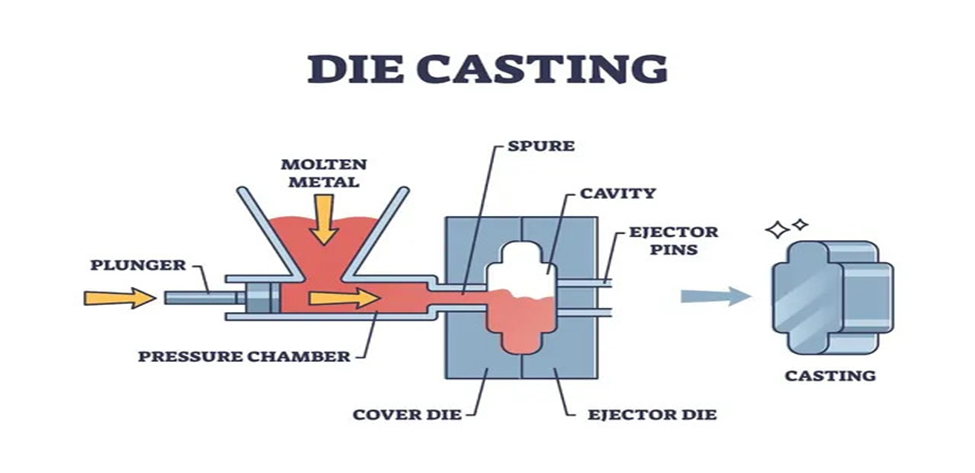
Se trata de un proceso de fabricación en el que el metal fundido se fuerza mediante presión para llenar la cavidad de un molde también conocido como fundición a presión. El molde suele ser de acero de alta calidad, por lo que la pieza puede fabricarse en grandes cantidades. La pieza acabada se produce abriendo el molde después de que el metal fundido se enfríe y forme una capa sólida. Este tipo de uso del proceso se aplica sobre todo en la fabricación de metales intrincados utilizados en la producción de diferentes piezas que requieren una gran precisión en la medición y superficies pulidas. La fundición a presión puede realizarse en aluminio, zinc y magnesio, pero también pueden utilizarse otros metales en función de la aplicación y otros requisitos. Fundición a presión se considera una de las técnicas de fabricación expertas en la concepción de la producción en serie de componentes de tamaño pequeño y mediano a partir de metales. La popularidad de este método se ha extendido a los sectores de la automoción, aeroespacial, electrónica y maquinaria industrial debido a su capacidad para producir piezas duraderas, ligeras e intrincadas. Sin embargo, este proceso es ampliamente reconocido por su capacidad para fabricar productos de geometría compleja que serían muy difíciles de realizar con técnicas convencionales.
Cómo funciona la fundición a presión

El moldeo es la primera parte del proceso de fundición a presión. En un lado del molde hay una mitad, y es una mitad de un diseño particular para que el molde tenga la forma del producto final. Se diseñan cavidades y núcleos para los moldes que suelen fabricarse a medida para que la pieza pueda reproducirse lo más fielmente posible.
1. Inyección de metal fundido:
A continuación, el metal fundido se inyecta en la cavidad del molde a alta presión para darle la forma deseada. El metal suele calentarse hasta un grado por encima de la tensión de fusión para hacerlo fluido. En la fundición a presión, la presión a la que se introduce el metal fundido en el molde puede ser de varios miles a decenas de miles de psi (libras por pulgada cuadrada), para asegurarse de que el metal fundido penetra en todos los detalles del molde.
2. Solidificación:
Esto ocurre cuando el metal se inyecta en la cavidad de la carcasa, por lo que se enfría y el metal se endurece. La calidad de la colada depende de la velocidad de enfriamiento. En este caso entran en juego otros modos de fallo (cizallamiento, trepado y deslizamiento) que dan como resultado un enfriamiento más rápido mayor resistencia mejor acabado superficial, y un enfriamiento más lento que podría dar lugar a más defectos internos y propiedades mecánicas inferiores. Los sistemas de refrigeración por agua integrados en el molde suelen utilizarse para ayudar en el proceso de enfriamiento.
3. Expulsión:
A continuación, se deja que el metal se enfríe y solidifique y entonces es fácil desmoldar la pieza de fundición más grande y expulsarla. A continuación, la mayor parte del tiempo se emplea en expulsar la pieza del molde mediante un sistema mecánico de expulsión. Esto depende de la complejidad de la pieza, que requiere otros pasos adicionales, a saber, recorte y mecanizado para darle la forma y dimensión finales.
4. 4. Control de calidad:
Tras la expulsión, se realiza un control de calidad de la pieza. Puede incluir una verificación dimensional, una inspección visual y pruebas mecánicas para confirmar que la pieza es igual o mejor que los requisitos. En teoría, en la fundición a presión se consigue una gran precisión y repetibilidad.
Tipos de fundición a presión
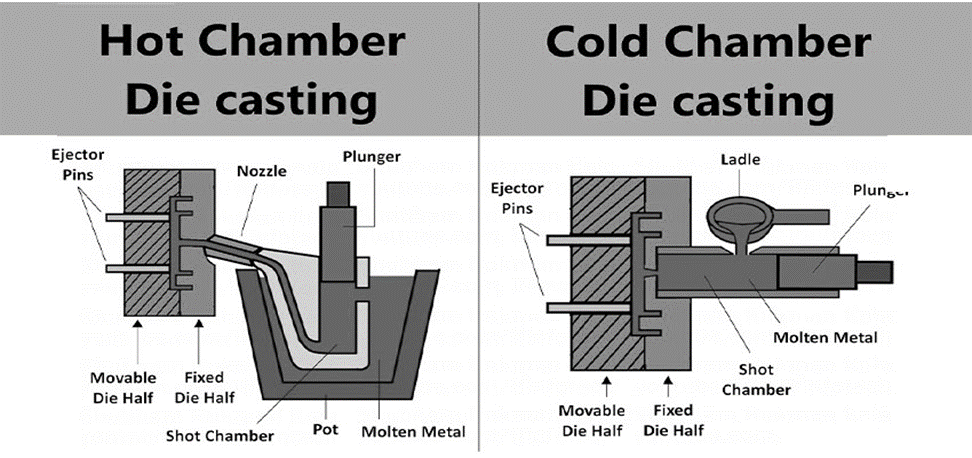
Existen dos tipos de fundición a presión: la fundición a presión en cámara caliente y la fundición a presión en cámara fría. Todos ellos son buenos y tienen sus ventajas, limitaciones y aplicaciones ideales.
1. Fundición a presión en cámara caliente
El proceso más adecuado para metales como el zinc, el magnesio y el plomo es la fundición a presión en cámara caliente, ya que el proceso se realiza a altas temperaturas y puntos de fusión. El sistema de inyección se instala dentro del horno de fusión de esta manera, el metal está siempre en contacto con la cámara.
Ventajas:
- Dado que el metal fundido está dispuesto para ser inyectado en la matriz porque se encuentra en la cámara de inyección, la fundición a presión en cámara caliente tarda menos tiempo que la fundición a presión en cámara fría.
- Etapa única: Requiere menos componentes y tiempo de preparación, por lo que se considera económica, especialmente en operaciones de gran volumen.
- Para determinados metales; La fundición a presión en cámara caliente es más apropiada en situaciones en las que los metales que se van a utilizar tienen bajas temperaturas de fusión, de modo que habrá poca o ninguna contaminación de los metales.
Desventajas:
- No se puede utilizar para trabajos en metal de alto punto de fusión como el aluminio y el latón debido a la alta temperatura en el metal que funde la cámara.
- Todos los componentes están expuestos al metal fundido, por lo que el nivel de desgaste es elevado con el paso del tiempo.
2. Fundición a presión en cámara fría
Los metales que tienen puntos de fusión más altos, como el aluminio, el latón y el cobre, se funden en cámara fría. En este caso, el metal fundido se extrae de un segundo horno y se inyecta en la cámara fría y, a continuación, en la cavidad del molde.
Ventajas:
- En términos de versatilidad en la elección de materiales, la fundición a presión en cámara fría ofrece versatilidad en el uso de materiales que permite utilizar materiales con puntos de fusión elevados.
- Mayor control de la calidad del metal: Dado que el cilindro de metal fundido se vierte en la cámara por separado, la calidad del metal puede controlarse bien para evitar la contaminación.
- Mayor vida útil de la herramienta: Al no estar en contacto con el metal durante todo el proceso de inyección, aumenta la vida útil de la herramienta.
Desventajas:
- Tiempo de ciclo más lento: El vertido manual del metal en la cámara prolonga el ciclo.
- El coste será mayor porque se trata de un procedimiento adicional con un equipo más complejo.
Comparación de los métodos de fundición a presión: cámara caliente frente a cámara fría
He aquí una comparación de los tipos más comunes de dos métodos de fundición a presión,
Característica | Fundición en cámara caliente | Fundición a presión en cámara fría |
Compatibilidad de metales | Mejor para metales de bajo punto de fusión (por ejemplo, zinc, plomo) | Ideal para metales de alto punto de fusión (aluminio, latón, etc.) |
Duración del ciclo | Ciclos más rápidos | Ciclos más lentos |
Desgaste del molde | Mayor desgaste del molde debido al contacto directo con el metal fundido | Menor desgaste del molde |
Coste | Menor coste para la producción de grandes volúmenes | Mayor coste inicial, pero mejor para metales de alta resistencia |
Complejidad de las piezas | Bueno para piezas sencillas | Mejor para piezas más complejas y grandes |
Ventajas de la fundición a presión
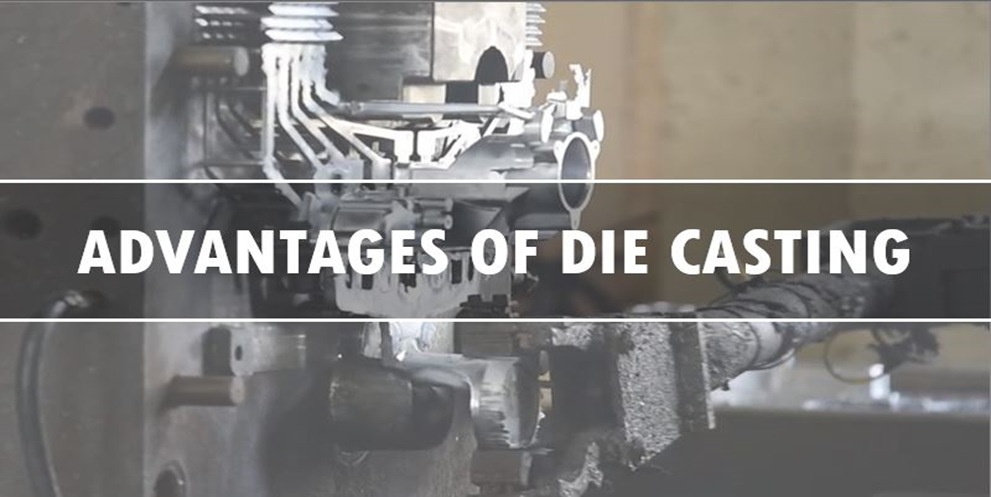
Es una de las mayores ventajas de que la fundición a presión sea uno de los principales métodos preferidos de producción a gran escala de productos a partir de aleaciones metálicas.
1. Alta precisión y exactitud
Son muchas las ventajas de la fundición a presión, que permite ofrecer una gran precisión en las matrices. Este método de producción también se utiliza ampliamente para la producción de piezas, que requiere una buena precisión dimensional que es muy crucial, ya que define los niveles de tolerancia requeridos en un trabajo específico. Hay que tener en cuenta que la fundición a presión es la única técnica de fabricación que puede producir piezas determinadas con las máximas complejidades, como las complejidades de sus geometrías.
2. Altas tasas de producción
En términos de grandes volúmenes, la fundición a presión es muy eficiente. Las piezas se fabrican de forma rápida y barata una vez creado el primer molde, con muy poca mano de obra. La demanda de polvos simulados es especialmente alta en sectores como la automoción y la electrónica, donde se necesitan grandes volúmenes de las mismas piezas.
3. Diseños complejos y paredes delgadas
La fundición a presión permite lograr diseños complejos que serían difíciles o imposibles de conseguir con los métodos de fabricación tradicionales. Este proceso permite fabricar piezas con paredes finas y estructuras internas complejas, así como realizar rebajes, lo que lo convierte en la aplicación más adecuada cuando el espacio es limitado.
4. Eficiencia material
La fundición a presión minimiza el desperdicio de material. La presión utilizada para inyectar el metal fundido llena cada parte de la cavidad del molde y, por tanto, se genera menos chatarra. Además, muchas piezas fundidas a presión pueden reciclarse, lo que contribuye a la sostenibilidad del proceso.
5. Excelente acabado superficial
El acabado superficial de las piezas producidas por fundición a presión es suave y estético. Requiere menos procesos de acabado secundarios, como el pulido o el revestimiento, con el consiguiente ahorro de tiempo y dinero.
¿Qué puede aplicarse en el proceso de fundición a presión?
Los metales no ferrosos se utilizan principalmente en la fundición a presión debido a sus buenas características de fundición. Las aleaciones de aluminio son los materiales más utilizados en la fundición a presión, como se indica a continuación.
1. Aleaciones de aluminio

Al ser ligero, resistente a la corrosión y excelente conductor del calor y la electricidad, el aluminio es el material más utilizado en la fundición a presión. Siguiendo con la lista, los grados especiales de aleaciones de aluminio se utilizan cuando la relación resistencia-peso es un factor a tener en cuenta, especialmente en las industrias del automóvil, aeroespacial y eléctrica. Por último, también son dimensionalmente estables, lo que las hace apropiadas para la producción de piezas de gran precisión.
2. Aleaciones de zinc
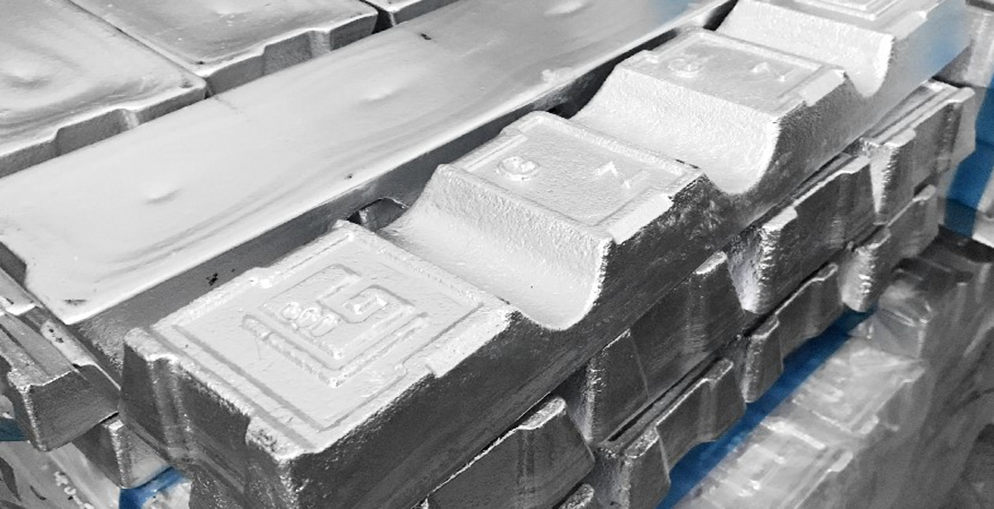
Se prefieren las aleaciones de zinc para fundición a presión por sus propiedades, como su bajo punto de fusión y su gran fluidez, que permiten realizar con facilidad y eficacia diseños complejos con secciones finas y detalles nítidos. Estas piezas de zinc poseen una gran tenacidad, son resistentes a la corrosión y tienen un pulido de alta calidad. Otro campo de aplicación de las aleaciones de zinc es la fabricación de piezas de recambio para automóviles y otros vehículos, así como la ferretería y la electrónica.
3. Aleaciones de magnesio

Cabe mencionar que el magnesio es el metal estructural más ligero y, por tanto, ofrece un peso significativo en piezas destinadas a automóviles o aviones. Esto se debe a que las aleaciones de magnesio se utilizan en piezas que deben ser fuertes pero lo más ligeras posible. Sin embargo, dado que el metal es muy reactivo, la aleación se gestiona bien cuando se somete al proceso de fundición a presión.
4. Aleaciones de cobre
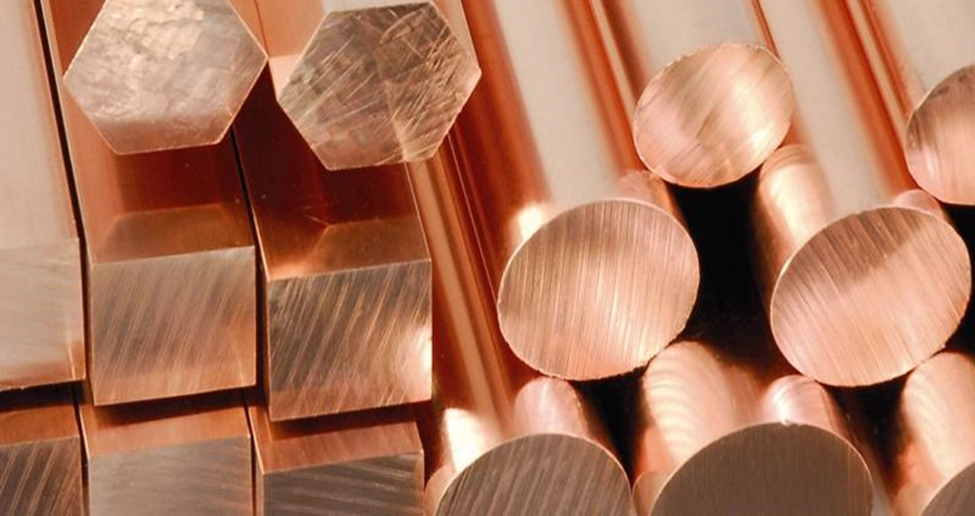
Además del aluminio y el zinc, las aleaciones a base de cobre, latón y bronce también se utilizan en fundición a presión, pero no con tanta frecuencia como el aluminio y el zinc. Ofrecen buenas propiedades de resistencia al desgaste y suelen ser útiles para aplicaciones eléctricas y de fontanería.
Es muy importante tener en cuenta que las diferentes formas de los materiales de base son adecuadas para diferentes aplicaciones y los costes varían entre estas formas y, por lo tanto, también lo hacen las propiedades del producto final.
Fundición a presión frente a otros métodos de fundición
En comparación con métodos de fundición como la fundición en arena, la fundición a la cera perdida y la fundición en molde permanente, esta sección podría ser la sección de comparación de la fundición a presión. Al hacerlo, es conveniente destacar los puntos fuertes y débiles de cada método, enseñando a los lectores cuándo elegir la fundición a presión frente a otras alternativas. Por lo tanto, ésta podría ser una visión general comparativa que ayudara a determinar el método de fundición óptimo en función del material de la pieza, la complejidad y el volumen de producción.
Característica | Fundición a presión | Fundición en arena | Fundición a la cera perdida |
Precisión | Alta precisión con tolerancias estrictas | Menor precisión y acabado superficial rugoso | Alta precisión y acabado liso |
Velocidad | Mayor rapidez en la producción de grandes volúmenes | Ciclo de producción más lento | Más lento debido a la preparación del molde |
Residuos materiales | Residuos mínimos | Mayor desperdicio debido a un acabado más rugoso | Residuos mínimos, pero moldes más complejos |
Coste | Rentabilidad en grandes volúmenes | Menor coste para la producción de bajo volumen | Mayores costes debido a la complejidad y la mano de obra |
Se compararán los procesos de producción de la fundición a presión y el moldeo por inyección.
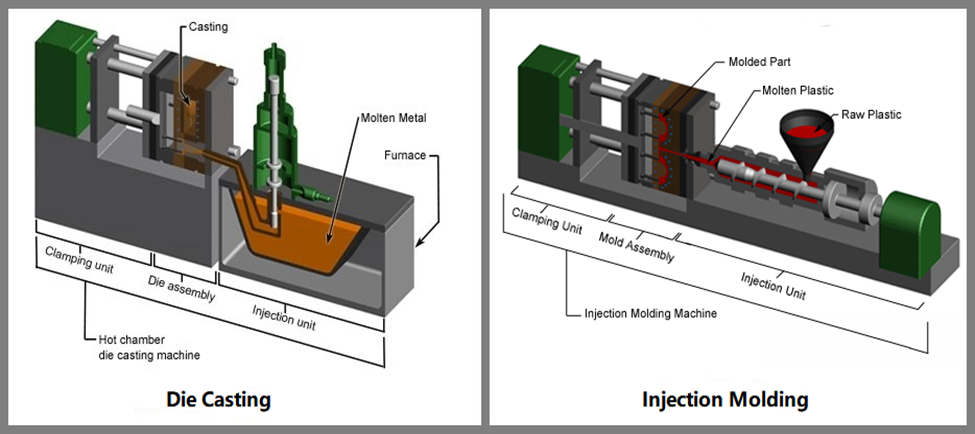
Dos técnicas comunes utilizadas para fabricar piezas de detalles finos con formas intrincadas son la fundición a presión y el moldeo por inyección. Aunque ambas técnicas implican el uso de material que forma detalles para producir productos finales, las dos tienen diferencias en cuanto al tipo de material, el producto formado y, específicamente, los beneficios en términos de cada proceso.
1. Materiales utilizados
Fundición a presión: La fundición a presión se prefiere sobre todo con otros metales aparte del grupo de metales férreos, especialmente aleaciones de aluminio, zinc, habilidades y cobre. Los metales se calientan y luego se vierten en un molde mediante el uso de presión hidráulica. En este sentido, la fundición a presión es el método más adecuado para fabricar piezas resistentes, duraderas y capaces de soportar altas temperaturas.
Moldeo por inyección: El moldeo por inyección se utiliza habitualmente entre materiales plásticos, y rara vez es posible en metales y vidrios. Entre estos polímeros se encuentran el polietileno, el polipropileno y el poliestireno. El material de formación del producto es también ligero y flexible, a lo que hay que añadir su bajo coste y sus formas bastante complejas, por lo que se puede constatar que el moldeo por inyección es perfecto para este tipo de productos.
2. Diferencias de proceso
Fundición a presión: Como su nombre indica, se trata del proceso de inyectar metal fundido a alta presión en la matriz. Surgen tras el enfriamiento y la solidificación del metal a muy alta velocidad con una tolerancia fina, y un buen acabado superficial, sin necesidad de realizar más operaciones.
Moldeo por inyección: Dado que el moldeo por inyección implica hacer uso de la inyección de material plástico fundido en una cavidad del molde mediante la aplicación de presión, entonces se trata de un moldeo por inyección. Cuando la temperatura del plástico fundido se ha reducido, el molde se abre y el producto es el molde de plástico. Aun así, el moldeo por inyección puede permitirse igualmente una gran precisión, aunque se suele utilizar para producir piezas relativamente más pequeñas y ligeras en comparación con el moldeo a presión.
3. Aplicaciones
Fundición a presión: La fundición a presión es útil para fabricar piezas duras y resistentes utilizadas en la fabricación de automóviles, aviones y otros productos electrónicos gracias a su excelente resistencia al calor.
Moldeo por inyección: Puede utilizarse para fabricar productos de consumo, envases, dispositivos médicos y juguetes, porque es ahí donde la flexibilidad, la facilidad de diseño y el bajo coste de producción son importantes.
Aplicaciones de la fundición a presión

Uno de los factores que han hecho de la fundición a presión un proceso de fabricación popular en muchas industrias es que permite producir piezas duraderas y de alta calidad con geometrías bastante complicadas. Algunas de sus aplicaciones son:
1. Industria del automóvil
Por lo general, los componentes del motor, los cárteres de transmisión y otras piezas importantes de automoción se fabrican mediante fundición a presión. Las piezas fundidas a presión tienen la precisión y resistencia necesarias para instalarse en aplicaciones exigentes de la industria del automóvil.
2. Industria electrónica
La fundición a presión en el sector de la electrónica se utiliza para fabricar carcasas de equipos electrónicos como teléfonos móviles, ordenadores portátiles y televisores. La técnica permite construir carcasas ligeras pero resistentes que protegen los componentes delicados.
3. Industria aeroespacial
La fundición a presión beneficia enormemente a las empresas de fabricación aeroespacial, ya que pueden producir piezas ligeras de gran resistencia necesarias para aviones y naves espaciales. Las piezas fundidas a presión tienen la precisión y las propiedades de material necesarias para su uso en aplicaciones en las que el rendimiento y la seguridad son cuestiones importantes.
4. Equipamiento industrial
Las piezas de maquinaria, herramientas y otros equipos industriales también se funden a presión. Como puede producir piezas con geometrías de detalles intrincados y buenas propiedades mecánicas, es una buena herramienta para estas aplicaciones.
Conclusión
La fundición a presión es un proceso de fabricación versátil, rentable y eficaz que se utiliza en muchas industrias. La calidad producida es extremadamente alta en términos de tolerancias de las piezas, acabado superficial y altos índices de producción, lo que la convierte en una excelente herramienta de fabricación para las prácticas de fabricación modernas de hoy en día. Aún así, la fundición a presión responde a las necesidades de muchas de estas industrias que requieren resistencia, precisión y eficacia en las piezas, desde la automoción hasta la industria aeroespacial, pasando por la electrónica y los equipos industriales.
Aunque la tecnología está creciendo rápidamente y probablemente seguirá utilizándose como fuente de componentes metálicos de excelente fabricación a enorme escala, en fundición a presión. Una mejor comprensión de los fundamentos de la fundición a presión puede ayudar a los profesionales de la ingeniería, la fabricación y el diseño a tomar decisiones informadas sobre cómo utilizar el proceso de fundición a presión para obtener el resultado deseado.
Preguntas frecuentes sobre la fundición a presión
1. ¿Cuál es el ciclo temporal de la fundición a presión y el moldeo por inyección?
El tiempo de ciclo para una pieza determinada oscila entre 15 y 5 minutos para la fundición a presión y entre 10 y 60 segundos para el moldeo por inyección.
2. ¿Puede utilizarse la fundición a presión para piezas de plástico?
La fundición a presión no se utiliza para piezas no metálicas. Comúnmente se utilizan las técnicas conocidas como moldeo por inyección para producir las piezas de plástico.
3. ¿Qué productos son los más adecuados para el proceso de fabricación de la fundición a presión?
La fundición a presión es la más adecuada para la fabricación de piezas complicadas de tamaño pequeño y medio con un alto grado de precisión que están hechas de metales. Algunos de los productos mecánicos que se fabrican son piezas y accesorios de coches y automóviles, carcasas y cajas de productos eléctricos, piezas electrónicas y carcasas de equipos, entre otros.
4. En qué se diferencia la fundición en coquilla de la fundición en arena.
Aun así, al comparar ambos La fundición a presión es más precisa y conlleva un proceso menos largo que la fundición en arena. Mientras que la fundición en arena es preferible para formas grandes y menos complicadas, la fundición en AL es preferible para formas pequeñas y complejas, ya que permite superficies más lisas y tolerancias más estrechas, típicas de las series de alta producción.
5. ¿Qué determina el coste de la fundición a presión?
Algunas de las consideraciones que pueden influir en el coste de la fundición a presión son: el tipo de material, la complejidad de la pieza, el diseño de la matriz y la cantidad de los pedidos. El utillaje ligero depende del volumen; aunque un volumen elevado mantiene bajo el coste por unidad, los costes iniciales del utillaje son elevados.