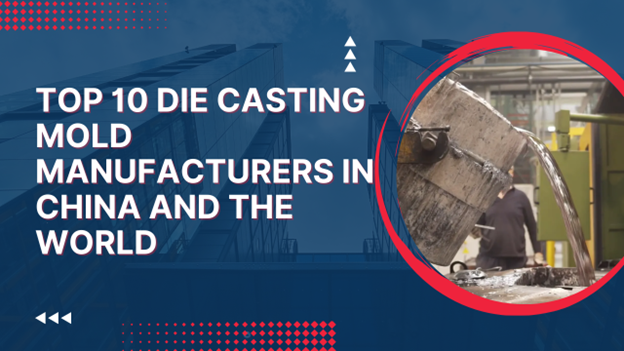
All modern industrial operations require precise manufacturing processes and high efficiency and product quality standards that become most relevant during die casting activities. Metal part formation during die casting predominantly depends on this vital element to create products with stronger performance features.
The strategic choice of fitting die casting mold manufacturers by automotive, aerospace, electronics, and consumer goods industries leads to significant business advantages through improved product performance and production efficiency, and market launch programs. The market values aluminum die casting molds because these molds offer the production of lightweight, corrosion-resistant components at high tolerances with minimal post-production requirements.
Chinese die casting mold suppliers gain business from numerous manufacturers because they offer reduced production costs and expanded industrial capabilities. Leading-edge die casting mold development occurs through Europeanand North American industrial leaders and international corporations who work with automated and bespoke solutions to redefine die casting possibilities.
The guideline performs a comprehensive assessment of primary die casting mold manufacturers operating across China and worldwide territories to aid in business partnership selection.
We choose mold manufacturing companies that demonstrate top-quality aluminum die casting abilities combined with exceptional client support under international quality standards.
What is Die Casting?
High-pressure metal injection through custom steel dies enables metal manufacturers to make precise parts as part of their production using die casting techniques. This production technique appeals to the automotive as well as aerospace industries, jointly with electronics manufacturers and consumer product producers, because it allows them to generate large quantities of precise parts with superior surfaces. Aluminum die casting molds serve as the preferred solution for making lightweight, powerful elements from aluminum and zinc, and magnesium non-ferrous metals. Engineers begin die preparation by designing molds based on precise specifications of the final product. The molten metal receives the exact dimensions of the die cavity while it solidifies at a fast rate. The manufacturing process ends with mold cooling procedures to remove the item, which can receive further operations like cutting and finishing or coating techniques. Die casting offers its maximum advantage in creating extremely difficult to copy and expensive to create intricate component designs. Industrial mass production benefits through cost-effective capabilities because molds can operate thousands of times in a single production cycle. Die casting serves manufacturers as an exceptional manufacturing approach to produce high-quality metal parts that achieve both precision and speed at low production costs.
1. Sincere Tech
Year Established: 2005
Employees: 200+
Business Type: Sincere Tech specializes in mold manufacturing, die casting molds, and aluminum die casting to provide high-quality die casting products.
Website and Contact
Website: https://www.plasticmold.net
Email: info@plasticmold.net
Phone: +86 135 30801277
Address: Building 1, No. 30 Huan Zhen Rd, Shang Dong village, Qi Shi Town, Dongguan City, Guangdong province, China, 523000
Company Profile
Sincere Tech operates as China’s top mold manufacturing company to create precise die casting molds dedicated to serving the automotive industry and electronics industry, alongside the consumer product sector. The company applies its twenty-year market knowledge to provide high-quality die casting products with advanced production systems. Sincere Tech provides customers with an entire service range that begins with mold design and extends to mold manufacturing services. The China die casting mold supplier, plasticmold.net, operates as Sincere Tech and provides reliable services to its clients. The company operates as an aluminum die casting mold specialist with magnesium and zinc die casting capabilities to provide mold making and CNC machining with complete manufacturing services.
Their Quality Commitments
For quality delivery at the company to succeed their products must pass verification by quality control systems that check for international standards compliance. The company uses organizational testing combined with inspection systems to confirm compliance of their die casting molds with quality standards across the globe. The organization benefits from both rapid development and high production speed for serving various industrial markets. The operational procedure at the company follows the fundamental requirements of ISO 9001 standards.
Why Choose Sincere Tech?
- One-stop solution from mold design to mass production
- Expertise in automotive, electronics, and industrial components
- ISO 9001:2015 certified
- The company proves its ability to create and manufacture die-casting mold components effectively.
- Sincere Tech has dedicated 18 years to producing mold elements through its die casting and injection molding services.
- The starting cost of $500 for alcohol makes it advantageous for all business types to obtain clear solutions.
- Competitive pricing with excellent quality.
- Quick lead time and rapid prototyping.
- The combination of reliable post-sales support, dependable service results in contented customers who express complete satisfaction.
- Reliable fast production times can be obtained using Multi-Cell Design technology that allows multiple cells to operate the same machines which span from 60 to 1800 tons.
2. GC Precision Mould
Year of Establishment: 1999
No of Employees: 150+
Business Type: GC Mould provides die casting mold manufacturing services exclusively for aluminum die casting and high-pressure die casting.
Website and Contact
Website: https://www.aludiecasting.com
Email: info@aludiecasting.com
Phone: +86 131 4886 5556
Address: No. 30 Huan Zhen Rd, Qi Shi Town, Dongguan City, Guangdong province China, 523516
Company Profile
GC Precision Mould operates as GC Mould to provide professional die casting mold manufacturing services exclusively for aluminum die casting molds of complex component shapes. The company serves its clients across the globe because of its superior tooling and high-pressure die casting expertise. GC Precision Mould provides die casting products manufactured from aluminum for the automotive sector and industrial market segments, alongside the electronics industry. The company implements complex solution techniques to design aluminum die casting molds that guarantee both high design detail precision and manufacturing productivity levels.
Their Quality Commitments
The company performs strict quality management checks concurrent with updating its equipment base and production materials. The company’s essential objective consists of manufacturing durable mold components that deliver accurate measurements. The production requirements at GC Precision Mould fulfil the standards of ISO 9001, resulting in sustained top-quality operational processes.
Why Choose GC Precision Mould
- The company manufactures die casting molds from start to finish as well as produces aluminum zinc magnesium die cast parts.
- The company provides services including aluminum die casting, together with zinc and magnesium die casting, grinding, and surface finishing, and secondary processing.
- Surface finishing and secondary processing
- The factory dedicates itself to aluminum die casting mold production.
- Reliable and timely deliveries.
- Competitive pricing.
- The organization provides complete service, beginning with design through manufacturing.
- The company delivers die casting and precision machining solutions from its operations that have exceeded 20 years in these industries.
- The company provides full-scale Aluminum, Zinc, Magnesium Die Casting services with CNC Machining and Plastic Injection Molding and Surface Finishing registered under Comprehensive Services.
- Modern processing gear with high-pressure-casting machines presently reaches 1650 tons of maximum production capacity.
- Alongside technical expertise, the organization gives personalized manufacturing solutions to match client requirements.
3. CNM Tech
Year of Establishment: 20+
No of Employees: 100-400
Business Type: CNM Tech is a manufacturer, supplier, and exporter specialized in manufacturing high-tolerance die casting molds while producing casts at a large scale.
Website and Contact
Website: https://www.diecastingschina.com
Email: info@diecastingschina.com
Phone: +86 130 4589 8002
Address: Rm 101, No.40, Donghu road, Jinglian, Qiaotou town, Dongguan city, Guangdong Province, China. 523520.
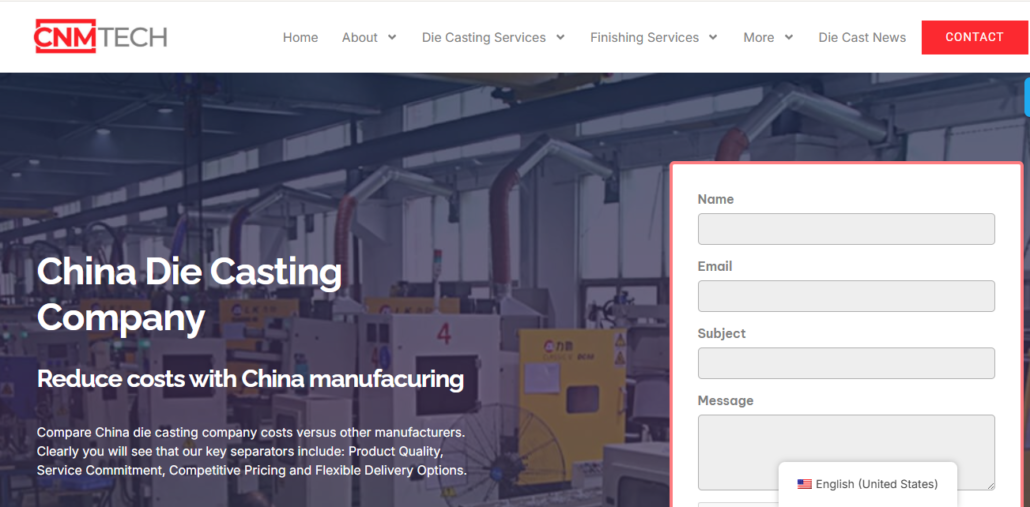
Company Profile
CNM Tech operates as an experienced China-based company specializing in manufacturing high-tolerance die casting molds while producing casts at a large scale. Through their years of manufacturing aluminum die casting molds, the company supports clients who work in aerospace and automotive, and medical sectors. CNM Tech, as a Chinese die casting mold manufacturer, leads the industry by supplying processing services through die casting molds for aluminum and zinc, and magnesium alloy materials. The company’s ten-year experience in mold making allows it to supply sturdy molds that serve the automotive, electrical, telecommunications, and home appliances markets.
Their Quality Commitments
The company follows rigorous quality requirements while dedicating itself to permanent improvement procedures. The company obtains ISO 9001 certification together with other worldwide certifications to supply products beyond rigorous requirements. Mold inspection platforms conduct a complete check of each mold before final delivery happens.
Why Choose CNM Tech?
- Strong engineering team
- Competitive pricing and global delivery
- The company focuses on producing precise, complex molds as a core component of its business operations.
- Die-casting aluminum parts are available through the extensive material options offered by the supplier.
- Exceptional customer service.
- Advanced mold-making technologies.
- Competitive prices and efficient lead times.
- The company achieved its status as a High-quality solutions provider through its twenty-five-year experience serving the die-casting industry.
- The organization provides end-to-end solution packages starting from die casting and advancing to CNC machining but avoids performing basic surface finishing or assembling processes.
- The global market selects Global Clientele first because they manage leading brands across automotive and electronics, as well as aerospace sectors and several other industries.
- The organization offers adaptable manufacturing solutions that meet specific client requirements through tailored responses.
- The factory operations at Global Clientele implement ISO 14001 standards, which allow them to operate in an environmentally friendly manner (ISO 14001, Sustainability Commitment).
4. Bruschi S.p.A.
Year of Establishment: 1948
No of Employees: 720
Business Type: Bruschi is a manufacturer and supplier that operates exclusively in zinc and aluminum die casting molds for industrial sectors.
Website and Contact
Website: https://www.bruschitech.com/
Email: info@bruschitech.com
Phone: 02 94 01 841
Address: Via Brisconno, 8 – 20081, Abbiategrasso – Milano, Italy
Company Profile
The European metal mold manufacturer Bruschi operates exclusively in zinc and aluminum die casting molds for industrial sectors as well as consumer markets. Our acquired top industrial technologies enable us to enhance the value of commissioned products by delivering innovative standards to our clients. Our organization performs multiple research and development operations on zinc products and industrial design applications. Our business maintains ongoing collaboration with European universities and research institutions, including Politecnico di Milano, along with Brescia University, in addition to Zink International Associations in Brussels.
Our research links with industry allow us to provide a top-level service throughout the production cycle as well as design development from initial stages to complete finished products.
Their Quality Commitments
Throughout 75 years, our company has focused on the industrial production of zinc die casting components. Our company established itself as a leading die caster because we excel at efficiency and precision, and maintain strong capabilities of customer feedback and continuous design and technical innovation. Our company breaks away from others through its proven solution capabilities, which enhance both the quality level and performance of industrial zinc alloy components while simplifying their integration into advanced structures.
Bruschi sets itself apart through its daily dedication, which surpasses customer requirements related to quality standards and innovation needs. Our business strategy centers around bringing customer requirements to the forefront: the various demands that your company needs regarding zinc die-casting design and manufacturing processes, together with all final finishing requirements.
Why Choose Bruschi?
- Advanced automation and Industry 4.0 integration
- Exceptional design-to-production pipeline
- Sustainability-driven production
- Yearly production volume consists of 6500 tons of zinc alloy.
5. DyCast Specialties Corporation
Year of Establishment: 1983
No of Employees: 100-300
Business Type: DyCast Specialities is a leading mold manufacturer that provides premium aluminum and zinc die-cast components.
Website and Contact
Website: dycastspec.com
Phone: +1 320-239-4799
Address: 29468 MN-28, Starbuck, MN 56381, United States
Company Profile
DyCast Specialties stands as a leading mold manufacturer in the United States that provides premium aluminum and zinc die-cast components. The company stands as a popular die casting mold supplier in North America because of its commitment to achieving stringent tolerances and exceptional finishes. The die casting mold development process at DyCast Specialties Corporation starts with engineering and continues with design before manufacturing precise die casting molds. Specialized die-casting services operated by DyCast Specialties Corporation gain recognition for serving automobile manufacturers and the markets of electronics alongside heavy-duty machines.
Their Quality Commitments
DyCast Specialties Corporation earned ISO 9001 certification to demonstrate that they would deliver excellent products through their standardization process. DyCast’s complete quality management system enables the company to produce every mold with exact specifications by consistently enhancing its production standards.
Why Choose DyCast Specialties Corporation?
- ISO 9001 certified
- On-time delivery with lean manufacturing practices
- High-performance casting alloys
- The company possesses extensive die casting expertise while delivering precise die casting services.
- Advanced manufacturing technologies.
- Strong commitment to quality and customer satisfaction.
- The business offers tailored die casting services that benefit various industrial markets.
6. Frech GmbH & Co. KG
Year of Establishment: 1949
No of Employees: 800
Business Type: Manufacturer, Supplier
Website and Contact
Website: https://www.frech.com
Phone: +49 (0) 7181 – 70 20
Email: info@frech.com
Address: Schorndorfer Straße 32, 73614 Schorndorf
Company Profile
Experimental findings indicate that France is well known as both a die casting mold manufacturer and a die casting machine producer. The company’s molds together with their machinery serve worldwide customers particularly in the manufacturing of premium aluminum die casting molds.
Their Quality Commitments
Frech GmbH & Co. KG remains globally known for its permanent dedication to innovation alongside precision and quality in die casting business operations. To lead the industry, Frech invests deeply in system development by applying state-of-the-art German engineering to produce die casting machines that operate with reliable, high-performance output. Every project at the company demonstrates full traceability and repeatability while achieving customer satisfaction because they follow ISO 9001-certified quality management standards that guide their operations. The real-world performance testing and validation at Frech laboratories occur directly in the company’s development and testing facilities before each machine goes to the client. Every French product benefits from long-term operation through their highly qualified specialists who maintain a worldwide network of international service bases.
Why Choose Frech GmbH & Co. KG?
- The manufacturing sector depends on German Engineering Excellence which provides advanced precision devices alongside dependable reliability features as well as state-of-the-art die casting technology innovation.
- Complete Die Casting Solutions – Offers both cold chamber and hot chamber machines for aluminum, zinc, and magnesium applications.
- The company provides industrial-specific solutions that adapt to the particular requirements of automotive production, along with electronics and medical sectors.
- Energy Efficiency & Sustainability – Focus on resource-saving operations and energy-optimized machine designs.
- Machines within their product line showcase rapid cycling with dependable operation at all times and low maintenance requirements.
- Global Presence & Support – Worldwide service network with fast spare parts delivery and expert technical support.
- The organization provides complete training programs with sustained collaborative partnerships to boost customer achievement.
- Smart Automation & Control – Advanced machine control systems and Industry 4.0 integration capabilities for modern production environments.
7. Granges AB
Year of Establishment: 1896
No of Employees: 2700+
Business Type: Manufacturer, Supplier
Website and Contact
Website: https://www.granges.com/
Email: info@granges.com
Phone: +46 84 59 59 00
Address: Linnégatan 18 114 47 Stockholm, Sweden
Company Profile
As an international industry leader, the company delivers aluminum rolling operations together with recycling solutions through circular industrial approaches in various economic sectors. Through six manufacturing sites around the world, the company produces materials that serve automotive heat exchangers and HVAC units, as well as special packaging components for industrial systems and electrification systems. Sustainability measures enable the company to pursue zero emissions because they endorse eco-friendly aluminum products. Stockholm, Sweden serves as the headquarters where this company directs its operations while covering Europe and the Americas, and Asia through its business activities. Jörgen Rosengren leads Gränges in his role as CEO to direct the company through innovation while focusing on efficiency and responsible business operations.
Their Quality Commitments
Multiple accreditations confirm that Gränges follows standards while proving its dedication to high-quality and sustainability as well as safety initiatives. The complete manufacturing network maintains dual accreditation as elements within the framework of ISO 9001 (quality) / ISO 14001 (environmental) systems. The majority of Gränges sites hold dual certifications of ISO 5000,1 energy standards together with ISO 45001 safety standards. All certifications operating under IATF 16949 and ASI sustainability prove Gränges’ environmental dedication to aluminum production and sustainability initiatives.
Why Choose Granges AB?
- High-quality standards and quick turnaround times.
- Extensive industry experience.
- Advanced manufacturing capabilities.
- The company occupies a primary status as a worldwide leader in aluminum solutions while employing experienced management for diverse aluminum rolling and recycling approaches.
- The company supplies aluminum solutions to automotive sectors and also serves HVAC electrical industries together with industrial applications and packaging operations.
- Innovative and Technologically Advanced – Invests in R&D for energy-efficient and high-performance materials.
- Through its Customer Relates approach, the company helps customers resolve their exclusive problems.
- Global Manufacturing Network – Operates production facilities across Asia, Europe, and the Americas.
- Efficient Supply Chain and Logistics – Ensures reliable, timely delivery of products worldwide.
8. Constellium SE
Year of Establishment: 2011
No of Employees: 12000-14000+ worldwide
Business Type: Manufacturer, Supplier
Website and Contact
Website: https://www.constellium.com/
Email: communications@constellium.com
Phone: +1 (226) 363 0100
Address: Astrex Inc. 383 Patillo Road, Lakeshore, Ontario N8N 2M1, Canada
Company Profile
The worldwide leader, Constellium SE, started its operations in 2011 in Paris to produce aluminum rolled and extruded products at its headquarters. The company holds operations in 28 production sites worldwide and maintains 12,000 staff members while delivering solutions for aerospace, military defense sectors, as well as automotive manufacturing and packaging services. The organization operates the CTEC research center to advance aluminum alloy development through its management. As the Aluminum Stewardship Initiative’s founding member, Constellium participates because this collective champions sustainability principles and material recycling initiatives. The leading marketplace player achieved $7.3 billion of revenue through 2024 because it maintained a dominating marketplace status.
Their Quality Commitments
Constellium SE enhances its commitments for quality management alongside sustainability practices as well as operational achievement standards across all aspects of its operations. Constellium SE holds ASI Aluminum Stewardship Initiative (ASI) Performance Standard Certification and multiple environmental and operational, and safety certifications, which include ISO 14001, 50001, 45001, and IATF 16949. Customers can trust Constellium SE for product quality and innovative service delivery because the company receives an EcoVadis (2024) Gold Rating, which positions it within the global top 2% while rigorously controlling quality together with sustainable operations.
Why Choose Constellium SE?
- The organization provides die casting mold services for both ferrous materials alongside non-ferrous materials.
- ISO certified for quality assurance.
- Expertise in complex mold designs.
- Reliable and cost-effective solutions.
- Through its 28 manufacturing facilities Constellium operates as a Global Leader in Aluminum Solutions to provide high-performance aluminum products for aerospace and automotive as well as packaging and defensive and industrial sectors.
- C-TEC Research Center of Advanced Research & Innovation conducts research-based activities for aluminum alloy developments and lightweight production alongside recycling technology advancement.
- The Aluminum Stewardship Initiative (ASI) selects Constellium as its co-founder to head sustainability and recycling efforts with a 23 billion can collection history that supports eco-friendly production development.
- The organization combines personal solution development with secure supply networks and specialized expertise to make sure customers receive quick and responsive solutions.
9. Arconic
Year of Establishment: 1888
No of Employees: 700
Business Type: Manufacturer, Supplier
Website and Contact
Website: https://www.arconic.com/hungary-en
Phone: +36-22-531-200
Address: Székesfehérvár 1-15 Verseci Street 8000, HUNGARY
Company Profile
The United States operates Arconic Corporation as its leading industrial manufacturer dedicated to lightweight metal engineering and manufacturing. Pittsburgh, Pennsylvania serves as the base where the primary headquarters of this company functions to produce exceptional aluminum products that meet requirements in aerospace and automotive sectors, together with the needs of transportation sectors and construction applications. From its establishment before independence in 2016 until 2020, Arconic served as an integral part of Alcoa Inc. before the company separated and underwent restructuring. The official announcement describes Arconic as a global market leader building aluminum sheets and plates, with its focus on developing innovative, sustainable products. Since Apollo Global Management purchased the company in 2023, Arconic has been developing modern industry-grade aluminum solutions of high quality.
Their Quality Commitments
Each facility under Arconic Corporation operates through exacting management systems backed by steady improvement procedures to earn top-quality certifications as well as multiple other standards, including ISO 9001:2015. The company bases its operations on three core values of integrity, through which it achieves operational excellence and customer loyalty through continuous research and development investments as well as collaborative solutions development. Arconic uses both groundbreaking innovation and full compliance for its aluminum products to deliver attainable performance excellence alongside reliability and sustainability across numerous industries.
Why Choose Arconic?
- The company provides specialized aluminum die casting mold production services.
- The business produces lightweight, ht durable molds as its main focus.
- Competitive pricing with superior quality.
- Custom solutions for various industries.
- The aerospace industry together with automotive and construction sectors utilize Arconic to achieve their light-weight aluminum needs for engineering lightweight metals manufacturing.
- The Company structures its operations through developing customized solutions that allow for prolonged client relationship maintenance.
- Operational energy efficiency stands as the key manufacturing goal at Arconic since it combines energy efficiency with environmental preservation in production operations.
- Arconic uses integrity operational excellence and customer loyalty as core values to achieve superior deliveries of products and services for its customers.
10. Alcoa
Year of Establishment: 1888
No of Employees: 13600+
Business Type: Manufacturer, Supplier
Website and Contact
Website: https://www.alcoa.com/
Phone: (+354) 470 7700
Address: Alcoa Fjarðaál Hrauni 1 730 Reyðarfjörður Iceland
Company Profile
Alcoa Corporation was founded by Charles Martin Hall in 1888 and has grown into the worldwide industry leader of bauxite alumina and aluminum production until today. The global corporation Alcoa operates from Pittsburgh, Pennsylvania, and serves aerospace aerospace automotive, packaging, construction, and commercial transportation sectors with aluminum products distributed across 10 international locations, including its headquarters. The organization achieves superior environmental standing through its unified approach of worldwide consciousness and responsibility for the environment. The total aluminum production output reached 2.5 million metric tons alongside 9.5 million metric tons of alumina production at Alcoa in 2024.
Their Quality Commitments
The environmental management and safety certifications, along with quality certifications of Alcoa Corporation, stem from its ISO 14001, 45001, and 9001 accreditations. ASI Performance Standard certifications have been obtained for all major global facilities Alcoa Corporation operates through, while the ASM (entity) Performance Standard certifications were granted to the company as well. EcoVadis Gold Rating from 2024 positioned Alcoa as one of the highest-performing companies worldwide that showcases substantial dedication to sustainability principles and manufacturing excellence.
Why Choose Alcoa?
- The company demonstrates special expertise in constructing precise die casting molds.
- Advanced manufacturing technologies.
- Custom solutions for complex requirements.
- Reliable and efficient service.
- The company operates globally through its 135-year span as an industry leader to produce bauxite and alumina, and aluminum.
- EcoVadis granted the Gold Rating for Sustainability & Innovation to Alcoa (2024) since the company belongs to the top 5% worldwide while actively working to reduce aluminum production and recycling emissions.
- Elysis carbon-free smelting technology represents an innovative process that the organization uses to fund its green aluminum production advancement.
- The company operates worldwide distribution and supports top quality solutions via ten countries to serve aerospace and automotive requirements as well as packaging and industrial uses.
Conclusion
One of the crucial factors of the metal casting world is being die casting molds to ensure product quality, consistency, and cost efficiency in the highly competitive and precision-driven world. There is no doubt that when you are attempting to make your die-cast parts for automotive, aerospace, consumer electronics, or industrial applications, the right die casting mold manufacturer plays a big role in your endeavor’s lifespan in production or not. Some of the leading players, including Frech GmbH & Co. KG, DyCast Specialties Corporation, Sincere Tech, GC Precision Mould, CNM Tech, and other older Chinese suppliers, have been recognized for their stability, precision, global presence, potential for growth, as well as loyalty towards innovation and after-sales. Aluminum die casting molds and other non-ferrous metals are manufactured with the aid of advanced technologies, detailed machine designs, and dependable support systems so that they can be relied on to make complex, high-performance parts. Whether you’re after a Chinese die casting mold production specialist, or perhaps the best there is in German engineering, whatever it is you need in terms of die casting industry expertise, you will find only experts of the first league with precision, value, and efficiency like no other.