Le moulage sous haute pression (HPDC) est l'un des procédés de moulage de métaux les plus utilisés dans la fabrication actuelle. Les fabricants choisissent le HPDC parce qu'il permet de produire des pièces métalliques complexes qui atteignent à la fois une grande précision et des taux de production rapides, une précision dimensionnelle supérieure et des finitions lisses. Le HPDC permet aux industries automobile et aérospatiale, ainsi qu'à la production de composants électroniques et de biens de consommation, de fabriquer des pièces durables et légères pour des applications telles que les moteurs et les boîtiers, les éléments structurels et les assemblages mécaniques. Le processus de fabrication du moulage sous haute pression comporte de nombreux risques qui créent des défauts substantiels qui diminuent la qualité du produit tout en raccourcissant sa durée de vie et en compromettant ses performances. Ces défauts sont dus à une mauvaise conception du moule, à un écoulement turbulent du métal en fusion, à des gaz piégés, à des vitesses de refroidissement incohérentes et à des contraintes thermiques au cours du processus de production. La technologie HPDC rencontre sept défauts principaux : la porosité, les fermetures à froid, les défauts de rétrécissement, la formation de bavures, les défauts de surface, les ratés, l'érosion de la matrice et le brasage. Ces types de défauts de fabrication entraînent une détérioration de la résistance du matériau tout en produisant des dimensions irrégulières et des effets visuels indésirables qui peuvent provoquer une panne du composant. Les fabricants combattent les problèmes de production en optimisant les paramètres de traitement et en améliorant les méthodes de minage, ainsi que les systèmes de température contrôlée et les procédures de coulée sous vide. La surveillance en temps réel et les logiciels de simulation sont des méthodes avancées de contrôle de la qualité qui renforcent l'efficacité et la fiabilité du processus de moulage sous pression.
Cet article propose une analyse complète des problèmes de fabrication standard lors de l'utilisation d'appareils à haute pression. moulage sous pression Les fabricants de pièces moulées sous pression peuvent également utiliser la technologie de l'emballage avec des explications sur les causes profondes et des stratégies de solution pour réduire ces défauts. Ce n'est qu'en comprenant ces défis et en appliquant les meilleures pratiques que les fabricants peuvent améliorer la qualité, la longévité et, bien sûr, la performance de leurs composants moulés sous pression, tout en réduisant les déchets et les coûts de production. La maîtrise de ces défauts de fabrication aidera les ingénieurs en moulage sous pression, les directeurs de production et les spécialistes du contrôle de la qualité à optimiser leurs processus pour obtenir les meilleurs résultats en matière de moulage sous pression.
1. La porosité
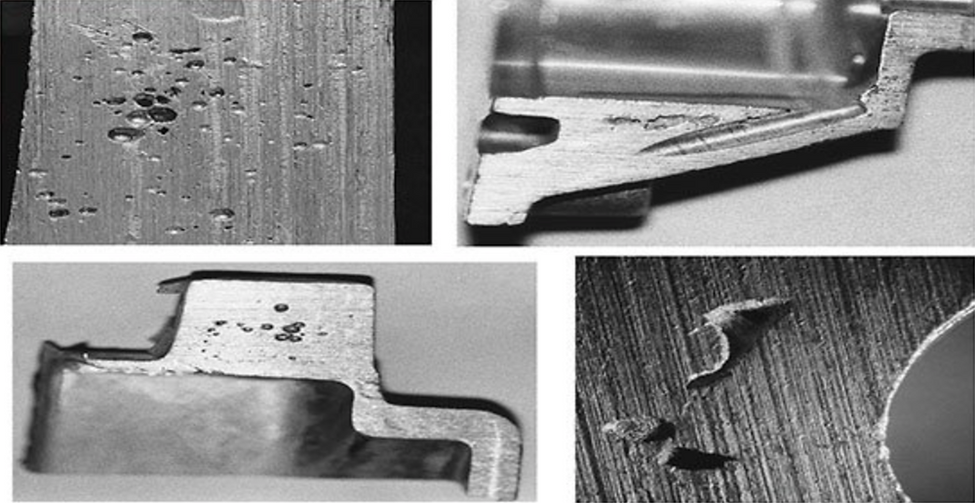
La porosité est définie par de petits trous ou des inclusions de gaz dans la matrice métallique, ce qui affecte les propriétés mécaniques, diminue la résistance, permet à l'air et aux gaz de passer à travers la structure et entraîne des défauts de surface visibles dans les produits moulés sous pression.
Les causes :
- Contenu gazeux présent dans les matériaux avant la coulée.
- Turbulences excessives dans le flux de métal en fusion.
- Mauvaise ventilation et mauvaise conception des moules.
- Solidification rapide qui provoque une porosité de retrait.
- Contamination du métal en fusion.
- Pression inadéquate qui ne permet pas un écoulement uniforme du métal.
Prévention et solutions :
- S'assurer qu'une bonne évacuation des gaz a été réalisée grâce à la conception des portes et des évents.
- Ralentir la vitesse d'injection pour améliorer la fluidité du métal entrant dans la cavité.
- Le problème de l'emprisonnement de l'air devrait être résolu par la technique de moulage sous pression assistée par le vide.
- Assurez-vous que le métal en fusion est suffisamment dégazé avant d'être injecté.
- Contrôler la vitesse de refroidissement pour résoudre le problème des fissures et de la formation d'autres défauts de solidification.
- Vérifiez et nettoyez souvent les surfaces des filières afin de réduire les risques de porosité dus aux contaminants.
2. Fermeture à froid
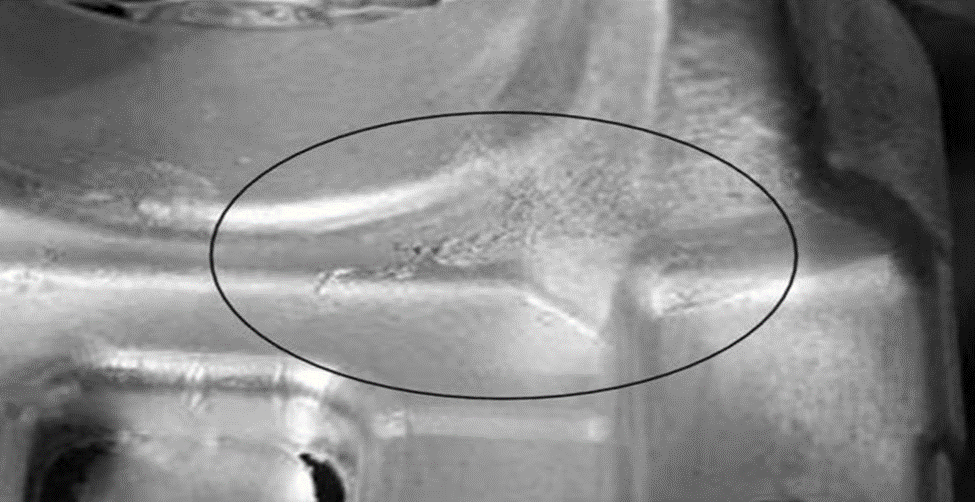
Une soudure à froid est créée lorsque deux flux de métal en fusion ne fusionnent pas correctement et forment des zones de liaison faibles ou des coutures visibles dans la pièce moulée. Ce défaut ne diminue pas seulement la résistance mécanique, mais augmente également le risque de fracture, tout en affectant négativement la durabilité et l'apparence du composant.
Les causes :
- Faible température du métal en fusion.
- Il est caractérisé par une vitesse d'injection lente, qui conduit généralement à une solidification prématurée.
- Mauvaise conception du moule avec des canaux d'écoulement insuffisants.
- Elle peut provoquer une oxydation excessive qui forme des films de surface empêchant une bonne fusion.
- Flux de métal incohérent en raison d'une mauvaise conception du système d'injection.
Prévention et solutions :
- De plus, la température optimale de coulée du métal doit être maintenue pour assurer une bonne fluidité.
- Augmenter la vitesse d'injection pour compléter le remplissage et obtenir une seule pièce.
- Éliminer les obstacles inutiles à l'écoulement lors de la conception du moule afin que le métal puisse se déplacer sans difficulté.
- Détection et résolution des problèmes d'écoulement avant la production à l'aide d'outils d'analyse thermique.
- Des techniques d'aération appropriées doivent être appliquées pour éviter le piégeage de l'air qui aggrave souvent les défauts de fermeture à froid.
3. Défauts de rétraction
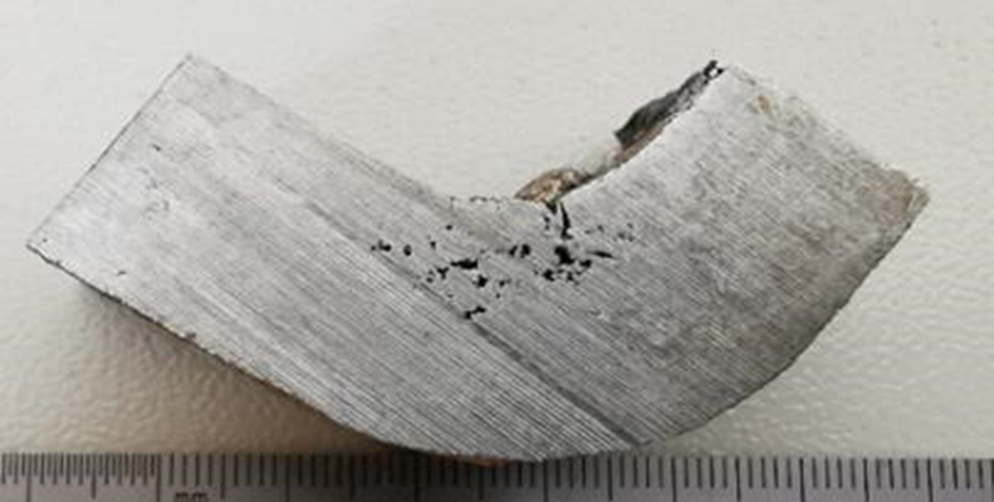
Les défauts de retrait sont dus à la contraction du métal pendant le refroidissement, ce qui entraîne la formation de vides ou de cavités internes qui détériorent l'intégrité structurelle de la pièce moulée. En conséquence, ces défauts réduisent la résistance mécanique du produit final, provoquent des défaillances potentielles sous l'effet de la contrainte et entraînent une mauvaise qualité de surface, ce qui affecte à la fois la fonctionnalité et l'esthétique des produits finaux.
Les causes :
- Alimentation inadéquate en métal pendant la solidification
- Les taux de refroidissement sont inégaux en raison d'une mauvaise conception de la matrice.
- Retrait élevé du métal en raison de la composition de l'alliage
- Refroidissement rapide provoquant une contraction localisée
- Pression insuffisante pendant la phase de solidification
Prévention et solutions :
- Modifier le moule pour obtenir un refroidissement uniforme et une alimentation correcte du métal en fusion.
- Utiliser des alliages ayant une tendance à la contraction plus faible et de meilleures propriétés de solidification.
- Il est utilisé pour optimiser les réglages de pression pendant la solidification afin de remplir et de minimiser les vides de retrait.
- Utiliser des méthodes de refroidissement contrôlées pour équilibrer les taux de solidification et réduire la contrainte thermique.
- Mettre en œuvre des outils de surveillance et de simulation en temps réel pour prévoir et prévenir les défauts de rétrécissement.
4. Formation de l'éclair

Les fines couches de métal excédentaires formées au niveau du plan de joint ou de l'interstice de la matrice en raison de l'échappement du métal sous haute pression sont appelées "bavures". Bien que la bavure puisse être éliminée après la coulée, l'excès de bavure entraîne une augmentation des déchets de matériaux, de l'usure des outils et des coûts de production associés, ce qui réduit l'efficacité globale du processus de coulée sous pression.
Les causes :
- La pression d'injection excessive fait que le métal en fusion est forcé dans les interstices de la matrice.
- Filière usée ou due à un mauvais verrouillage de la filière permettant des fuites.
- Lorsque la force de serrage est insuffisante, ce qui entraîne une séparation de la matrice pendant l'injection.
- Ils seront mal posés et présenteront des interstices permettant au métal de s'échapper.
- Contrôle imprécis du flux de métal par la lubrification de la matrice
Prévention et solutions :
- Une force de serrage adéquate doit être maintenue pour éviter la séparation de la matrice et la formation de bavures.
- Inspecter et remplacer régulièrement les matrices usées afin d'assurer une bonne étanchéité.
- Veillez à ce que la pression soit réglée de manière optimale afin que le remplissage se fasse avec un minimum de flash.
- Le réalignement des filières doit être amélioré pour éviter les écarts involontaires et les fuites de métal.
- Utiliser des techniques précises de lubrification des matrices pour contrôler le flux de métal et réduire les fuites excessives de métal.
5. Inspection des défauts de surface (cloques, fissures et rides)

Divers défauts de surface, cloques, fissures et rides, dégradent l'aspect visuel et la résistance mécanique de la pièce moulée et doivent être évités et éliminés. Ils provoquent des défauts de soudure qui réduisent la durabilité du produit, augmentent le taux de rejet et rendent le produit peu adhérent après les traitements post-coulée tels que la peinture ou le revêtement.
Les causes :
- L'air emprisonné dans le plastique liquide lors de la coulée.
- Il existe également des contraintes thermiques et des irrégularités de surface dues à des vitesses de refroidissement non uniformes.
- Surchauffe ou température mal contrôlée pendant la solidification.
- Ou les impuretés ou inclusions métalliques susceptibles d'affecter la surface de coulée
- Une mauvaise lubrification de la matrice entraînait un écoulement irrégulier du métal et des imperfections de surface.
Prévention et solutions :
- Dégazage correct du métal en fusion pour éviter les gaz piégés avant la coulée.
- Contrôler la solidification et éviter les contraintes thermiques en utilisant des techniques de refroidissement uniforme.
- Le contrôle de la température des moules doit être optimisé pour éviter la surchauffe et un refroidissement inégal.
- Créer un contrôle strict de sa qualité qui lui permettra de détecter toutes les impuretés avant la coulée.
- Appliquer des revêtements et des lubrifiants pour les matrices en fonction de la qualité de la surface et de la réduction des défauts.
6. Inclusions et contamination
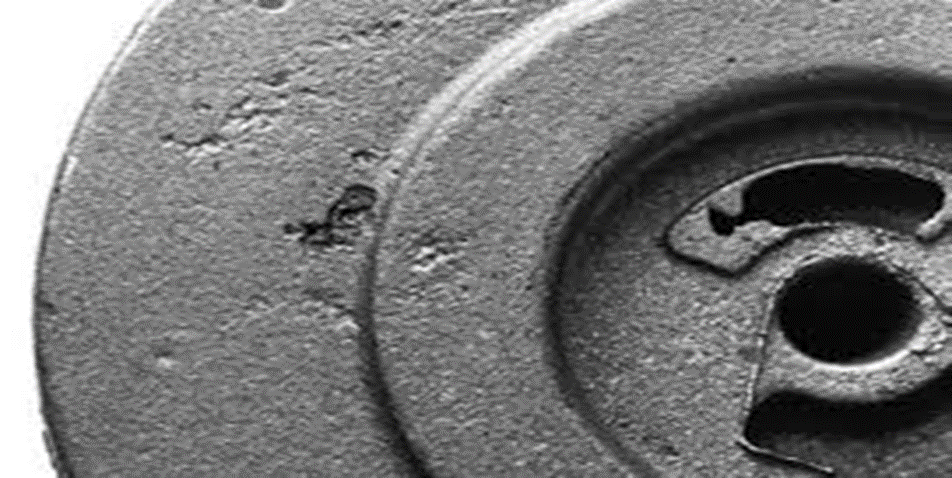
Les particules étrangères indésirables, telles que le laitier, les films d'oxyde, la saleté ou d'autres impuretés, qui sont piégées dans un moulage final, créent de mauvaises propriétés mécaniques, une faible intégrité structurelle et des défauts de surface et sont appelées inclusions. La présence de ces contaminants peut réduire les performances et la durabilité des composants moulés sous pression, de sorte qu'ils ne conviennent pas aux applications de haute précision.
Les causes :
- Par exemple, les matières premières contaminées sont constituées d'impuretés indésirables.
- Les particules étrangères présentes dans le métal en fusion ne peuvent pas être filtrées de manière satisfaisante en raison de l'absence d'un système de filtrage.
- En raison d'une exposition prolongée à l'air pendant la fusion ou le coulage du métal
- Inclut des pratiques inefficaces de manipulation des métaux qui entraînent à leur tour une formation accrue de scories.
- Une lubrification insuffisante de la filière comprend l'introduction d'un corps étranger dans le métal en fusion.
Prévention et solutions :
- Les matières premières de haute qualité doivent être raffinées correctement et sans contaminants.
- Mettre en place des systèmes de filtration efficaces pour éliminer les scories, les oxydes et autres impuretés du métal en fusion avant l'injection.
- Contrôler la manipulation des métaux en fusion et, le cas échéant, utiliser des gaz inertes pour limiter l'oxydation.
- Nettoyer et entretenir régulièrement les équipements de coulée afin d'éviter la contamination par des matières résiduelles.
- Utilisez une lubrification appropriée de la matrice pour éviter toute accumulation de matériaux étrangers dans la cavité du moule.
7. Fautes de parcours et remplissage incomplet
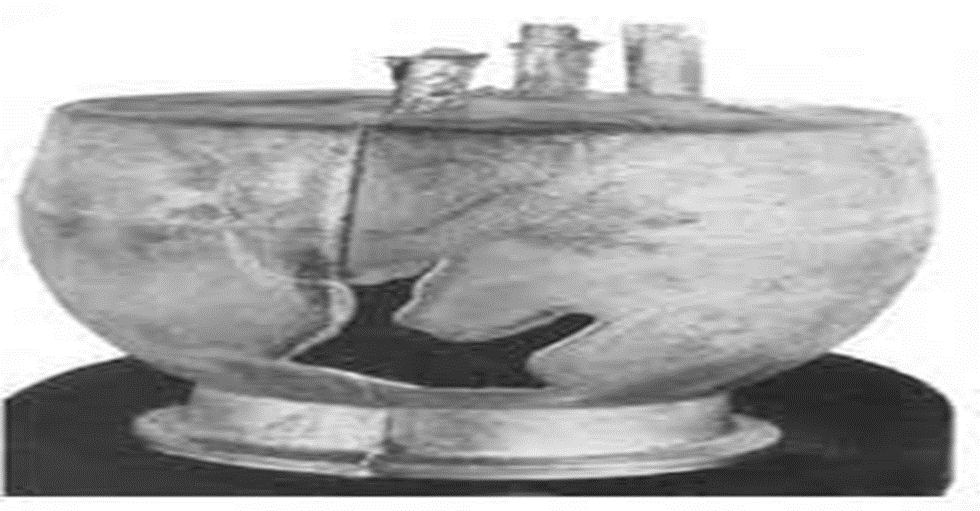
Un faux-rond se produit lorsque la cavité du moule n'est pas suffisamment remplie, ce qui entraîne des sections manquantes, des parois minces et des points faibles dans le composant final. Cela a des effets négatifs sur l'intégrité structurelle et la fonctionnalité de la pièce, qui n'est donc pas adaptée à des applications performantes.
Les causes :
- En cas de vitesse ou de pression d'injection faible, le moule n'est pas entièrement recouvert.
- Surfaces d'outils froides empêchant l'écoulement du métal et une solidification prématurée
- Provoque un volume de métal fondu inadéquat, ce qui entraîne un remplissage insuffisant de la cavité.
- Une mauvaise conception de l'entrée et de la sortie, qui entraîne une distribution inégale du métal en fusion.
- Des turbulences excessives produisent des poches d'air qui bloquent le flux de métal.
Prévention et solutions :
- Augmenter la température du métal pour qu'il puisse s'écouler et éviter une solidification prématurée.
- En outre, le remplissage de la cavité doit être optimisé en réglant correctement la pression et la vitesse d'injection.
- Maintenir la température de travail des matrices et éviter qu'elles ne refroidissent prématurément.
- Amélioration de la conception de la grille et de la glissière pour favoriser une distribution homogène et régulière du métal.
- Simuler le flux de métal et les risques de ratés à l'aide d'un logiciel de simulation avant la production.
8. Érosion et usure des matrices
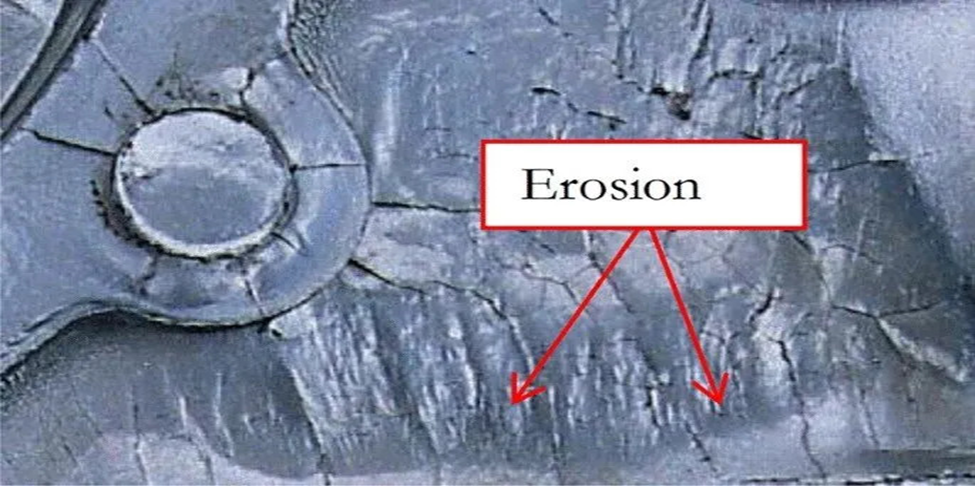
L'usure des matrices d'érosion en fusion est la perte des surfaces du moule due à l'usure continue par le métal à haute vitesse des surfaces de la pièce moulée jusqu'à ce que les dimensions requises soient atteintes, ce qui entraîne un mauvais état de surface et une courte durée de vie de l'outil de moulage. Si ce défaut se produit, le remplacement des moules est courant et, par conséquent, les coûts de production augmentent tandis que la qualité de la coulée varie.
Les causes :
- Il est également exposé de manière répétée à du métal en fusion à haute température, ce qui entraîne une usure progressive.
- Matériaux de matrices de qualité relativement médiocre, présentant une mauvaise résistance aux contraintes thermiques et mécaniques
- Des cycles thermiques excessifs peuvent provoquer des fissures dans le matériau en raison de la fatigue.
- Ce qui entraîne une dégradation du matériau de la filière sous forte injection.
- Peu de lubrification ? Plus de friction et plus d'usure.
Prévention et solutions :
- L'une d'entre elles consiste à utiliser des matrices de haute qualité résistantes à la chaleur et plus durables.
- Des revêtements de surface protecteurs, tels que la nitruration ou les revêtements céramiques, peuvent être appliqués pour prolonger la durée de vie des matrices.
- Des méthodes de refroidissement contrôlé visant à réduire les contraintes thermiques et à induire une usure prématurée doivent être mises en œuvre.
- Trouver un équilibre entre la vitesse et la pression avec un minimum de contraintes sur la matrice.
- Inspectez régulièrement les matrices et entretenez-les afin de détecter et de traiter l'érosion dès que possible.
9. Fissuration à chaud
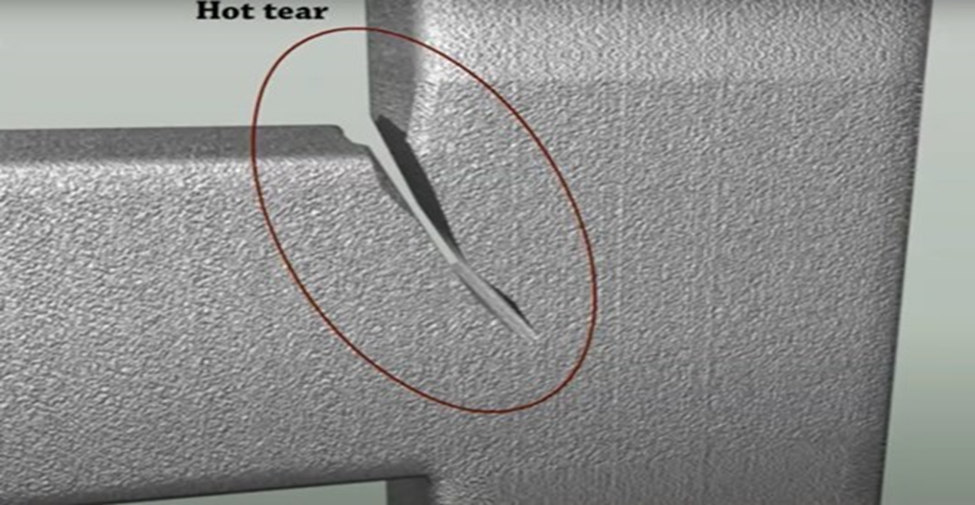
Les fissures qui se produisent à l'état semi-solide du métal, en raison d'une forte contrainte thermique et d'un retrait excessif, sont connues sous le nom de fissures à chaud. Ces fissures dégradent l'intégrité mécanique de la pièce moulée, c'est-à-dire qu'elles augmentent le risque de défaillance de la pièce moulée à l'endroit où les fissures sont présentes sous l'effet d'une contrainte ou d'une charge.
Les causes :
- Des taux de refroidissement peu fiables dans le moule, entraînant des points de tension dans des zones spécifiques.
- Il est très sensible aux contraintes thermiques et aux fissures dans la composition de l'alliage.
- Elle provoque également des contraintes résiduelles excessives formées lors de la solidification rapide et une restriction de la contraction du métal.
- Si la conception du moule est mauvaise, il y aura des variations de température dans la coulée.
- La pression pendant la solidification était trop faible pour empêcher la propagation des fissures.
Prévention et solutions :
- Il s'agira également d'optimiser les taux de refroidissement afin d'obtenir une solidification uniforme et de minimiser les contraintes thermiques.
- Augmenter la résistance à la fissuration des alliages par l'utilisation appropriée d'alliages ayant une meilleure structure de grain.
- Utilisation de techniques de réduction des contraintes après la coulée, c'est-à-dire un traitement thermique contrôlé.
- Concevoir des moules avec un différentiel de température moindre.
- Assurer une pression adéquate pendant la solidification du métal afin qu'il s'écoule et qu'il n'y ait pas de fissures.
10. Soudure
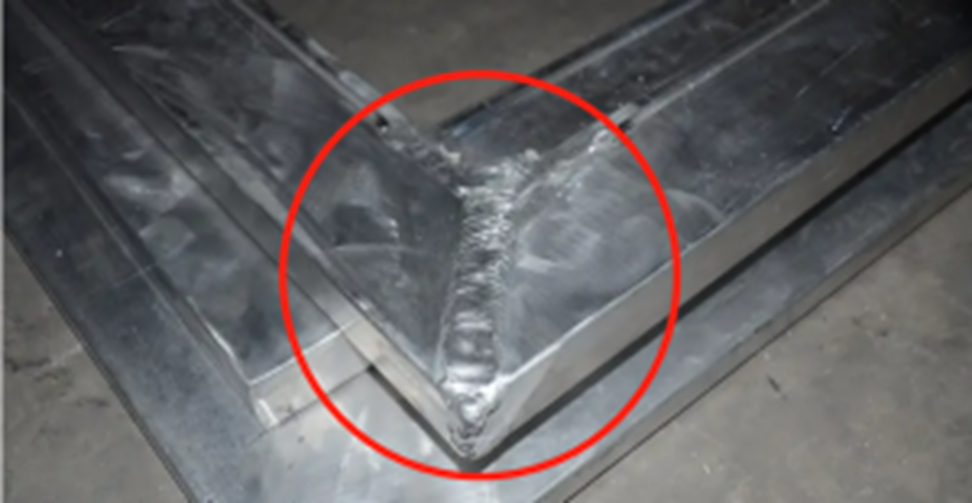
Le métal en fusion adhère à la surface de la matrice, ce qui est difficile à enlever avec la coulée, et provoque des défauts de surface, l'usure de la matrice ainsi que des temps d'arrêt de production prolongés. Les imprécisions dimensionnelles et la mauvaise finition de la surface sont également causées par ce défaut, qui compromet la qualité globale du produit final.
Les causes :
- Augmentation de l'adhérence du métal dans l'alliage en raison de sa haute teneur en aluminium
- Température excessivement élevée de la matrice, afin que le métal adhère à la surface de la matrice.
- Protection insuffisante contre le collage en raison d'une mauvaise lubrification de la matrice
- Un refroidissement insuffisant fait que le métal en fusion reste trop longtemps en contact avec la filière. Les surfaces supérieures de la filière sont écaillées ou endommagées, ce qui favorise l'adhérence du métal.
Prévention et solutions :
- Des lubrifiants de haute qualité sont toujours appliqués pour éviter le collage du métal.
- Il permet de contrôler la température de la matrice dans la plage optimale si l'adhérence à chaud est trop forte.
- Réduire l'adhérence du métal en utilisant des revêtements de matrice appropriés, par exemple des couches de céramique ou de nitrure.
- Réduire le temps de contact entre le métal et la pièce et améliorer l'efficacité du système de refroidissement.
- Inspecter et polir régulièrement les surfaces des matrices afin d'obtenir une finition de surface lisse et non adhésive.
Conclusion
La haute pression moulage sous pression est un processus de fabrication puissant qui permet de créer des pièces métalliques complexes avec une grande précision et une efficacité maximale. Cependant, différents types de défauts apparaissent en raison de paramètres de processus inappropriés, de problèmes de matériaux et/ou de défauts de conception des moules. Les fabricants peuvent prendre des mesures préventives, par exemple un contrôle optimal du processus de moulage, une sélection appropriée des matériaux, etc., après avoir compris ces défauts de fabrication habituels.
Une entreprise peut améliorer la qualité de ses produits, réduire ses coûts de production et accroître l'efficacité de ses opérations de moulage sous pression en mettant l'accent sur l'amélioration continue des processus et sur les stratégies de prévention des défauts.
Foire aux questions (FAQ)
1. Quelles sont les principales raisons des défauts dans le moulage sous pression ?
Les principales causes de défauts dans le moulage sous pression sont une mauvaise conception du moule, un mauvais écoulement du métal, des gaz piégés, une contrainte thermique élevée, un refroidissement inégal et des matières premières contaminées. Ces défauts peuvent être réduits grâce à l'optimisation des paramètres du processus et à l'utilisation de mesures de contrôle de la qualité.
2. Quel est le rôle de la porosité dans la performance des composants moulés sous pression ?
La présence de porosité affaiblit l'intégrité structurelle des composants moulés sous pression, diminuant la résistance et provoquant des fuites d'air dans les composants étanches à la pression ainsi que des imperfections anesthésiques. La porosité peut être minimisée en utilisant un dégazage approprié, des systèmes d'ouverture optimisés et une coulée assistée par le vide.
3. Comment éviter les fermetures à froid dans le moulage sous pression ?
Une température de coulée correcte, des vitesses d'injection plus élevées, une conception optimisée du moule pour faciliter l'écoulement du métal et l'application d'outils d'analyse thermique pour identifier d'éventuels problèmes d'écoulement peuvent contribuer à éviter les fermetures à froid.
4. L'érosion des moules est une préoccupation importante dans le domaine du moulage sous pression, car ?
L'exposition répétée du métal en fusion à haute température aux moules provoque l'érosion des moules, ce qui raccourcit leur durée de vie et diminue la précision des pièces moulées. La durée de vie des moules peut être prolongée par l'utilisation de matériaux de haute qualité, de revêtements protecteurs et d'un refroidissement contrôlé des moules.
5. Qu'est-ce qui améliore la qualité et la régularité des produits moulés sous pression ?
Un contrôle strict de la qualité, l'optimisation des paramètres du processus, le contrôle de la température des moules, l'utilisation d'alliages de haute qualité et l'inspection des moules et des machines sont effectués périodiquement pour améliorer constamment la qualité des produits moulés sous pression.