La pressofusione ad alta pressione (HPDC) è uno dei processi di fusione dei metalli più utilizzati nella produzione attuale. I produttori scelgono l'HPDC perché consente la produzione di parti metalliche complesse che raggiungono un'elevata precisione e velocità di produzione, un'accuratezza dimensionale superiore e finiture uniformi. L'HPDC consente all'industria automobilistica e aerospaziale, alla produzione di componenti elettronici e di beni di consumo di produrre pezzi leggeri e durevoli per applicazioni come motori e alloggiamenti, elementi strutturali e assemblaggi meccanici. Il processo di produzione della pressofusione ad alta pressione è soggetto a numerosi rischi che creano difetti sostanziali che riducono la qualità del prodotto, la durata di vita e le prestazioni. Diversi difetti si formano a causa di una progettazione impropria dello stampo, di un flusso turbolento di metallo fuso, di gas intrappolati, di velocità di raffreddamento incoerenti e di stress termico durante il processo di produzione. La tecnologia HPDC è soggetta a sette difetti principali, tra cui porosità, chiusura a freddo, difetti di ritiro, formazione di bagliori, difetti superficiali, errori di esecuzione, erosione dello stampo e saldature. Questi tipi di difetti di produzione causano il deterioramento della resistenza del materiale e producono dimensioni irregolari ed effetti visivi indesiderati che possono provocare la rottura dei componenti. I produttori combattono i problemi di produzione ottimizzando i parametri di lavorazione e migliorando i metodi di estrazione, oltre a sistemi di temperatura controllata e procedure di colata sottovuoto. Il monitoraggio in tempo reale e il software di simulazione sono metodi avanzati di controllo della qualità che aumentano l'efficienza e l'affidabilità del processo di pressofusione.
Questo articolo fornisce un'analisi completa dei problemi di produzione standard durante la produzione ad alta pressione. pressofusione con spiegazioni sulle cause principali e strategie di soluzione per ridurre questi difetti. Solo comprendendo queste sfide e applicando le migliori pratiche, i produttori possono migliorare la qualità, la longevità e, naturalmente, le prestazioni dei loro componenti pressofusi, riducendo contemporaneamente gli scarti e i costi di produzione. La conoscenza di questi difetti di produzione aiuterà gli ingegneri di pressofusione, i responsabili di produzione e gli specialisti del controllo qualità a ottimizzare i loro processi per ottenere i migliori risultati di pressofusione.
1. Porosità
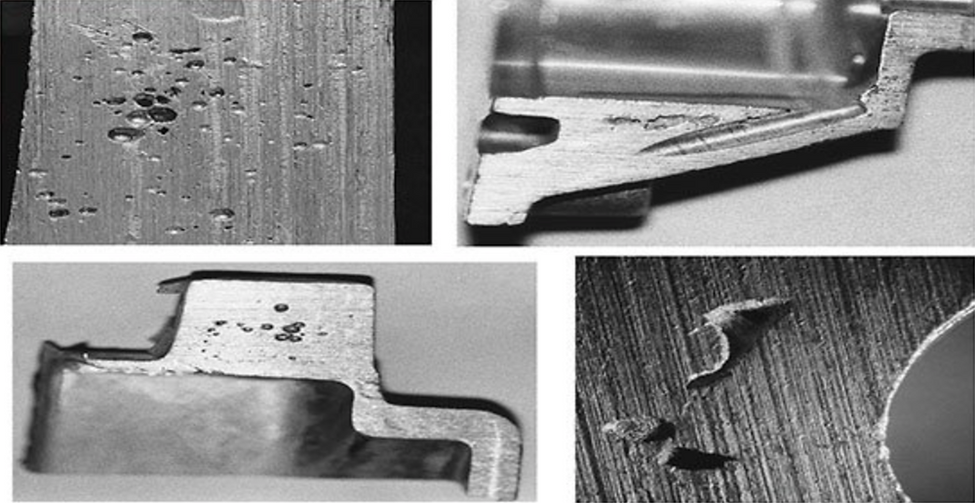
La porosità è definita da piccoli fori o inclusioni di gas che si trovano all'interno della matrice metallica e, di conseguenza, influisce sulle proprietà meccaniche, diminuendo la resistenza, consentendo il passaggio di aria e gas attraverso la struttura e portando a difetti superficiali visibili nei prodotti pressofusi.
Cause:
- Contenuto gassoso presente nei materiali prima della colata.
- Eccessiva turbolenza nel flusso di metallo fuso.
- Scarsa ventilazione e progettazione impropria dello stampo.
- Solidificazione rapida che causa porosità da ritiro.
- Contaminazione del metallo fuso.
- Pressione inadeguata che non provoca un flusso uniforme di metallo.
Prevenzione e soluzioni:
- Assicurarsi che sia stata ottenuta una corretta dispersione del gas attraverso la progettazione di varchi e sfiati.
- Rallentare la velocità di iniezione per migliorare la scorrevolezza del metallo che entra nella cavità.
- Il problema dell'intrappolamento dell'aria dovrebbe essere risolto con la tecnica di pressofusione assistita dal vuoto.
- Assicurarsi che il metallo fuso sia sufficientemente degassato prima di essere iniettato.
- Controllare la velocità di raffreddamento per superare il problema delle cricche e della formazione di altri difetti di solidificazione.
- Controllare e pulire spesso le superfici degli stampi per ridurre le possibilità di porosità dovute a contaminanti.
2. Chiusura a freddo
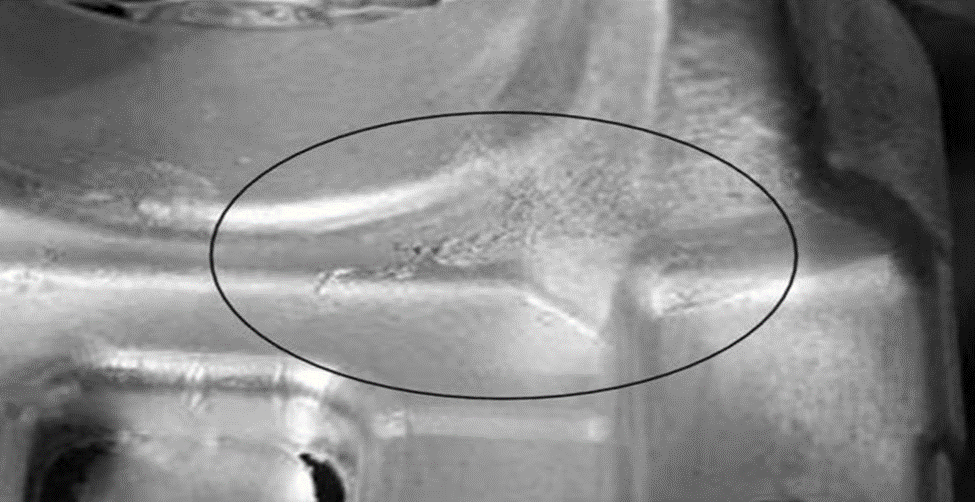
Una chiusura a freddo si crea quando due flussi di metallo fuso non si fondono correttamente e formano aree di legame deboli o cuciture visibili nella fusione. Questo difetto non solo riduce la resistenza meccanica, ma aumenta anche il rischio di frattura e influisce negativamente sulla durata e sull'aspetto del componente.
Cause:
- Bassa temperatura del metallo fuso.
- È contrassegnata da una bassa velocità di iniezione, che generalmente porta a una solidificazione prematura.
- Progettazione inadeguata dello stampo con canali di flusso insufficienti.
- Può causare un'ossidazione eccessiva che forma pellicole superficiali che impediscono la corretta fusione.
- Flusso di metallo incoerente a causa di una progettazione inadeguata del sistema di gating.
Prevenzione e soluzioni:
- Inoltre, è necessario mantenere la temperatura ottimale di colata del metallo per garantire una fluidità adeguata.
- Aumentare la velocità di iniezione per completare il riempimento e renderlo un pezzo unico.
- Eliminare le barriere di flusso non necessarie nella progettazione dello stampo, in modo che il metallo possa muoversi senza difficoltà.
- Individuazione e risoluzione di problemi di flusso prima della produzione mediante l'uso di strumenti di analisi termica.
- È necessario applicare tecniche di sfiato adeguate per evitare l'intrappolamento dell'aria che spesso aggrava i difetti di chiusura a freddo.
3. Difetti di restringimento
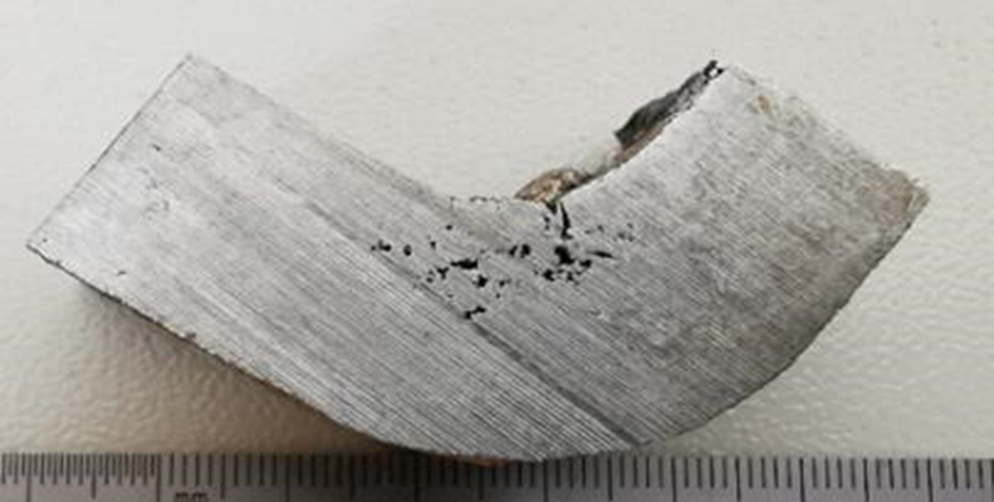
I difetti da ritiro si verificano a causa della contrazione del metallo durante il raffreddamento, che porta alla formazione di vuoti o cavità interne che deteriorano l'integrità strutturale della colata. Di conseguenza, questi difetti riducono la resistenza meccanica del prodotto finale, causano potenziali cedimenti sotto sforzo e provocano una scarsa qualità della superficie, compromettendo la funzionalità e l'estetica dei prodotti finali.
Cause:
- Alimentazione inadeguata del metallo durante la solidificazione
- Le velocità di raffreddamento sono irregolari a causa di una progettazione impropria dello stampo
- Elevato ritiro del metallo dovuto alla composizione della lega
- Il rapido raffreddamento provoca una contrazione localizzata
- Pressione insufficiente durante la fase di solidificazione
Prevenzione e soluzioni:
- Modificare lo stampo per ottenere un raffreddamento uniforme e una corretta alimentazione del metallo fuso.
- Utilizzare leghe con una minore tendenza al ritiro e con migliori proprietà di solidificazione.
- Viene utilizzato per ottimizzare le impostazioni di pressione durante la solidificazione per riempire e minimizzare i vuoti da ritiro.
- Utilizzare metodi di raffreddamento controllati per raggiungere un equilibrio nei tassi di solidificazione e ridurre lo stress termico.
- Implementare strumenti di monitoraggio e simulazione in tempo reale per prevedere e prevenire i difetti di contrazione.
4. Formazione del flash

Gli strati metallici sottili in eccesso che si formano sulla linea di divisione o nella fessura dello stampo a causa della fuoriuscita di metallo ad alta pressione sono chiamati flash. Sebbene l'erosione possa essere eliminata dopo la colata, l'eccesso di fiamma comporta un aumento dello scarto di materiale, dell'usura degli utensili e dei costi di produzione associati, riducendo così l'efficienza complessiva del processo di pressofusione.
Cause:
- L'eccesso di pressione di iniezione fa sì che il metallo fuso venga spinto nelle fessure dello stampo.
- Stampo usurato o dovuto a un blocco improprio dello stampo che consente perdite.
- In presenza di una forza di serraggio insufficiente, che causa la separazione dello stampo durante l'iniezione.
- I pannelli non sono adatti per la fuoriuscita del metallo.
- Controllo del flusso di metallo non chiaro tramite lubrificazione dello stampo
Prevenzione e soluzioni:
- È necessario mantenere una forza di serraggio adeguata per evitare la separazione dello stampo e la formazione di bolle.
- Ispezionare e sostituire regolarmente gli stampi usurati per ottenere una corretta tenuta.
- Assicurare le impostazioni ottimali per la pressione, in modo che il riempimento avvenga con un minimo di bagliori.
- Per evitare lacune involontarie e perdite di metallo, è necessario migliorare il riallineamento degli stampi.
- Eseguire tecniche precise di lubrificazione degli stampi per controllare il flusso di metallo e ridurre l'eccessiva fuoriuscita di metallo.
5. Ispezione dei difetti superficiali (bolle, crepe e rughe)

Una serie di difetti superficiali, bolle, crepe e rughe, degradano l'aspetto visivo e la resistenza meccanica della colata e devono essere prevenuti ed eliminati. I difetti di saldatura riducono la durata del prodotto, aumentano il tasso di scarto e fanno sì che il prodotto non aderisca bene ai trattamenti successivi alla colata, come la verniciatura o il rivestimento.
Cause:
- L'aria intrappolata nella plastica liquida durante il versamento.
- Inoltre, si verificano stress termici e irregolarità superficiali dovute a velocità di raffreddamento non uniformi.
- Surriscaldamento o temperatura non controllata durante la solidificazione.
- O le impurità o le inclusioni metalliche che possono influire sulla superficie di colata.
- La scarsa lubrificazione dello stampo causava un flusso di metallo non uniforme e imperfezioni superficiali.
Prevenzione e soluzioni:
- Degassificazione corretta del metallo fuso per evitare gas intrappolati prima della colata.
- Controllare la solidificazione ed evitare lo stress termico utilizzando tecniche di raffreddamento uniformi.
- Il controllo della temperatura dello stampo deve essere ottimizzato per evitare il surriscaldamento e il raffreddamento non uniforme.
- Creare un controllo rigoroso della sua qualità che permetta di individuare tutte le impurità prima della colata.
- Applicare rivestimenti e lubrificanti per gli stampi in base alla qualità della superficie e alla riduzione dei difetti.
6. Inclusioni e contaminazione
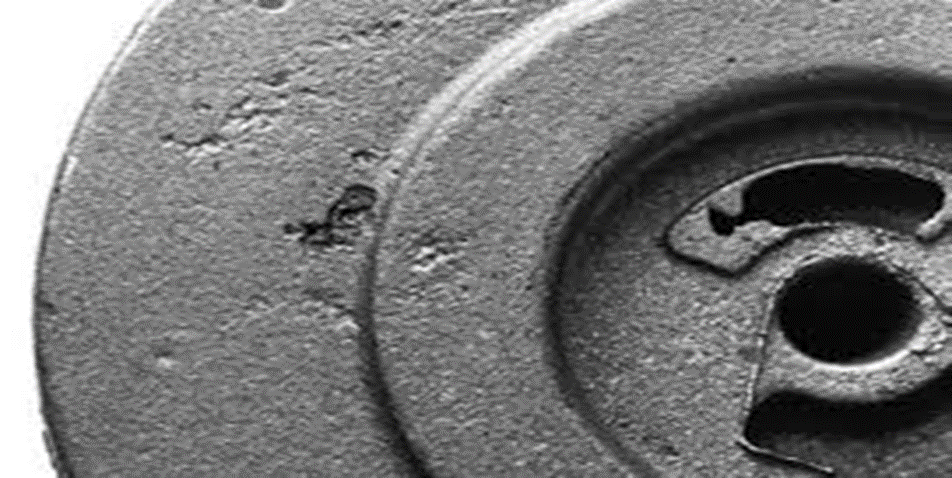
Le particelle estranee indesiderate, come scorie, pellicole di ossido, sporcizia o altre impurità, che rimangono intrappolate nella colata finale, creano proprietà meccaniche scadenti, debole integrità strutturale e difetti superficiali e sono chiamate inclusioni. La presenza di questi contaminanti può ridurre le prestazioni e la durata dei componenti pressofusi, rendendoli inadatti ad applicazioni di alta precisione.
Cause:
- Ad esempio, le materie prime contaminate sono costituite da impurità indesiderate.
- Le particelle estranee in un metallo fuso non possono essere filtrate bene come risultato
- A causa dell'esposizione prolungata all'aria durante la fusione o la colata di metalli
- Include pratiche di manipolazione del metallo inefficienti che a loro volta determinano una maggiore formazione di scorie.
- L'insufficiente lubrificazione dello stampo comporta l'introduzione di un corpo estraneo nel metallo fuso.
Prevenzione e soluzioni:
- Le materie prime di alta qualità devono essere raffinate correttamente e senza contaminanti.
- Predisporre sistemi di filtraggio efficaci per rimuovere scorie, ossidi e altre impurità dal metallo fuso prima dell'iniezione.
- Mantenere una manipolazione controllata del metallo fuso e, ove applicabile, utilizzare una schermatura a gas inerte per limitare l'ossidazione.
- Pulire e mantenere regolarmente le attrezzature di colata per evitare la contaminazione da materiale residuo.
- Utilizzare un'adeguata lubrificazione dello stampo per garantire che non si accumulino materiali estranei nella cavità dello stampo.
7. Errori e riempimenti incompleti
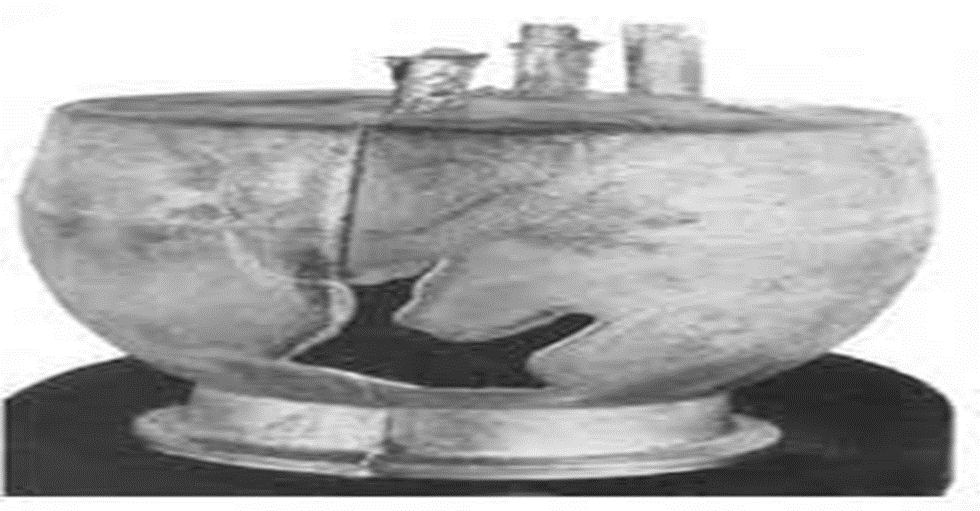
Una corsa errata si verifica quando si verifica un breve riempimento della cavità dello stampo, che causa sezioni mancanti, pareti sottili e punti deboli nel componente finale. Gli effetti negativi sull'integrità strutturale e sulla funzionalità del pezzo sono quindi inadeguati per le applicazioni ad alte prestazioni.
Cause:
- A bassa velocità o pressione di iniezione, non coprendo interamente lo stampo
- Superfici dello stampo fredde che impediscono il flusso di metallo e la solidificazione prematura
- Provoca un volume di metallo fuso inadeguato che porta a un riempimento insufficiente della cavità
- Da una cattiva progettazione dei canali e dei canali, che causano una distribuzione non uniforme del metallo fuso.
- L'eccessiva turbolenza produce sacche d'aria che bloccano il flusso del metallo
Prevenzione e soluzioni:
- Aumentare la temperatura del metallo per renderlo scorrevole ed evitare una solidificazione prematura.
- Inoltre, il riempimento della cavità deve essere ottimizzato impostando correttamente la pressione e la velocità di iniezione.
- Mantenere le corrette temperature di lavoro degli stampi ed evitare che si raffreddino prematuramente.
- Migliorare il design dei canali e delle guide per promuovere una distribuzione uniforme del metallo.
- Simulare il flusso di metallo e il potenziale di errore di produzione con un software di simulazione prima della produzione.
8. Erosione e usura degli stampi
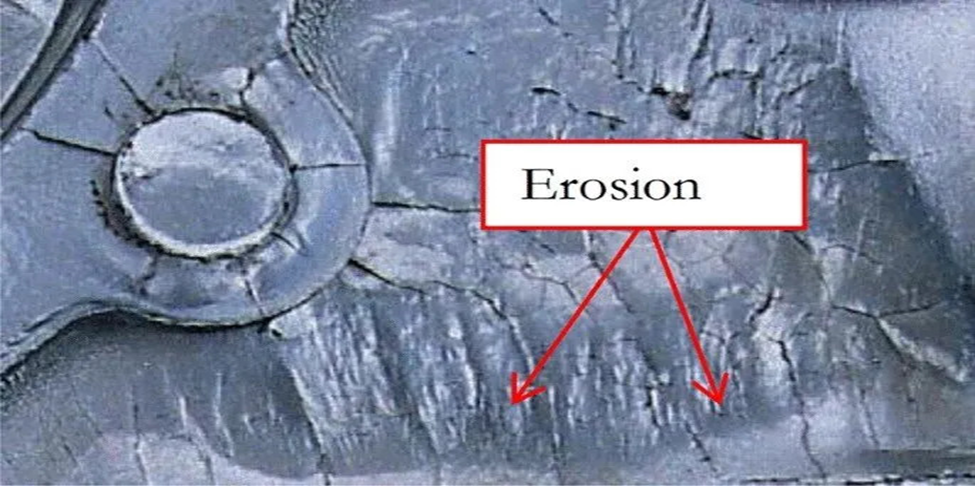
L'usura degli stampi per erosione fusa è la perdita delle superfici dello stampo dovuta alla continua usura del metallo ad alta velocità sulle superfici della parte dello stampo fino al raggiungimento delle dimensioni richieste, con conseguente scarsa finitura superficiale e breve durata dell'utensile dello stampo. Se si verifica questo difetto, è frequente la sostituzione dello stampo e di conseguenza i costi di produzione aumentano, mentre la qualità della colata varia.
Cause:
- Inoltre, l'esposizione ripetuta al metallo fuso ad alta temperatura provoca un'usura graduale.
- Materiali dello stampo di qualità relativamente scadente, con scarsa resistenza alle sollecitazioni termiche e meccaniche
- Cicli termici eccessivi possono causare cricche del materiale dovute alla fatica.
- Con conseguente degrado del materiale dello stampo in presenza di un'iniezione elevata.
- Poca lubrificazione? Ne consegue un maggiore attrito e una maggiore usura.
Prevenzione e soluzioni:
- Uno di questi è l'utilizzo di materiali per stampi di alta qualità resistenti al calore e più duraturi.
- Per prolungare la durata degli stampi si possono applicare rivestimenti superficiali protettivi, come la nitrurazione o i rivestimenti ceramici.
- È necessario implementare metodi di raffreddamento controllati per ridurre lo stress termico e l'usura precoce.
- Per raggiungere un equilibrio tra velocità e pressione con una sollecitazione minima della matrice.
- Ispezionare regolarmente le matrici e sottoporle a manutenzione per individuare e affrontare l'erosione il prima possibile.
9. Criccatura a caldo
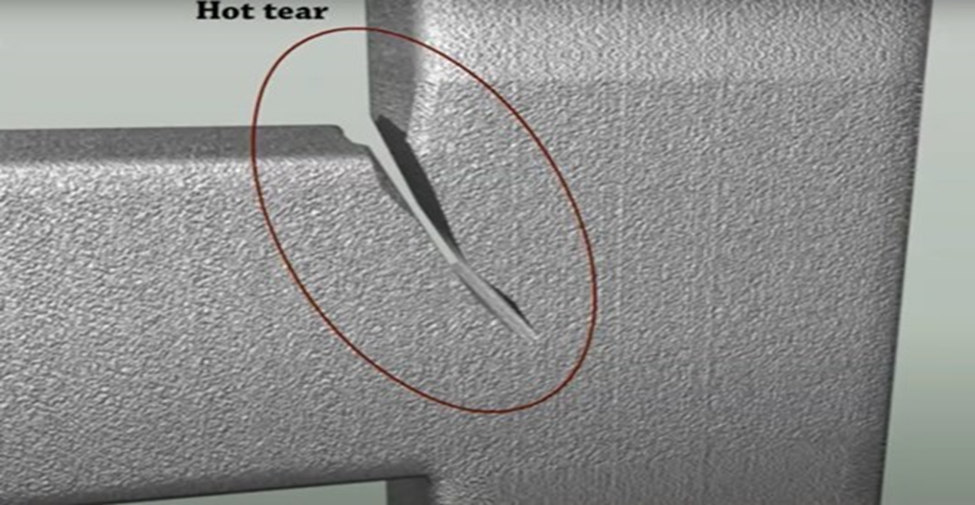
Le cricche che si verificano durante lo stato semisolido del metallo, a causa di elevate sollecitazioni termiche e di un eccessivo ritiro, sono note come cricche a caldo. Queste cricche degradano l'integrità meccanica del getto, ovvero aumentano la possibilità di cedimento del getto nel punto in cui le cricche sono presenti sotto sforzo o carico.
Cause:
- Velocità di raffreddamento inaffidabili nello stampo, con conseguenti punti di stress in aree specifiche
- Presenta un'elevata suscettibilità alle sollecitazioni termiche e alle cricche nella composizione della lega.
- Inoltre, causa un'eccessiva tensione residua formatasi durante la solidificazione rapida, una restrizione alla contrazione del metallo.
- Se la progettazione dello stampo è scadente, si verificheranno variazioni di temperatura in tutto il getto.
- La pressione durante la solidificazione era troppo bassa per impedire la propagazione delle cricche.
Prevenzione e soluzioni:
- Si tratterà anche di ottimizzare le velocità di raffreddamento per ottenere una solidificazione uniforme e ridurre al minimo lo stress termico.
- Aumentare la resistenza alle cricche delle leghe mediante l'uso appropriato di leghe con una migliore struttura dei grani.
- Utilizzo di tecniche di distensione dopo la colata, ovvero trattamento termico controllato.
- Progettare stampi con un minore differenziale di temperatura.
- Assicurare una pressione adeguata durante la solidificazione del metallo, in modo che fluisca e non si verifichino crepe.
10. Saldatura
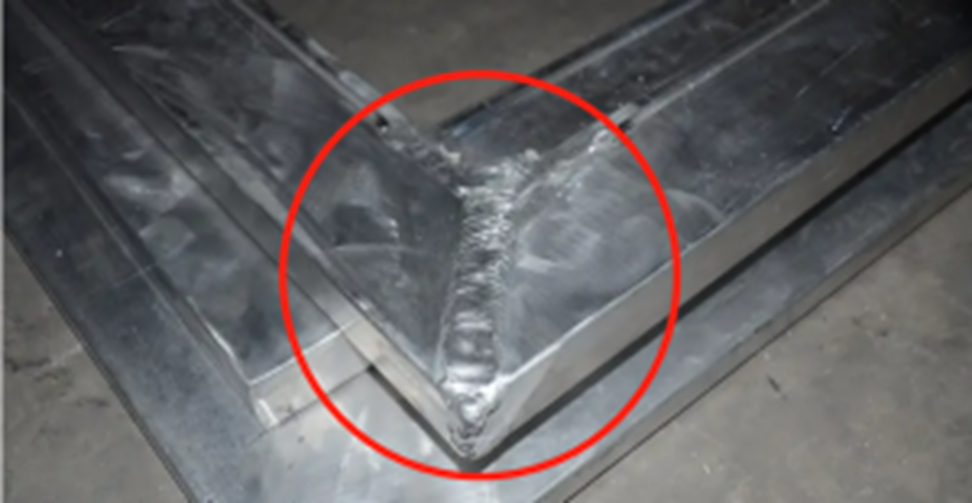
Il metallo fuso aderisce alla superficie dello stampo, che è difficile da rimuovere con la colata, causando difetti superficiali, usura dello stampo e prolungati tempi di fermo della produzione. Anche le imprecisioni dimensionali e la scarsa finitura superficiale sono causate da questo difetto, che si traduce in una qualità complessiva compromessa del prodotto finale.
Cause:
- Aumento dell'adesione dei metalli nella lega a causa dell'elevato contenuto di alluminio.
- Per ottenere temperature di stampaggio eccessivamente elevate, in modo che il metallo si leghi alla superficie dello stampo.
- Protezione insufficiente contro l'incollaggio a causa della scarsa lubrificazione dello stampo
- Un raffreddamento insufficiente fa sì che il metallo fuso rimanga a contatto con lo stampo per troppo tempo - Superfici superiori dello stampo incrinate o danneggiate che favoriscono l'adesione del metallo.
Prevenzione e soluzioni:
- Per evitare che il metallo si attacchi, vengono sempre utilizzati lubrificanti per stampi di alta qualità.
- Consente di controllare la temperatura dello stampo nell'intervallo ottimale se l'adesione a caldo è troppo forte.
- Ridurre l'adesione del metallo mediante l'uso di rivestimenti adatti allo stampo, ad esempio strati di ceramica o nitruro.
- Per ridurre il tempo di contatto metallo-stampo e migliorare l'efficienza del sistema di raffreddamento.
- Ispezionare e lucidare regolarmente le superfici degli stampi per ottenere una finitura superficiale liscia e non adesiva.
Conclusione
L'alta pressione pressofusione è un potente processo di produzione che crea pezzi metallici complessi ad alta precisione e con la massima efficienza. Tuttavia, diversi tipi di difetti si manifestano a causa di parametri di processo non corretti, problemi di materiale e/o difetti di progettazione degli stampi. I produttori possono adottare misure preventive, ad esempio uno stampo di controllo del processo ottimale, un materiale selezionato correttamente e così via, dopo aver compreso questi difetti di produzione abituali.
Un'azienda può migliorare la qualità del prodotto, ridurre i costi di produzione e ottenere una maggiore efficienza produttiva nelle operazioni di pressofusione enfatizzando il miglioramento continuo del processo e le strategie di prevenzione dei difetti.
Domande frequenti (FAQ)
1. Quali sono le principali cause di difetti nella pressofusione ad alta pressione?
Le cause principali dei difetti nella pressofusione ad alta pressione includono una progettazione impropria dello stampo, un flusso di metallo insufficiente, gas intrappolati, elevato stress termico, raffreddamento non uniforme e materie prime contaminate. Questi difetti possono essere ridotti con l'ottimizzazione dei parametri di processo e con l'uso di misure di controllo della qualità.
2. Che ruolo ha la porosità nelle prestazioni dei componenti pressofusi?
La presenza di porosità indebolisce l'integrità strutturale dei componenti pressofusi, riducendo la resistenza e causando perdite d'aria nei componenti a tenuta di pressione e imperfezioni anestetiche. La porosità può essere ridotta al minimo utilizzando un degasaggio adeguato, sistemi di gating ottimizzati e colata sotto vuoto.
3. Come si possono evitare le chiusure a freddo nella pressofusione?
La corretta temperatura di colata del metallo, velocità di iniezione più elevate, progettazione ottimizzata dello stampo per fluidificare il flusso del metallo e l'applicazione di strumenti di analisi termica per identificare eventuali problemi di flusso possono aiutare a prevenire le chiusure a freddo.
4. L'erosione degli stampi è un problema importante nella pressofusione ad alta pressione perché?
L'esposizione ripetuta del metallo fuso ad alta temperatura agli stampi provoca l'erosione degli stampi che ne riduce la durata e la precisione dei pezzi fusi. La durata degli stampi può essere prolungata utilizzando materiali di alta qualità, rivestimenti protettivi e un raffreddamento controllato degli stampi.
5. Cosa rende migliore la qualità e la consistenza dei prodotti pressofusi?
Il controllo della qualità, l'ottimizzazione dei parametri di processo, il controllo della temperatura degli stampi, l'utilizzo di leghe di alta qualità e l'ispezione degli stampi e dei macchinari vengono effettuati periodicamente per migliorare costantemente la qualità dei prodotti pressofusi.