
Table of Contents
ToggleFactory
China aluminum die casting factory indeed plays a significant role in the global die casting industry. Here are some reasons why China has become a major player in the aluminum die casting sector:
- Manufacturing Capabilities: China aluminum die casting factory has extensive manufacturing capabilities. They are equipped with advanced machinery, technologies, and skilled workforces to handle large-scale production. China’s manufacturing infrastructure enables the efficient and cost-effective production of aluminum die cast components.
- Cost Competitiveness: Chinese aluminum die casting factory is known for their cost competitiveness. Factors such as lower labor costs, economies of scale, and a well-established supply chain contribute to competitive pricing. This cost advantage has made China an attractive option for companies seeking cost-effective manufacturing solutions.
- Vast Experience and Expertise: China has accumulated significant experience and expertise in die casting over the years. The country has a long history of metalworking and has developed a deep understanding of the die casting process. Chinese factories have honed their skills and craftsmanship, offering high-quality die cast components that meet international standards.
- Wide Range of Industries Served: Chinese aluminum die casting factory caters to diverse industries, including automotive, aerospace, electronics, consumer goods, and industrial equipment. This versatility showcases their ability to produce components for various applications, demonstrating the breadth of their expertise.
- Production Capacity: China’s vast manufacturing infrastructure allows for high production capacity. The country has the capability to handle both large-volume orders and smaller, customized production runs. Chinese die casting factories can accommodate the needs of different customers, regardless of the order size or complexity.
- Continuous Innovation and Technology Adoption: Chinese aluminum die casting factories actively embrace innovation and technology adoption. They invest in research and development, machinery upgrades, and process improvements to stay at the forefront of the industry. This commitment to innovation ensures that Chinese factories remain competitive and capable of meeting evolving customer demands.
- Global Supply Chain Integration: China’s die casting industry has successfully integrated into the global supply chain. Many international companies collaborate with Chinese factories to access a wide range of manufacturing capabilities, cost advantages, and efficient production processes. This integration allows for seamless coordination and efficient delivery of components worldwide.
Injection Mold Price
Unlock High-Performance, Cost-Effective Solutions for Your Injection Molds
Get a Quote
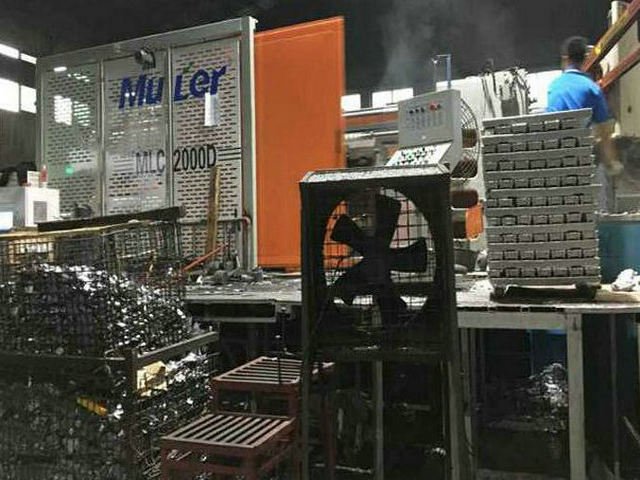
While China aluminum die casting factory has played a significant role in the industry, it is important to note that the choice of a factory should be based on individual project requirements, quality standards, and specific needs. Conducting thorough research, due diligence, and maintaining open communication will help ensure a successful partnership with a Chinese die casting factory.
Advantages of Aluminum Die Casting
Aluminum die casting offers numerous advantages that make it a preferred choice for manufacturing various components. Firstly, its lightweight nature coupled with high strength properties makes it ideal for applications where weight reduction is crucial without compromising on structural integrity. Additionally, aluminum exhibits exceptional thermal conductivity, enabling efficient heat dissipation in components such as heat sinks.
The superior corrosion resistance of aluminum makes it suitable for outdoor and harsh environment applications, ensuring long-lasting durability. The die casting process allows for the production of complex shapes with precision, facilitating the creation of intricate designs that may be difficult to achieve using other manufacturing methods. Furthermore, aluminum die casting provides cost-effective production, allowing for high volume manufacturing at a relatively low cost per unit.


Aluminum Die Casting Process
The aluminum die casting process involves several key stages. Firstly, mold preparation is essential, where a die or mold is created to shape the molten aluminum. Next, molten aluminum is injected into the mold under high pressure, ensuring it fills all the cavities and forms the desired shape.
The cooling and solidification phase follows, allowing the aluminum to solidify and take the shape of the mold. Once solidified, the casting is ejected from the mold, and any excess material or imperfections are removed through finishing operations, such as trimming, polishing, and surface treatments.
Role of an Aluminum Die Casting Factory
An aluminum die casting factory plays a vital role in ensuring the production of high-quality components. These facilities boast advanced manufacturing capabilities, including cutting-edge equipment and technology, to meet various customer requirements.
Quality assurance and control processes are rigorously implemented to guarantee the precision and reliability of the manufactured components. Skilled workforces with expertise in die casting techniques ensure efficient production and adherence to stringent quality standards. Moreover, reputable factories offer customization and prototyping services to fulfill unique client specifications.
Factors to Consider when Choosing an Aluminum Die Casting Factory
When selecting an aluminum die casting factory, several factors should be taken into account. Experience and expertise are crucial indicators of a factory’s competence, as they demonstrate a proven track record in delivering top-notch results. Production capacity and lead times are vital considerations to ensure that the factory can accommodate your manufacturing needs within the required timeframe.
Quality standards and certifications, such as ISO 9001, assure adherence to stringent quality control processes. Pricing and cost efficiency should be evaluated to ensure a balance between quality and affordability, while excellent customer support and communication facilitate a smooth collaboration.
Applications of Aluminum Die Casting
Aluminum die casting finds extensive use across various industries. In the automotive sector, it is utilized for engine components, transmission cases, and structural parts, benefiting from aluminum’s lightweight properties. Aerospace applications include aircraft components, where weight reduction is paramount to enhance fuel efficiency.
The electrical and electronics industry relies on aluminum die casting for heat sinks, electrical connectors, and housings. Aluminum die casting is also prevalent in consumer goods, such as kitchen appliances and sporting equipment, due to its aesthetic appeal and durability. Industrial equipment, including machinery and tools, utilizes aluminum die casting for its excellent mechanical properties.
Environmental Sustainability in Aluminum Die Casting
Environmental sustainability is a crucial consideration in modern manufacturing practices. Aluminum die casting offers several sustainable advantages, including energy efficiency and resource conservation. The process requires less energy compared to other casting methods, reducing carbon emissions.
Moreover, aluminum is highly recyclable, with recycled material retaining its original properties, resulting in reduced waste and a more circular economy. Aluminum die casting factories actively engage in recycling initiatives, ensuring the responsible disposal of waste and the efficient use of resources.
Compliance with environmental regulations is a priority for reputable aluminum die casting factories. They adhere to strict guidelines and standards to minimize the impact on the environment and maintain a sustainable operation. Additionally, these factories emphasize sustainable material sourcing, opting for suppliers who follow ethical and environmentally friendly practices in the extraction and processing of aluminum.
Conclusion
Choosing the right aluminum die casting factory is paramount to achieving high-quality manufacturing outcomes. The advantages of aluminum die casting, including its lightweight nature, superior strength, thermal conductivity, corrosion resistance, and cost-effectiveness, make it a preferred choice across industries. The intricate die casting process, coupled with advanced equipment and skilled workforces in factories, ensures precision, reliability, and customization.
When selecting an aluminum die casting factory, factors such as experience, production capacity, quality standards, pricing, and customer support should be carefully evaluated. The applications of aluminum die casting span various industries, including automotive, aerospace, electrical and electronics, consumer goods, and industrial equipment, underscoring its versatility and importance in modern manufacturing.
Furthermore, environmental sustainability is a key consideration in aluminum die casting, with energy efficiency, recycling, waste management, and responsible material sourcing being vital components of environmentally friendly practices.
By understanding the role and significance of an aluminum die casting factory, you can make informed decisions that lead to successful collaborations and the production of high-quality components. Embrace the benefits of aluminum die casting and partner with a reliable factory to unlock the full potential of this remarkable manufacturing technique.
We can produce components in Aluminium die casting, Magnesium die casting & Zinc die casting up to 300 tons in Aluminium( Magnesium ) & 100 tons in Zinc per month depending upon the size of the component. Facilities for die casting of rotors for FHP Motors, machining, anodizing & Powder Coating of rotors, riveting of stacks, CNC machining of end-shields also exist.
State-of-the-art facilities for making of Die Casting Molds, machining, drilling, tapping, buffing, painting, blackening, powder coating of components as per customer’s requirements.
FACILITIES
- In-house tool room facility to make & maintain precision Die Casting molds.
- Facilities for machining, trimming, drilling, lapping, tapping, polishing exist. Electroplating & powder coating as per client’s specifications..
OUR CAPACITY & CAPABILITY
- We have die casting machines ranging from 100 tons to 2000 tons
- We can die cast components ranging between a few grams to 20 kg