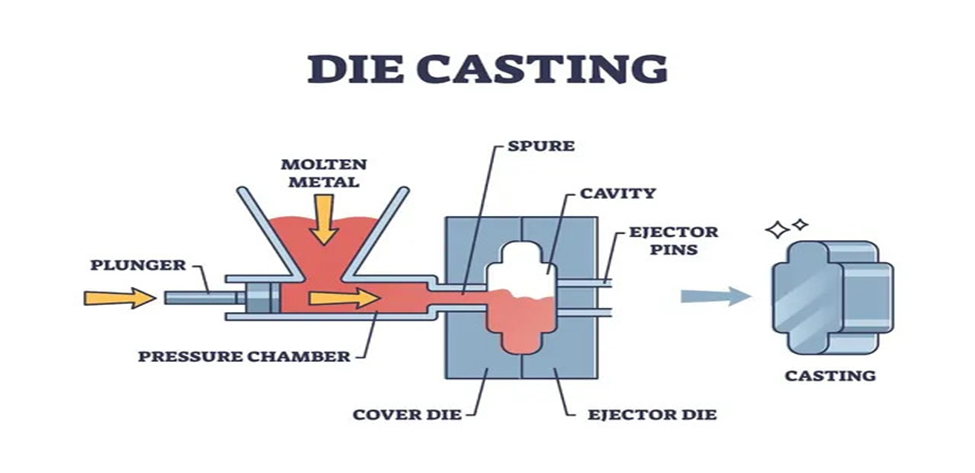
これは、ダイカストとも呼ばれる金型の空洞に溶融金属を圧力で押し込んで充填する製造工程である。金型は通常、高品質の鋼鉄製であるため、部品を大量に生産することができ、この用語は多くの部品の製造を意味するために使用されます。その後、溶融金属が冷却され、固体層が形成された後、金型を開くことによって完成部品が製造される。このような使い方は、測定精度の高さや研磨された表面を必要とするさまざまな部品の製造に使用される複雑な金属を作る際に多く適用されます。ダイカストは、アルミニウム、亜鉛、マグネシウムで行うことができますが、用途やその他の要件に応じて他の金属を使用することもできます。 ダイカスト は、金属から小・中型の部品を大量生産するという発想において、熟練した製造技術のひとつであると考えられている。この方法は、耐久性のある軽量で複雑に調整された部品を製造する能力があるため、自動車、航空宇宙、電子機器、産業機械に普及している。しかし、この製法は、従来の技術では製造が非常に困難な複雑な形状の製品を製造できることで広く認知されている。
ダイカストの仕組み

成形はダイカストの最初の工程です。金型の片側には半分があり、最終製品のような形の金型にするために特定のデザインの半分です。キャビティと中子は、部品をできるだけ忠実に再現できるように、通常は特注の金型用に設計されます。
1.溶融金属射出:
次に、溶融金属を高圧下で金型キャビティに注入し、所望の形状を形成する。金属は通常、流動性を持たせるために溶融ひずみより1度高い温度まで加熱される。ダイカストでは、溶融金属が金型の細部まで確実に入るように、溶融金属を金型に押し込む圧力は数千から数万psi(平方インチあたりポンド)になることがあります。
2.固化:
これは、金属がケーシングの空洞に注入され、冷却されて金属が硬化するときに発生する。鋳物の品質は冷却速度に左右される。この場合、さらなる破壊モード(せん断、上昇、グライド)が作用し、冷却が速いほど強度が高く表面仕上げが良くなり、冷却が遅いほど内部欠陥が多くなり機械的特性が低下する可能性があります。金型に組み込まれた水冷システムは、通常、冷却プロセスを補助するために使用されます。
3.退場:
その後、金属を冷却して凝固させ、大きな鋳物から鋳型を取り外して部品を排出するのは簡単です。その後、ほとんどの時間は、機械的なエジェクターシステムを使用して金型から部品を押し出すことに使用されます。これは、最終的な形状や寸法を実現するためのトリミングや機械加工など、他の余分な工程を必要とする部品の複雑さによって異なります。
4.品質管理:
品質検査は、射出後の部品に対して行われる。寸法確認、外観検査、機械的試験などを行い、部品が要求と同等かそれ以上であることを確認します。ダイカスト鋳造では、高い精度と再現性が理論的に達成されます。
ダイカストの種類
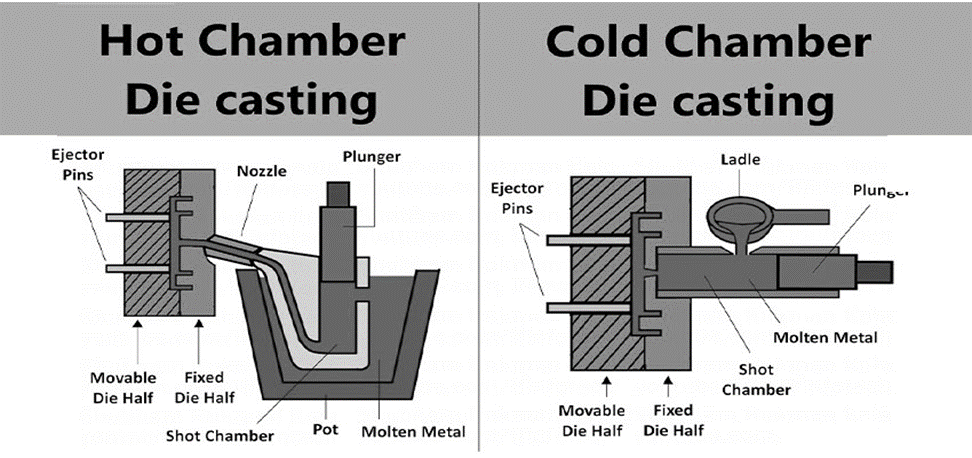
ダイカストには、ホットチャンバーダイカストとコールドチャンバーダイカストの2種類があります。これらはすべて良いものであり、それぞれの利点、限界、理想的な用途があります。
1.ホットチャンバーダイカスト
亜鉛、マグネシウム、鉛などの金属に最も適したプロセスは、高温、融点で行われるため、ホットチャンバーダイカストです。射出システムは溶解炉の中に設置され、この方法で金属は常にチャンバーと接触している。
メリット
- ホットチャンバーダイカストは、溶湯が射出チャンバー内にあるため、金型内に射出されるように配置されるため、コールドチャンバーダイカストよりも短時間で鋳造が完了する。
- シングルステージ:部品点数が少なく、セットアップに時間がかからないため、特に大量生産では経済的とされる。
- ホットチャンバー・ダイカストは、使用する金属の溶融温度が低く、金属の汚染がほとんどない場合に最適です。
デメリット
- アルミニウムや真鍮のような融点の高い金属加工には使用できない。
- すべての部品は溶けた金属にさらされているため、ある程度の時間が経つと消耗が激しくなる。
2.コールドチャンバーダイカスト
アルミニウム、真鍮、銅のような融点の高い金属は、コールドチャンバーダイカストで鋳造されます。この場合、溶融金属は第二の炉からコールドチャンバーに注入され、その後金型キャビティに注入されます。
メリット
- 材料選択の多様性という点では、コールド・チャンバー・ダイカストは、高融点材料の使用を可能にする材料使用の多様性を提供する。
- 金属の品質管理:溶融金属シリンダーは別々にチャンバーに注入されるため、汚染を防ぐために金属の品質を十分に管理することができます。
- 工具寿命の向上:射出工程で金属と接触することがなくなるため、工具寿命が延びる。
デメリット
- サイクルタイムの短縮: 手動で金属を流し込むため、サイクルが長くなる。
- より複雑な器具を使用する追加手術となるため、費用は高くなる。
ダイカスト鋳造法の比較:ホットチャンバーとコールドチャンバー
ここでは、最も一般的な2つのダイカスト法の種類を比較します、
特徴 | ホットチャンバー・ダイカスト | コールド・チャンバー・ダイカスト |
金属との互換性 | 低融点金属に最適(亜鉛、鉛など) | 高融点金属に最適(アルミニウム、真鍮など) |
サイクルタイム | サイクルタイムの短縮 | サイクルタイムの短縮 |
モールドウェア | 溶融金属との直接接触による金型摩耗の増大 | 金型摩耗の低減 |
コスト | 大量生産のための低コスト化 | 初期コストは高いが、高強度金属に適している。 |
部品の複雑さ | シンプルな部品に適している | より複雑で大きな部品に適している |
ダイカストの利点
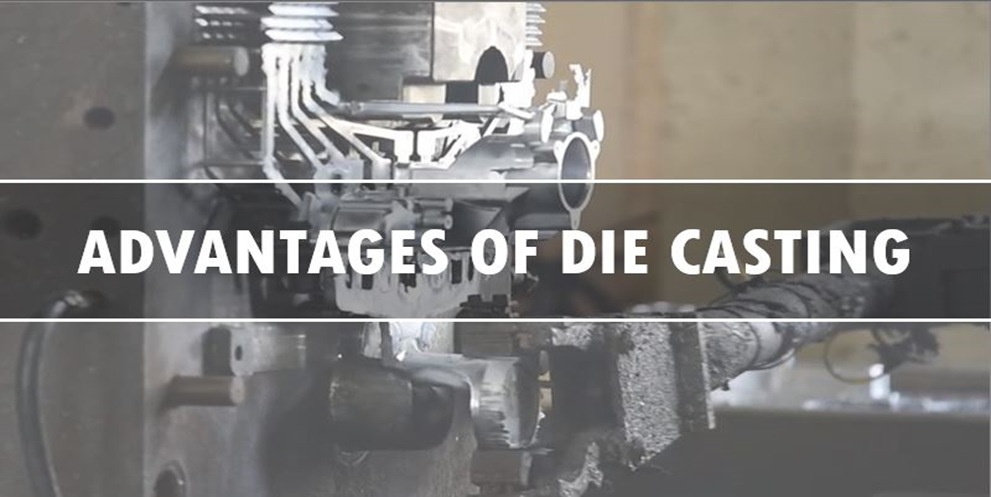
ダイカスト鋳造が、金属合金から製品を大量生産するための主要な方法のひとつであることは、最大の利点のひとつである。
1.高精度と正確さ
ダイカスト鋳造には多くの利点があり、高い金型精度を提供するのに便利です。この製造方法は、特定の作業で必要とされる公差レベルを定義するため、非常に重要な優れた寸法精度を必要とする部品の製造にも広く使用されています。ダイカストは、複雑な形状の部品を製造できる唯一の製造技術です。
2.高い生産率
大量生産という点では、ダイカストは非常に効率的だ。最初の金型さえ作れば、あとはほとんど手間をかけずに、素早く安く部品を生産できる。自動車やエレクトロニクスのように、同じ部品を大量に必要とする業界では、シミュレーテッド・パウダーの需要が特に高い。
3.複雑なデザインと薄い壁
ダイカスト鋳造では、従来の製造方法では困難または不可能な複雑なデザインを実現することができる。ダイカスト鋳造は、薄肉で複雑な内部構造を持つ部品を作ることができ、アンダーカットにも対応できるため、スペースが限られている場合に最適です。
4.材料効率
ダイカストは材料の無駄を最小限に抑えます。溶融金属を注入するために使用される圧力は、金型キャビティのすべての部分を埋めるため、スクラップの発生が少なくなります。さらに、ダイカスト部品の多くはリサイクルできるため、プロセスの持続可能性につながります。
5.優れた表面仕上げ
ダイカストで作られた部品の表面仕上げは、滑らかで美しい。そのため、研磨やコーティングなどの二次的な仕上げ工程が少なくて済み、時間とコストを節約できます。
ダイカストの工程で何が応用できるか?
非鉄金属は、優れた鋳造特性によりダイカスト鋳造で主に使用されます。アルミニウム合金は、以下の材料で示されるように、ダイカスト鋳造に使用される一般的な材料です。
1.アルミニウム合金

軽量で耐食性に優れ、熱と電気の伝導性に優れているため、アルミはダイカストで最も広く使用されている材料です。強度と重量の比が考慮される場合、特に自動車、航空宇宙、電気産業では、特殊グレードのアルミ合金が使用されます。最後に、アルミ合金は寸法的にも安定しているため、高精度部品の製造に適しています。
2.亜鉛合金
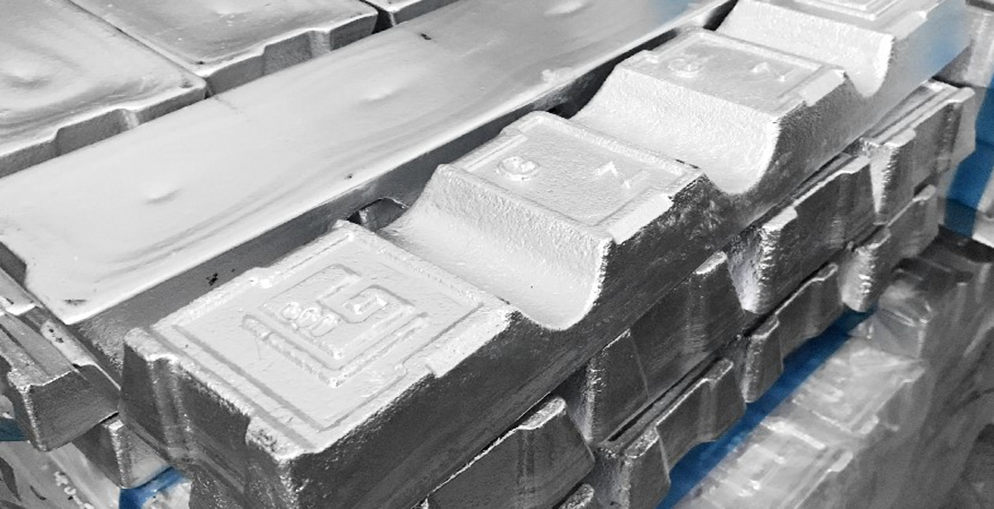
亜鉛ダイカスト合金は、低融点、高流動性などの特性により、薄い部分やシャープな細部を持つ複雑な設計を簡単かつ効率的に行うことができます。このような亜鉛部品は高い靭性を持ち、耐腐食性にも優れ、高品質な光沢があります。亜鉛合金のもう一つの応用分野は、自動車やその他の乗り物のスペアパーツ、金物、電子機器です。
3.マグネシウム合金

マグネシウムは最も軽い構造用金属であるため、自動車や航空機用の部品で大きな重量を提供できることは特筆に値する。これは、マグネシウム合金が、強靭でありながら可能な限り軽量であることが要求される部品に使用されるからである。しかし、この金属は非常に反応しやすいため、ダイカスト加工を行う際には合金の管理が必要です。
4.銅合金
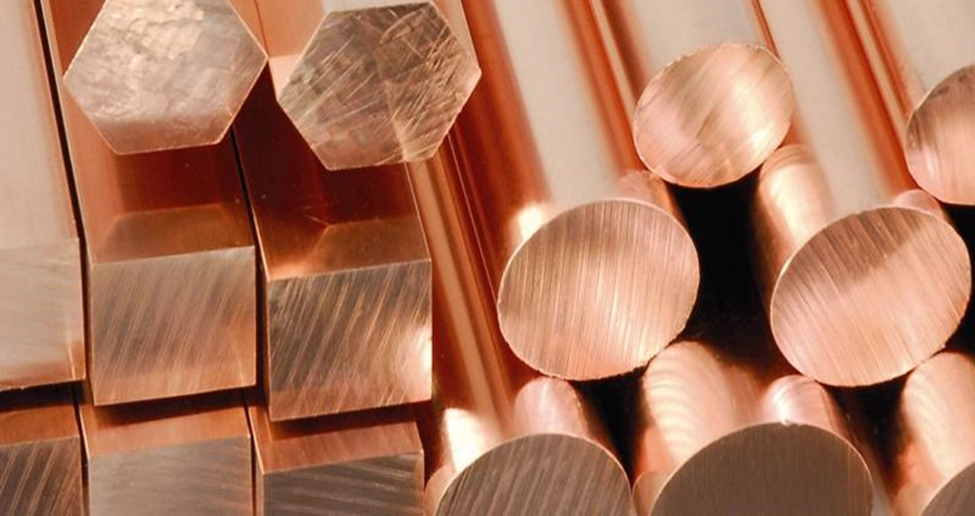
アルミや亜鉛の他に、銅をベースとした合金、真鍮や青銅もダイカストで使用されますが、アルミや亜鉛ほど頻繁ではありません。耐摩耗性に優れた強度特性を持ち、電気や配管の用途に役立つことが多い。
最も重要なことは、基材の形状が異なれば用途も異なり、コストも異なるため、最終製品の特性も異なるということである。
ダイカストと他の鋳造法との比較
砂型鋳造、インベストメント鋳造、永久鋳型鋳造のような鋳造方法と比較すると、このセクションはダイカストの比較セクションと言えるかもしれません。その際、それぞれの方法の長所と短所を強調し、他の選択肢からダイカストを選択するタイミングを読者に教えるのが賢明である。そのため、部品の材質、複雑さ、生産量によって最適な鋳造方法を決定するのに役立つ比較の概要となる可能性がある。
特徴 | ダイカスト | 砂型鋳造 | インベストメント鋳造 |
精密 | 公差の厳しい高精度 | 精度が低く、表面仕上げが粗い | 高い精度と滑らかな仕上げ |
スピード | 大量生産のための高速化 | より遅い生産サイクル | 金型の準備に時間がかかる |
廃棄物 | 最小限の廃棄物 | 仕上げが粗いため廃棄物が多い | 無駄は少ないが、より複雑な金型 |
コスト | 大量生産時の費用対効果 | 少量生産のための低コスト | 複雑さと労力によるコスト増 |
ダイカストと射出成形の製造工程を比較する。
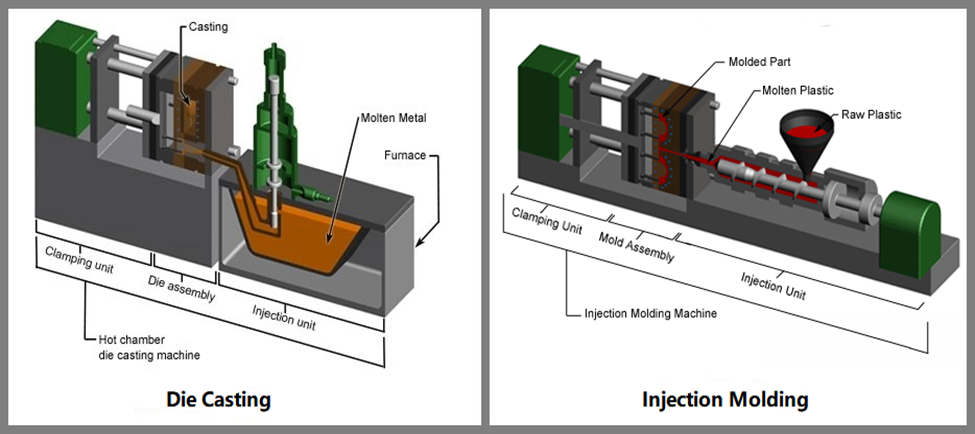
ダイカストと射出成形は、複雑な形状を持つ細部の部品を作るために使用される2つの一般的な技術です。どちらの技法も最終製品を製造するために細部を形成する材料を使用しますが、材料の種類、形成される製品、特に各プロセスの利点の点で違いがあります。
1.使用材料
ダイカスト: ダイカスト鋳造は、鉄系金属、特にアルミニウム、亜鉛、技能、銅合金以外の他の金属に好んで用いられる。金属を加熱し、油圧を利用して金型に流し込む。そのため、ダイカストは丈夫で耐久性があり、高温にも耐えられる部品を製造する最も適切な方法です。
射出成形: 射出成形は一般的にプラスチック材料間で使用され、金属やガラスではほとんど不可能である。よく使われるポリマーには、ポリエチレン、ポリプロピレン、ポリスチレンなどがある。製品の形成材料も軽量で柔軟性があり、さらに低コストで複雑な形状が可能であるため、射出成形はこの種の製品に最適であると言える。
2.プロセスの違い
ダイカスト: その名が示すように、溶融金属を高圧で金型に注入するプロセスである。金属が非常に高速で冷却・凝固した後、微細な公差と良好な表面仕上げが得られ、それ以上の操作は必要ありません。
射出成形: 射出成形は、溶融したプラスチック材料を金型のキャビティに射出し、圧力を加えて成形するものである。溶融プラスチックの温度が下がると金型が開き、プラスチックの金型ができあがります。射出成形は、ダイカストと比較すると、比較的小型で軽量な部品を製造するために一般的に使用されますが、それでも、同様に高い精度を余裕ができます。
3.アプリケーション
ダイカスト: ダイカストは、その優れた耐熱性により、自動車製造、航空機、その他の電子製品に使用される硬くて丈夫な部品を作るのに有用である。
射出成形: 柔軟性、設計のしやすさ、低コスト生産が重視される消費者製品、パッケージ、医療機器、玩具の生産に使用できる。
ダイカストの用途

ダイカストが多くの産業で人気のある製造工程となった要因のひとつは、かなり複雑な形状を持つ高品質で耐久性のある部品の製造を可能にしたことである。その用途には以下のようなものがある:
1.自動車産業
一般的に、エンジン部品、トランスミッションハウジング、その他の重要な自動車部品はダイカストで作られています。ダイカスト部品は、自動車産業の厳しい用途に取り付けられる精度と強度を備えています。
2.エレクトロニクス産業
エレクトロニクス分野におけるダイカストは、携帯電話、ノートパソコン、テレビなどの電子機器の筐体を製造するために使用される。この技術により、繊細な部品を保護する軽量かつ強靭な筐体を作り上げることができます。
3.航空宇宙産業
ダイカスト鋳造は、航空機や宇宙船に必要とされる高い強度を持つ軽量部品を製造できるため、航空宇宙製造企業に大きな利益をもたらしている。ダイカスト部品は、性能と安全性が重要な問題となる用途に使用できる精度と材料特性を持っています。
4.産業機器
機械、工具、その他の産業機器の部品もダイカストで鋳造される。ダイカスト鋳造は、複雑な細部を持つ形状の部品を製造でき、機械的特性も優れているため、これらの用途に適している。
結論
ダイカストは、汎用性が高く、費用対効果が高く、効率的な製造プロセスであり、多くの産業で使用されています。製造される品質は、部品の公差、表面仕上げ、高い生産率の点で非常に高く、今日の近代的な製造方法にとって優れた製造ツールとなっています。ダイカストは、自動車から航空宇宙、電子機器、産業機器に至るまで、部品の強度、精度、効率を必要とする多くの産業のニーズに応えています。
しかし、テクノロジーは急速に発展しており、おそらく今後も、優れた金属部品の供給源として膨大な規模で使われ続けるだろう。 ダイカスト.ダイカストの基礎知識をより深く理解することは、エンジニアリング、製造、設計の専門家が、ダイカスト・プロセスをどのように利用すれば望ましい結果が得られるかについて、十分な情報を得た上で意思決定を行う際に役立つであろう。
ダイカストに関するFAQ
1.ダイカストと射出成形のタイムサイクルは?
ある部品のサイクルタイムの範囲は、ダイカストでは15~5分、射出成形では10~60秒である。
2.プラスチック部品にダイカストは使えますか?
ダイカストは非金属には使われない。一般的には、射出成形と呼ばれる技術を使ってプラスチック部品を製造する。
3.ダイカストの製造工程に最も適した製品は?
ダイカストは、金属製の精度の高い小型・平均サイズの複雑な部品の製造に最も適しています。製造される機械製品としては、自動車や自動車の部品や付属品、電気製品のケーシングやケース、電子部品や機器のケーシングなどがあります。
4.ダイカストと砂型鋳造の違い
それでもこの2つを比較するとダイカストは砂型鋳造よりも精度が高く、時間のかからないプロセスです。砂型鋳造は大型であまり複雑でないものに適していますが、AL鋳造は小型で複雑なものに適しています。
5.ダイカストのコストを決めるものは何ですか?
ダイカスト鋳造のコストに影響を与える可能性の高い考慮事項には、材料の種類、部品の複雑さ、金型の設計、注文数量などがあります。軽い金型は数量に左右され、数量が多ければ1個あたりのコストは低く抑えられるが、金型の初期コストは高くなる。