L'un de ces alliages, largement utilisé dans les industries de fabrication et de moulage, est l'alliage Zamak 5 à base de zinc, qui présente des caractéristiques uniques. En effet, le Zamak 5 offre une grande solidité, une excellente durabilité et une grande résistance à la corrosion, ce qui en fait un matériau idéal pour les opérations de moulage sous pression. Après extraction, le zamak 5 a une température de fusion extrêmement basse et d'excellentes caractéristiques de coulée, ce qui en fait un matériau idéal pour la construction automobile et les industries des produits de consommation et de la quincaillerie. Les acteurs de l'industrie auront la certitude des propriétés de l'alliage de zamak 5, telles que sa composition et ses diverses utilisations concrètes, pour prendre des décisions en matière de production et optimiser le processus d'efficacité opérationnelle.
L'article traite de l'alliage Zamak 5 à travers sa composition chimique et l'utilisation de l'alliage Zamak. fabrication Les méthodes de contrôle de la température et de maintien de la pression, ainsi que les attributs de la substance mécanique, ont une incidence sur les performances industrielles.
Aperçu de l'alliage Zamak 5
Le Zamak 5 est l'un des principaux alliages à base de zinc que l'industrie désigne sous le nom d'alliage de zinc-aluminium. Le Zamak 5 est chimiquement composé de 3,5 à 4,3 % d'aluminium, de 0,03 à 0,08 % de magnésium et de 0,75 à 1,25 % de cuivre. Il doit sa résistance supérieure aux éléments que le fabricant peut utiliser pour créer des composants à haute résistance destinés aux secteurs de l'automobile, de l'aérospatiale et des biens de consommation. La résistance à la traction, ainsi qu'une densité de 6,7 g/cm³ et un point de fusion relativement large de 380-385°C, sont présents dans cet alliage en raison de sa bonne durabilité et de sa bonne précision.
Composition et propriétés du zamak 5

Composition chimique du zamak 5
Les propriétés mécaniques du Zamak 5 sont améliorées par le mélange d'un alliage à base de zinc dans des pourcentages contrôlés de zinc, d'aluminium, de cuivre et de magnésium.
Cette propriété de fusion facile est l'une des qualités qui font du Zamak 5 un excellent alliage de moulage sous pression par rapport au ZINC 96-98%. Pour obtenir des résultats supérieurs, il est essentiel d'utiliser du zinc d'une pureté de 99,99% afin d'éviter les contaminants qui pourraient nuire à la résistance et à l'intégrité structurelle de l'alliage.
La solidification du matériau Zamak 5 est améliorée par l'ajout d'aluminium (3,5 à 4,3%) qui améliore la microstructure de l'alliage. Les régions sont formées d'une composition qui combine les caractéristiques de ductilité et de dureté dans la structure du matériau. La teneur exacte en aluminium du zamak doit être mesurée afin d'éviter les défauts du matériau tels que les fissures et les problèmes de fragilité.
La présence de magnésium entre 0,03% et 0,08% dans le zamak 5 s'explique par le fait qu'avec cet élément, la corrosion des microfissures dans les joints de grains est bloquée par les impuretés. Comme cet ajout rend l'alliage plus fluide, le moule en bénéficie en obtenant de meilleures caractéristiques de remplissage. L'absence de magnésium rendra la surface du Zamak 5 défectueuse et très difficile à usiner.
Le Zamak 5 est coulé en graphite et présente une bonne résistance à l'usure et une bonne aptitude au traitement thermique lorsque la quantité de cuivre ajoutée est comprise entre 0,75 et 1,25 %, ce qui améliore la résistance au fluage et convient aux applications de variation thermique. Comme le Zamak 5 devient cassant lorsque les limites correctes sont dépassées, la proportion de cuivre est importante.
Propriétés physiques du zamak 5

Le poids d'un matériau en Zamak 5 est de 6,7 g/cm³, avec une densité comprise entre celle de l'acier et celle des alliages d'aluminium. Grâce à son rapport poids/résistance favorable, le Zamak 5 convient à de nombreuses structures faisant appel à des matériaux résistants et de faible poids.
Le zamak 5 fond entre 380 et 385 degrés Celsius, ce qui rend le moulage exact du zamak 5 plus économique que l'aluminium.
À une température moyenne de 120 °C, la résistance à la traction du Zamak 5 était de 330 MPa avec une limite d'élasticité de 220 MPa et un potentiel d'allongement de 7-10%, ce qui répond aux exigences d'une utilisation industrielle. Le Zamak 5 est solide et adaptable car il présente une limite d'élasticité élevée de 220 MPa et l'allongement maximal avant rupture de 7-10%.
Propriétés mécaniques du zamak 5
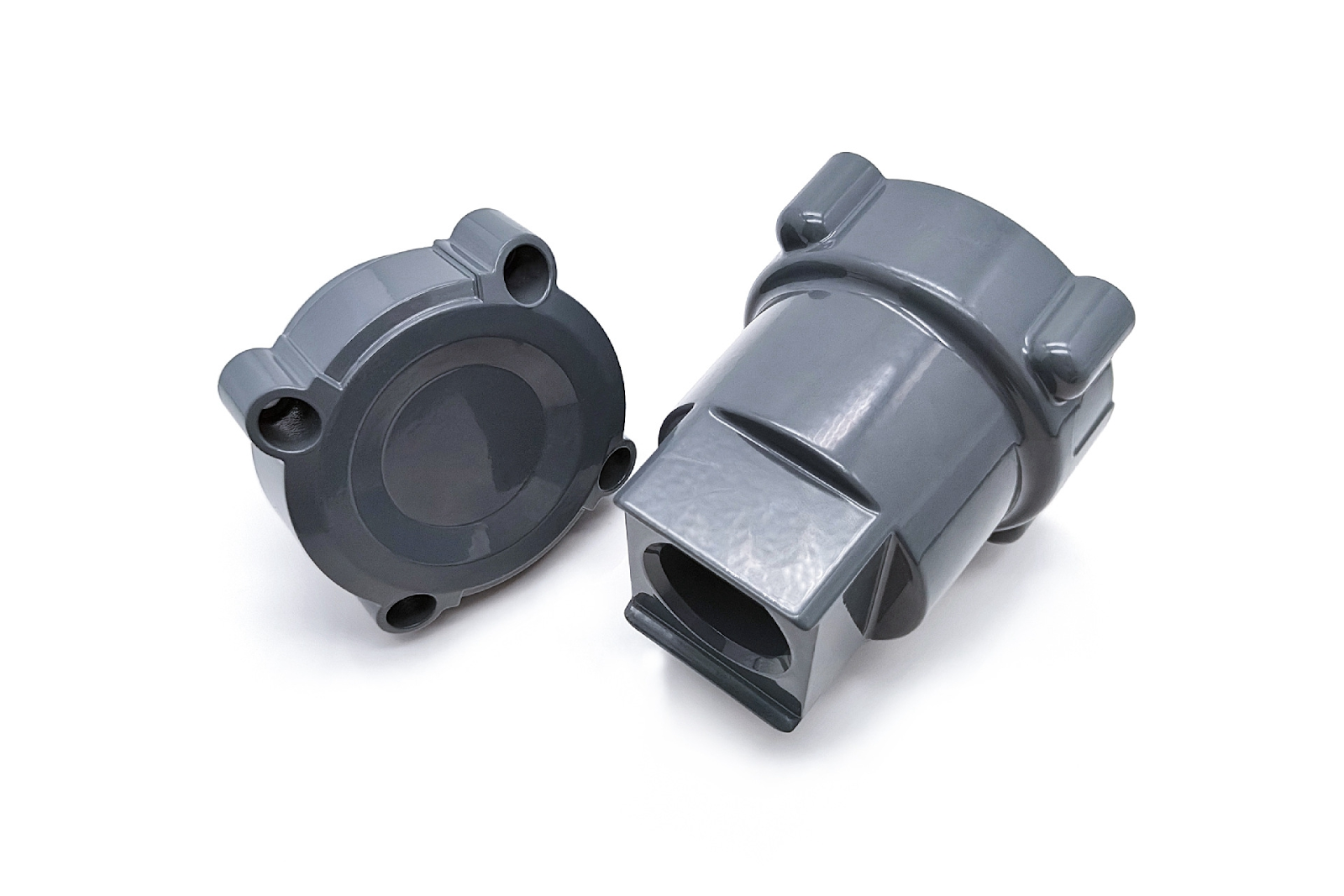
Le Zamak 5 a une dureté Brinell de 91 HB, parfaitement équilibrée entre la résistance et la dureté superficielle, ce qui en fait une excellente combinaison pour les poignées décoratives ou d'autres pièces exigeant une protection contre l'usure.
Résistance à l'impact :
La résistance à l'impact Charpy à température ambiante du matériau est de 53 J, tandis qu'à -20°C, elle est réduite à 35 J. L'alliage présente une résistance à l'impact élevée qui lui permet de se protéger contre les contraintes mécaniques et les vibrations dans des conditions de force dynamique.
Le Zamak 5 peut résister à des contraintes cycliques de 100 MPa et survivre sans défaillance jusqu'à 1 million de cycles. Dans la pratique, le Zamak 5 offre une stabilité fiable sous une charge continue et convient donc aux composants des machines et aux pièces des lave-linge.
Propriétés mécaniques de l'alliage Zamak 5
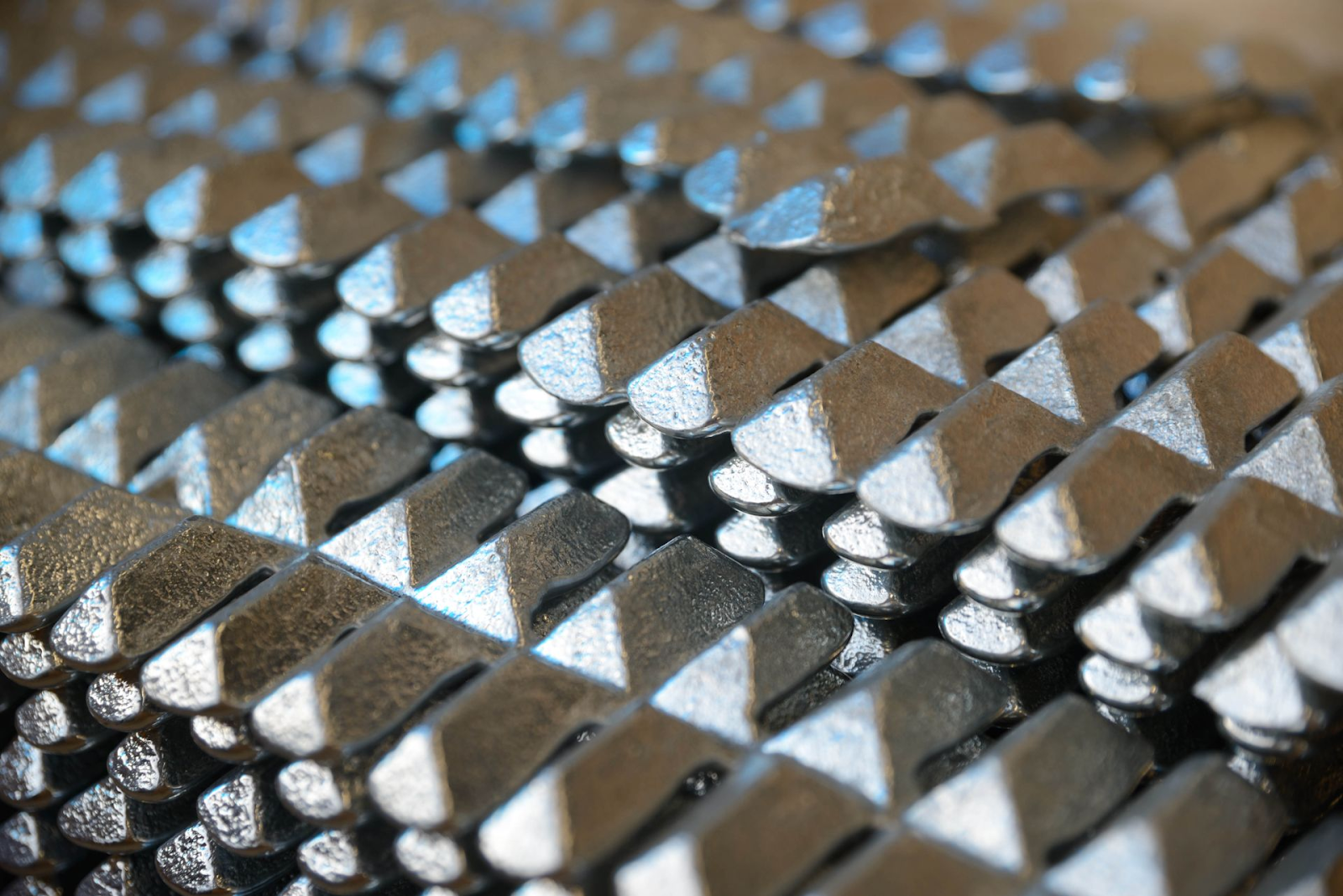
Le tableau ci-dessous présente les caractéristiques mécaniques essentielles de l'alliage d'aluminium Zamak 5.
Propriété | Valeur |
Dureté Brinell | 91 HB |
Résistance ultime à la traction | 328 MPa |
Limite d'élasticité (0.2%) | 269 MPa |
Résistance au cisaillement | 262 MPa |
Résistance à la compression | 600 MPa |
Résistance à la fatigue | 56,5 MPa |
Résistance aux chocs | 65 J |
Module d'élasticité | 96 GPa |
Élongation | 7% en 50mm |
Les valeurs de résistance de l'alliage Zamak montrent comment il peut résister aux contraintes et le placent parmi d'autres matériaux où il peut être utilisé dans des applications exigeantes. Le Zamak 5 offre une résistance supérieure aux charges de fatigue et aux impacts, et convient donc aux pièces soumises à des charges de force répétées.
Propriétés physiques de l'alliage Zamak 5
Grâce à l'ensemble de ses caractéristiques, le comportement du Zamak 5 est contrôlé par ses propriétés physiques.
Propriété | Valeur |
Plage de fusion | 380-386°C |
Densité | 6,60 g/cm³ |
Conductivité électrique | 26% IACS |
Conductivité thermique | 109 W/mK |
Capacité thermique spécifique | 419 J/kg-°C |
Coefficient de dilatation thermique | 27,4 µm/m°K |
Rapport de Poisson | 0.30 |
La combinaison des propriétés du Zamak 5 lui permet d'être performant dans différents contextes et dans des conditions d'application qui conviennent à la conductivité thermique et électrique. Les caractéristiques de densité appropriées et la capacité thermique font du Zamak 5 un produit indispensable pour les systèmes sensibles à la chaleur. Il possède également de bonnes propriétés électriques, ce qui permet de varier la forme d'utilisation d'une pièce électrique.
Avantages de l'alliage Zamak 5
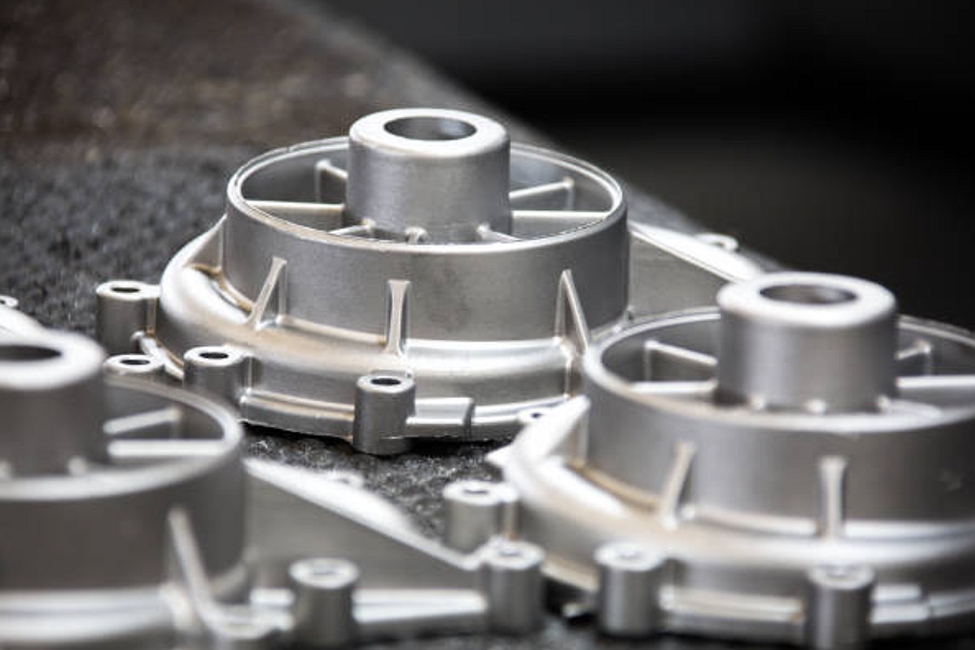
En comparaison, les propriétés de résistance supérieures que le Zamak 5 présente en même temps qu'un poids inférieur s'expliquent par son rapport résistance/poids de 49 MPa, qui dépasse celui de l'aluminium A380. En raison de sa caractéristique dominante, à savoir un niveau de résistance élevé avec une efficacité de poids élevée, le Zamak 5 peut être utilisé avec succès dans diverses applications industrielles liées aux secteurs de l'automobile et de l'aérospatiale.
Bonne résistance à la corrosion : Son alliage rend le Zamak 5 supérieur à la corrosion dans d'autres conditions salines et humides, où son alliage offre des avantages parfaits pour la quincaillerie marine et les applications exposées. Le Zamak 5 a été testé en laboratoire et l'exposition au brouillard salin pendant plus de 500 heures sur le matériau n'endommage pas la surface.
Excellente coulabilité : Le Zamak 5 est particulièrement adapté au moulage sous pression, car le métal est suffisamment fluide pour s'écouler facilement dans des formes de moulage complexes. La coulabilité du Zamak 5 est utilisée par les fabricants pour sa post-production rapide et facile, nécessitant un minimum d'efforts, en particulier lorsque les variations des dimensions géométriques n'affectent pas une fonction.
Haute ductilité : Le Zamak 5 peut être formé à froid en utilisant des processus qui réussissent grâce à sa ductilité, comprise entre 7% et 10%. Le Zamak 5 permet des opérations de pliage, d'évasement et de perçage, ce qui permet d'améliorer le Zamak 5 en augmentant sa polyvalence de fabrication.
Processus de fabrication du zamak 5
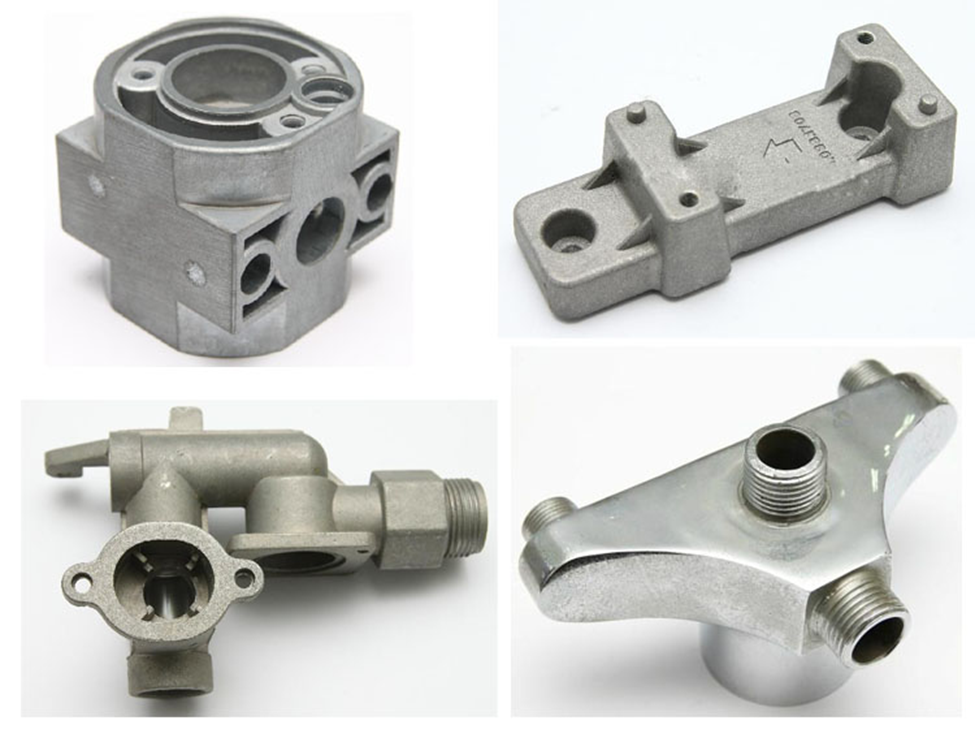
Processus de moulage sous pression
Le matériau Zamak 5 a un point de fusion bas, ce qui signifie qu'il ne peut pas être produit sur une matrice de macro-injection, mais qu'il est possible de le produire à partir d'une matrice à chambre chaude. Le métal en fusion est reçu sous haute pression dans le moule en acier pour fabriquer des pièces avec une tolérance étroite et une surface fine. Cette méthode permet toutefois d'atteindre des taux d'efficacité exceptionnels, en particulier lorsqu'il s'agit de fabriquer de grandes quantités de produits.
Paramètres du processus
En fait, les trois paramètres cruciaux du processus sont : la pression d'injection allant de 700 à 1000 bars en conjonction avec la température de la matrice de 150 à 200 °C et des taux de refroidissement de 50 °C / s. La qualité mécanique, excellente, doit être contrôlée très précisément avant d'atteindre les défauts du produit au niveau le plus bas.
Usinage et finition
Grâce à ses caractéristiques, le zamak 5 est facilement disponible pour les processus de finition après la phase de coulée. La grande ductilité du produit permet des protocoles de filetage et de rainurage précis, ainsi que des procédures précises de galvanoplastie et des méthodes de revêtement par poudre pour améliorer la protection contre la corrosion et les caractéristiques esthétiques.
Différences entre Zamak 5 et Zamak 3
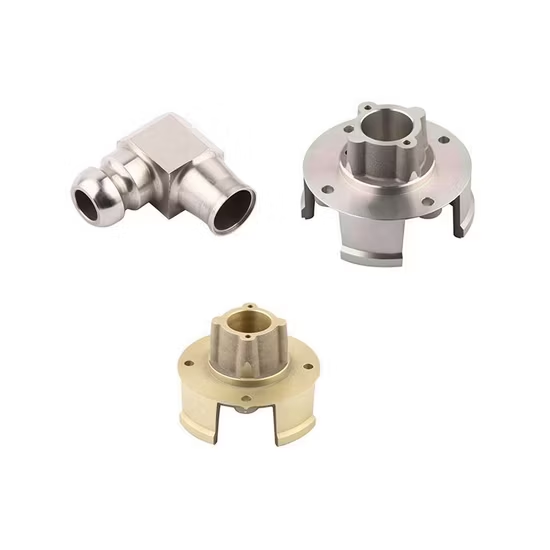
Composition chimique : Le Zamak 5 n'est pas le Zamak 3 car il présente une tolérance à la chaleur grâce à l'inclusion d'un élément en cuivre. Le Zamak 3 ne contient pas de cuivre car il offre les meilleures capacités de coulée et de protection contre l'humidité.
Propriétés mécaniques : Le Zamak 5 a une résistance et une dureté plus élevées, il a donc de meilleures propriétés mécaniques et il est plus utile dans les pièces qui ont des exigences de charge que le Zamak 3.
Comparaison entre Zamak 5 et Zamak 3
Propriété | Zamak 5 | Zamak 3 |
Composition chimique | Zinc (96-98%), Aluminium (3.5-4.3%), Magnésium (0.03-0.08%), Cuivre (0.75-1.25%) | Zinc (95-97%), Aluminium (3.5-4.3%), Magnésium (0.02-0.06%), Cuivre (<0.1%) |
Résistance à la traction | 330 MPa | 240 MPa |
Limite d'élasticité | 220 MPa | 160 MPa |
Élongation | 7-10% | 10-15% |
Dureté | 91 HB (Brinell) | 80 HB (Brinell) |
Densité | 6,7 g/cm³ | 6,6 g/cm³ |
Point de fusion | 380-385°C | 380-385°C |
Applications | Automobile, aérospatiale, biens de consommation, applications à haute résistance | Jouets, articles de décoration, applications à faible contrainte |
Avantage principal | Résistance aux températures élevées, résistance à l'usure, solidité et durabilité accrues | Excellente coulabilité, résistance à la corrosion en milieu humide |
Inconvénient | Moins ductile, plus susceptible d'être fragilisé à des températures plus élevées | Résistance aux températures et aux contraintes plus faibles |
Le Zamak 5 et le Zamak 3 possèdent des structures chimiques, des caractéristiques mécaniques et des cas d'utilisation communs, et ce tableau les présente en un seul endroit.
Zamak 5 (ASTM AC41A, Z35531, Mazak 5) Alliage de zinc
Le Zamak 5 est un alliage de zinc et d'aluminium qui trouve de nombreuses applications en raison de ses excellentes propriétés de résistance et de sa polyvalence. Dans l'industrie, cet alliage est largement connu sous le nom de Zamak 5, bien qu'il soit classé AC41A selon les normes ASTM et Z35531 selon le système de classification UNS. Le Zamak 5 est composé de zinc primaire allié à de l'aluminium et du cuivre pour renforcer ses caractéristiques mécaniques, telles que la solidité, la résistance à la corrosion et la dureté. Comme indiqué, les propriétés de fabrication s'appliquent au Zamak 5 dans son état avant tout processus de trempe ou autre traitement. L'alliage Zamak 5 est utilisé pour le moulage sous pression parce qu'il permet de produire des pièces complexes et détaillées ainsi que des pièces de haute qualité. Comme il offre une capacité opérationnelle à la fois économique et fiable, le Zamak 5 s'est imposé dans les produits automobiles et électroniques ainsi que dans les articles de décoration.
Point de fusion du zamak 5
Les valeurs de fusion de l'alliage Zamak 5 se situent entre 380°C et 386°C (716°F à 727°F), ce qui est inférieur à d'autres matériaux métalliques. L'utilisation du Zamak 5, dont la température de fusion est inférieure à la moyenne, joue un rôle important dans les opérations de moulage sous pression en raison de la facilité de moulage à des températures plus basses. La faible plage de fusion de l'alliage facilite le travail sur la fabrication de précision en raison de la nécessité d'une fusion et d'une solidification rapides pour la fabrication de composants complexes. Le Zamak 5 a un point de fusion bas, ce qui permet aux fabricants de produits de finition de l'utiliser dans de nombreuses productions automobiles, ainsi que dans la fabrication de meubles et de biens de consommation.
Module d'Young du zamak 5
L'alliage de zamak 5 présente certaines caractéristiques techniques. Le module d'Young est de ~96 Giga pascals (GPa). Cette valeur donne la rigidité du matériau puisqu'elle reflète la résistance du matériau à la déformation sous la contrainte appliquée. La rigidité moyenne du Zamak 5 est due à un module d'Young de 96 GPa, suffisamment proche pour répondre aux exigences de résistance et de flexibilité. Le matériau possède la résistance pour laquelle il a été conçu, tout en restant flexible puisque sa rigidité sur l'échelle modérée de 96 GPa (Giga pascals) permet à l'alliage de conserver son intégrité structurelle au cours des applications mécaniques.
Matériaux équivalents à Zamak 5
Différentes applications nécessitent différentes substances, l'alliage de zinc Zamak 5 ayant des propriétés particulières, mais il existe un grand nombre de matériaux équivalents ainsi que des substances supplémentaires. Les trois principaux matériaux de remplacement du Zamak 5 sont le Zamak 3 (ZnAl4Cu1), le Zamak 2 et le Zamak 13.
Zamak 3 (ZnAl4Cu1)
Parmi les alliages de la famille Zamak, Zamak 3 compte parmi les types les plus populaires en raison de ses caractéristiques similaires à celles du Zamak 5. Les substances de zinc, d'aluminium et de cuivre dont ces alliages tirent leurs structures cristallines. Le Zamak 3 est utilisé comme substitut du Zamak 5 parce qu'il contient moins de cuivre, qui est responsable d'une plus faible solidité et d'une plus faible résistance à la corrosion.
Zinc moulé sous pression
En outre, le Zamak 2 et le Zamak 7 ont une bonne aptitude à la coulée qui les rend aptes à être utilisés dans des productions exigeant une grande précision et une qualité de finition élevée, à l'instar des alliages de zinc coulés sous pression. Bien que ces alliages aient des propriétés mécaniques différentes, les mêmes procédés de fabrication sont utilisés pour ces alliages.
ALSi12
Lorsqu'ils ont besoin d'une résistance légèrement plus élevée à des températures plus élevées, les utilisateurs peuvent remplacer l'alliage aluminium-silicium ALSi12 par d'autres fournitures pour l'approvisionnement. Il n'est pas nécessaire que le Zamak 5 et l'ALSi12 aient la même composition chimique, car ils sont tous deux utilisés dans la production de pièces moulées et de pièces coulées sous pression.
ADC 12 (alliage d'aluminium)
Lorsqu'une bonne résistance à la corrosion et une bonne coulabilité sont requises, l'alliage d'aluminium ADC 12 peut être utilisé comme matériau équivalent pour remplacer certaines applications de fabrication. Le Zamak 5 pouvant être légèrement plus dur, le choix doit se faire en fonction de critères de performance.
En fonction de l'équilibre des propriétés mécaniques individuelles acquises en matière de résistance à la traction et à la corrosion, ainsi que de dureté, un tel équivalent est choisi par les équipes de production.
Processus de coulée du Zamak 5
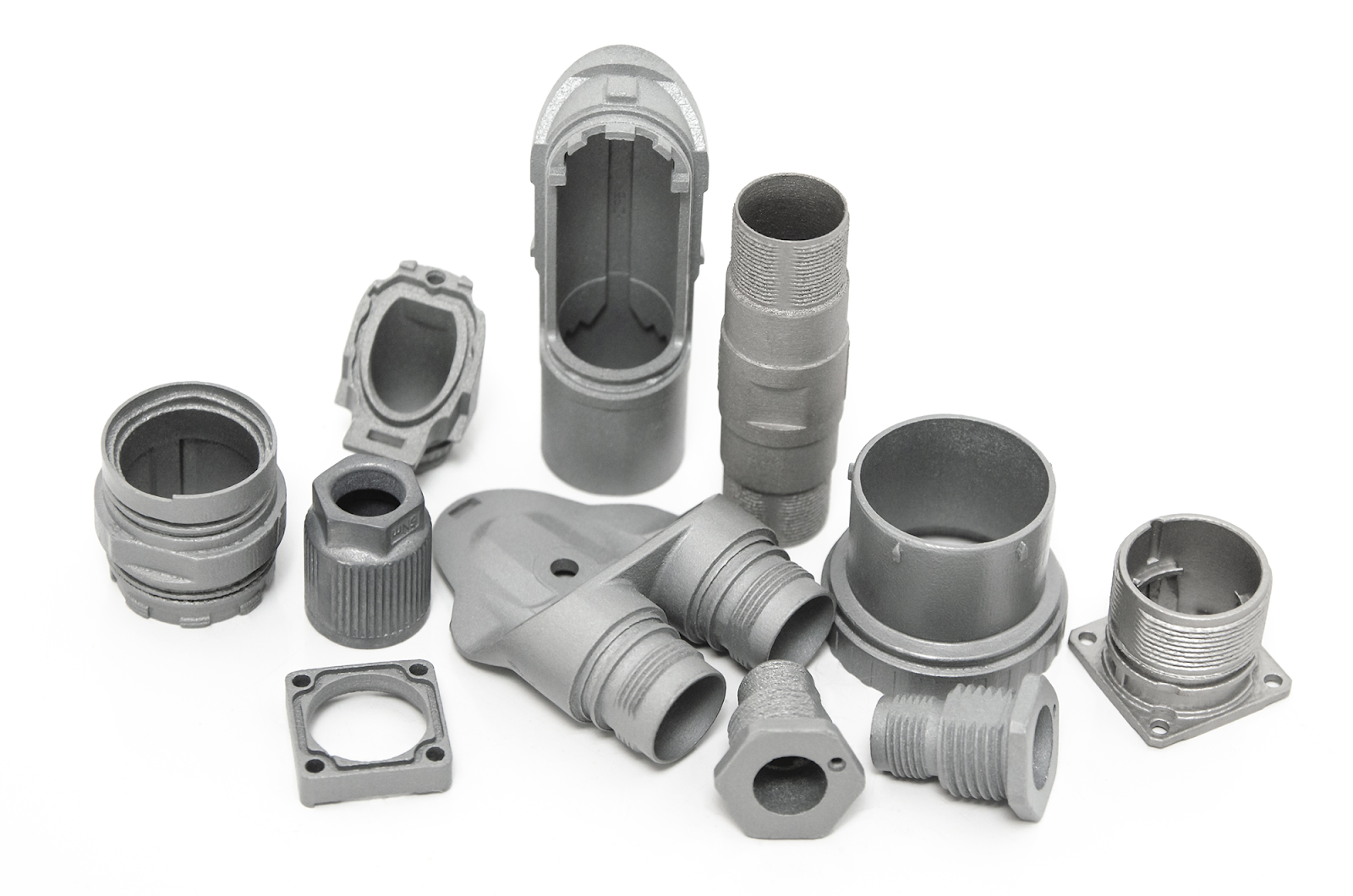
Le Zamak 5 coulé peut être préservé et optimisé dans le produit final par différentes étapes de la procédure de coulée du Zamak 5. La principale méthode de production du Zamak 5 est le moulage sous pression,g où le métal fondu est injecté sous haute pression dans des moules métalliques. L'opération de coulée du Zamak 5 se compose de plusieurs opérations successives.
Préparation du moule :
La matrice doit être chauffée au-dessus d'une certaine température afin d'éviter tout choc thermique sur l'échantillon pendant le processus d'injection. Nous autorisons ensuite l'utilisation du courant à l'extérieur pour nous assurer que la surface de coulée et la production sont toujours exemptes de défauts.
Fusion de l'alliage Zamak 5 :
Le zamak 5 doit atteindre une température comprise entre 380 et 390°C (716-734°F) avant de devenir totalement liquide. L'alliage est chauffé dans le four jusqu'à cette température spécifique, et l'état de l'alliage devient liquide, susceptible d'être injecté.
Injection de l'alliage fondu :
L'alliage Zamak 5 passe de la forme liquide à la cavité du moule correctement préparée sous haute pression après la fusion. Les pressions d'injection pour différentes complexités de pièces et leur ampleur sont de 30 à 60 MPa, qui sont appliquées par les fabricants pour former.
Refroidissement et éjection :
Ensuite, lorsque le moule reçoit l'alliage en fusion, il commence à refroidir et à devenir solide. La pièce est démoulée lorsqu'elle cesse de rester à une température de refroidissement adéquate. La durée de refroidissement du moule et sa température peuvent être contrôlées pour garantir la qualité du moulage final (éviter les déformations).
Opérations de finition :
L'éjection des pièces en Zamak 5 nécessite leur traitement par le biais de diverses procédures de finition au cours desquelles les pièces sont ébarbées, polies et enfin revêtues afin de répondre aux exigences finales.
Le procédé de moulage Zamak 5 est efficace pour une production en grande série, car il permet de créer des objets complexes avec des exigences de tolérance précises. Un alliage d'une fluidité exceptionnelle corrige le remplissage des zones complexes de la cavité du moule, de sorte que l'alliage convient à la production de composants aux détails fins dans les secteurs de l'automobile et du matériel informatique, ainsi que des appareils électroniques grand public.
Différentes normes pour l'alliage Zamak 5 : Une perspective mondiale
Le Zamak 5, un alliage de zinc assez polyvalent, est généralement connu sous différents noms ; cependant, ces identifications proviennent de la norme particulière ainsi que du pays d'origine. Les différentes spécifications relatives au Zamak 5 ont des tendances différentes selon les régions, en fonction de la méthode de production et de la désignation antérieure. Ces désignations sont très importantes pour les utilisateurs de Zamak 5 car elles définissent des protocoles pour l'entreprise en fonction des spécifications de l'alliage dans divers secteurs du marché et des normes régionales. Toutes les normes mondiales et les noms alternatifs de l'alliage Zamak 5 sont présentés dans une vue d'ensemble considérable.
Noms et normes mondiales pour l'alliage Zamak 5
Le tableau suivant présente les différents étalons nationaux et les appellations de l'alliage Zamak 5.
Nom traditionnel | Zamak 5 |
Nom abrégé de la composition | ZnAl4Cu1 |
ASTM | AC 41A |
Nom commun | Alliage 5 |
Chine | ZX03 |
JIS (Japon) | Type de lingot 1 (lingot) ZDC1 (alliage) |
Désignation européenne abrégée | ZL0410 (lingot) ZP0410 (alliage) |
Allemagne DIN 1743-2 | Z420 |
France NFA 55-010 | Z-A4UI |
UK BS 1004 | Alliage B |
UNS (système de numérotation unifié) | Z35530 (lingot) Z35531 (alliage) |
Pourquoi ces normes sont-elles importantes ?
Différentes normes d'alliage Zamak 5 ont été adoptées en raison de l'adoption mondiale d'une combinaison de pratiques industrielles influencées par la région et d'exigences internationales en matière de communication. Cela signifie que les entreprises qui produisent des matériaux en Zamak 5, ainsi que leurs ingénieurs, doivent connaître les normes régionales et les désignations de ce matériau en particulier afin de sélectionner le matériau approprié pour leur application. Les normes sont des détails impératifs de la composition chimique de l'alliage Zamak 5, des normes de performance, afin de choisir les matériaux appropriés pour les opérations de moulage et d'usinage.
Avantages de l'alliage Zamak 5
Le Zamak 5 est utilisé dans de nombreuses applications industrielles en tant qu'alliage de zinc polyvalent et robuste, offrant de nombreux attributs utiles à divers efforts de fabrication. Le Zamak 5 triple les caractéristiques de résistance supérieure, de ténacité et de propriétés protectrices, ce qui le rend adapté à de nombreuses applications matérielles dans les appareils grand public et les équipements industriels. Tels sont les avantages fondamentaux que l'alliage Zamak 5 offre aux fabricants.
1. Solidité, durabilité et sécurité
L'alliage de zinc Zamak 5 conserve des qualités de performance exceptionnelles en termes de résistance et de dureté. L'alliage est une source importante de résistance à la force, c'est pourquoi il reste une solution solide pour les applications exigeantes qui nécessitent des pourcentages de contrainte très élevés. Le Zamak 5 est important pour les industries parce qu'il est très résistant physiquement et qu'il répond en même temps aux mesures de sécurité absolues pour les événements de contact.
Le Zamak 5 offre un avantage en matière de sécurité par rapport à certains métaux, tels que le magnésium, en échappant aux problèmes liés au feu. Le zamak 5 possède une qualité rare qui le distingue des autres matériaux courants, car il n'absorbe jamais l'humidité, ce qui évite les problèmes d'absorption d'eau semblables à ceux du plastique. En raison de son innocuité pour le contact humain, le Zamak 5 est utilisé dans la fabrication d'emballages de produits cosmétiques.
En raison de ses caractéristiques liées à la fiabilité, qui sécurisent les fabricants ainsi que les utilisateurs finaux, le Zamak 5 est choisi pour de nouvelles applications technologiques.
2. Qualité supérieure du moulage sous pression
Le Zamak 5 est utilisé pour les applications de moulage sous pression en raison de la capacité de cet alliage à produire des pièces de haute qualité exemptes de défauts. Grâce à sa capacité à créer des produits lisses et finis avec un minimum de défauts, l'alliage Zamak 5 produit des pièces moulées sous pression de haute qualité qui nécessitent un processus de post-production minimal.
Le zamak 5 possède les propriétés du zam naturel, ce qui permet d'utiliser des techniques de moulage exactes pour fabriquer des produits dont le niveau de perfection est élevé dans le processus de production. Comme le Zamak 5 ne présente aucune étape de finition formelle, le processus de fabrication permet de gagner du temps et de réduire le coût des opérations de fabrication. Les pièces en Zamak 5 ont une belle apparence car les concepteurs peuvent les peindre ou les chromer selon leurs goûts.
La simplicité de finition du Zamak 5 en fait un produit idéal pour les applications dans les produits de décoration intérieure, les détails des meubles et les composants d'éclairage décoratifs. Les pièces en Zamak 5 résistent aux effets de ternissement grâce à son effet durable.
3. Transformés en différents produits finaux
Le Zamak 5 est d'une nature supérieure pour le travail de production. Le fait que l'alliage soit souple par nature, parce que le zinc est ductile, permet de le façonner facilement pour différentes opérations de travail au cours de la production. Le Zamak 5 peut facilement être utilisé avec différentes méthodes de production, telles que le moulage, le cintrage, l'usinage et le rivetage, afin de répondre aux exigences de la fabrication.
Le Zamak 5 possède des caractéristiques de traitement faciles, ce qui en fait un accessoire essentiel pour différentes industries qui ont bénéficié de la réduction des coûts de fabrication et du maintien d'un processus de production facile. Le Zamak 5 étant le choix privilégié pour l'assemblage de produits verrouillés et de composants de poignée moulés, le processus d'assemblage des pièces en Zamak 5 devient moins fastidieux.
4. Fabrication rentable
Le Zamak 5 est un matériau qui permet aux fabricants de bénéficier d'un prix exceptionnellement abordable. Le Zamak 5 est si bon marché qu'il est moins cher que d'autres alliages et très rentable lorsqu'il est moulé. Sa structure de coût raisonnable invite toutefois les fabricants à atteindre des normes de rentabilité supérieures, et ses propriétés supérieures attirent les fabricants.
Le zamak 5 a un grand potentiel de recyclage, ce qui fait de la capacité à le recycler un facteur important de réduction des coûts de fabrication à long terme. Les articles en zamak 5 sont réutilisables et conduisent à la production de ferraille qui sera récupérée, ce qui permet d'économiser des coûts et de minimiser les déchets qui en découlent.
5. Cycle de production respectueux de l'environnement
La production de Zamak 5 est en grande partie respectueuse de l'environnement. Le Zamak 5 ne pose pas de grands risques pour l'environnement, car il est fabriqué selon une procédure différente des procédures dangereuses utilisées pour certains métaux. La fabrication de l'alliage ne présente aucune pollution nocive car aucun sous-produit n'est formé. En ce qui concerne la législation environnementale, le Zamak 5 est un bon choix, et il fournit également à une entreprise une méthode respectueuse de l'environnement pour se conformer à ses propres réglementations.
Limites de Zamak 5
Bien que le Zamak 5 présente de nombreux avantages, il doit d'abord être sélectionné sur la base de ses limites fixes dans le processus de sélection.
Faible résistance à l'humidité
Le contact du Zamak 5 avec des conditions humides entraînera la formation d'oxydation sur sa surface, car il présente une faible résistance à l'humidité. Les fabricants de produits en Zamak 5 doivent prévoir des mesures de protection contre l'humidité excessive et, si ce n'est pas le cas, des revêtements de protection supplémentaires doivent être prévus pour empêcher sa dégradation.
Résistance limitée aux températures élevées
La capacité de résistance thermique du Zamak 5 est modérée. Le Zamak 5 ne doit pas être utilisé pour des applications où la température dépasse 80°C en raison d'une très forte baisse de la résistance à la traction, ce qui augmente le risque de rupture ou de flexion.
Pas idéal pour les applications légères
La pièce obtenue avec le Zamak 5 est plus lourde car sa densité est supérieure à celle des alliages non ferreux concurrents. L'élément léger pour de telles applications doit donc être considéré comme un autre matériau d'alliage, car c'est lui qui détermine les exigences.
Problèmes de résistance à la corrosion avec d'autres métaux
Lorsque le zinc ou l'étain sont combinés au plomb pour fabriquer ce matériau, la durabilité du Zamak 5 est compromise en raison de la résistance réduite à la corrosion de l'alliage obtenu. Dans le cadre d'un usage particulier, il convient de prêter une attention particulière à la combinaison des matériaux lors de l'utilisation du Zamak 5.
Propriétés d'impact à basse température
Dans les environnements froids, la résistance à l'effet du Zamak 5 est affectée aux points où la température descend à des niveaux extrêmement bas, et il n'est donc pas fonctionnel dans les conditions froides.
Où utiliser Zamak 5 ?
Le Zamak 5 est largement utilisé dans de nombreux secteurs, y compris l'industrie du moulage sous pression. Le Zamak 5 excelle entre les deux extrémités du spectre de production dans la fabrication d'éléments automobiles et d'articles décoratifs. Parmi les utilisations les plus courantes, on peut citer
Accessoires de salle de bains: Le Zamak 5 a la capacité de se protéger contre la corrosion. Il est donc largement utilisé dans la production d'accessoires de salle de bains tels que les robinets et les poignées.
Composants d'armes à feu: L'alliage est très durable et solide, et fonctionne donc très bien dans la fabrication de pièces d'armes à feu.
Jouets et objets de collection: Cependant, en raison de son processus de moulage simple et de sa finition de surface de premier ordre, le Zamak 5 est un choix populaire pour le moulage sous pression de jouets et d'objets miniatures ainsi que de produits de collection.
Fabrication de serrures et de quincaillerie: Le Zamak 5 est prédominant dans l'industrie manufacturière pour produire des serrures avec poignées, des boutons de serrures et d'autres pièces de quincaillerie grâce aux bonnes propriétés de résistance et à la facilité d'usinage de cet alliage.
Électronique et appareils électroménagers : Le Zamak 5 présente des aspects de durabilité et des qualités attrayantes, et les articles ménagers tels que les mixeurs, les agrafeuses et les ventilateurs de plafond, ainsi que d'autres appareils, apprécient le Zamak 5.
Propriétés mécaniques de l'alliage Zamak 5
L'alliage Zamak 5 est déterminé par ses qualités structurelles pour fonctionner bien ou mal dans diverses opérations industrielles. L'alliage Zamak 5 possède une résistance à la traction, ainsi qu'un allongement, une dureté et une résistance à la corrosion. Les valeurs sont modifiées quantitativement lorsque le processus de coulée est différent et que la composition de l'alliage métallique et la vitesse de refroidissement sont modifiées.
Résistance à la traction : L'alliage Zamak 5 conserve une résistance à la traction de 280-300 MPa, ce qui est plus élevé que les autres alliages à base de zinc.
Limite d'élasticité : L'alliage Zamak 5 présente une excellente résistance à la déformation sous contrainte car sa limite d'élasticité est d'environ 230 MPa.
Élongation : L'alliage Zamak 5 a un cercle de ductilité moyen (entre 3 et 6%) dans son taux d'allongement. Ses propriétés permettent de faibles déformations qui ne s'accompagnent pas de fissures, et il convient donc à une utilisation dans des systèmes flexibles.
Dureté : La dureté du Zamak 5 est de 90-120 HB (dureté Brinell), ce qui rend le matériau utilisable pour des applications nécessitant une résistance à l'usure relativement faible.
Résistance à la corrosion : Même en présence d'un taux d'humidité moyen et de substances chimiques standard, l'alliage Zamak 5 résiste très bien à la corrosion. Le Zamak 5 convient parfaitement comme matériau pour les composants extérieurs et automobiles.
Applications de l'alliage Zamak 5
Le Zamak 5 est choisi pour une large gamme d'industries parce qu'il combine ses bonnes caractéristiques de coulée avec de fortes propriétés mécaniques. Ses applications sont les suivantes
Industrie automobile : Le Zamak 5 est un matériau essentiel pour la fabrication de composants fonctionnels fins pour les moteurs automobiles, les boîtiers d'habillage des véhicules et les boîtiers d'appareils électroniques.
Quincaillerie et accessoires : Ces matériaux, comme le Zamak 5, sont utilisés dans le secteur automobile, car ils allient résistance et durabilité et donnent des produits agréables à l'œil.
Biens de consommation : L'alliage Zamak 5 est le matériau que les producteurs utilisent en raison de sa solidité et de sa résistance à la corrosion favorables, ainsi que de sa capacité à être façonné pour produire des jouets et des connecteurs électriques, ainsi que des appareils électroménagers.
Électronique : Le Zamak 5 conduit bien l'électricité, se moule bien dans des formes complexes et est utilisé pour fabriquer des boîtiers et des boîtiers d'appareils électroniques.
Avantages de l'alliage Zamak 5
Le Zamak 5 présente plusieurs avantages importants qui en font l'alliage de choix pour les fabricants.
Rapport coût-efficacité : Le coût du Zamak 5 est une excellente option car il offre une bonne durabilité et un moulage facile à un tarif plus simple et moins cher que les autres alternatives métalliques.
Polyvalence : La raison pour laquelle le Zamak 5 est choisi pour fabriquer des pièces complexes et précises est qu'il est facile de produire des formes compliquées, sans accommodement.
Qualité de la finition: Le Zamak 5 produisant d'excellentes surfaces lisses, il est nécessaire de réaliser des travaux de finition de haute qualité, afin que les fabricants puissent obtenir une meilleure qualité de finition.
Rapport résistance/poids élevé : L'alliage Zamak 5 convient parfaitement à l'industrie automobile ainsi qu'à d'autres secteurs, car cet alliage offre une grande résistance et une grande indépendance par rapport au poids.
Défis et considérations liés à l'utilisation de Zamak 5
Bien que l'alliage Zamak 5 présente de nombreux avantages, il existe plusieurs points critiques quant à son utilisation.
Sensibilité à la température : Cependant, le Zamak 5 a un comportement thermosensible car il ne présente pas de dégradation de ses propriétés en présence d'une augmentation de température inférieure à 250°C (482°F). Les pièces en Zamak 5 doivent être limitées, pendant leur durée de vie utile, à des environnements où la température est suffisamment basse pour ne pas dépasser ce seuil.
Limites de l'usinage : Bien que le processus de coulée du Zamak 5 soit simple, ce matériau pose des problèmes lors des opérations de machinerie qui impliquent des méthodes agressives, car il a tendance à se gripper et à s'user. Pour obtenir des résultats probants, les techniciens doivent disposer d'outils et de techniques appropriés.
Impact sur l'environnement : La bonne résistance à la corrosion du Zamak 5 doit également être prise en compte dans l'impact environnemental que le Zamak 5 provoque dans les processus de production et de cycle. Le Zamak 5 peut encore être amélioré par le recyclage et la réduction des déchets dans les émissions de coulée, et l'industrie s'y emploie afin d'accroître la durabilité de l'alliage de zinc.
Services de moulage sous pression Zamak 5 à CNM TECH
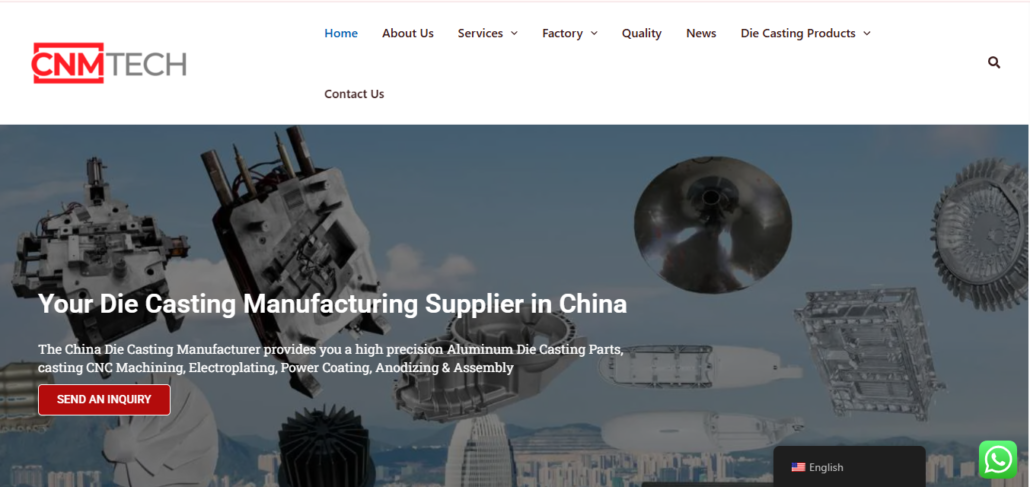
Nous offrons des solutions exceptionnelles de moulage sous pression en Zamak 5 sous le portefeuille de CNM TECH pour les besoins de diverses industries, de l'automobile à l'aérospatiale, en passant par la production de produits de consommation. Nous sommes une organisation spécialisée dans l'expérience approfondie et les systèmes modernes de moulage sous pression qui nous permettent de développer des pièces qui offrent d'excellentes performances, capacités et maintenance.
En appliquant notre méthode moderne de moulage sous pression, nous fournissons des produits Zamak 5 ayant de bonnes dimensions, une excellente qualité de surface et un temps de fabrication systématique pour une quantité de production économique. En d'autres termes, avec CNM TECH, les clients peuvent dicter avec précision leurs spécifications au matériau de moulage sous pression et obtenir des délais d'exécution serrés.
Jetez un coup d'œil à toutes nos offres Zamak 5 qui fournissent des capacités de prototypage et de fabrication à grande échelle. Sur le site www.thediecasting.com, vous découvrirez comment les solutions Zamak 5 de notre société augmentent la durée de vie des produits.
Vous devez choisir les services de moulage sous pression en Zamak 5 de CNM TECH car ils sont précis.
Conclusion
Le Zamak 5 est un alliage couramment utilisé dans l'industrie pour la fabrication de pièces de précision, en particulier dans les secteurs de l'automobile, de la quincaillerie et de l'électronique, qui se caractérisent par de faibles coûts de production et une grande efficacité. Le mélange de zinc, d'aluminium, de cuivre et de magnésium de l'alliage de zinc 5 en fait un matériau solide doté d'excellentes caractéristiques mécaniques, d'une grande résistance à la corrosion et d'une bonne coulabilité. Les techniques de fabrication utilisant la coulée de Zamak 5, si elles sont abordées correctement, avec les contrôles de température et de pression, produisent des composants de haute qualité avec très peu d'imperfections chaque fois qu'elles sont mises en œuvre. Cependant, le Zamak 5 a un point de fusion bas et des caractéristiques de fluidité qui le rendent adapté à des conceptions très sophistiquées, ce qui explique ses nombreuses applications industrielles.
FAQ
1. Quelles sont les caractéristiques essentielles du processus de moulage sous pression de CNM TECH qui conduisent au Zamak 5 ?
A : L'alliage de zinc à haute performance présente des caractéristiques telles que : une excellente résistance et stabilité dimensionnelle, ainsi qu'une protection exceptionnelle contre la corrosion. L'un d'entre eux est le Zamak 5. Le Zamak 5 présente une capacité de coulée exceptionnelle, grâce à laquelle des composants extrêmement détaillés et complexes peuvent être fabriqués avec un minimum d'usinage. CNM TECH utilise le Zamak 5 pour fabriquer des composants fiables et rentables qui peuvent être utilisés dans les applications automobiles, l'électronique grand public et l'industrie du matériel informatique.
2. CNM TECH peut-il produire certaines pièces en Zamak 5 selon les exigences de mon projet ?
A : Absolument. En tant qu'entreprise spécialisée, CNM TECH propose une solution individuelle de moulage sous pression en Zamak 5. L'entreprise fabrique des moules avec des clients, des entreprises qui ont besoin de prototypes de faible volume ainsi que de pièces de grand volume qui doivent être exactement comme spécifié. Le travail dévoué de nos employés dans les processus de production nous permet de fournir des résultats précis et des performances fiables.
3. Quels sont les types de traitements possibles pour compléter les produits de coulée Zamak 5 ?
A : Chez CNM TECH, les multiples finitions disponibles pour les pièces en Zamak 5 comprennent la galvanisation en combinaison avec le thermolaquage et le chromage, ainsi que la peinture et le polissage. Les techniques de finition permettent d'améliorer l'aspect, la résistance à l'usure et la protection contre la corrosion de pièces fonctionnelles ou décoratives.