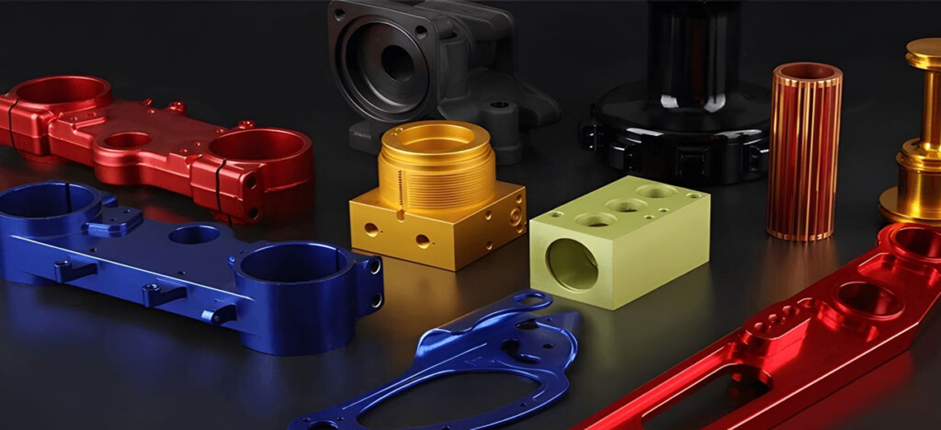
Anodisé matériau en aluminium est utilisé principalement parce qu'il est léger, solide et résistant à la corrosion. Bien que l'aluminium brut offre une certaine durabilité et une résistance aux rayures, il est sujet à l'oxydation, aux bosses et aux rayures, ce qui peut l'altérer à long terme et lui conserver son aspect d'origine. Pour rendre l'aluminium plus solide et plus durable, il est ensuite anodisé afin de former une couche d'oxyde protectrice sur sa surface. Cette couche durcit le métal et lui confère une surface plus résistante à la corrosion et à l'usure, ainsi qu'un aspect plus agréable. L'aluminium anodisé est préféré en raison de ces facteurs et est largement utilisé dans l'aérospatiale, automobile, l'industrie de la construction et de l'électronique grand public. L'anodisation consiste en plusieurs étapes : nettoyage de la surface, immersion dans un bain d'électrolyte, oxydation à l'aide d'un courant électrique et scellement. En plus de rendre le matériau plus résistant, ce traitement peut être coloré dans différentes teintes et finitions. La coloration électrolytique, la coloration par immersion, la coloration intégrale et la coloration par interférence sont des techniques de coloration courantes.
L'anodisation ordinaire et l'anodisation dure sont les deux principaux types d'anodisation. Il existe généralement deux procédés : l'anodisation ordinaire, utilisée principalement pour la finition et les applications de faible poids, et l'anodisation dure, qui offre une excellente durabilité, une bonne résistance à l'usure et une grande solidité pour les applications militaires, industrielles et aérospatiales. Outre l'anodisation, l'aluminium peut faire l'objet d'autres traitements de surface tels que la galvanisation, le revêtement par poudre, le revêtement par conversion au chromate, le revêtement PVD, les revêtements céramiques ou la galvanisation par immersion à chaud. L'aluminium anodisé ne possède pas ces propriétés de manière uniforme et est donc utilisé comme un matériau polyvalent et fiable dans de nombreuses industries, chaque méthode conférant au matériau des propriétés améliorées spécifiques - résistance à la corrosion, dureté, conductivité, etc.
Dans cet article, nous examinerons les propriétés, les avantages, les applications et l'entretien de l'aluminium anodisé, et nous verrons pourquoi il s'agit d'une meilleure alternative aux autres métaux et traitements. Si nous connaissons ces aspects, nous pouvons comprendre quel matériau utiliser pour une industrie particulière et pour le consommateur.
Qu'est-ce que l'aluminium anodisé ?

L'aluminium anodisé est un aluminium soumis à un processus électrochimique visant à produire une couche d'oxyde plus épaisse et plus durable sur sa surface. La présence de cette couche d'oxyde anodique augmente la résistance du métal à la corrosion, améliore la dureté de la surface et accroît la capacité du métal à adhérer aux colorants et aux revêtements.
Le processus d'anodisation
En d'autres termes, le processus d'anodisation comprend plusieurs étapes clés.
- La surface de l'aluminium est nettoyée pour éliminer la saleté, la graisse ou les impuretés avant les étapes de séchage, de nettoyage et de prétraitement. La surface peut également être gravée pour obtenir une finition uniforme.
- Bain d'anodisation - L'aluminium est plongé dans une solution électrolytique (généralement de l'acide sulfurique) et une tension électrique est appliquée. Cela déclenche l'oxydation et forme la couche d'oxyde d'aluminium épaissie.
- La couche d'oxyde poreux peut être simultanément colorée (facultatif) par des colorants ou des pigments similaires, selon les besoins.
- Obturation des pores - L'obturation de la couche anodisée se fait à l'aide d'eau chaude ou de vapeur, ce qui permet d'obturer les pores et d'améliorer encore la résistance à la corrosion.
Matériau en aluminium anodisé Propriétés principales

1. Résistance accrue à la corrosion
L'aluminium anodisé est l'un des matériaux les plus résistants à la corrosion. Il est donc pratiquement inutilisable à l'extérieur ou lorsqu'il est immergé dans l'eau, car la couche d'oxyde protège le métal de l'humidité et de notre environnement.
2. Dureté accrue de la surface
L'anodisation améliore considérablement la dureté de l'aluminium, qui devient ainsi plus résistant aux rayures, aux bosses et à l'usure. L'aluminium anodisé dur est très durable et est utilisé dans des applications de haute performance.
3. Attrait esthétique et variété des couleurs
De plus, l'aluminium anodisé est disponible en noir, or, bronze, argent, etc. sans changer la texture naturelle du métal. C'est pourquoi il s'agit d'un choix privilégié pour les applications architecturales et décoratives.
4. Léger mais solide
Bien que la couche d'oxyde soit placée sur l'aluminium, cela ne rend pas l'aluminium beaucoup plus lourd, et il est toujours plus léger que des matériaux plus lourds tels que l'acier inoxydable.
5. Isolation électrique
L'aluminium anodisé étant un mauvais conducteur d'électricité par rapport à l'aluminium non traité, c'est un matériau intéressant à utiliser dans les applications où une isolation est nécessaire à des fins électriques ou électroniques.
6. Respect de l'environnement et développement durable
L'aluminium anodisé est totalement non toxique, recyclable et ne dégage pas de COV (composés organiques volatils) dangereux et nocifs pour la santé ; il est donc respectueux de l'environnement.
Comment ajouter de la couleur aux pièces en aluminium anodisé ?

L'anodisation de l'aluminium est bien connue pour sa capacité à conserver des couleurs très vives. La coloration électrolytique et la coloration par immersion sont deux des nombreuses techniques utilisées pour colorer l'aluminium anodisé.
1. Coloration électrolytique

La coloration électrolytique est un moyen populaire d'embellir l'aluminium anodisé. L'aluminium anodisé est alors coloré avec des teintes durables et résistantes aux UV. Une fois que l'aluminium a subi le processus d'anodisation, il est placé dans un bain contenant des sels métalliques. Ces dernières années, des sels métallisés ont été mis au point. Sous l'effet d'un courant électrique, ils se déposent dans les pores ouverts de la surface anodisée, créant ainsi de manière permanente une surface de couleur métallique.
Enfin, la couleur dépend du type de sels métalliques utilisés. Les sels de cuivre, par exemple, donnent à la solution un ton rougeâtre, et d'autres métaux peuvent lui donner d'autres teintes. Cette technique est largement utilisée parce que les couleurs obtenues de cette manière durent longtemps et ne se décolorent pas, ce qui la rend idéale pour les utilisations en extérieur ou en cas de forte exposition.
2. Coloration par immersion

Une autre méthode de coloration est la coloration par immersion, qui offre une grande variété de choix de couleurs. Au cours de ce type de traitement, la couche poreuse est immergée dans une solution de teinture où l'aluminium anodisé absorbe le pigment. Une fois la teinte obtenue, l'aluminium est scellé dans de l'eau pour empêcher les réactions de se poursuivre.
La coloration par immersion offre des teintes contrastées beaucoup plus vibrantes et personnalisables, mais elle n'est pas résistante aux UV et les couleurs se décolorent dans une moindre mesure lorsqu'elles sont exposées à la lumière du soleil. Toutefois, ce manque de durabilité est la principale raison pour laquelle il n'est pas couramment utilisé dans les applications où la durabilité des pièces est un facteur important.
3. Coloration intégrale (processus en une étape)
La coloration intégrale est un procédé unique qui incorpore l'anodisation et la coloration en un seul processus, ce qui est plus efficace que les méthodes en plusieurs étapes. Contrairement à d'autres techniques, les électrolytes, qui réagissent à la surface de l'aluminium et sèchent rapidement, créent des tons métalliques riches et profonds, tels que le noir, l'or ou le bronze. La couleur est formée dans la couche d'oxyde même, ce qui lui confère une grande durabilité : elle ne se raye pas, n'est pas sujette à la corrosion et ne s'estompe pas.
Bien que la coloration intégrale permette d'obtenir des finitions de qualité, elle est rare en raison de son coût et de sa complexité. Les composants architecturaux, l'électronique haut de gamme et les équipements industriels dans lesquels les pièces doivent pouvoir résister à des conditions exigeantes et pour lesquels un aspect attrayant et une longévité sont nécessaires sont généralement concernés.
4. Coloration des interférences
La coloration interférentielle est un procédé d'anodisation avancé de haute technologie dans lequel l'épaisseur de la couche d'oxyde du produit peut être manipulée pour créer des bleus, des verts et des violets multi-tons iridescents sans colorants ni pigments. Plutôt que d'absorber la couleur, l'aluminium réagit aux ondes lumineuses en reflétant différentes couleurs selon le point de vue.
Cette méthode est couramment utilisée dans l'architecture, les produits de luxe ou la métallurgie décorative pour obtenir les effets visuels uniques souhaités. Sa résistance exceptionnelle aux intempéries en fait un matériau idéal pour la signalisation haut de gamme et les applications artistiques, ainsi que pour les surfaces extérieures. Bien qu'il soit très complexe, il n'est pas facile de le produire en série.
Alternatives à l'aluminium anodisé

Le traitement de surface de l'aluminium, tel que l'anodisation, est largement utilisé pour améliorer la durabilité, la résistance à la corrosion et l'apparence de l'aluminium. La raison en est qu'il forme une couche d'oxyde protectrice électrochimique qui rend l'aluminium adapté à de nombreuses applications. Néanmoins, il existe d'autres méthodes de traitement de surface qui peuvent offrir des résultats similaires, voire meilleurs, lorsque les conditions requises sont convenablement choisies. Contrairement à ces alternatives, elles présentent des avantages uniques, tels qu'une meilleure protection, de meilleures propriétés d'adhérence et des finitions décoratives. Quelques alternatives courantes à l'aluminium anodisé sont présentées ci-dessous.
1. La galvanoplastie
La galvanoplastie est la technique qui consiste à déposer une fine couche de métal, par exemple de nickel, de chrome, d'or... sur la surface de l'aluminium ou d'autres métaux. Cette opération est réalisée par un processus électrochimique qui améliore la résistance à la corrosion, la durabilité et l'esthétique de l'article. Les garnitures automobiles, ainsi que les bijoux et les composants électriques, sont quelques-uns des matériaux qui font couramment l'objet d'une galvanoplastie. Le plus grand avantage de cette méthode est que les fabricants peuvent choisir un matériau de placage et personnaliser les propriétés de l'aluminium. Par exemple, il peut s'agir d'un placage d'or pour la conductivité, ou d'un placage de chrome pour la dureté et la résistance à l'usure.
2. Revêtement par poudre
Le revêtement par poudre est l'une des méthodes les plus répandues pour la finition des métaux, grâce à l'utilisation de particules de peinture sèches et chargées électrostatiquement. Le résultat à haute température est un film durable et protecteur sur la pièce revêtue. Cette méthode est largement utilisée en raison de sa bonne résistance à la corrosion, de sa bonne résistance aux chocs et de la multitude de couleurs disponibles. Contrairement à la peinture liquide traditionnelle sans solvants, le revêtement en poudre n'utilise pas de solvants nocifs. Il est largement utilisé dans les composants architecturaux, les pièces automobiles et les appareils ménagers, car il peut résister à des conditions environnementales difficiles sans s'écailler ni se décolorer.
3. Revêtement de conversion au chromate (alodine ou film chimique)
L'alodine ou film chimique est un procédé chimique utilisé pour recouvrir l'aluminium d'une fine couche protectrice appelée revêtement de conversion au chromate. Il améliore la résistance à la corrosion sans altérer la conductivité électrique et convient donc aux applications aérospatiales et électroniques. Contrairement à l'anodisation, qui crée une épaisse couche d'oxyde, le revêtement de conversion au chromate permet une meilleure adhérence de la peinture et des adhésifs. Les matériaux légers dotés de revêtements protecteurs fiables sont utiles, en particulier dans les industries où ils sont nécessaires. Et bien qu'il ne soit pas aussi durable que l'anodisation, il peut être mieux adapté à des applications moins sollicitées.
4. Revêtement par dépôt physique en phase vapeur (PVD)
Le revêtement PVD est un traitement de surface de l'aluminium qui implique le dépôt de composés métalliques sous forme de fines couches sur l'aluminium dans le vide. Ce procédé améliore considérablement la dureté, la résistance à l'usure et l'aspect esthétique. Parmi les revêtements PVD, les revêtements TiN et CrN peuvent être appliqués sur des surfaces très dures (outils industriels, armes à feu, montres de luxe) en raison de leur durabilité supérieure. Avec une variété de finitions métalliques telles que l'or, le noir et les couleurs irisées, les revêtements PVD permettent d'obtenir un grand nombre de finitions sans modifier la forme de la pièce.
5. Revêtements céramiques
Les revêtements céramiques sont d'excellents protecteurs de surface résistants à l'usure et à la chaleur pour l'aluminium et d'autres métaux. Ils sont appliqués sous la forme d'une couche très fine et très durable par pulvérisation thermique ou par dépôt chimique en phase vapeur (CVD). Les revêtements céramiques sont particulièrement appréciés dans les applications automobiles, aérospatiales et industrielles, où les composants sont soumis à des températures extrêmes et à des conditions difficiles. Outre leur extrême durabilité, les revêtements céramiques peuvent être thermiquement isolants, ce qui explique qu'ils soient utilisés dans les pièces de moteur, les systèmes d'échappement et les ustensiles de cuisine.
6. Galvanisation à chaud
La galvanisation à chaud est un procédé de revêtement de surface par lequel un objet métallique tel que l'acier ou le fer est galvanisé lorsqu'il est immergé dans un bain de zinc en fusion. Il en résulte un revêtement de zinc qui offre une résistance à la corrosion à long terme, adaptée à l'extérieur, aux ponts ou aux équipements industriels. Bien que la galvanisation à chaud ne soit pas normalement utilisée pour protéger l'aluminium, elle reste un outil idéal pour protéger les métaux ferreux contre la rouille et les dommages causés par l'environnement. Ce qui rend ce procédé si important, c'est que la couche de zinc peut s'auto-guérir, de sorte que si la surface est rayée, la corrosion ne s'installera plus jamais et empêchera la rouille de la surface de l'acier.
Quelle alternative choisir ?
Alternative | Meilleur pour | Principaux avantages |
Placage électrolytique | Pièces métalliques décoratives et fonctionnelles | Finition brillante, résistance à la corrosion, personnalisable |
Revêtement par poudre | Finitions colorées durables | Résistant aux chocs, respectueux de l'environnement, disponible dans de nombreuses couleurs |
Revêtement de conversion au chromate | Aérospatiale et électronique | Améliore l'adhérence, la résistance à la corrosion, la conductivité |
Revêtement PVD | Outils de haute performance et produits de luxe | Finition métallique extrêmement dure et résistante à l'usure |
Revêtements céramiques | Applications résistantes à la chaleur | Barrière thermique, haute durabilité, anti-rayures |
Galvanisation à chaud | Structures en acier très résistantes | Protection durable contre la corrosion, idéale pour une utilisation en extérieur |
Différence entre l'anodisation dure et l'anodisation ordinaire

L'anodisation est un procédé qui permet d'améliorer la résistance à la corrosion, la durabilité et l'apparence de l'aluminium. Les deux types d'anodisation les plus courants sont l'anodisation ordinaire et l'anodisation dure. Les deux méthodes génèrent une couche d'oxyde, bien que les conditions du processus, les propriétés de la couche d'oxyde et l'application soient différentes pour chacune d'entre elles.
1. Différences dans le processus d'anodisation
Concentration d'acide
C'est la concentration d'acide utilisée dans le processus d'anodisation qui affecte le revêtement final. L'anodisation ordinaire implique des concentrations d'acide d'environ 20% pour la formation d'une couche d'oxyde lisse et uniforme.
En revanche, l'anodisation dure utilise une concentration d'acide plus faible, de l'ordre de 15% ou moins, et le revêtement est plus dense et plus résistant.
Exigences en matière de température
La dureté de la couche d'oxyde est un facteur important qui dépend entièrement de la température. L'anodisation ordinaire est réalisée à 18 22°C (en fonction du type et de la quantité d'additifs, la température maximale est de 30°C).
En cas de température élevée, le revêtement peut se poudrer ou se fissurer. L'anodisation dure ne permet d'obtenir un revêtement plus solide et plus résistant à l'usure qu'à des températures beaucoup plus basses, inférieures à 5°C.
Niveaux de courant et de tension
L'anodisation ordinaire s'effectue à une densité de courant de 1 à 1,5 A/dm² et à une tension ne dépassant pas 18 V.
L'anodisation dure, en revanche, doit être réalisée à une tension beaucoup plus élevée, pouvant aller jusqu'à 120 volts, afin d'obtenir un oxyde beaucoup plus épais et également très dur.
2. Différences dans les performances du revêtement
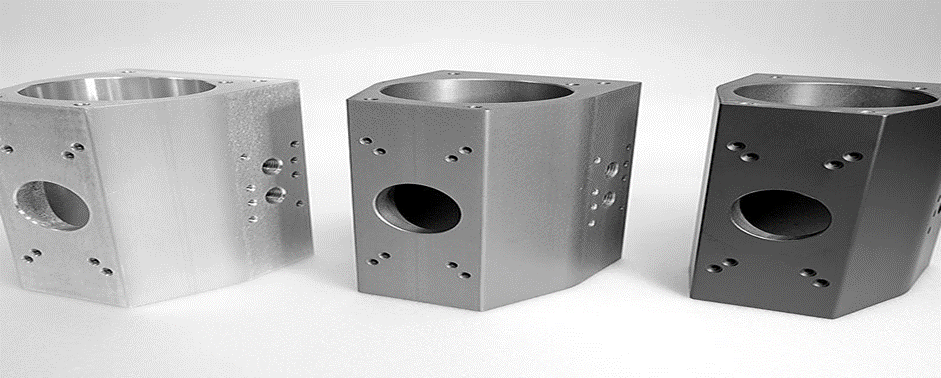
Applications et utilisations
La décoration et le lissage sont les principales utilisations de l'anodisation ordinaire, qui permet de colorer une surface anodisée et de la lisser. Les biens de consommation, les meubles et les composants architecturaux sont les lieux typiques où l'on trouve ce type d'anodisation.
Cependant, l'anodisation dure est utilisée dans les applications industrielles, militaires et automobiles, pour une résistance à l'usure et une durabilité supérieures.
Aspect de la surface
La méthode d'anodisation détermine la texture de la surface de l'aluminium anodisé. Les surfaces anodisées sont généralement lisses et uniformes, ce qui convient aux applications esthétiques. Les surfaces anodisées dures sont plus rugueuses à l'œil microscopique, ce qui leur confère une plus grande capacité à résister à l'usure et à la friction.
Porosité
La porosité fait référence au nombre de minuscules ouvertures dans la couche d'oxyde. Les couches anodisées ordinaires très poreuses sont meilleures pour la teinture et la coloration, mais un peu moins pour la résistance à l'usure. Les couches anodisées dures sont moins poreuses et donc plus solides et résistantes aux dommages.
Épaisseur du revêtement
La protection de base et l'esthétique sont assurées par la couche d'oxyde, généralement inférieure à 15μm, créée par anodisation ordinaire.
Cependant, l'anodisation dure forme une couche beaucoup plus épaisse, généralement supérieure à 15μm, nécessaire pour les applications dures et résistantes à l'usure.
Transparence et opacité
La façon dont la lumière passe dépend de l'épaisseur de la couche d'oxyde, ainsi que du matériau utilisé. Les revêtements anodisés ordinaires étant transparents, ils peuvent être facilement teintés en différentes couleurs.
Les revêtements anodisés durs sont opaques en raison de leur plus grande épaisseur et ne conviennent donc pas à la coloration décorative.
Produits courants en aluminium anodisé
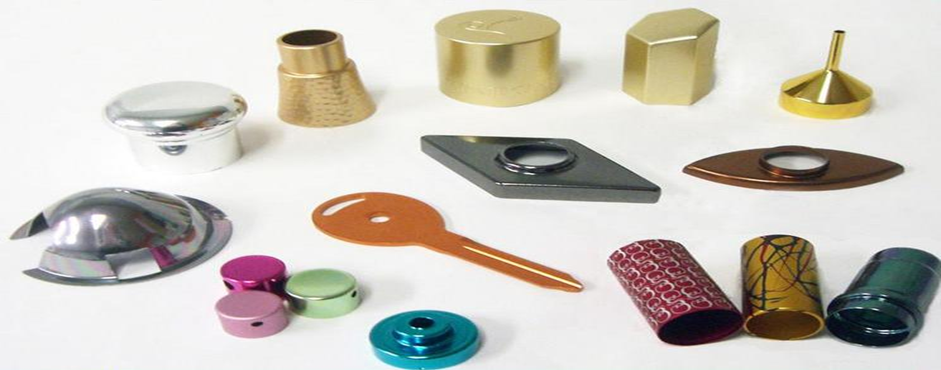
1. Étuis pour smartphones et ordinateurs portables
L'aluminium anodisé est utilisé pour les boîtiers extérieurs de nombreux smartphones et ordinateurs portables haut de gamme. Grâce à ce matériau, les appareils résistent aux rayures, aux bosses et à l'usure. Il leur confère également une finition lisse et élégante, tout en les rendant légers et faciles à transporter.
2. Boîtiers de tablettes
En raison de leur légèreté et de leur excellente protection, les boîtiers pour tablettes sont parfois fabriqués en aluminium anodisé. Les fabricants sont également en mesure de choisir parmi une grande variété de couleurs qui ne dégraderont pas les tablettes puisqu'elles peuvent passer par le processus d'anodisation.
3. Cadres de fenêtres et de portes
L'aluminium anodisé est utilisé pour les cadres de fenêtres et de portes dans les bâtiments parce qu'il est résistant à la rouille et qu'il ne se décolore pas. Il s'agit donc d'une excellente option pour les applications domestiques et les bâtiments commerciaux qui requièrent une longue durée de vie et peu d'entretien.
4. Garnitures automobiles et cadres de bicyclettes
Les propriétés de l'aluminium anodisé en font un bon choix pour les consommateurs à la recherche d'une grande durabilité et d'un poids réduit dans les véhicules, deux facteurs qui peuvent augmenter l'efficacité énergétique. Les cadres de vélo en aluminium anodisé sont populaires dans l'industrie du cyclisme en raison de leur solidité et de leur légèreté. Ils conviennent à une utilisation dans le cyclisme régulier et dans les courses de compétition.
Types d'aluminium anodisé
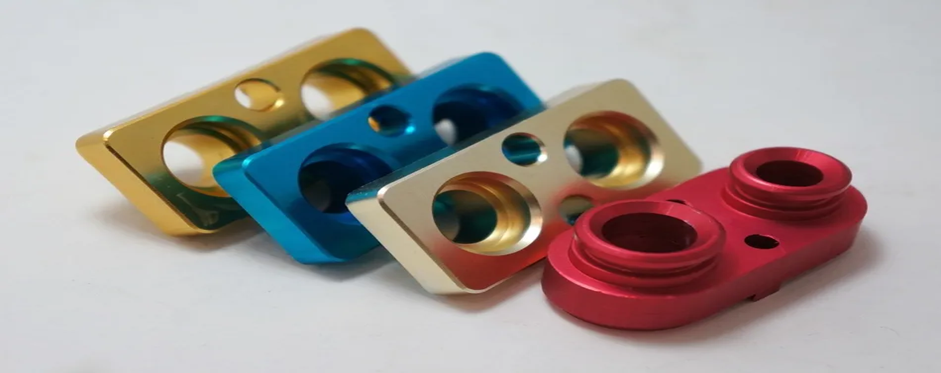
Il existe différents types d'aluminium anodisé, chacun ayant des propriétés et des avantages uniques en fonction des différentes caractéristiques et de la réponse requise pour l'application et la performance. Le type d'anodisation sera choisi en fonction de paramètres tels que la durabilité, la résistance à la corrosion, l'épaisseur et les caractéristiques esthétiques. Les principaux types d'aluminium anodisé et leurs utilisations spécifiques sont présentés ci-dessous.
1. Type I (anodisation à l'acide chromique)

Dans l'anodisation de type I, l'acide chromique crée une couche d'oxyde fine mais très résistante à la corrosion. Il s'agit d'une méthode idéale pour l'aérospatiale sans besoin important de réduction de poids, car elle ne modifie pas les dimensions normales. L'aluminium anodisé de type I a une épaisseur inférieure à celle du type II et ne convient donc pas à l'anodisation colorée, mais il offre une bonne adhérence aux peintures et aux apprêts.
Caractéristiques principales
- Produit une fine couche d'oxyde résistante à la corrosion
- Maintient la conductivité de l'aluminium
- Idéal pour les applications aérospatiales et de défense
- Offre une excellente adhérence aux revêtements.
2. Type II (anodisation à l'acide sulfurique)

Le type d'anodisation le plus courant est le type II, qui utilise de l'acide sulfurique pour produire une couche d'oxyde d'épaisseur moyenne. Ce type d'anodisation peut être coloré et est utilisé dans les biens de consommation, les composants architecturaux et les pièces automobiles. Il offre une bonne résistance à la corrosion et à l'usure, tout en améliorant l'esthétique.
Caractéristiques principales
- Processus d'anodisation standard
- Fournit une couche d'oxyde d'épaisseur modérée
- Permet l'anodisation en couleur
- Il est couramment utilisé dans l'électronique, l'ameublement et la construction.
3. Type III (anodisation dure)
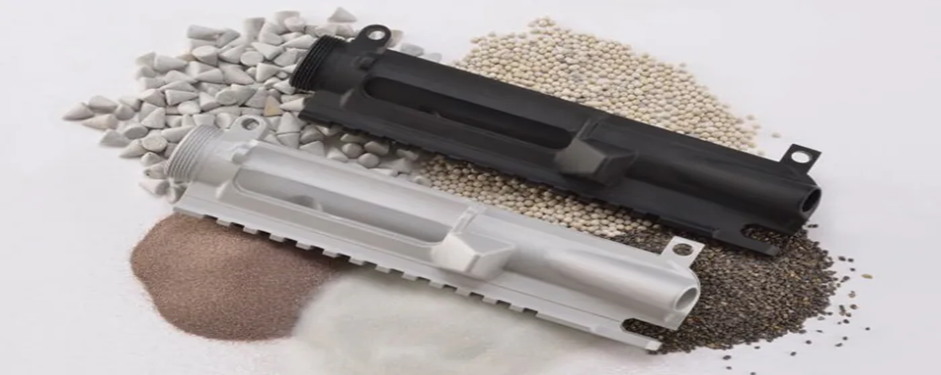
L'anodisation de type III, également connue sous le nom d'anodisation à couche dure, produit la couche d'oxyde la plus épaisse et la plus dure ; elle est très résistante à l'usure et durable. Ce type d'anodisation est largement utilisé dans les applications militaires, industrielles et dans les ustensiles de cuisine qui nécessitent une grande solidité, une résistance supérieure à l'abrasion et une protection supérieure contre la corrosion. L'aluminium anodisé de type III présente une grande durabilité et est souvent utilisé dans les composants de machines, les pièces d'armes à feu et les appareils médicaux.
Caractéristiques principales
- Produit une couche d'oxyde épaisse et résistante à l'usure
- Offre une durabilité et une dureté maximales
- Utilisé dans des applications industrielles de haute performance
- Offre une résistance supérieure à la corrosion
Applications de l'aluminium anodisé
En raison de ses propriétés supérieures, l'aluminium anodisé est utilisé dans plusieurs industries et produits.
1. Industrie aérospatiale et automobile
- Composants d'aéronefs tels que les panneaux de fuselage et les structures d'ailes
- Panneaux de carrosserie, pièces de moteur et pièces d'habillage entrant dans la composition de la voiture
- Durable grâce à ses propriétés de légèreté et de résistance à la corrosion
2. Construction et architecture
- Cadres de fenêtres, murs-rideaux, portes, etc.
- Matériaux de couverture et garde-corps
- Les gratte-ciel modernes et les façades des bâtiments sont utilisés pour leur attrait esthétique.
3. Électronique grand public et appareils ménagers
- Le MacBook d'Apple utilise de l'aluminium anodisé et des smartphones, des ordinateurs portables et des tablettes.
- Appareils de cuisine tels que cafetières et grille-pain
- L'anodisation empêche les empreintes digitales, les rayures et les taches.
4. Équipement médical et de laboratoire
- Instruments chirurgicaux et plateaux médicaux
- La nature non réactive a conduit à l'utilisation de surfaces de laboratoire stériles.
- La longévité dans un environnement de soins de santé dépend de la résistance à la corrosion
5. Équipements de sport et de plein air
- Cadres de bicyclettes, matériel de randonnée et de camping.
- Matériaux durables et légers pour les conditions extrêmes
6. Articles de cuisine et ustensiles de cuisine
- Poêles ou ustensiles antiadhésifs en aluminium anodisé
- Il résiste aux rayures et aux températures élevées.
- Il s'agit d'une alternative plus sûre aux revêtements antiadhésifs traditionnels.
Comparaison entre l'aluminium anodisé et les autres métaux
Fonctionnalité | Aluminium anodisé | Acier inoxydable | Titane |
Poids | Léger | Lourd | Modéré |
Résistance à la corrosion | Excellent | Très élevé | Excellent |
Dureté de la surface | Haut | Très élevé | Extrêmement élevé |
Conductivité électrique | Faible | Modéré | Faible |
Options esthétiques | Diverses couleurs | Limitée | Limitée |
Coût | Abordable | Coûteux | Très cher |
Maintenance et entretien de l'aluminium anodisé
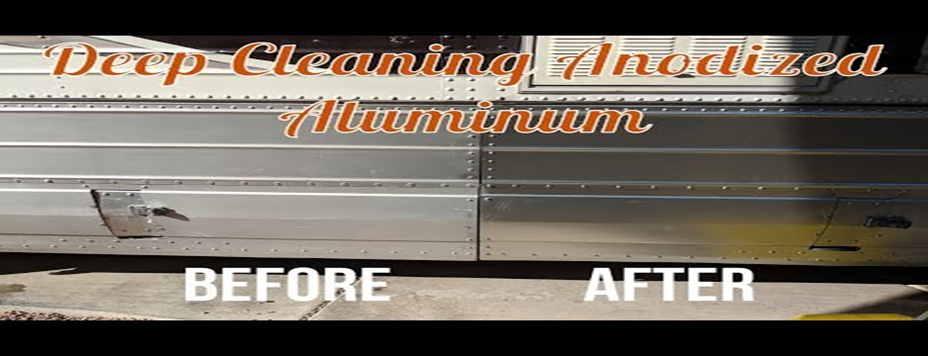
L'aluminium anodisé est très durable et peut résister à la corrosion. Cependant, l'anodisation régulière de l'aluminium permet de conserver son aspect solide et durable. L'entretien préventif, comme la manière dont l'aluminium anodisé naturel se détériore, change de couleur ou est endommagé, permet de conserver le matériau en bon état pendant des années. Voici quelques conseils pour l'entretien des surfaces en aluminium anodisé.
1. Nettoyage régulier
L'aluminium anodisé doit rester propre en utilisant souvent du savon doux et de l'eau. Utilisez un chiffon doux ou une éponge pour enlever la poussière, la saleté et la crasse. Abstenez-vous d'utiliser des nettoyants rugueux ou de la laine d'acier, car ils risquent de rayer la couche anodisée. Un détergent doux dans de l'eau chaude fera des merveilles sur les taches difficiles. Après le nettoyage, rincez à l'eau claire et séchez la surface avec une serviette douce pour éviter les taches d'eau.
2. Éviter les produits chimiques agressifs
Résistant également à de nombreux éléments environnementaux, il peut toutefois être endommagé par des acides forts, des solutions alcalines ou des nettoyants industriels agressifs qui affectent sa couche d'oxyde protectrice. N'utilisez PAS d'eau de Javel, de nettoyants à base d'ammoniaque ou de substances acides qui décoloreraient ou piqueraient le matériau. Si des produits de nettoyage plus puissants sont nécessaires, il faut toujours utiliser une solution au pH neutre, spécialement conçue pour les métaux anodisés.
3. Polissage et protection
Pour que l'aluminium anodisé reste brillant et lisse, utilisez un chiffon doux en microfibres ou une éponge et ne polissez la surface que très légèrement. Si une protection supplémentaire est nécessaire, appliquez une cire non abrasive ou une sorte de produit de protection de l'aluminium anodisé. Cette couche supplémentaire permet de prévenir l'oxydation et de conserver l'éclat et la teinte du métal dans la plupart des cas.
4. Prévenir les rayures et les dommages dus aux chocs
L'aluminium anodisé résiste bien aux rayures, mais il n'est pas à l'épreuve des égratignures. N'utilisez pas d'objets pointus, d'outils lourds ou de matériaux rugueux directement sur la surface afin d'éviter les bosses, les rayures ou les ébréchures. Pour éviter d'endommager accidentellement les composants en aluminium anodisé, il convient d'avoir à portée de main des housses de protection ou même un marqueur Sharpie.
5. Protection contre les conditions environnementales difficiles
Les surfaces anodisées sont progressivement usées par une exposition prolongée à l'eau salée, aux rayons UV et aux intempéries. En revanche, l'aluminium anodisé doit être inspecté périodiquement s'il est utilisé à l'extérieur. Dans les environnements marins ou côtiers, un rinçage à l'eau douce de la surface peut éliminer les dépôts de sel qui accélèrent la corrosion.
Conclusion
L'aluminium anodisé s'est avéré être un matériau très polyvalent et fiable pour de nombreuses industries en raison de sa légèreté, de sa durabilité, de la dureté accrue de sa surface et de sa résistance à la corrosion. L'anodisation permet non seulement de durcir l'aluminium, mais aussi de lui donner un aspect attrayant. C'est la raison pour laquelle il est privilégié dans les secteurs de la construction, de l'automobile, de l'aérospatiale, de l'électronique et des ustensiles de cuisine.
L'aluminium anodisé est l'un des principaux avantages du circuit en termes de longévité et d'entretien minimal. La résistance à l'usure et à la corrosion est excellente, mais il est essentiel de choisir le type d'anodisation (anodisation ordinaire ou anodisation dure) en fonction de l'application envisagée.
L'électrodéposition, le revêtement par poudre et les revêtements PVD sont d'autres types de traitements alternatifs qui offrent leurs propres propriétés. Bien que l'aluminium anodisé ne soit pas aussi respectueux de l'environnement que ce revêtement vert, il lui est néanmoins très complémentaire en tant que favori parmi les solutions respectueuses de l'environnement en raison de son prix abordable et de ses performances supérieures dans différents environnements.
Foire aux questions (FAQ)
1. Dans quel but l'aluminium anodisé est-il utilisé ?
En raison de ses propriétés - légèreté, résistance à la corrosion et durabilité - l'aluminium anodisé est utilisé dans l'aérospatiale, l'automobile, la construction, l'électronique, les ustensiles de cuisine et les équipements industriels.
2. L'aluminium anodisé peut-il rouiller ?
Aluminium anodisé ne rouille pas car l'anodisation forme une couche d'oxyde qui résiste à l'humidité et aux agressions extérieures.
3. L'aluminium anodisé est-il sans danger pour les ustensiles de cuisine ?
L'aluminium anodisé, oui, est non toxique et sans danger pour la cuisine. Il est logiquement utilisé dans les ustensiles de cuisine car il ne réagit pas avec les aliments et forme une surface résistante aux rayures.
4. Quelle est la meilleure façon de nettoyer une surface en aluminium anodisé ?
Pour nettoyer une surface en aluminium anodisé, il suffit d'utiliser un savon doux et de l'eau tiède à l'aide d'un chiffon doux. N'utilisez que des nettoyants doux et non abrasifs, des produits chimiques non agressifs et jamais de laine d'acier qui pourrait endommager la surface anodisée.
5. Qu'est-ce que l'aluminium anodisé et l'aluminium revêtu par poudre ?
La couche d'oxyde protectrice sur l'aluminium anodisé est formée par un processus électrochimique, tandis que la peinture utilisée sur l'aluminium revêtu par poudre est une peinture sèche qui est durcie à haute température. Le revêtement en poudre offre généralement une plus grande variété de couleurs que l'aluminium anodisé, mais il est plus susceptible de s'écailler avec le temps ; l'aluminium anodisé est plus durable et résiste mieux à la décoloration.