
La fundición y la matricería son dos importantes procesos de fabricación vitales para fabricar componentes metálicos con la precisión, durabilidad y eficacia deseadas. La fundición consiste en verter material fundido en un molde y dejar que se enfríe y solidifique. La fundición en arena, la fundición a la cera perdida y la fundición en molde permanente son algunos tipos de fundición. Sin embargo, la fundición a presión es una fundición especial que utiliza alta presión para inyectar metal fundido en la cavidad de un molde con gran precisión y un buen acabado superficial. Para aplicaciones de automoción, aeroespaciales, electrónicas e industrias afines en las que se necesitan piezas ligeras, fuertes y resistentes a la corrosión, se utiliza mucho la fundición a presión. A lo largo del tiempo se han desarrollado diferentes variantes de fundición a presión para adaptarse a las distintas necesidades de las industrias. La fundición a presión por gravedad (GDC) depende de la gravedad para llenar el molde y la fundición a presión de baja presión (LPDC) elimina la turbulencia para lograr una mayor calidad de integridad del material. La presión extrema aplicada por la fundición a presión crea piezas de alta resistencia y sin porosidades, y el aire atrapado se elimina en la fundición al vacío para obtener un componente sin defectos. Además, la fundición a presión semisólida (Rheocasting) se consigue utilizando metal parcialmente solidificado para mejorar las propiedades mecánicas y la precisión.El término general fundición en fabricación se utiliza para referirse a la forma de dar forma al metal llenándolo en un molde y dejándolo solidificar. Este método se utiliza habitualmente en la fundición en arena, la fundición a la cera perdida y la fundición en molde permanente. La matriz en la fundición a presión es el molde metálico utilizado en el proceso de fundición a alta presión, mientras que la matriz en el proceso de fundición a presión se refiere al molde metálico fijado a la cara de la matriz. Suelen fabricarse matrices de acero templado, diseñadas para la producción en serie.
Este artículo tratará sobre los conceptos de fundición y moldeado a presión, las diferencias entre estos dos conceptos y también sobre los tipos de cada uno, las posibles aplicaciones de los anteriores, así como los pros y los contras asociados a este proceso de fundición.
1. ¿Qué es el casting?
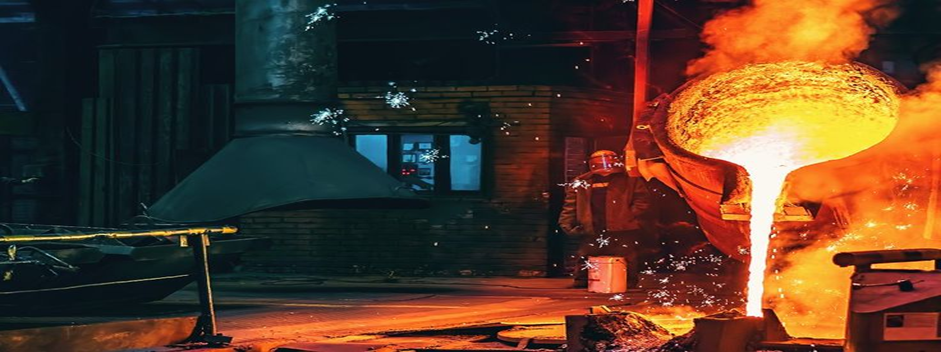
La fundición es un proceso industrial en el que un material líquido se introduce a la fuerza en un molde, donde se solidifica. El líquido puede ser básicamente cualquier metal o plástico u otro material fundible. Tras endurecerse, el material adopta una forma que corresponde a la cavidad del molde. Durante los últimos miles de años, con esta técnica se han creado herramientas, armas e intrincadas esculturas.
El proceso de fundición
Varias de estas etapas desempeñan un papel esencial en la naturaleza del proceso de fundición de un componente metálico o plástico.
- 1. Se fabrica un modelo del producto final en madera, plástico o metal. A partir de este modelo se determina la forma y las dimensiones de la cavidad del molde.
- 2. En la preparación del molde, la cavidad del molde se diseña de acuerdo con el patrón. El método de fundición determinará si es de arena, metal o cerámica. Se incorporan adecuadamente sistemas de ventilación y compuerta para permitir un flujo suave del material fundido.
- 3. Se trata de fundir la materia prima, normalmente metal o plástico, a alta temperatura en un horno. La temperatura específica para el tipo de material utilizado es diferente.
- 4. El material fundido se vierte cuidadosamente en la cavidad del molde en la cantidad correcta para evitar defectos, ya que el vertido es uniforme. Para ello pueden utilizarse sistemas de vertido manuales o automatizados.
- 5. Solidificación - El material se enfría y solidifica dentro del molde formando la forma de la cavidad. Se sabe que es la velocidad de enfriamiento la que afecta a las propiedades finales del producto moldeado.
- 6. Tras la solidificación, la pieza fundida se extrae del molde, se recorta el material sobrante, como compuertas, canales o rebabas, y a continuación el conjunto se somete a un proceso de extracción y acabado. Posteriormente pueden someterse a procesos de acabado adicionales, como esmerilado, pulido o tratamiento térmico, para mejorar el aspecto y las propiedades mecánicas del producto final.
Con este enfoque estructurado, la fundición se realiza con mayor fiabilidad y calidad.
2. ¿Qué es la fundición a presión?
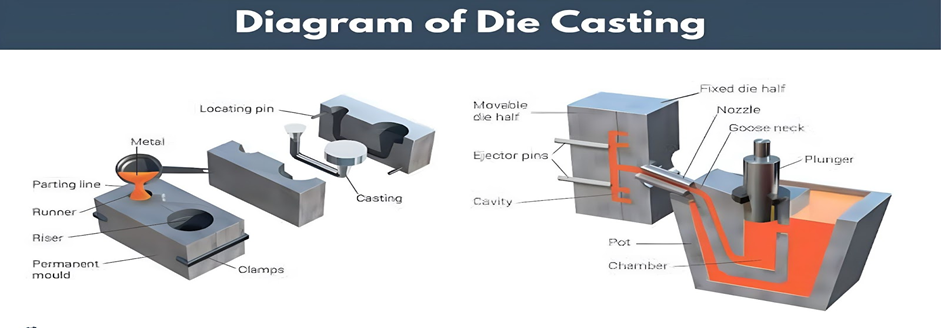
Matrices significa moldes, de ahí el nombre del proceso de fundición a presión en el que un metal fundido es forzado a alta presión para llenar una cavidad del molde. Es el más adecuado para fabricar piezas de gran volumen, complejas y dimensionalmente precisas.
El proceso de fundición a presión
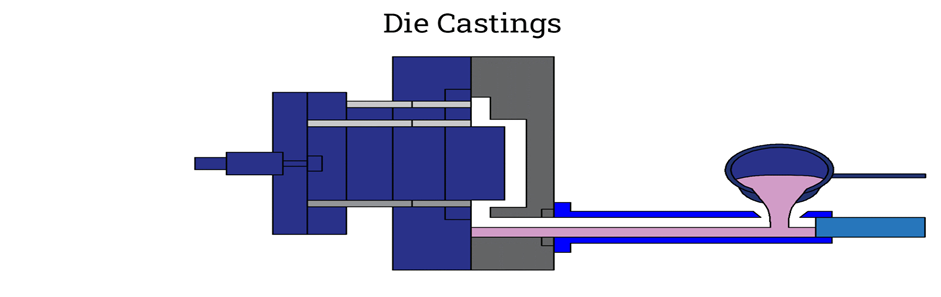
La fundición a presión es un proceso de fabricación en el que los componentes metálicos se moldean en la forma de la cavidad de una matriz a alta presión, al tiempo que se requiere una gran precisión y exactitud dimensional y de acabado superficial. Para ello se siguen los pasos que se indican a continuación:
- 1. Inyección de metal fundido: se aplica una alta presión de entre 1.500 y 25.000 psi para inyectar metal fundido (como aluminio, zinc o magnesio) en un molde de acero (matriz), que funde el metal seleccionado en un horno. Así se rellenan todos los detalles del molde con el metal fundido.
- 2. Molde o matriz - El metal fundido se enfría realmente y se solidifica dentro de la matriz, dando lugar a una pieza fuerte y precisa. Las propiedades mecánicas del producto final dependen de la velocidad de enfriamiento.
- 3. Expulsión y recorte - Una vez solidificada, la pieza fundida se expulsa de la matriz mediante pasadores eyectores. El material sobrante, incluidas las rebabas, los patines y las compuertas, se recorta para darle la forma deseada.
- 4. Acabado de la superficie - Dependiendo de la aplicación, la pieza de fundición puede necesitar un acabado posterior esmerilado, pulido pintura, anodizado o recubrimiento en polvo para aumentar su aspecto, durabilidad y resistencia a la corrosión.
Con este proceso se obtienen piezas complejas de alta resistencia y bajo peso, con poco procesamiento posterior. Los materiales más comunes en los que se utiliza la fundición a presión son los metales no ferrosos, como el aluminio, el zinc y el magnesio.
Tipos de procesos de fundición
Existen varios tipos de fundición en función del método utilizado
1 Fundición en arena

- Es uno de los métodos de fundición más versátiles y económicos que utilizan moldes de arena.
- Común en las industrias automovilística, aeroespacial y artística.
2 Fundición a la cera perdida
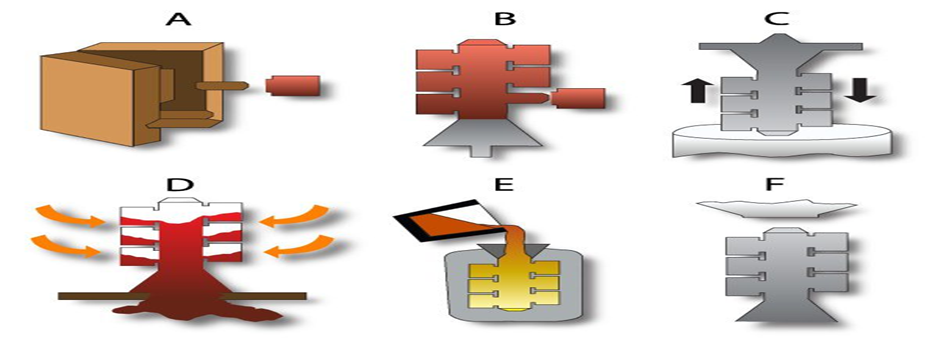
- También conocida como fundición a la cera perdida, permite fabricar piezas muy detalladas y complejas.
- Para uso en joyería, implantes médicos y componentes aeroespaciales.
3 Fundición centrífuga

- Consiste en hacer girar un molde para integrar a fondo el metal fundido.
- Se utiliza habitualmente para fabricar tubos, cilindros y anillos.
4 Fundición en molde permanente
- Reduce los residuos y el uso de moldes mediante la reutilización.
- Es ideal para la producción repetida de piezas metálicas de alta calidad.
Tipos de fundición a presión
Existen principalmente dos formas de fundición a presión:
1. Fundición a presión en cámara caliente
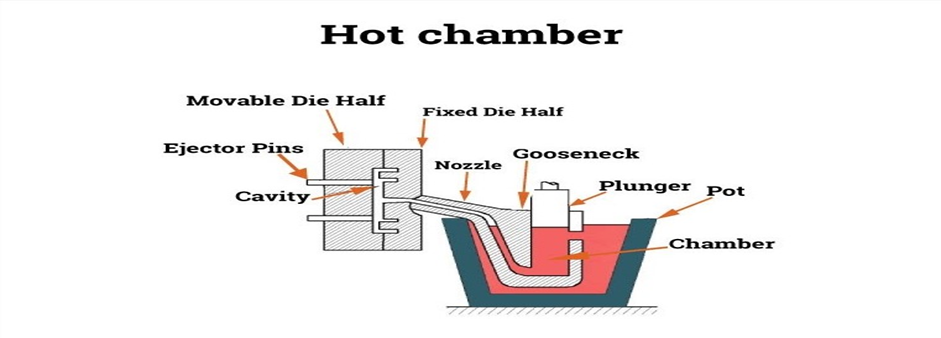
- Se utiliza para metales de bajo punto de fusión, como el zinc y el magnesio.
- Proceso más rápido con mayores índices de producción.
2. Fundición a presión en cámara fría

- Se utiliza para metales de alto punto de fusión, como el aluminio y el latón.
- Ralentiza los pasos de fusión e inyección, además de ser adecuado para piezas duraderas.
5. Diferencias entre fundición y moldeado a presión
Característica | Fundición | Fundición a presión |
proceso | Molde Metal vertido en él | El metal fundido se inyecta a alta presión |
Materiales | Metales y plásticos diversos | Principalmente metales no ferrosos como aluminio y zinc |
Precisión | Moderado | Alta precisión |
coste | Coste inicial reducido | Alto coste inicial del utillaje |
Aplicaciones | Piezas grandes y sencillas | Piezas pequeñas, complejas y de gran volumen |
Aplicaciones de la fundición y el moldeo a presión

La fundición y la fundición a presión, a su manera, desempeñan un papel inmenso en diferentes industrias y son rentables, ya que facilitan la fabricación de componentes metálicos complejos con excelente precisión.
- En la industria automovilística produce bloques de motor, carcasas de transmisión, cubos de rueda, piezas de freno y piezas de suspensión. En cuanto a las piezas ligeras de aluminio, la fundición a presión es especialmente favorecida para este fin, ya que cumple mayores niveles de eficiencia en el consumo de combustible.
- Aeroespacial: Los componentes aeroespaciales, como álabes de turbina, componentes estructurales de fuselajes, carcasas y componentes de trenes de aterrizaje, se funden para que sean duraderos y resistentes a la vez que ligeros.
- En electrónica, la fundición y el moldeado a presión son esenciales, ya que se necesitan carcasas y componentes de fundición a presión como disipadores de calor, conectores y dispositivos de blindaje para expulsar el calor y proporcionar mentalidad de seguridad a los frágiles circuitos electrónicos.
- Construcción - Tuberías, accesorios, soportes, válvulas y barandillas para la construcción de edificios, puentes, etc. que proporcionan estabilidad estructural y longevidad.
- Equipos médicos: los componentes de fundición de precisión se utilizan ampliamente en el campo médico para instrumentos quirúrgicos, carcasas de equipos de diagnóstico por imagen, implantes ortopédicos, etc.
- Maquinaria industrial - La fundición es necesaria para proporcionar solidez y resistencia al desgaste en cajas de engranajes, bombas y otras piezas de maquinaria pesada que trabajan en condiciones duras.
La aplicación de la fundición y el moldeo a presión está muy extendida, por lo que son componentes indispensables de las industrias manufactureras modernas.
Variantes de la fundición a presión
Uno de los procesos de fabricación más populares es la fundición a presión, en la que el metal fundido se introduce en el molde para fabricar componentes de características complejas y prescritas. A lo largo del tiempo se han desarrollado distintas variantes de fundición a presión para adaptarse a los materiales, los requisitos de producción y las normas de calidad. Cada método tiene sus ventajas y será más o menos adecuado para distintos tipos de aplicaciones. A continuación se presentan las principales variantes de fundición a presión con sus respectivos procesos y ventajas.
Fundición por gravedad (GDC)
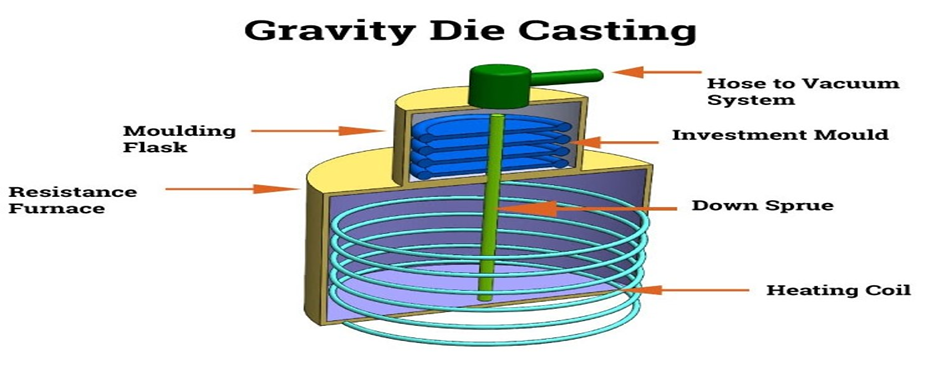
Visión general
La fundición a presión por gravedad (GDC) consiste en verter metal fundido en un molde sin utilizar alta presión. Más bien, la gravedad ayuda a guiar el metal para que llene la cavidad y se organice, como si lo hiciera por sí mismo. Este proceso es preferible para aleaciones de puntos de fusión más bajos, y se suele utilizar cuando se desea un proceso de solidificación más controlado.
Características principales
- Es más eficaz que la fundición en arena, ya que utiliza moldes reutilizables.
- Más lenta que la fundición a presión, pero la pieza es más resistente gracias a la forma más densa.
- Limitado a aleaciones específicas, como el aluminio y el magnesio.
Aplicaciones comunes
- Componentes de automóviles (culatas, piezas de motor).
- Accesorios de tuberías y cuerpos de válvulas.
- Maquinaria industrial y piezas estructurales.
Fundición a baja presión (LPDC)

Visión general
La fundición a baja presión (LPDC) se produce cuando el metal fundido se introduce en el molde a baja presión, del orden de 0,1 a 1 MPa. Con este llenado controlado, se minimizan las turbulencias y se suaviza el flujo, con lo que se reducen al mínimo los defectos, como las bolsas de aire y las inclusiones.
Características principales
- Mejor integridad del material gracias a la reducción de las turbulencias.
- Esta opción es adecuada para piezas grandes y complejas que requieren una gran resistencia estructural.
- Es fiable (calidad constante) en el caso de la producción en serie.
Aplicaciones comunes
- Llantas de aluminio para automóviles.
- Piezas estructurales de aeronaves.
- Componentes resistentes al calor en maquinaria industrial.
Fundición a presión

Visión general
En el proceso de fundición Squeezedie, se impone una alta presión al metal fundido dentro de la cavidad del molde. Como la fuerza aplicada alcanza más de 20.000 psi (libras por pulgada cuadrada), el metal rellena hasta el más mínimo detalle del molde y elimina la porosidad.
Características principales
- Crea piezas extremadamente densas y resistentes.
- Reduce la porosidad y proporciona mejores propiedades mecánicas.
- Aplicable a aplicaciones de alta resistencia donde la durabilidad es importante.
Aplicaciones comunes
- Componentes de suspensión para automóviles.
- Piezas aeroespaciales de alto rendimiento.
- Herramientas y equipos industriales pesados.
Fundición en vacío

Visión general
La fundición a presión por vacío utiliza su diseño para evacuar el aire y los gases atrapados fuera de la cavidad del molde antes y durante el proceso de fundición. Este método se aplica creando un vacío y consigue una reducción significativa de la porosidad, que es un defecto común en la fundición a presión estándar. El resultado es una fundición más precisa, resistente y sin defectos.
Características principales
- Mejora las propiedades mecánicas del producto final.
- Minimiza el atrapamiento de aire, lo que la hace adecuada para piezas de paredes estrechas y de alta precisión.
- Mejora la calidad general de la fundición, reduciendo el procesamiento posterior.
Aplicaciones comunes
- Soldadura de las piezas estructurales del automóvil para cumplir los requisitos de durabilidad del peso ligero.
- Componentes de equipos médicos de alta precisión.
- La integridad de las piezas aeroespaciales.
Fundición en molde semisólido (Rheocasting)

Visión general
La fundición en coquilla o semisólida utiliza metal parcialmente solidificado en lugar de totalmente líquido. De este modo, el metal se mantiene en un estado semilíquido o de lechada, por lo que fluye suavemente en el molde y se reducen las turbulencias y la porosidad.
Características principales
- Produce componentes con propiedades mecánicas superiores.
- Reduce los defectos de contracción y la porosidad.
- Ideal para piezas complejas de alta precisión.
Aplicaciones comunes
- Cualquier pieza de automóvil que exija propiedades de alta resistencia y ligereza.
- Carcasas electrónicas con finos detalles.
- Para maquinaria industrial con componentes que deben soportar el desgaste.
Metales comunes utilizados en la fundición a presión
El proceso de fabricación utilizado para inyectar metal fundido en un molde a alta presión es la fundición a presión. El metal seleccionado en este proceso también es esencial en la resistencia y durabilidad del producto final y en su aplicación. Se pueden utilizar varios metales para este tipo de fundición, pero los metales no ferrosos (o sin hierro) son los más utilizados, ya que tienen puntos de fusión más bajos y son más moldeables.
A continuación se mencionan los metales más utilizados en la fundición a presión con sus propiedades y usos.
1. Aluminio
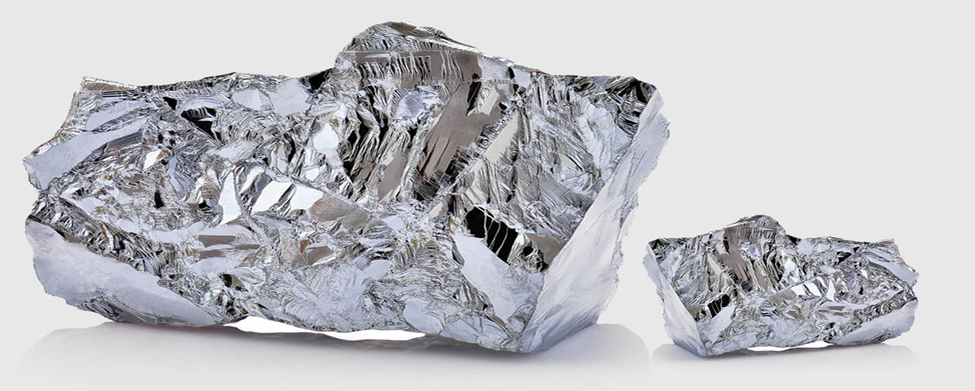
Entre los metales utilizados en fundición a presión, Sin embargo, el aluminio es el más utilizado y presenta la combinación ideal de buena resistencia, bajo peso y resistencia a la corrosión. Con una densidad relativamente baja, es un buen candidato para ser utilizado en industrias donde se necesitan componentes de baja densidad con alta resistencia.
Ventajas del aluminio en la fundición a presión
- Es ligero y resistente, por lo que se utiliza en las industrias automovilística y aeroespacial para reducir el peso.
- Resistente a la corrosión - Adecuado para aplicaciones marinas y al aire libre.
- Buena conductividad térmica y eléctrica - Se utiliza en carcasas electrónicas y disipadores de calor.
Aplicaciones comunes de las piezas moldeadas a presión de aluminio
- Bloques de motor, cajas de transmisión, ruedas, etc. (piezas de automóvil).
- Componentes aeroespaciales (armazones de aviones, soportes).
- Electrónica de consumo (cuerpos de smartphones, carcasas de portátiles).
Normalmente, el aluminio se funde a presión mediante fundición en cámara fría debido a su elevado punto de fusión.
2. Zinc
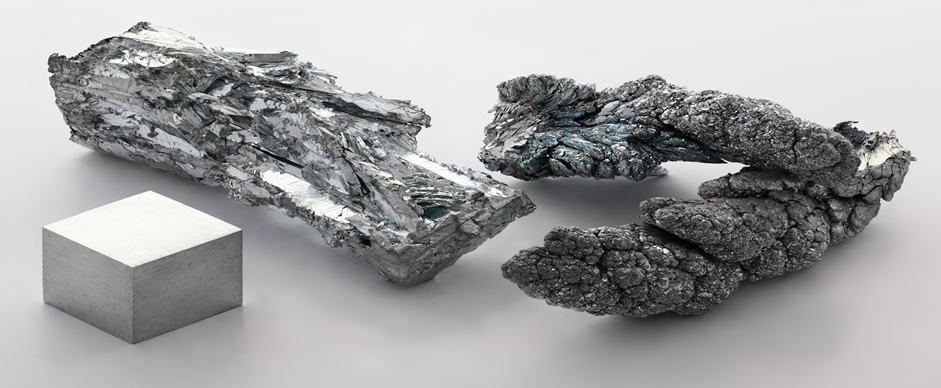
Otro metal popular de fundición a presión es el zinc, conocido por su gran precisión, resistencia y facilidad de fundición. Sin embargo, el punto de fusión más bajo de zinc en comparación con el aluminio, lo que hace que sea muy adecuado para la fundición a presión de cámara caliente y produce ciclos de producción más rápidos.
Ventajas del zinc en la fundición a presión
- Alta resistencia y durabilidad - Ideal para componentes mecánicos.
- Bajo punto de fusión - Permite una producción más rápida y una mayor vida útil del molde.
- Buen acabado superficial: reduce la necesidad de un tratamiento posterior exhaustivo.
Aplicaciones comunes de las piezas moldeadas a presión de zinc
- Pequeños componentes mecánicos (engranajes, cierres, bisagras).
- Conectores eléctricos y electrónicos.
- Incluye componentes adicionales como piezas para automóviles (soportes, manillas, cerraduras de puertas).
Además, el zinc es más barato que el aluminio, por lo que es el material preferido en la fabricación de piezas pequeñas.
3. Magnesio
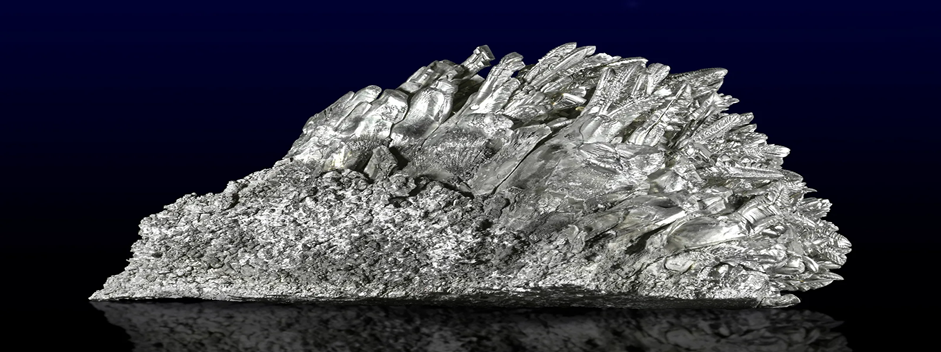
Como metal estructural para la fundición a presión, el magnesio es el metal más ligero que se utiliza y ofrece una excepcional relación resistencia-peso. Pesa aproximadamente 30% menos que el aluminio, lo que lo convierte en una buena opción para aplicaciones que exigen una reducción de peso.
Ventajas del magnesio en la fundición a presión
- Extremadamente ligero: ideal para aplicaciones aeroespaciales y de automoción.
- Buena solidez y resistencia al impacto - Puede soportar tensiones mecánicas.
- Es muy fácil de trabajar (maquinabilidad) que otros metales.
Aplicaciones comunes de las piezas moldeadas a presión de magnesio
- Se utiliza en la industria del automóvil (volantes, marcos de salpicaderos).
- Industria aeroespacial (drones y piezas de aviones).
- Electrónica de consumo (ordenadores portátiles y cámaras).
Aunque la forma en polvo del magnesio es bastante inflamable, las piezas fundidas a presión son suficientemente estables y seguras para su uso industrial.
4. Cobre y aleaciones de cobre (latón y bronce)

Tiene una gran conductividad térmica y eléctrica, por lo que el cobre y sus aleaciones (latón, bronce) se utilizan en aplicaciones eléctricas y de fontanería. Aunque su precio es más elevado y pesan más que el zinc y el aluminio, tienen mayor resistencia a la corrosión y al desgaste.
Ventajas del cobre y sus aleaciones en la fundición a presión
- Excelente conductividad eléctrica - Se utiliza en componentes electrónicos y eléctricos.
- Es resistente a la corrosión y muy adecuado para aplicaciones de fontanería y marinas.
- Mayor resistencia al desgaste: garantiza piezas más duraderas.
Aplicaciones comunes de las piezas moldeadas a presión de cobre y aleaciones de cobre
- Conectores y terminales eléctricos.
- Accesorios y válvulas de fontanería.
- Componentes de maquinaria industrial.
Aunque el cobre no suele utilizarse tanto como el aluminio o el zinc en la fundición a presión, sigue siendo crucial en aplicaciones tan especializadas en las que se necesita una gran durabilidad y conductividad.
5. También plomo y estaño (no demasiado comunes hoy en día)

Para aplicaciones especializadas, la fundición a presión de plomo y estaño estuvo muy extendida en el pasado por sus bajos puntos de fusión y su excelente resistencia a la corrosión. Sin embargo, su uso ha disminuido drásticamente en los últimos años por motivos sanitarios y medioambientales.
Ventajas del plomo y el estaño en la fundición a presión (históricamente)
- La resistencia a la corrosión es buena - Se utiliza en fontanería y componentes de baterías.
- Suave y maleable - Adecuado para aplicaciones de baja tensión.
- Tienen una alta densidad, por lo que se utilizan en aplicaciones de blindaje contra radiaciones e insonorización.
Aplicaciones comunes de las piezas moldeadas a presión de plomo y estaño (ahora limitadas)
- Terminales de batería.
- Rodamientos y piezas de soldadura blanda.
- Componentes de blindaje en protección radiológica.
A medida que aumenta la normativa medioambiental, los fabricantes se ven obligados a encontrar materiales más seguros, como el aluminio, el zinc y el magnesio.
Ventajas y desventajas
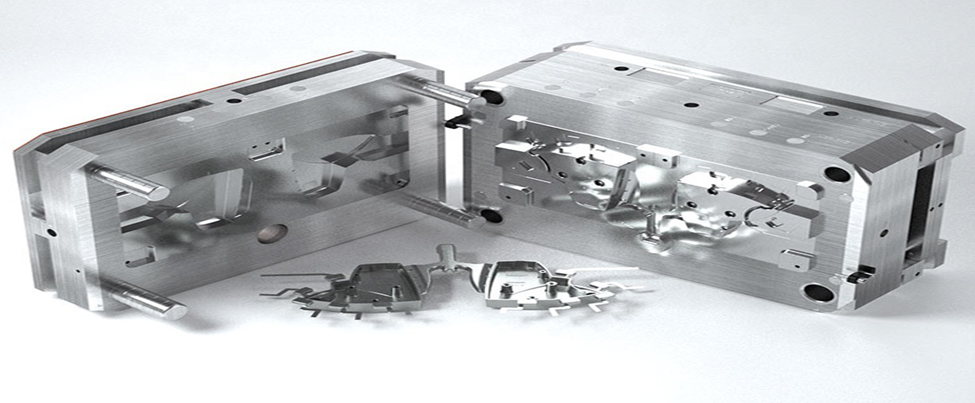
Ventajas de la fundición
- Bajo precio de producción - La fundición es un método de fabricación rentable, sobre todo para pequeñas series de producción, porque requiere poco utillaje (herramienta y matriz) en comparación con otros procesos de fabricación.
- Puede fabricar formas grandes o complejas - La fundición puede crear formas difíciles de tratar en un torno o con mecanizado, o demasiado grandes para manejarlas.
- Funde una gran variedad de materiales: hierro, acero, aluminio, bronce, etc.
- Uso eficiente del material - La fundición no desperdicia material porque el metal fundido se vierte directamente en los moldes y no pierde mucho material sobrante.
- Adecuada para la producción en serie - Una vez establecido el molde, se pueden producir muchas piezas iguales con relativa facilidad.
Desventajas de la fundición
- Menos preciso que la fundición a presión. Los métodos de fundición tradicionales tienden a producir imperfecciones superficiales y variaciones dimensionales que deben mecanizarse.
- Los tiempos de enfriamiento más largos y el proceso de enfriamiento y solidificación pueden afectar a la eficiencia global de la producción.
- Se requiere más trabajo de acabado - Las piezas de fundición tendrán una superficie rugosa o un exceso de material (rebabas) que deberá eliminarse mediante mecanizado, como esmerilado y pulido.
- Problemas de porosidad: puede tratarse de bolsas de aire o huecos que se forman durante el proceso de fundición y que debilitan la integridad estructural.
- Degradación de moldes - El uso de moldes reutilizables, con el tiempo, degradará estos moldes y aumentará el grosor de las paredes de las piezas, con los consiguientes defectos de producción y mayores costes de mantenimiento.
Ventajas de la fundición a presión
- La fundición a presión permite tanto producciones de alta velocidad, adecuadas para series de producción de gran volumen, como lotes de baja producción.
- Crea piezas resistentes y de dimensiones precisas: gracias al proceso de inyección a alta presión, las piezas salen de forma consistente, con tolerancias ajustadas y una buena calidad que minimiza los ajustes posteriores.
- No requiere mucho procesamiento posterior - Las piezas de fundición inyectada suelen tener superficies lisas y detalles limpios que no requieren mecanizado secundario.
- La fundición a presión es excelente en repetibilidad, lo que permite la uniformidad en la producción en numerosos ciclos de producción, razón por la que es un método preferido para la producción en serie.
- Buen acabado superficial - No requiere ningún acabado, lo que lo hace muy adecuado para fabricar productos que tengan en cuenta la estética.
Desventajas de la fundición a presión
- Mayor coste inicial (las matrices son caras) - El diseño y la fabricación de moldes de fundición a presión pueden ser caros y, por tanto, no resultar económicos si la producción es a pequeña escala.
- No apto para metales ferrosos - La fundición a presión se congela al aluminio, el zinc y el magnesio, lo que limita la gama de materiales posibles.
- No es adecuado para piezas grandes o gruesas - Los componentes de paredes finas son más adecuados para la fundición a presión que los masivos o de paredes gruesas. La fundición a presión implica un proceso de enfriamiento rápido.
- Porosidad - Es posible que el producto se haya llenado de aire durante el proceso de moldeo por inyección y eso dará lugar a porosidad, lo que hace que el producto final sea débil.
- Menor flexibilidad en las modificaciones de diseño - Una vez fabricada la matriz, la modificación del diseño de las piezas fundidas será costosa y llevará mucho tiempo en comparación con otros métodos de fundición.
8. Futuro de la fundición y la matricería
La fundición y la matricería tienen un futuro prometedor (al menos en breve) gracias a la automatización y la impresión en 3D. Algunas tendencias clave son:
- Materiales ecológicos: aleaciones sostenibles y reciclables.
- Fabricación inteligente: automatización basada en inteligencia artificial para aumentar la eficiencia.
- Integración de la fabricación aditiva en forma de procesos híbridos de fundición con impresión 3D.
En las industrias modernas, estas innovaciones mejorarán la productividad, reducirán los residuos y disminuirán los costes de producción, lo que hará aún más indispensables los procesos de producción.
Conclusión
En diversas industrias, el proceso de fabricación de componentes metálicos de alta calidad sigue siendo uno de los principales procesos de fabricación. Las opciones de fundición a presión presentan muchas variantes, cada una de las cuales aporta distintas ventajas para aplicaciones específicas. Las piezas fuertes y densas se producen mediante fundición a presión por gravedad; las piezas son estructuralmente sólidas con defectos mínimos mediante fundición a baja presión. La fundición a presión ofrece una resistencia y durabilidad extraordinarias, mientras que la fundición al vacío reduce la porosidad. Sin embargo, la fundición a presión semisólida tiene ventajas en las propiedades mecánicas y la precisión para aplicaciones de alto rendimiento, y la elección del método de fundición a presión depende de la selección de materiales, la complejidad de la pieza, el volumen de la pieza y el tipo de propiedades mecánicas deseadas. El proceso sigue perfeccionándose gracias a los nuevos avances en automatización, desarrollo de aleaciones e ingeniería de precisión, lo que hace que su uso sea cada vez más eficaz, menos costoso y respetuoso con el medio ambiente.
Debido a la demanda de componentes más ligeros, fuertes y resistentes por parte de las industrias, la tecnología evolucionará continuamente. Sin embargo, los fabricantes pueden evitar el mal rendimiento del producto, los residuos y la ineficacia de la producción eligiendo el método de fundición a presión adecuado. Para elegir la mejor opción de fabricación es necesario comprender estas variantes de fundición a presión y obtener la máxima calidad, fiabilidad y eficacia en la producción.
Preguntas más frecuentes (FAQ)
1. ¿Cómo funciona la fundición a presión y de qué forma trabaja?
La fundición de metales mediante el proceso conocido como fundición a presión es un proceso en el que el metal fundido se inyecta en un molde a alta presión. Esto permite a los fabricantes producir piezas metálicas complejas de alta precisión con un magnífico acabado superficial y muy poco mecanizado.
2. ¿Cuántos tipos de fundición a presión existen?
Las principales formas de fundición a presión son la fundición por gravedad (GDC), la fundición a baja presión (LPDC), la fundición a presión, la fundición al vacío y la fundición semisólida. Las ventajas y desventajas de cada método dependen del material y la aplicación.
3. ¿Qué metales se utilizan normalmente en el proceso de fundición a presión?
El aluminio, el zinc, el magnesio, el cobre y sus aleaciones son los metales más utilizados en la fundición a presión. El metal se elige por su peso, resistencia, resistencia a la corrosión y conductividad térmica.
4. ¿Por qué es tan beneficiosa la fundición a presión?
Alta eficiencia de producción, excelente precisión dimensional, mínimo desperdicio de material, acabado superficial liso y es posible producir formas complejas con poco procesamiento posterior.