
In the fast pace of manufacturing, CNC machine shops are the backbone of precision engineering, efficient machine shops, and technological advancement. The advanced facilities use Computer Numerical Control (CNC) technology to produce highly precise components for aerospace, automotive medical, and other industries. Traditional machining using manual labor and operator knowledge requires constant quality, slower production, less cost-effective. In contrast, CNC machining automates the whole process and has reliable consistency, fast production, and cost efficiency. A CNC machine shop is powered by a variety of super cool high-tech machines including CNC mills, lathes, routers, plasma cutters, and EDM machines that run on a computer with precise, auto-guided functions. The process starts by using computer-aided design (CAD) software and engineers making detailed 3D models of the particular component required in the system.
Using these designs, they are then converted into machine-readable G code that specifies the exact movements of cutting tools to create and shape raw materials products. Each material possessed specific mechanical and physical properties which made them suitable for a particular CNC machine shop. Without CNC machining, it would be difficult to work with such diverse materials and people would require durable, lightweight, heat-resistant, and even corrosion-proof parts when they need them. CNC machine shops have high precision and can be done with high efficiency, besides this, they provide scalability, repeatability and flexibility, enabling businesses to create from prototypes to mass production runs with little human involvement. CNC machining is at the forefront for industries that are actively trying to build more advanced and more complicated designs.
This article details the how CNC machine shops operate, what type of machines they use, what materials they work with, and the industries they service. Knowing their role, capabilities, and the advantages the businesses can see who CNC machining service is best for.
What is a CNC Machine Shop?

A CNC (Computer Numerical Control) machine shop is a place equipped with modern machine tools controlled by computer programs. They make shop with the sole purpose of producing high precision, complex parts for aerospace, automotive, medical, electronics and industrial manufacturing industries. Unlike traditional machining, which is done with the aid of hands-on operation, CNC machining makes the process automatic and facilitates higher accuracy, efficiency and consistency in production.
How CNC Machine Shops Work
In CNC machine shops, a computer aided design (CAD) software creates the digital model of the part. The G-code is then generated of this design which the CNC machine reads and uses to make the operations and movements. It precisely cuts, drills, shapes, or mills the material according to programmed instructions thus making the automation repeatable and free of errors.
Types of CNC Machines in a CNC Shop
There is usually a wide variety of CNC automated machining tools housed in CNC machine shops such as:
CNC Milling Machines: are rotary-type cutting tool machines that use them to remove material from the workpiece and create shapes, holes and surface finishes.

CNC Lathes: these machines are meant to make cylindrical parts, by turning the workpiece while cutting tools perform its predefine shaping with high accuracy.

CNC Routers: The CNC router has long been in use for cutting wood, plastic and composites by carving intricate designs and patterns.

CNC Plasma Cutters: They use a high-temperature plasma torch to cut through metal sheets and the most readily useable metal in bulk quantities, depending on their size, is perfect for things like sheet metal fabrication.

Electrical Discharge Machines (EDM): EDM uses electric discharges (sparks) to cut away material; thus without using cutting tools, it is ideal for detailing or fine cuts in hardened metals.
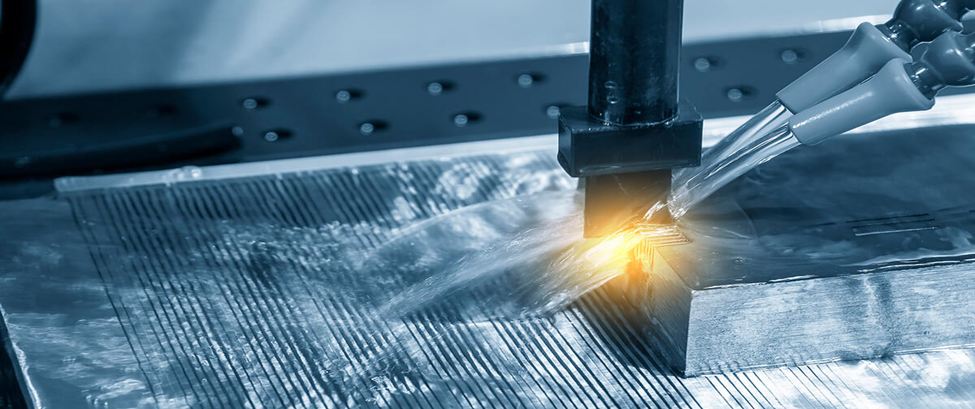
Materials Used in CNC Machine Shops
A huge variety of materials are used in CNC machine shops to produce high precision components for the aerospace, automotive, medical or manufacturing industries. But it is important to select the right material since it determines the durability, functionality and in general, the extent of the performance of the final product. Some of the most commonly used CNC machining materials are mentioned below.
Metals

Aluminum: 알루미늄 is famous for its lightweight properties, and corrosion resistance features which make the way to aerospace, automotive and consumer electronics. It also has good thermal and electrical conductivity and is therefore useful in heat exchangers and electronic components.
Steel & Stainless Steel: It is a very durable metal that does not rust, does not wear out and does not get damaged in heat; hence used for medical tools, food processing machines, structural parts. It is very strong as well as durable.
Titanium: is a strong material with high strength and excellent corrosion resistance, which makes it a top choice for aerospace, medical implant, automotive etc. Extremely high temperature and extremely harsh conditions cause no problem to it.
Brass & Copper: A metal commodity that is prized for its outstanding machinability, anti-corrosion and electric conductivity. Electrical fittings, plumbing fixtures and decorative hardware commonly use it.
Plastics

Acetal (Branded Delrin): Strong and rigid, with good moisture resistance, acetal is a used in gears, bushings, and similar mechanical components that require low friction and high wear resistance.
Polyethylene: is a lightweight, chemically resistant material that is well suited for piping, containers and insulating parts. Food processing additionally makes use of it and so does medical application.
Nylon: It is known for its toughness and wear resistance and is often used in gears, bearings and automotive parts. It is also used for more industrial machinery components.
Acrylic: This has very good optical properties along with weather resistance. You will commonly find it used in signage, display cases and optical lenses.
Composites

Carbon fibre reinforced plastic (CFRP): material with a very strong and lightweight material, and it is widely used in the aerospace industry, sports equipment, automotive industries, etc. High rigidity and durability are provided.
Fiberglass: One of the popular composite materials that’s well known for its strength, low weight and corrosion resistance. It is widely employed in automotive bodies, boat hulls and in industrial applications.
Ceramics

Zirconia: the excellent hardness, and wear-resistance make it used in cutting tools, bearings and dental implants. It also has a high-temperature resistance.
Ceramic material called alumina: can be used, since it is known for its excellent electrical insulation as well as durability. It is extensively used in electrical parts, wear-resistant parts and the machinery industries.
In fact, CNC machine shops pick materials very thoughtfully with reference to the project requirements. Strength, weight, corrosion resistance, and thermal properties are all factors that have to be taken into account in order to ensure that machined parts are strong enough and suitable for use in their applications.
How a CNC Machine Shop Works: A Step-by-Step Guide
A CNC shop can be described as a facility where high precision parts are manufactured using automated machinery which are controlled by computer program. The shops are necessary for industries ranging from metal, plastic, and composite component production with regard to tight tolerances, consistency and efficiency.
The purpose of this article is to explain how a CNC machine shop works, maintaining each stage right from the initial design, developing CNC programs, performing the final quality check, and its delivery.
Step 1: Design & Programming
The first stage of the process is the design and programming phase where machining does not yet occur.
1. CAD (Computer-Aided Design) Modeling
CAD software such as SolidWorks, AutoCAD or Fusion 360 are used by engineers and designers to create a 3D model of the part.
The model contains detailed dimensions, features and specification requirements for manufacturing.
2. CAM (Computer-Aided Manufacturing) Programming
Using CAM software such as Mastercam or Fusion 360, CAD design will be converted into a CNC compatible program.
It also shows the toolpaths that the CNC machine would use for a specific part, cutting speed, and movement instructions.
The program is loaded into the CNC machine’s computer, once completed.
Step 2: Material Selection & Preparation
1. Choosing the Right Material
Different kinds of materials are worked with in the CNC machine shops.
- Metals (Aluminum, Steel, Titanium, Brass)
- Plastics (ABS, Nylon, Polycarbonate)
- Composites (Carbon Fiber, Fiberglass)
2. Material Setup
- The raw material is cut to the size necessary for the part.
- After that, it is put into a CNC machine using clamps, vices, or fixtures which are designed to have clamps, vices, or fixtures to prevent movement during machining.
Step 3: CNC Machining Process
1. Machine Calibration & Setup
It is equipped with CNC machine calibration to ensure tools and workpieces are perfectly aligned.
Operators check the tool offsets, machine zero points and the spindle speeds to a specification that match the project.
2. Execution of CNC Program
The next step after the setup is complete, the CNC machine goes on a path, which has been programmed in the G code, a machine language that directs movements.
Automatic cutting, drilling, milling, turning, or shaping operations are performed by the machine.
3. In this regard, machining processes used in CNC shops are discussed in this thesis.
- We will rotate a tool to cut away the material that is used to shape the workpiece.
- Lathe – The material is rotated while turning it and cutting tools from it.
- Drills – Some drills are quite high speed to create accurate holes.
- Grinding & Polishing – Used to increase surface finish for use.
Step 4: Quality Control & Inspection
After being machined the part is put through stringent quality control to guarantee the level of accuracy and consistency with the design specifications.
1. Dimensional Inspection
Among the things that check dimensions are precision measuring tools such as micrometres, callipers, and height gauges.
2. CMM (Coordinate Measuring Machine) Inspection
Laser or probe technology is used by a CMM machine to inspect complex parts with extreme accuracy.
3. Visual & Surface Finish Inspection
It is approved once it has been examined for no scratches rough edges or surface imperfections.
Step 5: Assembly & Delivery
1. Finishing Processes
Some parts need more processing including:
- Or anodize or plate for corrosion resistance.
- Heat Treatment (for strength enhancement)
- It is foreseen to coat the conductors with either a paint or powder coat (for looks and protection).
2. Assembly & Packaging
- In case there are more parts, then they are assembled as a final product.
- The assembled parts are carefully packed for release when they reach their destination.
3. Delivery to Clients
The product is then shipped to the client and s/he returns the product now in manufacturing, aerospace and automotive or medical applications.
The Differences between CNC Machine shop and traditional Machine Shop

Both a CNC (Computer Numerical Control) machine shop and a traditional machine shop do the role of manufacturing parts with precision but the technology, efficiency and accuracy are quite different.
1. Automation & Control
CNC Machine Shop: This is the type of machine shop that operates on computer-controlled machines which are highly precise and repeatable with minimum operator intervention.
Traditional Machine Shop: The operator controls the tools through manual machining and is a slower and more labor intensive methods.
2. Precision & Consistency
CNC Machine Shop: Parts that are created using this machine are accurate within microns and consistent throughout big batches.
Traditional Machine Shop: Predisposed to error introduced by humans, thereby causing its end products to vary slightly.
3. Efficiency & Speed
CNC: Faster production with continuous 24/7 operation and reduced downtime.
Traditional: It is slow, and needs to be operated by skilled machinists in machine by machine basis.
4. Cost & Labor
CNC: Initial investment is higher, but labour costs are cheaper in the future.
Traditional: Skilled labor is still required, and lower machine costs but it increases the cost of production as it goes.
Traditional machine shops still have their uses for custom, small scale jobs however, the cases where CNC machine shops are the logical choice are in the production of high precision, mass production and efficiency of industry.
Industries That Rely on CNC Machine Shops
CNC machine shops are essential to a broad assortment of businesses, each fed up with the most extreme precision and productivity in the assembling procedure. There are some of the top industries that use CNC machining as follows:
1. Aerospace Industry

Due to the tight tolerances and requirement of high durability on aircraft and spacecraft components, these play a very important role in improving the product’s solidity. Turbine blades, engine parts and structural parts that meet the stringent requirements for aerospace are made with the CNC machining processes.
2. Automotive Industry

In automotive parts, CNC machining provides everything from engine parts to suspension components so that these parts are made with high precision and to be lightweight and of high performance.
3. Medical & Healthcare

CNC machining is widely used in the medical field where it is used to make surgical tools, orthopaedic implants, and prosthetics. For these parts, you need high precision and also those duties have to be strictly adhered to the FDA regulations.
4. Electronics & Technology

CNC machining is used in the electronics manufacturing to make components such as heat sinks, connectors and enclosures of computers, smartphones and other electronic devices.
5. Defense & Military

Gun manufacturing, military vehicles, and defence equipment are brought to us due to CNC machining that guarantees reliability and durability under extreme operating conditions.
Advantages of CNC Machine Shops
Many advantages are contained in CNC machining over other traditional manufacturing methods. There are some of the major benefits here:
1. High Precision & Accuracy
CNC machines operate with micron level precision, each time parts are produced they will meet precise specification. This is very important in fields such as aerospace or medicine where a slight mistake could cause failure.
2. Efficiency & Speed
CNC machines are automated and, therefore work 24/7 with no fatigue and the production is quicker and more efficient.
3. Consistency & Repeatability
Unlike manual machining, CNCs guarantee that any part that is produced is identical so it is ideal for mass production and quality assurance.
4. Cost-Effectiveness
CNC machining may be more expensive initially, but long term it is one of the ways that cuts down on labor costs, wasted material, and mistakes in the final product.
5. Versatility in Material & Design
CNC machines are able to manufacture with a lot of different materials and create geometries that are just too complex or difficult with conventional methods.
Tips to Select the Best CNC Machine Shop
The following factors are to be taken into consideration when selecting a CNC machine shop for your manufacturing needs:
1. Experience & Expertise
Check for your nearest shop which is well known with years of experience in precision machining industry. Skilled team guarantees the quality of production.
2. Advanced Equipment & Technology
With complex projects, top-tier CNC shops should have state-of-the-art machinery and software to take them on.
3. Quality Assurance & Certifications
Make sure the facility has industry certifications such as ISO 9001, AS9100 (Aerospace) and ITAR compliance (Defense) for high production standards.
4. Customization & Flexibility
Every project has unique requirements. Select a shop that provides custom machining as these shops can adapt to your special needs.
5. Competitive Pricing & Lead Times
Although cost must be considered, the shop must offer competitive costs, without any sacrifices for quality and delivery times.
결론
Today CNC machine shops have completely revolutionised manufacturing through precision, efficiency and automation that could not have been equalled with old-school production methods. Cutting-edge technology is used at these facilities to make complex parts with a high level of accuracy and repeatability giving all production runs the same high accuracy. CNC machine shops perform well in providing services to several industries including aerospace and medical, automotive and electronics because they can handle different materials and intricate designs. The transition from traditional machining to CNC-controlled has not only increased production time and reduced costs but also decreased the amount of human error and eased the amount of quality of the components. Further adv, ance multi-axis CNC machines help carry capabilities to create exceedingly precise and complex geometries as well as high-fidelity portions that can not be accomplished until you do it manually. CNC machine shops will have an even greater impact on the manufacturing industry as technology continues to develop. In an ever-competitive, demanding market, companies that are looking for precision-engineered parts, as well as reduced production times and scalable solutions should consider investing in CNC machining services. Businesses can confidently make superior manufacturing outcomes by selecting the right CNC machine shop, one in which the shop has experience, advanced equipment, and commitment to quality, so they can satisfy industry standards and project requirements. CNC machining is the cornerstone of modern industry, no matter whether it is used for prototyping, small batch production, or mass manufacturing of components — since it enables innovation, efficiency and excellence, in everything produced.
FAQs About CNC Machine Shops
1. What is more critical, the traditional machining or CNC machine shop?
The precision, automation, as well as the efficiency of these CNC machine shops are higher than manual machining. It reduces human error and is able to produce complex designs and mass produce with quality.
2. What industries use CNC machining?
However, CNC machining is important in the aerospace, automotive, medical, electronics, and defence industries. It is also used in robotics, manufacturing and consumer products.
3. According to me, CNC machine uses what materials are available to them?
Depending on project needs, they work with metals (aluminium, steel, titanium, etc.), plastics (acetal, nylon, etc.), composites (carbon fibre, fibreglass, etc.) and ceramics (zirconia, alumina, etc.).
4. How long does CNC machining need?
Depending on how complex the part or situation is, if the material is intricate, or the order is big or small, the time it takes to produce varies. On simple parts it may take hours, intricate designs or prototypes can take days.
5. How to select the appropriate CNC machine shop?
Find experience, certifications (ISO 9001 AS9100), advanced equipment, material expertise, quality control, fair pricing, and other similar to get high-quality results.