
Turnarea și turnarea sub presiune sunt două procese de fabricație importante care sunt vitale pentru realizarea componentelor metalice cu precizia, durabilitatea și eficiența dorite. Turnarea presupune trecerea materialului topit într-o matriță și lăsarea acestuia să se răcească și să se solidifice. Turnarea în nisip, turnarea în investiție și turnarea în matriță permanentă sunt câteva tipuri de turnare. Cu toate acestea, turnarea sub presiune este o turnare specială care utilizează presiune ridicată pentru a injecta metal topit într-o cavitate de matriță cu o precizie ridicată și un finisaj de suprafață bun. Pentru aplicațiile din industria auto, aerospațială, electronică și alte industrii conexe în care sunt necesare piese ușoare, puternice, rezistente la coroziune, turnarea sub presiune este utilizată pe scară largă. De-a lungul timpului, au fost dezvoltate diferite variante de turnare sub presiune pentru a răspunde diferitelor nevoi ale industriilor. Gravity Die Casting (GDC) depinde de gravitație pentru a umple matrița, iar Low Pressure Die Casting (LPDC) elimină turbulențele pentru a obține o calitate superioară a integrității materialului. Presiunea extremă aplicată prin turnarea sub presiune (Squeeze Die Casting) creează piese de înaltă rezistență, fără porozități, iar aerul prins este eliminat în turnarea sub vid (Vacuum Die Casting) pentru a obține o componentă fără defecte. În plus, turnarea semisolidă sub presiune (Rheocasting) se realizează prin utilizarea metalului parțial solidificat pentru a îmbunătăți proprietățile mecanice și precizia.termenul general de turnare în producție este utilizat pentru a se referi la forma de modelare a metalului prin umplerea acestuia într-o matriță și lăsarea sa să se solidifice. Această metodă este frecvent utilizată în turnarea în nisip, turnarea în investiție și turnarea în matriță permanentă. Matrița în turnarea sub presiune este matrița metalică utilizată în procesul de turnare sub înaltă presiune, în timp ce matrița în procesul de turnare sub presiune înseamnă matrița metalică atașată la fața matriței. De obicei, se realizează matrițe din oțel călit, concepute pentru producția de masă.
Acest articol va aborda conceptele din spatele turnării și turnării sub presiune, diferențele dintre aceste două concepte și, de asemenea, despre tipurile fiecăruia, aplicațiile posibile ale celor de mai sus, precum și avantajele și dezavantajele asociate cu turnarea acestui proces.
1. Ce este turnarea?
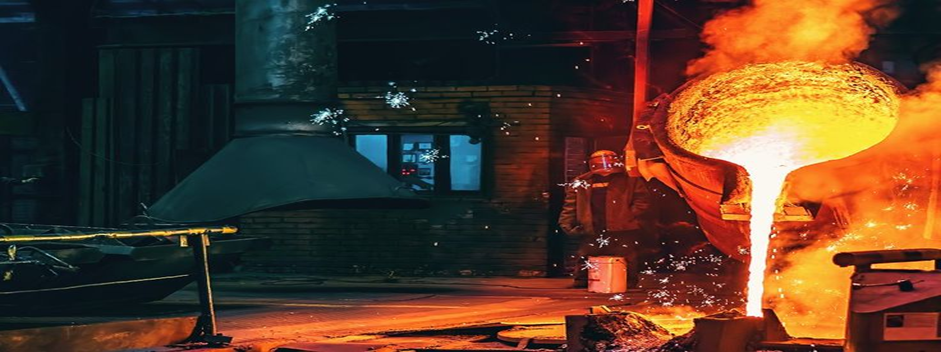
Turnarea este un proces industrial prin care un material lichid este forțat să intre într-o matriță, unde se solidifică. Lichidul poate fi practic orice metal sau plastic sau alt material topibil. După întărire, materialul capătă o formă corespunzătoare cavității matriței. În ultimele câteva mii de ani, prin utilizarea acestei tehnici s-au creat unelte, arme și sculpturi complicate.
Procesul de turnare
Câteva dintre aceste etape joacă un rol esențial în natura procesului de turnare pentru o componentă din metal sau plastic.
- 1. Se realizează un model al produsului final din lemn, plastic sau metal. Pe baza acestui model se determină forma și dimensiunile cavității matriței.
- 2. În pregătirea matriței, cavitatea matriței este proiectată în funcție de model. Metoda de turnare va determina dacă aceasta este realizată din nisip, metal sau ceramică. Sunt încorporate în mod corespunzător sistemele de ventilație și de închidere pentru a permite curgerea lină a materialului topit.
- 3. Această topire a materiei prime, de obicei metal sau plastic, la o temperatură ridicată într-un cuptor. Temperatura specifică tipului de material utilizat este diferită.
- 4. Materialul topit este turnat cu grijă în cavitatea matriței în cantitatea corectă pentru a evita defectele, deoarece turnarea este uniformă. Pentru aceasta se pot utiliza sisteme de turnare manuale sau automate.
- 5. Solidificarea - Materialul se răcește și se solidifică în interiorul matriței, formând forma cavității. Se știe că rata de răcire este cea care afectează proprietățile finale ale produsului turnat.
- 6. După solidificare, piesa turnată este scoasă din matriță, materialul în exces, cum ar fi porțile, patinele de alunecare sau brizura, este tăiat și apoi ansamblul este supus procesului de îndepărtare și finisare. Ulterior, acestea pot fi supuse unor procese de finisare suplimentare, cum ar fi măcinarea, lustruirea sau tratamentul termic, pentru a aduce o îmbunătățire a aspectului și a proprietăților mecanice ale produsului final.
Cu această abordare structurată, turnarea se face cu mai multă fiabilitate și calitate.
2. Ce este turnarea sub presiune?
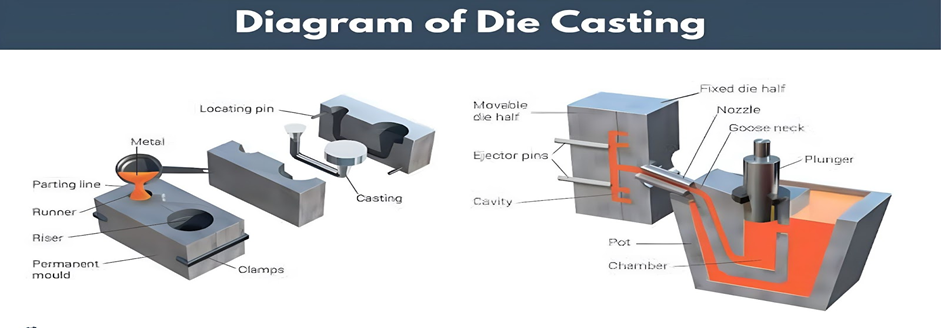
Matrițe înseamnă matrițe, de unde și numele procesului de turnare sub presiune în care un metal topit este forțat sub presiune ridicată pentru a umple o cavitate de matriță. Este cel mai potrivit pentru realizarea de piese de volum mare, complexe și precise din punct de vedere dimensional.
Procesul de turnare sub presiune
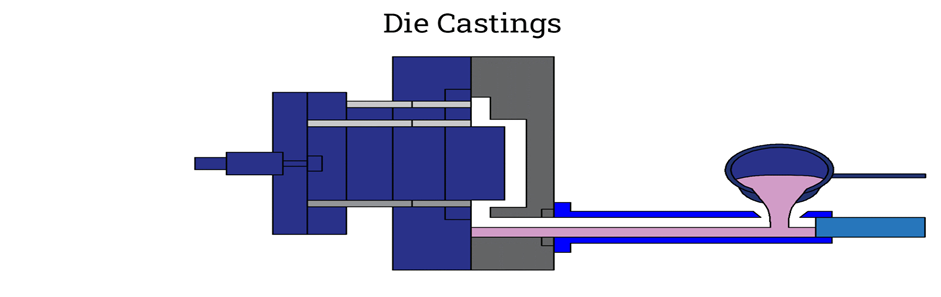
Turnarea sub presiune este un proces de fabricație în care componentele metalice sunt formate în forma cavității unei matrițe sub presiune ridicată, necesitând în același timp o precizie ridicată și o precizie dimensională exactă și un finisaj de suprafață. Aceasta este o urmare a pașilor de mai jos:
- 1. Injectarea metalului topit - Se aplică o presiune ridicată cuprinsă între 1.500 și 25.000 psi pentru a injecta metal topit (cum ar fi aluminiu, zinc sau magneziu) într-o matriță de oțel (matriță), care topește metalul selectat într-un cuptor. Acest lucru va umple fiecare detaliu al matriței cu metalul topit.
- 2. Matriță sau matriță - Metalul topit se răcește cu adevărat și se solidifică în matriță, rezultând o piesă puternică și precisă. Proprietățile mecanice ale produsului final depind de rata de răcire.
- 3. Ejectare și tăiere - După solidificare, piesa turnată este ejectată din matriță cu ajutorul știfturilor ejectoare. Materialul în exces, inclusiv bavura, patinele și porțile, este tăiat la forma dorită.
- 4. Finisarea suprafeței - În funcție de aplicație, este posibil ca piesele turnate să necesite o finisare suplimentară Rectificare la Nisa, lustruire, vopsire, anodizare sau acoperire cu pulbere pentru a-i spori aspectul, durabilitatea și rezistența la coroziune.
Acest proces va avea ca rezultat o rezistență ridicată, o greutate redusă, piese complexe cu procesare ulterioară redusă. Cele mai comune materiale pentru care se utilizează turnarea sub presiune includ metalele neferoase, cum ar fi aluminiul, zincul și magneziul.
Tipuri de procese de turnare
Există diferite tipuri de turnare în funcție de tipul de metodă utilizată
1 Sand Casting

- Este una dintre cele mai versatile și mai economice metode de turnare cu ajutorul matrițelor de nisip.
- Comun în industria auto, aerospațială și artistică.
2 Turnare de investiții
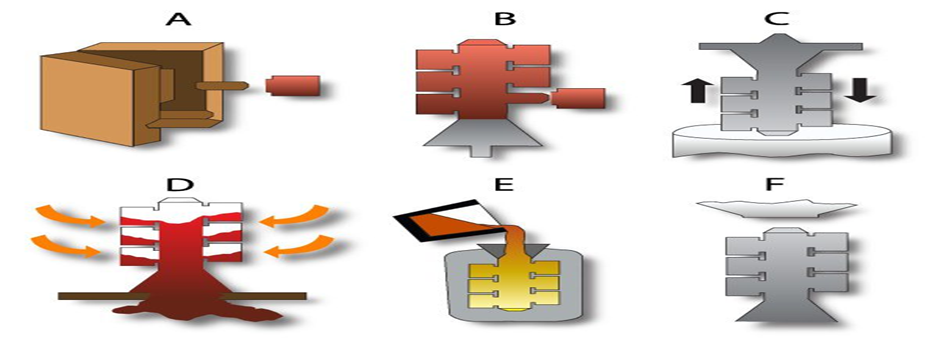
- Cunoscută și sub denumirea de turnare cu ceară pierdută, această metodă produce piese extrem de detaliate și complexe.
- Pentru utilizare ca bijuterii, implanturi medicale și componente aerospațiale.
3 Turnare centrifugă

- Aceasta implică rotirea unei matrițe pentru a integra bine metalul topit.
- Utilizat în mod obișnuit pentru fabricarea țevilor, cilindrilor și inelelor.
4 Turnarea permanentă a matrițelor
- Reducerea deșeurilor și a utilizării matrițelor prin reutilizare.
- Este ideal pentru producția repetată de piese metalice de înaltă calitate.
Tipuri de turnare sub presiune
Există în principal două modalități de turnare sub presiune:
1. Turnare sub presiune cu cameră fierbinte
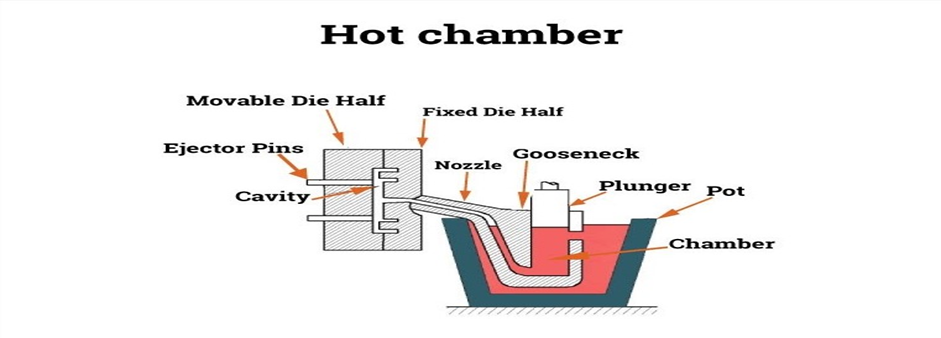
- Se utilizează pentru metale cu punct de topire scăzut, cum ar fi zincul și magneziul.
- Proces mai rapid cu rate de producție mai mari.
2. Turnare sub presiune cu cameră rece

- Este utilizat pentru metale cu punct de topire ridicat, cum ar fi aluminiul și alama.
- Încetinește etapele de topire și injectare, fiind potrivit pentru piese durabile.
5. Diferențe între turnare și turnare sub presiune
Caracteristică | Turnare | Turnare sub presiune |
proces | Matriță Metal turnat în ea | Metalul topit este injectat sub presiune ridicată |
Materiale | Diverse metale și materiale plastice | În principal metale neferoase, cum ar fi aluminiul și zincul |
Precizie | Moderat | Precizie ridicată |
cost | Cost inițial redus | Costuri inițiale ridicate pentru scule |
Aplicații | Piese mari și simple | Piese mici, complexe, cu volum mare |
Aplicații de turnare și turnare sub presiune

Turnarea și turnarea sub presiune, în felul lor, au roluri imense în diferite industrii și sunt rentabile, deoarece facilitează fabricarea de componente metalice complexe cu o precizie excelentă.
- În industria automobilelor se produc blocuri motor, carcase de transmisie, butuci de roți, piese de frână și de suspensie. În ceea ce privește piesele ușoare din aluminiu, turnarea sub presiune este deosebit de favorizată în acest scop, deoarece îndeplinește niveluri mai ridicate de eficiență a consumului de combustibil.
- Industria aerospațială: Componentele aerospațiale, cum ar fi paletele turbinei, componentele structurale ale fuselajului, carcasele și componentele trenului de aterizare sunt turnate pentru a fi durabile și puternice, dar în același timp ușoare.
- În electronică, turnarea și turnarea sub presiune sunt esențiale, deoarece sunt necesare carcase și componente de turnare sub presiune, cum ar fi radiatoare, conectori și dispozitive de ecranare, pentru a expulza căldura și a oferi siguranță circuitelor electronice fragile.
- Construcții - Țevi, fitinguri, suporturi, supape și balustrade pentru construcția de clădiri, poduri etc. care asigură stabilitate structurală și longevitate.
- Echipamente medicale - Componentele turnate cu precizie sunt utilizate pe scară largă în domeniul medical pentru instrumente chirurgicale, carcase de echipamente de imagistică, implanturi ortopedice etc.
- Mașini industriale - Turnarea este necesară pentru a oferi rezistență și rezistență la uzură în cutii de viteze, pompe și alte piese de mașini grele care lucrează în condiții dificile.
Aplicarea turnării și a turnării sub presiune este larg răspândită și, prin urmare, acestea sunt componente indispensabile ale industriilor moderne de producție.
Variante de turnare sub presiune
Unul dintre cele mai populare procese de fabricație este turnarea sub presiune, în care metalul topit ajunge în matriță pentru a produce componente cu caracteristici complexe și prescrise. Diferite variante de turnare sub presiune au fost dezvoltate de-a lungul timpului pentru a se adapta materialelor, cerințelor de producție, precum și standardelor de calitate. Fiecare metodă are avantajele sale și va fi mai mult sau mai puțin potrivită pentru diferite tipuri de aplicații. În continuare sunt prezentate principalele variante de turnare sub presiune, cu procesul și avantajele aferente.
Gravity Die Casting (GDC)
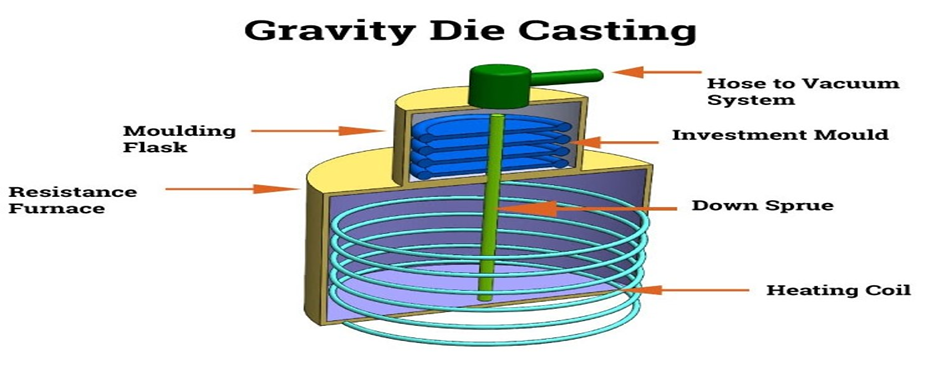
Prezentare generală
Gravity Die Casting (GDC) are ca aplicație turnarea metalului topit într-o matriță fără utilizarea unei presiuni ridicate. Mai degrabă, gravitația ajută la ghidarea metalului în umplerea cavității și la organizarea sa, ca și cum ar fi de la sine. Acest proces este preferat pentru aliajele cu puncte de topire scăzute și este utilizat în mod obișnuit atunci când se dorește un proces de solidificare mai controlat.
Caracteristici principale
- Este mai eficientă decât turnarea în nisip, deoarece utilizează matrițe reutilizabile.
- Mai lent decât turnarea sub presiune, dar piesa este mai rezistentă datorită formei mai dense.
- Limitat la anumite aliaje, cum ar fi aluminiul și magneziul.
Aplicații comune
- Componente auto (capete de cilindri, piese de motor).
- Racorduri pentru țevi și corpuri de supape.
- Mașini industriale și părți structurale.
Turnare sub presiune joasă (LPDC - Low-Pressure Die Casting)

Prezentare generală
Turnarea sub presiune scăzută (LPDC) este atunci când metalul topit este presurizat în matriță sub presiune scăzută, de ordinul a 0,1-1 MPa. Prin această umplere controlată, turbulențele sunt reduse la minimum, iar curgerea este mai lină, menținând astfel aceste defecte la un nivel minim, cum ar fi buzunarele de aer și incluziunile.
Caracteristici principale
- Integritate mai bună a materialului datorită turbulențelor reduse.
- Opțiunea este potrivită pentru piese mari, complexe, care necesită o rezistență structurală ridicată.
- Este fiabil (calitate constantă) în cazul producției în masă.
Aplicații comune
- Jante din aluminiu pentru automobile.
- Piese structurale pentru aeronave.
- Componente rezistente la căldură în utilajele industriale.
Squeeze Die Casting

Prezentare generală
În procesul de turnare Squeezedie, se impune o presiune ridicată asupra metalului topit din interiorul cavității matriței. Deoarece forța aplicată se extinde la mai mult de 20.000 psi (lire pe inch pătrat), metalul umple chiar și cele mai fine detalii ale matriței și elimină porozitatea.
Caracteristici principale
- Creează piese extrem de dense și rezistente.
- Reduce porozitatea și oferă proprietăți mecanice mai bune.
- Aplicabil în aplicații cu rezistență ridicată, unde durabilitatea este importantă.
Aplicații comune
- Componente de suspensie pentru automobile.
- Piese aerospațiale de înaltă performanță.
- Unelte și echipamente industriale grele.
Turnare sub presiune în vid

Prezentare generală
Turnarea sub presiune în vid își folosește designul pentru a evacua aerul și gazele prinse în cavitatea matriței înainte și în timpul procesului de turnare. Această metodă este implementată prin crearea unui vid și realizează o reducere semnificativă a porozității, care este un defect comun în turnarea sub presiune standard. Rezultatul este o turnare mai precisă, mai puternică și fără defecte.
Caracteristici principale
- Îmbunătățește proprietățile mecanice ale produsului final.
- Minimizează captarea aerului, ceea ce îl face adecvat pentru piese cu pereți interiori și de înaltă precizie.
- Îmbunătățește calitatea generală a piesei turnate, reducând post-procesarea.
Aplicații comune
- Sudarea pieselor structurale ale autovehiculelor pentru a respecta durabilitatea ușoară.
- Componente pentru echipamente medicale cu precizie ridicată.
- Integritatea pieselor aerospațiale.
Turnare semisolidă sub presiune (Rheocasting)

Prezentare generală
Rheocasting sau turnarea sub presiune semisolidă utilizează metal parțial solidificat mai degrabă decât complet lichid. Acest lucru menține metalul într-o stare semilichidă sau de suspensie, prin care curge ușor în matriță și reduce turbulențele și porozitatea.
Caracteristici principale
- Produce componente cu proprietăți mecanice superioare.
- Reduce defectele de contracție și porozitatea.
- Ideal pentru piese complexe, de înaltă precizie.
Aplicații comune
- Orice piese auto care necesită rezistență ridicată și proprietăți ușoare.
- Carcase electronice cu detalii fine.
- Pentru utilaje industriale cu componente care trebuie să reziste la uzură.
Metale comune utilizate în turnarea sub presiune
Procesul de fabricație utilizat pentru injectarea metalului topit într-o matriță sub presiune ridicată este turnarea sub presiune. Metalul selectat în acest proces este, de asemenea, esențial pentru rezistența, durabilitatea și aplicarea produsului final. Diferite metale pot fi utilizate pentru o astfel de turnare, dar metalele neferoase (sau metalele fără fier) sunt cele mai utilizate de obicei, deoarece au puncte de topire mai scăzute și sunt mai turnabile.
Cele mai utilizate metale în turnarea sub presiune cu proprietățile și utilizările lor sunt menționate mai jos.
1. Aluminiu
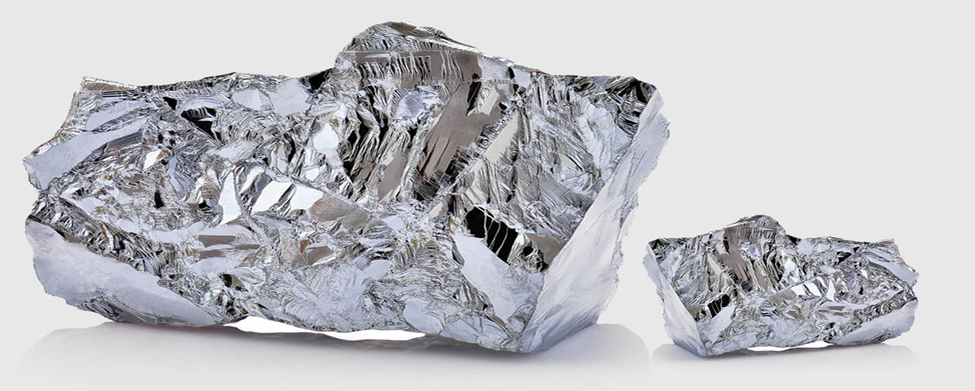
Printre metalele utilizate în turnare sub presiune, Cu toate acestea, aluminiul este cel mai utilizat și are combinația ideală de rezistență bună, greutate redusă și rezistență la coroziune. Având o densitate relativ scăzută, este un bun candidat pentru a fi utilizat în industriile în care sunt necesare componente cu densitate redusă și rezistență ridicată.
Avantajele aluminiului în turnarea sub presiune
- Este ușor și puternic, deoarece este utilizat în industria auto și aerospațială pentru a reduce greutatea.
- Rezistent la coroziune - Potrivit pentru aplicații exterioare și marine.
- Conductivitate termică și electrică bună - utilizat în carcase electronice și radiatoare.
Aplicații comune ale pieselor turnate sub presiune din aluminiu
- Blocuri de motor, carcase de transmisie, roți, etc. (piese auto).
- Componente aerospațiale (cadre de aeronave, suporturi).
- Electronice de consum (corpuri de smartphone, carcase de laptop).
Aluminiul este în mod normal turnat sub presiune prin turnare sub presiune cu cameră rece, datorită punctului său de topire ridicat.
2. Zinc
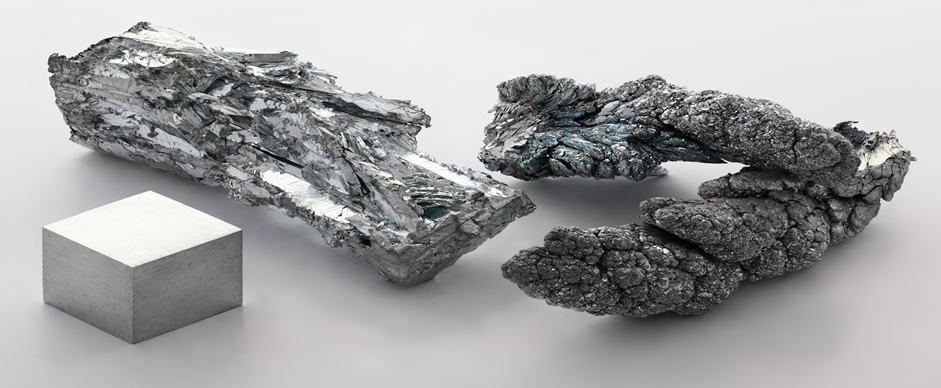
Un alt metal popular de turnare sub presiune este zincul, care este cunoscut pentru precizia sa ridicată, rezistența și ușurința de turnare. Cu toate acestea, punctul de topire mai scăzut al zincului în comparație cu aluminiul, ceea ce îl face potrivit pentru turnarea sub presiune cu cameră fierbinte și produce cicluri de producție mai rapide.
Avantajele zincului în turnarea sub presiune
- Rezistență și durabilitate ridicate - Ideal pentru componente mecanice.
- Punct de topire scăzut - Permite o producție mai rapidă și o durată de viață mai lungă a matriței.
- Finisaj bun al suprafeței - Reduce nevoia de post-procesare extensivă.
Aplicații comune ale pieselor turnate sub presiune din zinc
- Componente mecanice mici (angrenaje, elemente de fixare, balamale).
- Conectoare electrice și electronice.
- Include componente suplimentare, cum ar fi piese auto (suporturi, mânere, încuietori de uși).
În plus, zincul este mai ieftin decât aluminiul și, prin urmare, este materialul preferat în producția de piese mici.
3. Magneziu
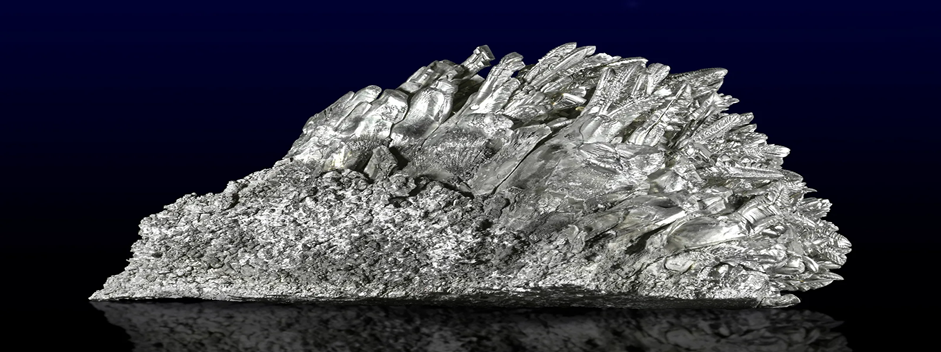
Ca metal structural pentru turnarea sub presiune, magneziul este cel mai ușor metal utilizat și oferă un raport excepțional rezistență/greutate. Cântărește cu aproximativ 30% mai puțin în comparație cu aluminiul, ceea ce îl face o opțiune bună pentru aplicațiile care necesită reducerea greutății.
Avantajele magneziului în turnarea sub presiune
- Extrem de ușor - Ideal pentru aplicații aerospațiale și auto.
- Rezistență bună și rezistență la impact - Poate rezista la solicitări mecanice.
- Este foarte ușor de prelucrat (prelucrabil) decât alte metale.
Aplicații comune ale pieselor turnate sub presiune din magneziu
- Este utilizat în industria automobilelor (volane, rame pentru tablouri de bord).
- Industria aerospațială (drone și piese pentru aeronave).
- Electronice de consum (laptopuri și aparate foto).
Deși pulberea de magneziu este foarte inflamabilă, piesele turnate sub presiune sunt suficient de stabile și sigure pentru utilizarea industrială.
4. Cupru și aliaje de cupru (alamă și bronz)

Are o conductivitate termică și electrică ridicată, iar cuprul și aliajele sale (alamă, bronz) sunt utilizate pentru aplicații electrice și sanitare datorită acestui fapt. Deși sunt mai scumpe și mai grele decât zincul și aluminiul, au o rezistență mai mare la coroziune și la uzură.
Avantajele cuprului și ale aliajelor sale în turnarea sub presiune
- Conductivitate electrică excelentă - utilizată în componente electronice și electrice.
- Este rezistent la coroziune și potrivit pentru instalații sanitare și aplicații marine.
- Rezistență superioară la uzură - Asigură o durată de viață mai mare a pieselor.
Aplicații comune ale pieselor turnate sub presiune din cupru și aliaje de cupru
- Conectori și terminale electrice.
- Fitinguri și supape.
- Componente pentru utilaje industriale.
Chiar dacă, de obicei, cuprul nu este utilizat la fel de mult ca aluminiul sau zincul în turnarea sub presiune, acesta este totuși esențial în astfel de aplicații specializate în care sunt necesare durabilitate și conductivitate ridicate.
5. De asemenea, plumb și staniu (nu prea frecvente astăzi)

Pentru aplicații specializate, turnarea sub presiune a plumbului și a staniului a fost odată foarte răspândită datorită punctelor lor de topire scăzute și rezistenței excelente la coroziune. Cu toate acestea, utilizarea lor a scăzut drastic în ultimii ani din motive de sănătate și de mediu.
Avantajele plumbului și staniului în turnarea sub presiune (istoric)
- Rezistența la coroziune este bună - este utilizat în instalațiile sanitare și în componentele bateriilor.
- Moale și maleabil - Potrivit pentru aplicații cu solicitări reduse.
- Au o densitate mare, motiv pentru care sunt utilizate în aplicații de ecranare împotriva radiațiilor și de izolare fonică.
Aplicații comune ale pieselor turnate sub presiune din plumb și staniu (acum limitată)
- Terminalele bateriei.
- Rulmenți și piese de lipire moale.
- Componente de ecranare în radioprotecție.
Pe măsură ce reglementările de mediu continuă să crească, a devenit necesar pentru producători să găsească materiale mai sigure, cum ar fi aluminiul, zincul și magneziul.
Avantaje și dezavantaje
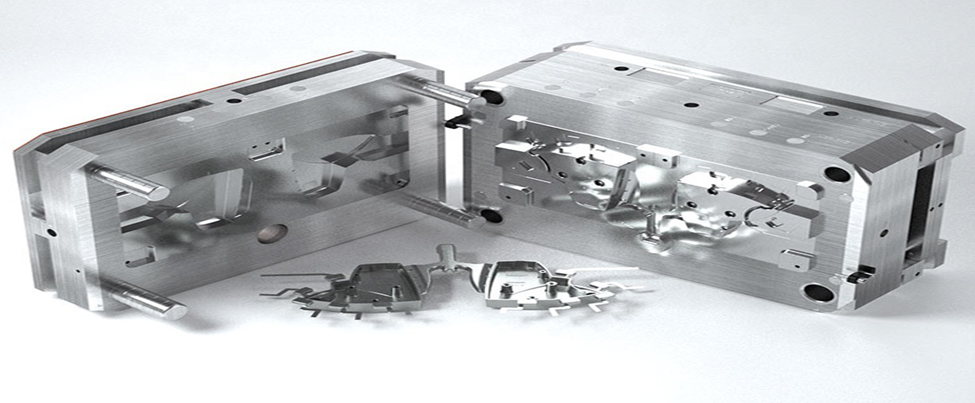
Avantajele turnării
- Preț scăzut de producție - Turnarea este o metodă de fabricație eficientă din punct de vedere al costurilor, în special pentru producții mici, deoarece este nevoie de puține scule (scule și matrițe) în comparație cu alte procese de fabricație.
- Poate realiza forme mari sau complexe - Turnarea poate crea forme care sunt greu de prelucrat la strung sau prin prelucrare, sau care sunt prea mari pentru a putea fi prelucrate.
- Toarnă o mare varietate de materiale - fier, oțel, bronz aluminiu etc.
- Utilizarea eficientă a materialelor - Turnarea nu risipește materiale deoarece metalul topit este turnat direct în matrițe și nu se pierde mult material în exces.
- Producție în masă adecvată - Odată ce matrița este stabilită, multe dintre aceleași piese pot fi produse relativ ușor.
Dezavantaje ale turnării
- Mai puțin precise decât turnarea sub presiune. Metodele tradiționale de turnare tind să producă imperfecțiuni de suprafață și variații dimensionale care trebuie prelucrate.
- Timpii de răcire mai lungi, precum și procesul de răcire și solidificare pot afecta eficiența generală a producției.
- Sunt necesare mai multe lucrări de finisare - Piesele turnate vor avea suprafețe rugoase sau material în exces (flash) care trebuie îndepărtat prin prelucrare, cum ar fi șlefuirea și lustruirea.
- Probleme legate de porozitate - Aceasta ar putea fi o problemă de buzunare de aer sau goluri care rezultă în timpul procesului de turnare și creează slăbiciuni în integritatea structurală.
- Degradarea matrițelor - Utilizarea matrițelor reutilizabile va duce, în timp, la degradarea acestor matrițe și la creșterea grosimii pereților pieselor, cu defectele de producție asociate și creșterea costurilor de întreținere.
Avantajele turnării sub presiune
- Turnarea sub presiune oferă atât producții de mare viteză, potrivite pentru volume mari de producție, cât și pentru loturi de producție mici.
- Creează piese puternice, cu dimensiuni precise - Datorită procesului de injecție la presiune ridicată, piesele ies în mod constant, cu toleranțe strânse și o calitate bună care minimizează ajustările ulterioare.
- Nu necesită multă post-procesare - Piesele turnate sub presiune au de obicei suprafețe netede și detalii curate care nu necesită prelucrare secundară.
- Turnarea sub presiune este excelentă în ceea ce privește repetabilitatea, permițând uniformitatea producției în numeroase cicluri de producție, acesta fiind motivul pentru care este o metodă preferată pentru producția de masă.
- Finisaj de suprafață bun - Nu necesită finisare, ceea ce îl face foarte potrivit pentru fabricarea produselor care au ținut cont de aspectul estetic.
Dezavantaje ale turnării sub presiune
- Cost inițial mai ridicat (matrițele sunt scumpe) - Proiectarea și fabricarea matrițelor de turnare sub presiune pot fi costisitoare și, prin urmare, nu sunt economice dacă producția este la scară mică.
- Nu este potrivit pentru metale feroase - Turnarea sub presiune este înghețată la aluminiu, zinc și magneziu, ceea ce limitează gama de materiale posibile.
- Nu este potrivit pentru piese mari sau groase - Componentele cu pereți subțiri sunt mai potrivite pentru turnarea sub presiune decât cele masive sau cu pereți groși. Turnarea sub presiune implică un proces de răcire rapidă.
- Porozitate - Este posibil ca produsul să se fi umplut cu aer în timpul procesului de turnare prin injecție și acest lucru va duce la porozitate, ceea ce face ca produsul final să fie slab.
- Mai puțină flexibilitate în modificările de proiectare - După realizarea unei matrițe, modificarea proiectării pieselor turnate va fi costisitoare și va necesita mult timp în comparație cu alte metode de turnare.
8. Viitorul turnării și al turnării sub presiune
Turnarea și turnarea sub presiune sunt promițătoare pentru viitor (cel puțin pe termen scurt) datorită automatizării și imprimării 3D. Unele tendințe cheie includ:
- Materiale ecologice - Aliaje durabile și reciclabile.
- Producție inteligentă - automatizare bazată pe inteligență artificială pentru eficiență.
- Integrarea producției aditive sub forma proceselor hibride de turnare cu imprimare 3D.
În industriile moderne, aceste inovații vor îmbunătăți productivitatea, vor reduce risipa și vor diminua costurile de producție, făcând astfel procesele de producție și mai indispensabile.
Concluzie
Din diverse industrii, procesul de producție a componentelor metalice de înaltă calitate continuă să fie unul dintre principalele procese de fabricație. Opțiunile de turnare sub presiune vin cu multe variante, fiecare oferind beneficii diferite pentru aplicații specifice. Piesele puternice și dense sunt produse prin turnarea sub presiune prin gravitație; piesele sunt solide din punct de vedere structural, cu defecte minime, prin turnarea sub presiune la joasă presiune (Low-Pressuree Die Casting). Turnarea sub presiune (Squeeze Die Casting) are o rezistență și o durabilitate minunate, în timp ce turnarea sub vid (Vacuum Die Casting) economisește porozitatea. Cu toate acestea, turnarea sub presiune semi-solidă prezintă avantaje în ceea ce privește proprietățile mecanice și precizia pentru aplicații de înaltă performanță, iar alegerea metodei de turnare sub presiune depinde de selectarea materialelor, complexitatea piesei, volumul piesei și tipul de proprietăți mecanice dorite. Procesul continuă să fie perfecționat în ceea ce privește noile evoluții în automatizare, dezvoltarea aliajelor și ingineria de precizie, ceea ce face ca utilizarea sa să fie din ce în ce mai eficientă, mai puțin costisitoare și ecologică.
Datorită cererii de componente mai ușoare, mai puternice și mai rezistente din partea industriilor, tehnologia va evolua continuu. Cu toate acestea, producătorii pot preveni performanța proastă a produselor, risipa și ineficiența producției prin alegerea metodei de turnare sub presiune adecvate. Pentru a alege cea mai bună opțiune de producție, este necesar să înțelegeți aceste variante de turnare sub presiune și să obțineți cea mai înaltă calitate, fiabilitate și eficiență în producție.
Întrebări frecvente (FAQ)
1. Cum funcționează turnarea sub presiune și în ce formă funcționează aceasta?
Turnarea metalelor prin procesul cunoscut sub numele de turnare sub presiune este un proces în care metalul topit este injectat într-o matriță sub presiune ridicată. Acest lucru permite producătorilor să producă piese metalice complexe, de înaltă precizie, cu un finisaj superb al suprafeței și foarte puține prelucrări.
2. Câte tipuri de turnare sub presiune?
Principalele forme de turnare sub presiune sunt turnarea prin gravitație (GDC), turnarea sub presiune joasă (LPDC), turnarea prin stoarcere, turnarea sub vid și turnarea semi-solidă. Diferitele avantaje și dezavantaje ale fiecărei metode depind de material și de aplicație.
3. Ce metale sunt utilizate în mod normal în procesul de turnare sub presiune?
Aluminiul, zincul, magneziul, cuprul și aliajele lor sunt cele mai frecvent utilizate metale în turnarea sub presiune. Metalul este ales pentru greutate, rezistență, rezistență la coroziune și conductivitate termică.
4. De ce turnarea sub presiune este atât de benefică?
Eficiență ridicată a producției, precizie dimensională excelentă, risipă minimă de material, finisare netedă a suprafeței și este posibil să se producă forme complexe cu o post-procesare redusă.