
Le moulage et le moulage sous pression sont deux processus de fabrication importants qui sont essentiels pour fabriquer des composants métalliques avec la précision, la durabilité et l'efficacité souhaitées. Le moulage consiste à placer un matériau en fusion dans un moule et à le laisser refroidir et se solidifier. Le moulage en sable, le moulage à la cire perdue et le moulage en moule permanent sont quelques types de moulage. Toutefois, le moulage sous pression est un moulage spécial qui utilise une pression élevée pour injecter le métal fondu dans une cavité de moule avec une grande précision et une bonne finition de surface. Le moulage sous pression est largement utilisé dans les secteurs de l'automobile, de l'aérospatiale, de l'électronique et d'autres applications industrielles connexes qui nécessitent des pièces légères, solides et résistantes à la corrosion. Au fil du temps, différentes variantes de moulage sous pression ont été développées pour répondre aux différents besoins des industries. Le moulage sous pression par gravité (GDC) dépend de la gravité pour remplir le moule et le moulage sous basse pression (LPDC) élimine les turbulences pour obtenir une meilleure qualité d'intégrité du matériau. La pression extrême appliquée par le moulage sous pression crée des pièces très résistantes, sans porosité, et l'air emprisonné est éliminé dans le moulage sous vide pour obtenir un composant sans défaut. En outre, le moulage sous pression à l'état semi-solide (rhéocoulage) est obtenu en utilisant un métal partiellement solidifié pour améliorer les propriétés mécaniques et la précision.Le terme général de moulage dans la fabrication est utilisé pour se référer à la forme de façonnage du métal en le remplissant dans un moule et en le laissant se solidifier. Cette méthode est couramment utilisée dans le moulage en sable, le moulage à la cire perdue et le moulage en moule permanent. La matrice dans le moulage sous pression est le moule métallique utilisé dans le processus de moulage sous haute pression, tandis que la matrice dans le processus de moulage sous pression est le moule métallique fixé à la face de la matrice. Des matrices en acier trempé, conçues pour la production de masse, sont généralement fabriquées.
Cet article aborde les concepts de la coulée et du moulage sous pression, les différences entre ces deux concepts, les types de chacun, les applications possibles, ainsi que les avantages et les inconvénients liés à ce processus de coulée.
1. Qu'est-ce que la coulée ?
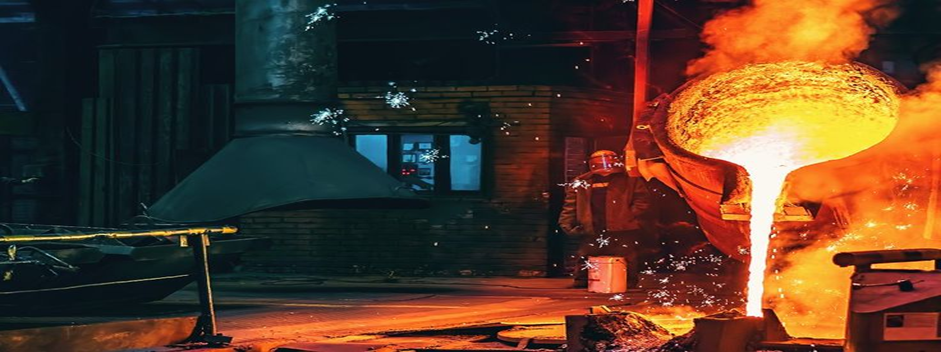
Le moulage est un processus industriel au cours duquel un matériau liquide est forcé dans un moule où il se solidifie. Le liquide peut être n'importe quel métal, plastique ou autre matériau pouvant être fondu. Après durcissement, le matériau prend une forme correspondant à la cavité du moule. Depuis plusieurs milliers d'années, cette technique a permis de créer des outils, des armes et des sculptures complexes.
Le processus de moulage
Plusieurs de ces étapes jouent un rôle essentiel dans la nature du processus de moulage d'un composant métallique ou plastique.
- 1. Un modèle du produit final est réalisé en bois, en plastique ou en métal. La forme et les dimensions de la cavité du moule sont déterminées sur la base de ce modèle.
- 2. Lors de la préparation du moule, la cavité du moule est conçue en fonction du modèle. La méthode de moulage déterminera s'il est fait de sable, de métal ou de céramique. Les systèmes d'aération et de fermeture permettant un écoulement fluide de la matière en fusion sont correctement intégrés.
- 3. Il s'agit de la fusion de la matière première, généralement du métal ou du plastique, à une température élevée dans un four. La température spécifique au type de matériau utilisé est différente.
- 4. Le matériau fondu est versé avec précaution dans la cavité du moule, en quantité suffisante pour éviter les défauts, car la coulée est régulière. Cette opération peut être effectuée manuellement ou à l'aide de systèmes de coulée automatisés.
- 5. Solidification - Le matériau se refroidit et se solidifie à l'intérieur du moule pour former la forme de la cavité. On sait que c'est la vitesse de refroidissement qui affecte les propriétés finales du produit moulé.
- 6. Après solidification, la pièce moulée est démoulée, les matériaux excédentaires tels que les portes, les coulisses ou les bavures sont coupés, puis l'assemblage est soumis à un processus de démoulage et de finition. Ils peuvent ensuite être soumis à des processus de finition supplémentaires tels que le meulage, le polissage ou le traitement thermique afin d'améliorer l'apparence et les propriétés mécaniques du produit final.
Grâce à cette approche structurée, le moulage est réalisé avec plus de fiabilité et de qualité.
2. Qu'est-ce que le moulage sous pression ?
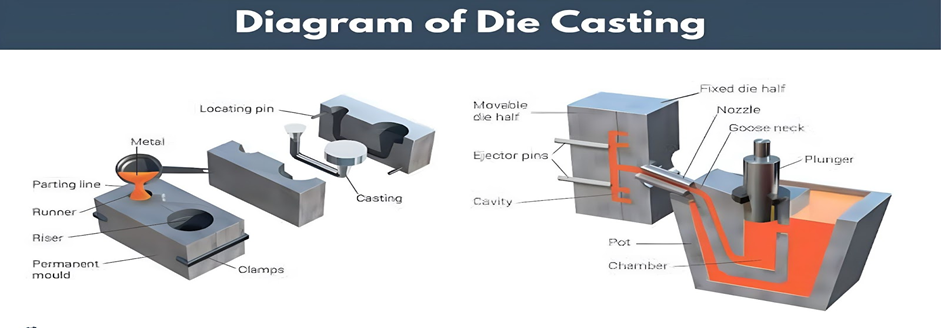
Dies signifie moules, d'où le nom du processus de moulage sous pression, dans lequel un métal en fusion est injecté sous haute pression pour remplir la cavité d'un moule. Ce procédé est le mieux adapté à la fabrication de pièces complexes, précises et de grand volume.
Le processus de moulage sous pression
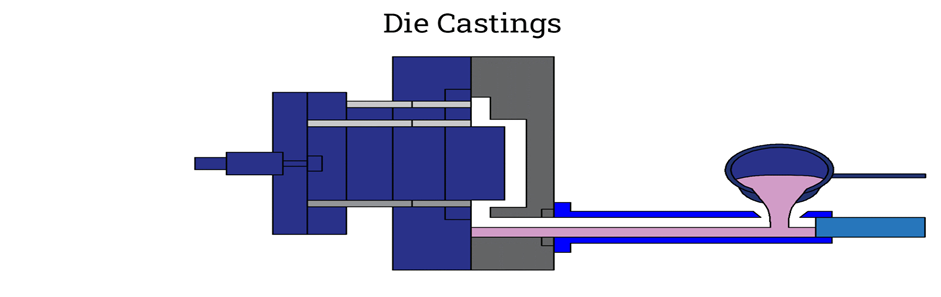
Le moulage sous pression est un processus de fabrication dans lequel les composants métalliques sont formés dans la forme de la cavité d'une matrice sous haute pression tout en nécessitant une grande précision et une exactitude des dimensions et de la finition de la surface. Il s'agit de suivre les étapes ci-dessous :
- 1. Injection de métal en fusion - Une pression élevée, comprise entre 1 500 et 25 000 psi, est appliquée pour injecter du métal en fusion (comme l'aluminium, le zinc ou le magnésium) dans un moule en acier (matrice), qui fait fondre le métal sélectionné dans un four. Le métal en fusion remplit ainsi le moule dans ses moindres détails.
- 2. Moule ou matrice - Le métal en fusion se refroidit et se solidifie réellement dans la matrice, ce qui permet d'obtenir une pièce solide et précise. Les propriétés mécaniques du produit final dépendent de la vitesse de refroidissement.
- 3. Éjection et ébarbage - Une fois solidifiée, la pièce moulée est éjectée de la matrice par des broches d'éjection. L'excédent de matière, y compris la bavure, les coulisses et les portillons, est ébarbé pour obtenir la forme souhaitée.
- 4. Finition de la surface - En fonction de l'application, le moulage peut nécessiter une finition supplémentaire : meulage de Nice, polissage, peinture, anodisation ou revêtement en poudre pour améliorer son aspect, sa durabilité et sa résistance à la corrosion.
Ce procédé permet d'obtenir des pièces complexes très résistantes et légères, avec peu de traitement ultérieur. Les matériaux les plus couramment utilisés pour le moulage sous pression sont les métaux non ferreux, tels que l'aluminium, le zinc et le magnésium.
Types de procédés de moulage
Il existe différents types de moulage en fonction du type de méthode utilisée
1 Moulage au sable

- Il s'agit de l'une des méthodes de moulage les plus polyvalentes et les plus économiques utilisant des moules en sable.
- Fréquent dans les industries automobile, aérospatiale et artistique.
2 Coulée en cire perdue
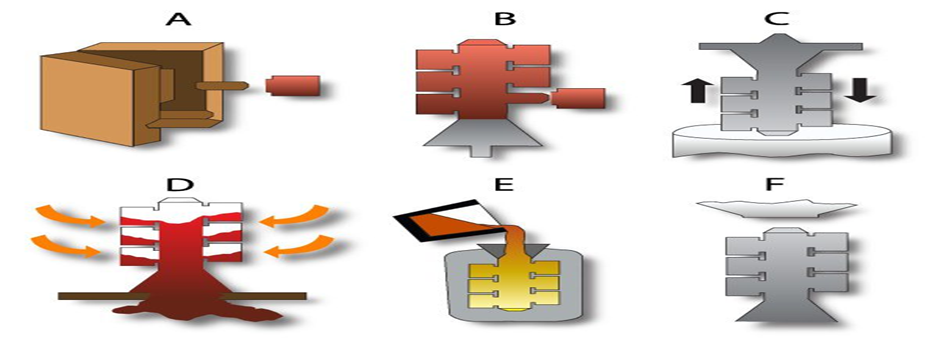
- Également connue sous le nom de fonte à la cire perdue, cette technique permet de réaliser des pièces complexes et très détaillées.
- Utilisé pour la bijouterie, les implants médicaux et les composants aérospatiaux.
3 Coulée centrifuge

- Il s'agit de faire tourner un moule pour intégrer complètement le métal en fusion.
- Utilisé couramment pour la fabrication de tuyaux, de cylindres et d'anneaux.
4 Moulage en moule permanent
- Réduit les déchets et l'utilisation de moules grâce à la réutilisation.
- Il est idéal pour la production répétée de pièces métalliques de haute qualité.
Types de moulage sous pression
Il existe principalement deux méthodes de moulage sous pression :
1. Moulage sous pression à chaud
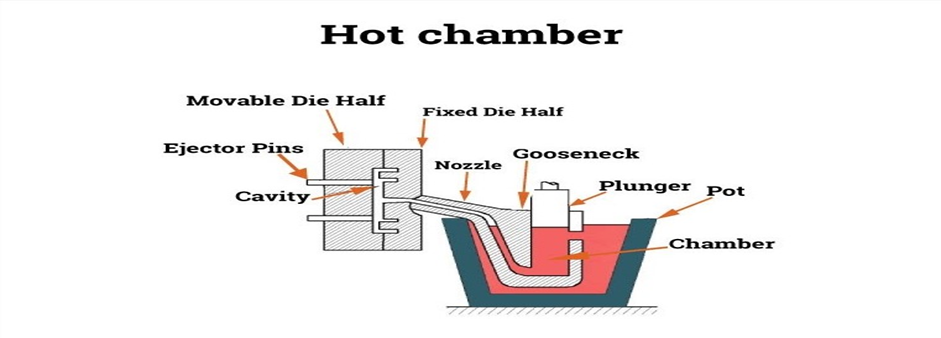
- Utilisé pour les métaux à bas point de fusion comme le zinc et le magnésium.
- Processus plus rapide avec des taux de production plus élevés.
2. Moulage sous pression en chambre froide

- Il est utilisé pour les métaux à point de fusion élevé tels que l'aluminium et le laiton.
- Ralentit les étapes de fusion et d'injection, tout en étant adapté aux pièces durables.
5. Différences entre le moulage et le moulage sous pression
Fonctionnalité | Casting | Moulage sous pression |
processus | Moule Métal versé dans le moule | Le métal en fusion est injecté sous haute pression |
Matériaux | Métaux et plastiques divers | Principalement des métaux non ferreux comme l'aluminium et le zinc |
Précision | Modéré | Haute précision |
coût | Coût initial peu élevé | Coût initial élevé de l'outillage |
Applications | Pièces simples et de grande taille | Pièces de petite taille, complexes et de grand volume |
Applications du moulage et de la coulée sous pression

Le moulage et le moulage sous pression jouent, chacun à leur manière, un rôle immense dans différentes industries et sont rentables car ils facilitent la fabrication de composants métalliques complexes avec une excellente précision.
- Dans l'industrie automobile, il s'agit de produire des blocs moteurs, des carters de transmission, des moyeux de roue, des pièces de freinage et des pièces de suspension. En ce qui concerne les pièces légères en aluminium, le moulage sous pression est particulièrement apprécié car il permet d'atteindre des niveaux plus élevés d'efficacité énergétique.
- Aérospatiale : Les composants aérospatiaux tels que les pales de turbines, les composants structurels des cellules, les boîtiers et les composants des trains d'atterrissage sont moulés pour être durables et résistants tout en étant légers.
- Dans le domaine de l'électronique, le moulage et le moulage sous pression sont essentiels car les boîtiers et les composants moulés sous pression, tels que les dissipateurs thermiques, les connecteurs et les dispositifs de blindage, sont nécessaires pour évacuer la chaleur et assurer la sécurité des circuits électroniques fragiles.
- Construction - Tuyaux, raccords, supports, vannes et garde-corps pour la construction de bâtiments, de ponts, etc. assurant la stabilité structurelle et la longévité.
- Équipement médical - Les composants moulés de précision sont largement utilisés dans le domaine médical pour les instruments chirurgicaux, les boîtiers d'équipement d'imagerie, les implants orthopédiques, etc.
- Machines industrielles - Le moulage est nécessaire pour assurer la solidité et la résistance à l'usure des boîtes de vitesses, des pompes et d'autres pièces de machines lourdes travaillant dans des conditions difficiles.
L'application du moulage et du moulage sous pression est très répandue et constitue donc un élément indispensable des industries manufacturières modernes.
Variantes du moulage sous pression
L'un des processus de fabrication les plus populaires est le moulage sous pression, dans lequel le métal fondu est introduit dans le moule pour fabriquer des composants aux caractéristiques complexes et prescrites. Différentes variantes du moulage sous pression ont été développées au fil du temps pour s'adapter aux matériaux, aux exigences de production et aux normes de qualité. Chaque méthode a ses avantages et sera plus ou moins adaptée à différents types d'applications. Voici les principales variantes de moulage sous pression, avec leurs processus et avantages respectifs.
Moulage sous pression par gravité (GDC)
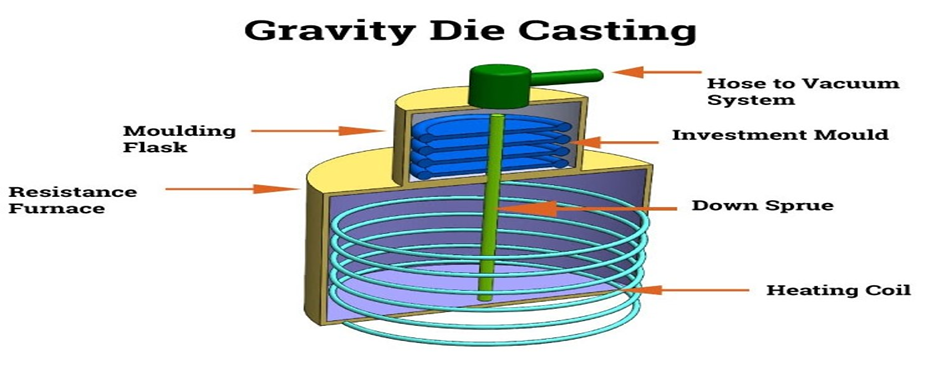
Vue d'ensemble
Le moulage sous pression par gravité (GDC) consiste à couler du métal en fusion dans un moule sans utiliser de pression élevée. C'est plutôt la gravité qui guide le métal pour qu'il remplisse la cavité et s'organise, comme s'il était tout seul. Ce procédé est préféré pour les alliages à bas point de fusion et est couramment utilisé lorsqu'un processus de solidification plus contrôlé est souhaité.
Caractéristiques principales
- Il est plus efficace que le moulage en sable, car il utilise des moules réutilisables.
- Plus lent que le moulage sous pression, mais la pièce est plus résistante grâce à la densité de la forme.
- Limité à des alliages spécifiques, tels que l'aluminium et le magnésium.
Applications courantes
- Composants automobiles (culasses, pièces de moteur).
- Raccords de tuyauterie et corps de vanne.
- Machines industrielles et pièces de structure.
Moulage sous pression (LPDC)

Vue d'ensemble
Le moulage sous pression (LPDC) consiste à pressuriser le métal fondu dans le moule sous une faible pression de l'ordre de 0,1 à 1 MPa. Grâce à ce remplissage contrôlé, les turbulences sont minimisées et l'écoulement est plus régulier, ce qui permet de réduire au minimum les défauts tels que les poches d'air et les inclusions.
Caractéristiques principales
- Meilleure intégrité des matériaux grâce à la réduction des turbulences.
- Cette option convient aux pièces complexes et de grande taille qui nécessitent une résistance structurelle élevée.
- Il est fiable (qualité constante) dans le cas d'une production de masse.
Applications courantes
- Roues en aluminium pour automobiles.
- Pièces de structure d'aéronefs.
- Composants résistants à la chaleur dans les machines industrielles.
Moulage sous pression

Vue d'ensemble
Dans le processus de coulée Squeezedie, une pression élevée est imposée au métal en fusion à l'intérieur de la cavité du moule. La force appliquée atteignant plus de 20 000 psi (livres par pouce carré), le métal remplit les moindres détails du moule et élimine les porosités.
Caractéristiques principales
- Crée des pièces extrêmement denses et résistantes.
- Réduit la porosité et améliore les propriétés mécaniques.
- Applicable aux applications à haute résistance où la durabilité est importante.
Applications courantes
- Composants de suspension pour automobiles.
- Pièces aérospatiales de haute performance.
- Outils et équipements industriels lourds.
Moulage sous vide

Vue d'ensemble
Le moulage sous vide utilise sa conception pour évacuer l'air et les gaz emprisonnés dans la cavité du moule avant et pendant le processus de moulage. Cette méthode est mise en œuvre en créant un vide et permet de réduire considérablement la porosité, qui est un défaut courant dans le moulage sous pression standard. Il en résulte un moulage plus précis, plus solide et sans défaut.
Caractéristiques principales
- Améliore les propriétés mécaniques du produit final.
- Il minimise l'emprisonnement de l'air, ce qui le rend approprié pour les pièces à parois profondes et de haute précision.
- Améliore la qualité globale du moulage, en réduisant les opérations de post-traitement.
Applications courantes
- Soudage des pièces structurelles de l'automobile pour assurer la durabilité du poids léger.
- Composants d'équipements médicaux de haute précision.
- L'intégrité des pièces aérospatiales.
Moulage sous pression semi-solide (Rheocasting)

Vue d'ensemble
Le rhéocasting ou moulage sous pression à l'état semi-solide utilise un métal partiellement solidifié plutôt que totalement liquide. Le métal reste ainsi dans un état semi-liquide ou boueux, ce qui lui permet de s'écouler en douceur dans le moule et de réduire les turbulences et la porosité.
Caractéristiques principales
- Produit des composants aux propriétés mécaniques supérieures.
- Réduit les défauts de retrait et la porosité.
- Idéal pour les pièces complexes et de haute précision.
Applications courantes
- Toutes les pièces automobiles qui exigent une grande résistance et des propriétés de légèreté.
- Boîtiers électroniques avec détails fins.
- Pour les machines industrielles dont les composants doivent résister à l'usure.
Métaux courants utilisés dans le moulage sous pression
Le procédé de fabrication utilisé pour injecter du métal en fusion dans un moule sous haute pression est le moulage sous pression. Le métal sélectionné dans ce processus est également essentiel pour la résistance et la durabilité du produit final, ainsi que pour son application. Différents métaux peuvent être utilisés pour ce type de moulage, mais les métaux non ferreux (ou exempts de fer) sont les plus couramment utilisés car ils ont des points de fusion plus bas et sont plus faciles à mouler.
Les métaux les plus utilisés dans le moulage sous pression, avec leurs propriétés et leurs utilisations, sont mentionnés ci-dessous.
1. L'aluminium
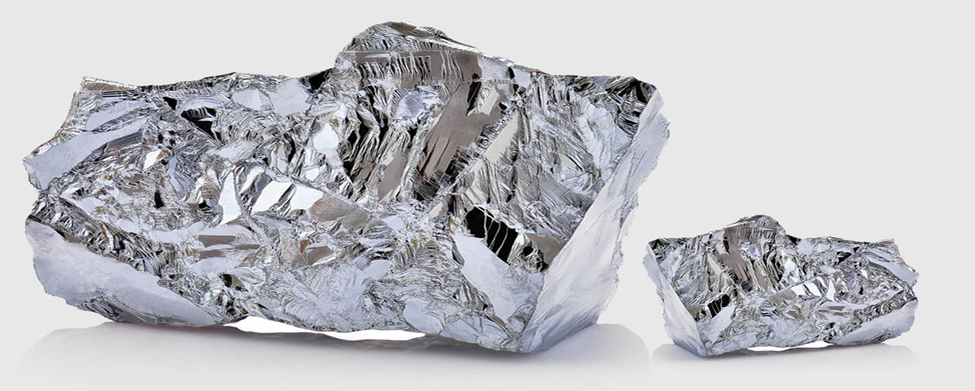
Parmi les métaux utilisés dans les le moulage sous pression, Cependant, l'aluminium est le plus largement utilisé et présente la combinaison idéale d'une bonne solidité, d'un faible poids et d'une bonne résistance à la corrosion. Avec une densité relativement faible, c'est un bon candidat pour être utilisé dans les industries où des composants à faible densité et à haute résistance sont nécessaires.
Avantages de l'aluminium dans le moulage sous pression
- Léger et solide, il est utilisé dans les industries automobile et aérospatiale pour réduire le poids.
- Résistant à la corrosion - Convient aux applications extérieures et marines.
- Bonne conductivité thermique et électrique - Utilisé dans les boîtiers électroniques et les dissipateurs thermiques.
Applications courantes des pièces moulées sous pression en aluminium
- Blocs moteurs, boîtiers de transmission, roues, etc. (pièces automobiles).
- Composants aérospatiaux (cadres d'avions, supports).
- L'électronique grand public (boîtiers de smartphones, boîtiers d'ordinateurs portables).
L'aluminium est normalement coulé sous pression en chambre froide en raison de son point de fusion élevé.
2. Zinc
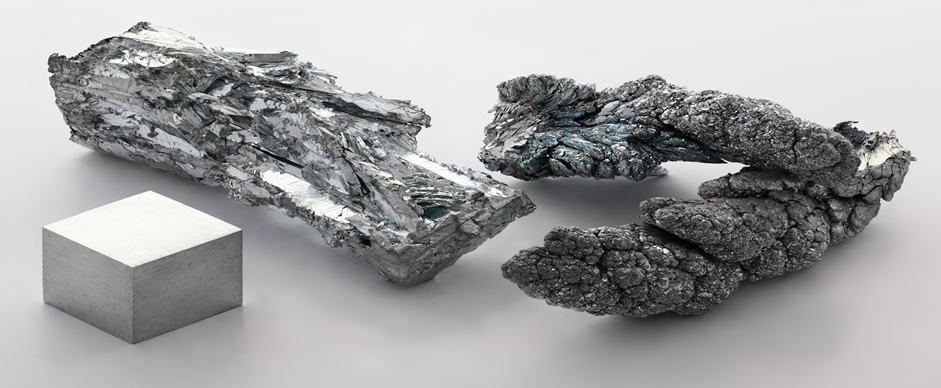
Le zinc est un autre métal de moulage sous pression populaire, connu pour sa haute précision, sa résistance et sa facilité de moulage. Cependant, le point de fusion du zinc étant plus bas que celui de l'aluminium, il est bien adapté au moulage sous pression en chambre chaude et permet d'obtenir des cycles de production plus rapides.
Avantages du zinc dans le moulage sous pression
- Haute résistance et durabilité - Idéal pour les composants mécaniques.
- Point de fusion bas - Permet une production plus rapide et une durée de vie plus longue des moules.
- Bon état de surface - Réduit la nécessité d'un traitement ultérieur approfondi.
Applications courantes des pièces moulées sous pression en zinc
- Petits composants mécaniques (engrenages, attaches, charnières).
- Connecteurs électriques et électroniques.
- Comprend des éléments supplémentaires tels que pièces automobiles (supports, poignées, serrures de porte).
En outre, le zinc est moins cher que l'aluminium, ce qui en fait le matériau de prédilection pour la production de petites pièces.
3. Magnésium
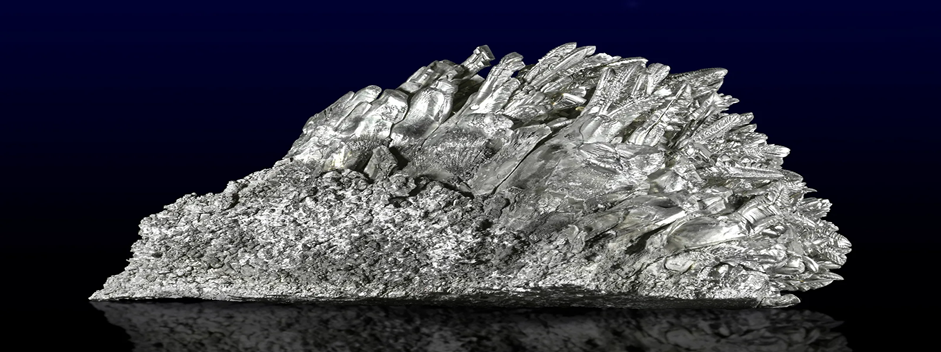
En tant que métal structurel pour le moulage sous pression, le magnésium est le métal le plus léger utilisé et offre un rapport résistance/poids exceptionnel. Il pèse environ 30% de moins que l'aluminium, ce qui en fait une bonne option pour les applications qui exigent une réduction du poids.
Avantages du magnésium dans le moulage sous pression
- Extrêmement léger - Idéal pour les applications aérospatiales et automobiles.
- Bonne solidité et résistance aux chocs - Peut supporter des contraintes mécaniques.
- Il est très facile à travailler (usinabilité) par rapport aux autres métaux.
Applications courantes des pièces moulées sous pression en magnésium
- Il est utilisé dans l'industrie automobile (volants, tableaux de bord).
- Industrie aérospatiale (drones et pièces détachées d'aéronefs).
- Électronique grand public (ordinateurs portables et appareils photo).
Bien que la forme en poudre du magnésium soit assez facilement inflammable, les pièces moulées sous pression sont suffisamment stables et sûres pour une utilisation industrielle.
4. Cuivre et alliages de cuivre (laiton et bronze)

Il possède une conductivité thermique et électrique élevée, ce qui explique que le cuivre et ses alliages (laiton, bronze) soient utilisés pour des applications électriques et de plomberie. Bien que leur prix soit plus élevé et qu'ils soient plus lourds que le zinc et l'aluminium, ils présentent une meilleure résistance à la corrosion et à l'usure.
Avantages du cuivre et de ses alliages pour le moulage sous pression
- Excellente conductivité électrique - Utilisé dans les composants électroniques et électriques.
- Il est résistant à la corrosion et convient parfaitement aux applications de plomberie et aux applications marines.
- Résistance supérieure à l'usure - Assure une plus grande longévité des pièces.
Applications courantes des pièces moulées sous pression en cuivre et en alliage de cuivre
- Connecteurs et bornes électriques.
- Raccords et vannes de plomberie.
- Composants de machines industrielles.
Même si le cuivre n'est généralement pas utilisé autant que l'aluminium ou le zinc dans le moulage sous pression, il reste crucial dans ces applications spécialisées où une durabilité et une conductivité élevées sont nécessaires.
5. Également le plomb et l'étain (pas très courants aujourd'hui)

Pour les applications spécialisées, le moulage sous pression du plomb et de l'étain était autrefois très répandu en raison de leur faible point de fusion et de leur excellente résistance à la corrosion. Néanmoins, leur utilisation a considérablement diminué ces dernières années pour des raisons de santé et d'environnement.
Avantages du plomb et de l'étain dans le moulage sous pression (historiquement)
- La résistance à la corrosion est bonne - Il est utilisé dans la plomberie et les composants de batteries.
- Souple et malléable - Convient aux applications à faible contrainte.
- Ils ont une densité élevée ; c'est pourquoi ils sont utilisés dans les applications de protection contre les radiations et d'insonorisation.
Applications courantes des pièces moulées sous pression en plomb et en étain (désormais limitées)
- Bornes de batterie.
- Roulements et pièces à souder.
- Composants de blindage en radioprotection.
Les réglementations environnementales étant de plus en plus strictes, les fabricants doivent trouver des matériaux plus sûrs, tels que l'aluminium, le zinc et le magnésium.
Avantages et inconvénients
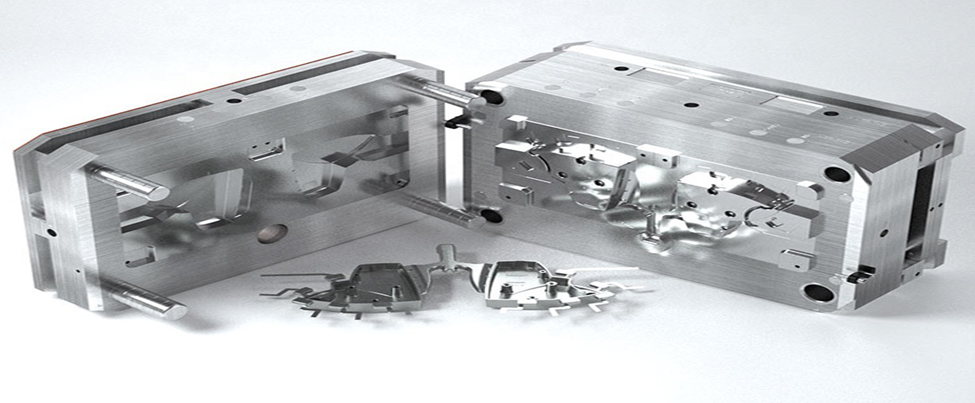
Avantages de la coulée
- Faible prix de production - Le moulage est une méthode de fabrication rentable, en particulier pour les petites séries, car il nécessite peu d'outillage (outil et matrice) par rapport à d'autres procédés de fabrication.
- Possibilité de réaliser des formes complexes ou de grande taille - Le moulage permet de créer des formes difficiles à traiter sur un tour ou par usinage, ou trop grandes pour être manipulées.
- Permet de couler une grande variété de matériaux - avec du fer, de l'acier, du bronze d'aluminium, etc.
- Utilisation efficace des matériaux - Le moulage ne gaspille pas de matériaux car le métal en fusion est versé directement dans les moules et il ne perd pas beaucoup de matériaux excédentaires.
- Production de masse adaptée - Une fois le moule établi, il est possible de produire relativement facilement un grand nombre de pièces identiques.
Inconvénients de la coulée
- Moins précis que le moulage sous pression. Les méthodes de moulage traditionnelles ont tendance à produire des imperfections de surface et des variations dimensionnelles qui doivent encore être usinées.
- Les temps de refroidissement plus longs et le processus de refroidissement et de solidification peuvent affecter l'efficacité globale de la production.
- Plus de travail de finition nécessaire - Les pièces moulées présentent une surface rugueuse ou un excès de matière (bavure) qui doit être éliminé par des opérations d'usinage telles que le meulage et le polissage.
- Problèmes de porosité - Il peut s'agir d'un problème de poches d'air ou de vides résultant du processus de moulage et créant des faiblesses dans l'intégrité structurelle.
- Dégradation des moules - L'utilisation de moules réutilisables entraîne, avec le temps, la dégradation de ces moules et l'augmentation de l'épaisseur de la paroi des pièces, ce qui entraîne des défauts de production et une augmentation des coûts de maintenance.
Avantages de la coulée sous pression
- Le moulage sous pression permet à la fois des productions à grande vitesse, convenant à des séries de production à haut volume, et des lots à faible production.
- Création de pièces solides et de dimensions précises - Grâce au processus d'injection à haute pression, les pièces sont produites de manière cohérente, avec des tolérances serrées et une bonne qualité, ce qui minimise les ajustements ultérieurs.
- Peu de post-traitement - Les pièces moulées sous pression présentent généralement des surfaces lisses et des détails nets qui ne nécessitent pas d'usinage secondaire.
- Le moulage sous pression est excellent en termes de répétabilité, ce qui permet d'obtenir une production uniforme au cours de nombreux cycles de production, raison pour laquelle il s'agit d'une méthode privilégiée pour la production de masse.
- Bonne finition de la surface - Il ne nécessite aucune finition, ce qui le rend très approprié pour la fabrication de produits qui tiennent compte de l'esthétique.
Inconvénients du moulage sous pression
- Coût initial plus élevé (les moules sont chers) - La conception et la fabrication des moules de coulée sous pression peuvent être coûteuses et ne sont donc pas rentables si la production est à petite échelle.
- Ne convient pas aux métaux ferreux - Le moulage sous pression est figé à l'aluminium, au zinc et au magnésium, ce qui limite la gamme des matériaux possibles.
- Ne convient pas aux pièces grandes ou épaisses - Les pièces à parois minces conviennent mieux au moulage sous pression que les pièces massives ou à parois épaisses. Le moulage sous pression implique un processus de refroidissement rapide.
- Porosité - Il est possible que le produit se soit rempli d'air pendant le processus de moulage par injection, ce qui entraînera une porosité qui rendra le produit final fragile.
- Moins de flexibilité dans les modifications de conception - Après la fabrication d'une matrice, les modifications de conception des pièces moulées seront coûteuses et prendront du temps par rapport à d'autres méthodes de moulage.
8. L'avenir du moulage et de la coulée sous pression
Le moulage et le moulage sous pression sont prometteurs pour l'avenir (du moins à court terme) en raison de l'automatisation et de l'impression 3D. Voici quelques tendances clés :
- Matériaux écologiques - Alliages durables et recyclables.
- Fabrication intelligente - Automatisation pilotée par l'IA pour plus d'efficacité.
- Intégration de la fabrication additive sous la forme de processus hybrides de moulage et d'impression 3D.
Dans les industries modernes, ces innovations amélioreront la productivité, réduiront les déchets et diminueront les coûts de production, rendant ainsi les processus de production encore plus indispensables.
Conclusion
Dans différents secteurs, le processus de fabrication de composants métalliques de haute qualité reste l'un des principaux processus de fabrication. Les options de moulage sous pression se déclinent en de nombreuses variantes, chacune offrant des avantages différents pour des applications spécifiques. Le moulage sous pression par gravité permet de produire des pièces solides et denses, tandis que le moulage sous basse pression permet d'obtenir des pièces structurellement saines avec un minimum de défauts. Le moulage sous pression offre une résistance et une durabilité remarquables, tandis que le moulage sous vide permet de réduire la porosité. Le choix de la méthode de moulage sous pression dépend de la sélection des matériaux, de la complexité de la pièce, du volume de la pièce et du type de propriétés mécaniques souhaitées. Le choix de la méthode de moulage sous pression dépend de la sélection des matériaux, de la complexité de la pièce, du volume de la pièce et du type de propriétés mécaniques souhaitées.
En raison de la demande de composants plus légers, plus solides et plus résistants de la part des industries, la technologie évoluera continuellement. Cependant, les fabricants peuvent éviter les mauvaises performances des produits, les déchets et l'inefficacité de la production en choisissant la méthode de moulage sous pression appropriée. Pour choisir la meilleure option de fabrication, il est nécessaire de comprendre ces variantes de moulage sous pression et d'obtenir la meilleure qualité, fiabilité et efficacité de production.
Foire aux questions (FAQ)
1. Comment fonctionne le moulage sous pression et sous quelle forme ?
Le moulage des métaux par le procédé connu sous le nom de moulage sous pression est un procédé dans lequel le métal en fusion est injecté dans un moule sous haute pression. Ce procédé permet aux fabricants de produire des pièces métalliques complexes et de haute précision avec un superbe état de surface et très peu d'usinage.
2. Combien y a-t-il de types de moulage sous pression ?
Les principales formes de moulage sous pression sont le moulage par gravité (GDC), le moulage sous basse pression (LPDC), le moulage par compression, le moulage sous vide et le moulage semi-solide. Les avantages et les inconvénients de chaque méthode dépendent du matériau et de l'application.
3. Quels sont les métaux normalement utilisés dans le processus de moulage sous pression ?
L'aluminium, le zinc, le magnésium, le cuivre et leurs alliages sont les métaux les plus couramment utilisés dans le moulage sous pression. Le métal est choisi en fonction de son poids, de sa solidité, de sa résistance à la corrosion et de sa conductivité thermique.
4. Pourquoi le moulage sous pression est-il si avantageux ?
Rendement de production élevé, excellente précision dimensionnelle, perte minimale de matériau, finition de surface lisse et possibilité de produire des formes complexes avec peu de post-traitement.