
La colata e la pressofusione sono due importanti processi produttivi, fondamentali per realizzare componenti metallici con la precisione, la durata e l'efficienza desiderate. La colata consiste nel versare il materiale fuso in uno stampo e nel lasciarlo raffreddare e solidificare. La colata in sabbia, la microfusione e la colata in stampo permanente sono alcuni tipi di colata. Tuttavia, la pressofusione è una fusione speciale che utilizza l'alta pressione per iniettare il metallo fuso in una cavità dello stampo con un'elevata precisione e una buona finitura superficiale. Per il settore automobilistico, aerospaziale, elettronico e per le applicazioni industriali correlate che richiedono componenti leggeri, robusti e resistenti alla corrosione, la pressofusione è ampiamente utilizzata. Nel corso del tempo sono state sviluppate diverse varianti di pressofusione per soddisfare le diverse esigenze delle industrie. La pressofusione per gravità (GDC) dipende dalla gravità per riempire lo stampo, mentre la pressofusione a bassa pressione (LPDC) elimina la turbolenza per ottenere una maggiore qualità di integrità del materiale. L'estrema pressione applicata dalla pressofusione crea pezzi ad alta resistenza e privi di porosità, mentre l'aria intrappolata viene eliminata nella pressofusione sotto vuoto per ottenere un componente privo di difetti. Inoltre, la pressofusione semi-solida (Rheocasting) si ottiene utilizzando metallo parzialmente solidificato per migliorare le proprietà meccaniche e la precisione.Il termine generico di fusione nella produzione si riferisce alla forma di modellare il metallo riempiendolo in uno stampo e lasciandolo solidificare. Questo metodo è comunemente utilizzato nella colata in sabbia, nella colata a iniezione e nella colata in stampo permanente. Lo stampo nella pressofusione è lo stampo metallico utilizzato nel processo di colata ad alta pressione, mentre per stampo nel processo di pressofusione si intende lo stampo metallico fissato alla faccia dello stampo. Di solito vengono realizzati stampi in acciaio temprato, progettati per la produzione di massa.
Questo articolo tratterà i concetti di colata e di pressofusione, le differenze tra questi due concetti e i tipi di ciascuno, le possibili applicazioni di questi, nonché i pro e i contro associati a questo processo di fusione.
1. Che cos'è il casting?
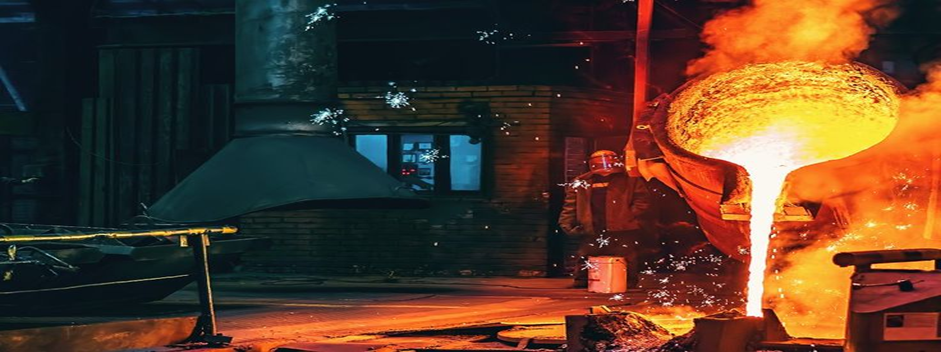
La colata è un processo industriale in cui un materiale liquido viene forzato in uno stampo, dove si solidifica. Il liquido può essere fondamentalmente qualsiasi metallo o plastica o altro materiale fondibile. Dopo l'indurimento, il materiale assume la forma corrispondente alla cavità dello stampo. Negli ultimi millenni, l'utilizzo di questa tecnica ha permesso di creare utensili, armi e sculture complesse.
Il processo di fusione
Diverse di queste fasi giocano un ruolo essenziale nella natura del processo di fusione di un componente in metallo o plastica.
- 1. Viene realizzato un modello del prodotto finale in legno, plastica o metallo. La cavità dello stampo viene determinata per forma e dimensioni sulla base di questo modello.
- 2. Nella preparazione dello stampo, la cavità dello stampo viene progettata in base al modello. Il metodo di colata determina se è fatto di sabbia, metallo o ceramica. I sistemi di sfiato e di chiusura per consentire un flusso regolare del materiale fuso sono incorporati correttamente.
- 3. La fusione della materia prima, solitamente metallo o plastica, avviene ad alta temperatura in un forno. La temperatura specifica del tipo di materiale utilizzato è diversa.
- 4. Il materiale fuso viene versato con cura nella cavità dello stampo nella quantità corretta per evitare difetti, poiché il versamento è uniforme. Si possono utilizzare sistemi di colata manuali o automatizzati.
- 5. Solidificazione - Il materiale si raffredda e si solidifica all'interno dello stampo formando la forma della cavità. È noto che è la velocità di raffreddamento a influenzare le proprietà finali del prodotto fuso.
- 6. Dopo la solidificazione, il getto viene rimosso dallo stampo, il materiale in eccesso, come cancelli, guide o scaglie, viene rifilato e quindi l'assemblaggio viene sottoposto a rimozione e finitura. In seguito possono essere sottoposti a ulteriori processi di finitura, come la rettifica, la lucidatura o il trattamento termico, per migliorare l'aspetto e le proprietà meccaniche del prodotto finale.
Con questo approccio strutturato, la fusione viene eseguita con maggiore affidabilità e qualità.
2. Che cos'è la pressofusione?
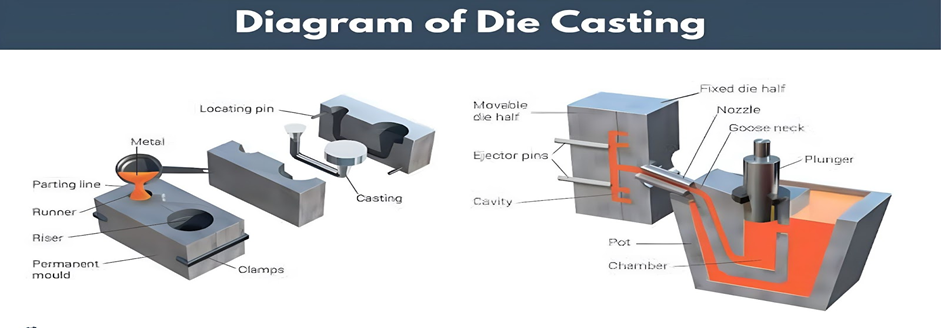
Dies significa stampi, da cui il nome del processo di pressofusione in cui un metallo fuso viene forzato ad alta pressione per riempire una cavità dello stampo. È il processo più adatto per la produzione di pezzi complessi e dimensionalmente precisi in grandi volumi.
Il processo di pressofusione
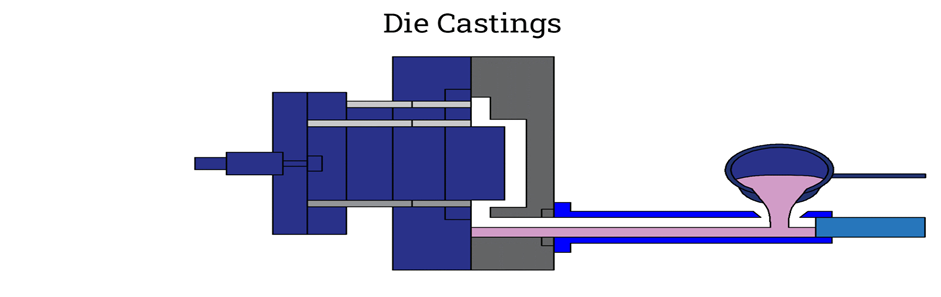
La pressofusione è un processo di produzione in cui i componenti metallici vengono formati nella forma della cavità di uno stampo ad alta pressione, richiedendo un'elevata precisione e accuratezza dimensionale e di finitura superficiale. Questo processo è seguito dalle fasi di seguito descritte:
- 1. Iniezione di metallo fuso - L'alta pressione, compresa tra 1.500 e 25.000 psi, viene applicata per iniettare metallo fuso (come alluminio, zinco o magnesio) in uno stampo in acciaio (matrice), che fonde il metallo selezionato in un forno. In questo modo il metallo fuso riempie ogni dettaglio dello stampo.
- 2. Stampo o matrice - Il metallo fuso si raffredda e si solidifica all'interno della matrice, dando vita a un pezzo forte e preciso. Le proprietà meccaniche del prodotto finale dipendono dalla velocità di raffreddamento.
- 3. Espulsione e rifilatura - Una volta solidificato, il pezzo fuso viene espulso dallo stampo mediante perni di espulsione. Il materiale in eccesso, comprese le scorie, le guide e le porte, viene rifilato per ottenere la forma desiderata.
- 4. Finitura superficiale - A seconda dell'applicazione, può essere necessario rifinire ulteriormente la fusione con molatura, lucidatura, verniciatura, anodizzazione o rivestimento in polvere per aumentarne l'aspetto, la durata e la resistenza alla corrosione.
Con questo processo si ottengono pezzi complessi ad alta resistenza e peso ridotto, con poche lavorazioni successive. I materiali più comunemente utilizzati per la pressofusione sono i metalli non ferrosi, come l'alluminio, lo zinco e il magnesio.
Tipi di processi di fusione
Esistono vari tipi di colata a seconda del tipo di metodo utilizzato
1 Colata in sabbia

- Si tratta di uno dei metodi di fusione più versatili ed economici che utilizzano stampi in sabbia.
- Comune nelle industrie automobilistiche, aerospaziali e artistiche.
2 Colata a iniezione
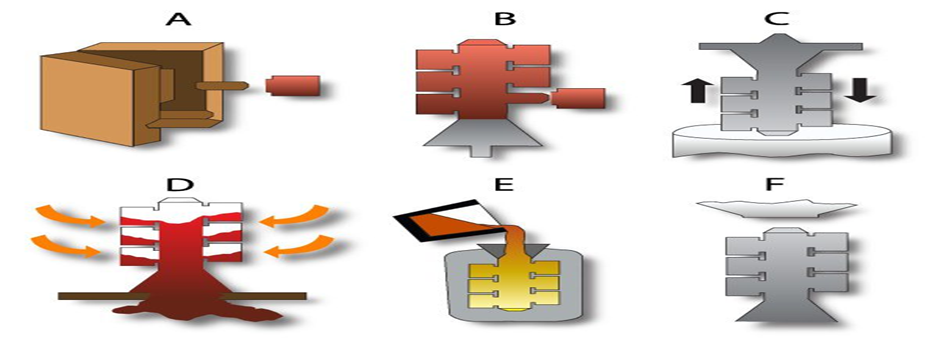
- Conosciuta anche come fusione a cera persa, permette di realizzare pezzi molto dettagliati e complessi.
- Per l'impiego in gioielleria, impianti medici e componenti aerospaziali.
3 Colata centrifuga

- Si tratta di ruotare uno stampo per integrare completamente il metallo fuso.
- Utilizzato comunemente per la produzione di tubi, cilindri e anelli.
4 Colata di stampi permanenti
- Riduce gli sprechi e l'uso di stampi grazie al riutilizzo.
- È ideale per la produzione ripetuta di pezzi metallici di alta qualità.
Tipi di pressofusione
Le modalità di pressofusione sono principalmente due:
1. Pressofusione a camera calda
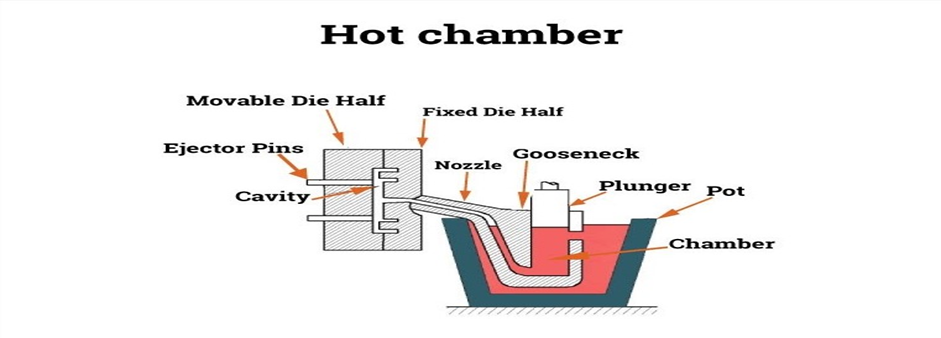
- Utilizzato per metalli a basso punto di fusione come zinco e magnesio.
- Processo più rapido con tassi di produzione più elevati.
2. Pressofusione a camera fredda

- Si utilizza per i metalli ad alto punto di fusione come l'alluminio e l'ottone.
- Rallenta le fasi di fusione e iniezione, oltre ad essere adatto per pezzi durevoli.
5. Differenze tra colata e pressofusione
Caratteristica | Colata | Pressofusione |
processo | Stampo Versare il metallo al suo interno | Il metallo fuso è iniettato ad alta pressione |
I materiali | Vari metalli e plastiche | Principalmente metalli non ferrosi come alluminio e zinco |
Precisione | Moderato | Alta precisione |
costo | Costo iniziale contenuto | Elevati costi iniziali di attrezzaggio |
Applicazioni | Parti grandi e semplici | Pezzi piccoli, complessi e ad alto volume |
Applicazioni della colata e della pressofusione

La colata e la pressofusione, a loro modo, hanno un ruolo immenso in diversi settori industriali e sono economicamente vantaggiose in quanto facilitano la produzione di componenti metallici complessi con una precisione eccellente.
- Nell'industria automobilistica si producono blocchi motore, carter della trasmissione, mozzi delle ruote, parti dei freni e delle sospensioni. Per quanto riguarda le parti leggere in alluminio, la pressofusione è particolarmente favorita a questo scopo, in quanto soddisfa livelli più elevati di efficienza del carburante.
- Aerospaziale: I componenti aerospaziali, come le pale delle turbine, i componenti strutturali della cellula, gli alloggiamenti e i componenti dei carrelli di atterraggio, vengono fusi per essere durevoli e resistenti, ma allo stesso tempo leggeri.
- Nel settore dell'elettronica, la fusione e la pressofusione sono essenziali in quanto gli involucri e i componenti di pressofusione, come dissipatori di calore, connettori e dispositivi di schermatura, sono necessari per espellere il calore e garantire la sicurezza dei fragili circuiti elettronici.
- Edilizia - Tubi, raccordi, staffe, valvole e parapetti per la costruzione di edifici, ponti, ecc. che garantiscono stabilità strutturale e durata nel tempo.
- Apparecchiature mediche - I componenti fusi di precisione trovano ampio impiego in campo medico per strumenti chirurgici, alloggiamenti di apparecchiature di imaging, impianti ortopedici, ecc.
- Macchinari industriali - La fusione è necessaria per garantire la forza e la resistenza all'usura di riduttori, pompe e altre parti di macchine per impieghi gravosi che lavorano in condizioni difficili.
L'applicazione della colata e della pressofusione è molto diffusa e quindi sono componenti indispensabili delle moderne industrie manifatturiere.
Varianti della pressofusione
Uno dei processi produttivi più diffusi è la pressofusione, in cui il metallo fuso entra nello stampo per realizzare componenti con caratteristiche complesse e prescritte. Nel corso del tempo sono state sviluppate diverse varianti di pressofusione per adattarsi ai materiali, ai requisiti di produzione e agli standard di qualità. Ogni metodo ha i suoi vantaggi e sarà più o meno adatto a diversi tipi di applicazioni. Di seguito sono riportate le principali varianti della pressofusione con i rispettivi processi e vantaggi.
Pressofusione a gravità (GDC)
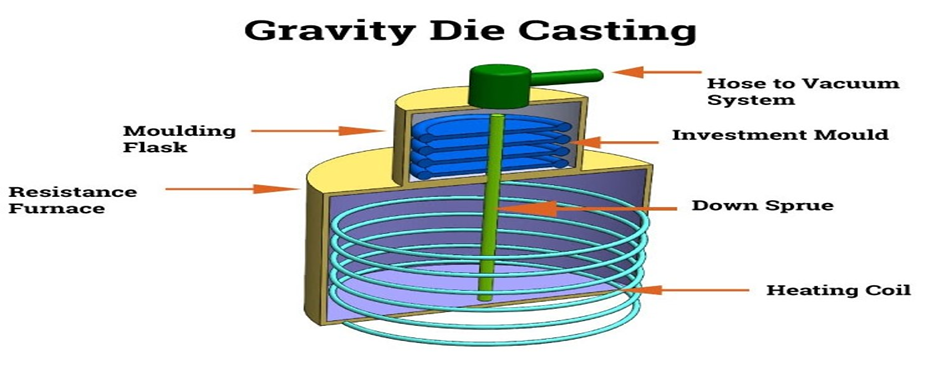
Panoramica
La pressofusione per gravità (GDC) consiste nel versare il metallo fuso in uno stampo senza l'uso di una pressione elevata. Piuttosto, la gravità aiuta il metallo a riempire la cavità e ad organizzarsi, come se fosse da solo. Questo processo è preferito per le leghe con punti di fusione più bassi ed è comunemente utilizzato quando si desidera un processo di solidificazione più controllato.
Caratteristiche principali
- È più efficiente della colata in sabbia, poiché utilizza stampi riutilizzabili.
- È più lenta della pressofusione, ma il pezzo è più resistente grazie alla densità della moda.
- Limitato a leghe specifiche, come alluminio e magnesio.
Applicazioni comuni
- Componenti per automobili (teste dei cilindri, parti del motore).
- Raccordi e corpi valvola.
- Macchinari industriali e parti strutturali.
Pressofusione a bassa pressione (LPDC)

Panoramica
La pressofusione a bassa pressione (LPDC) avviene quando il metallo fuso viene pressurizzato nello stampo a bassa pressione, nell'ordine di 0,1-1 MPa. Con questo riempimento controllato, la turbolenza è ridotta al minimo e il flusso è reso più fluido, riducendo al minimo i difetti come le sacche d'aria e le inclusioni.
Caratteristiche principali
- Migliore integrità del materiale grazie alla riduzione delle turbolenze.
- L'opzione è adatta per pezzi grandi e complessi che richiedono un'elevata resistenza strutturale.
- È affidabile (qualità costante) nel caso della produzione di massa.
Applicazioni comuni
- Ruote in alluminio per automobili.
- Parti strutturali di aeromobili.
- Componenti resistenti al calore nei macchinari industriali.
Pressofusione a pressione

Panoramica
Nel processo di fusione Squeezedie, al metallo fuso all'interno della cavità dello stampo viene imposta un'elevata pressione. Poiché la forza applicata supera i 20.000 psi (libbre per pollice quadrato), il metallo riempie anche i dettagli più sottili dello stampo ed elimina le porosità.
Caratteristiche principali
- Crea parti estremamente dense e resistenti.
- Riduce la porosità e fornisce migliori proprietà meccaniche.
- Applicabile alle applicazioni ad alta resistenza in cui è importante la durata.
Applicazioni comuni
- Componenti per sospensioni di automobili.
- Componenti aerospaziali ad alte prestazioni.
- Strumenti e attrezzature industriali per impieghi gravosi.
Pressofusione sotto vuoto

Panoramica
La pressofusione sottovuoto utilizza il suo design per evacuare l'aria e i gas intrappolati dalla cavità dello stampo prima e durante il processo di colata. Questo metodo viene attuato creando il vuoto e consente di ridurre in modo significativo la porosità, che è un difetto comune nella pressofusione standard. Il risultato è una colata più precisa, più forte e priva di difetti.
Caratteristiche principali
- Migliora le proprietà meccaniche del prodotto finale.
- Riduce al minimo l'intrappolamento dell'aria, rendendolo appropriato per i pezzi a parete continua e ad alta precisione.
- Migliora la qualità complessiva del getto, riducendo la post-elaborazione.
Applicazioni comuni
- Saldatura delle parti strutturali del settore automobilistico per garantire la resistenza alla leggerezza.
- Componenti di apparecchiature mediche ad alta precisione.
- L'integrità delle parti aerospaziali.
Pressofusione semisolida (Rheocasting)

Panoramica
La reofusione o pressofusione semisolida utilizza un metallo parzialmente solidificato anziché completamente liquido. In questo modo il metallo viene mantenuto in uno stato semi-liquido o di slurry, in modo da scorrere agevolmente nello stampo e ridurre le turbolenze e la porosità.
Caratteristiche principali
- Produce componenti con proprietà meccaniche superiori.
- Riduce i difetti di ritiro e la porosità.
- Ideale per pezzi complessi e di alta precisione.
Applicazioni comuni
- Qualsiasi componente automobilistico che richieda elevate proprietà di resistenza e leggerezza.
- Involucri elettronici con dettagli raffinati.
- Per macchinari industriali con componenti che devono resistere all'usura.
Metalli comuni utilizzati nella pressofusione
Il processo di produzione utilizzato per iniettare metallo fuso in uno stampo ad alta pressione è la pressofusione. Il metallo scelto in questo processo è essenziale per la resistenza, la durata e l'applicazione del prodotto finale. Per questo tipo di colata si possono utilizzare diversi metalli, ma i metalli non ferrosi (o privi di ferro) sono i più utilizzati in quanto hanno punti di fusione più bassi e sono più colabili.
I metalli più utilizzati nella pressofusione, con le loro proprietà e i loro impieghi, sono citati di seguito.
1. Alluminio
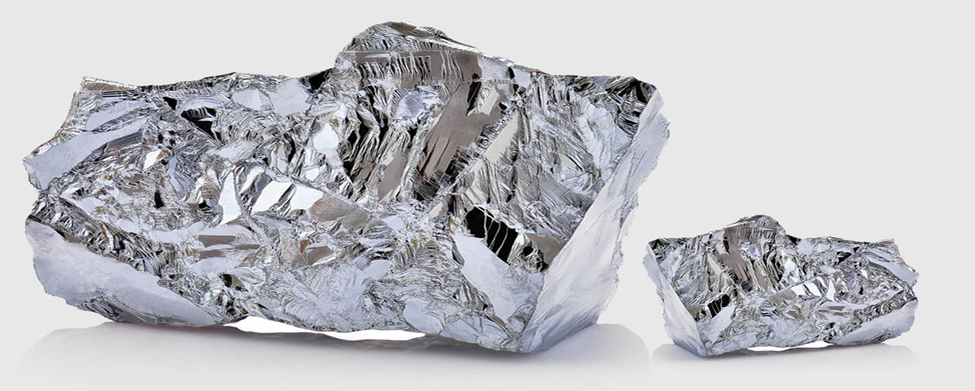
Tra i metalli utilizzati in pressofusione, Tuttavia, l'alluminio è il più utilizzato e presenta la combinazione ideale di buona resistenza, peso ridotto e resistenza alla corrosione. Con una densità relativamente bassa, è un buon candidato per essere utilizzato in settori in cui sono necessari componenti a bassa densità e alta resistenza.
Vantaggi dell'alluminio nella pressofusione
- È leggero e resistente, in quanto viene utilizzato nell'industria automobilistica e aerospaziale per ridurre il peso.
- Resistente alla corrosione - Adatto per applicazioni esterne e marine.
- Buona conducibilità termica ed elettrica - Utilizzato in alloggiamenti elettronici e dissipatori di calore.
Applicazioni comuni delle pressofusioni di alluminio
- Blocchi motore, scatole di trasmissione, ruote, ecc. (parti di automobili).
- Componenti aerospaziali (telai di aerei, staffe).
- Elettronica di consumo (scocche di smartphone, involucri di laptop).
L'alluminio viene di norma pressofuso con la pressofusione a camera fredda a causa del suo elevato punto di fusione.
2. Zinco
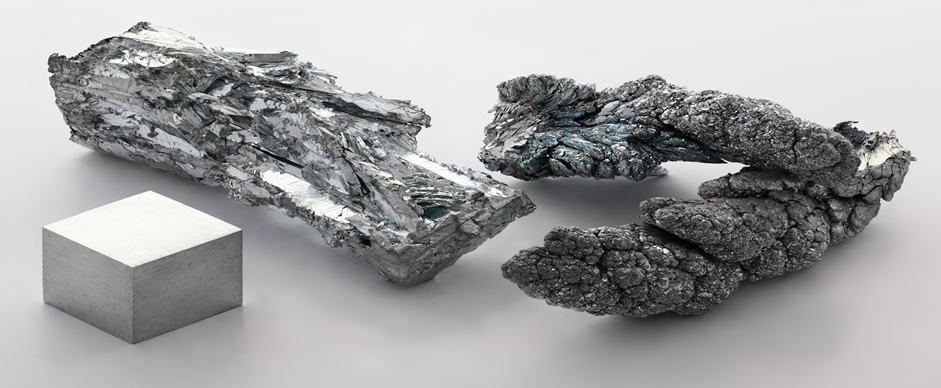
Un altro metallo popolare per la pressofusione è lo zinco, noto per la sua elevata precisione, resistenza e facilità di fusione. Tuttavia, il punto di fusione più basso dello zinco rispetto all'alluminio lo rende adatto alla pressofusione a camera calda e produce cicli di produzione più rapidi.
Vantaggi dello zinco nella pressofusione
- Elevata resistenza e durata - Ideale per i componenti meccanici.
- Basso punto di fusione - Consente una produzione più rapida e una maggiore durata dello stampo.
- Buona finitura superficiale - Riduce la necessità di un'estesa post-elaborazione.
Applicazioni comuni delle pressofusioni di zinco
- Piccoli componenti meccanici (ingranaggi, elementi di fissaggio, cerniere).
- Connettori elettrici ed elettronici.
- Include componenti aggiuntivi come parti di ricambio per autoveicoli (staffe, maniglie, serrature).
Inoltre, lo zinco è più economico dell'alluminio e quindi è il materiale preferito per la produzione di piccoli pezzi.
3. Il magnesio
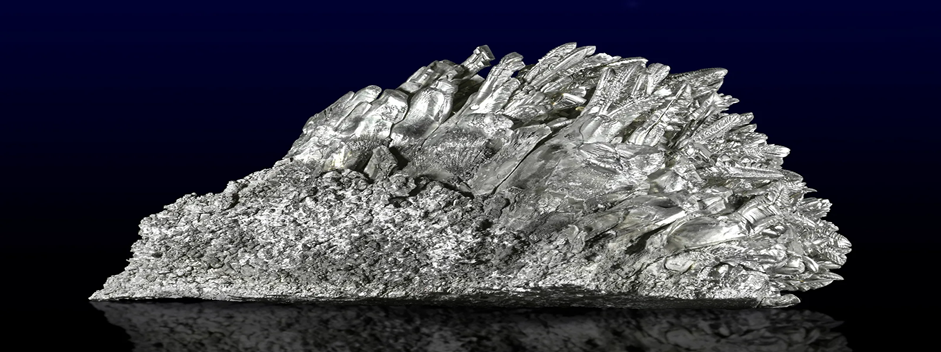
Come metallo strutturale per la pressofusione, il magnesio è il più leggero tra quelli utilizzati e offre un eccezionale rapporto resistenza/peso. Pesa circa 30% in meno rispetto all'alluminio, il che lo rende una buona opzione per le applicazioni che richiedono una riduzione del peso.
Vantaggi del magnesio nella pressofusione
- Estremamente leggero - Ideale per applicazioni aerospaziali e automobilistiche.
- Buona forza e resistenza agli urti - Può sopportare sollecitazioni meccaniche.
- È molto facile da lavorare (lavorabilità) rispetto ad altri metalli.
Applicazioni comuni delle pressofusioni di magnesio
- Viene utilizzato nell'industria automobilistica (volanti, cornici del cruscotto).
- Industria aerospaziale (parti di droni e aerei).
- Elettronica di consumo (laptop e corpi macchina).
Sebbene la polvere di magnesio sia altamente infiammabile, i pezzi pressofusi sono sufficientemente stabili e sicuri per l'uso industriale.
4. Rame e leghe di rame (ottone e bronzo)

Il rame e le sue leghe (ottone, bronzo) sono utilizzati per applicazioni elettriche e idrauliche. Pur avendo un prezzo più elevato e un peso maggiore rispetto allo zinco e all'alluminio, hanno una maggiore resistenza alla corrosione e all'usura.
Vantaggi del rame e delle sue leghe nella pressofusione
- Eccellente conduttività elettrica - Utilizzato nei componenti elettronici ed elettrici.
- È resistente alla corrosione e ben si adatta alle applicazioni idrauliche e marine.
- Resistenza all'usura superiore - Assicura una maggiore durata dei componenti.
Applicazioni comuni delle pressofusioni in rame e in lega di rame
- Connettori e terminali elettrici.
- Raccordi e valvole idrauliche.
- Componenti per macchinari industriali.
Anche se il rame non viene solitamente utilizzato come l'alluminio o lo zinco nella pressofusione, è comunque fondamentale in queste applicazioni specializzate in cui sono necessarie un'elevata durata e conduttività.
5. Anche piombo e stagno (oggi non troppo comuni).

Per applicazioni specializzate, la pressofusione di piombo e stagno era un tempo molto diffusa grazie ai loro bassi punti di fusione e all'eccellente resistenza alla corrosione. Tuttavia, negli ultimi anni il loro utilizzo è diminuito drasticamente per motivi sanitari e ambientali.
Vantaggi del piombo e dello stagno nella pressofusione (storicamente)
- La resistenza alla corrosione è buona - Viene utilizzato nei componenti idraulici e nelle batterie.
- Morbido e malleabile - Adatto per applicazioni a bassa sollecitazione.
- Hanno un'elevata densità; per questo motivo sono utilizzati nelle applicazioni di schermatura delle radiazioni e di insonorizzazione.
Applicazioni comuni delle fusioni in piombo e stagno (ora limitate)
- Terminali della batteria.
- Cuscinetti e parti di saldatura morbida.
- Componenti di schermatura nella radioprotezione.
Con l'aumento delle normative ambientali, è diventato necessario per i produttori trovare materiali più sicuri come l'alluminio, lo zinco e il magnesio.
Vantaggi e svantaggi
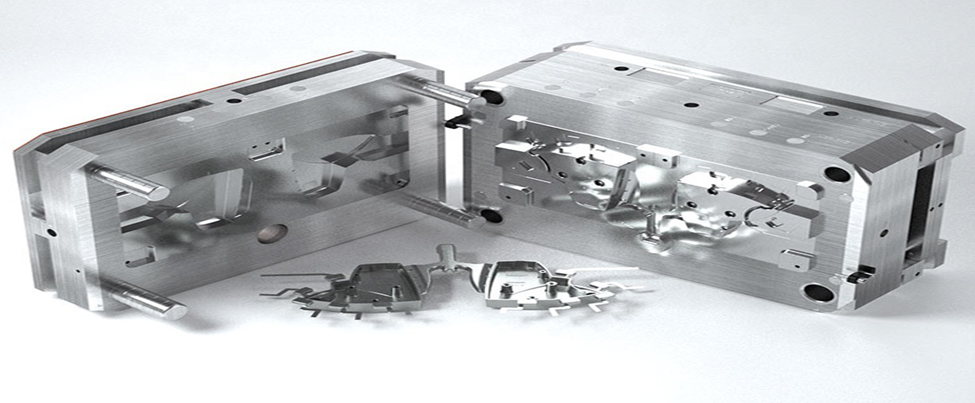
Vantaggi della fusione
- Basso prezzo di produzione - La colata è un metodo di produzione efficiente dal punto di vista dei costi, in particolare per le piccole serie, perché richiede pochi strumenti (utensili e stampi) rispetto ad altri processi di produzione.
- Può realizzare forme grandi o complesse - La fusione può creare forme difficili da gestire al tornio o con la lavorazione, o troppo grandi per essere gestite.
- Fusione di un'ampia varietà di materiali - con ferro, acciaio, alluminio, bronzo, ecc.
- Uso efficiente del materiale - La fusione non comporta sprechi di materiale perché il metallo fuso viene versato direttamente negli stampi e non perde molto materiale in eccesso.
- Adatta alla produzione di massa - Una volta creato lo stampo, è possibile produrre molti pezzi uguali con relativa facilità.
Svantaggi della fusione
- Meno preciso della pressofusione. I metodi di fusione tradizionali tendono a produrre imperfezioni superficiali e variazioni dimensionali che devono essere lavorate.
- I tempi di raffreddamento più lunghi e il processo di raffreddamento e solidificazione possono influire sull'efficienza produttiva complessiva.
- È necessario un maggior lavoro di finitura - I pezzi fusi presentano una superficie ruvida o un eccesso di materiale (flash) che deve essere rimosso attraverso lavorazioni come la rettifica e la lucidatura.
- Problemi di porosità - Potrebbe trattarsi di sacche d'aria o vuoti che si formano durante il processo di fusione e che creano debolezze nell'integrità strutturale.
- Degrado degli stampi - L'utilizzo di stampi riutilizzabili comporta, nel tempo, il degrado degli stampi e l'aumento dello spessore delle pareti dei pezzi, con conseguenti difetti di produzione e maggiori costi di manutenzione.
Vantaggi della pressofusione
- La pressofusione offre sia produzioni ad alta velocità, adatte a volumi elevati, sia lotti a bassa produzione.
- Crea pezzi robusti e di dimensioni precise - Grazie al processo di iniezione ad alta pressione, i pezzi escono in modo costante, con tolleranze strette e una buona qualità che riduce al minimo ulteriori aggiustamenti.
- Non richiede grandi lavorazioni successive - I pezzi pressofusi hanno solitamente superfici lisce e dettagli puliti che non richiedono lavorazioni secondarie.
- La pressofusione ha un'eccellente ripetibilità, che consente l'uniformità della produzione in numerosi cicli produttivi, motivo per cui è il metodo preferito per la produzione di massa.
- Buona finitura superficiale - Non richiede alcuna finitura, il che lo rende molto adatto alla realizzazione di prodotti che tengono conto dell'estetica.
Svantaggi della pressofusione
- Costo iniziale più elevato (gli stampi sono costosi) - La progettazione e la produzione di stampi per la pressofusione possono essere costose e quindi non convenienti se la produzione è di piccola scala.
- Non è adatto ai metalli ferrosi - La pressofusione è limitata all'alluminio, allo zinco e al magnesio, il che limita la gamma di materiali possibili.
- Non è adatto per pezzi grandi o spessi - I componenti a parete sottile sono più adatti alla pressofusione rispetto a quelli a parete massiccia o spessa. La pressofusione comporta un processo di raffreddamento rapido.
- Porosità - È possibile che il prodotto si sia riempito d'aria durante il processo di stampaggio a iniezione e che questo determini una porosità che rende il prodotto finale debole.
- Minore flessibilità nelle modifiche alla progettazione - Dopo la realizzazione dello stampo, le modifiche alla progettazione dei getti sono costose e richiedono tempo rispetto ad altri metodi di fusione.
8. Il futuro della colata e della pressofusione
La colata e la pressofusione sono promettenti per il futuro (almeno a breve) grazie all'automazione e alla stampa 3D. Alcune tendenze chiave includono:
- Materiali eco-compatibili - Leghe sostenibili e riciclabili.
- Smart Manufacturing - Automazione guidata dall'intelligenza artificiale per l'efficienza.
- Integrazione della produzione additiva sotto forma di processi ibridi di fusione e stampa 3D.
Nelle industrie moderne, queste innovazioni miglioreranno la produttività, ridurranno gli sprechi e gli oneri di produzione, rendendo i processi produttivi ancora più indispensabili.
Conclusione
In diversi settori industriali, il processo di produzione di componenti metallici di alta qualità continua a essere uno dei processi principali della produzione. Le opzioni di pressofusione presentano numerose varianti, ognuna delle quali offre vantaggi diversi per applicazioni specifiche. I pezzi forti e densi sono prodotti dalla pressofusione a gravità; quelli strutturalmente solidi e con difetti minimi dalla pressofusione a bassa pressione. La pressofusione a compressione ha un'ottima resistenza e durata, mentre la pressofusione sottovuoto risparmia sulla porosità. Tuttavia, la pressofusione semi-solida presenta vantaggi in termini di proprietà meccaniche e precisione per applicazioni ad alte prestazioni e la scelta del metodo di pressofusione dipende dalla selezione dei materiali, dalla complessità del pezzo, dal volume del pezzo e dal tipo di proprietà meccaniche desiderate. Il processo continua a essere perfezionato in termini di nuovi sviluppi nell'automazione, nello sviluppo di leghe e nell'ingegneria di precisione, rendendo il suo utilizzo sempre più efficiente, meno costoso e rispettoso dell'ambiente.
A causa della richiesta di componenti più leggeri, più resistenti e più durevoli da parte delle industrie, la tecnologia si evolverà continuamente. Tuttavia, i produttori possono evitare prestazioni scadenti, sprechi e inefficienze produttive scegliendo il metodo di pressofusione più adatto. Per scegliere la migliore opzione di produzione è necessario comprendere le varianti di pressofusione e ottenere la massima qualità, affidabilità ed efficienza nella produzione.
Domande frequenti (FAQ)
1. Come funziona la pressofusione e in quale forma?
La fusione di metalli mediante il processo noto come pressofusione è un processo in cui il metallo fuso viene iniettato in uno stampo ad alta pressione. Ciò consente ai produttori di produrre parti metalliche complesse e di alta precisione con una finitura superficiale eccellente e una lavorazione molto ridotta.
2. Quanti sono i tipi di pressofusione?
Le principali forme di pressofusione sono la pressofusione a gravità (GDC), la pressofusione a bassa pressione (LPDC), la pressofusione a compressione, la pressofusione sotto vuoto e la pressofusione semi-solida. I vantaggi e gli svantaggi di ciascun metodo dipendono dal materiale e dall'applicazione.
3. Quali metalli vengono normalmente utilizzati nel processo di pressofusione?
Alluminio, zinco, magnesio, rame e le loro leghe sono i metalli più comunemente utilizzati nella pressofusione. Il metallo viene scelto per il peso, la forza, la resistenza alla corrosione e la conducibilità termica.
4. Perché la pressofusione è così vantaggiosa?
Elevata efficienza produttiva, eccellente precisione dimensionale, minimo spreco di materiale, finitura superficiale liscia e possibilità di produrre forme complesse con poche lavorazioni successive.