高圧ダイカスト(HPDC)は、現在の製造業で最も頻繁に利用されている金属鋳造プロセスの1つです。製造業者がHPDCを選択する理由は、高精度で迅速な生産速度、優れた寸法精度と滑らかな仕上げの両方を達成する複雑な金属部品の生産を可能にするからです。HPDCは、自動車や航空宇宙産業、電子部品や消費財の製造において、エンジンやハウジング、構造要素、機械組立品などの用途に使用される軽量で耐久性のある部品の製造を可能にします。高圧ダイカストの製造工程は、製品の品質を低下させ、寿命を縮め、性能を損なう重大な欠陥を生み出す多くのリスクに直面しています。様々な欠陥は、不適切な金型設計、乱れた溶湯の流れ、閉じ込められたガス、一貫性のない冷却速度、製造工程中の熱応力などから発生します。HPDC技術では、ポロシティ、コールド・シャット、収縮欠陥、フラッシュ形成、表面欠陥、ミスラン、金型浸食、はんだ付けといった7つの主要欠陥が発生します。これらのタイプの製造欠陥は、材料強度の劣化を引き起こすと同時に、不規則な寸法や望ましくない視覚効果を生じさせ、部品の故障を誘発する可能性がある。メーカー各社は、温度制御システムや真空アシスト鋳造手順とともに、加工パラメーターやより優れたアンダーマイニング方法を最適化することで、製造上の問題に対処しています。リアルタイムのモニタリングとシミュレーション・ソフトウェアは、ダイカスト・プロセスの効率と信頼性をさらに高める高度な品質管理手法です。
この記事では、高圧力下での標準的な製造上の問題を包括的に分析する。 ダイカスト このような欠陥を減少させるための根本的な原因と解決策を解説した技術です。これらの課題を理解し、ベストプラクティスを適用することによってのみ、製造業者はダイカスト部品の品質、寿命、そしてもちろん性能を向上させ、同時に廃棄物や製造コストを削減することができます。このような製造上の欠陥に精通することは、ダイカスト・エンジニア、生産管理者、品質管理専門家が、最高のダイカスト成果を得るためにプロセスを最適化するのに役立ちます。
1.気孔率
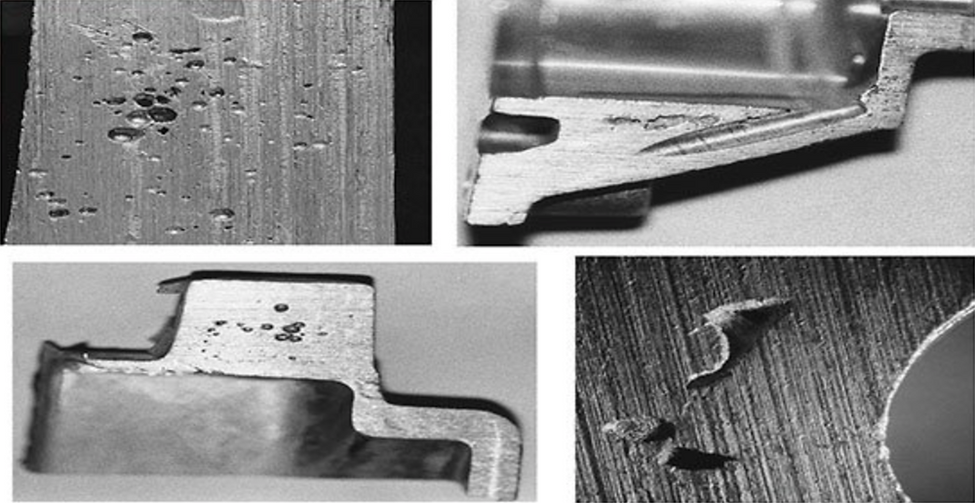
気孔は、金属マトリックス内に見られる小さな穴や気体の混入によって定義され、その結果、機械的特性に影響を与え、強度を低下させ、空気やガスが構造体を通過するのを許し、ダイカスト製品の目に見える表面欠陥につながる。
原因がある:
- 鋳造前の材料に含まれるガス状物質。
- 溶融金属の流れに過度の乱れがある。
- 換気が悪く、金型の設計が不適切。
- 収縮気孔の原因となる急速な凝固。
- 溶融金属の汚染。
- メタルが均一に流れない不十分な圧力。
予防と解決策:
- ゲートとベントの設計により、適切なガス遮断が達成されていることを確認する。
- 射出速度を遅くして、キャビティに入る金属の平滑性を高める。
- 空気の閉じ込め問題は、真空アシストダイカスト技術によって解決されるはずだ。
- 溶湯を注入する前に、溶湯が十分に脱気されていることを確認する。
- クラックやその他の凝固欠陥の形成の問題を克服するために、冷却速度を制御する。
- 汚染物質による気孔の可能性を減らすため、金型表面を頻繁にチェックし、清掃する。
2.コールドシャット
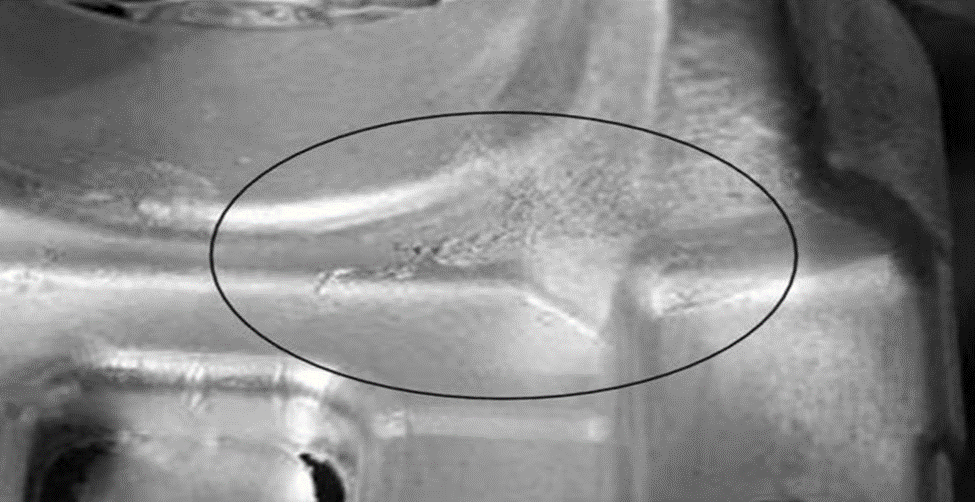
コールドシャットは、溶融金属の2つの流れが適切に融合せず、鋳造品に弱い接合部分や目に見える継ぎ目が形成された場合に生じます。この欠陥は機械的強度を低下させるだけでなく、破断の危険性を高め、部品の耐久性や外観にも悪影響を及ぼします。
原因がある:
- 溶湯温度が低い。
- 射出速度が遅いため、一般に凝固が早まる。
- 流路が不十分な金型設計。
- 過度の酸化を引き起こし、適切な融合を妨げる表面膜を形成する可能性がある。
- ゲートシステムの設計不良による、一貫性のないメタルフロー。
予防と解決策:
- また、適切な流動性を確保するために、最も最適な金属注湯温度を維持しなければならない。
- 射出速度を上げて充填を完了し、1枚にする。
- 金型設計において不必要な流動障壁を排除し、金属が問題なく移動できるようにする。
- 熱分析ツールを使用することにより、生産前に流れの問題を検出し、解決する。
- コールドシャットの欠陥を悪化させることの多い空気の滞留を避けるため、適切な換気技術を適用すべきである。
3.収縮不良
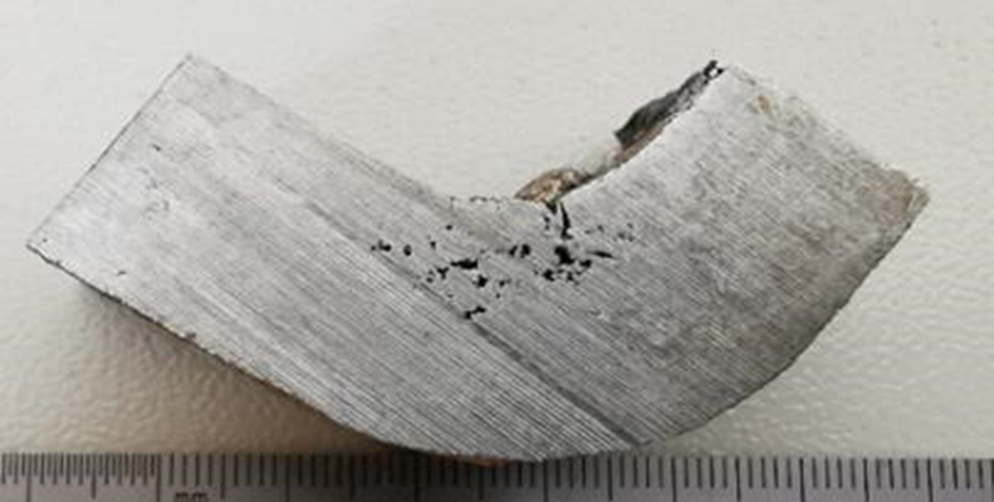
収縮欠陥は、冷却中の金属の収縮が原因で発生し、鋳物の構造的完全性を悪化させる内部空洞や空洞をもたらす。その結果、これらの欠陥は最終製品の機械的強度を低下させ、応力下で破損する可能性を引き起こし、表面品質が悪くなるため、最終製品の機能性と美観の両方に影響を与える。
原因がある:
- 凝固中の不十分な金属供給
- 金型設計が不適切なため、冷却速度にばらつきがある。
- 合金組成による高い金属収縮率
- 局所的な収縮を引き起こす急激な冷却
- 凝固段階での圧力不足
予防と解決策:
- 均一な冷却と溶融金属の適切な供給ができるように金型を修正する。
- 収縮傾向が少なく、凝固特性の良い合金を使用する。
- 固化時の圧力設定を最適化し、収縮ボイドを充填して最小化するために使用される。
- 凝固速度のバランスをとり、熱応力を下げるために、制御された冷却方法を使用する。
- 収縮の不具合を予測・防止するためのリアルタイムモニタリングとシミュレーションツールを導入する。
4.フラッシュ形成

高圧の金属逃げによってパーティングラインやダイギャップに形成される余分な薄い金属層は、フラッシュと呼ばれる。フラッシュは鋳造後に切り落とすことができますが、過剰なフラッシュは材料の無駄、工具の摩耗、関連する生産コストの増加につながり、ダイカスト工程の全体的な効率を低下させます。
原因がある:
- 過剰な射出圧力により、溶融金属が金型の隙間に押し込まれる。
- 金型が磨耗しているか、金型のロックが不適切なために漏れが生じている。
- クランプ力が不足し、射出中に金型が剥離する場合。
- 金属が漏れるような隙間があると、寝心地が悪くなる。
- 金型潤滑による不明瞭なメタルフロー制御
予防と解決策:
- ダイの剥離やバリ発生を避けるため、適切なクランプ力を維持しなければならない。
- 定期的に点検し、摩耗したダイスを交換することで、適切なシーリングを実現する。
- 充填物が最小限のフラッシュで充填されるように、圧力の最適設定を確認する。
- 意図しない隙間や金属漏れを防ぐために、ダイの再調整を改善すべきである。
- メタルフローを制御し、過剰なメタルエスケープを減らすために、正確なダイ潤滑技術を行う。
5.表面欠陥(ブリスター、クラック、しわ)の検査

様々な表面欠陥、ブリスター、クラック、しわは、鋳物の外観や機械的強度を低下させるため、防止・除去する必要があります。溶接欠陥の原因となり、製品の耐久性を低下させ、不合格率を高め、塗装やコーティングなど鋳造後の処理後の製品の密着性を悪くする。
原因がある:
- 注湯中に液体プラスチックに閉じ込められた空気。
- また、不均一な冷却速度による熱応力や表面の凹凸もある。
- 凝固中の過熱または不適切な温度管理。
- または、鋳造表面に影響を及ぼす可能性のある金属不純物や介在物
- ダイスの潤滑不良により、メタルフローが不均一になり、表面が不完全になった。
予防と解決策:
- 鋳造前に溶融金属を適切にガス抜きし、ガスがこもらないようにすること。
- 均一な冷却技術を使用することにより、凝固を制御し、熱応力を回避する。
- 金型の温度制御は、過熱や冷却ムラを防ぐために最適化されるべきである。
- 鋳造前にすべての不純物を検出できるよう、厳格な品質管理を行う。
- 表面品質と欠陥の低減に基づき、金型にコーティング剤や潤滑剤を塗布する。
6.インクルージョンとコンタミネーション
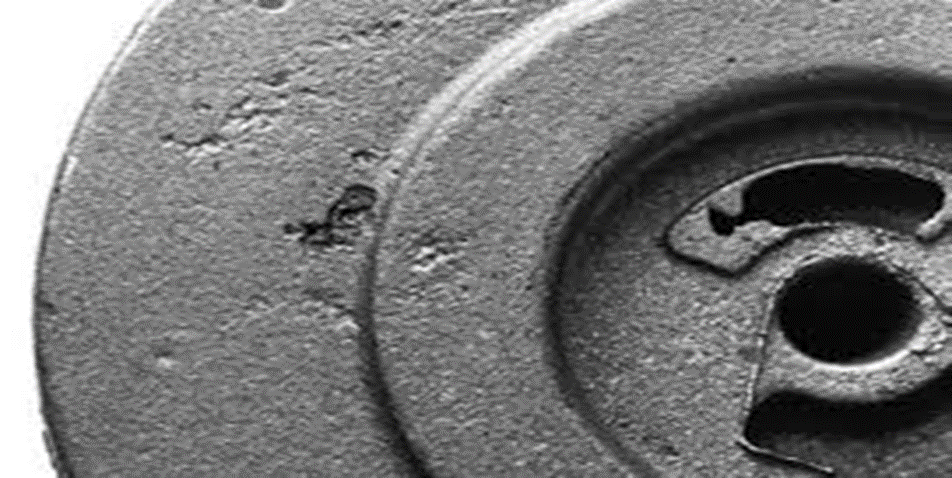
スラグ、酸化膜、汚れ、その他の不純物などの不要な異物が最終鋳造品に捕捉されると、機械的特性の低下、構造的完全性の低下、表面欠陥が生じ、介在物と呼ばれます。これらの異物が存在すると、ダイカスト部品の性能や耐久性が低下し、高精度な用途には適さなくなります。
原因がある:
- 例えば、汚染された原料は不要な不純物でできている。
- その結果、溶融金属中の異物はうまく濾過されない。
- 金属の溶解や注湯の際に空気に長時間さらされるため
- 非効率的な金属取り扱いが含まれ、その結果、スラグが多く生成される。
- 金型の潤滑不足には、溶融金属への異物の混入も含まれる。
予防と解決策:
- 高品質の原料は、汚染物質を含まず、適切に精製されなければならない。
- 注入前に溶融金属からスラグ、酸化物、その他の不純物を除去するための効果的な濾過システムを設置する。
- 溶融金属の取り扱いを管理し、場合によっては不活性ガス・シールドを使用して酸化を抑える。
- 残留物質による汚染を防ぐため、鋳造設備を定期的に清掃し、維持する。
- 金型キャビティに異物が堆積しないよう、適切な金型潤滑を行う。
7.ミスランとインコンプリート・フィル
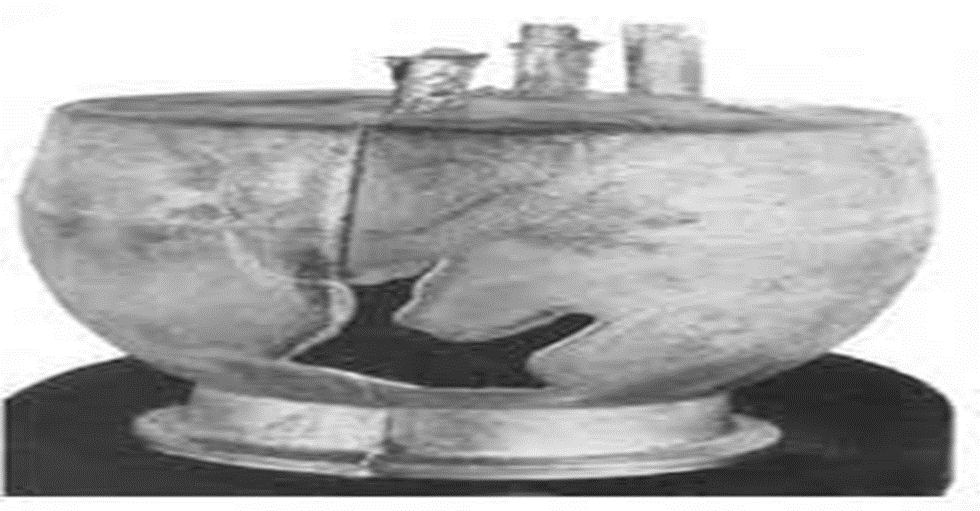
ミスランは、金型キャビティへの充填が不足することで発生し、最終的な部品に欠落部、薄肉部、弱点が生じる。部品の構造的完全性と機能性に悪影響を及ぼし、性能の高い用途には適さない。
原因がある:
- 射出速度や圧力が低い場合、金型を完全に覆わない。
- メタルフローと早期凝固を防止するコールドダイ表面
- 溶湯量が不十分で、窩洞への充填が不十分となる。
- 溶湯の不均等な分配を引き起こすゲートやランナーの設計不良によるもの。
- 過度の乱流は、金属の流れを妨げる空気のポケットを作り出す。
予防と解決策:
- 金属の温度を上げ、流動性を高め、早期凝固を避ける。
- さらに、射出圧力と射出速度を適切に設定することで、キャビティ充填を最適化しなければならない。
- 金型の適切な作業温度を維持し、金型が早期に冷却されるのを防ぐ。
- ゲートとランナーの設計を改善し、スムーズで均一なメタル配分を促進する。
- 生産前にシミュレーションソフトウェアでメタルフローとミスランの可能性をシミュレートする。
8.金型の浸食と摩耗
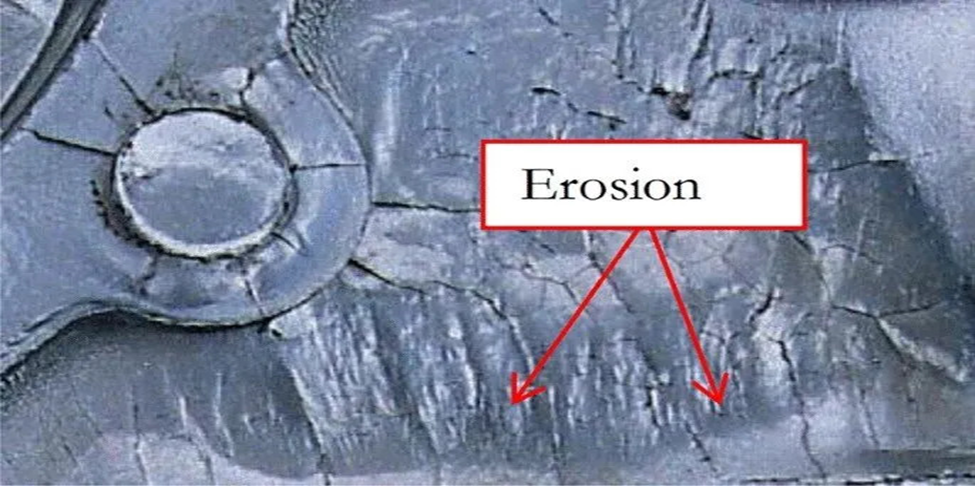
溶損金型の摩耗とは、高速の金属が必要な寸法に達するまで金型部品表面を連続的に摩耗させるために金型表面が損なわれることであり、その結果、表面仕上げが悪くなり、金型工具の寿命が短くなる。この欠陥が発生すると、金型の交換が一般的になり、その結果、鋳造品質が変化する一方で生産コストが上昇する。
原因がある:
- また、高温の溶融金属に繰り返しさらされるため、徐々に摩耗が進む。
- 熱的・機械的ストレスへの耐性が低い、相対的に質の低い金型材料
- 過度の熱サイクルは、疲労による材料のクラックを引き起こす可能性がある。
- 高射出での金型材料の劣化につながる。
- 潤滑が少ない?摩擦が増え、摩耗が進む。
予防と解決策:
- そのひとつが、耐久性に優れた高品質の耐熱金型素材を使用することだ。
- ダイの寿命を延ばすために、窒化やセラミックコーティングなどの保護表面コーティングを施すことができる。
- 熱応力を低減し、早期摩耗を誘発する制御された冷却方法が実施される。
- 金型への負担を最小限に抑えながら、スピードと圧力のバランスを取る。
- ダイスを定期的に点検し、侵食をできるだけ早く発見し、対処できるように維持する。
9.ホットクラッキング
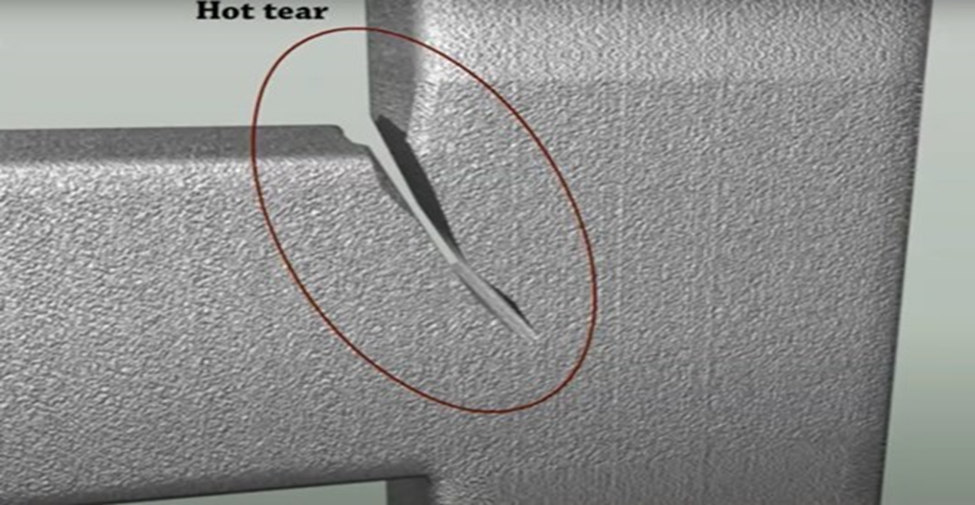
金属の半凝固状態で発生するクラックは、高い熱応力と過度の収縮によるもので、熱間クラックとして知られています。これらのひび割れは鋳物の機械的完全性を低下させ、ひび割れが存在する箇所で応力や荷重により鋳物が破損する可能性を高めます。
原因がある:
- 金型の冷却速度が不安定なため、特定の部分に応力点が生じる。
- 熱応力に対する感受性が高く、合金組成にクラックが発生しやすい。
- また、急冷凝固時に過大な残留応力が発生し、金属の収縮が制限される。
- 金型の設計が悪ければ、鋳物全体に温度差が生じる。
- 凝固時の圧力が小さすぎて、クラックの伝播を防ぐことができなかった。
予防と解決策:
- また、均一な凝固と熱応力の最小化のために冷却速度を最適化することも含まれる。
- より優れた結晶粒組織を持つ合金を適切に使用することで、合金の耐クラック性を向上させる。
- 鋳造後の応力除去技術の使用、つまり制御された熱処理。
- 温度差の少ない金型を設計する。
- 金属が流動し、亀裂が生じないように、凝固中に適切な圧力を確保する。
10.ハンダ付け
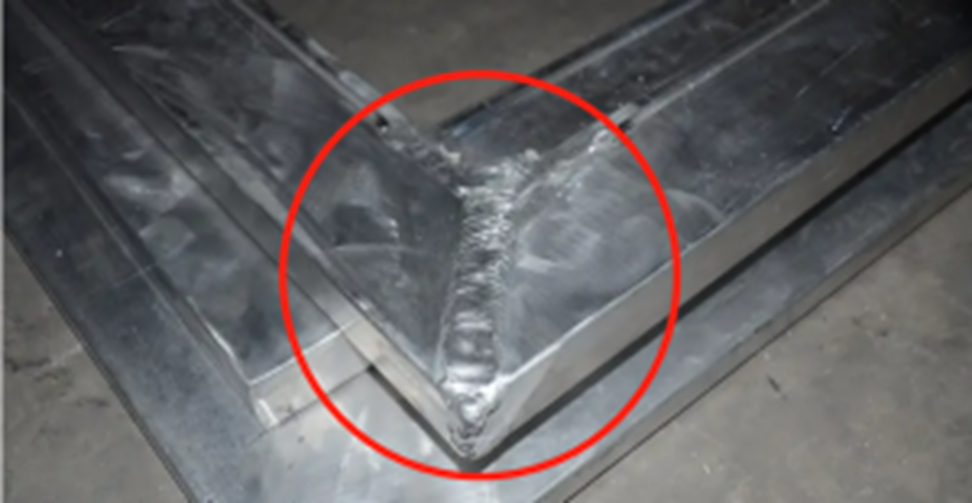
溶融金属は金型表面に付着し、鋳造で除去することは困難であるため、表面欠陥、金型の摩耗、生産停止時間の長期化を引き起こす。寸法の不正確さや表面仕上げの悪さもこの欠陥が原因で、最終製品の品質が全体的に損なわれる。
原因がある:
- アルミニウムの含有量が高いため、合金中の金属付着の事実が増加する。
- 金属が金型表面に接着するように、金型温度を過度に高くすること。
- 金型潤滑不良による固着防止が不十分
- 冷却が不十分で、溶融金属が金型に長時間接触したままになる。金型上面がスケーリングまたは損傷し、金属の付着を促進する。
予防と解決策:
- 金属の固着を防ぐため、高品質の金型潤滑剤が常に塗布されている。
- これにより、熱間接着が強すぎる場合、金型温度を最適な範囲に制御することができる。
- セラミック層や窒化物層など、適切なダイコーティングを施すことで、金属との密着性を低下させる。
- メタルとダイの接触時間を短縮し、冷却システムの効率を向上させる。
- 金型表面を定期的に検査し、研磨して、非粘着性の滑らかな表面仕上げにする。
結論
高圧 ダイカスト は、複雑な金属部品を高精度で最大の効率で製造する強力な製造プロセスである。しかし、不適切なプロセスパラメータ、材料の問題、金型設計の欠陥などを利用して、さまざまな種類の欠陥が発生します。製造者は、これらの通常の製造欠陥を理解した上で、最適なプロセス制御金型、適切に選択された材料などの予防措置を取ることができます。
企業は、欠陥防止戦略だけでなく、継続的なプロセス改善を重視することで、ダイカスト作業における製品品質の向上、生産コストの削減、生産効率の向上を達成することができる。
よくある質問 (FAQ)
1.高圧ダイカストで欠陥が発生する主な理由は何ですか?
高圧ダイカストにおける欠陥の主な原因には、不適切な金型設計、メタルフロー不良、ガスの閉じ込め、高い熱応力、不均等な冷却、汚染された原材料などがある。これらの欠陥は、プロセスパラメーターの最適化と品質管理手段の使用によって減らすことができます。
2.ダイカスト部品の性能に関して、気孔率はどのような役割を果たしますか?
気孔の存在は、ダイカスト部品の構造的完全性を弱め、強度を低下させ、圧密部品の空気漏れや麻酔薬の欠陥を引き起こす。ポロシティは、適切なガス抜き、最適化されたゲートシステム、および真空アシスト鋳造を使用することで最小限に抑えることができます。
3.ダイカストでコールドシャットを避けるには?
適切な注湯温度、射出速度の高速化、金属の流れをスムーズにするための金型設計の最適化、流れの問題を特定するための熱分析ツールの活用などが、コールドシャットの防止に役立つ。
4.高圧ダイカスト鋳造において金型浸食が重要な懸念事項である理由は?
高温の溶融金属が金型に繰り返しさらされると、金型の寿命を縮め、鋳造部品の精度を低下させる金型浸食が発生する。金型の寿命は、高品質の金型材料の使用、保護コーティングの使用、および制御された金型冷却によって延ばすことができます。
5.ダイカスト製品の品質と一貫性を高めるものは何ですか?
厳格な品質管理、工程パラメータの最適化、金型温度管理、高品質合金の使用、金型と機械の検査は、ダイカスト製品の品質を常に向上させるために定期的に行われている。