Turnarea sub presiune înaltă (HPDC) este unul dintre cele mai frecvent utilizate procese de turnare a metalelor în producția actuală. Producătorii aleg HPDC deoarece permite producerea de piese metalice complexe care ating atât o precizie ridicată și rate rapide de producție, cât și o precizie dimensională superioară și finisaje netede. HPDC permite industriilor auto și aerospațiale și producției de componente electronice și bunuri de consum să producă piese durabile ușoare pentru aplicații precum motoare și carcase, elemente structurale și ansambluri mecanice. Procesul de producție al turnării sub presiune de înaltă presiune se confruntă cu numeroase riscuri care creează defecte substanțiale care scad calitatea produselor, reducând în același timp durata de viață și compromițând performanța. Diferitele defecte apar ca urmare a proiectării necorespunzătoare a matriței, a curgerii turbulente a metalului topit, a gazelor captive, a ratelor de răcire inconsecvente și a stresului termic în timpul procesului de producție. Tehnologia HPDC se confruntă cu șapte defecte principale, care includ porozitatea, închiderea la rece, defectele de contracție, formarea scânteii, defectele de suprafață, erorile de execuție, eroziunea matriței și lipirea. Aceste tipuri de defecte de fabricație cauzează deteriorarea rezistenței materialului, producând în același timp dimensiuni neregulate și efecte vizuale nedorite care pot instiga la defectarea componentelor. Producătorii combat problemele de producție prin optimizarea parametrilor de prelucrare și prin metode de subminare mai bune, împreună cu sisteme de temperatură controlată și proceduri de turnare asistată de vid. Monitorizarea în timp real și software-ul de simulare sunt metode avansate de control al calității care sporesc eficiența și fiabilitatea procesului de turnare sub presiune.
Acest articol oferă o analiză cuprinzătoare a problemelor standard de fabricație în timpul proceselor de înaltă presiune turnare sub presiune cu explicații privind cauzele principale și strategiile de soluționare pentru a reduce aceste defecte. Numai prin înțelegerea acestor provocări și aplicarea celor mai bune practici, producătorii pot îmbunătăți calitatea, longevitatea și, bineînțeles, performanța componentelor lor turnate sub presiune și, în același timp, pot reduce deșeurile și costurile de producție. Cunoașterea acestor defecte de fabricație va ajuta inginerii de turnare sub presiune, managerii de producție și specialiștii în controlul calității să își optimizeze procesele pentru a obține cele mai bune rezultate în materie de turnare sub presiune.
1. Porozitatea
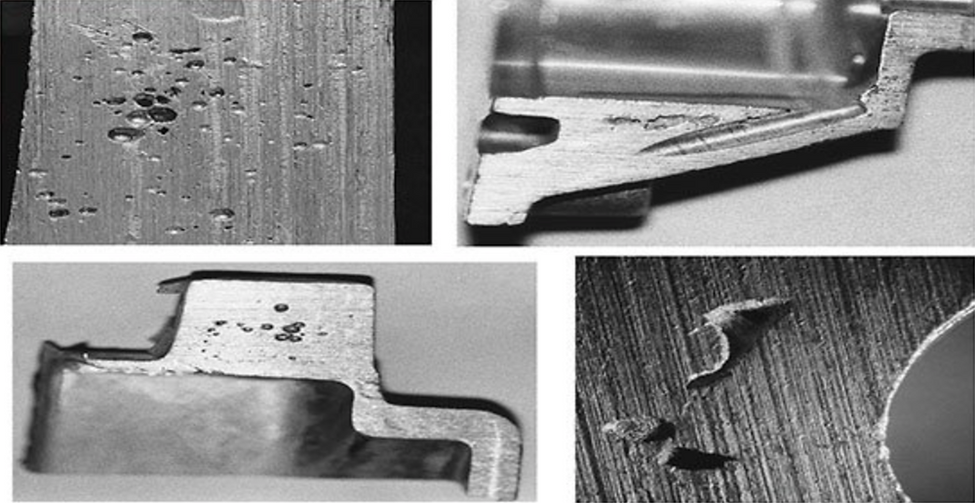
Porozitatea este definită prin găuri mici sau incluziuni de gaz găsite în matricea metalică și, ca rezultat, afectează proprietățile mecanice, reducând rezistența, permițând aerului și gazelor să treacă prin structură și ducând la defecte de suprafață vizibile în produsele turnate sub presiune.
Cauze:
- Conținut gazos care este prezent în materiale înainte de turnare.
- Turbulențe excesive în fluxul de metal topit.
- Ventilație slabă și design necorespunzător al mucegaiului.
- Solidificare rapidă care cauzează porozitate de contracție.
- Contaminarea metalului topit.
- Presiune necorespunzătoare care nu determină o curgere uniformă a metalului.
Prevenire și soluții:
- Asigurați-vă că a fost realizată o evacuare adecvată a gazelor prin proiectarea gurilor și a ventilațiilor.
- Încetiniți rata de injecție pentru a îmbunătăți netezimea metalului care intră în cavitate.
- Problema captării aerului ar trebui rezolvată prin tehnica de turnare sub presiune asistată de vid.
- Asigurați-vă că metalul topit este suficient degazat înainte de a fi injectat.
- Controlul ratei de răcire pentru a depăși problema fisurilor și a formării altor defecte de solidificare.
- Verificați și curățați frecvent suprafețele matrițelor pentru a reduce șansele de porozitate din cauza contaminanților.
2. Închidere la rece
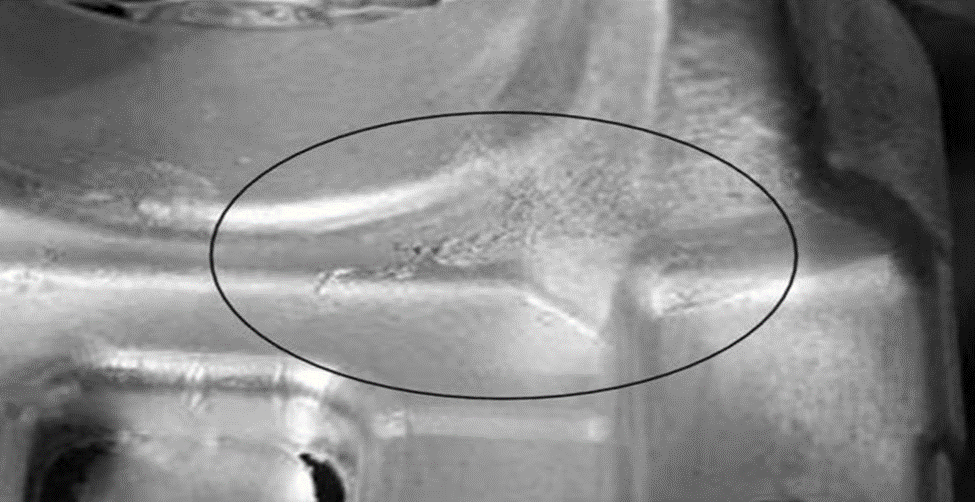
O închidere la rece este creată atunci când două fluxuri de metal topit nu fuzionează corespunzător și formează zone de lipire slabă sau cusături vizibile în piesă. Acest defect nu numai că scade rezistența mecanică, dar crește și riscul de fractură, precum și afectează negativ durabilitatea și aspectul componentei.
Cauze:
- Temperatură scăzută a metalului topit.
- Acesta este marcat pentru viteza redusă de injectare, care duce în general la solidificarea prematură.
- Design necorespunzător al matriței, cu canale de curgere insuficiente.
- Aceasta poate provoca oxidarea excesivă care formează pelicule de suprafață care împiedică fuziunea corespunzătoare.
- Flux de metal inconsistent din cauza proiectării necorespunzătoare a sistemului de gating.
Prevenire și soluții:
- De asemenea, trebuie menținută cea mai optimă temperatură de turnare a metalului pentru a asigura fluiditatea corespunzătoare.
- Creșteți viteza de injectare pentru a finaliza umplerea și pentru a obține o singură piesă.
- Eliminați barierele de curgere inutile în proiectarea matriței, astfel încât metalul să se poată mișca fără dificultate.
- Detectarea și rezolvarea problemelor de flux înainte de producție prin utilizarea instrumentelor de analiză termică.
- Trebuie aplicate tehnici adecvate de aerisire pentru a evita blocarea aerului, care adesea agravează defectele de închidere la rece.
3. Defecte de contracție
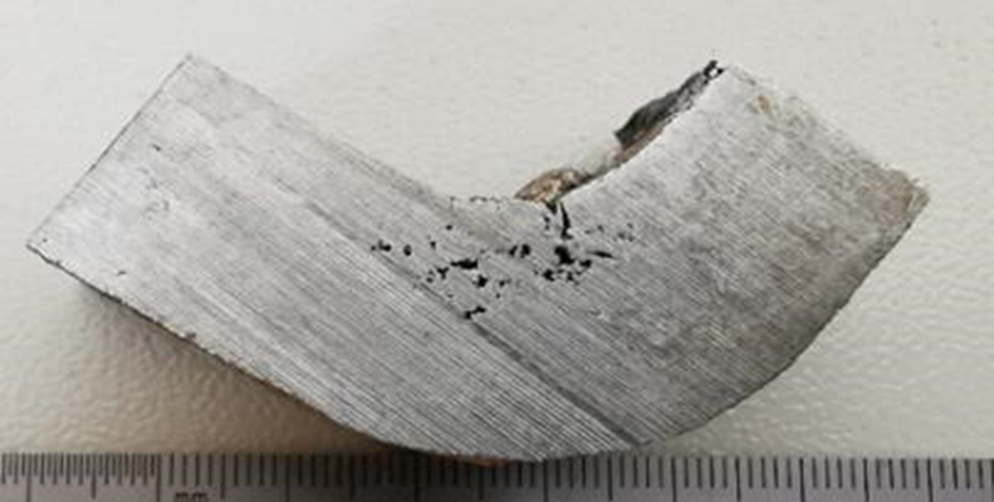
Defectele de contracție apar din cauza contracției metalului în timpul răcirii, care duce la apariția unor goluri sau cavități interne, care deteriorează integritatea structurală a piesei turnate. Ca urmare, aceste defecte reduc rezistența mecanică a produsului final, cauzează posibile defecțiuni sub presiune și determină o calitate slabă a suprafeței, afectând astfel atât funcționalitatea, cât și estetica produselor finale.
Cauze:
- Alimentarea necorespunzătoare a metalului în timpul solidificării
- Ratele de răcire sunt inegale din cauza proiectării necorespunzătoare a matriței
- Retracție ridicată a metalului datorită compoziției aliajului
- Răcirea rapidă care provoacă contracții localizate
- Presiune insuficientă în timpul fazei de solidificare
Prevenire și soluții:
- Modificați matrița pentru a asigura răcirea uniformă și alimentarea corespunzătoare a metalului topit.
- Utilizați aliaje cu tendință de contracție mai redusă și cu proprietăți de solidificare mai bune.
- Acesta este utilizat pentru a optimiza setările de presiune în timpul solidificării pentru a umple și a minimiza golurile de contracție.
- Utilizați metode de răcire controlată pentru a obține un echilibru între ratele de solidificare și pentru a reduce stresul termic.
- Implementarea instrumentelor de monitorizare și simulare în timp real pentru previzionarea și prevenirea defectelor de contracție.
4. Formarea blițului

Excesul de straturi subțiri de metal formate la linia de separare sau la golul matriței din cauza scăpării metalului la presiune ridicată este denumit "flash". Deși flash-ul poate fi eliminat după turnare, excesul de flash duce la creșterea risipei de material, a uzurii sculelor și a costurilor de producție asociate și reduce astfel eficiența generală a procesului de turnare sub presiune.
Cauze:
- Presiunea de injecție excesivă face ca metalul topit să fie forțat să intre în golurile matriței.
- Matriță uzată sau din cauza blocării necorespunzătoare a matriței pentru a permite scurgeri.
- Atunci când forța de strângere este insuficientă, provocând separarea matriței în timpul injecției.
- Acestea vor fi așezate prost, cu goluri prin care metalul să se scurgă.
- Controlul neclar al debitului de metal prin lubrifierea matriței
Prevenire și soluții:
- Forța de strângere corespunzătoare trebuie menținută pentru a evita separarea matriței și formarea de scântei.
- Inspectați și înlocuiți periodic matrițele uzate pentru a obține o etanșare corespunzătoare.
- Asigurați setările optime pentru presiune, astfel încât umplutura să fie umplută și umplută cu un flash minim.
- Pentru a preveni golurile neintenționate și scurgerile de metal, realinierea matriței ar trebui îmbunătățită.
- Utilizați tehnici precise de lubrifiere a matriței pentru a controla fluxul de metal și pentru a reduce scurgerea excesivă de metal.
5. Inspecția defectelor de suprafață (bășici, fisuri și riduri)

O varietate de defecte de suprafață, bășici, fisuri și riduri, degradează aspectul vizual și rezistența mecanică a piesei turnate și trebuie prevenite și eliminate. Acestea cauzează defecte de sudură care reduc durabilitatea produsului, cresc rata de respingere și fac ca produsul să nu reziste bine după tratamentele ulterioare turnării, cum ar fi vopsirea sau acoperirea.
Cauze:
- Aerul prins în plasticul lichid în timpul turnării.
- De asemenea, există tensiuni termice și neregularități ale suprafeței din cauza ratelor neuniforme de răcire.
- Supraîncălzire sau temperatură prost controlată în timpul solidificării.
- Sau impuritățile sau incluziunile metalice care pot afecta suprafața de turnare
- Lubrifierea slabă a matriței a cauzat o curgere neuniformă a metalului și imperfecțiuni ale suprafeței.
Prevenire și soluții:
- Degazarea corespunzătoare a metalului topit pentru a evita blocarea gazelor înainte de turnare.
- Controlul solidificării și evitarea stresului termic prin utilizarea tehnicilor de răcire uniformă.
- Controlul temperaturii matriței trebuie optimizat pentru a preveni supraîncălzirea și răcirea neuniformă.
- Crearea unui control strict al calității sale care îi va permite să detecteze toate impuritățile înainte de turnare.
- Aplicați acoperiri și lubrifianți pentru matrițe în funcție de calitatea suprafeței și reducerea defectelor.
6. Incluziuni și contaminare
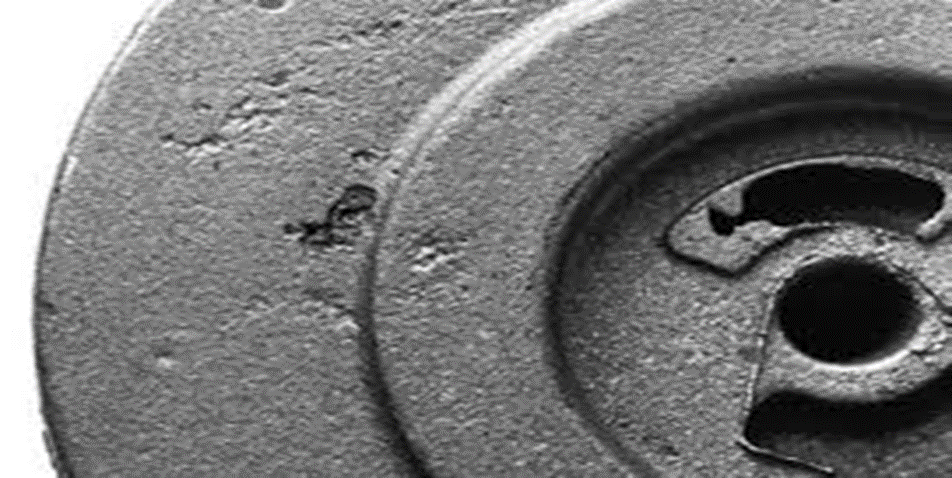
Particulele străine nedorite, cum ar fi zgura, peliculele de oxid, murdăria sau alte impurități, care sunt prinse într-o piesă turnată finală, creează proprietăți mecanice slabe, integritate structurală slabă și defecte de suprafață și sunt numite incluziuni. Prezența acestor contaminanți poate reduce performanța și durabilitatea componentelor turnate sub presiune, astfel încât acestea nu sunt adecvate pentru aplicații de înaltă precizie.
Cauze:
- De exemplu, materiile prime contaminate sunt alcătuite din impurități nedorite.
- Particulele străine dintr-un metal topit nu pot fi filtrate bine ca urmare a
- Datorită expunerii prelungite la aer în timpul topirii sau turnării metalului
- Include practici ineficiente de manipulare a metalelor care, la rândul lor, duc la o formare mai mare de zgură
- Lubrifierea insuficientă a matriței include introducerea unei materii străine în metalul topit.
Prevenire și soluții:
- Materiile prime de înaltă calitate trebuie rafinate corespunzător și fără contaminanți.
- Configurați sisteme de filtrare eficiente pentru a elimina zgura, oxizii și alte impurități din metalul topit înainte de injectare.
- Mențineți controlul manipulării metalului topit și, dacă este cazul, utilizați ecranarea cu gaz inert pentru a limita oxidarea.
- Curățați și întrețineți periodic echipamentele de turnare pentru a preveni contaminarea cu materiale reziduale.
- Utilizați lubrifierea adecvată a matriței pentru a vă asigura că nu se acumulează materiale străine în cavitatea matriței.
7. Derapaje și umplere incompletă
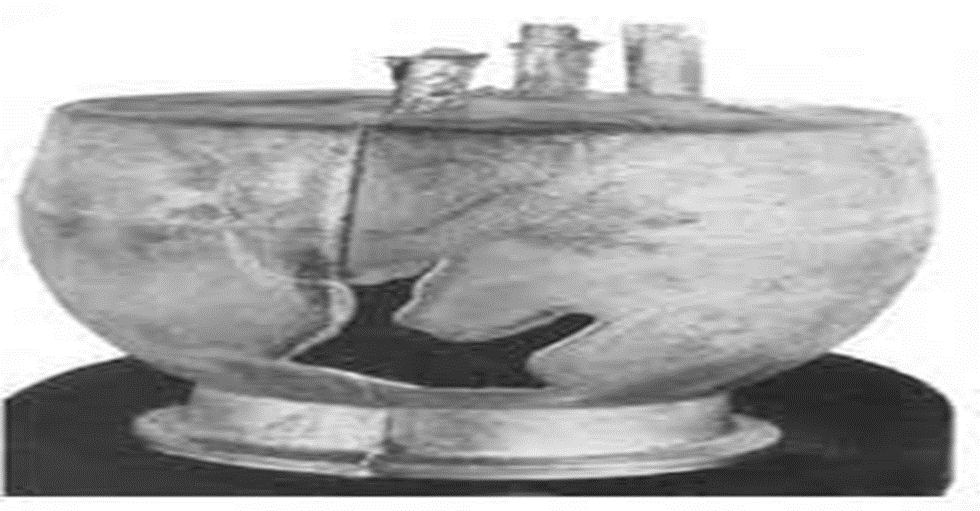
O eroare de execuție apare atunci când există o umplere scurtă a cavității matriței, ceea ce determină secțiuni lipsă, pereți subțiri și puncte slabe în componenta finală. Efecte negative asupra integrității structurale și funcționalității piesei și, în acest fel, nepotrivite pentru aplicații performante.
Cauze:
- La viteze sau presiuni de injecție scăzute, nu acoperă complet matrița
- Suprafețe reci ale matriței care previn curgerea metalului și solidificarea prematură
- Cauzează un volum inadecvat de metal topit, ceea ce duce la umplerea insuficientă a cavității
- De la proiectarea necorespunzătoare a gurilor și a canalelor, care determină distribuirea inegală a metalului topit
- Turbulența excesivă produce buzunare de aer care blochează fluxul de metal
Prevenire și soluții:
- Creșteți temperatura metalului pentru a-l face să curgă și pentru a evita solidificarea prematură.
- În plus, umplerea cavității trebuie să fie optimizată prin setarea corectă a presiunii și vitezei de injecție.
- Mențineți temperaturile de lucru adecvate ale matrițelor și împiedicați răcirea lor prematură.
- Îmbunătățirea designului canalelor și al canalelor de rulare pentru a promova distribuția lină și uniformă a metalului.
- Simulați fluxul de metal și potențialul de eroare cu ajutorul unui software de simulare înainte de producție.
8. Eroziunea și uzura matrițelor
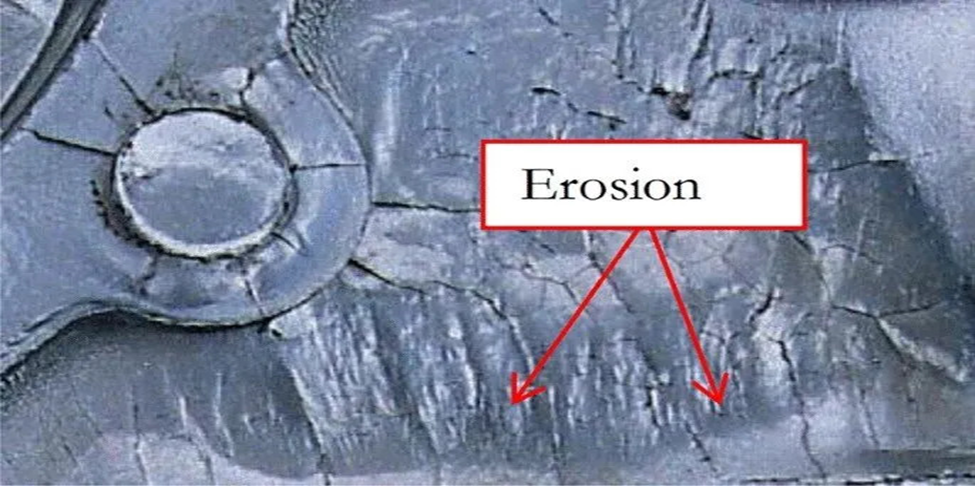
Uzura matrițelor de eroziune topită este pierderea suprafețelor matriței din cauza metalului de mare viteză care uzează continuu suprafețele pieselor matriței până când sunt atinse dimensiunile necesare, ceea ce duce la un finisaj superficial slab și la o durată scurtă de viață a sculei matriței. Dacă apare acest defect, înlocuirea matriței este frecventă și, în consecință, costurile de producție cresc în timp ce calitatea turnării variază.
Cauze:
- De asemenea, este expus în mod repetat la metal topit la temperaturi înalte, ceea ce provoacă uzură treptată.
- Materiale pentru matrițe de calitate relativ slabă, cu rezistență scăzută la stres termic și mecanic
- Ciclurile termice excesive pot provoca fisurarea materialului din cauza oboselii.
- Aceasta duce la degradarea materialului matriței în condiții de injecție ridicată.
- Puțină lubrifiere? Rezultă mai multă frecare și mai multă uzură.
Prevenire și soluții:
- Una dintre acestea este utilizarea de materiale de înaltă calitate, rezistente la căldură, care sunt mai durabile.
- Pentru a prelungi durata de viață a matriței, se pot aplica acoperiri de protecție, cum ar fi nitrurarea sau acoperiri ceramice.
- Trebuie puse în aplicare metode de răcire controlată pentru a reduce stresul termic și a induce uzura prematură.
- Pentru a găsi un echilibru între viteză și presiune cu o presiune minimă asupra matriței.
- Inspectați matricele în mod regulat și întrețineți-le pentru a descoperi și aborda eroziunea cât mai curând posibil.
9. Cracare la cald
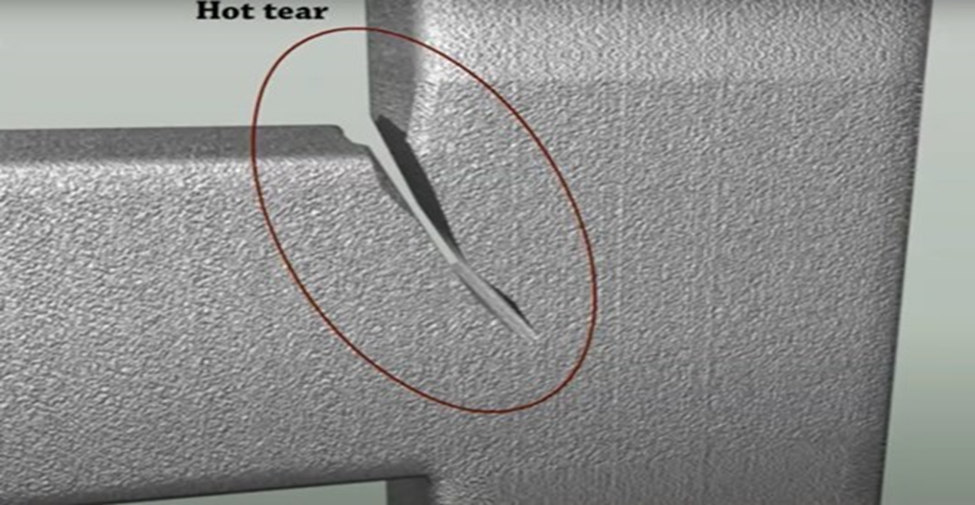
Fisurile care apar în timpul stării semisolide a metalului, din cauza stresului termic ridicat și a contracției excesive, sunt cunoscute ca fisuri la cald. Aceste fisuri degradează integritatea mecanică a piesei turnate, adică cresc șansele de defectare a piesei turnate în locul în care sunt prezente fisurile sub stres sau sarcină.
Cauze:
- Ratele de răcire nesigure în matriță, rezultând puncte de tensiune în anumite zone
- Are o susceptibilitate ridicată la stres termic și fisurare în compoziția aliajului.
- De asemenea, provoacă tensiuni reziduale excesive formate în timpul solidificării rapide o restricție privind contracția metalului
- Dacă designul matriței este slab, atunci vor exista variații de temperatură de-a lungul turnării.
- Presiunea din timpul solidificării a fost prea mică pentru a preveni propagarea fisurilor.
Prevenire și soluții:
- Aceasta va implica, de asemenea, optimizarea ratelor de răcire pentru solidificare uniformă și minimizarea stresului termic.
- Creșterea rezistenței la fisurare a aliajelor prin utilizarea adecvată a aliajelor cu o structură de granulație mai bună.
- Utilizarea tehnicilor de reducere a tensiunilor după turnare, adică tratamentul termic controlat.
- Proiectarea matrițelor cu o diferență de temperatură mai mică.
- Asigurați o presiune adecvată în timpul solidificării metalului, astfel încât acesta să curgă și să nu apară fisuri.
10. Lipire
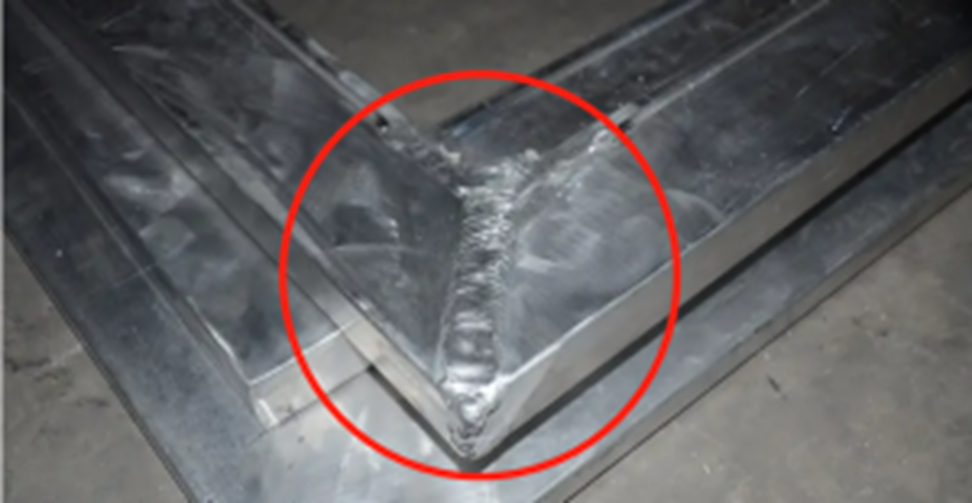
Metalul topit aderă la suprafața matriței, ceea ce este dificil de îndepărtat prin turnare, cauzând defecte de suprafață, uzura matriței, precum și opriri prelungite ale producției. Inexactitățile dimensionale și finisarea slabă a suprafeței sunt, de asemenea, cauzate de acest defect, deoarece duce la compromiterea calității generale a produsului final.
Cauze:
- Creșterea aderenței metalelor în aliaj datorită conținutului ridicat de aluminiu din acesta
- Temperaturi de matrițare excesiv de ridicate, astfel încât metalul să se lipească de suprafața matriței
- Protecție insuficientă împotriva lipirii din cauza lubrifierii slabe a matriței
- Răcirea insuficientă face ca metalul topit să fie lăsat prea mult timp în contact cu matrița - Suprafețe superioare ale matriței calcinate sau deteriorate care favorizează aderența metalului.
Prevenire și soluții:
- Se aplică întotdeauna lubrifianți de înaltă calitate pentru matrițe pentru a preveni lipirea metalului.
- Aceasta permite controlul temperaturii matriței în intervalul optim dacă aderența la cald este prea puternică.
- Reducerea aderenței la metal prin utilizarea unor acoperiri adecvate ale matriței, de exemplu straturi ceramice sau de nitrură.
- Pentru a reduce timpul de contact dintre metal și matriță și pentru a îmbunătăți eficiența sistemului de răcire.
- Inspectați și lustruiți periodic suprafețele matrițelor pentru a obține o suprafață netedă neadezivă.
Concluzie
Presiunea înaltă turnare sub presiune este un proces de fabricație puternic care creează piese metalice complexe cu o precizie ridicată și o eficiență maximă. Cu toate acestea, apar diferite tipuri de defecte folosind parametri de proces necorespunzători, probleme legate de materiale și/sau defecte de proiectare a matriței. Producătorii pot lua măsuri preventive, de exemplu, controlul optim al procesului de matriță, materialul selectat corespunzător etc., după înțelegerea acestor defecte de fabricație obișnuite.
O întreprindere poate îmbunătăți calitatea produselor, reduce costurile de producție și atinge o eficiență mai mare a producției în operațiunile de turnare sub presiune, punând accentul pe îmbunătățirea continuă a proceselor, precum și pe strategiile de prevenire a defectelor.
Întrebări frecvente (FAQ)
1. Care sunt principalele cauze ale defectelor în turnarea sub presiune de înaltă presiune?
Principalele cauze ale defectelor în turnarea sub presiune înaltă includ proiectarea necorespunzătoare a matriței, curgerea slabă a metalului, gazul blocat, stresul termic ridicat, răcirea inegală și materiile prime contaminate. Aceste defecte pot fi reduse prin optimizarea parametrilor procesului și prin utilizarea măsurilor de control al calității.
2. Ce rol joacă porozitatea în ceea ce privește performanța componentelor turnate sub presiune?
Prezența porozității slăbește integritatea structurală a componentelor turnate sub presiune, reducând rezistența și cauzând scurgeri de aer în componentele etanșe la presiune, precum și imperfecțiuni anestezice. Porozitatea poate fi redusă la minimum prin utilizarea unei degazări corespunzătoare, a unor sisteme optimizate de grilaj și a turnării asistate de vid.
3. Cum pot fi evitate închiderile la rece în turnarea sub presiune?
Temperatura corectă de turnare a metalului, vitezele de injecție mai mari, proiectarea optimizată a matriței pentru a fluidiza curgerea metalului și aplicarea instrumentelor de analiză termică pentru a identifica eventualele probleme de curgere pot contribui la prevenirea închiderilor la rece.
4. Eroziunea matriței este o preocupare importantă în turnarea sub presiune de înaltă presiune deoarece?
Expunerea repetată a metalului topit la temperaturi ridicate la matrițe cauzează eroziunea matriței care scurtează durata de viață a matrițelor și scade precizia pieselor turnate. Durata de viață a matrițelor poate fi prelungită prin utilizarea unor materiale de înaltă calitate, a unor acoperiri de protecție și prin răcirea controlată a matrițelor.
5. Ce îmbunătățește calitatea și consecvența produselor turnate sub presiune?
Controlul strict al calității, optimizarea parametrilor de proces, controlul temperaturii matriței, utilizarea de aliaje de înaltă calitate și inspecția matriței și a utilajelor sunt efectuate periodic pentru îmbunătățirea obișnuită a calității produselor turnate sub presiune.