kullanılmasa da, yüksek dayanıklılık ve iletkenliğin gerekli olduğu bu tür özel uygulamalarda hala çok önemlidir.
5. Ayrıca kurşun ve kalay (bugün çok yaygın değil)

Özel uygulamalar için, düşük erime noktaları ve mükemmel korozyon dirençleri nedeniyle kurşun ve kalayın basınçlı dökümü bir zamanlar yaygındı. Bununla birlikte, sağlık ve çevresel nedenlerden dolayı son yıllarda kullanımları büyük ölçüde azalmıştır.
Basınçlı Dökümde Kurşun ve Kalayın Avantajları (Tarihsel Olarak)
- Korozyon direnci iyidir - Sıhhi tesisat ve akü bileşenlerinde kullanılır.
- Yumuşak ve dövülebilir - Düşük gerilimli uygulamalar için uygundur.
- Yüksek yoğunluğa sahiptirler; bu nedenle radyasyon kalkanı ve ses yalıtımı uygulamalarında kullanılırlar.
Kurşun ve Kalay Basınçlı Dökümlerin Yaygın Uygulamaları (Artık Sınırlı)
- Akü terminalleri.
- Rulmanlar ve yumuşak lehim parçaları.
- Radyasyondan korunmada ekranlama bileşenleri.
Çevresel düzenlemeler artmaya devam ettikçe, üreticilerin alüminyum, çinko ve magnezyum gibi daha güvenli malzemeler bulmaları gerekli hale gelmiştir.
Avantajlar ve Dezavantajlar
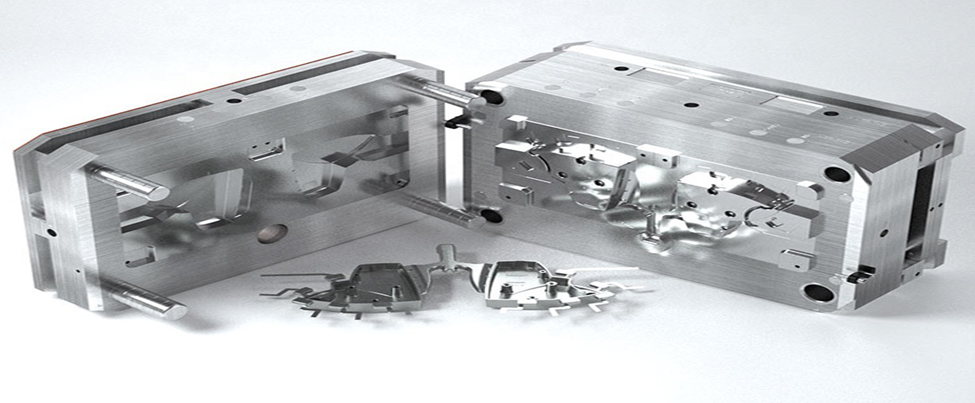
Dökümün Avantajları
- Düşük üretim fiyatı - Döküm, diğer üretim süreçlerine kıyasla çok az takım (takım ve kalıp) gerektirdiğinden, özellikle küçük üretim çalışmaları için uygun maliyetli bir üretim yöntemidir.
- Büyük veya karmaşık şekiller oluşturabilir - Döküm, torna tezgahında veya talaşlı imalatta üstesinden gelinmesi zor veya bunların üstesinden gelemeyeceği kadar büyük şekiller oluşturabilir.
- Çok çeşitli malzemeleri döker - Demir, çelik, alüminyum bronz vb.
- Verimli malzeme kullanımı - Döküm, erimiş metal doğrudan kalıplara döküldüğü ve fazla malzeme kaybetmediği için malzeme israfına yol açmaz.
- Seri üretime uygun - Kalıp oluşturulduktan sonra, aynı parçaların birçoğu nispeten kolay bir şekilde üretilebilir.
Dökümün Dezavantajları
- Basınçlı dökümden daha az hassas. Geleneksel döküm yöntemleri, yine de işlenmesi gereken yüzey kusurları ve boyutsal varyasyonlar üretme eğilimindedir.
- Daha uzun soğutma süreleri ve soğutma ve katılaştırma süreci, genel üretim verimliliğini etkileyebilir.
- Daha fazla bitirme işi gerekir - Döküm parçalar, taşlama ve parlatma gibi işleme yoluyla çıkarılması gereken pürüzlü yüzeye veya fazla malzemeye (flaş) sahip olacaktır.
- Gözeneklilik sorunları - Bu, döküm işlemi sırasında ortaya çıkan ve yapısal bütünlükte zayıflık yaratan hava cepleri veya boşluklar sorunu olabilir.
- Kalıp bozulması - Yeniden kullanılabilir kalıpların kullanılması, zamanla bu kalıpları bozar ve parçaların et kalınlığı artar, buna bağlı olarak üretim hataları ve bakım maliyetleri artar.
Basınçlı Dökümün Avantajları
- Basınçlı döküm, hem yüksek hacimli üretim çalışmaları hem de düşük üretim partileri için uygun olan yüksek hızlı üretimler sağlar.
- Güçlü, hassas boyutlandırılmış parçalar oluşturur - Yüksek basınçlı enjeksiyon işlemi sayesinde parçalar tutarlı bir şekilde, sıkı toleranslarla ve daha fazla ayarlamayı en aza indiren iyi bir kaliteyle çıkar.
- Çok fazla son işlem gerektirmez - Döküm parçalar genellikle pürüzsüz yüzeylere ve ikincil işleme gerektirmeyen temiz detaylara sahiptir.
- Basınçlı döküm, tekrarlanabilirlik açısından mükemmeldir ve çok sayıda üretim döngüsünde üretimde tekdüzelik sağlar, bu da seri üretim için tercih edilen bir yöntem olmasının nedenidir.
- İyi yüzey kalitesi - Herhangi bir son işlem gerektirmez, bu da onu estetiği göz önünde bulunduran ürünler yapmak için çok uygun hale getirir.
Basınçlı dökümün dezavantajları
- Daha yüksek başlangıç maliyeti (kalıplar pahalıdır) - Basınçlı döküm kalıplarının tasarımı ve üretimi pahalı olabilir ve bu nedenle üretim küçük ölçekliyse ekonomik olmayabilir.
- Demirli metaller için uygun değildir - Basınçlı döküm alüminyum, çinko ve magnezyum için donmuştur, bu da olası malzeme aralığını sınırlar.
- Büyük veya kalın parçalar için uygun değildir - İnce duvarlı bileşenler, büyük veya kalın duvarlı olanlara göre basınçlı döküm için daha uygundur. Basınçlı döküm hızlı bir soğutma süreci içerir.
- Gözeneklilik - Enjeksiyon kalıplama işlemi sırasında ürünün hava ile dolması mümkündür ve bu da nihai ürünü zayıflatan gözenekliliğe yol açacaktır.
- Tasarım değişikliklerinde daha az esneklik - Bir kalıp yapıldıktan sonra, dökümlerde tasarım değişikliği yapmak diğer döküm yöntemlerine kıyasla maliyetli ve zaman alıcı olacaktır.
8. Döküm ve Basınçlı Dökümün Geleceği
Döküm ve basınçlı döküm, otomasyon ve 3D baskı nedeniyle gelecek için (en azından kısa vadede) umut vaat ediyor. Bazı önemli trendler şunlardır:
- Çevre Dostu Malzemeler - Sürdürülebilir ve geri dönüştürülebilir alaşımlar.
- Akıllı Üretim - Verimlilik için yapay zeka destekli otomasyon.
- 3D baskı ile dökümün hibrit süreçleri şeklinde eklemeli üretim entegrasyonu.
Modern endüstrilerde bu yenilikler verimliliği artıracak, israfı azaltacak ve üretim masraflarını düşürecek, dolayısıyla üretim süreçlerini daha da vazgeçilmez hale getirecektir.
Sonuç
Çeşitli sektörlerde, yüksek kaliteli metal bileşenler üretme süreci, üretimdeki ana süreçlerden biri olmaya devam ediyor. Basınçlı döküm seçenekleri, her biri belirli uygulamalar için farklı faydalar sağlayan birçok varyantla birlikte gelir. Yerçekimli Basınçlı Döküm ile güçlü ve yoğun parçalar üretilir; Düşük Basınçlı Basınçlı Döküm ile parçalar minimum kusurla yapısal olarak sağlamdır. Sıkıştırmalı Basınçlı Döküm harika bir mukavemet ve dayanıklılığa sahipken, Vakumlu Basınçlı Döküm gözeneklilikten tasarruf sağlar. Bununla birlikte, Yarı Katı Basınçlı Döküm, yüksek performanslı uygulamalar için mekanik özellikler ve hassasiyet açısından avantajlara sahiptir ve basınçlı döküm yönteminin seçimi Malzeme seçimine, Parçanın Karmaşıklığına, Parça Hacmine ve istenen mekanik özelliklerin türüne bağlıdır. Süreç, otomasyon, alaşım geliştirme ve hassas mühendislikteki yeni gelişmeler açısından rafine edilmeye devam etmekte ve kullanımını giderek daha verimli, daha az maliyetli ve çevre dostu hale getirmektedir.
Endüstrilerin daha hafif, daha güçlü ve daha sert bileşenlere olan talebi nedeniyle teknoloji sürekli olarak gelişecektir. Ancak üreticiler uygun basınçlı döküm yöntemini seçerek kötü ürün performansını, israfı ve üretim verimsizliğini önleyebilirler. En iyi üretim seçeneğini seçmek için bu basınçlı döküm çeşitlerini anlamak ve üretimde en yüksek kalite, güvenilirlik ve verimliliği elde etmek gerekir.
Sıkça Sorulan Sorular (SSS)
1. Basınçlı Döküm Nasıl İşler ve Ne Şekilde Çalışır?
Basınçlı döküm olarak bilinen işlemle metal dökümü, erimiş metalin yüksek basınç altında bir kalıba enjekte edildiği bir işlemdir. Bu, üreticilerin mükemmel yüzey kalitesi ve çok az işleme ile karmaşık, yüksek hassasiyetli metal parçalar üretmesini sağlar.
2. Kaç çeşit basınçlı döküm vardır?
Basınçlı dökümün ana formları Yerçekimi Basınçlı Döküm (GDC), Düşük Basınçlı Basınçlı Döküm (LPDC), Sıkıştırmalı Basınçlı Döküm, Vakumlu Basınçlı Döküm ve Yarı Katı Basınçlı Dökümdür. Her yöntemin farklı avantaj ve dezavantajları malzemeye ve uygulamaya bağlıdır.
3. Basınçlı döküm sürecinde normalde hangi metaller kullanılır?
Alüminyum, çinko, magnezyum, bakır ve bunların alaşımları basınçlı dökümde en yaygın kullanılan metallerdir. Metaller ağırlık, mukavemet, korozyon direnci ve termal iletkenlik için seçilir.
4. Basınçlı döküm neden bu kadar faydalıdır?
Yüksek üretim verimliliği, mükemmel boyutsal doğruluk, minimum malzeme israfı, pürüzsüz yüzey kalitesi ve çok az işlem sonrası ile karmaşık şekiller üretmek mümkündür.