Yksi tällainen metalliseos, jota käytetään laajalti valmistus- ja valuteollisuudessa, on sinkkipohjainen Zamak 5 -seos, jolla on joitakin ainutlaatuisia ominaisuuksia. Tämä johtuu Zamak 5:n suuresta lujuudesta, erinomaisesta kestävyydestä ja hyvästä korroosionkestävyydestä, mikä tekee siitä ihanteellisen materiaalin käytettäväksi painevalutoiminnoissa. Uuttamisen jälkeen Zamak 5 sulaa erittäin vähän ja sillä on erinomaiset valuominaisuudet, mikä tekee Zamak 5:stä ihanteellisen materiaalin autoteollisuudelle sekä kulutustuote- ja rautateollisuudelle. Teollisuuden osallistujat saavat varmuuden Zamak 5 -seoksen ominaisuuksista, kuten koostumuksesta ja erilaisista konkreettisista käyttökohteista, jotta he voivat tehdä tuotantopäätöksiä ja optimoida prosessin toiminnan tehokkuuden.
Artikkelissa käsitellään Zamak 5 metalliseos kautta sen kemiallisen koostumuksen ja valmistus menetelmiä lämpötilan ja paineen ylläpidon ohella sekä mekaanisen aineen ominaisuuksia teolliseen suorituskykyyn.
Zamak 5 Alloy Yleiskatsaus
Zamak 5 toimii johtavana sinkkipohjaisena seoksena, jota teollisuus kutsuu sinkki-alumiiniseokseksi. Zamak 5 koostuu kemiallisesti 3,5-4,3 prosentista alumiinia, 0,03-0,08 prosentista magnesiumia ja 0,75-1,25 prosentista kuparia. Se saa ylivoimaisen lujuutensa myös elementeistä, joita valmistaja voi käyttää luodakseen lujia komponentteja, joita käytetään auto- ja ilmailuteollisuudessa sekä kulutustavarateollisuudessa. Vetolujuus sekä tiheys 6,7 g/cm³ ja suhteellisen laaja sulamispistealue 380-385 °C ovat tässä metalliseoksessa sen hyvän kestävyyden ja hyvän tarkkuuden vuoksi.
Zamakin koostumus ja ominaisuudet 5

Zamakin kemiallinen koostumus 5
Zamak 5:n mekaanisia ominaisuuksia parannetaan sekoittamalla siihen sinkkipohjaista seosta, jossa on hallittu sinkki-, alumiini-, kupari- ja magnesiumprosentti.
Tämä helposti sulava ominaisuus on yksi niistä ominaisuuksista, jotka tekevät Zamak 5:stä erinomaisen painevaluseoksen verrattuna 96-98%-seokseen, joka on sinkkiä. Erinomaisten tulosten saavuttamiseksi on ratkaisevan tärkeää käyttää sinkkimateriaalia, jonka puhtausaste on 99,99%, jotta vältetään epäpuhtaudet, jotka heikentäisivät seoksen lujuutta ja rakenteellista eheyttä.
Zamak 5 -materiaalin jähmettyminen paranee lisäämällä alumiinia (3,5-4,3%), koska se parantaa seoksen mikrorakennetta. Alueilla on e koostumus, joka muodostaa ne, joissa yhdistyvät materiaalirakenteen sitkeys- ja kovuusominaisuudet. Zamakissa oli mitattava tarkka alumiinipitoisuus, jotta vältettäisiin materiaalivirheet, kuten halkeilu sekä haurausongelmat.
Magnesiumin esiintyminen zamak 5:ssä välillä 0,03%-0,08% johtuu siitä, että tämän alkuaineen kanssa epäpuhtaudet estävät mikrosäröjen korroosion raerajoilla. Koska tämä lisäys tekee seoksesta juoksevamman, muotti hyötyy siitä, että se saa paremmat täyttöominaisuudet. Magnesiumin pois jättäminen tekee Zamak 5:n pinnasta viallisen ja lisäksi sen työstäminen on erittäin vaikeaa.
Zamak 5 on grafiittivalettu, ja sillä on hyvä kulutuskestävyys ja lämpökäsittelykyky, kun kuparia lisätään 0,75-1,25 prosenttia, mikä parantaa virumiskestävyyttä, mikä soveltuu lämpövaihtelusovelluksiin. Koska Zamak 5 haurastuu, kun oikeat rajat ylitetään, kuparin osuus on tärkeä.
Zamakin fysikaaliset ominaisuudet 5

Zamak 5 -materiaalin paino on 6,7 g/cm³, ja sen tiheys on teräksen välillä ja suurempi kuin alumiiniseosten. Suotuisan paino-lujuus-suhteensa ansiosta Zamak 5 soveltuu moniin rakenteisiin, joissa käytetään vahvoja materiaaleja, joiden paino on pieni.
Zamak 5 sulaa 380-385 celsiusasteen välillä, mikä tekee zamak 5:n tarkasta valusta kustannustehokasta alumiiniin verrattuna.
Zamak 5:n vetolujuus 120 °C:n keskilämpötilassa oli 330 MPa, ja sen myötölujuus oli 220 MPa ja venymispotentiaali 7-10%, mikä täyttää teollisen käytön vaatimukset. Zamak 5 on vahva ja mukautuva, koska sillä on korkea myötölujuus 220 MPa ja 7-10%:n suurin venymä ennen lähes murtumista.
Zamakin mekaaniset ominaisuudet 5
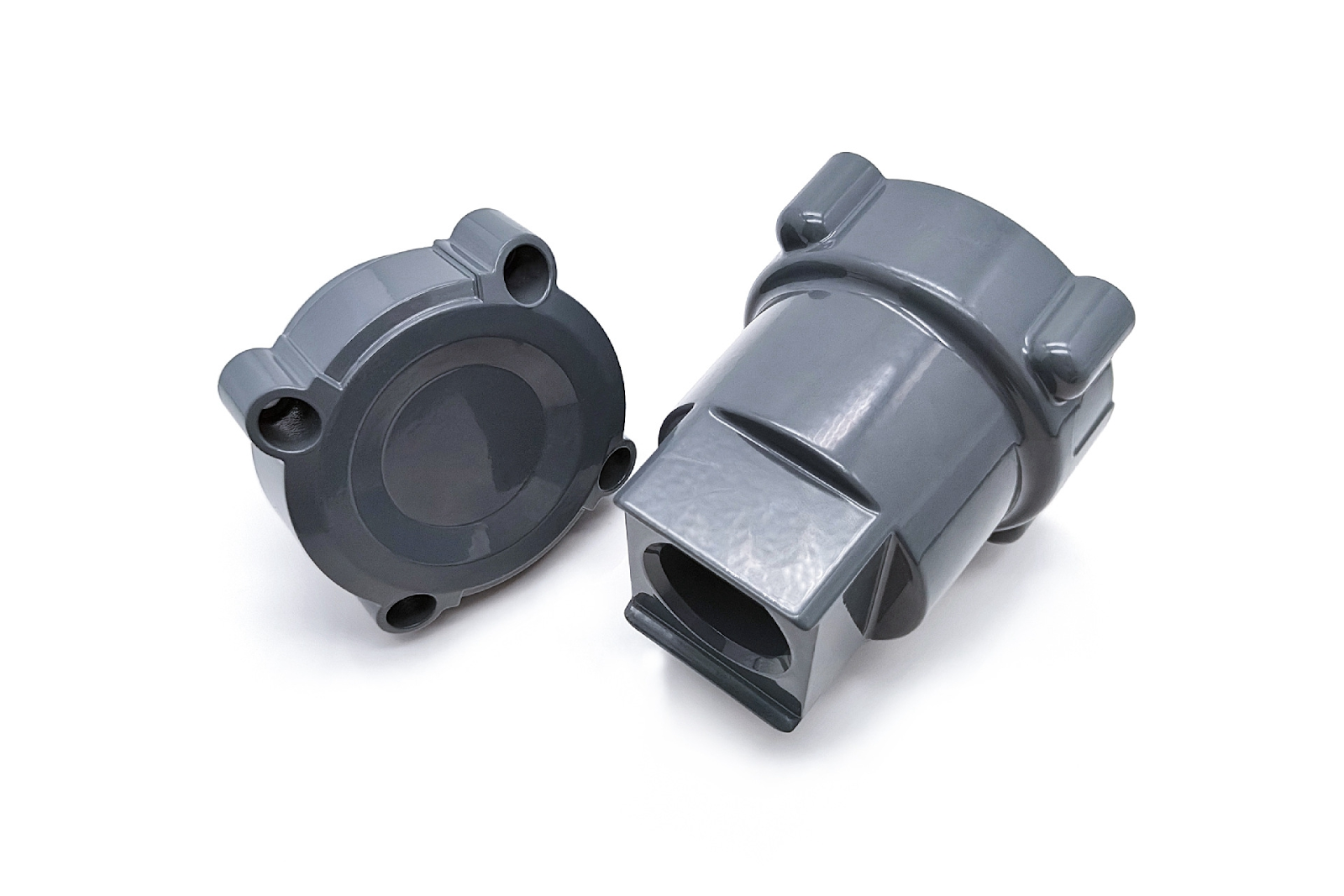
Zamak 5:n 91 HB Brinell-kovuus on täydellisesti lujuuden ja pintakovuuden välissä, joten se on erinomainen yhdistelmä koristeellisiin kahvoihin tai muihin kulumissuojaa vaativiin osiin.
Iskunkestävyys:
Materiaalin huoneenlämpötilan Charpy-iskulujuus on 53 J, kun taas -20 °C:ssa se laskee 35 J:iin. Seoksella on korkea iskunkestävyys, joten se voi suojautua mekaanisilta rasituksilta ja värähtelyiltä dynaamisissa voimaolosuhteissa.
Zamak 5 kestää 100 MPa:n syklistä rasitusta ja selviää vioittumatta jopa 1 miljoonasta syklistä. Zamak 5 toimii käytännössä luotettavan vakaasti jatkuvassa kuormituksessa, joten se soveltuu koneen osiin ja pesukoneen osiin.
Zamak 5 -seoksen mekaaniset ominaisuudet
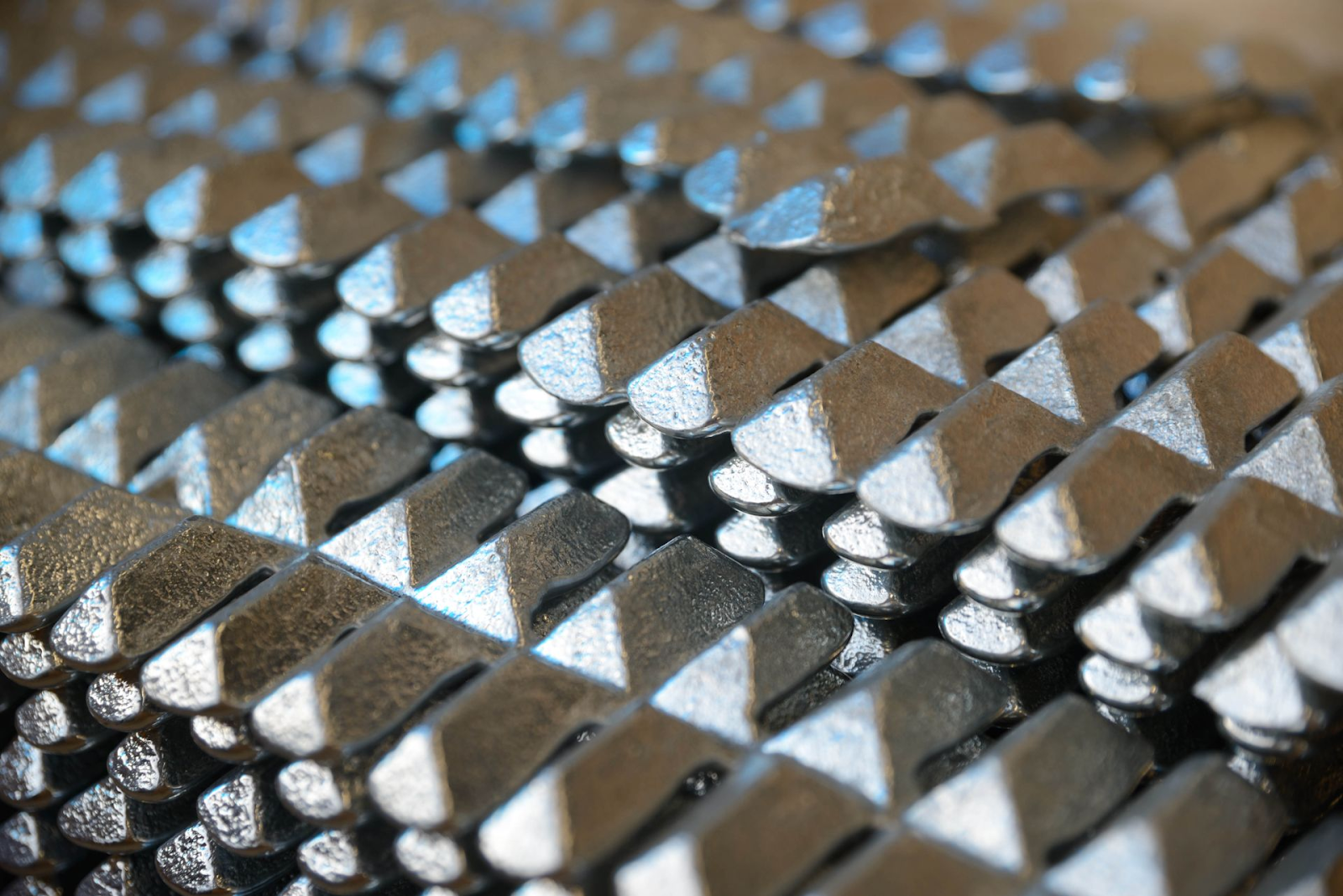
Alla olevassa taulukossa esitetään Zamak 5 -alumiiniseoksen keskeiset mekaaniset ominaisuudet.
Kiinteistö | Arvo |
Brinellin kovuus | 91 HB |
Murtovetolujuus | 328 MPa |
Myötölujuus (0.2%) | 269 MPa |
Leikkauslujuus | 262 MPa |
Puristuslujuus | 600 MPa |
Väsymislujuus | 56,5 MPa |
Iskulujuus | 65 J |
Kimmomoduuli | 96 GPa |
Venymä | 7% 50 mm:n mitoissa |
Zamak-seoksen lujuusarvot osoittavat, miten se kestää rasitusta, ja sijoittavat sen muiden materiaalien joukkoon, jossa sitä voidaan käyttää vaativissa sovelluksissa. Zamak 5 kestää erinomaisesti väsytyskuormitusta ja iskuja, joten se soveltuu osiin, joihin kohdistuu toistuvia voimakuormituksia.
Zamak 5 -seoksen fysikaaliset ominaisuudet
Zamak 5:n käyttäytymistä säätelevät kaikki sen ominaisuudet.
Kiinteistö | Arvo |
Sulamisalue | 380-386°C |
Tiheys | 6,60 g/cm³ |
Sähkönjohtavuus | 26% IACS |
Lämmönjohtavuus | 109 W/mK |
Ominaislämpökapasiteetti | 419 J/kg-°C |
Lämpölaajenemiskerroin | 27,4 µm/m°K |
Poissonin luku | 0.30 |
Zamak 5:n ominaisuuksien yhdistelmän ansiosta se toimii hyvin erilaisissa ympäristöissä ja käyttöolosuhteissa, jotka soveltuvat sekä lämmön- että sähkönjohtavuuden kannalta. Sopivat tiheysominaisuudet ja lämpökyky tekevät Zamak 5:stä välttämättömän lämpöherkissä järjestelmissä, ja sillä on myös hyvät sähköiset ominaisuudet, jotka tarjoavat vaihtelua sähköisen osan käyttömuodossa.
Zamak 5 -seoksen edut
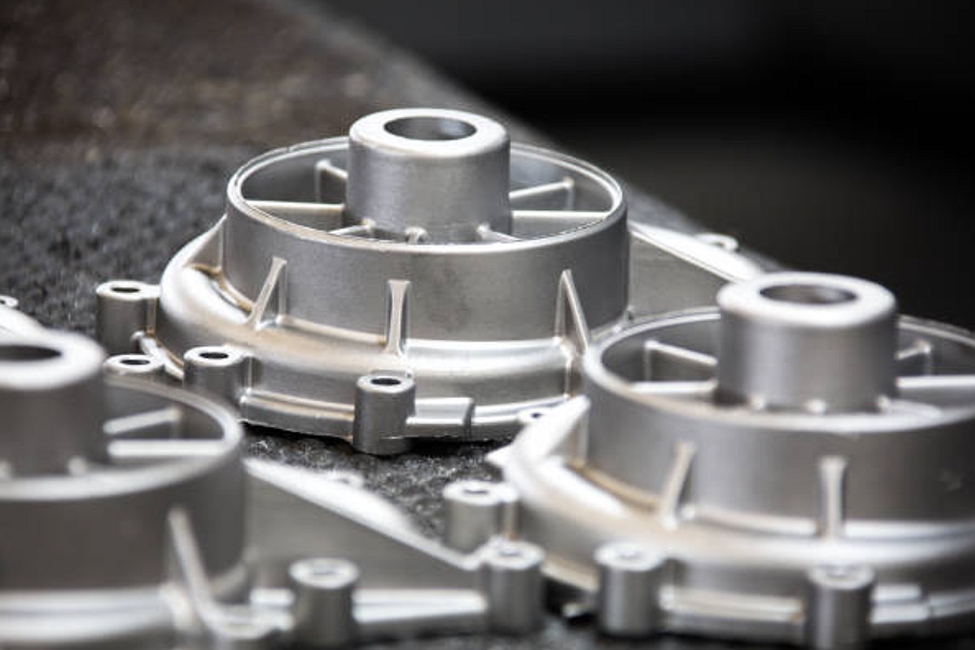
Vertailun vuoksi Zamak 5:n ylivoimaiset lujuusominaisuudet, joita se osoittaa samalla pienemmällä painolla, johtuvat siitä, että sen lujuus/paino-suhde on 49 MPa, joka ylittää A380-alumiinin. Koska Zamak 5:lle on ominaista korkea lujuus ja korkea painotehokkuus, sitä voidaan käyttää menestyksekkäästi erilaisissa teollisissa sovelluksissa, jotka liittyvät auto- ja ilmailu- ja avaruusteollisuuteen.
Hyvä korroosionkestävyys: Seoksensa ansiosta Zamak 5 on ylivoimainen korroosiota vastaan muissa suolaisissa ja kosteissa olosuhteissa, joissa seos tarjoaa täydelliset edut merenkulun laitteistoille ja alttiille sovelluksille. Zamak 5 on testattu laboratoriossa, eikä materiaalin altistaminen suolasuihkulle yli 500 tunnin ajan vahingoita pintaa.
Erinomainen valettavuus: Zamak 5 soveltuu erityisen hyvin painevaluun, koska metalli on riittävän juoksevaa, jotta se virtaa helposti monimutkaisiin valumuotoihin. Valmistajat käyttävät Zamak 5:n valettavuutta hyväkseen nopealla ja helpolla helppokäyttöisellä jälkituotannolla, joka vaatii minimaalista ja erityisesti silloin, kun geometristen mittojen vaihtelut eivät vaikuta toimintaan.
Suuri sitkeys: Zamak 5 voidaan kylmämuovata prosesseilla, jotka onnistuvat sen sitkeyden vuoksi ja jotka vaihtelevat välillä 7% ja 10%. Zamak 5 sallii taivutus- ja kuristus- sekä poraustoiminnot, mikä mahdollistaa Zamak 5:n parantamisen sen valmistuksen monipuolisuuden lisäämisen ansiosta.
Zamakin valmistusprosessi 5
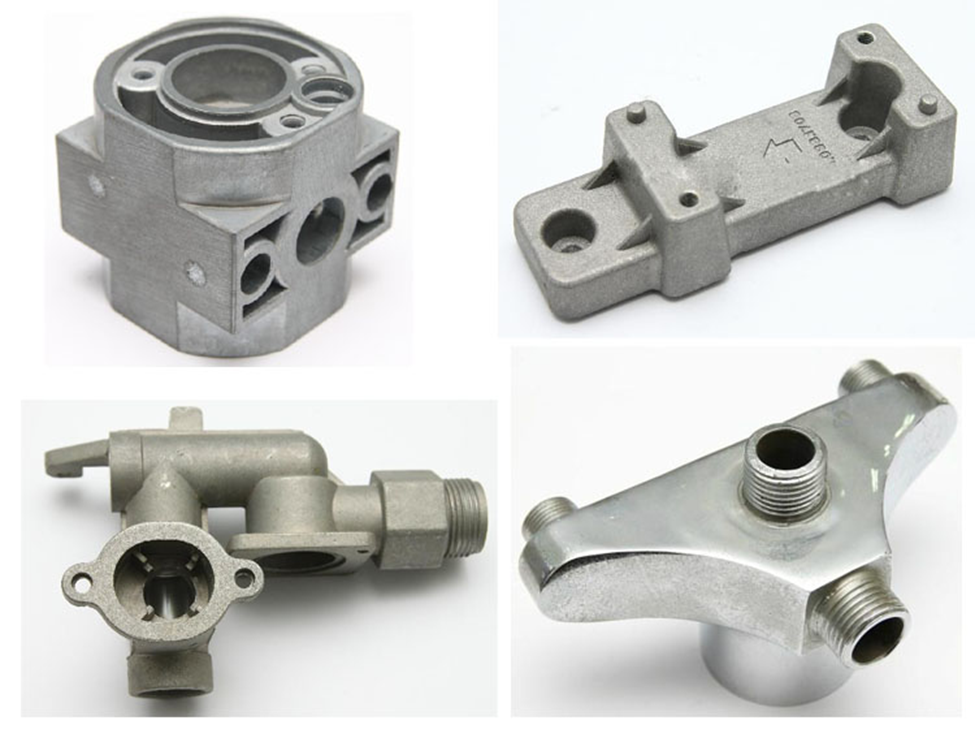
Die Casting prosessi
Zamak 5 -materiaalin sulamispiste on alhainen, minkä vuoksi materiaalia ei voida valmistaa makroruiskupuristimella, vaan se on mahdollista valmistaa kuumakammiopuristimella. Sula metalli otetaan korkeassa paineessa teräsmuottiin, josta valmistetaan kappaleita, joissa on tiukka toleranssi ja hieno pinta. Menetelmällä saavutetaan kuitenkin erinomaiset hyötysuhteet erityisesti silloin, kun tuotteita on valmistettava suuria määriä.
Prosessin parametrit
Itse asiassa kolme ratkaisevaa prosessiparametria ovat: ruiskutuspaine 700-1000 bar yhdessä muotin lämpötilan 150-200 °C ja jäähdytysnopeuden 50 °C/s kanssa. Mekaanista laatua, joka on erinomainen, on valvottava erittäin tarkasti, jotta tuotteen virheet saadaan mahdollisimman pieniksi.
Koneistus ja viimeistely
Zamak 5 on ominaisuuksiensa ansiosta helposti käytettävissä valuvaiheen jälkeisiin viimeistelyprosesseihin. Tuotteen suuri sitkeys mahdollistaa tarkat kierteitys- ja uraprotokollat sekä tarkat galvanointimenetelmät ja jauhemaalausmenetelmät korroosiosuojauksen ja esteettisten ominaisuuksien parantamiseksi.
Zamak 5:n ja Zamak 3:n erot
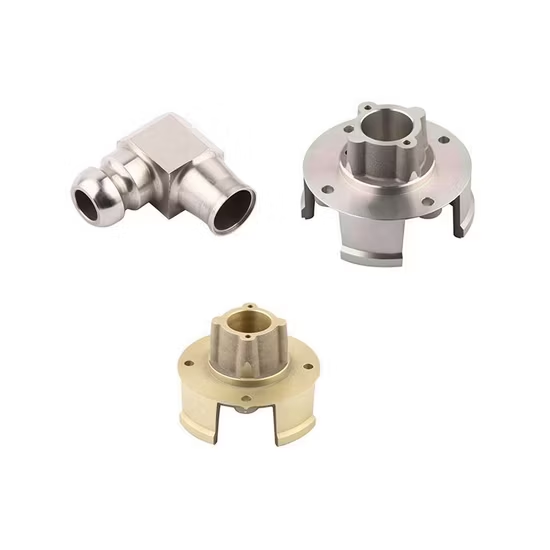
Kemiallinen koostumus: Zamak 5 ei ole Zamak 3, koska se kestää lämpöä kuparielementin sisällyttämisen ansiosta, ja Zamak 3:ssa ei ole kuparia, koska se tarjoaa parhaat valu- ja kosteudenkestävyysominaisuudet.
Mekaaniset ominaisuudet: Zamak 5:llä on suurempi lujuus ja kovuus, joten sillä on paremmat mekaaniset ominaisuudet ja se on käyttökelpoisempi osissa, joissa on kuormitusvaatimuksia kuin Zamak 3.
Zamak 5:n ja Zamak 3:n vertailu
Kiinteistö | Zamak 5 | Zamak 3 |
Kemiallinen koostumus | Sinkki (96-98%), alumiini (3,5-4,3%), magnesium (0,03-0,08%), kupari (0,75-1,25%). | Sinkki (95-97%), alumiini (3,5-4,3%), magnesium (0,02-0,06%), kupari (<0,1%). |
Vetolujuus | 330 MPa | 240 MPa |
Myötölujuus | 220 MPa | 160 MPa |
Venymä | 7-10% | 10-15% |
Kovuus | 91 HB (Brinell) | 80 HB (Brinell) |
Tiheys | 6,7 g/cm³ | 6,6 g/cm³ |
Sulamispiste | 380-385°C | 380-385°C |
Sovellukset | Autoteollisuus, ilmailu- ja avaruusteollisuus, kulutustavarat, lujat sovellukset | Lelut, koriste-esineet, vähän rasitusta aiheuttavat sovellukset |
Tärkein etu | Korkean lämpötilan kestävyys, kulutuskestävyys, parempi lujuus ja kestävyys. | Erinomainen valettavuus, korroosionkestävyys kosteissa ympäristöissä |
Haitta | Vähemmän sitkeää, haurastuu herkemmin korkeammissa lämpötiloissa. | Alhaisempi lämpötilan ja rasituksen kestävyys |
Zamak 5:llä ja Zamak 3:lla on samankaltaiset kemialliset rakenteet, mekaaniset ominaisuudet ja yhteiset käyttötapaukset, ja tämä taulukko osoittaa ne yhdessä paikassa.
Zamak 5 (ASTM AC41A, Z35531, Mazak 5) sinkkiseos
Zamak 5 on sinkki-alumiiniseos, jolla on lukuisia käyttökohteita sen erinomaisten lujuusominaisuuksien ja monipuolisuuden ansiosta. Tämä metalliseos tunnetaan teollisuudessa laajalti Zamak 5:nä, vaikka ASTM-standardien mukaan se on AC41A ja UNS-luokitusjärjestelmän mukaan Z35531. Zamak 5 koostuu primäärisestä sinkistä, joka on seostettu alumiinilla ja kuparilla sen mekaanisten ominaisuuksien, kuten lujuuden, korroosionkestävyyden ja kovuuden, parantamiseksi. Kuten todettu, valmistusominaisuudet koskevat Zamak 5:tä siinä tilassa, jossa se on ennen karkaisuprosesseja tai muita käsittelyjä. Koska Zamak 5 -seosta käytetään painevaluun, sillä voidaan valmistaa sekä monimutkaisia, yksityiskohtaisia että korkealaatuisia osia. Koska Zamak 5 tarjoaa sekä taloudellisen että luotettavan toimintakyvyn, se on vakiinnuttanut asemansa auto- ja elektroniikkatuotteissa sekä koriste-esineissä.
Zamakin sulamispiste 5
Zamak 5 -seoksen sulamisarvot ovat välillä 380-386 °C (716-727 °F), jotka ovat alhaisemmat kuin muiden metallimateriaalien. Koska Zamak,5:n sulamislämpötila on keskimääräistä alhaisempi, sen käytöllä on tärkeä merkitys painevalutoiminnoissa, koska se on helposti muovattavissa alhaisemmissa prosessilämpötiloissa. Seoksen matala sulamisalue helpottaa tarkkuusvalmistusta, koska se vaatii nopeaa sulamista ja jähmettymistä monimutkaisten komponenttien valmistuksessa. Zamak 5:llä on alhainen sulamispiste, minkä vuoksi viimeistelyvalmistajan on helppo valita se lukuisissa autoteollisuudessa sekä huonekalujen ja kulutustavaroiden valmistuksessa.
Zamakin Youngin moduuli 5
Zamak 5 -seoksella on tietyt tekniset ominaisuudet. Youngin moduuli on ~96 giga pascalia (GPa). Tämä arvo kertoo materiaalin jäykkyyden, sillä se kertoo, kuinka paljon materiaali kestää muodonmuutoksia käytetyn rasituksen alaisena. Zamak 5:n keskimääräinen jäykkyys johtuu 96 GPa:n Youngin moduulista, joka on riittävän lähellä sekä lujuus- että joustavuusvaatimusten saavuttamista. Materiaalilla on lujuus, johon se on suunniteltu, ja se on silti joustava, koska sen jäykkyys kohtuullisella asteikolla 96 GPa:ssa (gigapascal) antaa seokselle mahdollisuuden säilyttää rakenteellinen eheys mekaanisten sovellusten aikana.
Vastaavat materiaalit kuin Zamak 5
Eri sovelluksissa tarvitaan erilaisia aineita, ja erityisellä sinkkiseoksella Zamak 5 on erityisominaisuuksia, mutta vastaavia materiaaleja ja muita aineita on olemassa lukuisia. Kolme ensisijaista vaihtoehtoista materiaalia, joita voidaan käyttää Zamak 5:n sijasta, ovat Zamak 3 (ZnAl4Cu1), Zamak 2 ja Zamak 13.
Zamak 3 (ZnAl4Cu1)
Zamak-perheen seosten joukossa, Zamak 3 kuuluu suosituimpiin tyyppeihin, koska se on ominaisuuksiltaan samanlainen kuin Zamak 5. Sinkki-, alumiini- ja kupariaineet, joista nämä seokset saavat kiderakenteensa. Zamak 3:a käytetään Zamak 5:n korvikkeena, koska se sisältää vähemmän kuparia, joka on vastuussa heikommasta lujuudesta ja korroosionkestävyydestä.
Sinkkivalut
Lisäksi Zamak 2:lla ja Zamak 7:llä on hyvä valukyky, minkä ansiosta ne soveltuvat käytettäväksi tuotantoon, jossa vaaditaan suurta tarkkuutta ja korkeaa viimeistelylaatua, sekä sinkkivaluseoksilla. Vaikka näillä seoksilla on erilaiset mekaaniset ominaisuudet, niihin käytetään samoja valmistusprosesseja.
ALSi12
Kun tarvitaan hieman korkeampaa lujuutta korkeammissa lämpötiloissa, käyttäjät voivat korvata ALSi12-alumiini-piiseoksen joillakin vaihtoehtoisilla hankintatarvikkeilla. Zamak 5:n ja ALSi12:n ei tarvitse olla kemialliselta koostumukseltaan samanlaisia, sillä niitä molempia käytetään valu- ja painevalutuotannossa.
ADC 12 (alumiiniseos)
Kun vaaditaan hyvää korroosionkestävyyttä ja valettavuutta, ADC 12 -alumiiniseosta voidaan käyttää vastaavana materiaalina korvaamaan joitakin valmistussovelluksia. Koska Zamak 5 voi olla hieman kovempi, valintaperusteena ovat suorituskykyperusteet.
Tuotantoryhmät valitsevat tällaisen vastineen vetolujuuden ja korroosionkestävyyden sekä kovuuden yksilöllisten mekaanisten ominaisuuksien tasapainon mukaan.
Zamak 5 Valuprosessi
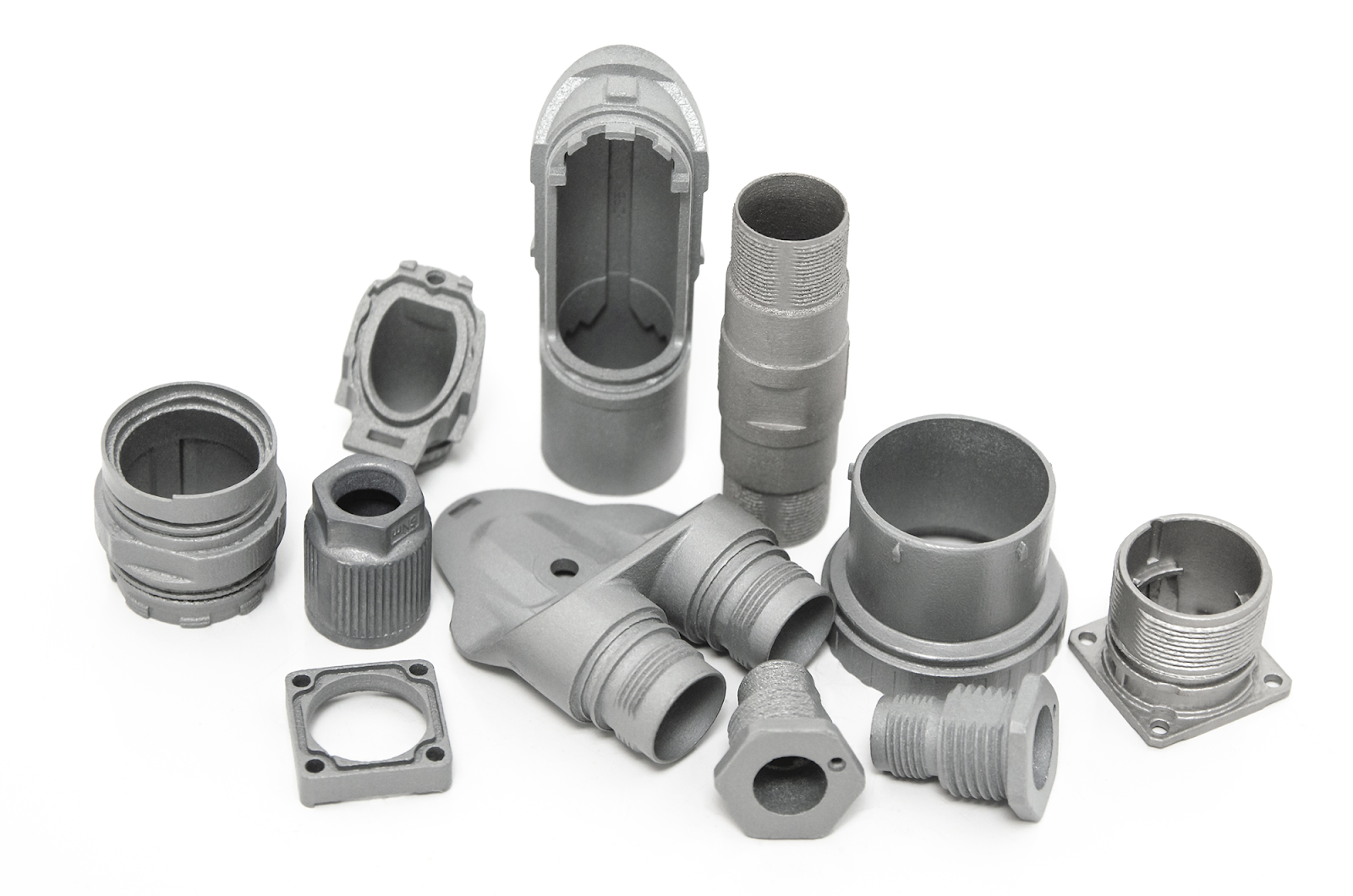
Zamak 5 -valu voidaan säilyttää ja optimoida lopputuotteessa Zamak 5 -valumenetelmän eri vaiheissa. Tärkein Zamak 5 -tuotantomenetelmä on painevalu,g jossa Zamak 5 -sulaa ruiskutetaan korkeassa paineessa metallimuottiin. Zamak 5 -valu koostuu useista peräkkäisistä toiminnoista.
Muotin valmistelu:
Muotti on lämmitettävä tietyn lämpötilan yläpuolelle, jotta näytteen lämpöshokki estetään ruiskutusprosessin aikana. Tämän jälkeen sallimme virran käytön ulkona, jotta varmistetaan, että valupinta ja tuotos ovat aina virheettömiä.
Zamak 5 -seoksen sulattaminen:
Zamak 5:n on kuumennettava 380-390 °C:n (716-734 °F) lämpötilaan, ennen kuin se muuttuu täysin nestemäiseksi. Seos kuumennetaan uunissa tähän määriteltyyn lämpötilaan, jolloin seos muuttuu nestemäiseksi, joka on altis ruiskutukselle.
Sulan seoksen ruiskutus:
Zamak 5 -seos siirtyy sulamisen jälkeen nestemäisestä olomuodosta asianmukaisesti valmisteltuun muottipesään korkeassa paineessa. Ruiskutuspaineet eri osien monimutkaisuuden ja niiden suuruuden mukaan ovat 30-60 MPa, joita valmistajat soveltavat muotoon.
Jäähdytys ja ulosheitto:
Kun muottiin tulee sulaa seosainetta, se alkaa jäähtyä ja muuttua kiinteäksi. Se valetaan muotista, kun se lakkaa pysymästä riittävässä jäähtymislämpötilassa. Muotin jäähdytyksen kestoa ja lämpötilaa voidaan säätää lopullisen valukappaleen laadun varmistamiseksi (muodonmuutosten välttämiseksi).
Viimeistelytoimet:
Zamak 5 -osien poistaminen edellyttää niiden käsittelyä erilaisilla viimeistelymenetelmillä, joissa osat leikataan, purseenpoistetaan, kiillotetaan ja lopuksi pinnoitetaan loppuvaatimusten täyttämiseksi.
Zamak 5 -valuprosessi on tehokas suuren volyymin tuotantoon, koska sillä voidaan valmistaa monimutkaisia esineitä, joilla on tarkat toleranssivaatimukset. Seos, jolla on poikkeuksellinen juoksevuus, korjaa monimutkaisten muottipesäalueiden täyttymisen, joten seos soveltuu hienojen yksityiskohtien komponenttien valmistukseen auto- ja laitteistoalalla sekä kulutuselektroniikan laitteissa.
Zamak 5 -seoksen eri standardit: Maailmanlaajuinen näkökulma
Zamak 5, hieman monipuolinen sinkkiseos, tunnetaan yleisesti eri nimillä, mutta nämä nimitykset ovat kuitenkin peräisin kyseisestä standardista ja alkuperämaasta. Zamak 5:een liittyvillä erilaisilla eritelmillä on tuotantomenetelmän ja aikaisemman nimityksen mukaan erilaisia aluekohtaisia suuntauksia. Nämä nimitykset ovat erittäin tärkeitä Zamak 5:n käyttäjille, koska ne määrittelevät yritykselle eri markkinasektoreilla ja alueellisissa standardeissa käytettävien seoseritelmien mukaiset protokollat. Kaikki Zamak 5 -seoksen maailmanlaajuiset standardit ja vaihtoehtoiset nimet esitetään yhdessä huomattavassa yleiskatsauksessa.
Zamak 5 -seoksen maailmanlaajuiset nimet ja standardit
Seuraavassa taulukossa esitetään eri maiden standardit ja niiden Zamak 5 -seoksen nimitykset.
Perinteinen nimi | Zamak 5 |
Lyhyt koostumus Nimi | ZnAl4Cu1 |
ASTM | AC 41A |
Yleinen nimi | Seos 5 |
Kiina | ZX03 |
JIS (Japani) | Harkko Tyyppi 1 (harkko) ZDC1 (metalliseos) |
Lyhyt eurooppalainen nimitys | ZL0410 (harkko) ZP0410 (metalliseos) |
Saksa DIN 1743-2 | Z420 |
Ranska NFA 55-010 | Z-A4UI |
YHDISTYNYT KUNINGASKUNTA BS 1004 | Seos B |
UNS (yhtenäinen numerointijärjestelmä) | Z35530 (harkko) Z35531 (seos) |
Miksi näillä standardeilla on merkitystä?
Erilaiset Zamak 5 -seosstandardit otettiin käyttöön, koska alueellisten teollisuuskäytäntöjen ja kansainvälisten viestintävaatimusten yhdistelmä otettiin maailmanlaajuisesti käyttöön. Se (Zamak 5) tarkoittaa, että myös Zamak 5 -materiaaleja valmistavien yritysten ja niiden insinöörien on tunnettava erityisesti kyseisen materiaalin alueelliset standardit ja nimitykset voidakseen valita oikean materiaalin sovellukseensa. Standardit ovat välttämättömiä yksityiskohtia Zamak 5 -seoksen kemiallisesta koostumuksesta, suoritusarvostandardeista, jotta voidaan valita sopivat materiaalit valu- ja työstötoimintoja varten.
Zamak 5 -seoksen edut
Zamak 5:tä käytetään teollisuudessa melko monissa sovelluksissa monipuolisena ja kestävänä sinkkiseoksena, joka tarjoaa runsaasti hyödyllisiä ominaisuuksia erilaisiin valmistustoimiin. Zamak 5:llä on kolminkertaisesti paremmat ominaisuudet, kuten ylivoimainen lujuus sekä suuri sitkeys ja suojaavat ominaisuudet, joiden ansiosta se soveltuu runsaisiin materiaalisovelluksiin kuluttajalaitteissa ja teollisuuslaitteissa. Nämä ovat Zamak 5 -seoksen valmistajille tarjoamat perusedut.
1. Lujuus, kestävyys ja turvallisuus
Sinkkiseos Zamak 5 säilyttää erinomaiset lujuus- ja kovuusominaisuudet. Seos on vahva voimankestävyyden lähde, minkä vuoksi se on edelleen vahva ratkaisu vaativiin sovelluksiin, joissa tarvitaan erittäin suuria rasitusprosentteja. Zamak 5 on tärkeä teollisuudelle, koska se on erittäin fysikaalisesti kestävä ja samalla se täyttää ehdottomat turvallisuustoimenpiteet kosketustapahtumien osalta.
Zamak 5 tarjoaa turvallisuusetua joihinkin metalleihin, kuten magnesiumiin, verrattuna, sillä se ei aiheuta tulipaloon liittyviä ongelmia. Zamak 5:llä on harvinainen ominaisuus, joka erottaa sen muista tavallisista materiaaleista, sillä se ei koskaan ime kosteutta, jolloin se ei aiheuta muovin kaltaisia veden imeytymisongelmia. Koska Zamak 5 on turvallinen ihmisten kosketukseen, sitä käytetään kosmetiikkapakkausten valmistuksessa.
Sen luotettavuuteen liittyvien ominaisuuksien ansiosta, jotka varmistavat sekä valmistajien että loppukäyttäjien turvallisuuden, Zamak 5 valitaan uusiin teknologisiin sovelluksiin.
2. Ylivoimainen laatu painevalussa
Zamak 5:tä käytetään painevalusovelluksissa, koska tämä metalliseos kykenee tuottamaan korkealaatuisia ja virheettömiä osia. Koska Zamak 5 -seos kykenee luomaan sileitä, valmiita tuotteita, joissa on vain vähän vikoja, se tuottaa korkealaatuisia painevalukappaleita, jolloin jälkikäsittelyä tarvitaan vain vähän.
Zamak 5:llä on luonnostaan zam-ominaisuuksia, joiden ansiosta voidaan käyttää tarkkoja valutekniikoita sellaisten tuotteiden valmistukseen, joiden tuotantoprosessissa on havaittu olevan erittäin täydellisiä. Koska Zamak 5:llä ei ole muodollisia viimeistelyvaiheita, valmistusprosessissa voidaan säästää aikaa ja valmistuskustannuksia. Zamak 5 -osilla on kaunis ulkonäkö, koska suunnittelijat voivat maalata tai kromata ne makunsa mukaan.
Zamak 5:n yksinkertainen viimeistelyominaisuus on tehnyt siitä ihanteellisesti soveltuvan tuotesovelluksiin kodin sisustustuotteiden, kodin huonekalujen yksityiskohtien ja koristeellisten valaistuskomponenttien tuotteissa. Zamak 5:n osat kestävät hämärtymisvaikutuksia sen kestävän vaikutuksen ansiosta.
3. Muunnetaan erilaisiksi lopputuotteiksi
Zamak 5 on luonteeltaan ylivertainen tuotantotyöhön. Se, että seos on luonteeltaan taipuisaa, koska sinkki on sitkeää, mahdollistaa sen helpon muokkaamisen eri työstötoimenpiteitä varten tuotannon aikana. Zamak 5:n kanssa voidaan helposti työskennellä erilaisilla tuotantomenetelmillä, kuten valamalla ja taivuttamalla, koneistamalla ja niittaamalla, valmistuksen vaatimusten täyttämiseksi.
Zamak 5:llä on helpot käsittelyominaisuudet, mikä tekee siitä elintärkeän lisävarusteen eri teollisuudenaloille, jotka ovat hyötyneet valmistuskustannusten alentamisesta ja helpon tuotantoprosessin ylläpitämisestä. Koska tämä on ensisijainen valinta valettujen lukittujen tuotteiden ja kahvan osien kokoonpanoon, Zamak 5 -osien kokoonpanoprosessi on vähemmän vaivalloista.
4. Kustannustehokas valmistus
Zamak 5 on materiaali, joka tarjoaa valmistajille poikkeuksellisen edullisen hinnan. Zamak 5 on niin edullinen, että se on muita seoksia edullisempi ja valettuna erittäin kustannustehokas. Sen kohtuullinen kustannusrakenne kuitenkin houkuttelee valmistajia saavuttamaan ylivoimaiset kustannustehokkuusstandardit, ja sen ylivoimaiset ominaisuudet tuovat valmistajia.
Zamak 5 -materiaalilla on suuri kierrätyspotentiaali, minkä vuoksi sen kierrätysmahdollisuus on tärkeä tekijä pitkän aikavälin valmistuskustannusten alentamisessa. Zamak 5 -esineet ovat uudelleenkäytettäviä ja johtavat metalliromun tuotantoon, joka otetaan talteen kustannussäästöjen ja siitä johtuvan jätteen minimoinnin perusteella.
5. Ympäristöystävällinen tuotantosykli
Zamak 5:n tuotanto vastaa suurelta osin ympäristöystävällisyyttä. Zamak 5 ei aiheuta suurta ympäristöuhkaa, koska sen valmistuksessa käytetään erilaista menettelyä kuin joidenkin metallien vaarallisten menettelyjen valmistuksessa. Seoksen valmistuksessa ei esiinny haitallista saastumista, koska sivutuotteita ei muodostu. Ympäristölainsäädännöstä Zamak 5 on hyvä valinta, ja se tarjoaa myös yritykselle ympäristöystävällisen menetelmän omien säännösten noudattamiseen.
Zamak 5:n rajoitukset
Vaikka Zamak 5:llä on monia hyviä puolia, se olisi ensin valittava sen kiinteiden rajoitusten perusteella valintaprosessissa.
Huono kosteudenkestävyys
Jos Zamak 5 joutuu kosketuksiin kosteiden olosuhteiden kanssa, sen pintaan muodostuu hapettumia, koska sen kosteudenkestävyys on heikko. Zamak 5 -tuotteiden valmistajien olisi tarjottava suojatoimenpiteitä liiallista kosteutta vastaan, ja jos näin ei ole, olisi tarjottava ylimääräisiä suojapinnoitteita sen hajoamista vastaan.
Rajoitettu kestävyys korkeissa lämpötiloissa
Zamak 5:n lämmönkestävyys on kohtalainen. Zamak 5:tä ei tulisi käyttää sovelluksissa, joissa lämpötila-altistus ylittää 80 °C, koska vetolujuus laskee erittäin paljon, mikä lisää murtumis- tai tai taipumisriskiä.
Ei ihanteellinen kevyisiin sovelluksiin
Zamak 5:llä valmistettu kappale on raskaampi, koska sen tiheys on suurempi kuin kilpailevien värimetalliseosten. Tällaisten sovellusten kevyeen elementtiin on tällöin otettava huomioon muut seosmateriaalit, koska ne määrittävät vaatimukset.
Korroosionkestävyysongelmat muiden metallien kanssa
Kun sinkkiä tai tinaa yhdistetään lyijyn kanssa tämän materiaalin valmistamiseksi, Zamak 5:n kestävyys heikkenee, koska tuloksena syntyvän seoksen korroosionkestävyys heikkenee. Erityisesti Zamak 5:tä käytettäessä on kiinnitettävä erityistä huomiota materiaalien yhdistämiseen.
Iskuominaisuudet alhaisissa lämpötiloissa
Kylmissä ympäristöissä Zamak 5:n vaikutuslujuus heikkenee kohdissa, joissa lämpötila laskee erittäin alhaiselle tasolle, joten se ei toimi kylmissä olosuhteissa.
Missä käyttää Zamak 5:tä?
Zamak 5:tä käytetään laajalti monilla aloilla, kuten painevaluteollisuudessa. Zamak 5 erottuu tuotantospektrin kahden ääripään välissä autojen osien ja koriste-esineiden valmistuksessa. Joitakin yleisiä käyttökohteita ovat mm:
Kylpyhuoneen kalusteet: Zamak 5:llä on kyky suojautua korroosiolta, minkä vuoksi sitä käytetään laajalti kylpyhuonetarvikkeiden, kuten hanojen ja kahvojen, valmistuksessa.
Ampuma-aseen komponentit: Seos on erittäin kestävä ja luja, ja siksi se toimii erittäin hyvin ampuma-aseiden osien valmistuksessa.
Lelut ja keräilyesineet: Zamak 5 on kuitenkin yksinkertainen valuprosessinsa ja ensiluokkaisen pintakäsittelynsä ansiosta suosittu valinta lelujen ja pienoismallien sekä keräilytuotteiden painevaluun.
Lukkojen ja laitteistojen valmistus: Zamak 5 on hallitseva valmistusteollisuudessa lukkojen kahvojen, lukkojen nuppien ja muiden rautateollisuuden osien valmistuksessa, koska seoksen lujuusominaisuudet ovat hyvät ja se on helposti työstettävissä.
Elektroniikka ja kodinkoneet: Zamak 5:llä on kestävyysnäkökohtia ja houkuttelevia ominaisuuksia, ja kotitaloustarvikkeet, kuten tehosekoittimet ja nitojien ja kattotuulettimien sekä muiden laitteiden valmistajat, arvostavat Zamak 5:tä.
Zamak 5 -seoksen mekaaniset ominaisuudet
Zamak 5 -seos määräytyy rakenteellisten ominaisuuksiensa perusteella toimimaan hyvin tai huonosti erilaisissa teollisissa toiminnoissa. Zamak 5 -seoksella on vetolujuus sekä venymä, kovuus ja korroosionkestävyys. Arvot muuttuvat määrällisesti, kun valuprosessi on erilainen ja metalliseoksen koostumusta ja jäähdytysnopeutta muutetaan.
Vetolujuus: Zamak 5 -seoksen vetolujuus on 280-300 MPa, mikä on korkeampi kuin muilla sinkkipohjaisilla seosmateriaaleilla.
Myötölujuus: Zamak 5 -seoksella on erinomainen jännitysmuodonmuutoskestävyys, koska myötölujuus on noin 230 MPa.
Pidennys: Zamak 5 -seoksen venymisnopeus on keskinkertainen (3 ja 6% välillä). Sen ominaisuudet mahdollistavat pienet muodonmuutokset, joihin ei liity halkeilua, ja siksi se soveltuu käytettäväksi joustavissa järjestelmissä.
Kovuus: Zamak 5:n kovuusarvo on 90-120 HB (Brinellin kovuus), minkä ansiosta materiaalia voidaan käyttää sovelluksissa, joissa vaaditaan suhteellisen pientä kulutuskestävyyttä.
Korroosionkestävyys: Jopa keskimääräisen kosteuspitoisuuden ja tavanomaisten kemiallisten aineiden kustannuksella Zamak 5 -seos kestää korroosiota erittäin hyvin. Zamak 5 toimii hyvin ulko- ja autoteollisuuden komponenttien materiaalina.
Zamak 5 -seoksen sovellukset
Zamak 5 valitaan monille teollisuudenaloille, koska siinä yhdistyvät hyvät valuominaisuudet ja vahvat mekaaniset ominaisuudet. Sen käyttökohteita ovat mm:
Autoteollisuus: Zamak 5 on keskeinen materiaali, josta valmistetaan hienoja toiminnallisia komponentteja autojen moottoreihin ja ajoneuvojen verhoilukoteloihin sekä elektronisten laitteiden koteloihin.
Laitteisto ja varusteet: Tällaiset materiaalit, kuten Zamak 5, ovat palvelleet autoteollisuutta, koska ne säilyttävät yhdessä suuren lujuuden ja kestävyyden ja viimeistelevät miellyttävät tuotteet.
Kulutustavarat: Zamak 5 -seos on materiaali, jota tuottajat käyttävät lelujen ja sähköliittimien sekä kodinkoneiden valmistukseen sen hyvän lujuuden ja korroosionkestävyyden sekä muokattavuuden vuoksi.
Elektroniikka: Zamak 5 johtaa hyvin sähköä, siitä saa hyviä muotteja monimutkaisiin muotoihin, ja sitä käytetään elektronisten laitteiden koteloiden ja koteloiden valmistukseen.
Zamak 5 -seoksen edut
Zamak 5:llä on useita tärkeitä etuja, jotka voivat tehdä siitä valmistajien suosiman seoksen.
Kustannustehokkuus: Zamak 5 on kustannuksiltaan erinomainen vaihtoehto, sillä se tarjoaa hyvän kestävyyden ja helpon valun yksinkertaisemmin ja halvemmalla kuin muut metallivaihtoehdot.
Monipuolisuus: Zamak 5 valitaan monimutkaisten ja tarkkojen osien valmistukseen siksi, että sillä on helppo valmistaa monimutkaisia muotoja ilman mukautumista.
Viimeistelyn laatu: Koska Zamak 5 tuottaa erinomaisen sileitä pintoja, tarvitaan korkealaatuista viimeistelyä, jotta valmistajat voivat saada paremman viimeistelylaadun.
Korkea lujuus-painosuhde: Zamak 5 -seos sopii hyvin autoteollisuudelle ja muille vastaaville aloille, sillä seos on erittäin luja ja kevyt.
Zamak 5:n käyttöön liittyvät haasteet ja näkökohdat
Huolimatta siitä, että Zamak 5 -seoksella on monia etuja, sen käytössä on useita kriittisiä kohtia.
Lämpötilaherkkyys: Zamak 5 on kuitenkin lämpöherkkä, koska sen ominaisuudet eivät heikkene, kun lämpötila nousee alle 250 °C:n (482 °F). Zamak 5 -osat on rajoitettava käyttöiän aikana ympäristöihin, joissa lämpötila on riittävän alhainen, jotta tämä kynnysarvo ei ylittyisi.
Työstörajoitukset: Vaikka Zamak 5:n valuprosessi on yksinkertainen, materiaali aiheuttaa ongelmia koneistuksessa, jossa käytetään aggressiivisia menetelmiä, sillä materiaalilla on taipumus aiheuttaa sekä hankautumista että kulumista. Onnistuneiden tulosten saavuttamiseksi hyvin teknikot tarvitsevat asianmukaiset työkalut ja oikeat tekniikat.
Ympäristövaikutukset: Arviointi Zamak 5:n hyvä korroosionkestävyys olisi otettava huomioon myös ympäristövaikutuksissa, joita Zamak 5 aiheuttaa tuotanto- ja kierrätysprosesseissa. Zamak 5:tä voidaan edelleen parantaa kierrättämällä ja vähentämällä valupäästöjen jätemäärää, ja teollisuus tekee molempia sinkkiseoksen kestävyyden lisäämiseksi.
Zamak 5 painevalupalvelut CNM TECH:ssä
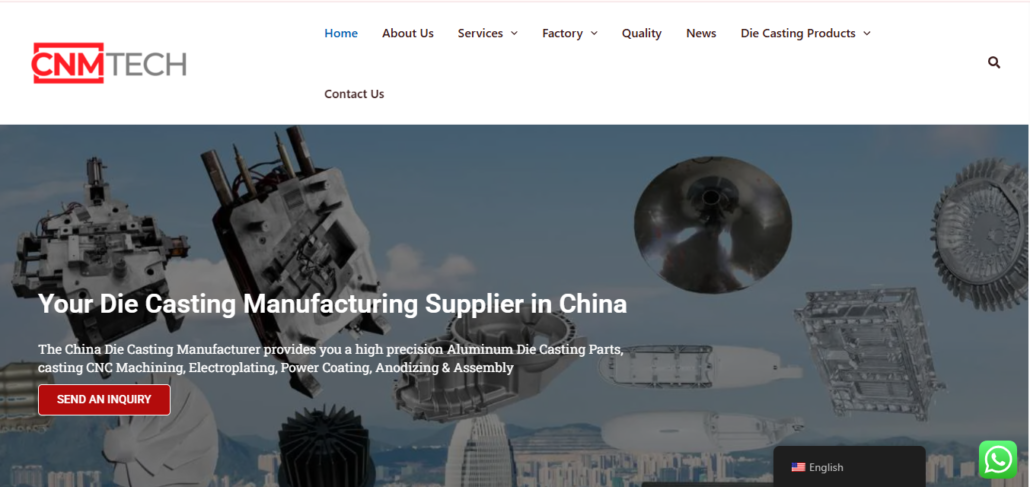
Tarjoamme erinomaisia Zamak 5 -valuratkaisuja CNM TECH-portfolion alla eri teollisuudenalojen tarpeisiin, kuten autoteollisuuteen, ilmailu- ja avaruusteollisuuteen ja kuluttajatuotteiden tuotantoon. Olemme organisaatio, joka on erikoistunut syvään kokemukseen ja nykyaikaisiin painevalujärjestelmiin, joiden avulla voimme kehittää osia, jotka antavat erinomaisen suorituskyvyn, kyvyn ja ylläpidon.
Nykyaikaisen painevalumenetelmämme avulla saadaan Zamak 5 -tuotteita, joilla on hyvät mitat, erinomainen pinnanlaatu ja järjestelmällinen valmistusaika taloudellista tuotantomäärää varten. Yksinkertaisesti sanottuna CNM TECH:n avulla asiakkaat voivat sanella eritelmänsä painevalumateriaalille tarkasti ja saada tiukat toimitusajat.
Tutustu kaikkiin Zamak 5 -tuotteisiimme, jotka tarjoavat prototyyppi- ja laajamittaisia valmistusominaisuuksia. Osoitteessa www.thediecasting.com voit tutustua siihen, miten yrityksemme Zamak 5 -ratkaisut lisäävät tuotteen elinkaarikestävyyttä.
Sinun on valittava CNM TECH:n Zamak 5 -valupalvelut, koska ne ovat tarkkoja.
Päätelmä
Zamak 5 on yleisesti käytetty metalliseosvalu teollisuudenaloilla tarkkuutta vaativien osien valmistukseen, erityisesti autoteollisuudessa, laitteistoissa ja elektroniikassa, joilla on mahdollisuus alhaisiin tuotantokustannuksiin ja tehokkuuteen. Sinkkiseos 5:n sinkki-, alumiini-, kupari-magnesiumseos muodostaa vahvan materiaalin, jolla on erinomaiset mekaaniset ominaisuudet, lujuus ja korroosiosuojaus sekä valettavuus. Valmistustekniikat, joissa käytetään Zamak 5 -valua, jos niitä lähestytään oikein ja lämpötilaa ja painetta valvotaan, tuottavat erittäin laadukkaita komponentteja, joissa on hyvin vähän epätäydellisyyksiä aina, kun ne suoritetaan. Zamak 5:llä on kuitenkin alhainen sulamispiste ja juoksevuusominaisuudet, jotka tekevät siitä sopivan erittäin hienostuneisiin malleihin, minkä vuoksi se on laajalle levinnyt teollisiin sovelluksiin.
UKK
1. Mitkä ovat CNM TECH:n painevaluprosessin olennaiset ominaisuudet, jotka johtavat Zamak 5:een?
A: Suorituskykyisellä sinkkiseoksella on muun muassa seuraavat ominaisuudet: erinomainen lujuus ja mittapysyvyys sekä erinomainen korroosiosuojaus. Yksi niistä on Zamak 5. Zamak 5:llä on poikkeuksellinen valukyky, jonka ansiosta erittäin yksityiskohtaisia ja monimutkaisia komponentteja voidaan valmistaa minimaalisella koneistuksella. CNM TECH käyttää Zamak 5:tä valmistamaan luotettavia, kustannustehokkaita komponentteja, jotka voivat toimia hyödyllisinä autoteollisuuden sovelluksissa ja kulutuselektroniikka- ja laitteistoteollisuudessa.
2. Voiko CNM TECH valmistaa tiettyjä Zamak 5 -osia projektini vaatimusten mukaisesti?
A: Ehdottomasti. Erikoistuneena yrityksenä CNM TECH tarjoaa yksilöllisen Zamak 5 -valuratkaisun. Yritys tekee muotit asiakkaiden kanssa, niiden yritysten kanssa, jotka tarvitsevat pienen volyymin prototyyppejä sekä suuren volyymin osia, joiden on oltava täsmälleen määriteltyjä. Työntekijöidemme omistautunut työ tuotantoprosesseissa johtaa tarkkojen tulosten ja luotettavan suorituskyvyn toimittamiseen.
3. Minkälaisia käsittelyjä Zamak 5 -valutuotteiden viimeistelyyn voidaan käyttää?
A: CNM TECH:ssä Zamak 5 -osille on saatavana useita erilaisia viimeistelyjä, kuten galvanointi yhdessä jauhemaalin, kromauksen, maalauksen ja kiillotuksen kanssa. Viimeistelytekniikoita käyttämällä voidaan parantaa toiminnallisten tai koristeellisten osien ulkonäköä, kulutuskestävyyttä ja korroosiosuojausta.