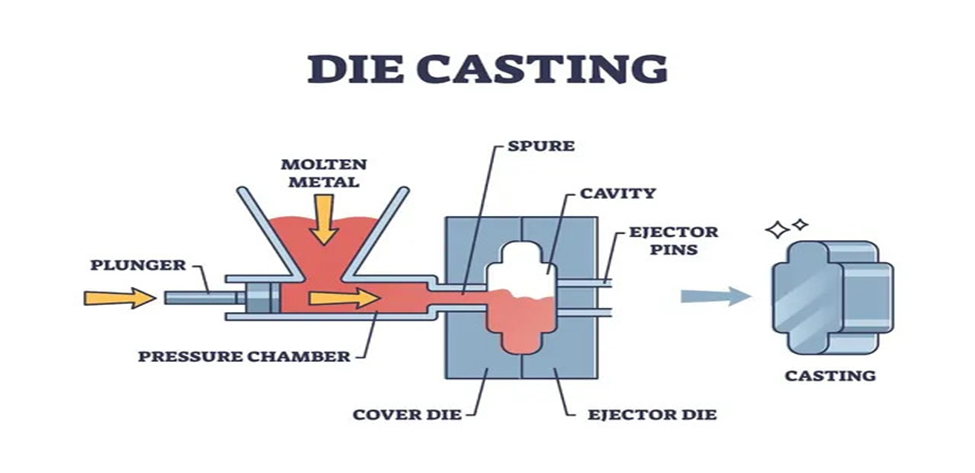
Si tratta di un processo di produzione in cui il metallo fuso viene forzato con la pressione per riempire la cavità di uno stampo, noto anche come pressofusione. Lo stampo è solitamente in acciaio di alta qualità e quindi il pezzo può essere prodotto in grandi quantità; il termine è usato per indicare la produzione di molti pezzi. Il pezzo finito viene poi prodotto aprendo lo stampo dopo che il metallo fuso si è raffreddato e ha formato uno strato solido. Questo tipo di utilizzo del processo viene applicato soprattutto per la produzione di metallo intricato utilizzato nella produzione di diversi pezzi che richiedono un'elevata precisione nelle misure e superfici lucide. La pressofusione può essere eseguita su alluminio, zinco e magnesio, ma è possibile utilizzare anche altri metalli a seconda dell'applicazione e di altri requisiti. Pressofusione è considerata una delle tecniche di produzione esperte nella concezione della produzione di massa di componenti di piccole e medie dimensioni in metallo. La popolarità di questo metodo si è diffusa nei settori automobilistico, aerospaziale, elettronico e delle macchine industriali, grazie alla sua capacità di produrre componenti durevoli e leggeri su misura. Tuttavia, questo processo è ampiamente riconosciuto per la sua capacità di fabbricare prodotti con geometrie complesse che sarebbero molto difficili da realizzare con le tecniche convenzionali.
Come funziona la pressofusione

Lo stampaggio è la prima parte del processo di pressofusione. Su un lato dello stampo, c'è una metà, ed è una metà di un design particolare per rendere lo stampo a forma del prodotto finale. Le cavità e le anime sono progettate per gli stampi, che di solito sono fatti su misura, in modo che il pezzo possa essere replicato il più fedelmente possibile.
1. Iniezione di metallo fuso:
Quindi il metallo fuso viene iniettato nella cavità dello stampo ad alta pressione per formare la forma desiderata. Il metallo viene solitamente riscaldato a un grado sopra il ceppo di fusione per renderlo fluido. Nella pressofusione, la pressione con cui il metallo fuso viene spinto nello stampo può variare da diverse migliaia a decine di migliaia di psi (libbre per pollice quadrato), per essere certi che il metallo fuso entri in ogni dettaglio dello stampo.
2. Solidificazione:
Questo avviene quando il metallo viene iniettato nella cavità dell'involucro, si raffredda e il metallo si indurisce. La qualità della colata dipende dalla velocità di raffreddamento. In questo caso entrano in gioco ulteriori modalità di rottura (taglio, salita e scivolamento) che determinano un raffreddamento più rapido, una maggiore resistenza e una migliore finitura superficiale, e un raffreddamento più lento, che potrebbe causare più difetti interni e proprietà meccaniche inferiori. Per favorire il processo di raffreddamento si utilizzano solitamente sistemi di raffreddamento ad acqua integrati nello stampo.
3. Espulsione:
In seguito, il metallo viene lasciato raffreddare e solidificare ed è quindi facile rimuovere lo stampo dalla colata più grande ed espellere il pezzo. La maggior parte del tempo viene impiegata per spingere fuori il pezzo dallo stampo utilizzando un sistema di espulsione meccanico. Questo dipende dalla complessità del pezzo che richiede altre fasi aggiuntive, come la rifilatura e la lavorazione per ottenere la forma e le dimensioni finali.
4. Controllo di qualità:
Dopo l'espulsione, il pezzo viene sottoposto a un controllo di qualità. Può comprendere la verifica dimensionale, l'ispezione visiva e le prove meccaniche per confermare che il pezzo è uguale o superiore ai requisiti. In teoria, la pressofusione consente di ottenere un'elevata precisione e ripetibilità.
Tipi di pressofusione
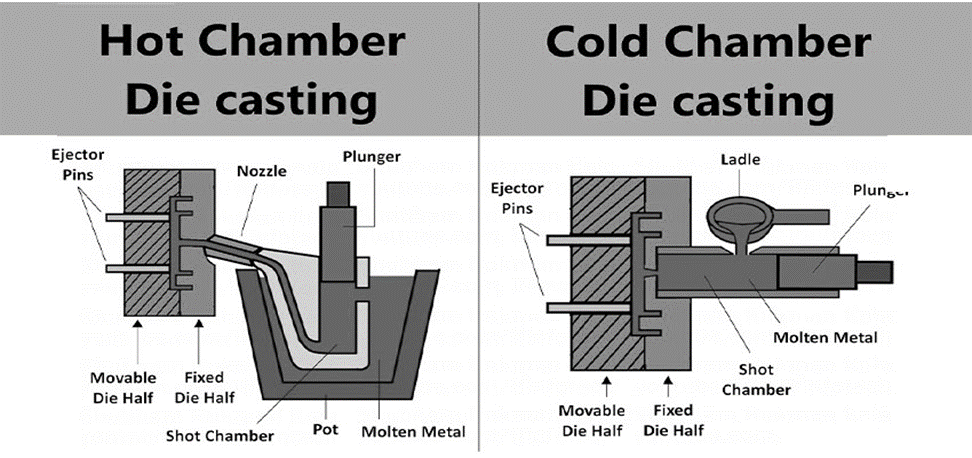
Esistono due tipi di pressofusione: la pressofusione a camera calda e la pressofusione a camera fredda. Sono tutti validi e hanno i loro vantaggi, limiti e applicazioni ideali.
1. Pressofusione a camera calda
Il processo più adatto per metalli come zinco, magnesio e piombo è la pressofusione a camera calda, poiché il processo avviene a temperature e punti di fusione elevati. Il sistema di iniezione è installato all'interno del forno di fusione: in questo modo, il metallo è sempre a contatto con la camera.
Vantaggi:
- Dato che il metallo fuso è predisposto per essere iniettato nello stampo perché si trova nella camera di iniezione, la pressofusione a camera calda richiede tempi più brevi rispetto alla pressofusione a camera fredda.
- Singolo stadio: comporta un numero inferiore di componenti e di tempo per la messa a punto, quindi è considerato economico, soprattutto nelle operazioni ad alto volume.
- Per alcuni metalli; la pressofusione a camera calda è più appropriata nelle situazioni in cui i metalli da utilizzare hanno basse temperature di fusione, in modo che la contaminazione dei metalli sia minima o nulla.
Svantaggi:
- Non può essere utilizzato per lavori in metallo ad alto punto di fusione, come alluminio e ottone, a causa dell'elevata temperatura del metallo che fonde la camera.
- Tutti i componenti sono esposti al metallo fuso e quindi il livello di usura è elevato nel tempo.
2. Pressofusione a camera fredda
I metalli che hanno punti di fusione più elevati, come l'alluminio, l'ottone e il rame, vengono fusi nella pressofusione a camera fredda. In questo caso, il metallo fuso viene prelevato da un secondo forno e iniettato nella camera fredda e poi nella cavità dello stampo.
Vantaggi:
- In termini di versatilità nella scelta dei materiali, la pressofusione a camera fredda offre una versatilità nell'uso dei materiali che consente di utilizzare materiali con punti di fusione elevati.
- Maggiore controllo sulla qualità del metallo: Poiché il cilindro di metallo fuso viene versato nella camera separatamente, la qualità del metallo può essere ben controllata per evitare contaminazioni.
- Maggiore durata degli utensili: Non essendo più a contatto con il metallo durante il processo di iniezione, la durata degli utensili aumenta.
Svantaggi:
- Tempo di ciclo più lento: il versamento manuale del metallo nella camera prolunga il ciclo.
- Il costo sarà più elevato perché si tratta di una procedura aggiuntiva con un'attrezzatura più complessa.
Il confronto tra i metodi di pressofusione: camera calda e camera fredda
Ecco un confronto tra i tipi più comuni di due metodi di pressofusione,
Caratteristica | Pressofusione a camera calda | Pressofusione a camera fredda |
Compatibilità dei metalli | Ideale per metalli a basso punto di fusione (ad es. zinco, piombo) | Ideale per metalli ad alto punto di fusione (es. alluminio, ottone) |
Tempo di ciclo | Tempi di ciclo più rapidi | Tempi di ciclo più lenti |
Usura dello stampo | Maggiore usura dello stampo a causa del contatto diretto con il metallo fuso | Minore usura dello stampo |
Costo | Costi ridotti per la produzione di grandi volumi | Costo iniziale più elevato, ma migliore per i metalli ad alta resistenza |
Complessità delle parti | Ottimo per le parti più semplici | Meglio per i pezzi più complessi e grandi |
Vantaggi della pressofusione
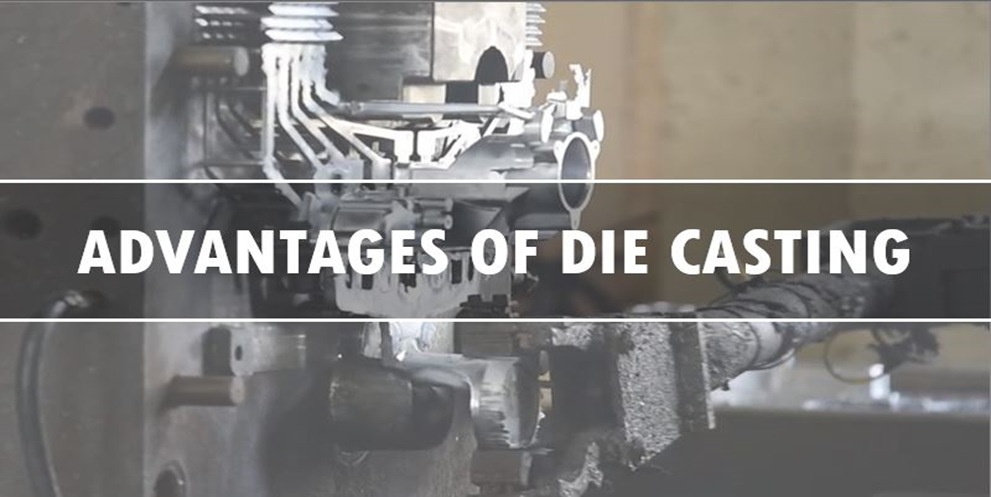
Uno dei maggiori vantaggi è che la pressofusione è uno dei principali metodi preferiti per la produzione su larga scala di prodotti in lega metallica.
1. Alta precisione e accuratezza
I vantaggi della pressofusione sono molteplici e consentono di offrire un'elevata precisione dello stampo. Questo metodo di produzione è anche ampiamente utilizzato per la produzione di pezzi che richiedono una buona precisione dimensionale, che è molto cruciale in quanto definisce i livelli di tolleranza richiesti in un lavoro specifico. Si noti che la pressofusione è l'unica tecnica di produzione in grado di produrre pezzi con la massima complessità, come ad esempio la complessità delle geometrie.
2. Tassi di produzione elevati
In termini di grandi volumi, la pressofusione è molto efficiente. Una volta creato il primo stampo, i pezzi vengono prodotti in modo rapido ed economico, con pochissima manodopera. La domanda di polveri simulate è particolarmente elevata in settori come quello automobilistico ed elettronico, dove sono richiesti grandi volumi degli stessi pezzi.
3. Progetti complessi e pareti sottili
La pressofusione consente di realizzare design complessi, che sarebbero difficili o impossibili da ottenere con i metodi di produzione tradizionali. Il processo può realizzare pezzi con pareti sottili e strutture interne complesse, e può accogliere sottosquadri; è quindi l'applicazione più adatta nei casi in cui lo spazio è limitato.
4. Efficienza dei materiali
La pressofusione riduce al minimo gli scarti di materiale. La pressione utilizzata per iniettare il metallo fuso riempie ogni parte della cavità dello stampo e quindi si creano meno scarti. Inoltre, molti pezzi pressofusi possono essere riciclati, contribuendo così alla sostenibilità del processo.
5. Eccellente finitura superficiale
La finitura superficiale dei pezzi prodotti in pressofusione è liscia ed estetica. Richiede meno processi di finitura secondaria, come la lucidatura o il rivestimento, con conseguente risparmio di tempo e di costi.
Cosa si può applicare al processo di pressofusione?
I metalli non ferrosi sono utilizzati principalmente nella pressofusione grazie alle buone caratteristiche di fusione. Le leghe di alluminio sono i materiali comunemente utilizzati per la pressofusione, come indicato dai seguenti materiali.
1. Leghe di alluminio

Grazie alla sua leggerezza, alla resistenza alla corrosione e all'eccellente conduttività di calore ed elettricità, l'alluminio è il materiale più utilizzato nella pressofusione. Procedendo con l'elenco, le leghe di alluminio di grado speciale sono utilizzate quando il rapporto resistenza-peso è un fattore importante, soprattutto nell'industria automobilistica, aerospaziale ed elettrica. Infine, sono anche stabili dal punto di vista dimensionale, il che li rende adatti alla produzione di pezzi di alta precisione.
2. Leghe di zinco
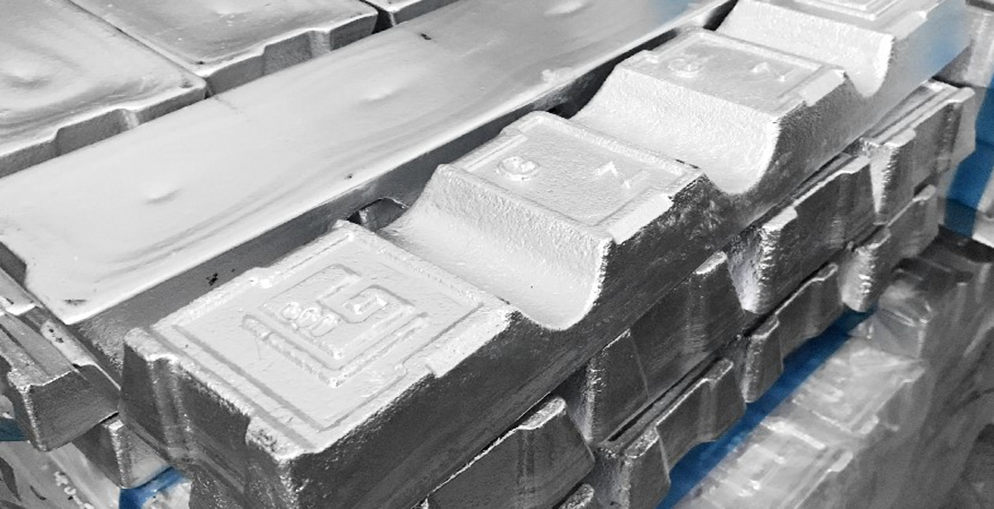
Le leghe di zinco per pressofusione possono essere preferite grazie alle loro proprietà, come il basso punto di fusione e l'elevata fluidità, che consentono di realizzare in modo semplice ed efficiente progetti complessi con sezioni sottili e dettagli nitidi. Questi pezzi di zinco possiedono un'elevata tenacità, sono altrettanto resistenti alla corrosione e possiedono una lucidatura di alta qualità. Un'altra area di applicazione delle leghe di zinco è la produzione di ricambi per auto e altri veicoli, la ferramenta e l'elettronica.
3. Leghe di magnesio

Vale la pena ricordare che il magnesio è il metallo strutturale più leggero e quindi offre un peso significativo nei componenti destinati alle automobili o agli aeroplani. Questo perché le leghe di magnesio sono utilizzate in componenti che devono essere forti ma il più possibile leggeri. Tuttavia, poiché il metallo è molto reattivo, la lega deve essere ben gestita durante il processo di pressofusione.
4. Leghe di rame
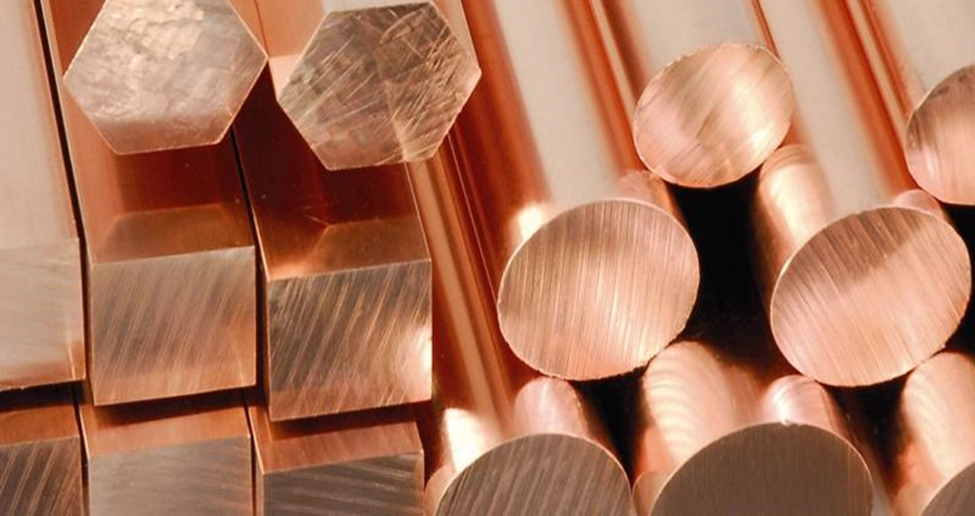
Oltre all'alluminio e allo zinco, anche le leghe a base di rame, l'ottone e il bronzo, sono utilizzate nella pressofusione, ma non così frequentemente come l'alluminio e lo zinco. Offrono buone proprietà di resistenza all'usura e sono spesso utili per applicazioni elettriche e idrauliche.
È molto importante notare che le diverse forme dei materiali di base sono adatte a diverse applicazioni e i costi variano da una forma all'altra, così come le proprietà del prodotto finale.
La pressofusione rispetto ad altri metodi di fusione
Rispetto a metodi di colata come la colata in sabbia, la colata per investimento e la colata in stampo permanente, questa sezione potrebbe essere la sezione di confronto della pressofusione. Nel farlo, è opportuno evidenziare i punti di forza e di debolezza di ciascun metodo, insegnando ai lettori quando scegliere la pressofusione rispetto ad altre alternative. Pertanto, questa potrebbe essere una panoramica comparativa che aiuterebbe a determinare il metodo di colata ottimale in base al materiale, alla complessità e al volume di produzione del pezzo.
Caratteristica | Pressofusione | Colata in sabbia | Colata a iniezione |
Precisione | Alta precisione con tolleranze ristrette | Precisione inferiore e finitura superficiale ruvida | Alta precisione e finitura liscia |
Velocità | Più veloce per la produzione di grandi volumi | Ciclo di produzione più lento | Rallentamento dovuto alla preparazione dello stampo |
Materiale di scarto | Rifiuti minimi | Scarti più elevati a causa della finitura più ruvida | Scarti minimi, ma stampi più complessi |
Costo | Economicamente vantaggioso per volumi elevati | Costo inferiore per la produzione di bassi volumi | Costi più elevati a causa della complessità e della manodopera |
Saranno messi a confronto i processi produttivi della pressofusione e dello stampaggio a iniezione.
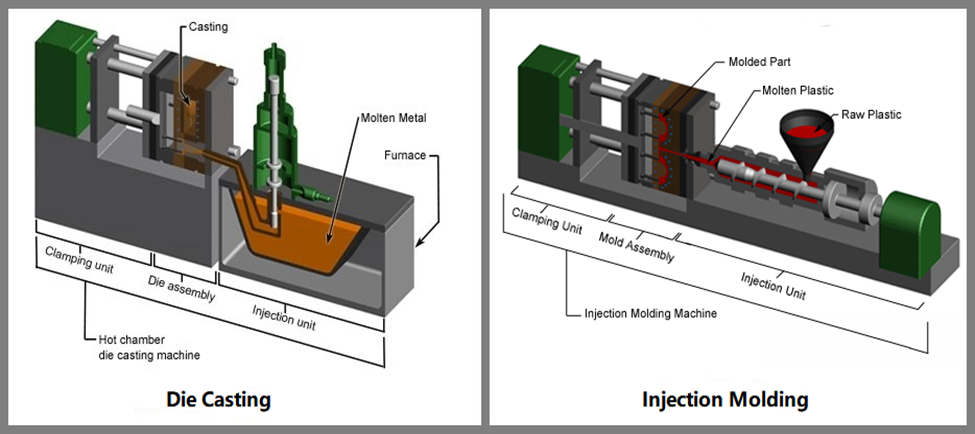
Due tecniche comuni utilizzate per la produzione di pezzi di dettaglio con forme intricate sono la pressofusione e lo stampaggio a iniezione. Anche se entrambe le tecniche prevedono l'uso di materiali che formano dettagli per produrre prodotti finali, le due tecniche presentano differenze in termini di tipo di materiale, di prodotto formato e, in particolare, di vantaggi in termini di ciascun processo.
1. Materiali utilizzati
Pressofusione: La pressofusione è preferita con altri metalli oltre al gruppo dei metalli ferrosi, in particolare alluminio, zinco, abilità e leghe di rame. I metalli vengono riscaldati e poi versati in uno stampo attraverso l'uso della pressione idraulica. Per questo motivo, la pressofusione è il metodo più appropriato per produrre pezzi forti, durevoli e in grado di resistere alle alte temperature.
Stampaggio a iniezione: Lo stampaggio a iniezione è comunemente utilizzato tra i materiali plastici, mentre è raramente possibile su metalli e vetri. Tra i polimeri più utilizzati figurano il polietilene, il polipropilene e il polistirene. Il materiale di formazione del prodotto è anche leggero e flessibile; inoltre, i costi sono bassi e le forme piuttosto complesse, quindi è possibile notare che lo stampaggio a iniezione è perfetto per questo tipo di prodotti.
2. Differenze di processo
Pressofusione: Come suggerisce il nome, si tratta del processo di iniezione di metallo fuso ad alta pressione nello stampo. Dopo il raffreddamento e la solidificazione del metallo ad altissima velocità, le stampi emergono con una tolleranza fine e una buona finitura superficiale, senza ulteriori operazioni da eseguire.
Stampaggio a iniezione: Poiché lo stampaggio a iniezione prevede l'iniezione di materiale plastico fuso in una cavità dello stampo mediante l'applicazione di una pressione, si tratta di uno stampaggio a iniezione. Quando la temperatura della plastica fusa si riduce, lo stampo si apre e il prodotto è lo stampo di plastica. Lo stampaggio a iniezione può comunque garantire un'elevata precisione, sebbene sia comunemente utilizzato per produrre pezzi relativamente più piccoli e leggeri rispetto alla pressofusione.
3. Applicazioni
Pressofusione: La pressofusione è utile per realizzare parti dure e robuste utilizzate nella produzione di automobili, aerei e altri prodotti elettronici, grazie alla sua eccellente resistenza al calore.
Stampaggio a iniezione: Può essere utilizzato per produrre prodotti di consumo, imballaggi, dispositivi medici e giocattoli, perché in questi casi sono importanti la flessibilità, la facilità di progettazione e la produzione a basso costo.
Applicazioni della pressofusione

Uno dei fattori che hanno reso la pressofusione un processo di produzione popolare in molti settori è che consente di produrre pezzi di alta qualità e durevoli con geometrie piuttosto complicate. Alcune delle applicazioni includono:
1. Industria automobilistica
In genere, i componenti del motore, gli alloggiamenti della trasmissione e altre parti importanti del settore automobilistico sono realizzati mediante pressofusione. I componenti pressofusi hanno la precisione e la resistenza necessarie per essere installati nelle applicazioni più impegnative dell'industria automobilistica.
2. Industria elettronica
La pressofusione nel settore dell'elettronica è utilizzata per produrre alloggiamenti per apparecchiature elettroniche come telefoni cellulari, computer portatili e televisori. La tecnica consente di realizzare involucri leggeri ma resistenti, in grado di proteggere i componenti più delicati.
3. Industria aerospaziale
La pressofusione è di grande utilità per le aziende manifatturiere del settore aerospaziale, in quanto consente di produrre pezzi leggeri ad alta resistenza, necessari per aerei e veicoli spaziali. I pezzi pressofusi hanno la precisione e le proprietà dei materiali per essere utilizzati in applicazioni in cui le prestazioni e la sicurezza sono importanti.
4. Attrezzature industriali
Anche le parti di macchinari, utensili e altre attrezzature industriali vengono fuse in pressofusione. Poiché è in grado di produrre pezzi con geometrie dai dettagli intricati e buone proprietà meccaniche, è un ottimo strumento per queste applicazioni.
Conclusione
La pressofusione è un processo produttivo versatile, economico ed efficiente, utilizzato in molti settori industriali. La qualità prodotta è estremamente elevata in termini di tolleranze dei pezzi, finitura superficiale e alti tassi di produzione, il che la rende uno strumento di produzione eccellente per le moderne pratiche di produzione. La pressofusione risponde alle esigenze di molti settori che richiedono resistenza, precisione ed efficienza nei componenti, dall'industria automobilistica a quella aerospaziale, dall'elettronica alle attrezzature industriali.
Sebbene la tecnologia sia in rapida crescita e probabilmente continuerà ad essere utilizzata come fonte di componenti metallici di eccellente fattura su scala enorme, in pressofusione. Una migliore comprensione dei fondamenti della pressofusione può aiutare i professionisti dell'ingegneria, della produzione e della progettazione a prendere decisioni informate su come utilizzare il processo di pressofusione per ottenere il risultato desiderato.
Domande frequenti sulla pressofusione
1. Qual è il ciclo temporale della pressofusione e dello stampaggio a iniezione?
Il tempo di ciclo per un determinato pezzo va da 15 a 5 minuti per la pressofusione e da 10 a 60 secondi per lo stampaggio a iniezione.
2. La pressofusione può essere utilizzata per le parti in plastica?
La pressofusione non è utilizzata per i non metalli. Per produrre le parti in plastica si ricorre comunemente alle tecniche note come stampaggio a iniezione.
3. Quali sono i prodotti più adatti al processo di produzione della pressofusione?
La pressofusione è particolarmente indicata per la produzione di pezzi complicati di piccole e medie dimensioni con un elevato grado di precisione, realizzati in metallo. Alcuni dei prodotti meccanici che vengono realizzati includono parti e accessori di automobili, involucri di prodotti elettrici, parti elettroniche e involucri di apparecchiature, tra gli altri.
4. In che modo la pressofusione è diversa dalla colata in sabbia.
Tuttavia, quando si confrontano i due metodi: La pressofusione è più accurata e richiede meno tempo rispetto alla fusione in sabbia. Mentre la colata in sabbia è preferibile per i lavori di grandi dimensioni e meno complicati, la colata in AL è preferibile per i lavori di piccole dimensioni e complessi, in quanto consente di ottenere superfici più lisce e tolleranze più strette, tipiche delle alte tirature.
5. Cosa determina il costo della pressofusione?
Alcune delle considerazioni che possono influenzare il costo della pressofusione sono: il tipo di materiale, la complessità del pezzo, la progettazione dello stampo e la quantità degli ordini. L'attrezzaggio leggero dipende dal volume, anche se un volume elevato mantiene basso il costo unitario, i costi iniziali dell'attrezzaggio sono elevati.