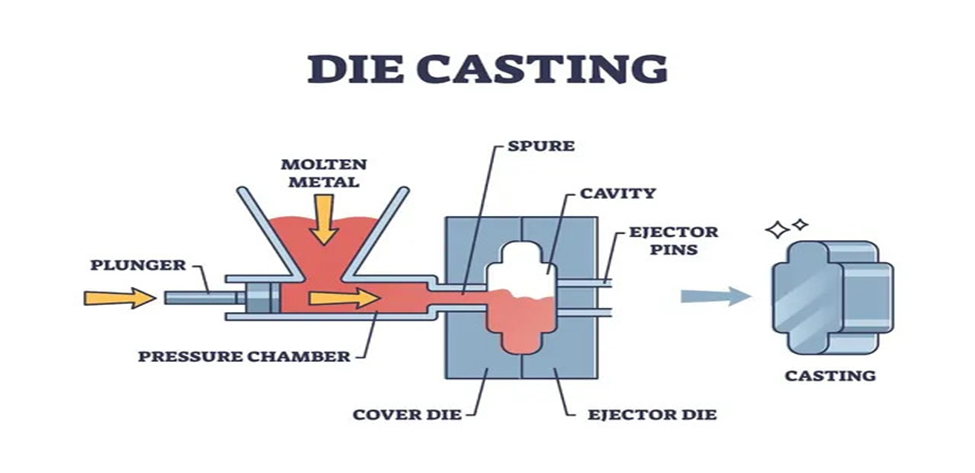
Bu, kalıp döküm olarak da bilinen bir kalıp boşluğunu doldurmak için erimiş metalin basınç kullanılarak zorlandığı bir üretim sürecidir. Kalıp genellikle yüksek kaliteli çelikten yapılır ve bu nedenle parça büyük miktarlarda üretilebilir, bu terim birçok parçanın üretimi anlamında kullanılır. Bitmiş parça, erimiş metal soğuduktan ve katı bir tabaka oluşturduktan sonra kalıbın açılmasıyla üretilir. Prosesin bu tür kullanımı çoğunlukla ölçümde yüksek doğruluk ve cilalı yüzeyler gerektiren farklı parçaların üretiminde kullanılan karmaşık metal yapımında uygulanır. Basınçlı döküm alüminyum, çinko ve magnezyum üzerinde yapılabilir, ancak uygulamaya ve diğer gereksinimlere bağlı olarak diğer metaller de bir kasa üzerinde kullanılabilir. Basınçlı döküm metallerden küçük ve orta ölçekli bileşenlerin seri üretimi anlayışında uzman üretim tekniklerinden biri olarak kabul edilmektedir. Yöntemin popülaritesi, dayanıklı, hafif ve özel olarak tasarlanmış parçalar üretme kabiliyeti nedeniyle otomotiv, havacılık, elektronik ve endüstriyel makinelere yayılmıştır. Bununla birlikte, bu süreç, geleneksel teknikler kullanılarak yapılması çok zor olan karmaşık geometriye sahip ürünleri üretme kabiliyetiyle yaygın olarak tanınmaktadır.
Basınçlı Döküm Nasıl Çalışır?

Kalıplama, basınçlı döküm işleminin ilk kısmıdır. Kalıbın bir tarafında bir yarım vardır ve kalıbı nihai ürün gibi şekillendirmek için belirli bir tasarımın yarısıdır. Genellikle özel yapım olan kalıplar için boşluklar ve maçalar tasarlanır, böylece parça mümkün olduğunca yakın bir şekilde çoğaltılabilir.
1. Erimiş Metal Enjeksiyonu:
Daha sonra erimiş metal, istenen şekli oluşturmak için yüksek basınç altında kalıp boşluğuna enjekte edilir. Metal, akışkan hale gelmesi için genellikle erime geriliminin bir derece üzerine kadar ısıtılır. Basınçlı dökümde, erimiş metalin kalıbın her ayrıntısına girdiğinden emin olmak için erimiş metalin kalıba itildiği basınç birkaç bin ila on binlerce psi (inç kare başına pound) arasında olabilir.
2. Katılaşma:
Bu, metalin muhafaza boşluğuna enjekte edilmesi, soğuması ve metalin sertleşmesiyle gerçekleşir. Dökümün kalitesi soğuma hızına bağlıdır. Bu durumda ek hata modları (kesme, tırmanma ve kayma) devreye girer ve daha hızlı soğutma daha yüksek mukavemet daha iyi yüzey kalitesi ve daha fazla iç kusur ve daha düşük mekanik özelliklerle sonuçlanabilecek daha yavaş soğutma ile sonuçlanır. Kalıp içine yerleştirilmiş su soğutma sistemleri genellikle soğutma işlemine yardımcı olmak için kullanılır.
3. Fırlatma:
Bunu takiben, metalin soğumasına ve katılaşmasına izin verilir ve daha sonra kalıbı daha büyük dökümden çıkarmak ve parçayı çıkarmak kolaydır. Daha sonra çoğu zaman mekanik bir ejektör sistemi kullanılarak parçanın kalıptan dışarı itilmesinde kullanılır. Bu, nihai şekli ve boyutu sağlamak için kırpma ve işleme gibi diğer ekstra adımları gerektiren parçanın karmaşıklığına bağlıdır.
4. Kalite Kontrol:
Fırlatmadan sonra parça üzerinde bir kalite kontrolü gerçekleştirilir. Parçanın gereksinimlere eşit veya daha iyi olduğunu doğrulamak için boyutsal doğrulama, görsel inceleme ve mekanik testleri içerebilir. Basınçlı dökümde teorik olarak yüksek hassasiyet ve tekrarlanabilirlik elde edilir.
Basınçlı Döküm Çeşitleri
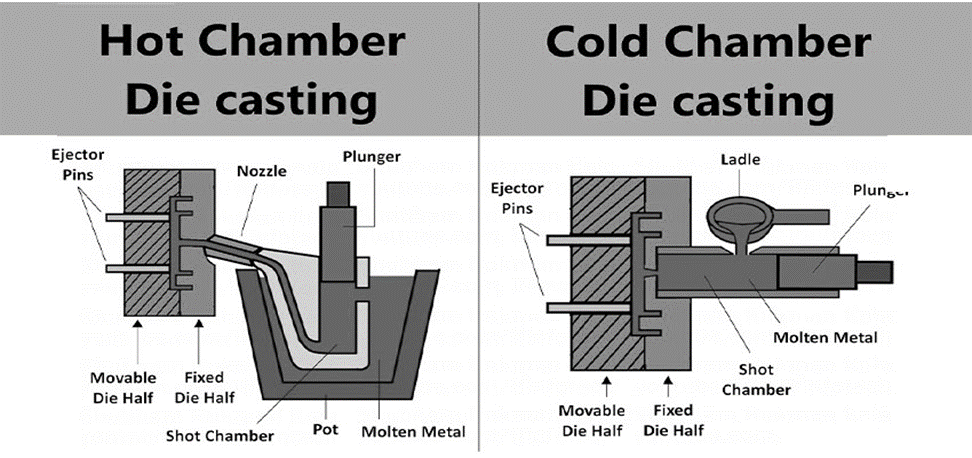
İki tip Basınçlı döküm vardır, bunlar sıcak kamaralı basınçlı döküm ve soğuk kamaralı basınçlı dökümdür. Bunların hepsi iyidir ve avantajları, sınırlamaları ve ideal uygulamaları vardır.
1. Sıcak Kamara Basınçlı Döküm
Çinko, magnezyum ve kurşun gibi metaller için en uygun proses, yüksek sıcaklıklarda ve erime noktalarında yapıldığı için sıcak kamaralı basınçlı dökümdür. Enjeksiyon sistemi ergitme fırınının içine kurulur, bu şekilde metal her zaman hazne ile temas halindedir.
Avantajlar:
- Erimiş metal enjeksiyon odasında olduğu için kalıba enjekte edilecek şekilde düzenlendiğinden, sıcak kamaralı basınçlı döküm soğuk kamaralı basınçlı döküme göre daha kısa sürer.
- Tek aşamalı: Daha az sayıda bileşen ve kurulum için zaman gerektirir, bu nedenle özellikle yüksek hacimli operasyonlarda ekonomik olarak kabul edilir.
- Belirli Metaller İçin; Sıcak Kamaralı Basınçlı Döküm, kullanılacak metallerin düşük erime sıcaklıklarına sahip olduğu durumlarda en uygun olanıdır, böylece metallerin kirlenmesi çok az olur veya hiç olmaz.
Dezavantajlar:
- Hazneyi eriten metaldeki yüksek sıcaklık nedeniyle Alüminyum ve pirinç gibi yüksek erime noktalı metal işlerinde kullanılamaz.
- Tüm bileşenler erimiş metale maruz kalır, bu nedenle aşınma ve yıpranma seviyesi bir süre boyunca yüksektir.
2. Soğuk Kamara Basınçlı Döküm
Alüminyum, pirinç ve bakır gibi daha yüksek erime noktasına sahip metaller soğuk kamaralı basınçlı dökümde dökülür. Bu durumda, erimiş metal ikinci bir fırından çekilerek soğuk hazneye ve ardından kalıp boşluğuna enjekte edilir.
Avantajlar:
- Malzeme Seçimlerinde Çok Yönlülük Açısından Soğuk kamaralı basınçlı döküm, yüksek erime noktalarına sahip malzemelerin kullanımına izin veren malzeme kullanımında çok yönlülük sunar.
- Metal Kalitesi Üzerinde Daha Fazla Kontrol: Erimiş metal silindir hazneye ayrı olarak döküldüğünden, kontaminasyonu önlemek için metalin kalitesi iyi kontrol edilebilir.
- Artan Takım Ömrü: Enjeksiyon işlemi boyunca metal ile artık temas halinde olmadığından, takım ömrü uzar.
Dezavantajlar:
- Daha Yavaş Döngü Süresi: Metalin hazneye manuel olarak dökülmesi döngüyü uzatır.
- Maliyet daha yüksek olacaktır çünkü bu daha karmaşık ekipmanlarla yapılan ek bir prosedürdür.
Basınçlı Döküm Yöntemlerinin Karşılaştırılması: Sıcak Kamara ve Soğuk Kamara
İşte en yaygın iki kalıp döküm yönteminin karşılaştırması,
Özellik | Sıcak Kamara Basınçlı Döküm | Soğuk Kamara Basınçlı Döküm |
Metal Uyumluluğu | Düşük erime noktalı metaller için en iyisi (örn. çinko, kurşun) | Yüksek erime noktalı metaller için en iyisi (örn. alüminyum, pirinç) |
Çevrim Süresi | Daha hızlı döngü süreleri | Daha yavaş döngü süreleri |
Kalıp Aşınması | Erimiş metal ile doğrudan temas nedeniyle daha yüksek kalıp aşınması | Daha düşük kalıp aşınması |
Maliyet | Yüksek hacimli üretim için daha düşük maliyet | Daha yüksek başlangıç maliyeti, ancak yüksek mukavemetli metaller için daha iyi |
Parçaların Karmaşıklığı | Daha basit parçalar için iyi | Daha karmaşık, daha büyük parçalar için daha iyi |
Basınçlı Dökümün Avantajları
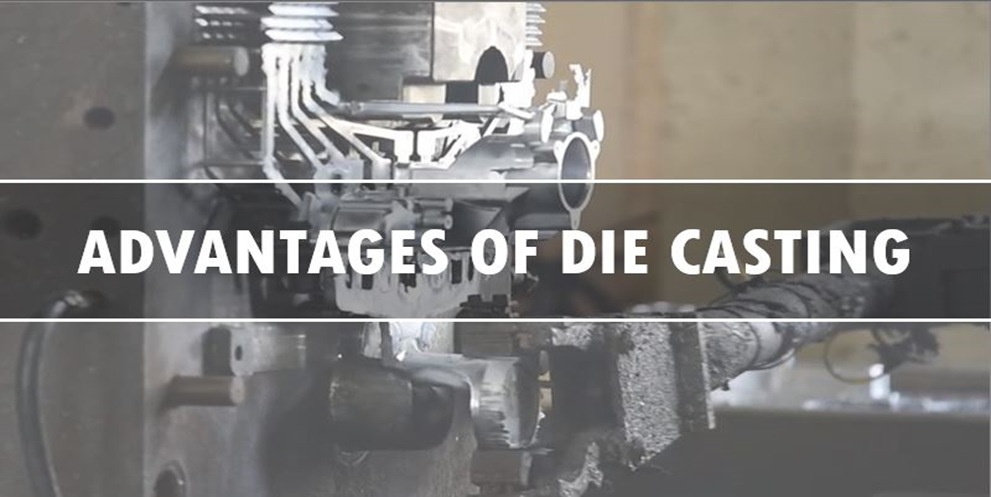
Basınçlı dökümün, metal alaşımlardan büyük ölçekli ürün üretiminde tercih edilen başlıca yöntemlerden biri olması en büyük avantajlardan biridir.
1. Yüksek Hassasiyet ve Doğruluk
Basınçlı dökümün, yüksek kalıp hassasiyeti sunmayı uygun hale getiren birçok avantajı vardır. Bu üretim yöntemi, belirli bir işte gerekli olan tolerans seviyelerini tanımladığı için çok önemli olan iyi boyutsal doğruluk gerektiren parçaların üretimi için de yaygın olarak kullanılmaktadır. Basınçlı dökümün, geometrilerinin karmaşıklığı gibi en üst düzeyde karmaşıklıklara sahip belirli parçaları üretebilen tek üretim tekniği olduğu unutulmamalıdır.
2. Yüksek Üretim Oranları
Büyük hacimler açısından basınçlı döküm çok verimlidir. Parçalar, ilk kalıp oluşturulduktan sonra çok az işçilikle hızlı ve ucuz bir şekilde üretilir. Simüle tozlara olan talep özellikle otomotiv ve elektronik gibi büyük hacimlerde aynı parçaların gerekli olduğu sektörlerde yüksektir.
3. Karmaşık Tasarımlar ve İnce Duvarlar
Geleneksel imalat yöntemleriyle elde edilmesi zor veya imkansız olan karmaşık tasarımlar basınçlı dökümle elde edilebilir. Süreç, ince duvarlı ve karmaşık iç yapılara sahip parçalar üretebilir ve alt kesimleri barındırabilir; böylece alanın sınırlı olduğu durumlarda en uygun uygulama haline gelir.
4. Malzeme Verimliliği
Basınçlı döküm malzeme israfını en aza indirir. Erimiş metali enjekte etmek için kullanılan basınç kalıp boşluğunun her parçasını doldurur ve bu nedenle daha az hurda oluşur. Ayrıca, birçok basınçlı döküm parça geri dönüştürülebilir, bu nedenle sürecin sürdürülebilirliğine yol açar.
5. Mükemmel Yüzey İşlemi
Basınçlı dökümle üretilen parçaların yüzey kalitesi pürüzsüz ve estetiktir. Parlatma veya kaplama gibi daha az ikincil bitirme işlemi gerektirir, böylece zaman ve maliyet tasarrufu sağlar.
Basınçlı döküm sürecinde neler uygulanabilir?
Demir dışı metaller, iyi döküm özellikleri nedeniyle basınçlı dökümde büyük ölçüde kullanılır. Alüminyum alaşımları, aşağıdaki malzemelerle gösterildiği gibi basınçlı dökümden geçen yaygın olarak kullanılan malzemelerdir.
1. Alüminyum Alaşımları

Hafif, korozyona dayanıklı, ısı ve elektrik iletkenliği mükemmel olduğu için alüminyum, basınçlı dökümde en yaygın kullanılan malzemedir. Listenin devamında, özellikle otomotiv, havacılık ve elektrik endüstrilerinde güç/ağırlık oranı dikkate alındığında özel alüminyum alaşımları kullanılır. Son olarak, boyutsal olarak da kararlıdırlar, bu nedenle yüksek hassasiyetli parçaların üretimi için uygun hale gelirler.
2. Çinko Alaşımları
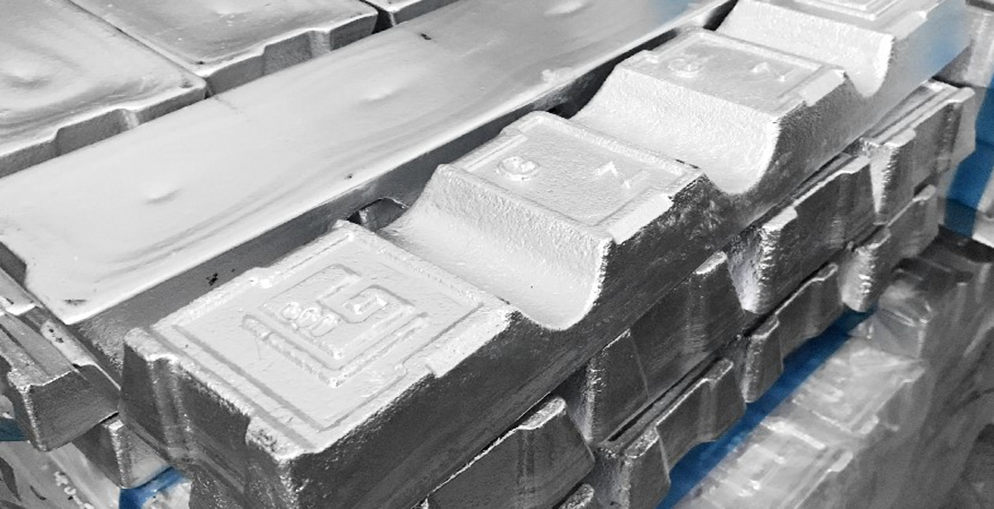
Düşük erime noktası ve yüksek akışkanlık gibi özellikleri nedeniyle tercih edilebilen çinko döküm alaşımları, ince kesitlere ve keskin detaylara sahip karmaşık tasarımların daha kolay ve verimli bir şekilde yapılmasına olanak tanır. Yüksek tokluğa sahip bu tür çinko parçalar korozyona karşı da aynı derecede dayanıklıdır ve yüksek kaliteli cilaya sahiptir. Çinko alaşımlarının bir başka uygulama alanı da otomobil ve diğer araçların yedek parça yapımı, donanım ve elektroniktir.
3. Magnezyum Alaşımları

Magnezyumun en hafif yapısal metal olduğunu ve bu nedenle otomobiller veya uçaklar için tasarlanan parçalarda önemli bir ağırlık sunduğunu belirtmek gerekir. Bunun nedeni, magnezyum alaşımlarının güçlü ancak mümkün olduğunca hafif olması gereken parçalarda kullanılmasıdır. Bununla birlikte, metal çok reaktif olduğundan, alaşım kalıp döküm işlemini üstlenirken iyi yönetilir.
4. Bakır Alaşımları
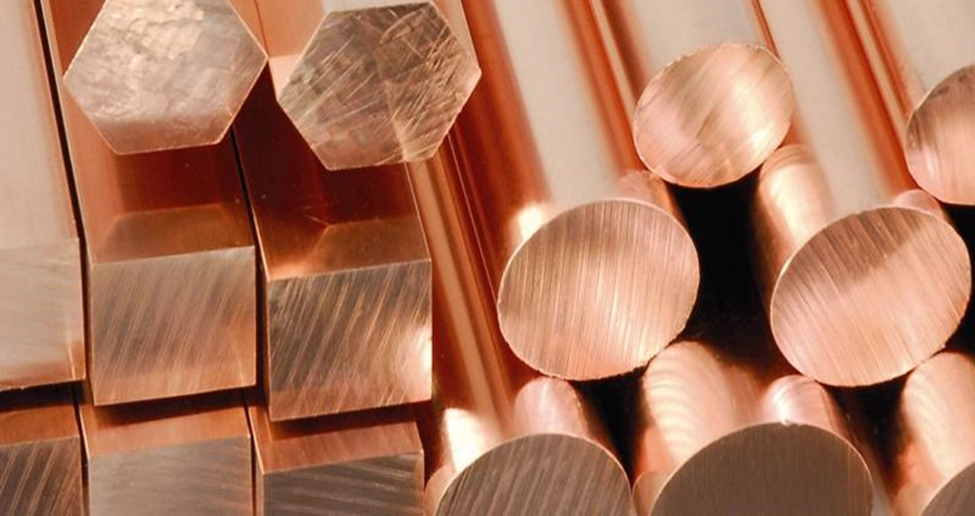
Alüminyum ve çinkonun yanı sıra, bakır bazlı alaşımlar, pirinç ve bronz da basınçlı dökümde kullanılır, ancak alüminyum ve çinko kadar sık değildir. Aşınma için iyi mukavemet özellikleri sunar ve genellikle elektrik ve sıhhi tesisat uygulamaları için kullanışlıdır.
Temel malzemelerin farklı formlarının farklı uygulamalar için uygun olduğunu ve maliyetlerin bu formlar arasında değiştiğini ve dolayısıyla nihai ürün özelliklerinin de değiştiğini belirtmek çok önemlidir.
Basınçlı Döküm ve Diğer Döküm Yöntemleri
Kum döküm, hassas döküm ve kalıcı kalıp dökümü gibi döküm yöntemleriyle karşılaştırıldığında, bu bölüm basınçlı dökümün karşılaştırma bölümü olabilir. Bunu yaparken, her yöntemin güçlü ve zayıf yönlerini vurgulamak ve okuyuculara diğer alternatifler yerine basınçlı dökümü ne zaman seçmeleri gerektiğini öğretmek akıllıca olacaktır. Bu nedenle, bu, parçanın malzemesi, karmaşıklığı ve üretim hacmine göre optimum döküm yönteminin belirlenmesine yardımcı olacak karşılaştırmalı bir genel bakış olabilir.
Özellik | Basınçlı Döküm | Kum Döküm | Yatırım Döküm |
Hassasiyet | Dar toleranslarla yüksek hassasiyet | Düşük hassasiyet ve pürüzlü yüzey kalitesi | Yüksek hassasiyet ve pürüzsüz yüzey |
Hız | Yüksek hacimli üretim için daha hızlı | Daha yavaş üretim döngüsü | Kalıp hazırlığı nedeniyle daha yavaş |
Malzeme Atıkları | Minimum atık | Daha pürüzlü yüzey nedeniyle daha yüksek atık | Minimum atık, ancak daha karmaşık kalıplar |
Maliyet | Yüksek hacimlerde uygun maliyetli | Düşük hacimli üretim için daha düşük maliyet | Karmaşıklık ve işçilik nedeniyle daha yüksek maliyetler |
Basınçlı Döküm ve Enjeksiyon Kalıplama üretim süreçleri karşılaştırılacaktır.
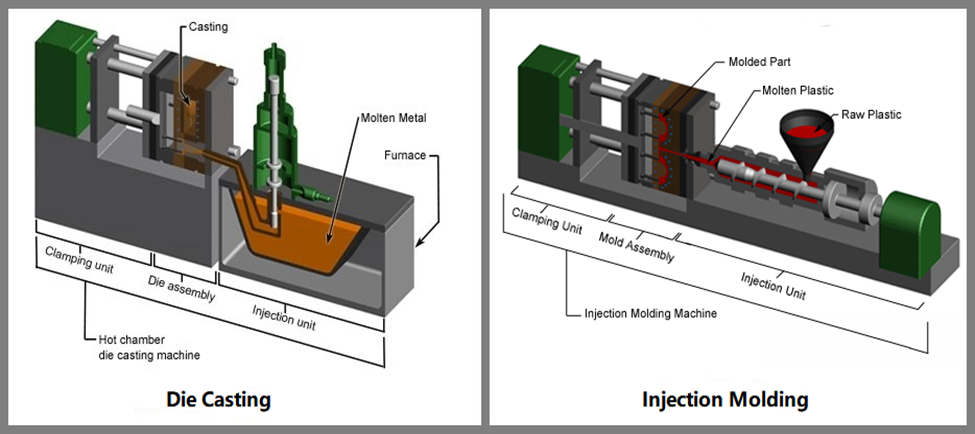
Karmaşık şekillere sahip ince detaylı parçalar yapmak için kullanılan iki yaygın teknik basınçlı döküm ve enjeksiyon kalıplamadır. Her iki teknik de nihai ürünler üretmek için malzeme şekillendirme detaylarının kullanımını içerse de, ikisi de malzeme türü, oluşturulan ürün ve özellikle her bir süreç açısından faydalar açısından farklılıklara sahiptir.
1. Kullanılan Malzemeler
Döküm: Basınçlı döküm, demirli metaller grubu dışında diğer metallerle, özellikle alüminyum, çinko, beceri ve bakır alaşımlarıyla tercih edilir. Metaller ısıtılır ve daha sonra hidrolik basınç kullanılarak bir kalıba dökülür. Bu kapsamda basınçlı döküm, güçlü, dayanıklı ve yüksek sıcaklıklara dayanabilen parçaların üretimi için en uygun yöntemdir.
Enjeksiyon kalıplama: Enjeksiyon kalıplama genellikle plastik malzemeler arasında kullanılır ve metaller ve camlar üzerinde nadiren mümkündür. Bu polimerler arasında polietilen, polipropilen ve sık kullanılan polimerler listesinde polistiren bulunmaktadır. Ürünün oluşum malzemesi de hafif ve esnektir ve buna ek olarak düşük maliyetleri ve oldukça karmaşık şekilleri vardır, bu nedenle enjeksiyon kalıplamanın bu tür ürünler için mükemmel olduğunu belirtmek mümkündür.
2. Süreç Farklılıkları
Basınçlı Döküm: Adından da anlaşılacağı gibi, erimiş metalin yüksek basınçta kalıp içine enjekte edilmesi işlemidir. Metalin çok yüksek hızda soğutulması ve katılaştırılmasından sonra, ince tolerans ve iyi yüzey kalitesi ile başka hiçbir işlem yapılmadan ortaya çıkarlar.
Enjeksiyon Kalıplama: Enjeksiyon kalıplama, erimiş plastik malzemenin basınç uygulanarak bir kalıp boşluğuna enjekte edilmesini gerektirdiğinden, bu bir enjeksiyon kalıplamadır. Erimiş plastiğin sıcaklığı düşürüldüğünde kalıp açılır ve ürün plastik kalıptır. Yine de, enjeksiyon kalıplama, basınçlı dökümle karşılaştırıldığında nispeten daha küçük ve daha hafif parçalar üretmek için yaygın olarak kullanılmasına rağmen, eşit derecede yüksek doğruluk sağlayabilir.
3. Uygulamalar
Basınçlı Döküm: Basınçlı döküm, mükemmel ısıya dayanıklı yapısı nedeniyle otomobil üretiminde, uçaklarda ve diğer elektronik ürünlerde kullanılan sert ve güçlü parçaların yapımında kullanışlıdır.
Enjeksiyon Kalıplama: Esneklik, tasarım kolaylığı ve düşük maliyetli üretimin önemli olduğu tüketici ürünleri, ambalaj, tıbbi cihazlar ve oyuncaklar üretmek için kullanılabilir.
Basınçlı döküm uygulamaları

Basınçlı dökümü birçok endüstride popüler bir üretim süreci haline getiren faktörlerden biri, oldukça karmaşık geometrilere sahip yüksek kaliteli, dayanıklı parçaların üretimine olanak sağlamasıdır. Uygulamalardan bazıları şunlardır:
1. Otomotiv Endüstrisi
Genellikle motor bileşenleri, şanzıman muhafazaları ve diğer önemli otomotiv parçaları basınçlı döküm ile yapılır. Basınçlı döküm parçalar, otomotiv endüstrisindeki zorlu uygulamalara monte edilebilecek hassasiyet ve dayanıklılığa sahiptir.
2. Elektronik Endüstrisi
Elektronik sektöründe basınçlı döküm, cep telefonları, dizüstü bilgisayarlar ve televizyonlar gibi elektronik ekipmanlar için muhafazalar üretmek için kullanılır. Bu teknik, hassas bileşenleri koruyan hafif ancak güçlü muhafazaların oluşturulmasına olanak tanır.
3. Havacılık ve Uzay Endüstrisi
Basınçlı döküm, uçak ve uzay araçları için gerekli olan yüksek mukavemetli ve hafif parçalar üretebildikleri için havacılık ve uzay imalat firmalarına büyük fayda sağlar. Basınçlı döküm parçalar, performans ve güvenliğin önemli olduğu uygulamalarda kullanılabilecek hassasiyete ve malzeme özelliklerine sahiptir.
4. Endüstriyel Ekipmanlar
Makine, alet ve diğer endüstriyel ekipmanların parçaları da basınçlı döküm ile dökülür. Karmaşık detaylara ve iyi mekanik özelliklere sahip geometrilere sahip parçalar üretebildiğinden, bu uygulamalar için iyi bir araçtır.
Sonuç
Basınçlı döküm, birçok endüstride kullanılan çok yönlü, uygun maliyetli ve verimli bir üretim sürecidir. Parça toleransları, yüzey kalitesi ve yüksek üretim oranları açısından son derece yüksek bir kaliteye sahip olması, onu günümüzün modern üretim uygulamaları için mükemmel bir üretim aracı haline getirmektedir. Yine de basınçlı döküm, otomotivden havacılığa, elektronikten endüstriyel ekipmana kadar parçalarda güç, doğruluk ve verimlilik gerektiren bu endüstrilerin çoğunun ihtiyaçlarına cevap vermektedir.
Her ne kadar teknoloji hızla gelişiyor ve muhtemelen muazzam ölçekte mükemmel metal bileşenler için bir kaynak olarak kullanılmaya devam edecek olsa da kalıp döküm. Basınçlı dökümün temellerinin daha iyi anlaşılması, mühendislik, imalat ve tasarım uzmanlarının basınçlı döküm işleminden istenen sonuç için nasıl yararlanılacağı konusunda bilinçli kararlar vermelerine yardımcı olabilir.
Basınçlı döküm hakkında SSS
1. Basınçlı döküm ve enjeksiyon kalıplama için zaman döngüsü nedir?
Belirli bir parça için döngü süresi aralığı basınçlı döküm için 15 ila 5 dakika ve enjeksiyon kalıplama için 10 ila 60 saniyedir.
2. Plastik parçalar için basınçlı döküm kullanılabilir mi?
Basınçlı döküm metal olmayanlar için kullanılmaz. Plastik parçaları üretmek için genellikle enjeksiyon kalıplama olarak bilinen teknikler kullanılır.
3. Basınçlı döküm üretim süreci için en uygun ürünler hangileridir?
Basınçlı döküm, metallerden yapılmış yüksek doğruluk derecesine sahip küçük ve ortalama büyüklükteki karmaşık parçaların üretimi için en uygun olanıdır. Üretilen mekanik ürünlerden bazıları otomobil ve otomobil parçaları ve aksesuarları, elektrikli eşya kasaları ve kılıfları, elektronik parçalar ve ekipman kasaları ve diğerleridir.
4. Basınçlı dökümün kum dökümden farkı nedir?
Yine de ikisini karşılaştırırken: Basınçlı döküm daha hassas ve kum dökümden daha az zaman alan bir süreçtir. Kum döküm büyük ve daha az karmaşık üretimler için tercih edilirken, AL döküm küçük ve karmaşık üretimler için tercih edilir çünkü daha pürüzsüz yüzeylere ve yüksek üretimlerde tipik olan daha yakın toleranslara izin verir.
5. Basınçlı dökümün maliyetini ne belirler?
Basınçlı döküm maliyetini etkileyebilecek bazı hususlar şunlardır: malzeme türü, parçanın karmaşıklığı, kalıbın tasarımı ve siparişlerin miktarı. Hafif takımlama hacme bağlıdır, yüksek hacim birim başına maliyeti düşük tutsa da, takımlamanın ilk maliyetleri yüksektir.