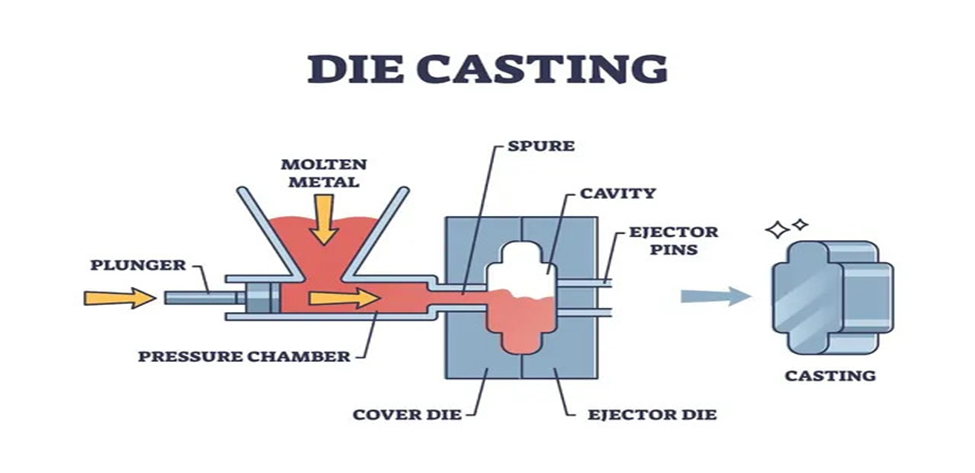
Il s'agit d'un processus de fabrication dans lequel le métal en fusion est poussé sous pression pour remplir la cavité d'un moule, également connu sous le nom de moulage sous pression. Le moule est généralement en acier de haute qualité et la pièce peut donc être produite en grandes quantités. La pièce finie est ensuite produite en ouvrant le moule une fois que le métal fondu est refroidi et forme une couche solide. Ce type d'utilisation du processus est principalement appliqué à la fabrication de métaux complexes utilisés dans la production de différentes pièces qui nécessitent une grande précision dans les mesures et des surfaces polies. Le moulage sous pression peut être effectué sur de l'aluminium, du zinc et du magnésium, mais d'autres métaux peuvent également être utilisés en fonction de l'application et d'autres exigences. Moulage sous pression est considérée comme l'une des techniques de fabrication expertes dans la conception de la production de masse de composants de petite et moyenne taille à partir de métaux. La popularité de cette méthode s'est étendue aux secteurs de l'automobile, de l'aérospatiale, de l'électronique et des machines industrielles en raison de sa capacité à produire des pièces durables, légères et sur mesure. Toutefois, ce procédé est largement reconnu pour sa capacité à fabriquer des produits à la géométrie complexe qui seraient très difficiles à réaliser avec des techniques conventionnelles.
Fonctionnement de la coulée sous pression

Le moulage est la première partie du processus de coulée sous pression. D'un côté du moule, il y a une moitié, et c'est une moitié d'une conception particulière pour que le moule ait la forme du produit final. Les cavités et les noyaux sont conçus pour les moules qui sont généralement fabriqués sur mesure afin que la pièce puisse être reproduite le plus fidèlement possible.
1. Injection de métal en fusion :
Le métal en fusion est ensuite injecté sous haute pression dans la cavité du moule pour lui donner la forme souhaitée. Le métal est généralement chauffé à un degré au-dessus de la température de fusion pour le rendre fluide. Dans le cas du moulage sous pression, la pression à laquelle le métal en fusion est poussé dans le moule peut aller de plusieurs milliers à des dizaines de milliers de psi (livres par pouce carré), afin de s'assurer que le métal en fusion pénètre dans tous les détails du moule.
2. Solidification :
Cela se produit lorsque le métal est injecté dans la cavité du boîtier, qu'il refroidit et qu'il durcit. La qualité de la coulée dépend de la vitesse de refroidissement. D'autres modes de défaillance (cisaillement, montée et glissement) entrent en jeu dans ce cas et se traduisent par un refroidissement plus rapide, une plus grande résistance et un meilleur état de surface, et par un refroidissement plus lent qui pourrait entraîner davantage de défauts internes et des propriétés mécaniques moindres. Les systèmes de refroidissement à l'eau intégrés au moule sont généralement utilisés pour faciliter le processus de refroidissement.
3. Expulsion :
Ensuite, on laisse le métal refroidir et se solidifier et il est alors facile de retirer le moule de la coulée plus importante et d'éjecter la pièce. La plupart du temps, il s'agit alors de pousser la pièce hors du moule à l'aide d'un système d'éjection mécanique. Cela dépend de la complexité de la pièce qui nécessite d'autres étapes supplémentaires, à savoir l'ébarbage et l'usinage pour obtenir la forme et les dimensions finales.
4. Contrôle de la qualité :
Un contrôle de qualité est ensuite effectué sur une pièce après son éjection. Il peut s'agir d'une vérification dimensionnelle, d'une inspection visuelle et d'essais mécaniques pour confirmer que la pièce est égale ou supérieure aux exigences. Le moulage sous pression permet théoriquement d'obtenir une précision et une répétabilité élevées.
Types de moulage sous pression
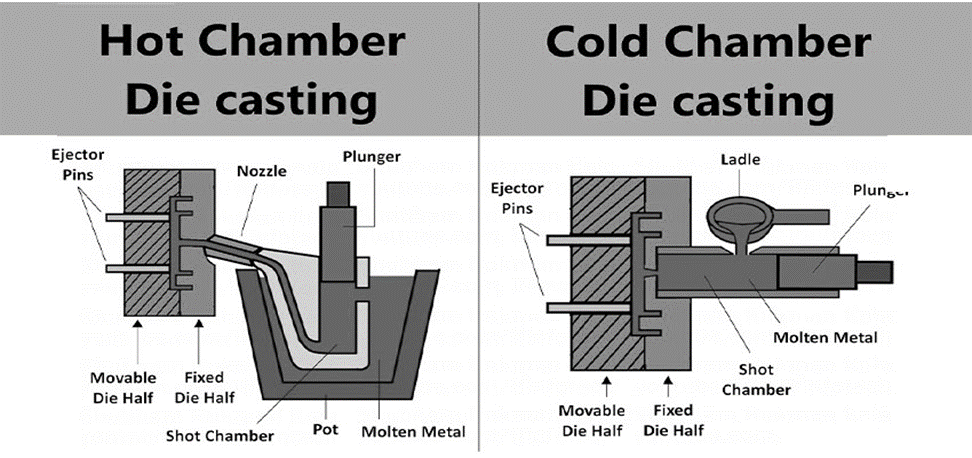
Il existe deux types de moulage sous pression : le moulage sous pression à chambre chaude et le moulage sous pression à chambre froide. Ils sont tous bons et ont leurs avantages, leurs limites et leurs applications idéales.
1. Moulage sous pression à chaud
Le procédé le plus adapté aux métaux tels que le zinc, le magnésium et le plomb est le moulage sous pression en chambre chaude, car le processus se déroule à des températures et des points de fusion élevés. Le système d'injection est installé à l'intérieur du four de fusion, de sorte que le métal est toujours en contact avec la chambre.
Avantages :
- Étant donné que le métal en fusion est disposé à être injecté dans la matrice parce qu'il se trouve dans la chambre d'injection, le moulage sous pression à chambre chaude prend moins de temps que le moulage sous pression à chambre froide.
- Une seule étape : elle implique un nombre réduit de composants et de temps de préparation et est donc considérée comme économique, en particulier pour les opérations à haut volume.
- Pour certains métaux : le moulage sous pression en chambre chaude est plus approprié lorsque les métaux à utiliser ont des températures de fusion basses, de sorte que la contamination des métaux est faible ou inexistante.
Inconvénients :
- Ne peut pas être utilisé pour les ouvrages métalliques à point de fusion élevé comme l'aluminium et le laiton en raison de la température élevée du métal qui fait fondre la chambre.
- Tous les composants sont exposés au métal en fusion et le niveau d'usure est donc élevé au fil du temps.
2. Moulage sous pression en chambre froide
Les métaux qui ont des points de fusion plus élevés, comme l'aluminium, le laiton et le cuivre, sont coulés dans une chambre froide. Dans ce cas, le métal en fusion est prélevé dans un second four et injecté dans la chambre froide, puis dans la cavité du moule.
Avantages :
- En termes de polyvalence dans le choix des matériaux, le moulage sous pression en chambre froide offre une polyvalence dans l'utilisation des matériaux qui permet d'utiliser des matériaux ayant des points de fusion élevés.
- Meilleur contrôle de la qualité du métal : Le cylindre de métal en fusion étant versé séparément dans la chambre, la qualité du métal peut être bien contrôlée afin d'éviter toute contamination.
- Augmentation de la durée de vie des outils : Comme il n'est plus en contact avec le métal tout au long du processus d'injection, la durée de vie de l'outil est prolongée.
Inconvénients :
- Temps de cycle plus lent : le versement manuel du métal dans la chambre prolonge le cycle.
- Le coût sera plus élevé car il s'agit d'une procédure supplémentaire avec un équipement plus complexe.
Comparaison des méthodes de moulage sous pression : chambre chaude et chambre froide
Voici une comparaison des types les plus courants de deux méthodes de coulée sous pression,
Fonctionnalité | Moulage sous pression à chaud | Moulage sous pression en chambre froide |
Compatibilité avec les métaux | Meilleur pour les métaux à bas point de fusion (par exemple, le zinc, le plomb) | Idéal pour les métaux à point de fusion élevé (aluminium, laiton, etc.) |
Durée du cycle | Des cycles plus rapides | Des temps de cycle plus lents |
Usure des moules | Usure plus importante des moules en raison du contact direct avec le métal en fusion | Diminution de l'usure des moules |
Coût | Coût réduit pour la production en grande quantité | Coût initial plus élevé, mais meilleur pour les métaux à haute résistance |
Complexité des pièces | Bon pour les pièces plus simples | Meilleur pour les pièces plus complexes et plus grandes |
Avantages de la coulée sous pression
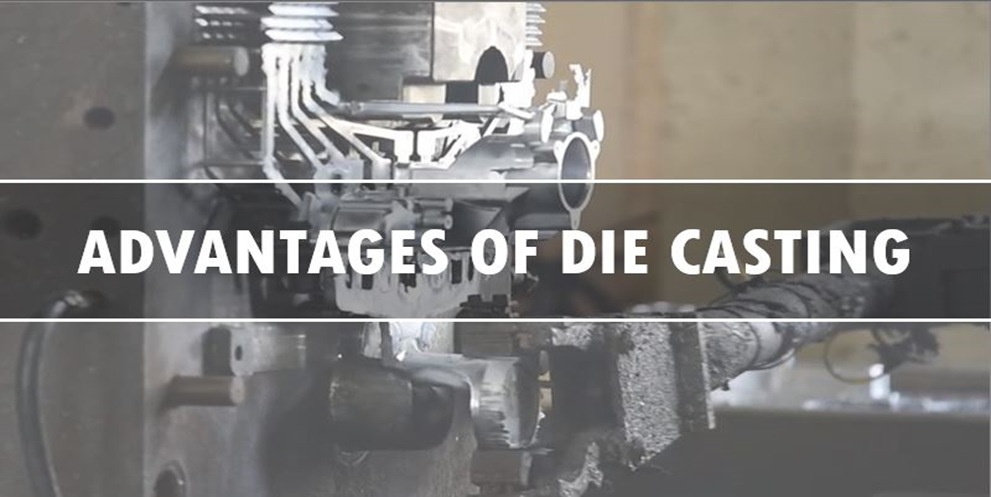
C'est l'un des principaux avantages du moulage sous pression, qui est l'une des principales méthodes privilégiées pour la production à grande échelle de produits à partir d'alliages métalliques.
1. Haute précision et exactitude
Le moulage sous pression présente de nombreux avantages et permet d'offrir une grande précision de moulage. Cette méthode de production est également largement utilisée pour la production de pièces qui nécessitent une bonne précision dimensionnelle, ce qui est très important car cela définit les niveaux de tolérance requis pour un travail spécifique. Il convient de noter que le moulage sous pression est la seule technique de fabrication capable de produire des pièces données avec la plus grande complexité, notamment en ce qui concerne la complexité des géométries.
2. Taux de production élevés
En termes de volumes importants, le moulage sous pression est très efficace. Les pièces sont produites rapidement et à moindre coût dès que le premier moule est créé, avec très peu de main-d'œuvre. La demande de poudres simulées est particulièrement élevée dans des secteurs tels que l'automobile et l'électronique, où de grands volumes de pièces identiques sont nécessaires.
3. Conceptions complexes et parois minces
Le moulage sous pression permet de réaliser des conceptions complexes qu'il serait difficile, voire impossible, d'obtenir par les méthodes de fabrication traditionnelles. Ce procédé permet de fabriquer des pièces à parois minces et à structures internes complexes, et de réaliser des contre-dépouilles, ce qui en fait l'application la plus appropriée dans les cas où l'espace est limité.
4. Efficacité des matériaux
Le moulage sous pression minimise les déchets de matériaux. La pression utilisée pour injecter le métal en fusion remplit chaque partie de la cavité du moule, ce qui réduit les déchets. En outre, de nombreuses pièces moulées sous pression peuvent être recyclées, ce qui contribue à la durabilité du processus.
5. Excellente finition de surface
La finition de surface des pièces produites par moulage sous pression est lisse et esthétique. Il nécessite moins de processus de finition secondaires, tels que le polissage ou le revêtement, ce qui permet d'économiser du temps et de l'argent.
Quelles sont les applications possibles dans le cadre du processus de moulage sous pression ?
Les métaux non ferreux sont principalement utilisés dans le moulage sous pression en raison de leurs bonnes caractéristiques de moulage. Les alliages d'aluminium sont les matériaux couramment utilisés pour le moulage sous pression, comme l'indiquent les matériaux suivants.
1. Alliages d'aluminium

En raison de sa légèreté, de sa résistance à la corrosion et de son excellente conductivité de la chaleur et de l'électricité, l'aluminium est le matériau le plus utilisé dans le moulage sous pression. Si l'on poursuit la liste, des qualités spéciales d'alliages d'aluminium sont utilisées lorsque le rapport résistance/poids est important, en particulier dans les industries automobile, aérospatiale et électrique. Enfin, ils sont également stables sur le plan dimensionnel, ce qui les rend appropriés pour la production de pièces de haute précision.
2. Alliages de zinc
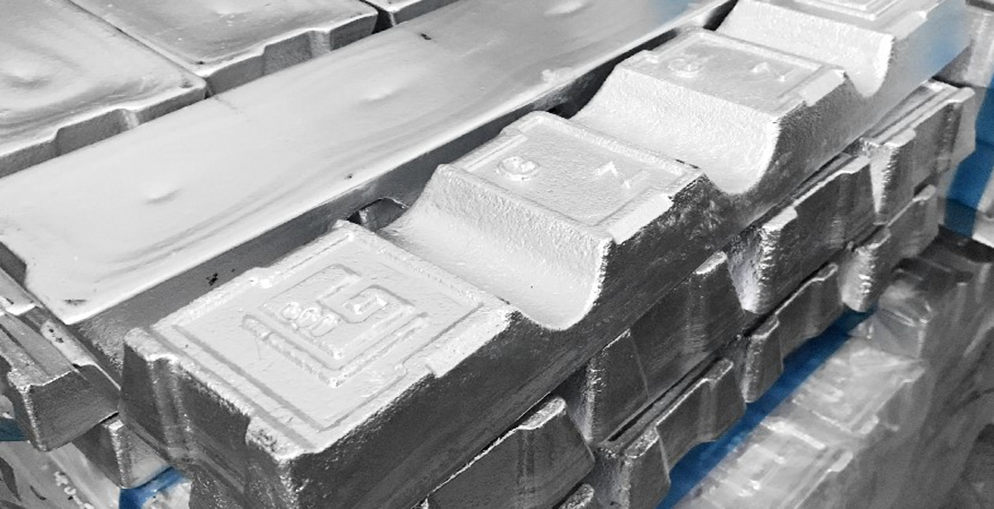
Les alliages de zinc coulés sous pression peuvent être préférés en raison de leurs propriétés telles qu'un point de fusion bas et une grande fluidité, ce qui permet de réaliser plus facilement et plus efficacement des conceptions complexes comportant des sections fines et des détails précis. Ces pièces en zinc possèdent une grande robustesse, sont également résistantes à la corrosion et présentent un polissage de haute qualité. Un autre domaine d'application des alliages de zinc est la fabrication de pièces détachées pour les voitures et autres véhicules, le matériel informatique et l'électronique.
3. Alliages de magnésium

Il convient de mentionner que le magnésium est le métal structurel le plus léger et qu'il offre donc un poids significatif dans les pièces destinées aux automobiles ou aux avions. En effet, les alliages de magnésium sont utilisés dans des pièces qui doivent être solides mais aussi légères que possible. Cependant, le métal étant très réactif, l'alliage est bien géré lorsqu'il est soumis au processus de moulage sous pression.
4. Alliages de cuivre
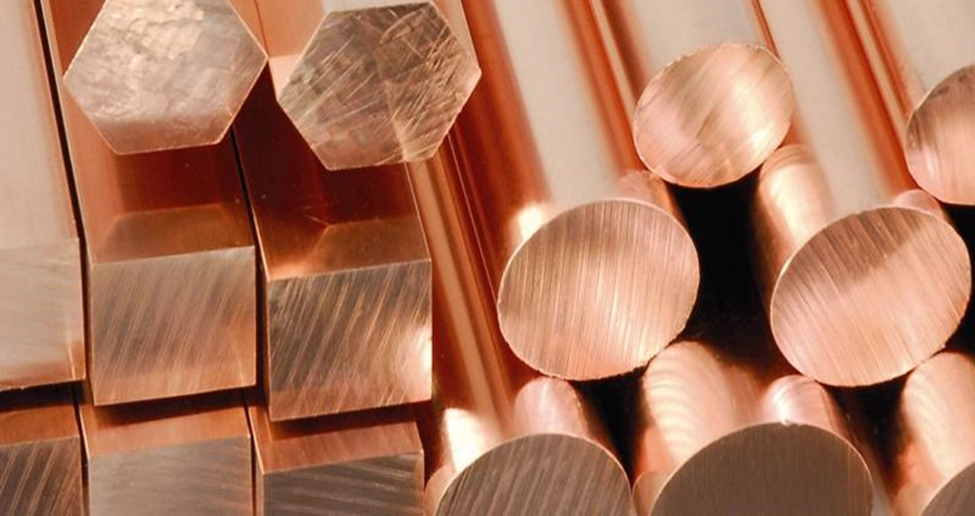
Outre l'aluminium et le zinc, les alliages à base de cuivre, le laiton et le bronze sont également utilisés dans le moulage sous pression, mais pas aussi fréquemment que l'aluminium et le zinc. Ils offrent de bonnes propriétés de résistance à l'usure et sont souvent utilisés pour des applications électriques et de plomberie.
Il est très important de noter que différentes formes de matériaux de base conviennent à différentes applications et que les coûts varient d'une forme à l'autre, de même que les propriétés du produit final.
Moulage sous pression et autres méthodes de moulage
Par rapport aux méthodes de moulage telles que le moulage en sable, le moulage à la cire perdue et le moulage en moule permanent, cette section pourrait être la section de comparaison du moulage sous pression. Ce faisant, il est judicieux de souligner les forces et les faiblesses de chaque méthode, afin d'enseigner aux lecteurs quand choisir le moulage sous pression par rapport à d'autres alternatives. Par conséquent, il pourrait s'agir d'un aperçu comparatif qui aiderait à déterminer la méthode de moulage optimale en fonction du matériau de la pièce, de sa complexité et du volume de production.
Fonctionnalité | Moulage sous pression | Moulage au sable | Moulage à la cire perdue |
Précision | Haute précision avec des tolérances serrées | Précision moindre et finition de surface rugueuse | Haute précision et finition lisse |
Vitesse | Plus rapide pour la production en grande série | Cycle de production plus lent | Ralentissement dû à la préparation du moule |
Déchets matériels | Un minimum de déchets | Plus de déchets en raison d'une finition plus rugueuse | Déchets minimes, mais moules plus complexes |
Coût | Rentabilité pour les volumes élevés | Coût réduit pour la production de faibles volumes | Coûts plus élevés en raison de la complexité et de la main-d'œuvre |
Les processus de production du moulage sous pression et du moulage par injection seront comparés.
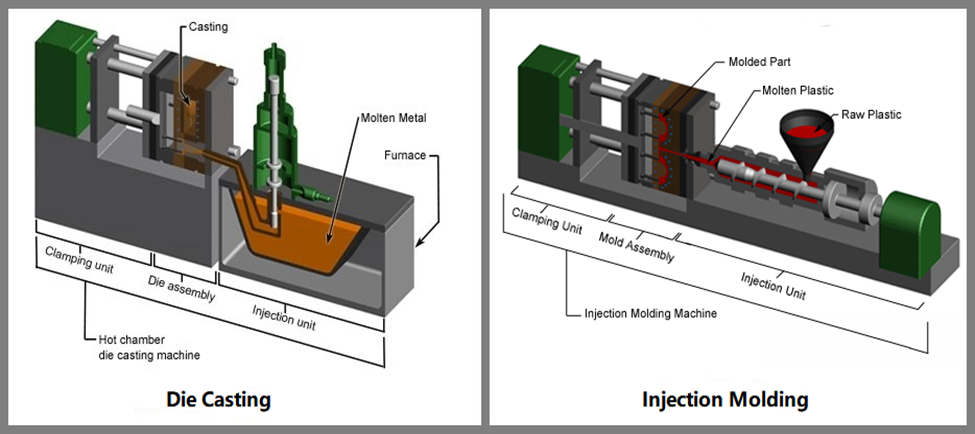
Le moulage sous pression et le moulage par injection sont deux techniques couramment utilisées pour fabriquer des pièces aux détails fins et aux formes complexes. Bien que ces deux techniques impliquent l'utilisation de matériaux formant des détails pour produire des produits finaux, elles présentent des différences en termes de type de matériau, de produit formé et, plus particulièrement, d'avantages liés à chaque processus.
1. Matériaux utilisés
Moulage sous pression : Le moulage sous pression est surtout utilisé avec d'autres métaux que les métaux ferreux, notamment les alliages d'aluminium, de zinc, d'acier et de cuivre. Les métaux sont chauffés puis coulés dans un moule par pression hydraulique. Le moulage sous pression est donc la méthode la plus appropriée pour fabriquer des pièces solides, durables et capables de résister à des températures élevées.
Moulage par injection : Le moulage par injection est couramment utilisé entre les matières plastiques, et est rarement possible sur les métaux et les verres. Ces polymères comprennent le polyéthylène, le polypropylène ainsi que le polystyrène dans leur liste de polymères fréquemment utilisés. Le matériau de formation du produit est également léger et flexible, et en plus, il y a ses faibles coûts et ses formes assez complexes, il est donc possible de noter que le moulage par injection est parfait pour ce type de produit.
2. Différences de processus
Moulage sous pression : Comme son nom l'indique, il s'agit d'un processus d'injection de métal en fusion à haute pression dans la matrice. Après le refroidissement et la solidification du métal à très grande vitesse, les pièces sortent avec une tolérance fine et un bon état de surface, sans qu'aucune autre opération ne soit nécessaire.
Moulage par injection : Le moulage par injection consiste à injecter de la matière plastique fondue dans une cavité du moule en appliquant une pression, il s'agit donc d'un moulage par injection. Lorsque la température du plastique fondu a baissé, le moule s'ouvre et le produit est le moule en plastique. Le moulage par injection peut également offrir une grande précision, bien qu'il soit généralement utilisé pour produire des pièces relativement plus petites et plus légères que le moulage sous pression.
3. Applications
Moulage sous pression : Le moulage sous pression est utile pour fabriquer des pièces dures et solides utilisées dans la construction automobile, l'aéronautique et d'autres produits électroniques en raison de son excellente résistance à la chaleur.
Moulage par injection : Elle peut être utilisée pour produire des produits de consommation, des emballages, des dispositifs médicaux et des jouets, car c'est là que la flexibilité, la facilité de conception et la production à faible coût sont importantes.
Applications du moulage sous pression

L'un des facteurs qui a fait du moulage sous pression un processus de fabrication populaire dans de nombreuses industries est qu'il permet de produire des pièces durables et de haute qualité avec des géométries assez compliquées. Voici quelques-unes de ses applications :
1. L'industrie automobile
En général, les composants des moteurs, les boîtiers de transmission et d'autres pièces automobiles importantes sont fabriqués par moulage sous pression. Les pièces moulées sous pression ont la précision et la résistance nécessaires pour être installées dans des applications exigeantes de l'industrie automobile.
2. Industrie électronique
Dans le secteur de l'électronique, le moulage sous pression est utilisé pour produire des boîtiers pour les équipements électroniques tels que les téléphones mobiles, les ordinateurs portables et les téléviseurs. Cette technique permet de construire des boîtiers légers, mais solides, qui protègent les composants délicats.
3. Industrie aérospatiale
Le moulage sous pression est très utile aux entreprises de fabrication aérospatiale, car il leur permet de produire des pièces légères très résistantes, nécessaires aux avions et aux engins spatiaux. Les pièces moulées sous pression ont la précision et les propriétés matérielles nécessaires pour être utilisées dans des applications où la performance et la sécurité sont des questions importantes.
4. Équipement industriel
Les pièces de machines, d'outils et d'autres équipements industriels sont également moulées sous pression. Parce qu'il permet de produire des pièces dont la géométrie présente des détails complexes et de bonnes propriétés mécaniques, le moulage sous pression est un bon outil pour ces applications.
Conclusion
Le moulage sous pression est un procédé de fabrication polyvalent, rentable et efficace, utilisé dans de nombreuses industries. La qualité produite est extrêmement élevée en termes de tolérances des pièces, d'état de surface et de cadences de production élevées, ce qui en fait un excellent outil de fabrication pour les pratiques de fabrication modernes d'aujourd'hui. Le moulage sous pression répond aux besoins d'un grand nombre d'industries qui exigent des pièces robustes, précises et efficaces - de l'automobile à l'aérospatiale, de l'électronique à l'équipement industriel.
Bien que la technologie se développe rapidement et qu'elle continuera probablement à être utilisée comme source de composants métalliques d'excellente qualité à grande échelle, dans les pays de l'Union européenne, il n'est pas possible d'obtenir des résultats satisfaisants. moulage sous pression. Une meilleure compréhension des principes fondamentaux du moulage sous pression peut aider les professionnels de l'ingénierie, de la fabrication et de la conception à prendre des décisions éclairées sur la manière d'utiliser le processus de moulage sous pression pour obtenir le résultat souhaité.
FAQ sur le moulage sous pression
1. Quel est le cycle de temps pour le moulage sous pression et le moulage par injection ?
La durée du cycle pour une pièce donnée est comprise entre 15 et 5 minutes pour le moulage sous pression et entre 10 et 60 secondes pour le moulage par injection.
2. Le moulage sous pression peut-il être utilisé pour des pièces en plastique ?
Le moulage sous pression n'est pas utilisé pour les non-métaux. On utilise généralement les techniques connues sous le nom de moulage par injection pour produire les pièces en plastique.
3. Quels sont les produits les mieux adaptés au processus de fabrication du moulage sous pression ?
Le moulage sous pression est plus approprié pour la fabrication de pièces compliquées de petite et moyenne taille, d'une grande précision, qui sont faites de métaux. Parmi les produits mécaniques fabriqués, on peut citer les voitures et les pièces et accessoires automobiles, les boîtiers et caisses de matériel électrique, les pièces électroniques et les boîtiers d'équipement, entre autres.
4. En quoi le moulage sous pression est différent du moulage en sable.
Pourtant, si l'on compare les deux, on constate que le moulage sous pression est plus précis : Le moulage sous pression est plus précis et prend moins de temps que le moulage en sable. Alors que le moulage au sable est préférable pour les pièces de grande taille et moins compliquées, le moulage sous pression est préféré pour les pièces de petite taille et complexes, car il permet d'obtenir des surfaces plus lisses et des tolérances plus étroites, qui sont typiques des grandes séries de production.
5. Qu'est-ce qui détermine le coût du moulage sous pression ?
Parmi les considérations susceptibles d'influencer le coût du moulage sous pression, citons : le type de matériau, la complexité de la pièce, la conception de la matrice et la quantité des commandes. L'outillage léger dépend du volume, bien qu'un volume élevé maintienne le coût unitaire à un faible niveau, les coûts initiaux de l'outillage sont élevés.