Sono pochi i luoghi in cui si può imparare a saldare l'alluminio fuso e le competenze necessarie per farlo sono altamente specializzate. Tuttavia, l'alluminio fuso è un materiale creato versando alluminio fuso in uno stampo, ottenendo un materiale poroso con impurità. Questo non accade con le leghe di alluminio standard. A causa di queste caratteristiche, la saldatura è più difficile e per produrre saldature forti e robuste è necessario prepararsi con attenzione, tenere sotto controllo il calore e utilizzare le tecniche appropriate. L'ossidazione è uno dei maggiori ostacoli alla saldatura dell'alluminio fuso. Questo sottile strato di ossido, che si forma quando è esposto all'aria, è molto più spesso di quello che si forma naturalmente sull'alluminio e fonde a una temperatura molto più alta dell'alluminio stesso, rendendo difficile la fusione. Inoltre, la presenza di impurità e di gas intrappolati nell'alluminio fuso può provocare porosità che, se non adeguatamente pulite e preriscaldate, rendono le saldature deboli.
Il TIG (Tungsten Inert Gas) è il metodo preferito per la precisione e la pulizia, mentre il MIG (Metal Inert Gas) è utile per la velocità e il materiale più spesso. Per ottenere una saldatura forte e priva di difetti, è necessario utilizzare il metallo d'apporto corretto (come 4045, 5356 o 4047) e la combinazione di gas di protezione (argon puro o miscele argon-elio). Una buona preparazione comprende una pulizia e un preriscaldamento adeguati, per quanto possibile, per ridurre al minimo le cricche, la porosità e la mancanza di fusione. La resistenza e la durata dei giunti saldati sono ulteriormente migliorate dai trattamenti post-saldatura, come la riduzione delle tensioni, la rettifica e la protezione dalla corrosione dopo la saldatura.
Mentre la maggior parte dei saldatori di alluminio fuso sono saldati in acciaio, i saldatori possono lavorare con successo con alluminio fuso utilizzando le tecniche, gli strumenti e l'attenzione ai dettagli giusti, finché nelle industrie sono richiesti componenti leggeri e ad alta resistenza. Si tratta di un processo che si può padroneggiare e che porta a un ulteriore sviluppo delle applicazioni di saldatura dell'alluminio e a prestazioni affidabili e prevedibili delle strutture in alluminio in ambienti critici.
Capire l'alluminio fuso
Tuttavia, prima di procedere con le tecniche di saldatura necessarie per l'alluminio fuso, è fondamentale avere una solida comprensione di ciò che costituisce l'alluminio fuso e di ciò che lo rende unico rispetto agli altri metalli. L'alluminio fuso si differenzia dall'alluminio battuto, che viene modellato meccanicamente mediante laminazione o estrusione, in quanto l'alluminio fuso può essere formato in forme complesse di alta precisione fondendo l'alluminio e versando questa forma fusa in uno stampo. La particolare struttura interna così prodotta, solitamente caratterizzata da porosità, impurità e composizione variabile della lega, ha un effetto importante sulla saldabilità.
Per poter saldare con successo l'alluminio fuso, è necessario conoscerne le proprietà chimiche e fisiche, i pro e i contro e i diversi tipi di leghe di alluminio fuso di varie industrie. Questi fattori saranno presi in considerazione per determinare il metodo di saldatura necessario, la scelta del materiale d'apporto e le tecniche di preparazione pre-saldatura per realizzare saldature resistenti e prive di difetti.
Proprietà dell'alluminio fuso: Cosa rende diversa una fusione?
Un'altra considerazione importante è che l'alluminio fuso ha diverse proprietà che lo rendono leggero, anti-corrosivo e molto flessibile. Tuttavia, le stesse proprietà pongono anche alcune difficoltà in fase di saldatura, a patto che non si adottino misure adeguate.
1. Porosità: La sfida nascosta
Una delle maggiori preoccupazioni legate alla saldatura dell'alluminio fuso è la porosità, ovvero le piccole bolle di gas che rimangono intrappolate nel metallo durante la fusione. Queste bolle derivano dall'intrappolamento di gas come l'idrogeno, dalla formazione di piccoli pori in seguito al ritiro durante il raffreddamento dell'alluminio e dalle impurità.
🔹 Come la porosità influisce sulla saldatura
- Indebolisce la resistenza meccanica e la saldatura è soggetta a cricche.
- Contribuisce alla contaminazione delle saldature e quindi compromette la resistenza delle giunzioni realizzate.
- Blocca i gas nell'area di saldatura, una volta formate le irregolarità della superficie.
🔹 Come ridurre al minimo la porosità durante la saldatura
- La preparazione della superficie del metallo attraverso la pulizia deve essere adeguata prima di iniziare la saldatura.
- Afferrare il foglio di alluminio e riscaldarlo per ridurre lo stress termico sull'alluminio e per minimizzare la formazione di bolle d'aria.
- Per evitare l'ossidazione, è necessario utilizzare un gas inerte di alta qualità, l'Argon 100%.
2. L'ossidazione: L'ostacolo alle saldature pulite
È un elemento che reagisce con altri elementi, in particolare con l'ossigeno presente nello spazio circostante il metallo. Questa ossidazione genera una pelle molto sottile ma estremamente dura di ossido di alluminio (Al₂O₃) attraverso la quale viene impedita l'ulteriore corrosione dell'alluminio. Tuttavia, lo strato di ossido è un problema critico durante la saldatura, poiché la sua temperatura di fusione è di circa 3700°F (2037°C), molto più alta di quella dell'alluminio, pari a 1221°F (660°C).
Indagine sui motivi per cui l'ossidazione è un problema nella saldatura
- È determinante per la formazione del legame lungo tra l'apporto di saldatura e il metallo base?
- Questo ha portato alla contaminazione del bagno di saldatura e quindi alla produzione di saldature scadenti.
- Deve essere preparato prima della saldatura poiché presenta uno strato di ossido.
🔹 Diverse tecniche di rimozione e controllo dell'ossidazione
- Sciacquare l'oggetto in alluminio con acqua tiepida, quindi utilizzare una spazzola in acciaio inossidabile, da usare solo per la pulizia dell'alluminio, per eliminare lo strato di ossido.
- Pulire la superficie con acetone o alcool come processo di pulizia pre-saldatura, perché l'olio galleggia sui metalli e il grasso vi affonda.
- Per eliminare l'ossidazione, si consiglia di utilizzare la corrente alternata nella saldatura TIG.
3. Sensibilità al calore: Gestione della conducibilità termica
A differenza dell'acciaio, l'alluminio ha un'elevata conducibilità termica e può facilmente assorbire ed emettere calore. Questo è sempre stato un problema nel mantenere una temperatura di saldatura standard; ciò tende a causare quanto segue:
- Fusione incompleta a causa della rapida perdita di calore.
- Tre, deformazioni o distorsioni soprattutto in parti sottili di alluminio.
- Bruciatura, in particolare nelle sezioni altamente porose o sottili dell'alluminio fuso.
🔹 Come superare le sfide della sensibilità al calore
- Ciò serve a regolare il flusso di calore in modo che tutte le parti del materiale utilizzato siano calde quanto la temperatura desiderata.
- Essere in grado di mettere a punto il sistema di controllo del calore e l'uso inclinato della saldatura TIG.
- È possibile ridurre la quantità di calore applicata all'area di saldatura in questo modo, ovvero utilizzando passate di saldatura più brevi.
Tipi comuni di leghe di alluminio fuso
È possibile fondere diversi tipi di leghe di alluminio in base alla loro composizione chimica e alle loro proprietà meccaniche. Ecco alcuni vantaggi e svantaggi di ciascun tipo, nonché le applicazioni in cui sono più utili.
1. Alluminio fuso A356: La lega ad alta resistenza
La sua composizione: Comprende principalmente alluminio (Al), silicio (Si) e magnesio (Mg).
🔹 Caratteristiche principali
- Ha un'elevata resistenza alla trazione ed è adatto per applicazioni strutturali.
- Eccellente resistenza alla corrosione, soprattutto in ambienti umidi.
- Ha una buona saldabilità, anche se potrebbe essere necessario un trattamento termico post-saldatura per recuperare la resistenza.
🔹 Applicazioni comuni
- Viene utilizzato nei componenti del motore, nelle ruote e nelle scatole di trasmissione dell'industria automobilistica.
- Industria aerospaziale - Si trova nelle parti strutturali degli aerei grazie al suo rapporto forza-peso.
- Dispositivi medici - Utilizzati in strumenti chirurgici e involucri ad alta resistenza.
2. 319 Alluminio fuso: La lega resistente all'usura
Composizione: Contiene livelli più elevati di silicio (Si) e rame (Cu) rispetto all'A356.
🔹 Caratteristiche principali
- Ottima resistenza all'usura per applicazioni pesanti.
- È più fragile e ha un contenuto di silicio più elevato, quindi è più difficile da saldare.
- Sono necessari materiali di riempimento specializzati (4047) per prevenire le fessurazioni.
🔹 Applicazioni comuni
- Varianti resistenti all'usura: teste di cilindri e blocchi motore per autoveicoli.
- Le pompe e gli alloggiamenti devono essere durevoli.
- I componenti per i macchinari industriali sono destinati alle condizioni più severe e ad alta sollecitazione meccanica.
3. 535 Alluminio fuso: La lega marina
Composizione: Contiene un'alta percentuale di magnesio (Mg) per la resistenza alla corrosione.
🔹 Caratteristiche principali
- Resistenza alla corrosione superiore, soprattutto in ambienti con acqua salata.
- La saldabilità è buona, ma è necessaria una pulizia completa prima della saldatura per evitare la contaminazione.
- Più facile da modellare e riparare rispetto al 319.
🔹 Applicazioni comuni
- L'elevata resistenza alla corrosione dell'acqua salata li rende adatti agli scafi delle imbarcazioni, alle parti dei motori marini e alle eliche.
- Viene utilizzato per le parti di aerei e aerospaziali che richiedono materiali resistenti e leggeri.
- Elementi che rappresentano una minaccia minima per i componenti industriali sottoposti ad ambienti chimici difficili.
Perché capire l'alluminio fuso è importante per la saldatura
Per iniziare a padroneggiare la saldatura dell'alluminio fuso è necessario determinare di cosa è fatto l'alluminio fuso, le sue proprietà e le sfide associate. Pertanto, poiché l'alluminio fuso è ampiamente utilizzato nell'ingegneria automobilistica, aerospaziale e navale, i saldatori necessitano di strategie per la porosità della fusione, l'ossidazione e la sensibilità al calore.
Diversi tipi di calco leghe di alluminio I materiali d'apporto, il gas di protezione e la tecnica di saldatura sono diversi e fanno la differenza tra una saldatura forte e affidabile e un giunto debole e poroso.
Con la preparazione del materiale, l'uso di procedure di pulizia corrette e la regolazione dell'apporto di calore, i saldatori possono affrontare i problemi associati all'alluminio fuso e generare saldature potenti e di lunga durata che soddisfano le applicazioni più difficili.
Sfide nella saldatura dell'alluminio fuso
La saldatura dell'alluminio fuso è notoriamente difficile a causa delle sue particolari proprietà fisiche e chimiche. La consapevolezza di queste difficoltà aiuta i saldatori a utilizzare gli strumenti e i metodi di applicazione giusti, ottenendo saldature robuste e prive di difetti.
1. Problemi di ossidazione: Un importante ostacolo alla saldatura
Quando l'alluminio viene esposto all'aria, si ossida quasi istantaneamente, producendo un ossido di alluminio molto sottile ma molto resistente (Al₂O₃). Ha poi spiegato che lo strato di ossido formatosi durante l'ossidazione iniziale dell'alluminio ha un punto di fusione di 3.700°F (2.037°C), tre volte superiore al punto di fusione dell'alluminio, che è di 1.221°F (660°C). Tuttavia, questa enorme differenza di punti di fusione causa gravi difficoltà nella saldatura, tra cui le seguenti:
- Fusione incompleta (lo strato di ossido impedisce al metallo d'apporto di legarsi correttamente al materiale di base).
- Saldature contaminate - Presenza di ossidazione che, se lasciata nella saldatura, può causare porosità, giunti deboli e inclusioni.
- L'ossido produce un arco instabile, che provoca un'oscillazione dell'arco e prestazioni di saldatura irregolari.
Soluzione
La saldatura TIG a corrente alternata (AC) aiuta a mantenere lo strato di ossido dal pezzo in lavorazione e a mantenere la stabilità dell'arco. Inoltre, una spazzola in acciaio inox dedicata e detergenti chimici come l'acetone possono pulire l'ossidazione prima della saldatura.
2. Impurità e contaminazione: La minaccia nascosta
L'alluminio è spesso fuso da materiali riciclati e può quindi includere gas intrappolati, residui di olio, sporcizia e altre impurità legate alla produzione della colata. Questi contaminanti devono essere puliti correttamente prima della saldatura, altrimenti possono provocare:
- La saldatura è indebolita e soggetta a cricche a causa di piccole sacche di gas (porosità).
- Inclusioni: - Ha intrappolato nella saldatura una sostanza non metallica che riduce la resistenza della saldatura.
- Alcune aree possono fondersi bene e altre possono rimanere deboli con una qualità di saldatura incoerente.
Soluzione
L'acetone o l'alcol vengono utilizzati per pulire a fondo la superficie da grasso e sporco. I gas intrappolati devono essere espulsi con una torcia di preriscaldamento prima della saldatura.
3. La conducibilità termica è troppo alta: È necessario controllare il calore
L'alluminio, invece, è destinato ad assorbire e trasmettere il calore con estrema rapidità, rispetto all'acciaio. Questo può portare a:
- Un calore eccessivo può sciogliere le sezioni più sottili (burn through).
- Riscaldamento sbilanciato (deformazione e distorsione) - Il metallo si deteriora perché è stato riscaldato in modo non uniforme.
- Penetrazione incoerente - Dissipazione troppo rapida del calore che provoca una fusione debole nel giunto di saldatura.
Soluzione
Inoltre, è consigliabile preriscaldare l'alluminio a 300°F - 600°F (150°C - 315°C) per ottenere una distribuzione uniforme del calore e una migliore penetrazione della saldatura. Un apporto di calore più elevato alla velocità di avanzamento controllata mantiene stabile il bagno di saldatura.
Strumenti e attrezzature essenziali per la saldatura dell'alluminio fuso
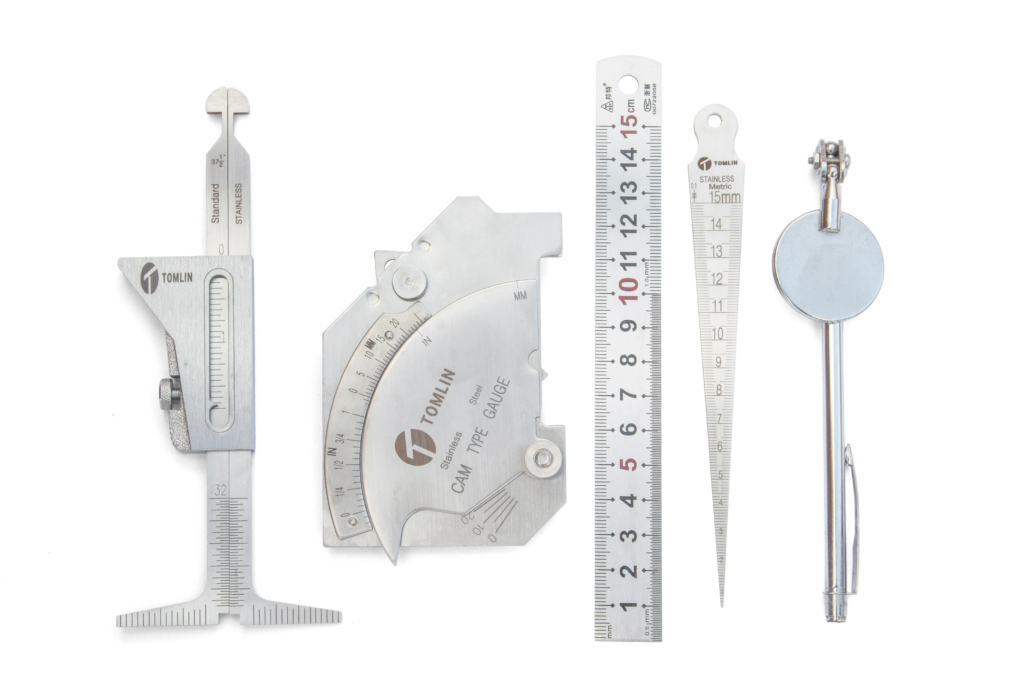
Quando si salda l'alluminio fuso, sono necessarie attrezzature specializzate e la saldatura deve essere accurata, resistente e duratura.
- Un processo di saldatura è di per sé uno strumento che deve essere scelto con attenzione, e questo è ciò che viene trattato in questa guida alle saldatrici.
- La scelta giusta della saldatrice è molto importante quando si deve saldare l'alluminio.
- Saldatrice TIG (Tungsten Inert Gas) (GTAW) - Ideale per saldature di precisione e di alta qualità. Consente un migliore controllo dell'apporto di calore ed è ottimo per le riparazioni di alluminio fuso.
- TIG (Tungsten Inert Gas) - Adatto ai metalli interni, ma molto più lento del MIG. Ideale per le sezioni di alluminio fuso più spesse.
1. Metalli d'apporto: Rafforzare la saldatura
Una saldatura forte e priva di cricche dipende da una buona barra d'apporto.
- 4045 Riempitivo per alluminio - Opzione generica per le riparazioni di alluminio fuso.
- Riempitivo di alluminio 5356 - Fornisce elevata forza e resistenza alla corrosione, ideale per le applicazioni marine.
- Filler di alluminio - 4047 ha un elevato contenuto di silicio per la riduzione delle fessurazioni, il miglioramento del dilavamento e la riduzione dei costi.
2. GAS DI SFIORAMENTO
Come suggerisce il nome, è un gas contenuto nel flusso di saldatura che impedisce l'ossidazione e la porosità. Si tratta in genere di gas inerti scelti per le loro proprietà desiderate.
- La saldatura è protetta dalla contaminazione atmosferica grazie al gas di protezione.
- Argon 100% - per la saldatura TIG e MIG, la scelta migliore per ottenere un arco stabile e un bagno di saldatura pulito.
- Miscela argon-elio - L'elio aumenta l'apporto di calore e la penetrazione e viene quindi utilizzato per tagliare sezioni di alluminio più spesse.
3. Strumenti di pulizia e preparazione
La saldatura non può avere successo finché non c'è una superficie pulita.
- Rimuove l'ossidazione senza contaminare la superficie, spazzola in acciaio inox.
- Se è necessario pulire olio, grasso o sporco prima della saldatura, l'acetone o l'alcool funzionano bene.
- Lo shock termico viene evitato e l'umidità e i gas intrappolati vengono allontanati.
Preparazione dell'alluminio fuso per la saldatura
I difetti devono essere evitati e una saldatura forte deve essere ottenuta con una preparazione adeguata.
Fase 1: pulizia della superficie
Poiché l'alluminio trattiene lo sporco, il grasso, l'ossidazione e l'umidità, non c'è altra scelta che la pulizia.
🔹 Perché la pulizia è importante?
- Previene la porosità e la contaminazione.
- Favorisce una migliore fusione tra metallo d'apporto e materiale di base.
- Contribuisce a mantenere stabile l'arco durante la saldatura.
🔹 Processo di pulizia:
- L'alluminio può essere sgrassato con acetone o alcol per rimuovere olio e contaminanti.
- Rimuovere SEMPRE lo strato di ossido con una spazzola in acciaio inox (dedicata solo all'alluminio).
- È importante evitare di toccare la superficie pulita a mani nude per prevenire la ricontaminazione.
Fase 2: preriscaldamento dell'alluminio
Riduce le tensioni interne e migliora la penetrazione della saldatura.
🔹 Perché il preriscaldamento?
- Riduce al minimo le crepe nell'alluminio fuso poroso.
- Assicura una migliore distribuzione del calore e la qualità della saldatura.
- Aiuta a rimuovere i gas e l'umidità intrappolati.
🔹 Come preriscaldare l'alluminio fuso:
- Rettificare il pezzo a 300°F - 600°F (150°C - 315°C).
- Per monitorare la temperatura si può utilizzare un termometro a infrarossi.
- Può anche essere indebolito dal surriscaldamento, da evitare.
Tecniche di saldatura per l'alluminio fuso
Per saldare con successo l'alluminio fuso, è necessario assicurarsi di utilizzare la tecnica corretta, mantenere un buon controllo del calore e utilizzare i parametri di saldatura adeguati. Di seguito sono riportati i migliori metodi di saldatura per l'alluminio fuso, con i relativi dettagli sulle migliori pratiche.
1. Saldatura TIG (migliore per precisione e resistenza)
Il metodo preferito per la saldatura dell'alluminio fuso è la saldatura a gas inerte di tungsteno (TIG) o la saldatura ad arco di tungsteno a gas (GTAW), perché ha la precisione necessaria per produrre saldature pulite e resistenti.
🔹 Suggerimenti chiave per la saldatura TIG
- Utilizzare la modalità CA: La modalità AC consente di rompere più efficacemente lo strato di ossido di alluminio e di garantire la stabilità dell'arco.
- A 15° è l'angolo migliore per la torcia: Questo garantisce una penetrazione uniforme e l'assenza di contaminazione.
- La lunghezza dell'arco è importante: più l'arco è corto, migliore è il controllo del calore e minore è la probabilità di bruciature e porosità.
- Scegliere la giusta barra d'apporto: il 4047 (ad alto contenuto di silicio) riduce le cricche e il 5356 offre una maggiore resistenza alla corrosione.
- Avvio ad alta frequenza, garantisce un avvio dell'arco regolare senza contaminare l'elettrodo con il tungsteno.
🔹 Ideale per: Pezzi sottili in alluminio fuso, riparazioni di precisione, applicazioni aerospaziali e marine.
2. Saldatura MIG (migliore per velocità ed efficienza)
Un'alternativa più rapida alla saldatura TIG, tranne che per sezioni di alluminio molto spesse, è la saldatura a gas inerte metallico (MIG), nota anche come saldatura ad arco a gas metallico (GMAW). Tuttavia, il controllo della tensione e della velocità del filo durante la saldatura MIG è molto importante per evitare difetti come porosità o bruciature.
🔹 Suggerimenti chiave per la saldatura MIG:
- Utilizzare una tecnica di spinta: Se si tira indietro per avvicinarsi, si contamina completamente la superficie e non è altrettanto pulita.
- In modalità Spray Transfer, gli spruzzi significativi vengono eliminati e l'arco è molto stabile, producendo una saldatura di alta qualità.
- Le impostazioni corrette consentono una buona fusione senza surriscaldamento.
- L'elio aumenta la penetrazione e può essere utilizzato per sezioni più spesse, oppure utilizzare argon puro o una miscela argon-elio.
- Il preriscaldamento del pezzo in lavorazione contribuisce a ridurre lo shock termico e la formazione di cricche.
🔹 Ideale per: Parti in alluminio fuso più spesse, riparazioni automobilistiche, applicazioni industriali.
3. Metodi di saldatura alternativi (in casi particolari)
A volte la saldatura TIG o MIG non è l'approccio migliore a causa della sensibilità al calore, della complessità del pezzo o della necessità di riparazione. In casi particolari, si possono utilizzare i seguenti metodi alternativi.
- La brasatura consiste nell'uso di un metallo d'apporto a bassa temperatura che riduce al minimo il rischio di distorsione o indebolimento dei componenti sensibili al calore.
- Il trasferimento di metallo a freddo (CMT) è a basso calore e lo stress termico è minore, ottimo per le riparazioni delicate.
- Saldatura laser - Può fornire un preciso apporto di calore locale ai componenti in alluminio a parete sottile.
🔹 Ideale per: Applicazioni a basso calore, piccole riparazioni e saldature di alta precisione.
Difetti di saldatura e come risolverli
I componenti in alluminio fuso pongono problemi anche ai saldatori esperti a causa di porosità, cricche e difficoltà di fusione. Questi difetti, e i modi per evitarli e risolverli, sono di vitale importanza se si vogliono ottenere saldature affidabili e durevoli.
1. Porosità (sacche di gas nelle saldature)
Le sacche di gas intrappolate nella saldatura sono considerate porosità, che indeboliscono la struttura. Poiché l'alluminio fuso è naturalmente "poroso", è più soggetto a questo difetto.
🔸 Cause
- O Contaminazione da sporco, olio, grasso o ossidazione.
- Una bassa portata di gas di schermatura o una perdita nel sistema.
- Il raffreddamento è rapido e trattiene il gas nella saldatura.
🔹 Soluzioni
- Prima di saldare, assicurarsi che la superficie dell'alluminio sia pulita e pulirla accuratamente con acetone o alcool.
- Rimuovere l'ossidazione con una spazzola in acciaio inox (dedicata all'alluminio).
- Mantenere la corretta portata del gas (15-25 CFH per l'argon puro).
- Ridurre l'espansione del gas intrappolato e aumentare la penetrazione preriscaldando il pezzo.
- Ridurre i problemi di porosità utilizzando un riempitivo a base di silicone più elevato (ad es. 4047).
Un consiglio da professionista: Mantenere sempre il metallo d'apporto asciutto e privo di umidità, poiché la presenza di umidità nelle barre d'apporto può introdurre porosità nella saldatura.
2. Cricche (saldature deboli e fragili)
Un elevato stress termico o la scelta di un materiale di riempimento sbagliato possono essere una causa comune di cricche. L'alluminio si contrae molto quando si raffredda, provocando l'accumulo di stress e quindi la formazione di cricche.
🔸 Cause
- Provoca crepe da ritiro in presenza di forti sollecitazioni termiche.
- Impiego del metallo d'apporto sbagliato e quindi incompatibilità.
- Il preriscaldamento è insufficiente, con conseguente raffreddamento non uniforme e accumulo di tensioni.
🔹 Soluzioni
- Riscaldare il pezzo a 300°F - 600°F (150°C -315°C) per ridurre al minimo lo shock termico.
- Utilizzare una barra di riempimento ad alto tenore di silicio 4047, che resiste alla fessurazione.
- Assicurarsi che la saldatura si raffreddi lentamente per evitare fratture da stress.
- Le fusioni di alluminio per pezzi di grandi dimensioni possono essere saldate con una tecnica multipass per distribuire il calore in modo uniforme e ridurre le sollecitazioni.
Un consiglio da professionista: Se dopo la saldatura compaiono delle crepe, rimuoverle con una smerigliatrice, pulire l'area e risaldarla con un preriscaldamento adeguato.
3. Mancanza di fusione (legame debole tra metallo e cordone di saldatura)
Si dice che la fusione è assente quando non si è realizzata la fusione tra il cordone di saldatura e il materiale di base, formando un giunto più debole. Spesso la causa di questo difetto è un apporto di calore insufficiente o tecniche di saldatura inadeguate.
🔸 Cause
- Un basso input di riscaldamento limita la possibilità di fondere correttamente.
- Velocità di spostamento elevata e nessuna penetrazione.
- Così si crea la fusione incompleta causata da un'angolazione errata della torcia.
🔹 Soluzioni
- Aumentare le impostazioni di calore per far penetrare correttamente il metallo di base.
- La velocità di spostamento deve essere rallentata per consentire ai nuclei di fondersi più profondamente.
- Mantenere un angolo costante della torcia (10-15 gradi) per una penetrazione uniforme.
- Per una miscela di gas elio-argon e alluminio fuso di elevato spessore, l'apporto di calore aumenterà.
Un consiglio da professionista: Se si riscontra una mancanza di fusione, la saldatura difettosa viene rettificata, la superficie viene pulita e la saldatura viene rifatta con un calore maggiore e una velocità di avanzamento inferiore.
Trattamento e finitura post-saldatura
Una volta completata l'operazione di saldatura, la forza, la durata e la resistenza alla corrosione possono essere garantite solo da un'adeguata finitura e da trattamenti post-saldatura.
Fase 1: Trattamento antistress
- Dopo che la saldatura si è raffreddata lentamente per evitare tensioni residue e cricche.
- Se necessario, si deve ricorrere a un trattamento termico post-saldatura per ripristinare la resistenza meccanica dei componenti critici.
- Non raffreddare la saldatura con acqua o aria compressa, poiché il rapido raffreddamento potrebbe causare nuove cricche.
Un consiglio da professionista: È consigliabile coprire la parte saldata con una coperta termica, in modo che la parte possa raffreddarsi gradualmente e il rischio di cricche da stress sia ridotto.
Fase 2: smerigliatura e lucidatura
- Per eliminare il materiale di saldatura in eccesso e lisciare la superficie, utilizzare un disco a lamelle o una smerigliatrice per stampi.
- Se l'applicazione prevede un'estetica lucida, lucidare l'alluminio con carta vetrata fine (grana 600 - 1200) o con ruote di lucidatura.
- Per finire, se necessario, fondere la saldatura con il metallo circostante.
Un consiglio da professionista: Non utilizzare un utensile di rettifica in acciaio al carbonio sull'alluminio, perché la contaminazione può causare problemi di corrosione.
Fase 3: Protezione dalla corrosione
Sebbene l'alluminio sia naturalmente resistente alla corrosione grazie allo strato di ossido, è possibile garantire un'ulteriore protezione in caso di ambienti difficili per aumentarne la durata.
- Anodizzazione - Si riferisce a una procedura in cui si forma uno strato di ossido protettivo per aumentare la resistenza alla corrosione e migliorare l'aspetto del pezzo.
- Vernice a polvere - Conferisce al pezzo una finitura durevole che protegge dall'usura e dai danni ambientali.
- Vernice o sigillanti - Fornisce una protezione economica per le parti non critiche.
Un consiglio da professionista: Quando si utilizza una vernice, è opportuno utilizzare un primer mordenzante per aumentare l'adesione e la durata.
Applicazioni pratiche della saldatura dell'alluminio fuso

La saldatura dell'alluminio fuso è comunemente utilizzata in molti settori, come le riparazioni automobilistiche, la produzione aerospaziale e altri ancora.
1. Riparazioni automobilistiche
- La capacità della saldatura TIG di individuare e riparare blocchi motore, testate e scatole di trasmissione.
- Riparazione di cerchi in lega e componenti delle sospensioni incrinati.
- Rinforzo delle parti del telaio per alte prestazioni o fuoristrada.
Un consiglio da professionista: I componenti in alluminio saldato sono presenti in molti veicoli da corsa ad alte prestazioni per contenere il peso, pur mantenendo la resistenza.
2. Aerospaziale e aviazione
- Riparazione di componenti della fusoliera dell'aereo e di parti del motore.
- Saldatura del carrello di atterraggio e delle strutture della cellula in alluminio per contenere il peso e mantenere la resistenza.
- Produzione di componenti aerospaziali personalizzati, come serbatoi di carburante, strutture alari e recipienti a pressione.
Un consiglio da professionista: L'A356 e il 7075 sono leghe di alluminio di tipo aerospaziale che si saldano solo se tecniche speciali e un controllo termico rigoroso possono mantenere l'integrità della saldatura.
3. Industria marina
- Riparazione di imbarcazioni in alluminio, eliche e carter di motori marini.
- Saldatura di alluminio marino per la resistenza all'acqua salata.
- Riparazione di strutture offshore e componenti navali normalmente sottoposti ad ambienti difficili.
Un consiglio da professionista: Per tutte le applicazioni marine, il materiale di riempimento deve sempre essere di tipo resistente all'acqua salata, come il 5 356.
4. Industria e costruzioni
- Riparazione di parti di macchinari pesanti e attrezzature di fabbrica.
- Rinforzo di ponteggi, tubazioni e travi di sostegno in alluminio.
- Realizzazione di strutture in alluminio personalizzate per la produzione e l'edilizia.
Un consiglio da professionista: Il preriscaldamento di grandi strutture in alluminio fuso per la saldatura, per evitare cricche e distorsioni, viene generalmente effettuato in ambienti industriali.
Conclusione
La saldatura dell'alluminio fuso è un processo esperto che richiede una miscela perfetta di preparazione, attrezzature e conoscenze di saldatura di prima classe per svolgere bene il compito. Seguendo i corretti metodi di pulizia, preriscaldamento e saldatura si ottengono saldature forti e affidabili. Tuttavia, per trarre vantaggio dalla saldatura dell'alluminio fuso per le riparazioni o la fabbricazione, non è necessario essere coinvolti in industrie aerospaziali, marine o automobilistiche o in applicazioni industriali. Con il tempo e la pratica, la pazienza e l'attenzione ai dettagli, l'alluminio fuso sarà saldato con pochi problemi, con difetti minimi e risultati di qualità professionale. Con la vostra tecnica, occorre investire tempo per creare saldature che durino per tutta la vita del pezzo, in applicazioni ad alta resistenza.
Domande frequenti sulla saldatura dell'alluminio fuso
1. Quali fattori sono considerati più impegnativi nella saldatura dell'alluminio fuso?
La porosità, l'ossidazione e l'elevata conducibilità termica dell'alluminio fuso aumentano le cricche, la porosità e la debolezza delle saldature. Lo strato di ossido che lo ricopre fonde a temperature molto più elevate di quelle a cui fonde l'alluminio stesso e, pertanto, è difficile da fondere.
2. Qual è il tipo di saldatura migliore per una fusione di alluminio?
Saldature precise e pulite sono possibili con il TIG, mentre il MIG è ottimo per i materiali più spessi. Le saldature forti richiedono un preriscaldamento, il giusto riempimento e il gas di protezione.
3. Quali sono i modi per evitare porosità e fessurazioni?
Ridurre lo stress termico pulendo accuratamente la superficie, utilizzando gas argon puro e preriscaldando a 300F - 600F. L'uso di un metallo d'apporto ad alto contenuto di silicio (4047) può favorire la resistenza allo sviluppo di cricche.