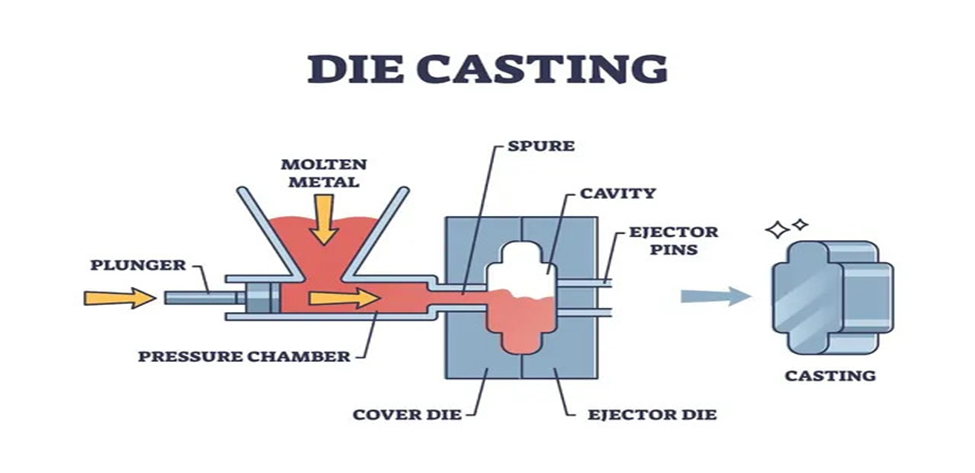
Tämä on valmistusprosessi, jossa sula metalli pakotetaan paineen avulla täyttämään muotin ontelo, joka tunnetaan myös nimellä painevalu. Muotti on yleensä korkealaatuista terästä, ja näin ollen osaa voidaan valmistaa suuria määriä, ja termiä käytetään tarkoittamaan monien osien valmistusta. Valmis osa valmistetaan avaamalla muotti sen jälkeen, kun sula metalli on jäähtynyt ja muodostanut kiinteän kerroksen. Tällaista prosessin käyttöä käytetään useimmiten valmistettaessa monimutkaista metallia, jota käytetään sellaisten erilaisten osien valmistuksessa, jotka vaativat suurta mittaustarkkuutta ja kiillotettuja pintoja. Muottiinvalu voidaan tehdä alumiinille, sinkille ja magnesiumille, mutta myös muita metalleja voidaan käyttää tapauksessa sovelluksesta ja muista vaatimuksista riippuen. Muottiinvalu pidetään yhtenä asiantuntijan valmistustekniikoista, kun ajatellaan pienien ja keskikokoisten metalliosien massatuotantoa. Menetelmän suosio on levinnyt autoteollisuuteen, ilmailu- ja avaruusalalle, elektroniikkaan ja teollisuuskoneisiin, koska sen avulla voidaan valmistaa kestäviä, kevyitä ja monimutkaisesti räätälöityjä osia. Prosessi on kuitenkin laajalti tunnustettu sen kyvystä valmistaa tuotteita, joiden geometria on monimutkainen ja joita olisi hyvin vaikea valmistaa tavanomaisilla tekniikoilla.
Miten painevalu toimii

Valaminen on painevaluprosessin ensimmäinen osa. Muotin toisella puolella on puolikas, ja se on tietyn muotoilun puolikas, jotta muotista saadaan lopputuotteen muotoinen. Muotteja varten suunnitellaan ontelot ja ytimet, jotka yleensä tehdään mittatilaustyönä, jotta osa voidaan jäljitellä mahdollisimman tarkasti.
1. Sulan metallin ruiskutus:
Sitten sula metalli ruiskutetaan muotin onteloon korkeassa paineessa halutun muodon muodostamiseksi. Metalli kuumennetaan yleensä asteen verran sulamislujuuden yläpuolelle, jotta se saadaan juoksevaksi. Paine, jolla sula metalli työnnetään muottiin, voi painevalussa olla useista tuhansista kymmeniin tuhansiin psi:iin (pounds per square inch), jotta voidaan varmistaa, että sula metalli pääsee muotin jokaiseen yksityiskohtaan.
2. Jähmettyminen:
Tämä tapahtuu, kun metalli ruiskutetaan kotelon onteloon, jolloin se jäähtyy ja metalli kovettuu. Valun laatu riippuu jäähdytysnopeudesta. Tällöin tulevat käyttöön ylimääräiset vikaantumistavat (leikkaus, nousu ja liukuminen), jotka johtavat nopeampaan jäähtymiseen, korkeampaan lujuuteen ja parempaan pintakäsittelyyn, ja hitaampaan jäähtymiseen, joka voi johtaa useampiin sisäisiin vikoihin ja heikompiin mekaanisiin ominaisuuksiin. Jäähdytysprosessin tukena käytetään yleensä muottiin sisäänrakennettuja vesijäähdytysjärjestelmiä.
3. Heitto:
Tämän jälkeen metallin annetaan jäähtyä ja jähmettyä, minkä jälkeen muotti on helppo irrottaa suuremmasta valukappaleesta ja heittää osa ulos. Tämän jälkeen suurin osa ajasta käytetään osan työntämiseen ulos muotista mekaanisen ulosheittimen avulla. Tämä riippuu osan monimutkaisuudesta, joka edellyttää muita ylimääräisiä vaiheita, nimittäin trimmausta ja koneistusta lopullisen muodon ja mitan saavuttamiseksi.
4. Laadunvalvonta:
Kappaleelle tehdään laatutarkastus ulosheittämisen jälkeen. Siihen voi sisältyä mittojen tarkistusta, silmämääräistä tarkastusta ja mekaanisia testejä, joilla varmistetaan, että osa vastaa vaatimuksia tai on niitä parempi. Teoriassa painevalussa saavutetaan suuri tarkkuus ja toistettavuus.
Die Casting-tyypit
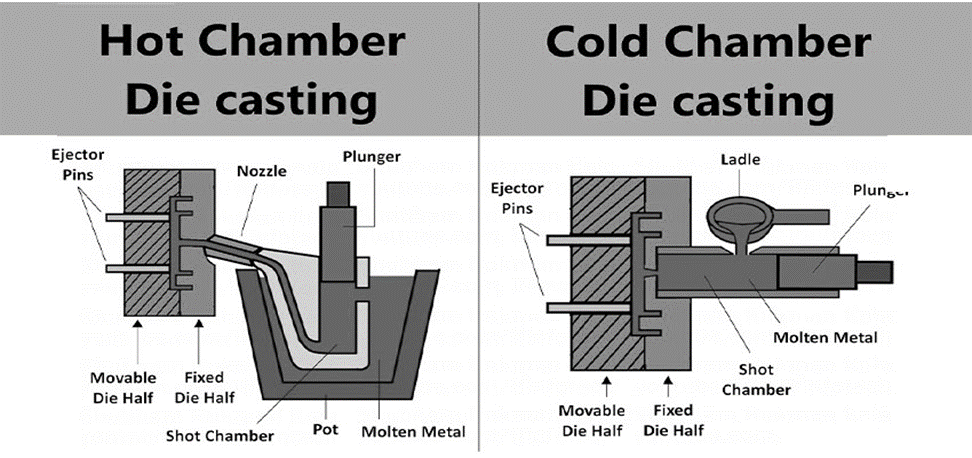
On olemassa kahdenlaisia painevalutyyppejä, kuumakammiovaluja ja kylmäkammiovaluja. Nämä kaikki ovat hyviä, ja niillä on omat etunsa, rajoituksensa ja ihanteelliset sovelluksensa.
1. Kuumakammion painevalu
Metalleille, kuten sinkille, magnesiumille ja lyijylle, parhaiten soveltuva prosessi on kuumakammiovalu, koska prosessi tapahtuu korkeissa lämpötiloissa ja sulamispisteissä. Ruiskutusjärjestelmä asennetaan sulatusuunin sisälle, jolloin metalli on aina kosketuksissa kammioon.
Edut:
- Koska sula metalli ruiskutetaan muottiin, koska se on ruiskutuskammiossa, kuumakammiossa tapahtuva painevalu kestää lyhyemmän ajan kuin kylmäkammiossa tapahtuva painevalu.
- Yksivaiheinen: Siinä tarvitaan vähemmän komponentteja ja vähemmän aikaa asennukseen, joten sitä pidetään taloudellisesti edullisena erityisesti suurissa tuotantomäärissä.
- Tietyille metalleille; Kuumakammiovalu soveltuu parhaiten tilanteisiin, joissa käytettävien metallien sulamislämpötilat ovat alhaiset, joten metallien kontaminaatio on vähäistä tai sitä ei tapahdu lainkaan.
Haitat:
- Ei voida käyttää korkean sulamispisteen omaaviin metallitöihin, kuten alumiiniin ja messinkiin, koska metallin korkea lämpötila sulattaa kammion.
- Kaikki osat altistuvat sulalle metallille, joten kulumisaste on korkea jonkin ajan kuluessa.
2. Kylmäkammion painevalu
Metallit, joilla on korkeampi sulamispiste, kuten alumiini, messinki ja kupari, valetaan kylmäkammiossa tapahtuvassa painevalussa. Tällöin sula metalli valetaan toisesta uunista, joka ruiskutetaan kylmäkammioon ja sitten muottipesään.
Edut:
- Materiaalivalintojen monipuolisuuden kannalta kylmäkammiovalu tarjoaa materiaalin käytön monipuolisuuden, joka mahdollistaa korkeiden sulamispisteiden omaavien materiaalien käytön.
- Metallin laadun parempi hallinta: Koska sulan metallin sylinteri kaadetaan kammioon erikseen, metallin laatua voidaan valvoa hyvin saastumisen estämiseksi.
- Pidempi työkalun käyttöikä: Koska se ei ole enää kosketuksissa metallin kanssa koko ruiskutusprosessin ajan, työkalun käyttöikä pitenee.
Haitat:
- Hitaampi syklin kesto: Metallin manuaalinen valaminen kammioon pidentää sykliä.
- Kustannukset ovat korkeammat, koska kyseessä on ylimääräinen toimenpide, jossa käytetään monimutkaisempia laitteita.
Valumenetelmien vertailu: kuumakammio ja kylmäkammio
Seuraavassa vertaillaan kahden painevalumenetelmän yleisimpiä tyyppejä,
Ominaisuus | Kuuma kammio Die Casting | Kylmäkammion painevalu |
Metallin yhteensopivuus | Parhaita matalan sulamispisteen metalleille (esim. sinkki, lyijy). | Parhaiten soveltuu korkean sulamispisteen omaaville metalleille (esim. alumiini, messinki). |
Syklin aika | Nopeammat sykliajat | Hitaammat sykliajat |
Muotin kuluminen | Suurempi muotin kuluminen suoran kosketuksen vuoksi sulan metallin kanssa | Alhaisempi muotin kuluminen |
Kustannukset | Alhaisemmat kustannukset suuren volyymin tuotannossa | Korkeammat alkukustannukset, mutta parempi lujille metalleille. |
Osien monimutkaisuus | Hyvä yksinkertaisemmille osille | Parempi monimutkaisemmille, suuremmille osille |
Die Casting -tekniikan edut
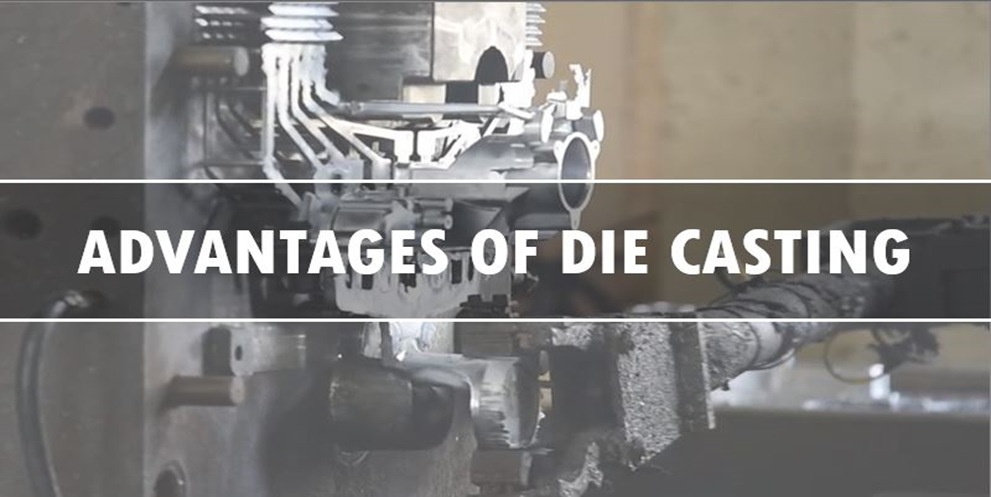
Yksi suurimmista eduista on se, että painevalu on yksi suosituimmista menetelmistä metalliseoksista valmistettujen tuotteiden laajamittaisessa tuotannossa.
1. Korkea tarkkuus ja tarkkuus
Muottiinvalulla on monia etuja, minkä ansiosta se on kätevä tarjota suurta tarkkuutta. Tätä tuotantomenetelmää käytetään laajalti myös sellaisten osien valmistukseen, jotka edellyttävät hyvää mittatarkkuutta, mikä on erittäin tärkeää, koska se määrittelee tietyssä työssä vaadittavat toleranssitasot. On huomattava, että painevalu on ainoa valmistustekniikka, jolla voidaan valmistaa tiettyjä osia, joiden geometria on erittäin monimutkainen.
2. Korkeat tuotantonopeudet
Suurten volyymien osalta painevalu on erittäin tehokasta. Osat valmistetaan nopeasti ja edullisesti, kun ensimmäinen muotti on luotu, ja siihen liittyy hyvin vähän työvoimaa. Simuloitujen jauheiden kysyntä on erityisen suurta esimerkiksi auto- ja elektroniikkateollisuudessa, jossa samoja osia tarvitaan suuria määriä.
3. Monimutkaiset mallit ja ohuet seinät
Painovalulla voidaan saavuttaa monimutkainen muotoilu, joka olisi vaikeaa tai mahdotonta toteuttaa perinteisillä valmistusmenetelmillä. Menetelmällä voidaan valmistaa osia, joissa on ohuet seinämät ja monimutkaiset sisäiset rakenteet, ja siihen mahtuu myös alimmaisia leikkauksia, mikä tekee siitä sopivimman sovelluksen tapauksissa, joissa tila on rajallinen.
4. Materiaalin tehokkuus
Muottiinvalu minimoi materiaalihävikin. Sulan metallin ruiskuttamiseen käytetty paine täyttää muotin ontelon jokaisen osan, joten romua syntyy vähemmän. Lisäksi monet painevaletut osat voidaan kierrättää, mikä lisää prosessin kestävyyttä.
5. Erinomainen pintakäsittely
Muotovalulla valmistettujen osien pinnanlaatu on sileä ja esteettinen. Se vaatii vähemmän jälkikäsittelyjä, kuten kiillotusta tai pinnoitusta, mikä säästää aikaa ja kustannuksia.
Mitä voidaan soveltaa painevaluprosessissa?
Painovalussa käytetään pääasiassa muita kuin rautametalleja niiden hyvien valuominaisuuksien vuoksi. Alumiiniseokset ovat yleisimmin käytettyjä materiaaleja, joita käytetään painevalussa, kuten seuraavat materiaalit osoittavat.
1. Alumiiniseokset

Koska alumiini on kevyt, korroosionkestävä ja johtaa erinomaisesti lämpöä ja sähköä, se on yleisimmin käytetty materiaali painevalussa. Luetteloa jatkamalla voidaan todeta, että alumiiniseosten erikoislaatuja käytetään silloin, kun lujuus-painosuhde on tärkeä, erityisesti auto-, ilmailu- ja avaruusteollisuudessa sekä sähköteknisessä teollisuudessa. Lisäksi ne ovat myös mittatarkkoja, minkä vuoksi ne soveltuvat erittäin tarkkojen osien valmistukseen.
2. Sinkkiseokset
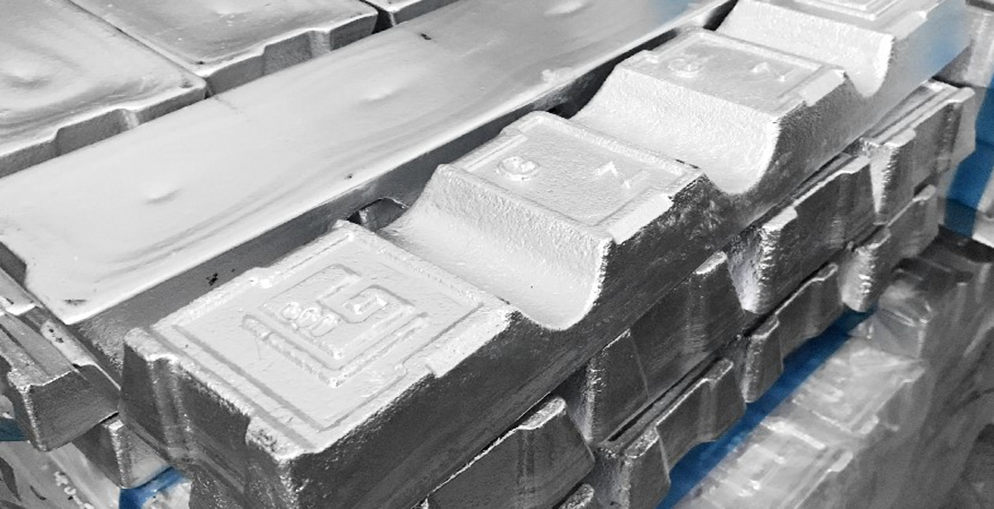
Sinkkivaluseoksia voidaan suosia niiden ominaisuuksien, kuten matalan sulamispisteen ja korkean juoksevuuden, ansiosta, mikä mahdollistaa monimutkaisen muotoilun, jossa on ohuita osia ja teräviä yksityiskohtia, tekemisen helpommin ja tehokkaammin. Tällaiset sinkkiosat, joilla on suuri sitkeys, kestävät yhtä hyvin korroosiota ja ovat laadukkaasti kiillotettuja. Toinen sinkkiseosten käyttöalue on autojen ja muiden ajoneuvojen varaosien valmistus, laitteistot ja elektroniikka.
3. Magnesiumseokset

On syytä mainita, että magnesium on kevyin rakennemetalli, ja siksi se tarjoaa merkittävän painon autoihin tai lentokoneisiin tarkoitetuissa osissa. Tämä johtuu siitä, että magnesiumseoksia käytetään osissa, joiden on oltava vahvoja mutta mahdollisimman kevyitä. Koska metalli on kuitenkin hyvin reaktiivinen, seosta on hallittava hyvin painevaluprosessin aikana.
4. Kupariseokset
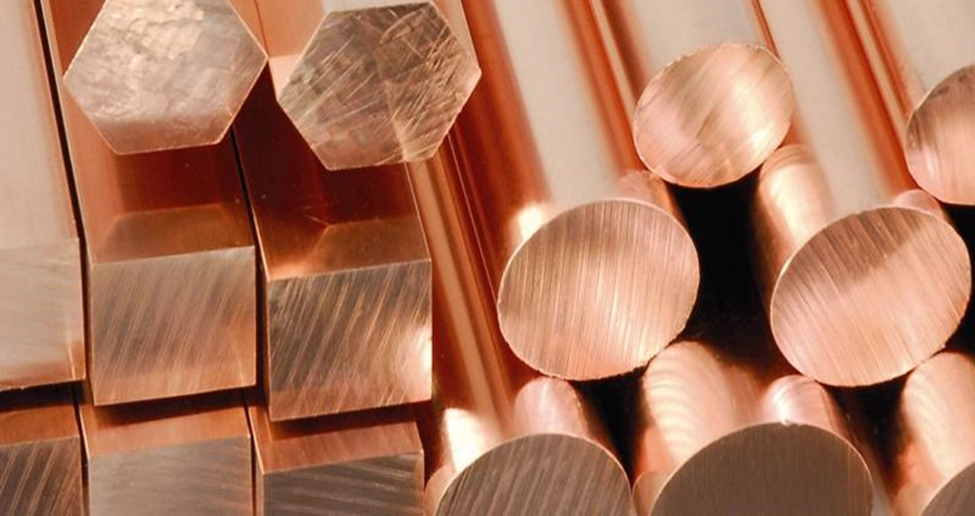
Alumiinin ja sinkin lisäksi painevalussa käytetään myös kupariseoksia, messinkiä ja pronssia, mutta niitä ei käytetä yhtä usein kuin alumiinia ja sinkkiä. Se tarjoaa hyvät lujuusominaisuudet kulutusta vastaan, ja sitä käytetään usein sähkö- ja LVI-sovelluksissa.
On erittäin tärkeää huomata, että perusmateriaalien eri muodot soveltuvat eri sovelluksiin, ja kustannukset vaihtelevat näiden muotojen välillä, ja näin ollen myös lopputuotteen ominaisuudet vaihtelevat.
Muottiinvalu vs. muut valumenetelmät
Verrattuna valumenetelmiin, kuten hiekkavaluun, tarkkuusvaluun ja kestomuottivaluun, tämä osa voisi olla painevalun vertailuosa. Tällöin on viisasta korostaa kunkin menetelmän vahvuuksia ja heikkouksia ja opettaa lukijoille, milloin painevalu kannattaa valita muiden vaihtoehtojen sijaan. Näin ollen tämä voisi olla vertaileva yleiskatsaus, joka auttaisi optimaalisen valumenetelmän määrittämisessä osan materiaalin, monimutkaisuuden ja tuotantomäärän mukaan.
Ominaisuus | Die Casting | Hiekkavalu | Sijoitusvalu |
Tarkkuus | Korkea tarkkuus ja tiukat toleranssit | Pienempi tarkkuus ja karkea pintakäsittely | Korkea tarkkuus ja sileä viimeistely |
Nopeus | Nopeampi suuren volyymin tuotantoon | Hitaampi tuotantosykli | Hitaampi muotin valmistuksen vuoksi |
Materiaalijäte | Vähäinen jäte | Suurempi hävikki karkeamman viimeistelyn vuoksi | Vähäinen jäte, mutta monimutkaisemmat muotit |
Kustannukset | Kustannustehokas suurilla volyymeillä | Alhaisemmat kustannukset pienen volyymin tuotannossa | Korkeammat kustannukset monimutkaisuuden ja työvoiman vuoksi |
Tuotantoprosesseja painevalussa ja ruiskuvalussa verrataan keskenään.
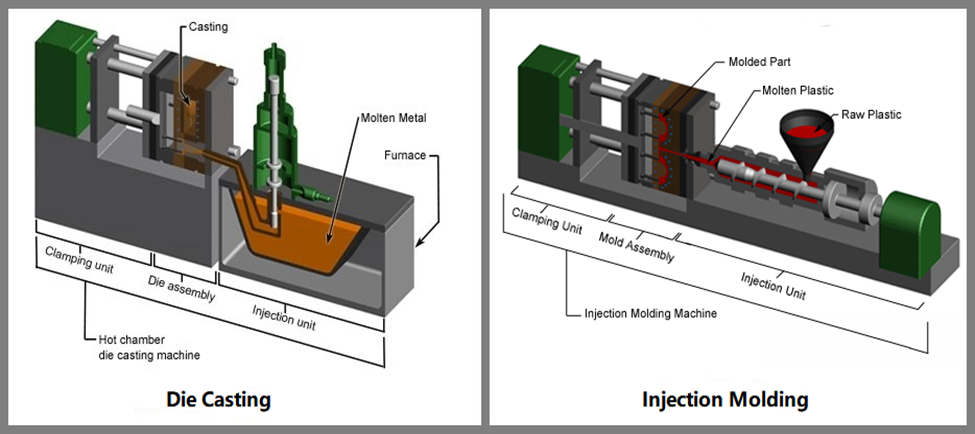
Kaksi yleistä tekniikkaa, joita käytetään yksityiskohtaisten ja monimutkaisten muotojen omaavien osien valmistukseen, ovat painevalu ja ruiskuvalu. Vaikka molemmissa tekniikoissa käytetään materiaalia, joka muodostaa yksityiskohtia lopputuotteiden valmistamiseksi, näillä kahdella tekniikalla on eroja materiaalityypin, muodostetun tuotteen ja erityisesti kunkin prosessin hyötyjen suhteen.
1. Käytetyt materiaalit
Muottiinvalu: Muottiinvalua suositaan useimmiten muiden metallien kuin rautametallien, erityisesti alumiinin, sinkin, taitojen ja kupariseosten, kanssa. Metallit kuumennetaan ja valetaan sitten muottiin hydraulisen paineen avulla. Sikäli painevalu on sopivin tapa valmistaa osia, jotka ovat vahvoja, kestäviä ja kestävät korkeita lämpötiloja.
Ruiskuvalu: ruiskuvalua käytetään yleisesti muovimateriaalien välillä, ja se on harvoin mahdollista metalleille ja lasille. Näihin polymeereihin kuuluvat polyeteeni, polypropeeni sekä polystyreeni usein käytettyjen polymeerien luettelossa. Tuotteen muodostusmateriaali on myös kevyt ja joustava, ja lisäksi siinä on alhaiset kustannukset ja melko monimutkaiset muodot, joten voidaan todeta, että ruiskuvalu soveltuu erinomaisesti tämäntyyppisiin tuotteisiin.
2. Prosessierot
Muottiinvalu: Kuten nimestä voi päätellä, sulaa metallia ruiskutetaan korkeassa paineessa muottiin. Ne syntyvät metallin jäähtymisen ja jähmettymisen jälkeen erittäin suurella nopeudella hienolla toleranssilla ja hyvällä pintakäsittelyllä, eikä muita toimenpiteitä tarvitse suorittaa.
Ruiskuvaluprosessi: Koska ruiskuvalussa käytetään sulan muovimateriaalin ruiskuttamista muotin onteloon painetta käyttämällä, kyseessä on ruiskuvalu. Kun sulan muovin lämpötila on laskenut, muotti aukeaa, ja tuotteeksi syntyy muovimuotti. Ruiskuvalu on kuitenkin yhtä tarkkaa kuin painevalu, vaikka sitä käytetäänkin yleisesti suhteellisen pienempien ja kevyempien osien valmistukseen verrattuna painevaluun.
3. Sovellukset
Muottiinvalu: Muotovalusta on hyötyä kovien ja vahvojen osien valmistuksessa, joita käytetään autonvalmistuksessa, lentokoneissa ja muissa elektroniikkatuotteissa, koska se kestää erinomaisesti lämpöä.
Ruiskuvaluprosessi: Voidaan käyttää kuluttajatuotteiden, pakkausten, lääkinnällisten laitteiden ja lelujen valmistukseen, koska joustavuus, suunnittelun helppous ja edullinen tuotanto ovat tärkeitä.
Painovalun käyttökohteet

Yksi tekijä, joka on tehnyt painevalusta suositun valmistusmenetelmän monilla teollisuudenaloilla, on se, että sillä voidaan valmistaa korkealaatuisia ja kestäviä osia, joiden geometria on melko monimutkainen. Joitakin sovelluksia ovat mm:
1. Autoteollisuus
Yleensä moottorin osat, vaihteistokotelot ja muut tärkeät autojen osat valmistetaan painevalulla. Valetut osat ovat tarkkoja ja lujia, joten ne voidaan asentaa vaativiin autoteollisuuden sovelluksiin.
2. Elektroniikkateollisuus
Elektroniikka-alalla painevalua käytetään elektroniikkalaitteiden, kuten matkapuhelinten, kannettavien tietokoneiden ja televisioiden, koteloiden valmistukseen. Tekniikan avulla voidaan rakentaa kevyitä mutta vahvoja koteloita, jotka suojaavat herkkiä komponentteja.
3. Ilmailu- ja avaruusteollisuus
Muotovalusta on suurta hyötyä ilmailu- ja avaruusteollisuuden yrityksille, koska niillä voidaan valmistaa kevyitä ja erittäin lujia osia, joita tarvitaan lentokoneissa ja avaruusaluksissa. Painovaletuilla osilla on tarkkuus ja materiaaliominaisuudet, joita voidaan käyttää sovelluksissa, joissa suorituskyky ja turvallisuus ovat tärkeitä asioita.
4. Teollisuuslaitteet
Myös koneiden, työkalujen ja muiden teollisuuslaitteiden osat valetaan painevalulla. Koska sillä voidaan valmistaa osia, joiden geometriassa on monimutkaisia yksityiskohtia ja hyvät mekaaniset ominaisuudet, se on hyvä väline näihin sovelluksiin.
Päätelmä
Muotovalumenetelmä on monipuolinen, kustannustehokas ja tehokas valmistusprosessi, jota käytetään monilla teollisuudenaloilla. Tuotettu laatu on erittäin korkea kappaleiden toleranssien, pintakäsittelyn ja korkean tuotantonopeuden osalta, mikä tekee siitä erinomaisen tuotantovälineen nykypäivän nykyaikaisiin tuotantokäytäntöihin. Silti painevalu vastaa monien näiden teollisuudenalojen tarpeisiin, jotka vaativat osien lujuutta, tarkkuutta ja tehokkuutta - autoteollisuudesta ilmailu- ja avaruusteollisuuteen, elektroniikkaan ja teollisuuslaitteisiin.
Vaikka teknologia kehittyy nopeasti ja sitä todennäköisesti käytetään jatkossakin erinomaisesti valmistettujen metalliosien lähteenä valtavassa mittakaavassa, on kuitenkin todennäköistä, että painevalu. Parempi ymmärrys painevalun perusteista voi auttaa insinööri-, valmistus- ja suunnitteluammattilaisia tekemään tietoon perustuvia päätöksiä siitä, miten painevaluprosessia voidaan käyttää halutun lopputuloksen saavuttamiseksi.
Usein kysytyt kysymykset painevalusta
1. Mikä on painevalun ja ruiskuvalun aikajakso?
Syklien kesto vaihtelee tietyn kappaleen osalta 15-5 minuutin välillä painevalussa ja 10-60 sekunnin välillä ruiskuvalussa.
2. Voidaanko painevalua käyttää muoviosiin?
Muiden kuin metallien painevalua ei käytetä. Muoviosien valmistukseen käytetään yleensä ruiskuvalumenetelmää.
3. Mitkä tuotteet soveltuvat parhaiten painevalun valmistusprosessiin?
Muottiinvalu soveltuu parhaiten pienten ja keskikokoisten, monimutkaisten ja erittäin tarkkojen, metalleista valmistettujen osien valmistukseen. Valmistettavia mekaanisia tuotteita ovat muun muassa autojen ja autojen osat ja tarvikkeet, sähkötuotteiden kotelot ja kotelot, elektroniikan osat ja laitteiden kotelot.
4. Miten painevalu eroaa hiekkavalusta.
Silti kun näitä kahta verrataan: painevalu on tarkempi ja vähemmän aikaa vievä prosessi kuin hiekkavalu. Hiekkavalua käytetään mieluummin suurissa ja vähemmän monimutkaisissa malleissa, mutta AL-valua käytetään mieluummin pienissä ja monimutkaisissa malleissa, koska se mahdollistaa tasaisemmat pinnat ja tarkemmat toleranssit, jotka ovat tyypillisiä suurille tuotantosarjoille.
5. Mikä määrittää painevalun kustannukset?
Joitakin näkökohtia, jotka todennäköisesti vaikuttavat painevalun kustannuksiin, ovat: materiaalityyppi, osan monimutkaisuus, muotin suunnittelu ja tilausten määrä. Kevyet työkalut riippuvat volyymista, ja vaikka suuri volyymi pitää yksikkökohtaiset kustannukset alhaisina, työkalujen alkukustannukset ovat korkeat.