
Valaminen ja painevalu ovat kaksi tärkeää valmistusprosessia, jotka ovat elintärkeitä, kun halutulla tarkkuudella, kestävyydellä ja tehokkuudella valmistetaan metallikomponentteja. Valussa sulaa materiaalia käytetään muottiin ja annetaan sen jäähtyä ja jähmettyä. Hiekkavalu, tarkkuusvalu ja kestomuottivalu ovat joitakin valutyyppejä. Muottiinvalu on kuitenkin erikoisvalu, jossa käytetään korkeaa painetta sulan metallin ruiskuttamiseen muottipesään erittäin tarkasti ja hyvällä pintakäsittelyllä. Muotovalua käytetään laajalti autoteollisuudessa, ilmailu- ja avaruusteollisuudessa, elektroniikassa ja niihin liittyvissä teollisuussovelluksissa, joissa tarvitaan kevyitä, vahvoja ja korroosionkestäviä osia. Erilaisia painevaluvaihtoehtoja on aikojen kuluessa kehitetty teollisuuden eri tarpeisiin sopiviksi. Painovoimavalu (Gravity Die Casting, GDC) on riippuvainen painovoimasta muotin täyttämisessä ja matalapainevalu (Low Pressure Die Casting, LPDC) poistaa turbulenssin, jotta saavutetaan parempi materiaalin eheys. Puristusvalussa käytetyllä äärimmäisellä paineella luodaan erittäin lujia, huokosettomia osia, ja tyhjiövalussa suljettu ilma poistetaan, jotta saadaan virheetön osa. Lisäksi puolikiinteä painevalu (Rheocasting) saavutetaan käyttämällä osittain jähmettynyttä metallia mekaanisten ominaisuuksien ja tarkkuuden parantamiseksi.Yleistä termiä valu valmistuksessa käytetään viittaamaan metallin muotoiluun täyttämällä se muottiin ja antamalla sen jähmettyä. Tätä menetelmää käytetään yleisesti hiekkavalussa, investointivalussa ja kestomuottien valussa. Muotti painevalussa on metallimuotti, jota käytetään korkeapainevaluprosessissa, kun taas painevaluprosessissa muotilla tarkoitetaan muotin pintaan kiinnitettyä metallimuottia. Yleensä valmistetaan massatuotantoa varten suunniteltuja karkaistuja teräsmuotteja.
Tässä artikkelissa käsitellään valun ja painevalun taustalla olevia käsitteitä, näiden kahden käsitteen välisiä eroja ja myös niiden tyyppejä, edellä mainittujen mahdollisia sovelluksia sekä tämän prosessin valamiseen liittyviä etuja ja haittoja.
1. Mitä on valu?
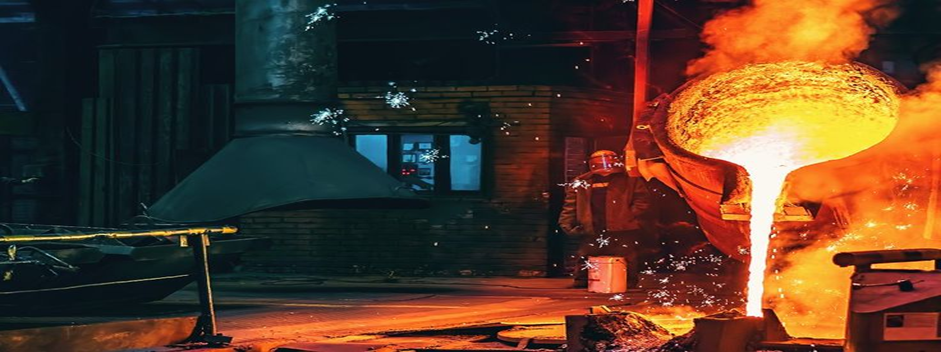
Valaminen on teollinen prosessi, jossa nestemäinen materiaali pakotetaan muottiin, jossa se jähmettyy. Neste voi olla periaatteessa mitä tahansa metallia, muovia tai muuta sulavaa materiaalia. Kovettumisen jälkeen materiaali saa muotin ontelon mukaisen muodon. Viimeisten useiden tuhansien vuosien aikana tätä tekniikkaa käyttämällä on luotu työkaluja, aseita ja monimutkaisia veistoksia.
Valuprosessi
Useat näistä vaiheista vaikuttavat olennaisesti metalli- tai muoviosien valuprosessin luonteeseen.
- 1. Lopputuotteesta tehdään malli puusta, muovista tai metallista. Muottipesän muoto ja mitat määritetään tämän mallin perusteella.
- 2. Muotin valmistelussa muotti ontelo suunnitellaan mallin mukaan. Valumenetelmä määrittää, tehdäänkö se hiekasta, metallista vai keraamisesta. Sulan materiaalin tasaisen virtauksen mahdollistavat tuuletus- ja porttijärjestelmät sisällytetään asianmukaisesti.
- 3. Raaka-aineen, yleensä metallin tai muovin, sulattaminen korkeassa lämpötilassa uunissa. Käytettävän materiaalin tyypille ominainen lämpötila on erilainen.
- 4. Sulaa materiaalia kaadetaan muotin onteloon varovasti oikea määrä, jotta vältytään virheiltä, koska kaato on tasaista. Tässä voidaan käyttää manuaalista kaatamista tai automaattisia kaatojärjestelmiä.
- 5. Jähmettyminen - Materiaali jäähtyy ja jähmettyy muotin sisällä muodostaen ontelon muodon. Jäähdytysnopeus vaikuttaa tunnetusti valetun tuotteen lopullisiin ominaisuuksiin.
- 6. Jähmettymisen jälkeen valukappale poistetaan muotista, ylimääräinen materiaali, kuten portit, juoksuputket tai välähdykset, leikataan ja sitten kokoonpano poistetaan ja viimeistellään. Myöhemmin niille voidaan tehdä muita viimeistelyprosesseja, kuten hiontaa, kiillotusta tai lämpökäsittelyä, jotta lopputuotteen ulkonäköä ja mekaanisia ominaisuuksia voidaan parantaa.
Tämän jäsennellyn lähestymistavan ansiosta valu on luotettavampaa ja laadukkaampaa.
2. Mitä on painevalu?
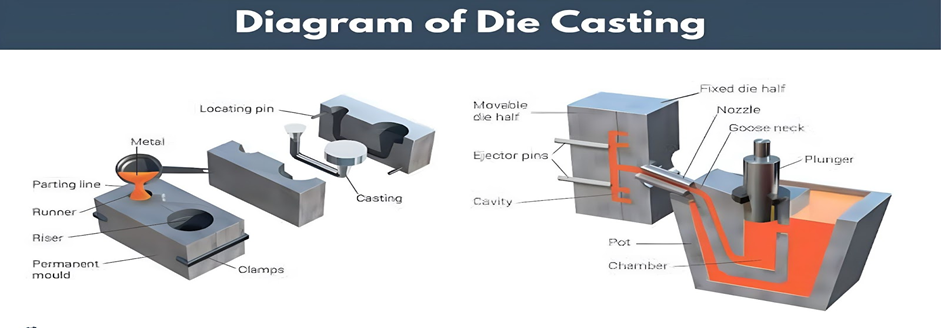
Dies tarkoittaa muotteja, mistä nimi johtuu myös painevaluprosessista, jossa sula metalli pakotetaan korkeassa paineessa täyttämään muotin ontelo. Se soveltuu parhaiten suurten määrien, monimutkaisten ja mittatarkkojen osien valmistukseen.
Valuprosessi
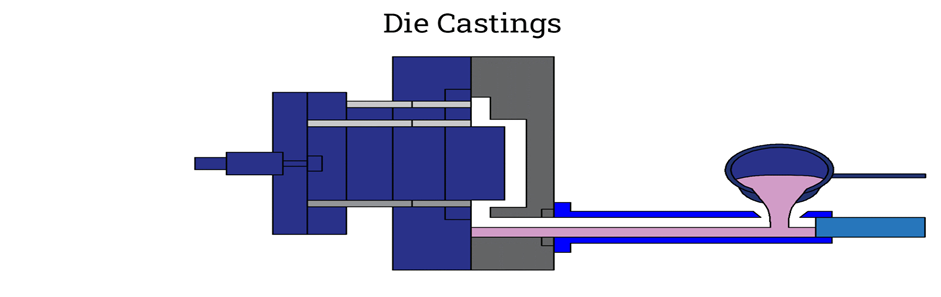
Muottiinvalu on valmistusprosessi, jossa metallikomponentit muovataan muotin ontelon muotoon korkeassa paineessa ja jossa tarvitaan suurta tarkkuutta ja mittatarkkuutta sekä pinnan viimeistelyä. Tämä seuraa alla olevia vaiheita:
- 1. Sulan metallin ruiskutus - Korkea paine, joka vaihtelee 1 500-25 000 psi:n välillä, ruiskutetaan sulan metallin (kuten alumiinin, sinkin tai magnesiumin) ruiskuttamiseksi teräsmuottiin (muottiin), joka sulattaa valitun metallin uunissa. Tämä täyttää muotin jokaisen yksityiskohdan sulalla metallilla.
- 2. Muotti tai muotti - Sula metalli todella jäähtyy ja jähmettyy muotissa, mikä johtaa vahvaan ja tarkkaan kappaleeseen. Lopputuotteen mekaaniset ominaisuudet riippuvat jäähdytysnopeudesta.
- 3. Eject & trimer - Kun valukappale on jähmettynyt, se heitetään ulos muotista heittotappien avulla. Ylimääräinen materiaali, mukaan luettuna leimahdus, juoksuputket ja portit, leikataan haluttuun muotoon.
- 4. Pintakäsittely - Käyttökohteesta riippuen valu voidaan joutua viimeistelemään Nizzan hionta, kiillotusmaalaus, anodisointi tai jauhemaalaus ulkonäön, kestävyyden ja korroosionkestävyyden parantamiseksi.
Tämän prosessin tuloksena saadaan erittäin lujia, kevyitä ja monimutkaisia osia, joiden jälkikäsittely on vähäistä. Yleisimpiä materiaaleja, joihin painevalua käytetään, ovat värimetallit, kuten alumiini, sinkki ja magnesium.
Valuprosessien tyypit
Valuja on erilaisia riippuen käytetystä menetelmästä.
1 Hiekkavalu

- Se on yksi monipuolisimmista ja taloudellisimmista hiekkamuotteja käyttävistä valumenetelmistä.
- Yleinen auto-, ilmailu- ja avaruusteollisuudessa sekä taideteollisuudessa.
2 Investment Casting
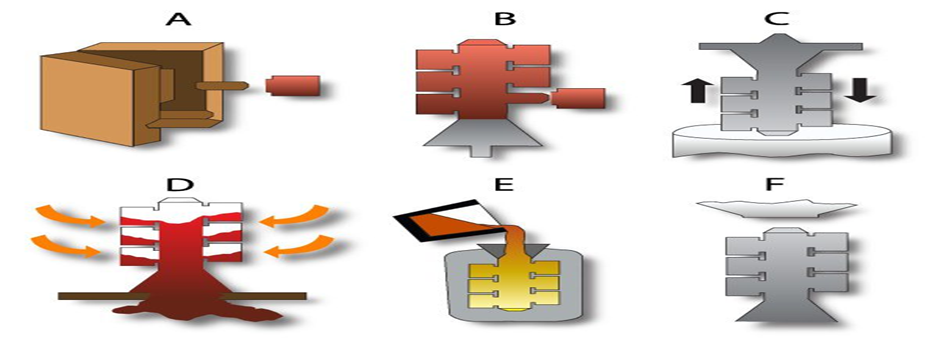
- Se tunnetaan myös nimellä kadotetun vahan valu, ja sillä valmistetaan erittäin yksityiskohtaisia ja monimutkaisia osia.
- Käytetään koruissa, lääketieteellisissä implantteissa ja ilmailu- ja avaruusalan osissa.
3 Keskipakovalut

- Siinä muottia pyöritetään, jotta sula metalli saadaan sulatettua perusteellisesti.
- Käytetään yleisesti putkien, sylintereiden ja renkaiden valmistukseen.
4 Kestomuottivalu
- Vähentää jätettä ja vähentää muottien käyttöä uudelleenkäytön ansiosta.
- Se on ihanteellinen toistuvaan, korkealaatuisten metalliosien valmistukseen.
Painovalutyypit
Die casting on pääasiassa kaksi tapaa:
1. Kuumakammion painevalu
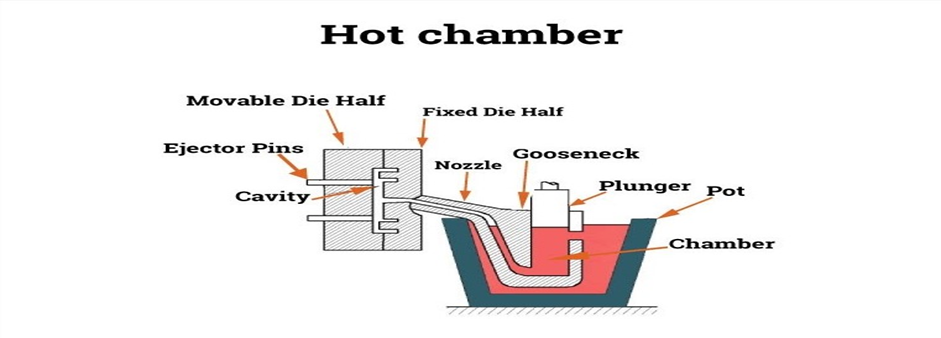
- Käytetään matalan sulamispisteen metalleille, kuten sinkille ja magnesiumille.
- Nopeampi prosessi ja korkeammat tuotantonopeudet.
2. Kylmäkammion painevalu

- Sitä käytetään korkean sulamispisteen omaaville metalleille, kuten alumiinille ja messingille.
- Hidastaa sulatus- ja ruiskutusvaiheita ja soveltuu kestäviin osiin.
5. Valun ja painevalun erot
Ominaisuus | Casting | Die Casting |
prosessi | Muotti Siihen kaadetaan metallia | Sulaa metallia ruiskutetaan korkeassa paineessa. |
Materiaalit | Erilaiset metallit ja muovit | Enimmäkseen ei-rautametalleja, kuten alumiinia ja sinkkiä. |
Tarkkuus | Kohtalainen | Korkea tarkkuus |
kustannukset | Edulliset aloituskustannukset | Korkeat alkuvaiheen työkalukustannukset |
Sovellukset | Suuret ja yksinkertaiset osat | Pienet, monimutkaiset, suuren volyymin osat |
Valun ja painevalun sovellukset

Valu ja painevalu ovat omalla tavallaan valtavan tärkeitä eri teollisuudenaloilla, ja ne ovat kustannustehokkaita, koska ne helpottavat monimutkaisten metallikomponenttien valmistusta erinomaisella tarkkuudella.
- Autoteollisuudessa moottorilohkojen, vaihteistokoteloiden, pyörännavojen, jarruosien ja jousitusosien valmistus. Kevyiden alumiiniosien osalta painevalua suositaan erityisesti tähän tarkoitukseen, koska se on polttoainetehokkaampaa.
- Ilmailu: Ilmailu- ja avaruusalan komponentit, kuten turbiinien lavat, rakenteelliset lentokoneen runko-osat, kotelot ja laskutelineiden osat, valetaan kestäviksi ja vahvoiksi, mutta kevyiksi.
- Elektroniikan alalla valu- ja painevalu ovat välttämättömiä, sillä koteloita ja painevalukomponentteja, kuten jäähdytyslevyjä, liittimiä ja suojalaitteita, tarvitaan lämmön poistamiseen ja hauraiden elektroniikkapiirien turvallisuuden takaamiseen.
- Rakentaminen - Rakennusten, siltojen jne. rakentamisessa käytettävät putket, liitososat, kiinnikkeet, venttiilit ja kaiteet, jotka takaavat rakenteellisen vakauden ja pitkäikäisyyden.
- Lääketieteelliset laitteet - Tarkkuusvalukomponentteja käytetään laajalti lääketieteen alalla kirurgisissa instrumenteissa, kuvantamislaitteiden koteloissa, ortopedisissä implantteissa jne.
- Teollisuuskoneet - Valua tarvitaan lujuuden ja kulutuskestävyyden takaamiseksi vaihdelaatikoissa, pumpuissa ja muissa kovissa olosuhteissa toimivissa raskaissa koneenosissa.
Valu- ja painevalutekniikkaa käytetään laajalti, ja siksi ne ovat nykyaikaisen valmistusteollisuuden välttämättömiä komponentteja.
Painovaluvaihtoehdot
Yksi suosituimmista valmistusmenetelmistä on painevalu, jossa sulaa metallia valetaan muottiin, jotta voidaan valmistaa komponentteja, joilla on monimutkaiset ja määrätyt ominaisuudet. Erilaisia painevalun muunnelmia on kehitetty aikojen saatossa materiaalien, tuotantovaatimusten ja laatuvaatimusten mukaan. Jokaisella menetelmällä on omat etunsa, ja se soveltuu enemmän tai vähemmän erilaisiin sovelluksiin. Seuraavassa on lueteltu tärkeimmät painevalun muunnelmat ja niiden prosessit ja edut.
Painovoimavalu (GDC)
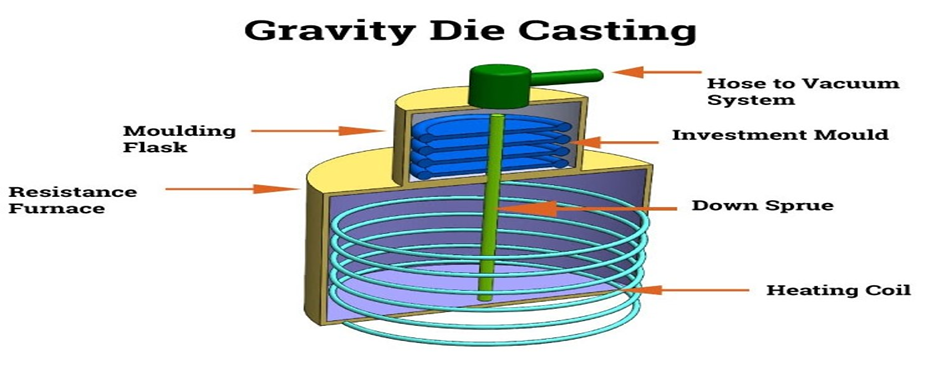
Yleiskatsaus
Painovoimavalussa (Gravity Die Casting, GDC) sulaa metallia kaadetaan muottiin ilman korkeaa painetta. Pikemminkin painovoima auttaa ohjaamaan metallia täyttämään ontelon ja järjestäytymään ikään kuin itsestään. Tätä prosessia suositaan seoksille, joiden sulamispisteet ovat alhaisemmat, ja sitä käytetään yleisesti silloin, kun halutaan kontrolloidumpi jähmettymisprosessi.
Tärkeimmät ominaisuudet
- Se on tehokkaampaa kuin hiekkavalu, koska siinä käytetään uudelleenkäytettäviä muotteja.
- Hitaampi kuin painevalu, mutta osa on vahvempi tiheämmän muodin ansiosta.
- Rajoittuu tiettyihin seoksiin, kuten alumiiniin ja magnesiumiin.
Yleiset sovellukset
- Autojen osat (sylinterin päät, moottorin osat).
- Putkien liitososat ja venttiilien rungot.
- Teollisuuskoneet ja rakenneosat.
Matalapainevalu (LPDC)

Yleiskatsaus
Matalapainevalussa (LPDC) sula metalli paineistetaan muottiin alhaisella paineella, joka on noin 0,1-1 MPa. Tällä hallitulla täytöllä turbulenssi minimoidaan ja virtaus saadaan tasaisemmaksi, jolloin virheet, kuten ilmataskut ja sulkeumat, jäävät mahdollisimman pieniksi.
Tärkeimmät ominaisuudet
- Parempi materiaalin eheys vähentyneen turbulenssin ansiosta.
- Vaihtoehto soveltuu suurille, monimutkaisille osille, jotka tarvitsevat suurta rakenteellista lujuutta.
- Se on luotettava (tasainen laatu), kun kyseessä on massatuotanto.
Yleiset sovellukset
- Autojen alumiinivanteet.
- Ilma-alusten rakenneosat.
- Teollisuuskoneiden kuumuutta kestävät komponentit.
Squeeze Die Casting

Yleiskatsaus
Squeezedie-valuprosessissa sulaan metalliin kohdistuu korkea paine muottipesän sisällä. Koska käytetty voima on yli 20 000 psi (puntaa neliötuumaa kohti), metalli täyttää muotin hienoimmatkin yksityiskohdat ja poistaa huokoset.
Tärkeimmät ominaisuudet
- Luo erittäin tiiviitä ja vahvoja osia.
- Vähentää huokoisuutta ja parantaa mekaanisia ominaisuuksia.
- Soveltuu lujateknisiin sovelluksiin, joissa kestävyys on tärkeää.
Yleiset sovellukset
- Autojen jousituksen osat.
- Suorituskykyiset ilmailu- ja avaruustekniikan osat.
- Raskaat teollisuustyökalut ja -laitteet.
Tyhjiövalu

Yleiskatsaus
Tyhjiövalussa käytetään sen suunnittelua, jotta muotin ontelosta saadaan poistettua ilma ja kaasut ennen valuprosessia ja sen aikana. Menetelmä toteutetaan luomalla tyhjiö, ja sillä saavutetaan merkittävä huokoisuuden väheneminen, joka on yleinen vika tavanomaisessa painevalussa. Tuloksena on tarkempi, vahvempi ja virheettömämpi valu.
Tärkeimmät ominaisuudet
- Parantaa lopputuotteen mekaanisia ominaisuuksia.
- Se minimoi ilmansulkeutumisen, joten se soveltuu hyvin paksuseinäisille ja erittäin tarkoille osille.
- Parantaa valun kokonaislaatua ja vähentää jälkikäsittelyä.
Yleiset sovellukset
- Autojen rakenneosien hitsaus kevyen kestävyyden saavuttamiseksi.
- Lääketieteellisten laitteiden komponentit, joissa on korkea tarkkuus.
- Ilmailu- ja avaruustekniikan osien eheys.
Puolikiinteä painevalu (Rheocasting)

Yleiskatsaus
Rheocasting eli puolikiinteä painevalu käyttää osittain jähmettynyttä eikä täysin nestemäistä metallia. Näin metalli pysyy puoliksi nestemäisessä tai lietteisessä tilassa, jolloin se virtaa tasaisesti muottiin ja vähentää turbulenssia ja huokoisuutta.
Tärkeimmät ominaisuudet
- Tuottaa komponentteja, joilla on erinomaiset mekaaniset ominaisuudet.
- Vähentää kutistumavikoja ja huokoisuutta.
- Ihanteellinen monimutkaisille, erittäin tarkoille osille.
Yleiset sovellukset
- Kaikki auton osat, jotka vaativat suurta lujuutta ja keveyttä.
- Elektroniset kotelot, joissa on hienoja yksityiskohtia.
- Teollisuuskoneisiin, joiden osien on kestettävä kulutusta.
Yleiset metallit, joita käytetään painevalussa
Valmistusprosessi, jossa sulaa metallia ruiskutetaan muottiin korkeassa paineessa, on painevalu. Tässä prosessissa valittu metalli on myös olennainen lopputuotteen lujuuden, kestävyyden ja käyttötarkoituksen kannalta. Tällaiseen valuun voidaan käyttää erilaisia metalleja, mutta tavallisimmin käytetään värimetalleja (tai metalleja, joissa ei ole rautaa), koska niiden sulamispisteet ovat alhaisemmat ja ne ovat helpommin valettavissa.
Jäljempänä mainitaan painevalussa käytetyimmät metallit sekä niiden ominaisuudet ja käyttötarkoitukset.
1. Alumiini
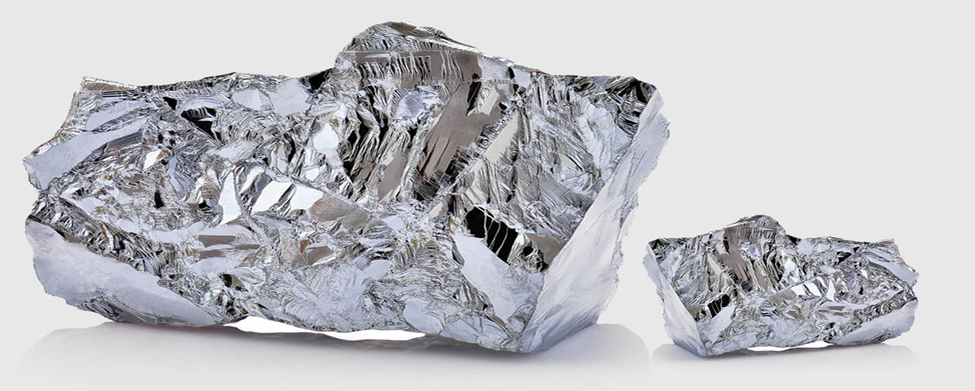
Metalleista, joita käytetään painevalu, Alumiini on kuitenkin yleisimmin käytetty, ja siinä yhdistyvät erinomaisesti hyvä lujuus, alhainen paino ja korroosionkestävyys. Koska alumiinin tiheys on suhteellisen pieni, se soveltuu hyvin käytettäväksi teollisuudenaloilla, joilla tarvitaan pienitiheyksisiä komponentteja, joilla on suuri lujuus.
Alumiinin edut painevalussa
- Se on kevyttä ja vahvaa, sillä sitä käytetään auto- ja ilmailuteollisuudessa painon vähentämiseksi.
- Korroosionkestävä - Soveltuu ulko- ja merisovelluksiin.
- Hyvä lämmön- ja sähkönjohtavuus - Käytetään elektroniikkakoteloissa ja jäähdytyslevyissä.
Alumiinivalujen yleiset sovellukset
- Moottorilohkot, vaihteistokotelot, pyörät jne. (autonosat).
- Ilmailu- ja avaruustekniikan komponentit (lentokoneiden rungot, kiinnikkeet).
- Viihde-elektroniikka (älypuhelinten rungot, kannettavien tietokoneiden kuoret).
Alumiini valetaan tavallisesti kylmävalukammiossa, koska sen sulamispiste on korkea.
2. Sinkki
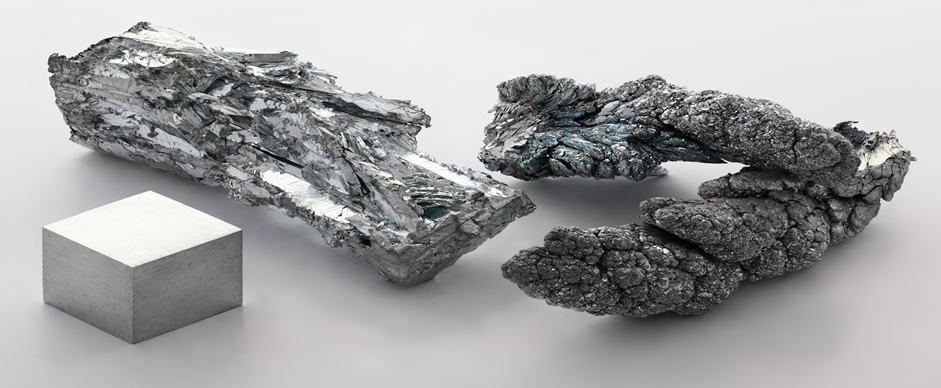
Toinen suosittu painevalumetalli on sinkki, joka on tunnettu suuresta tarkkuudestaan, lujuudestaan ja helppoudestaan. Sinkin alhaisempi sulamispiste alumiiniin verrattuna tekee siitä kuitenkin hyvin soveltuvan kuumakammiossa tapahtuvaan painevaluun ja nopeuttaa tuotantosykliä.
Sinkin edut painevalussa
- Korkea lujuus ja kestävyys - Ihanteellinen mekaanisille komponenteille.
- Matala sulamispiste - Mahdollistaa nopeamman tuotannon ja pidemmän muotin käyttöiän.
- Hyvä pintakäsittely - Vähentää tarvetta laajoihin jälkikäsittelyihin.
Sinkkivalujen yleiset sovellukset
- Pienet mekaaniset osat (hammaspyörät, kiinnittimet, saranat).
- Sähköiset ja elektroniset liittimet.
- Sisältää seuraavat lisäkomponentit autonosat (kiinnikkeet, kahvat, ovien lukot).
Lisäksi sinkki on alumiinia halvempaa, ja siksi se on suositeltavin materiaali pienten osien valmistuksessa.
3. Magnesium
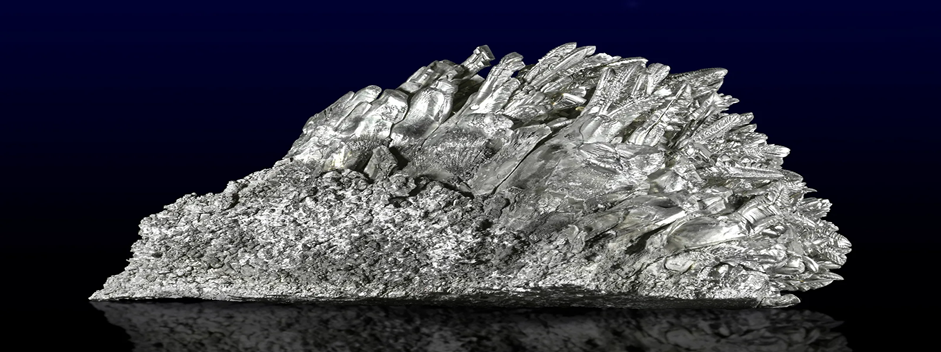
Magnesium on painevalussa käytettävä rakennemetalli, joka on kevyin käytetty metalli, ja sen lujuus-painosuhde on poikkeuksellisen hyvä. Se painaa noin 30% vähemmän kuin alumiini, mikä tekee siitä hyvän vaihtoehdon sovelluksiin, jotka vaativat painon vähentämistä.
Magnesiumin edut painevalussa
- Erittäin kevyt - ihanteellinen ilmailu- ja autoteollisuuden sovelluksiin.
- Hyvä lujuus ja iskunkestävyys - Kestää mekaanista rasitusta.
- Se on erittäin helppo työstää (työstettävyys) kuin muut metallit.
Magnesiumin painevalujen yleiset sovellukset
- Sitä käytetään autoteollisuudessa (ohjauspyörät, kojelaudan kehykset).
- Ilmailu- ja avaruusteollisuus (lennokkien ja lentokoneiden osat).
- Viihde-elektroniikka (kannettavat tietokoneet ja kamerarungot).
Vaikka magnesiumjauhe on melko helposti syttyvää, painevaletut osat ovat riittävän vakaita ja turvallisia teollisuuskäyttöön.
4. Kupari ja kupariseokset (messinki ja pronssi)

Sillä on korkea lämmön- ja sähkönjohtavuus, ja tämän vuoksi kuparia ja sen seoksia (messinki, pronssi) käytetään sähkö- ja LVI-sovelluksissa. Vaikka niiden hinta on korkeampi ja ne ovat painavampia kuin sinkki ja alumiini, niiden korroosionkestävyys ja kulutuskestävyys on parempi.
Kuparin ja sen seosten edut painevalussa
- Erinomainen sähkönjohtavuus - Käytetään elektroniikka- ja sähkökomponenteissa.
- Se on korroosionkestävä ja soveltuu hyvin LVI- ja merenkulkusovelluksiin.
- Erinomainen kulutuskestävyys - takaa pidempikestoiset osat.
Kuparin ja kupariseosten painevalujen yleiset sovellukset
- Sähköliittimet ja -liittimet.
- LVI-tarvikkeet ja -venttiilit.
- Teollisuuskoneiden osat.
Vaikka kuparia ei yleensä käytetä painevalussa yhtä paljon kuin alumiinia tai sinkkiä, se on silti ratkaisevan tärkeää tällaisissa erikoissovelluksissa, joissa tarvitaan suurta kestävyyttä ja johtavuutta.
5. Myös lyijy ja tina (ei nykyään kovin yleistä).

Lyijyn ja tinan painevalu oli aikoinaan yleistä erikoissovelluksissa, koska niiden sulamispisteet olivat alhaiset ja korroosionkestävyys erinomainen. Niiden käyttö on kuitenkin viime vuosina vähentynyt jyrkästi terveys- ja ympäristösyistä.
Lyijyn ja tinan edut painevalussa (historiallisesti)
- Korroosionkestävyys on hyvä - Sitä käytetään putkisto- ja akkukomponenteissa.
- Pehmeä ja muokattava - Soveltuu matalan rasituksen sovelluksiin.
- Niiden tiheys on suuri, minkä vuoksi niitä käytetään säteilysuojauksessa ja äänieristyksessä.
Lyijy- ja tinavalujen yleiset sovellukset (nyt rajoitettu)
- Akun liittimet.
- Laakerit ja pehmeät juotososat.
- Säteilysuojelussa käytettävät suojakomponentit.
Ympäristömääräysten tiukentuessa valmistajien on välttämätöntä löytää turvallisempia materiaaleja, kuten alumiinia, sinkkiä ja magnesiumia.
Edut ja haitat
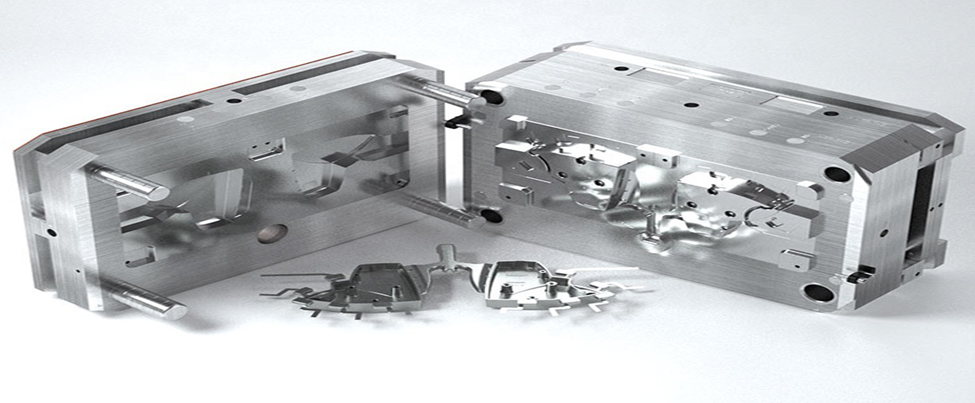
Valun edut
- Alhainen tuotantohinta - Valaminen on kustannustehokas valmistusmenetelmä, erityisesti pienissä tuotantosarjoissa, koska muihin valmistusmenetelmiin verrattuna tarvitaan vain vähän työkaluja (työkaluja ja muotteja).
- Voidaan valmistaa suuria tai monimutkaisia muotoja - Valamalla voidaan valmistaa muotoja, joita on vaikea käsitellä sorvilla tai koneistuksella tai jotka ovat liian suuria.
- Valaa monenlaisia materiaaleja - rautaa, terästä, alumiinipronssia jne.
- Tehokas materiaalin käyttö - Valaminen ei aiheuta materiaalihukkaa, koska sula metalli kaadetaan suoraan muotteihin, eikä ylimääräistä materiaalia kulu paljon.
- Soveltuu massatuotantoon - Kun muotti on valmis, voidaan suhteellisen helposti valmistaa useita samoja osia.
Valamisen haitat
- Epätarkempi kuin painevalu. Perinteiset valumenetelmät tuottavat yleensä pintapuutteita ja mittamuutoksia, jotka on vielä työstettävä.
- Pidemmät jäähdytysajat sekä jäähdytys- ja jähmettymisprosessi voivat vaikuttaa tuotannon kokonaistehokkuuteen.
- Tarvitaan enemmän viimeistelyä - Valetuissa osissa on karkea pinta tai ylimääräistä materiaalia (flash), joka on poistettava koneistamalla, kuten hiomalla ja kiillottamalla.
- Huokoisuusongelmat - Tämä voi johtua ilmataskuista tai huokosista, jotka syntyvät valuprosessin aikana ja aiheuttavat heikkoutta rakenteelliseen eheyteen.
- Muottien hajoaminen - Uudelleenkäytettävien muottien käyttö johtaa ajan myötä muottien hajoamiseen ja osien seinämän paksuuden kasvuun, mikä aiheuttaa tuotantovirheitä ja lisää huoltokustannuksia.
Die Casting -tekniikan edut
- Muottiinvalu mahdollistaa sekä nopean tuotannon, joka soveltuu suurille tuotantomäärille, että pienille tuotantoerille.
- Luo vahvoja, tarkkaan mitoitettuja osia - Korkeapaineruiskutusprosessin ansiosta osat valmistuvat tasaisesti, tiukkojen toleranssien ja hyvän laadun ansiosta, mikä minimoi lisäsäätöjä.
- Ei vaadi paljon jälkikäsittelyä - Valetut osat ovat yleensä sileitä ja yksityiskohdiltaan siistejä, eivätkä ne vaadi jälkikäsittelyä.
- Muotovalulla on erinomainen toistettavuus, joka mahdollistaa tuotannon tasalaatuisuuden lukuisissa tuotantosykleissä, minkä vuoksi se on massatuotannon suosikkimenetelmä.
- Hyvä pintakäsittely - Se ei vaadi mitään viimeistelyä, mikä tekee siitä erittäin sopivan esteettisten tuotteiden valmistukseen.
Painovaluihin liittyvät haitat
- Korkeammat alkukustannukset (muotit ovat kalliita) - Muottien suunnittelu ja valmistus voi olla kallista, joten se ei ole taloudellista, jos tuotanto on pienimuotoista.
- Ei sovellu rautametalleille - painevalu on jähmettynyt alumiiniin, sinkkiin ja magnesiumiin, mikä rajoittaa mahdollisten materiaalien valikoimaa.
- Ei sovellu suurille tai paksuille osille - Ohutseinäiset osat soveltuvat paremmin painevaluun kuin massiiviset tai paksuseinäiset osat. Muotovaluun liittyy nopea jäähdytysprosessi.
- Huokoisuus - On mahdollista, että tuote on täyttynyt ilmalla ruiskuvaluprosessin aikana, mikä johtaa huokoisuuteen, joka tekee lopputuotteesta heikon.
- Vähemmän joustavuutta suunnittelumuutoksissa - Kun valumuotti on tehty, valukappaleiden suunnittelumuutokset ovat kalliita ja aikaa vieviä verrattuna muihin valumenetelmiin.
8. Valun ja painevalun tulevaisuus
Valu- ja painevalu on lupaava tulevaisuus (ainakin lähitulevaisuudessa) automaation ja 3D-tulostuksen ansiosta. Joitakin keskeisiä suuntauksia ovat mm:
- Ympäristöystävälliset materiaalit - Kestävät ja kierrätettävät seokset.
- Älykäs valmistus - tekoälyohjattu automaatio tehokkuutta varten.
- Additiivisen valmistuksen integrointi 3D-tulostuksen ja valun hybridiprosessien muodossa.
Nykyaikaisessa teollisuudessa nämä innovaatiot parantavat tuottavuutta, vähentävät hukkaa ja pienentävät tuotantokustannuksia, mikä tekee tuotantoprosesseista entistäkin välttämättömämpiä.
Päätelmä
Laadukkaiden metallikomponenttien valmistusprosessi on eri teollisuudenaloilla edelleen yksi tärkeimmistä valmistusprosesseista. Painovaluvaihtoehtoja on monia muunnelmia, joista jokainen tarjoaa erilaisia etuja tiettyihin sovelluksiin. Vahvoja ja tiiviitä osia valmistetaan painovoimavalulla; osat ovat rakenteellisesti vankkoja ja niissä on mahdollisimman vähän vikoja matalapainemuotoisella painevalulla. Puristusvalulla on erinomainen lujuus ja kestävyys, kun taas tyhjiövalulla säästetään huokoisuutta. Semi Solid Die Casting -menetelmällä on kuitenkin etuja mekaanisten ominaisuuksien ja tarkkuuden suhteen korkean suorituskyvyn sovelluksissa, ja painevalumenetelmän valinta riippuu materiaalien valinnasta, osan monimutkaisuudesta, osan tilavuudesta ja haluttujen mekaanisten ominaisuuksien tyypistä. Prosessi kehittyy jatkuvasti automaation, seoskehityksen ja tarkkuustekniikan uusien kehitystulosten myötä, minkä ansiosta sen käyttö on yhä tehokkaampaa, edullisempaa ja ympäristöystävällisempää.
Koska teollisuus vaatii kevyempiä, vahvempia ja kestävämpiä komponentteja, teknologia kehittyy jatkuvasti. Valmistajat voivat kuitenkin estää tuotteen huonon suorituskyvyn, jätteen ja tuotannon tehottomuuden valitsemalla sopivan painevalumenetelmän. Parhaan valmistusvaihtoehdon valitsemiseksi on välttämätöntä ymmärtää nämä painevaluvaihtoehdot ja saada aikaan korkein laatu, luotettavuus ja tehokkuus tuotannossa.
Usein kysytyt kysymykset (FAQ)
1. Miten painevalu toimii ja missä muodossa se toimii?
Metallin valaminen painevaluna tunnetulla menetelmällä on prosessi, jossa sula metalli ruiskutetaan muottiin korkeassa paineessa. Tämän ansiosta valmistajat voivat valmistaa monimutkaisia, erittäin tarkkoja metalliosia, joiden pinnanlaatu on erinomainen ja joiden työstö on hyvin vähäistä.
2. Kuinka monta painevalutyyppiä?
Tärkeimmät painevalun muodot ovat painovoimavalu (GDC), matalapainevalu (LPDC), puristusvalu, tyhjiövalu ja puolikiinteä painevalu. Kunkin menetelmän erilaiset edut ja haitat riippuvat materiaalista ja sovelluksesta.
3. Mitä metalleja käytetään yleensä painevaluprosessissa?
Alumiini, sinkki, magnesium, kupari ja niiden seokset ovat yleisimpiä painevalussa käytettäviä metalleja. Metalli valitaan painon, lujuuden, korroosionkestävyyden ja lämmönjohtavuuden perusteella.
4. Miksi painevalu on niin hyödyllistä?
Korkea tuotantotehokkuus, erinomainen mittatarkkuus, minimaalinen materiaalihukka, sileä pintakäsittely ja mahdollisuus tuottaa monimutkaisia muotoja vähäisellä jälkikäsittelyllä.