
ZAMAK est le nom donné à un alliage à base de zinc utilisé avec l'aluminium, le cuivre (Kupfer) et le magnésium. Le ZAMAK a été nommé en allemand à partir de ces mots. Cet alliage contient généralement du zinc 94% à 96%, les autres matériaux étant ajoutés à la feuille ou au film. Plusieurs qualités remarquables font que les alliages ZAMAK conviennent bien aux applications de moulage sous pression. Le fait que ces alliages aient un point de fusion bas, une grande fluidité et une résistance élevée par rapport au poids les rend extraordinairement utiles pour fabriquer des pièces dures, résistantes et précises. En plus de ces caractéristiques clés, les alliages ZAMAK offrent d'autres caractéristiques qui les qualifient pour plusieurs applications industrielles.
Le moulage sous pression du zamak s'est imposé dans le monde du moulage des métaux comme une méthode de moulage très rentable et confortable. Le zamak est une famille d'alliages de zinc largement utilisée pour fabriquer des pièces complexes de haute qualité dans de nombreuses industries. Le processus consiste à injecter de l'alliage de zamak en fusion dans un moule ou une matrice métallique sous haute pression. Ce procédé permet de fabriquer des pièces complexes avec des tolérances très étroites et de très bons états de surface, ce qui le rend adapté à la fabrication de pièces de précision. Le rôle du moulage sous pression en zamak est d'autant plus important que les industries évoluent avec le besoin croissant de matériaux durables, légers et résistants. Dans cet article, nous analysons l'importance du moulage sous pression Zamak et les raisons pour lesquelles une personne devrait préférer le moulage sous pression Zamak à d'autres méthodes de moulage.
Les alliages ZAMAK sont utilisés dans les fonderies de moulage sous pression pour couler des pièces, et leurs pièces moulées sont utilisées dans de nombreuses industries telles que l'automobile, l'électronique et la quincaillerie. Cela ajoute un avantage supplémentaire car ces alliages sont entièrement recyclables, conformément aux objectifs de durabilité. Cependant, les pièces moulées sous pression ZAMAK offrent des options de surface supplémentaires, ce qui aidera les fabricants à obtenir des produits esthétiquement attrayants avec un aspect haut de gamme, en particulier ces pièces décoratives.
Qu'est-ce que ZAMAK Die Casting ?
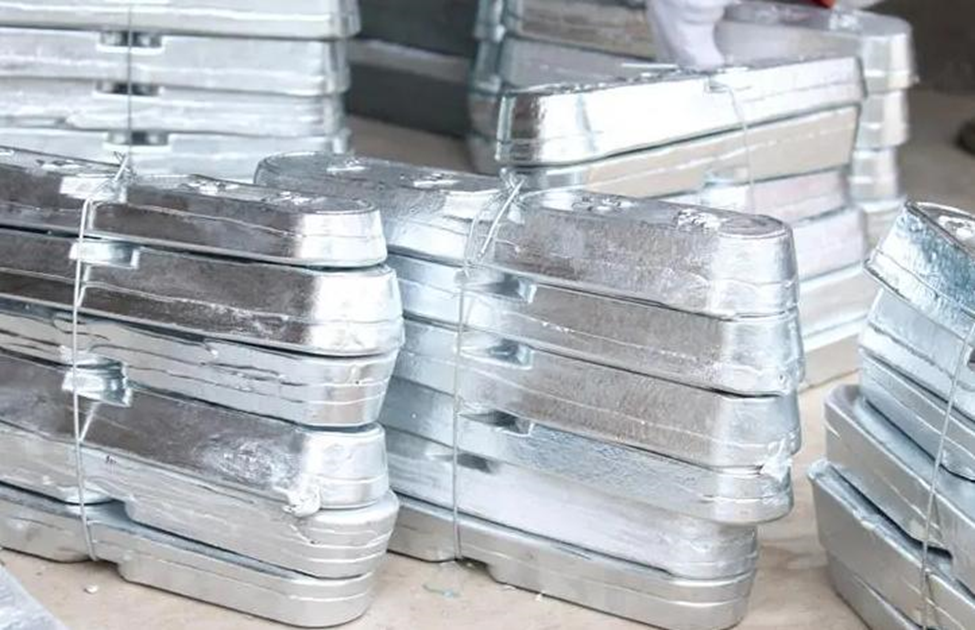
Le moulage sous pression de ZAMAK est une technique de moulage de métal largement utilisée dans laquelle l'alliage ZAMAK fondu est injecté sous haute pression dans un moule. Le moule est généralement fabriqué en acier à outils durable. Différents moules sont nécessaires pour chaque forme, et le processus de moulage sous pression ZAMAK ne nécessite qu'une machine de moulage sous pression à chambre chaude.
Une machine de moulage sous pression à chambre chaude à deux alvéoles est composée d'une moitié fixe et d'une moitié mobile. Ces moitiés sont ensuite fermées et le métal en fusion est injecté dans le moule par une chambre d'injection. Lorsque le métal est solidifié, la pièce moulée est retirée du moule par des broches d'éjection. Le moulage sous pression ZAMAK utilise cette méthode pour les alliages ZAMAK.
Le moulage sous pression à chambre chaude (HPDC), le moulage sous basse pression (LPDC) et le moulage par gravité (GDC) sont des types possibles d'alliages ZAMAK adaptés aux processus de moulage sous pression avec leurs avantages respectifs pour différentes applications.
1. Le processus de moulage sous pression de ZAMAK
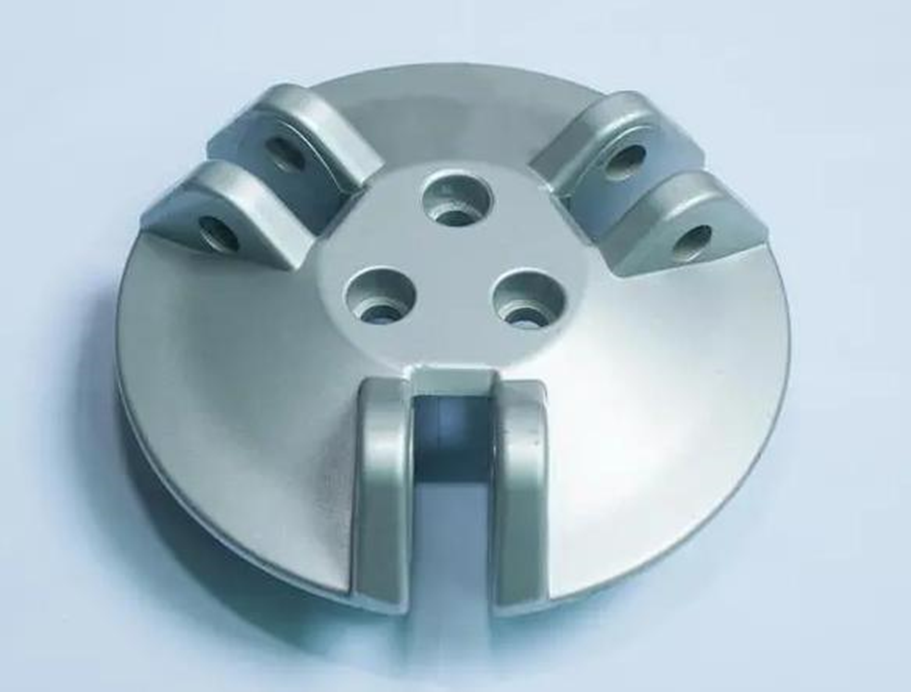
Comme d'autres types de moulage sous pression de l'aluminium ou du magnésium, la méthode de moulage sous pression ZAMAK nécessite une attention particulière dans la mesure du possible, car les résultats ne sont bons que dans la mesure où le processus de moulage ZAMAK l'est également. Le processus typique de moulage sous pression ZAMAK est décrit ci-dessous de manière détaillée :
Étape #1 : Conception et création de la matrice
Le processus commence par la conception du moule ou de la matrice et la conception de la pièce finale dans le processus de moulage sous pression ZAMAK. Elle est importante car elle détermine le résultat final du moulage en tant que tel. Tout d'abord, les ingénieurs conçoivent un modèle 3D de la pièce à mouler à l'aide d'un logiciel de CAO spécialisé. Généralement, un prototype est fabriqué et testé, la conception est améliorée jusqu'à l'approbation de la version finale. Deuxièmement, une fois la conception finale de la pièce établie, le moule est créé :
Le type d'injection : Le point de fusion du ZAMAK est suffisamment bas pour qu'il soit suffisamment chaud pour être injecté dans le moule.
- Les ingénieurs décident du nombre de cavités : Celles-ci sont disposées de manière à obtenir une efficacité maximale.
- Détermination du système de séparation : Il s'agit de la façon dont les deux moitiés du moule se rejoignent.
- Cela garantit un retrait en douceur de la pièce moulée, sans dommage, et une conception précise du système d'éjection.
- Planification du système de refroidissement : Sans refroidissement, des défauts se produiraient et la qualité des pièces ne pourrait pas être constante.
- Choix du matériau du moule : Les métaux tels que le H13, le SKD61 ou d'autres aciers à outils sont bons pour la durabilité et la résistance à la chaleur.
Étape #2 : Préparation de l'alliage ZAMAK
Ensuite, il faut préparer l'alliage ZAMAK. L'alliage ZAMAK est purifié à l'aide de plusieurs méthodes d'affinage, telles que l'affinage thermique, la réaction chimique, l'affinage électrolytique et l'affinage par zone.
L'alliage est fondu dans un four à des températures strictement contrôlées afin d'éviter que l'alliage ne devienne liquide et ne contienne des impuretés. Après l'affinage final, le métal fondu est conservé dans une chambre d'injection afin de contrôler la température et d'éviter toute contamination.
Étape #3 : Injection du ZAMAK fondu dans la matrice.
L'une des phases critiques du moulage sous pression est l'injection de ZAMAK en fusion dans le moule. Après préparation et stockage du métal en fusion dans la chambre d'injection, celui-ci est injecté sous haute pression dans le moule à l'aide d'un plongeur ou d'un piston. L'alliage en fusion subit une pression qui l'oblige à pénétrer dans tous les coins du moule, puisque tout l'espace de la cavité est rempli.
Il est ainsi possible d'obtenir une surface plane et lisse de la pièce et de produire des résultats de bonne qualité grâce à des techniques d'injection appropriées. La conception des canaux d'injection du moule est également un facteur déterminant pour y parvenir.
Étape 4 : Refroidissement et solidification de la pièce
Cependant, dès que le métal en fusion entre dans le moule, le refroidissement commence. Le moule en acier à outils de haute qualité est soumis à un cycle rapide afin d'évacuer la chaleur du métal en fusion suffisamment rapidement pour qu'il se solidifie. Le système de refroidissement est également utilisé par de nombreux moules pour accélérer le processus de solidification.
Simplement, pour obtenir la qualité de pièce souhaitée et éviter les défauts, une vitesse de refroidissement constante est nécessaire, et les systèmes les plus couramment utilisés sont les systèmes de refroidissement à l'eau et à l'air.
Étape #5 : Ejection de la coulée de ZAMAK solidifié
L'étape suivante de la solidification de l'alliage ZAMAK consiste à éjecter le moulage de la matrice. Il faut veiller à conserver la qualité de la pièce. Pour expulser la pièce solidifiée du moule, on utilise des goupilles d'éjection. Le moule s'ouvre en deux parties, la goupille d'éjection est actionnée et la pièce coulée est libérée. Cette étape exige une grande précision, car une force trop importante sur la pièce coulée peut l'endommager. Un bon alignement de la goupille d'éjection permet également d'éviter les imperfections de surface et les bosses.
Étape #6 : Finition et découpage
La pièce moulée est généralement éjectée avec un excédent de matière, appelé "flashing", qui doit être enlevé. Ceux-ci peuvent également affecter le fonctionnement de la pièce et doivent être soigneusement ébarbés. Le nettoyage de la pièce est réalisé à l'aide de divers outils d'ébarbage - machines de meulage et de polissage. Certaines fonderies peuvent procéder à un ébarbage manuel. Les pièces ébarbées peuvent faire l'objet d'un traitement de surface supplémentaire afin d'améliorer la finition de la pièce.
Étape #7 : Traitement de surface
Le traitement de surface est l'étape finale du moulage sous pression ZAMAK. Améliorant l'aspect de la pièce et la protégeant de la corrosion et de l'usure, les traitements de surface ne sont pas simplement décoratifs. Le ZAMAK est l'une des finitions de surface les plus utilisées commercialement, le plus souvent par la méthode du zingage, où la surface à zinguer, par exemple la pièce en ZAMAK, est recouverte d'une couche de zinc ou de tout autre matériau, c'est-à-dire de zinc ou de nickel noir, de chrome ou autre. Un autre secteur très populaire est celui de la peinture, qui comprend la peinture par pulvérisation et le revêtement par poudre. L'avantage du processus de revêtement par poudre est qu'il est généralement moins sensible à l'écaillage et à l'usure.
Ainsi, l'anodisation, bien que moins couramment utilisée, permet d'augmenter la dureté de la surface, tout en ajoutant une résistance à la corrosion, principalement pour les applications de la plus haute qualité telles que l'industrie automobile ou l'industrie de l'ameublement, entre autres.
2. Types de moulage sous pression ZAMAK Alloys
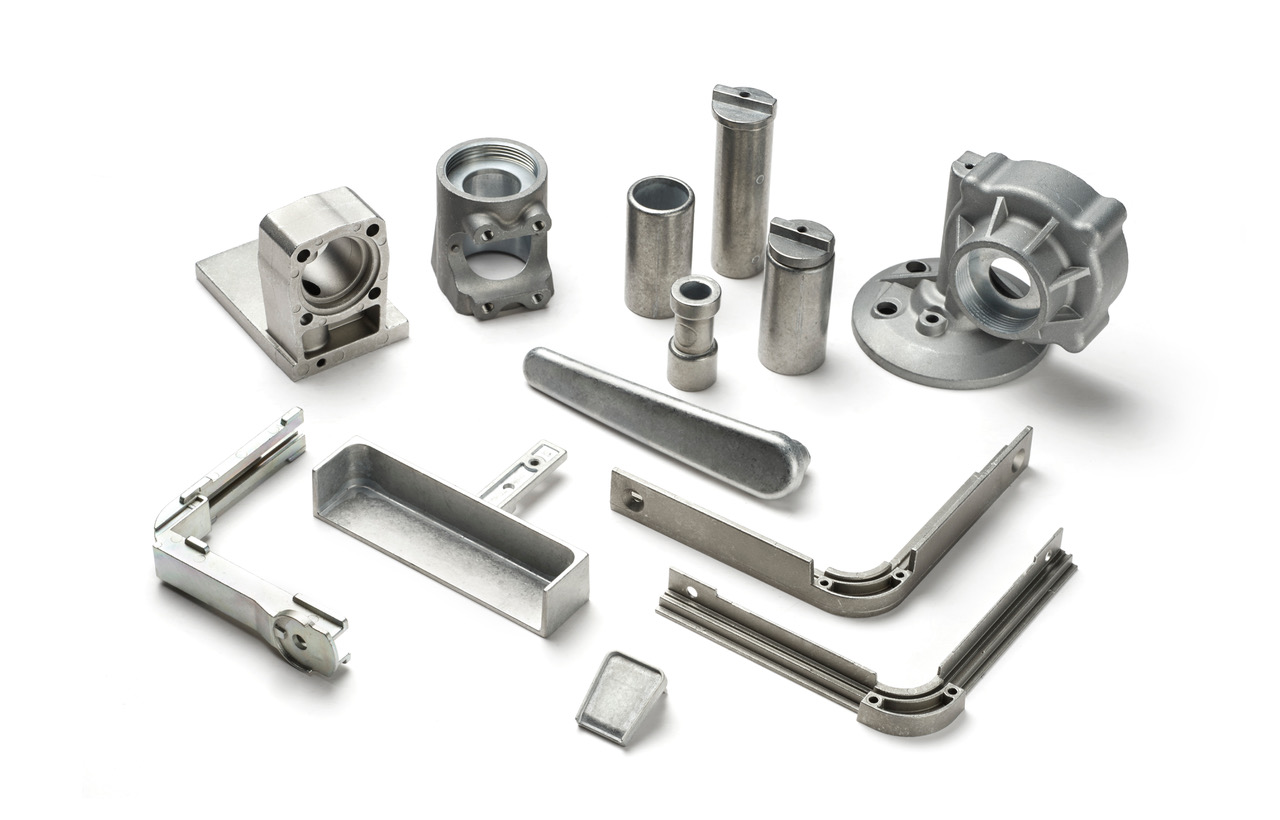
Ils sont disponibles sous forme d'alliages ZAMAK moulés sous pression de différentes qualités, en fonction des exigences particulières. Les nuances disponibles dans ces gammes présentent une variété de caractéristiques, une plus grande résistance ou une plus grande flexibilité, en fonction de l'utilisation du composant.
ZAMAK 3 et ZAMAK 5 sont parmi les grades de ZAMAK les plus utilisés. Le ZAMAK 3 est un bon équilibre entre résistance et flexibilité pour de nombreuses applications. Par rapport au ZAMAK 5, ce matériau présente une dureté et une résistance excellentes, ce qui le rend idéal pour les composants structurellement solides.
Le ZAMAK est également disponible dans d'autres qualités. Les tableaux suivants présentent la composition, les avantages et les applications de ces alliages dans l'ordre suivant.
Tableau 1 : Composition des alliages de moulage sous pression ZAMAK
ZAMAK Grade d'alliage | Zinc (%) | Aluminium (%) | Magnésium (%) | Cuivre (%) | Autres éléments |
ZAMAK Grade 2 | Équilibre | 4% | 0.035% | 1% | - |
ZAMAK Grade 3 | Équilibre | 3,5 à 4,3% | 0,02 à 0,05% | 0.25% | Fe <0,1%, Pb <0,005%, Cd <0,004%, Sn <0,003% |
ZAMAK 5e année | Équilibre | 3,5 à 4,3% | 0,03 à 0,06% | 0,75 à 1,25% | Fe 0,75%, Pb 0,004%, Cd 0,003%, Sn 0,002% |
ZAMAK 7e année | Équilibre | 3,5 à 4,3% | 0,005 à 0,02% | 0.25% | Fe 0,075%, Pb 0,003%, Cd 0,002%, Sn 0,001% |
Tableau 2 : Caractéristiques et applications de l'alliage de coulée sous pression ZAMAK
ZAMAK Grade d'alliage | Caractéristiques | Applications |
ZAMAK Grade 2 | Alliage ZAMAK le plus résistant et le plus dur | Outils lourds, pièces de machines |
ZAMAK Grade 3 | Équilibre entre la résistance, la flexibilité et la coulabilité | Composants automobiles, quincaillerie et boîtiers électriques |
ZAMAK 5e année | Résistance et dureté accrues, excellente résistance au fluage | Engrenages, leviers, petites pièces de machines |
ZAMAK 7e année | Excellente flexibilité et fluidité | Bornes électriques, connecteurs |
3. Avantages des alliages ZAMAK pour le moulage sous pression
Les principales raisons pour lesquelles les alliages ZAMAK sont utilisés dans le processus de moulage sous pression sont les suivantes :
Point de fusion bas : Les alliages ZAMAK ont un point de fusion bas et, en général, ils fondent à des températures relativement basses (généralement entre 380°C et 420°C), ce qui permet d'économiser de l'énergie et d'augmenter la vitesse de production.
Facilité de moulage : Les alliages ZAMAK ont des caractéristiques d'écoulement facile qui permettent au métal en fusion de remplir facilement la cavité de la matrice, ce qui les rend propices à la production de pièces complexes et hautement dimensionnelles avec des tolérances étroites.
Rapport résistance/poids : Les alliages ZAMAK offrent un excellent compromis entre résistance et poids, et constituent un bon choix pour les composants légers et résistants aux contraintes mécaniques.
Finition de la surface : La finition de surface des alliages ZAMAK est excellente, ce qui les rend appropriés pour des applications où l'esthétique est un facteur suprême. Cependant, ces alliages peuvent subir différents traitements de surface tels que le placage, l'anodisation ou la peinture, qui améliorent non seulement leur apparence mais aussi leur endurance.
Recyclage : Les alliages ZAMAK sont entièrement recyclables, ce qui permet de réduire les coûts des matériaux et les déchets. Le recyclage permet non seulement de préserver les ressources, mais aussi d'accroître la durabilité d'un cycle de fabrication.
4. Applications courantes des alliages ZAMAK
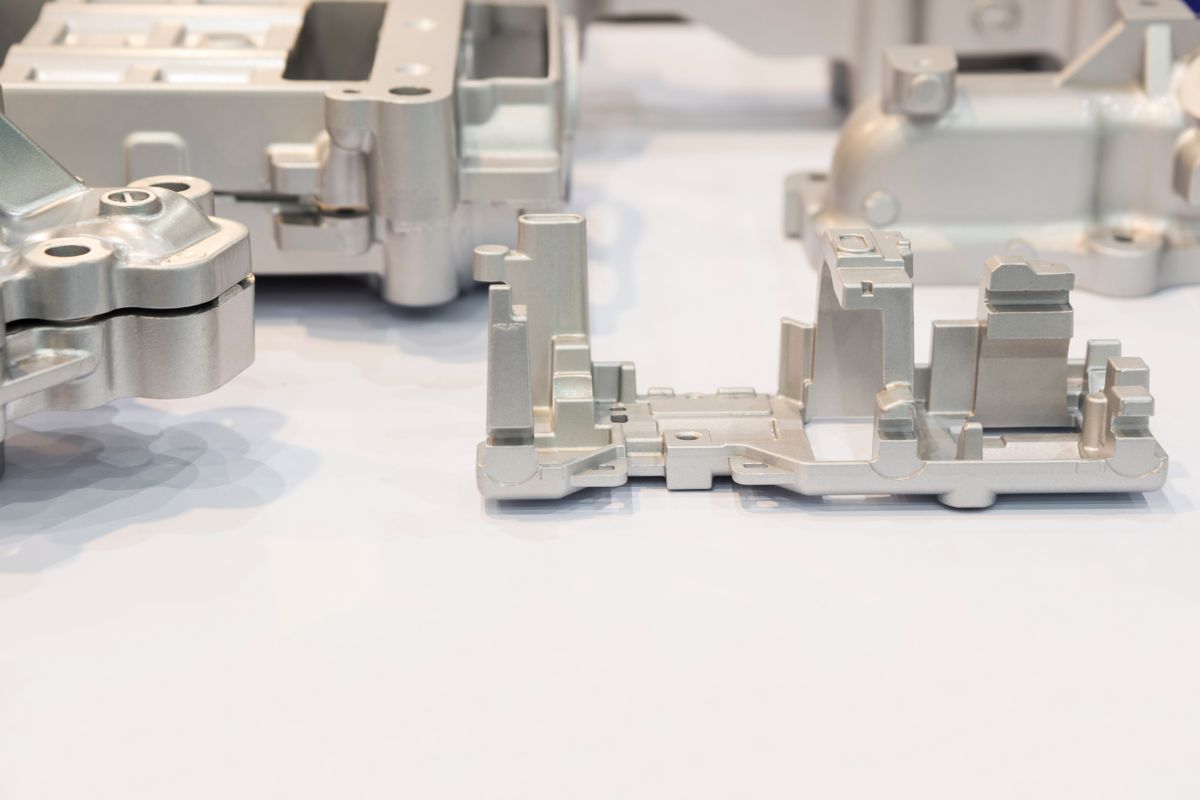
Les alliages ZAMAK sont utilisés dans un grand nombre d'industries :
- Équivalent en mousse de carbone Le ZAMAK moulé sous pression est utilisé pour des pièces telles que les poignées de porte, les pièces de moteur et les boîtiers électriques en raison de la résistance, de la légèreté et de l'intégrité thermique du matériau ZAMAK moulé sous pression.
- Les alliages ZAMAK sont le choix parfait pour l'électronique, comme ceux des boîtiers de téléphones portables, des cartes de circuits imprimés ou des connecteurs, et ils offrent un bon blindage EMI et une bonne durabilité.
- Les matériaux couramment utilisés pour la quincaillerie, qui sont à la fois solides et résistants à la corrosion, sont les alliages ZAMAK, qui sont utilisés dans la production de robinets, de quincaillerie de porte, de serrures et de boutons.
- Applications de finition de surface : Le ZAMAK se prête bien aux applications décoratives où de nombreuses finitions de surface peuvent être appliquées, qu'il s'agisse d'applications artistiques comme la bijouterie, les objets de collection ou les ornements.
Vous trouverez ci-dessous le tableau décrivant l'application des pièces moulées sous pression ZAMAK dans différents domaines, ainsi que des paragraphes consacrés à chaque catégorie mentionnée dans ce tableau.
Applications des pièces moulées sous pression ZAMAK
L'industrie | Exemples d'utilisation |
Industrie automobile | Poignées de porte, boutons, groupes, ventilateurs de climatisation, systèmes audio, pièces de réglage des ceintures de sécurité, composants du moteur, démarreurs, gadgets électroniques pour voitures. |
Industrie électronique | Pièces moulées et pièces pour ordinateurs portables, téléphones portables, écouteurs, télécommandes de télévision. |
Quincaillerie et mobilier | Poignées, leviers, tirettes, articulations, rails de tiroirs, pièces de mobilier décoratif. |
Plomberie et appareils ménagers | Poignées de robinet, pommeaux de douche, cadrans d'appareils, interrupteurs, bordures décoratives. |
Jouets et articles de sport | Véhicules jouets moulés sous pression, petits trains, pièces d'armes à feu jouets et pièces d'équipements sportifs. |
1. L'industrie automobile
L'industrie automobile est l'un des plus grands utilisateurs de pièces moulées sous pression en ZAMAK en raison de sa résistance, de sa précision et de sa légèreté. Les pièces ZAMAK sont légères, ce qui est très bénéfique pour l'amélioration de l'efficacité énergétique tout en maintenant les performances des différents composants automobiles. Les pièces complexes fabriquées, telles que les poignées de porte, les boutons et les groupes de commandes, sont durables et très esthétiques, ce qui fait des alliages ZAMAK le choix idéal. En outre, le ZAMAK est utilisé dans des pièces vitales telles que les ventilateurs de climatisation, les pièces du système audio, les dispositifs de réglage des ceintures de sécurité et les pièces du moteur, afin que le véhicule fonctionne correctement, même dans des conditions difficiles.
2. Industrie électronique
Le ZAMAK moulé sous pression est d'une importance capitale pour l'industrie électronique en raison de son efficacité en matière de protection contre les interférences électromagnétiques (EMI). Les propriétés uniques du ZAMAK permettent d'éviter les perturbations potentielles du signal qui sont courantes dans les gadgets électroniques. Divers produits tels que les pièces moulées pour ordinateurs portables, les pièces pour téléphones portables, les télécommandes de télévision et les écouteurs utilisent des pièces en ZAMAK. Les alliages ZAMAK offrent un niveau élevé de précision et de durabilité et constituent donc un bon choix pour les composants électroniques qui doivent présenter à la fois une intégrité structurelle et une résistance à l'influence des champs électromagnétiques.
3. Matériel et mobilier
C'est pourquoi les pièces moulées sous pression ZAMAK sont largement utilisées dans les industries de la quincaillerie et de l'ameublement en raison de leur capacité à produire d'excellentes qualités d'adhérence et à obtenir une finition de surface de haute qualité. En tant que tels, les alliages ZAMAK conviennent aux applications décoratives. Ils sont également couramment utilisés dans ce domaine pour les poignées et les leviers, les tirettes et les joints, ainsi que pour les rails de tiroirs et les composants de meubles décoratifs. Les alliages ZAMAK peuvent être recouverts d'une variété de revêtements - chromés ou en poudre, par exemple - afin de fournir une finition de qualité supérieure tout en restant fonctionnelle et durable.
4. Plomberie et appareils
La résistance à la corrosion rend également les pièces moulées sous pression en ZAMAK courantes dans les industries de la plomberie et de l'électroménager, où les pièces doivent être solides. La principale raison de la nature hautement malléable des alliages ZAMAK est qu'ils peuvent être façonnés dans les formes complexes requises dans les applications de plomberie. Les poignées de robinet, les pommes de douche, les cadrans d'appareils et les interrupteurs sont des exemples de pièces en ZAMAK dans ce domaine. Le ZAMAK peut résister aux conditions difficiles de l'eau et de la vapeur tout en conservant son intégrité structurelle, ce qui en fait un bon matériau pour ces applications.
5. Jouets et articles de sport
Le moulage sous pression du ZAMAK est généralement utilisé par les industries du jouet et de l'équipement sportif en raison de ses caractéristiques de résistance, de précision et de légèreté. Les alliages ZAMAK permettent de fabriquer des pièces spécifiques et complexes telles que des véhicules jouets moulés sous pression, des petits trains ou des composants d'armes à feu jouets. En outre, le ZAMAK est également durable et capable de résister à l'usure dans les pièces d'équipement sportif. ZAMAK veille à ce que le produit final, tel qu'une voiture jouet ou un article de sport, présente les caractéristiques susmentionnées.
5. Les alliages ZAMAK sont utilisés dans le moulage sous pression pour diverses raisons.
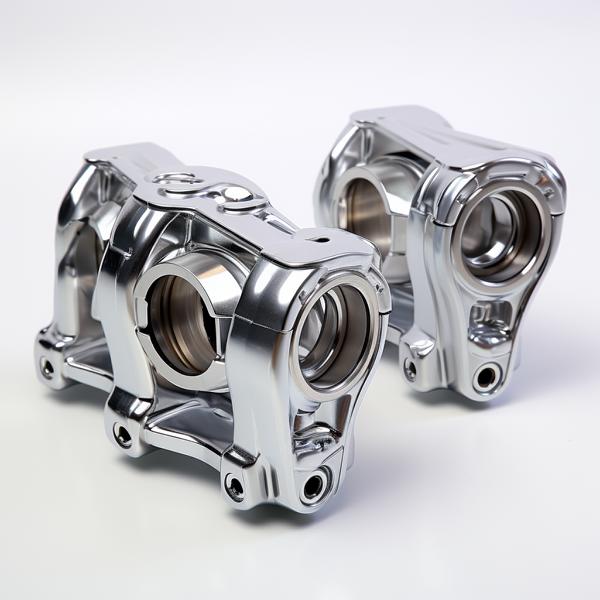
Les alliages ZAMAK, dont le spectre est principalement constitué de zinc, d'aluminium, de magnésium et de cuivre, sont de plus en plus utilisés dans le moulage sous pression en raison de leurs propriétés spécifiques. En général, ils offrent des avantages qui surpassent ceux des autres métaux dans des applications spécifiques. Par conséquent, voici quelques raisons clés pour lesquelles les alliages ZAMAK sont les plus préférés dans le domaine du moulage sous pression :
Motif #1 : Fluidité élevée
Les alliages ZAMAK présentent toutefois l'une des caractéristiques exceptionnelles, à savoir une grande fluidité. La facilité avec laquelle le métal en fusion s'écoule dans la cavité du moule pendant la coulée est appelée fluidité. Comme le ZAMAK possède cette propriété, il est plus facile de le remplir dans des moules aux formes complexes. Comme le métal en fusion peut s'écouler librement dans toutes les parties de la cavité du moule, les pièces moulées sous pression finies présentent des surfaces lisses, cohérentes et uniformes. Cette qualité est particulièrement utile pour les pièces fonctionnelles telles que les pièces à géométrie complexe qui exigent des détails très fins.
Raison #2 : ténacité et grande rigidité
Les alliages ZAMAK ont une bonne ténacité et se déforment facilement. Ces alliages sont assez durables et peuvent être utilisés en fonctionnement continu ou dans des conditions de contraintes élevées. L'un des principaux avantages des alliages ZAMAK 2 et 5 est leur grande rigidité et leur ténacité, qui conviennent aux produits soumis à une utilisation intensive. Les alliages de moulage sous pression ZAMAK sont fiables pour les composants utilisés dans des conditions de stress et d'usure fréquents, car l'alliage est durable.
Raison #3 : Rapport résistance/poids élevé
Bien que la résistance à la traction des alliages d'aluminium soit légèrement supérieure, les alliages ZAMAK se comparent toujours très bien en termes de résistance par rapport au poids. Les pièces moulées sous pression en ZAMAK sont légères tout en ayant une résistance à la traction de 280 MPa, ce qui les rend adaptées à de nombreuses applications dans diverses industries où la résistance et la réduction du poids sont les caractéristiques recherchées. L'équilibre dont jouissent les ZAMAK en fait un substitut idéal à l'aluminium dans le cas de pièces qui doivent être à la fois résistantes et légères.
Raison #4 : Point de fusion bas
Les alliages ZAMAK ont l'avantage d'avoir un point de fusion relativement bas qui varie entre 380°C et 420°C (sauf ZAMAK 2). Cette caractéristique présente plusieurs avantages clés :
- Elle est donc moins coûteuse en énergie, car elle nécessite moins d'énergie pour fondre le métal à des températures plus basses.
- Point de fusion plus bas : Il en résulte une solidification plus rapide des pièces moulées et donc une production plus rapide.
- Moins de défauts de coulée : Après une solidification très rapide d'une pièce, il est plus difficile d'être affecté par des défauts de coulée.
Raison #5 : Excellente adhérence
Les alliages ZAMAK sont considérés comme de bons liants avec différents matériaux de revêtement. Cette caractéristique permet une grande variété (par opposition à la haute précision) de matériaux conducteurs dans le traitement de surface (c'est-à-dire la galvanoplastie ou la peinture) pour un produit final à l'apparence particulière. La forte adhérence garantit que les revêtements resteront en place au fil du temps, ce qui contribue à améliorer à la fois l'esthétique et la durabilité des pièces moulées sous pression. La disponibilité de cette propriété convient parfaitement aux produits exigeant à la fois la fonctionnalité et une finition haut de gamme.
Raison #6 Excellentes propriétés d'usure et de roulement
Les alliages ZAMAK ont une bonne résistance à l'usure et sont résistants à la friction rencontrée dans les pièces mobiles. Les composants ZAMAK conservent leur fonctionnalité sous une contrainte continue. En raison de leur résistance à l'usure, les alliages de moulage sous pression ZAMAK peuvent être utilisés pour des applications spécifiques aux pièces mobiles telles que les engrenages, les leviers et autres composants mécaniques. Cela permet de minimiser la nécessité de les remplacer fréquemment et d'offrir une fiabilité à long terme avec un coût de maintenance réduit.
Raison #7 : 100% Recyclable et respectueux de l'environnement
Les alliages ZAMAK sont recyclables et constituent donc un matériau écologiquement sain. La qualité du produit final ne souffre pas de la refonte et de la réutilisation des déchets ZAMAK. De plus, le produit est recyclable, ce qui réduit les déchets et les coûts des matières premières. Les alliages ZAMAK peuvent être réutilisés dans de nombreuses industries maintenant que la durabilité est devenue importante, et l'utilisation des alliages ZAMAK contribue à améliorer le processus de fabrication respectueux de l'environnement.
Raison #8 : Rentabilité
D'autre part, les alliages ZAMAK pour le moulage sous pression coûtent un peu plus cher que les alliages d'aluminium, mais le coût est abordable car il est inférieur à celui des autres métaux. Les alliages ZAMAK sont moins chers (et donc économiques) que les alliages à haute performance comme le laiton et le cuivre. Les alliages ZAMAK présentent d'excellentes propriétés de coulée et sont très durables, tout en étant économiques, ce qui est intéressant pour les fabricants qui cherchent à trouver le bon équilibre entre performance et budget.
6. Comment choisir le bon fabricant de pièces moulées sous pression en zamak ?
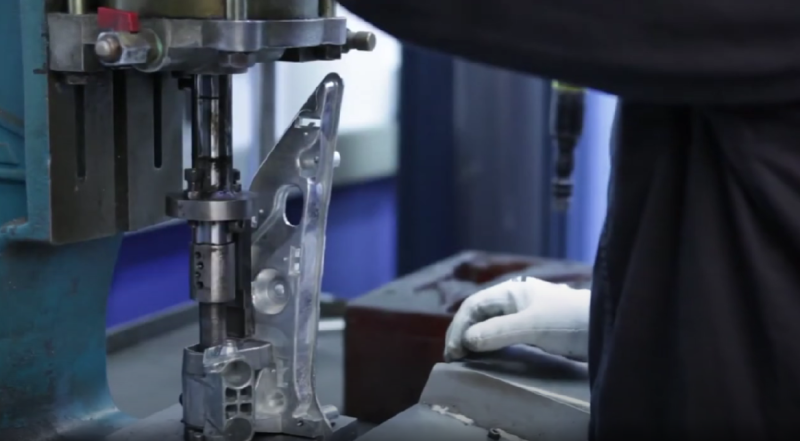
Il y a quelques éléments à prendre en compte lors de l'évaluation d'un fabricant ou d'un fournisseur de pièces moulées sous pression en zamak afin de garantir des résultats optimaux pour votre projet :
- Le fabricant doit avoir de l'expérience dans le moulage sous pression du Zamak ainsi qu'une bonne expérience de cet alliage et de la procédure de moulage. Il peut ainsi produire votre pièce de haute qualité selon vos spécifications.
- Capacités et équipement - Recherchez un fabricant disposant d'un équipement de pointe lui permettant de réaliser de grandes séries de production avec précision et qualité, capable de gérer de grandes séries de production.
- Un producteur digne de confiance doit pouvoir se prévaloir de certifications telles que ISO 9001, indiquant qu'il suit des procédures strictes de contrôle de la qualité afin d'assurer la cohérence et le respect de normes élevées à chaque étape.
- Chaque projet doit être unique, et un bon fabricant de pièces moulées sous pression en zamak doit proposer des options de personnalisation en fonction de vos besoins, comme des finitions personnalisées, des revêtements spéciaux ou des alliages spéciaux tels que le Zamak 3 moulé sous pression.
- Une relation solide avec le fabricant est essentielle - Assistance à la clientèle. Vérifiez les fournisseurs qui offrent un bon service d'assistance à la clientèle tout au long du processus, de la conception à la production et à l'après-livraison.
7. Pourquoi le Zamak 3 moulé sous pression est-il un choix si populaire pour les projecteurs ?
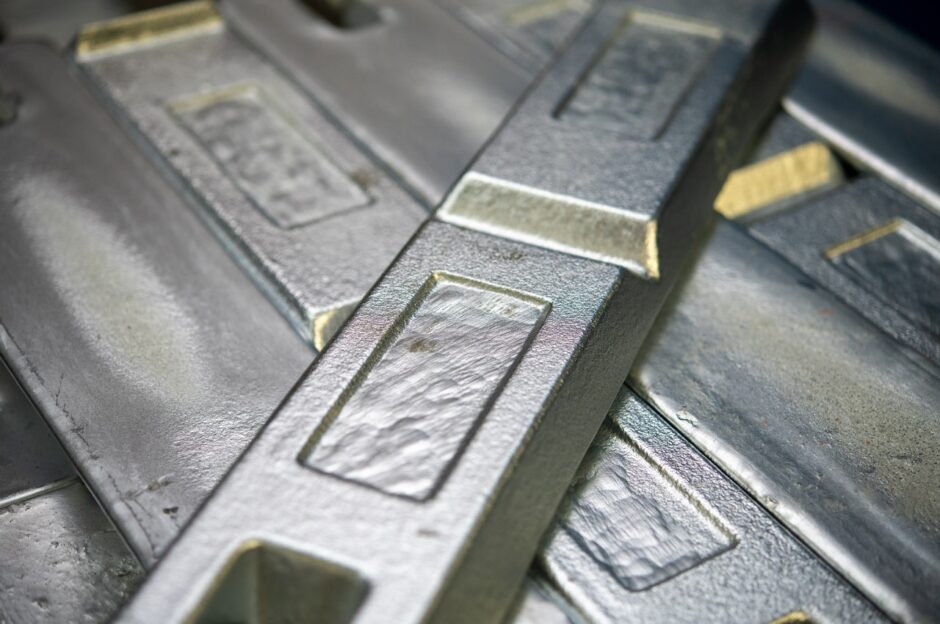
L'un des alliages de zamak les plus utilisés dans l'industrie du moulage sous pression est le Zamak 3. Le Zamak 3 est connu pour ses bonnes propriétés mécaniques, sa résistance, sa durabilité et sa facilité de moulage. En raison de sa teneur élevée en zinc, il a une bonne capacité à résister à la corrosion, ce qui le rend approprié pour les pièces exposées à des environnements extérieurs et dans l'industrie automobile. En outre, le Zamak 3 peut être facilement moulé dans des formes complexes, ce qui facilite les projets à petite et grande échelle.
Grâce à ces avantages, le Zamak 3 Die Cast reste la solution pour de nombreuses applications où la solidité, le poids et la résistance à la corrosion sont essentiels.
Nous sommes CNM TECH - l'un des principaux fabricants de pièces moulées sous pression ZAMAK.
Chez CNM TECH, nous sommes experts dans la fourniture de pièces moulées sous pression ZAMAK de haute qualité. En tant que professionnel de l'industrie depuis des années, nous sommes fiers de produire des pièces moulées sous pression ZAMAK durables, précises et relativement bon marché pour une variété d'industries. Nous utilisons des processus de fabrication de pointe pour nous assurer que nous produisons des pièces de qualité et fiables.
Nous savons donc quels matériaux vous devez utiliser. C'est pourquoi nous nous concentrons sur les alliages ZAMAK qui présentent une excellente fluidité, des rapports résistance/poids élevés, un point de fusion bas et une bonne recyclabilité. Nos composants moulés sous pression en ZAMAK conviennent aux applications automobiles, électroniques ou matérielles et fonctionnent dans les conditions les plus extrêmes.
Chez thediecasting.com, nous travaillons avec nos clients pour comprendre leurs besoins exacts et leur fournir des solutions spécialement conçues pour eux. Grâce à notre expertise en matière d'innovation et à notre équipe d'ingénieurs qualifiés, nous nous engageons à fournir des produits conçus avec précision et présentant d'excellentes finitions de surface.
Si vous avez besoin d'une Moulage sous pression ZAMAKCNM TECH est le partenaire idéal pour faire de votre projet une réalité. Si vous souhaitez en savoir plus sur la manière dont nous pouvons vous aider dans votre prochain projet, consultez le site thediecasting.com !
8. Conclusion
Enfin, il est conclu que le moulage sous pression du zamak présente des avantages inégalés en termes de coût, d'efficacité et de polyvalence. Que vous ayez besoin de pièces pour l'automobile, l'électronique ou les biens de consommation, le moulage sous pression du zamak est un processus qui peut vous permettre d'obtenir des pièces durables de haute qualité. Le moulage sous pression du Zamak 3 offre des avantages uniques et, associé à l'utilisation d'un fabricant de moulage sous pression du Zamak approprié, peut garantir que votre travail répond à tous les mandats tout en maintenant vos coûts de production à un niveau bas. Grâce à cette force, à la précision et à l'efficacité du moulage sous pression Zamak, les entreprises sont toujours en mesure de créer des pièces de haute performance pour continuer à répondre aux besoins changeants des industries modernes.
FAQ
1. Qu'est-ce que le moulage sous pression en zamak ?
Il s'agit également du processus de création de pièces précises et durables par l'injection d'un alliage de zamak fondu dans un moule. Il est populaire parce qu'il est rentable, solide et qu'il peut être utilisé pour produire des formes complexes nécessitant peu de finition.
2. Quelle est la différence entre le Zamak 3 et les autres alliages de Zamak ?
Le Zamak 3 est l'alliage de Zamak le plus courant en raison de l'équilibre entre la résistance et la facilité de coulée. D'autres alliages, comme le Zamak 5, offrent une résistance ou une dureté plus élevée en fonction des besoins, mais le Zamak 3 est extrêmement polyvalent.
3. Le moulage sous pression du zamak est utilisé dans ?
Dans les secteurs de l'automobile, de l'électronique, des biens de consommation et des équipements industriels, les composants durables et précis qu'elle produit grâce au moulage sous pression en zamak jouissent d'une grande popularité.
4. Quel est le processus de sélection d'un fabricant de pièces moulées sous pression en zamak ?
Sélectionnez un fabricant de pièces moulées sous pression en zamak qui possède l'expérience, la capacité d'équipement, la certification de qualité, la personnalisation et un solide service à la clientèle.