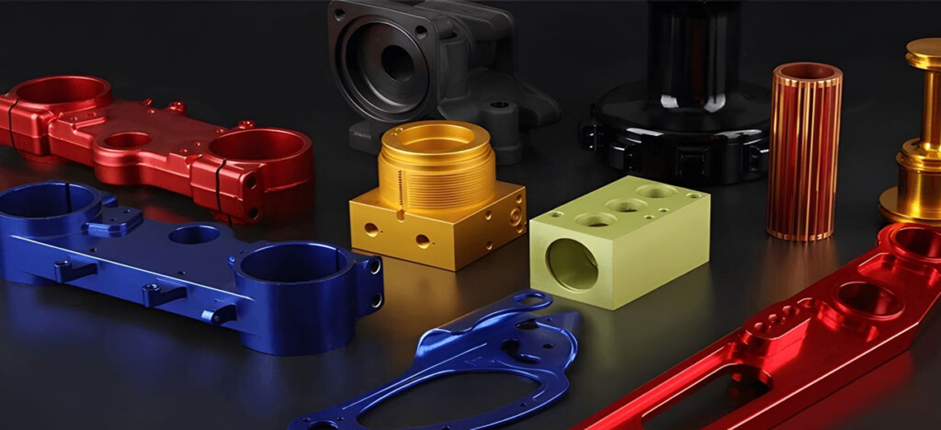
Anodizado material de aluminio se utiliza principalmente porque es ligero, fuerte y resistente a la corrosión. Aunque el aluminio en bruto ofrece cierta durabilidad y resistencia a los arañazos, es propenso a la oxidación, las abolladuras y los arañazos, que pueden alterarlo a largo plazo y mantener su aspecto. Para que el aluminio sea más resistente y duradero, se anodiza para formar una capa protectora de óxido en su superficie. El motivo de esta capa es que endurece el metal, dándole una superficie que no se corroe ni desgasta y un aspecto más agradable. El aluminio anodizado es el preferido por estos factores y se utiliza mucho en el sector aeroespacial, automoción, construcción y electrónica de consumo. La anodización consta de varias fases: limpieza de la superficie, inmersión en un baño electrolítico, oxidación mediante corriente eléctrica y sellado. Además de reforzar el material, este tratamiento puede colorearse en diferentes tonos y acabados. La coloración electrolítica, la coloración por inmersión, la coloración integral y la coloración por interferencia son diferentes técnicas comunes de coloración.
El anodizado ordinario y el anodizado duro son los dos tipos principales de anodizado. Normalmente hay dos procesos disponibles: el anodizado ordinario, utilizado principalmente para aplicaciones de acabado y bajo peso, y el anodizado duro, que proporciona una excelente durabilidad, resistencia al desgaste y solidez para aplicaciones militares, industriales y aeroespaciales. Además del anodizado, el aluminio puede procesarse mediante otros tratamientos superficiales como la galvanoplastia, el recubrimiento en polvo, el recubrimiento por conversión de cromatos, el recubrimiento PVD, los recubrimientos cerámicos o el galvanizado en caliente. El aluminio anodizado no posee estas propiedades de manera uniforme, por lo que se utiliza como material versátil y fiable en muchas industrias, y cada método proporciona al material propiedades específicas mejoradas: resistencia a la corrosión, dureza, conductividad, etc.
En este artículo hablaremos de las propiedades, ventajas, aplicaciones y mantenimiento del aluminio anodizado, y de por qué es una alternativa mejor que otros metales y tratamientos. Si conocemos estos aspectos podremos entender qué material utilizar para una industria y un consumidor concretos.
¿Qué es el aluminio anodizado?

El aluminio anodizado es un aluminio que se ha sometido a un proceso electroquímico para producir una capa de óxido más gruesa y duradera en su superficie. La presencia de esta capa de óxido anódico aumenta la resistencia del metal a la corrosión, mejora la dureza de la superficie y aumenta la capacidad del metal para adherirse a tintes y revestimientos.
El proceso de anodización
En otras palabras, el proceso de anodización incluye varios pasos clave.
- La superficie de aluminio se limpia para eliminar la suciedad, grasa o impurezas de la superficie antes de los pasos de secado, limpieza y pretratamiento. La superficie también puede grabarse para obtener un acabado uniforme.
- Baño de anodizado: el aluminio se introduce en una solución electrolítica (normalmente ácido sulfúrico) y se aplica corriente eléctrica. Se inicia la oxidación y se forma la capa de óxido de aluminio engrosada.
- La capa de óxido poroso puede colorearse simultáneamente (Opcional) proporcionando de forma similar colorantes o pigmentos según se desee.
- Cierre de los poros - El sellado de la capa anodizada se realiza mediante agua caliente o vapor, con lo que se cierran los poros, mejorando aún más la resistencia a la corrosión.
Material de aluminio anodizado Propiedades principales

1. Mayor resistencia a la corrosión
El aluminio anodizado es uno de los más resistentes a la corrosión. Esto lo hace prácticamente inservible en exteriores o cuando se sumerge en agua, ya que la capa de óxido protege el metal de la humedad y de nuestro entorno.
2. Mayor dureza superficial
La anodización mejora notablemente la dureza del aluminio, que se vuelve más resistente a arañazos, abolladuras y desgaste. Uno de estos aluminios anodizados duros es muy duradero y, de hecho, se utiliza en aplicaciones de alto rendimiento.
3. Atractivo estético y variedad de colores
Además, el aluminio anodizado se ofrece en negro, oro, bronce, plata, etc. sin cambiar la textura natural del metal. Por eso es la opción preferida tanto para aplicaciones arquitectónicas como decorativas.
4. Ligero pero resistente
Aunque la capa de óxido se pone encima del aluminio, esto no hace que el aluminio sea significativamente más pesado, y sigue siendo más ligero que materiales más pesados como el acero inoxidable.
5. Aislamiento eléctrico
Dado que el aluminio anodizado es un mal conductor de la electricidad en comparación con el aluminio sin tratar, es un material atractivo para utilizar en aplicaciones en las que se necesita aislamiento con fines eléctricos o electrónicos.
6. Respetuoso con el medio ambiente y sostenible
El aluminio anodizado no es tóxico en absoluto, es reciclable y no emite COV (compuestos orgánicos volátiles) peligrosos y perjudiciales para la salud, por lo que es respetuoso con el medio ambiente.
¿Cómo dar color a las piezas de aluminio anodizado?

Es bien sabido que el aluminio anodizado es capaz de mantener los colores de forma muy vibrante. La coloración electrolítica y la coloración por inmersión son dos de las muchas técnicas utilizadas para colorear el aluminio anodizado.
1. Coloración electrolítica

Una forma popular de embellecer el aluminio anodizado es la coloración electrolítica, mediante la cual el aluminio anodizado se colorea con tonos duraderos y resistentes a los rayos UV. Una vez que el aluminio ha pasado por el proceso de anodizado, se introduce en un baño con sales metalizadas. En los últimos años se han desarrollado sales metalizadas que, al aplicar una corriente eléctrica, se depositan en los poros abiertos de la superficie anodizada creando permanentemente una superficie de color metálico.
Por último, el color depende del tipo de sales metálicas que intervengan. Las sales de cobre, por ejemplo, dan a la solución un tono rojizo, y otros metales pueden darle otras tonalidades. Su uso está muy extendido porque los colores obtenidos de este modo duran mucho y no pierden intensidad, lo que los hace ideales para exteriores o usos de alta exposición.
2. Coloración por inmersión

Otro método de coloración es la "coloración por inmersión", que ofrece una gran variedad de colores. Durante este tipo de proceso, la capa porosa se sumerge en una solución colorante en la que el aluminio anodizado absorbe el pigmento. Una vez alcanzado un tono, el aluminio se sella en agua para impedir que continúen las reacciones.
La coloración por inmersión ofrece tonos contrastados mucho más vibrantes y personalizables, pero no son resistentes a los rayos UV y los colores se decoloran en mucha menor medida cuando se exponen a la luz solar. Sin embargo, esta falta de durabilidad es la principal razón por la que no se suele utilizar en aplicaciones en las que la durabilidad de las piezas es un factor importante.
3. Coloración integral (proceso de un solo paso)
La coloración integral es un proceso único que incorpora el anodizado y la coloración en un solo proceso más eficaz que los métodos de varios pasos. A diferencia de otras técnicas, los electrolitos, que reaccionan con la superficie del aluminio y se secan rápidamente, crean tonos metálicos profundos y ricos, como el negro, el dorado o el bronce. El color se forma en la propia capa de óxido y, gracias a ello, es muy duradero y no se raya, no es propenso a la corrosión y no se decolora.
Aunque la coloración integral produce acabados de calidad, es poco frecuente debido a su coste y complejidad. Suelen aplicarse a componentes arquitectónicos, electrónica de gama alta y equipos industriales en los que las piezas deben soportar condiciones exigentes en las que se requiere un aspecto atractivo y longevidad.
4. Coloreado de interferencias
La coloración por interferencia es un proceso de anodizado avanzado de alta tecnología en el que el grosor de la capa de óxido del producto puede manipularse para crear azules, verdes y morados iridiscentes de varios tonos sin tintes ni pigmentos. En lugar de absorber el color, el aluminio reacciona a las ondas de luz reflejando diferentes colores según el punto de vista.
Los usos habituales de este método en arquitectura, productos de lujo o metalistería decorativa son conseguir los efectos visuales únicos deseados. Su excepcional resistencia a la intemperie lo hace adecuado para aplicaciones artísticas y de señalización de alta gama, así como para superficies exteriores. Aunque es muy complejo, no es fácil fabricarlo en serie.
Alternativas al aluminio anodizado

El tratamiento superficial del aluminio, como el anodizado, se utiliza ampliamente para mejorar la durabilidad, la resistencia a la corrosión y el aspecto del aluminio. El motivo es que forma una capa de óxido protectora electroquímica que hace que el aluminio sea adecuado para diversas aplicaciones. No obstante, existen diferentes métodos de tratamiento de superficies que pueden ofrecer resultados similares o incluso mejores cuando se eligen adecuadamente los requisitos. A diferencia de estas alternativas, presentan ventajas únicas como, por ejemplo, una mayor protección, mejores propiedades de adherencia y acabados decorativos. A continuación se presentan algunas alternativas comunes al aluminio anodizado.
1. Galvanoplastia
La galvanoplastia es la técnica de depositar una fina capa de metal, por ejemplo, níquel, cromo, oro... sobre la superficie del aluminio u otros metales. Se hace mediante un proceso electroquímico que mejora la resistencia a la corrosión, la durabilidad y la estética del artículo. Embellecedores de automóviles, así como joyas y componentes eléctricos, son algunos de los materiales que se electrochapan habitualmente. La mayor ventaja de este método es que los fabricantes pueden decidir el material de chapado y personalizar las propiedades del aluminio. Por ejemplo, puede hacerse para obtener la conductividad del chapado en oro, o la mayor dureza y resistencia al desgaste del cromado.
2. Recubrimiento en polvo
El recubrimiento en polvo es uno de los métodos más utilizados para el acabado de metales mediante el uso de partículas de pintura secas cargadas electrostáticamente. El resultado a altas temperaturas es una película duradera y protectora sobre la pieza recubierta. Este método tiene una amplia aplicación por su buena resistencia a la corrosión, buena resistencia a los impactos y multitud de selecciones de color. A diferencia de la pintura líquida tradicional sin disolventes, el recubrimiento en polvo no utiliza disolventes nocivos. Se utiliza mucho en componentes arquitectónicos, piezas de automoción y electrodomésticos, ya que resiste las duras condiciones ambientales sin descascarillarse ni desteñirse.
3. Recubrimiento de conversión de cromatos (alodine o película química)
La alodina o película química se utiliza como proceso químico para cubrir el aluminio con una fina capa protectora denominada revestimiento de conversión al cromato. Mejora la resistencia a la corrosión sin afectar a la conductividad eléctrica, por lo que es adecuado para aplicaciones aeroespaciales y electrónicas. A diferencia del anodizado, que crea una gruesa capa de óxido, el revestimiento de conversión de cromato proporciona una mejor adherencia de la pintura y los adhesivos. Los materiales ligeros con revestimientos protectores fiables son útiles, sobre todo en las industrias, donde son necesarios. Y aunque no es tan duradero como el anodizado, puede ser más adecuado para aplicaciones con menos desgaste.
4. Recubrimiento por deposición física de vapor (PVD)
El revestimiento PVD es un tratamiento de superficies de aluminio que consiste en la deposición de compuestos metálicos en forma de finas capas sobre el aluminio en el vacío. Esto mejora enormemente la dureza, la resistencia al desgaste y el aspecto estético. Entre los revestimientos PVD, los duraderos TiN y CrN pueden aplicarse en superficies superduras (por ejemplo, herramientas industriales, armas de fuego, relojes de lujo) gracias a su durabilidad superior. Con una gran variedad de acabados metálicos como el dorado, el negro y los colores iridiscentes, los revestimientos de PVD se adaptan a un amplio número de acabados sin modificar la forma de la pieza.
5. Recubrimientos cerámicos
Los revestimientos cerámicos son excelentes protectores de superficies resistentes al desgaste y al calor para el aluminio y otros metales. Se aplican como una capa muy fina y muy duradera mediante pulverización térmica o deposición química de vapor (CVD). Mención especial merecen los revestimientos cerámicos aplicados en aplicaciones industriales, aeroespaciales y de automoción, donde los componentes están sometidos a temperaturas extremas y condiciones duras. Además de tener una durabilidad extrema, los revestimientos cerámicos pueden ser aislantes térmicos, por lo que se utilizan en piezas de motores, sistemas de escape y utensilios de cocina.
6. Galvanización en caliente
El galvanizado en caliente es un proceso de revestimiento de superficies por el que un objeto metálico, como el acero o el hierro, se galvaniza al sumergirlo en un baño de zinc fundido. Deja un revestimiento de zinc que ofrece resistencia a la corrosión a largo plazo, adecuado para exteriores, puentes o equipos industriales. Aunque el galvanizado en caliente no se utiliza normalmente como protección del aluminio, sigue siendo una herramienta ideal para proteger los metales ferrosos contra la oxidación y los daños ambientales. Lo que hace que este proceso sea tan clave es el hecho de que se permite que el revestimiento de zinc se cure por sí mismo, de modo que si se araña la superficie, la corrosión no volverá a producirse y evitará la oxidación de la superficie de acero.
¿Qué alternativa elegir?
Alternativa | Lo mejor para | Principales ventajas |
Galvanoplastia | Piezas metálicas decorativas y funcionales | Acabado brillante, resistente a la corrosión, personalizable |
Recubrimiento en polvo | Acabados de color duraderos | Resistente a los impactos, respetuoso con el medio ambiente, disponible en muchos colores |
Revestimiento de conversión de cromatos | Aeroespacial y electrónica | Mejora la adherencia, resistencia a la corrosión, conductividad |
Revestimiento PVD | Herramientas de alto rendimiento y artículos de lujo | Acabado metálico extremadamente duro y resistente al desgaste |
Revestimientos cerámicos | Aplicaciones resistentes al calor | Barrera térmica, alta durabilidad, antiarañazos |
Galvanización en caliente | Estructuras de acero resistentes | Protección duradera contra la corrosión, ideal para exteriores |
Diferencia entre anodizado duro y anodizado ordinario

El anodizado es un proceso para mejorar la resistencia a la corrosión, la durabilidad y el aspecto del aluminio. Dos tipos comunes son el anodizado ordinario y el anodizado duro. Ambos métodos generan una capa de óxido, aunque las condiciones del proceso, las propiedades de la capa de óxido y la aplicación son diferentes en cada caso.
1. Diferencias en el proceso de anodizado
Concentración de ácido
Es la concentración de ácido utilizada en el proceso de anodizado lo que afecta al revestimiento final. El anodizado ordinario implica concentraciones de ácido de 20% más o menos en la formación de una capa de óxido lisa y uniforme.
Por otro lado, el anodizado duro utiliza una concentración de ácido más baja, como una concentración de aproximadamente 15% o menos, y el revestimiento es más denso y resistente.
Requisitos de temperatura
La dureza de la capa de óxido es un factor importante, que depende totalmente de la temperatura. El anodizado ordinario se realiza a 18 22°C (en función del tipo y la cantidad de aditivos, la temperatura máxima es de 30°C).
En caso de altas temperaturas, podría pulverizar o agrietar el revestimiento. Un revestimiento más fuerte y resistente al desgaste solo puede crearse con anodizado duro a temperaturas mucho más bajas, inferiores a 5 °C.
Niveles de corriente y tensión
El anodizado ordinario se realiza con una densidad de corriente de 1 - 1,5 A/dm² y una tensión no superior a 18 V.
El anodizado duro, sin embargo, debe realizarse a una tensión mucho más alta, incluso de hasta 120 voltios, para crear un óxido mucho más grueso y también muy duro.
2. Diferencias en el rendimiento del revestimiento
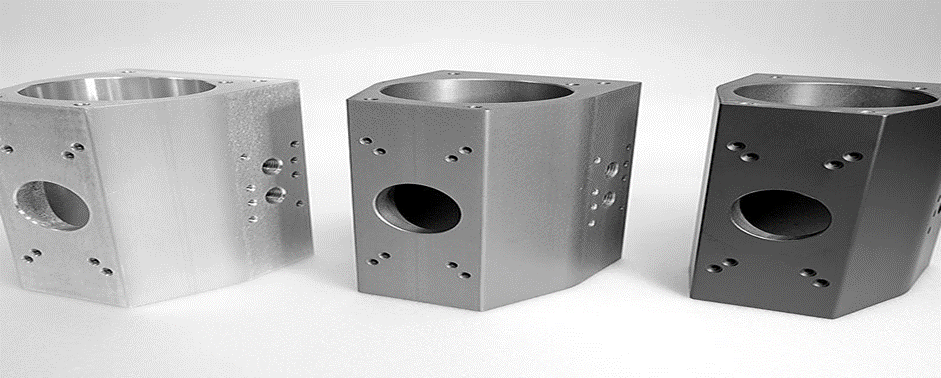
Aplicaciones y usos
La decoración y el alisado son los principales usos del anodizado ordinario, ya que puede colorear una superficie anodizada y alisar la superficie. Los bienes de consumo, los muebles y los componentes arquitectónicos son lugares típicos donde se encuentra.
Sin embargo, el anodizado duro se utiliza en aplicaciones industriales, militares y de automoción, por su mayor resistencia al desgaste y durabilidad.
Aspecto de la superficie
El método de anodizado determina la textura de la superficie del aluminio anodizado. Las superficies anodizadas ordinarias son lisas y uniformes, lo que resulta apropiado para aplicaciones estéticas. Las superficies anodizadas duras son más rugosas al ojo microscópico, lo que les confiere mayor capacidad para soportar el desgaste y la fricción.
Porosidad
La porosidad se refiere al número de pequeñas aberturas en la capa de óxido. Las capas anodizadas ordinarias muy porosas son mejores para teñir y colorear, pero algo menos resistentes al desgaste. Las capas anodizadas duras son menos porosas y, por tanto, más fuertes y resistentes a los daños.
Espesor del revestimiento
La protección básica y la estética las proporciona la capa de óxido, que suele ser inferior a 15μm, creada mediante anodizado ordinario.
Sin embargo, el anodizado duro forma una capa mucho más gruesa, normalmente superior a 15μm, necesaria para aplicaciones duras y resistentes al desgaste.
Transparencia y opacidad
El paso de la luz depende del grosor de la capa de óxido y del material utilizado. Se pueden teñir fácilmente de distintos colores, ya que los revestimientos anodizados ordinarios son transparentes.
Los revestimientos anodizados duros son opacos debido a su mayor grosor y, por tanto, inadecuados para la coloración decorativa.
Productos comunes de aluminio anodizado
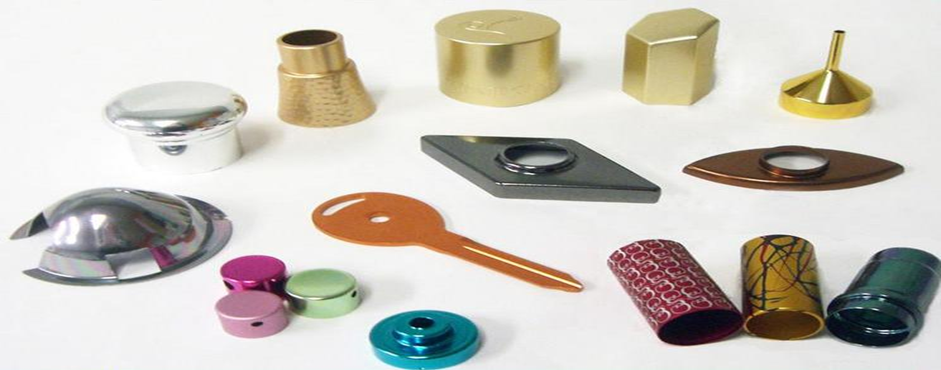
1. Fundas para smartphones y portátiles
El aluminio anodizado se utiliza como carcasa exterior de muchos smartphones y portátiles de gama alta. Gracias a este material, los dispositivos son resistentes a arañazos, abolladuras y desgaste. Además, les proporcionan un acabado suave y elegante y, al mismo tiempo, los mantienen ligeros y fáciles de transportar.
2. Carcasas para tabletas
Por su ligereza y excelente protección, las carcasas para tabletas se fabrican a veces con aluminio anodizado. Los fabricantes también pueden elegir entre una amplia variedad de colores que no degradan las tabletas, ya que pueden pasar por el proceso de anodizado.
3. Marcos de puertas y ventanas
El aluminio anodizado se utiliza en los marcos de puertas y ventanas de los edificios porque es resistente a la oxidación y no se decolora ni descascarilla. Esto lo convierte en una gran opción para su uso en aplicaciones domésticas y edificios comerciales en los que se requiere una larga vida útil y poco mantenimiento.
4. Embellecedores de automóviles y marcos de bicicletas
Las propiedades del aluminio anodizado lo convierten en una buena opción para los consumidores que buscan una gran durabilidad y un menor peso en los vehículos, dos factores que pueden aumentar la eficiencia del combustible. Los cuadros de bicicleta de aluminio anodizado son populares en el sector del ciclismo por su resistencia y menor peso, aptos para su uso en ciclismo regular y carreras de competición.
Tipos de aluminio anodizado
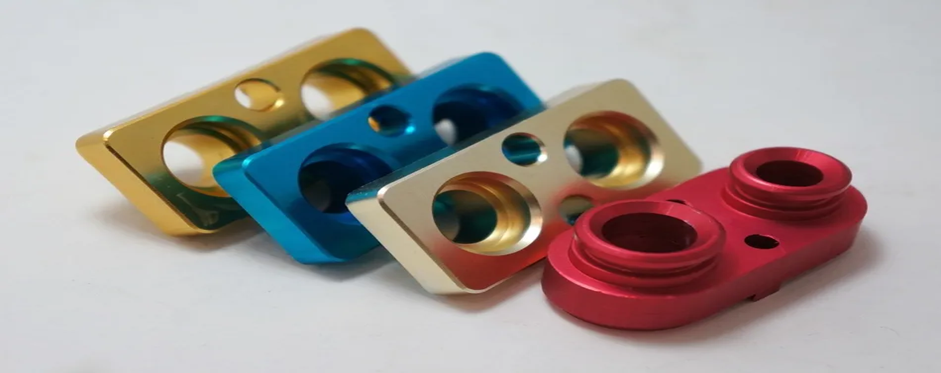
Existen diferentes tipos de aluminio anodizado, cada uno con sus propiedades y ventajas únicas en función de las diferentes características y respuesta requeridas en función de la aplicación y el rendimiento. El tipo de anodizado se elegirá en función de parámetros como la durabilidad, la resistencia a la corrosión, el grosor y las características estéticas. A continuación se indican los principales tipos de aluminio anodizado y sus usos específicos.
1. Tipo I (anodizado con ácido crómico)

En el anodizado de tipo I, el ácido crómico crea una capa de óxido fina pero muy resistente a la corrosión. Es un método excelente para el sector aeroespacial sin necesidad de reducir mucho el peso, ya que no altera las dimensiones normales. El aluminio anodizado de tipo I tiene un grosor inferior al de tipo II, por lo que no es adecuado para el anodizado de color, aunque proporciona una buena adherencia de pinturas e imprimaciones.
Características principales
- Produce una fina capa de óxido resistente a la corrosión
- Mantiene la conductividad del aluminio
- Ideal para aplicaciones aeroespaciales y de defensa
- Proporciona una excelente adherencia para revestimientos.
2. Tipo II (anodizado con ácido sulfúrico)

El tipo de anodización más común es el Tipo II, que utiliza ácido sulfúrico para hacer crecer una capa de óxido de grosor medio. Este tipo puede anodizarse para darle color y se utiliza en bienes de consumo, componentes arquitectónicos y piezas de automoción. Porque ofrece buena resistencia a la corrosión y al desgaste, además de mejorar la estética.
Características principales
- Proceso de anodización estándar
- Proporciona una capa de óxido de espesor moderado
- Permite el anodizado en color
- Se utiliza habitualmente en electrónica, muebles y construcción.
3. Tipo III (anodizado duro)
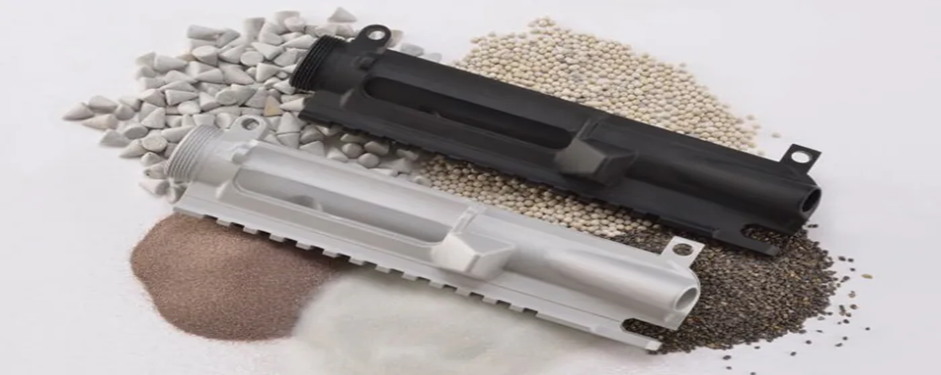
El anodizado de tipo III, también conocido como anodizado de capa dura, produce la capa de óxido más gruesa y dura y es muy resistente al desgaste y duradero. Este tipo se utiliza mucho en aplicaciones militares, industriales y utensilios de cocina en los que se necesita una gran resistencia, una mayor resistencia a la abrasión y una mayor protección contra la corrosión. El aluminio anodizado de tipo III tiene una gran durabilidad y se utiliza a menudo en componentes de maquinaria, piezas de armas de fuego y dispositivos médicos.
Características principales
- Produce una capa de óxido gruesa y resistente al desgaste
- Ofrece la máxima durabilidad y dureza
- Se utiliza en aplicaciones industriales de alto rendimiento
- Proporciona una resistencia superior a la corrosión
Aplicaciones del material de aluminio anodizado
Debido a sus propiedades superiores, el aluminio anodizado se utiliza en varias industrias y productos.
1. Industria aeroespacial y del automóvil
- Componentes de aeronaves como paneles del fuselaje y estructuras de las alas
- Paneles de la carrocería, piezas del motor y piezas de adorno que van en el coche
- Duradero gracias a su ligereza y resistencia a la corrosión
2. Construcción y arquitectura
- Marcos de ventanas, muros cortina, puertas, etc.
- Materiales para tejados y barandillas
- Los rascacielos modernos y las fachadas de los edificios se utilizan por su atractivo estético.
3. Electrónica de consumo y electrodomésticos
- El MacBook de Apple utiliza aluminio anodizado.
- Aparatos de cocina como cafeteras y tostadoras
- El anodizado evita las huellas dactilares, los arañazos y las manchas.
4. Equipos médicos y de laboratorio
- Instrumental quirúrgico y bandejas médicas
- La naturaleza no reactiva llevó al uso de superficies estériles de laboratorio
- La longevidad en un entorno sanitario depende de la resistencia a la corrosión
5. Equipamiento deportivo y para actividades al aire libre
- Cuadros de bicicleta, material de senderismo y camping.
- Materiales duraderos y ligeros para condiciones extremas
6. Utensilios de cocina
- Sartenes o utensilios de aluminio anodizado antiadherente
- Es resistente al rayado y a las altas temperaturas.
- Es una alternativa más segura a los revestimientos antiadherentes tradicionales.
Comparación del aluminio anodizado con otros metales
Característica | Aluminio anodizado | Acero inoxidable | Titanio |
Peso | Ligero | Pesado | Moderado |
Resistencia a la corrosión | Excelente | Muy alta | Excelente |
Dureza de la superficie | Alta | Muy alta | Extremadamente alto |
Conductividad eléctrica | Bajo | Moderado | Bajo |
Opciones estéticas | Varios colores | Limitado | Limitado |
Coste | Asequible | Caro | Muy caro |
Mantenimiento y cuidado del aluminio anodizado
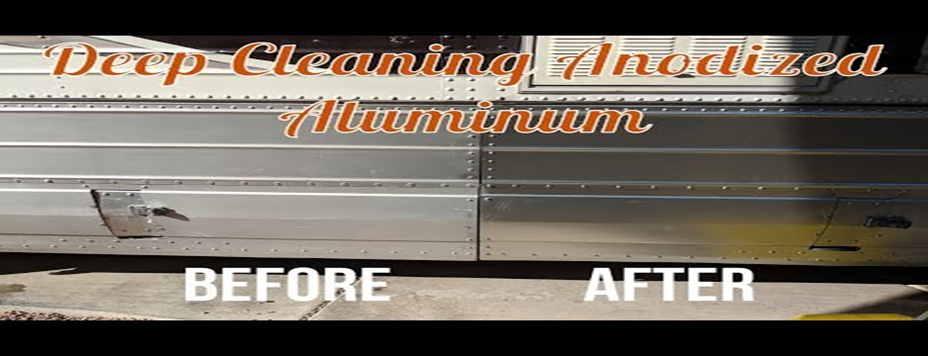
El aluminio anodizado es muy duradero y puede soportar la corrosión, sin embargo, anodizar el aluminio con regularidad mantiene su aspecto fuerte y duradero. Los cuidados preventivos, como la forma natural de anodizar el aluminio ante el deterioro, el cambio de color o los daños en la superficie, mantendrán el material en buena forma durante años. A continuación se ofrecen algunos consejos para el mantenimiento de las superficies de aluminio anodizado.
1. Limpieza regular
Debe mantener limpio el aluminio anodizado utilizando agua y jabón suave con frecuencia. Utilice un paño suave o una esponja para eliminar el polvo, la suciedad y la mugre. Absténgase de utilizar limpiadores ásperos o estropajos de acero, ya que pueden rayar la capa anodizada. Un detergente suave en agua tibia hará maravillas con las manchas problemáticas. Tras la limpieza, aclare con agua limpia y seque la superficie con una toalla suave para evitar manchas de agua.
2. Evite los productos químicos agresivos
Resistente también a muchos elementos ambientales, puede, sin embargo, resultar dañado por ácidos fuertes, soluciones alcalinas o limpiadores industriales agresivos que afectan a su capa protectora de óxido. NO utilice lejía, limpiadores a base de amoniaco ni sustancias ácidas que decoloren o agujereen el material. En caso de necesitar productos de limpieza más fuertes, utilice siempre una solución de pH neutro específica para metales anodizados.
3. Pulido y protección
Para mantener el aluminio anodizado brillante y liso, utilice un paño de microfibra suave o una esponja y pula la superficie sólo muy ligeramente. Si necesita más protección, aplique una cera no abrasiva o algún tipo de protector del aluminio anodizado. La capa añadida ayuda a prevenir la oxidación y a mantener el brillo y el tono del metal en la mayoría de las ocasiones.
4. Evitar arañazos y daños por impacto
El aluminio anodizado tiene una gran resistencia a los arañazos, pero no es a prueba de arañazos. No utilice objetos afilados, herramientas pesadas o materiales ásperos directamente sobre la superficie para no sufrir abolladuras, arañazos o desconchones. Debe tener a mano fundas protectoras o incluso un rotulador Sharpie para evitar daños accidentales en los componentes de aluminio anodizado.
5. Protección contra condiciones ambientales adversas
Las superficies anodizadas se desgastan gradualmente por la exposición prolongada al agua salada, la radiación UV y la intemperie extrema. Por otra parte, el aluminio anodizado debe inspeccionarse periódicamente si se utiliza en exteriores. En entornos marinos o costeros, el enjuague de la superficie con agua dulce puede eliminar los depósitos de sal que acelerarán la corrosión.
Conclusión
El aluminio anodizado es un material muy versátil y fiable para muchas industrias por su ligereza, durabilidad, mayor dureza superficial y resistencia a la corrosión. El anodizado no solo endurece, sino que también confiere al aluminio un aspecto atractivo, razón por la cual se prefiere en los sectores de la construcción, la automoción, el aeroespacial, la electrónica y los utensilios de cocina.
El aluminio anodizado es una de las principales ventajas del circuito en términos de larga vida útil con mínimos requisitos de mantenimiento. Sin embargo, con una simple limpieza con agua y jabón suave, evitando los productos químicos agresivos, y protegiéndolo de arañazos y daños por impacto, la usabilidad se prolongará.Hay una excelente resistencia al desgaste y la corrosión, sin embargo, es crítico qué tipo de anodizado (anodizado ordinario o duro) se elige para la aplicación prevista.
La galvanoplastia, el recubrimiento en polvo y los recubrimientos PVD son otros tipos de tratamientos alternativos que proporcionan su propio conjunto de propiedades. Aunque el aluminio anodizado puede no ser tan respetuoso con el medio ambiente como este revestimiento ecológico, sigue siendo muy complementario a este revestimiento ecológico como uno de los principales favoritos entre las soluciones respetuosas con el medio ambiente debido a su asequibilidad y rendimiento superior en diferentes entornos.
Preguntas más frecuentes (FAQ)
1. ¿Para qué se utiliza el aluminio anodizado?
Por sus propiedades de ligereza, resistencia a la corrosión y durabilidad, el aluminio anodizado se utiliza en la industria aeroespacial, de automoción, construcción, electrónica, utensilios de cocina y equipos industriales.
2. ¿Puede oxidarse el aluminio anodizado?
Aluminio anodizado no se oxida porque tras la anodización se forma una capa de óxido que resiste la humedad y los daños ambientales.
3. ¿Es seguro el aluminio anodizado en los utensilios de cocina?
El aluminio anodizado, sí, no es tóxico y es seguro para cocinar. Es comprensible que se utilice en utensilios de cocina porque no reacciona con los alimentos y forma una superficie resistente a los arañazos.
4. ¿Cuál es la mejor manera de limpiar una superficie de aluminio anodizado?
Para limpiar una superficie de aluminio anodizado, sólo se necesita jabón suave y agua tibia, utilizando un paño suave. Utilice únicamente productos de limpieza suaves y no abrasivos, productos químicos no agresivos y no utilice nunca estropajos de acero, ya que podrían dañar la superficie anodizada.
5. ¿Qué son el aluminio anodizado y el aluminio con recubrimiento de polvo?
La capa de óxido protectora del aluminio anodizado se forma mediante un proceso electroquímico, mientras que la pintura utilizada en el aluminio con revestimiento en polvo es una pintura seca que se cura a altas temperaturas. El recubrimiento en polvo suele tener más variedad de colores de pintura que el aluminio anodizado, pero es más probable que se desconche con el tiempo; el aluminio anodizado es más duradero y resistente a la decoloración.