Since the modern manufacturing world is surrounded by die-cast tooling, it is no wonder that die-cast tooling has become a critical step in manufacturing precise and reliable metal components. Whether it be automotive parts or consumer electronics, the aim is that the products are of the highest quality standards as regards durability, function, and appearance. It is this comprehensive guide of every part of die-cast tooling from the types to its advantages and disadvantages to the applications that you will find extremely helpful if you are fully into manufacturing.
Although the cost of producing parts out of die-cast tooling is higher initially, on the other hand, it provides you with reduced material waste, faster production cycle time, and being ability to make complex designs with very little post-processing if any at all. Not only did advances in cooling systems and more efficient substitution parts like replacement inserts, surface coatings, and the like increase efficiency and durability but also less worn grids and better purge for the electrical system helped.
What is Die Cast Tooling?
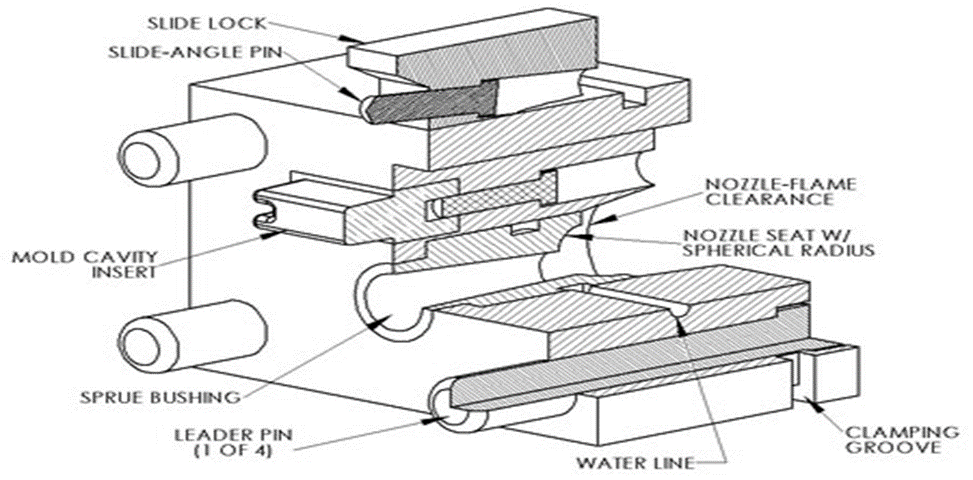
Die-casting tooling means the tools and processes for die-cast tooling. These dies (molds) also shape molten metal into complex and accurate components under high pressure. The engineering of advanced die-cast tooling requires materials and meticulous design practice, as well as advanced engineering skills to facilitate the production of consistently produced defect-free parts.
First, metal (usually aluminium, zinc, or magnesium) is melted and passed under high pressure into the die. The quality of the final product is dependent on the precision of the tooling, and that is why die-cast tooling is vital to industrial manufacturing.
Components of Die Cast Tooling
The process of die casting is a precision manufacturing process that greatly relies on the array of tools needed to produce high-quality metal parts. The combination of these tools is such that they are accurate, durable and efficient. The most common tools used in die casting are listed below.
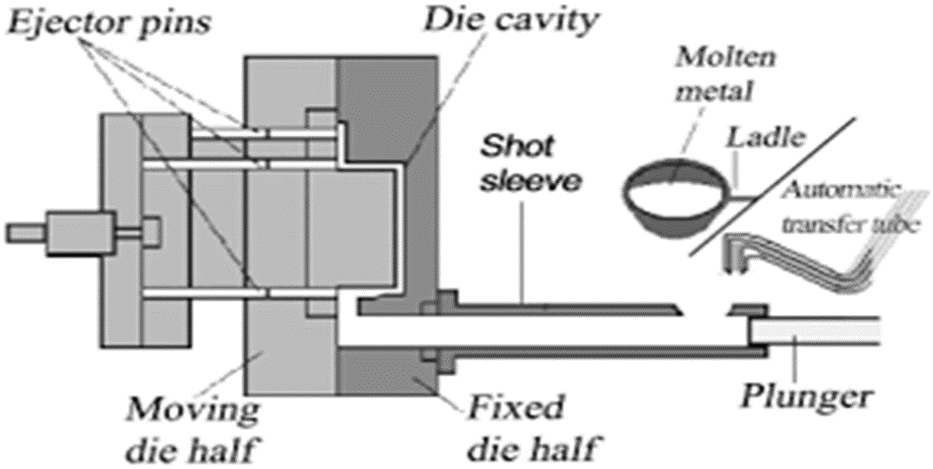
1. Dies (Molds)
The most critical tool in the process is the die, also called the mold. It consists of two halves:
• The cover die; stays stationary and aligned to the injection system.
• If it is an ejector Die, it moves to release the solidified casting. Hardened steel is used to make dies to withstand extreme pressures and high temperatures. They set what dimensions they will build, the complexity the final product will have and how precise it will be.
2. Cavity Inserts
The internal shape of the die is formed by cavity inserts to create the intricate ones. Because of this, these inserts are replaceable, facilitating changing the die for different components without having to fabricate a new tool.
3. Core Pins
To manufacture internal holes, slots, or intricate recesses, an internal feature is created with a core pin. To get the finished product or product of the finest quality possible, they are necessary.
4. Ejector Pins
The completed casting is removed from the die cavity without damaging it by ejector pins. These pins are used for the ejection system, given for smooth and easy part removal.
5. Cooling Channels
The die includes cooling channels to allow for regulating the respective temperature during casting. Because uniform cooling avoids defects like warping, cracking, or shrinkage, it also provides for constant quality.
6. Vents and Overflow Wells
Trapped air is released from vents when molten metal is injected into the die and overflow wells are used to collect excess material. The final product is free of voids or air pockets, and both tools lend to that.
7. Trim Dies
Trim dies are specialized tools to remove excess material i.e. flash from castings. Clean edges and accurate dimensions for the final product are assured because they promise it.
8. Lubrication Systems
The die is lubricated with some aqueous lubricants to minimize wear, reduce friction, and also facilitate the removal of the part. Lubrication in its proper form improves die lifespan, prevents die shutoff and ensures smooth casting operations.
9. Shot Sleeves
Guides to the injection system are shot sleeves that guide the molten metal to the die cavity. The way they are designed to handle extreme heat and pressure means they work to smooth metal flow.
10. Sprayers
Release agents are coated in the die using sprayers to prevent the molten metal from sticking to the die and making part removal easier.
In order words, these tools work together to deliver consistent parts, high quality and without defects – indispensable for industries such as automotive, aerospace, electronics, etc.
Types of Die Cast Tooling
From die-cast tooling, there is nothing one size fits all. Depending on production requirements, various types of tooling are designed.
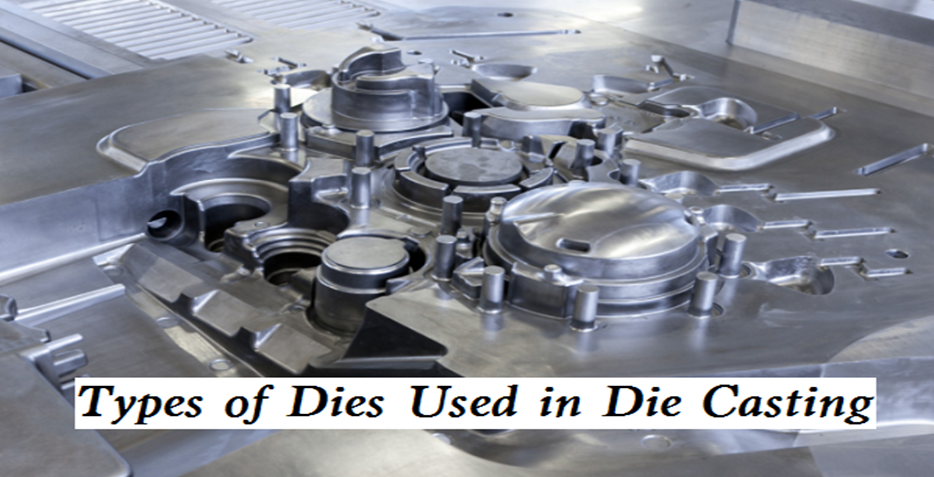
Single-Cavity Tooling: This type of tooling produces one part per cycle. A low-volume production or prototyping system will suit.
Multi-Cavity Tooling: Multi-cavity tooling enables the simultaneous production of multiple identical parts improving production efficiency. For high volume manufacturing it is very commonly used.
Family Tooling: The entire tooling method is innovative, it produces many different parts in one cycle. It is particularly appropriate when assembling components that are to be manufactured together.
Unit Die Tooling: Modular unit dies can substitute insert types or portions of the dies without redrawing the entire die. This reduces costs and downtime.
Trim Dies: They are used to get rid of excess material (flash) from the finished part, making sure that the finished part meets the exact specifications.
Benefits of Die-Cast Tooling

Nowadays, die-cast tooling is indispensable because of its many advantages:
Precision and Accuracy: High dimensional accuracy is achieved of course with die casting, part production with relatively tight tolerances, and intricate designs.
Langlebigkeit: These tools are from hard steel and are well capable of withstanding the rigours of high-pressure casting and increased use.
Effizienz: The process gives a quick, economical way to produce identical parts without much scrap and is thus economical for large-scale production.
Design Flexibility: With die-cast tooling, there are complex shapes, thin walls, and intricate details that are not possible under other manufacturing methods.
Material Savings: The tooling is unparalleled, enabling minimum waste and scrap, which is the making for a more sustainable manufacturing process.
Surface Finishing: Most commonly, die-cast parts have relatively smooth surfaces that need little or no post-processing and save time and time.
Challenges in Die Cast Tooling
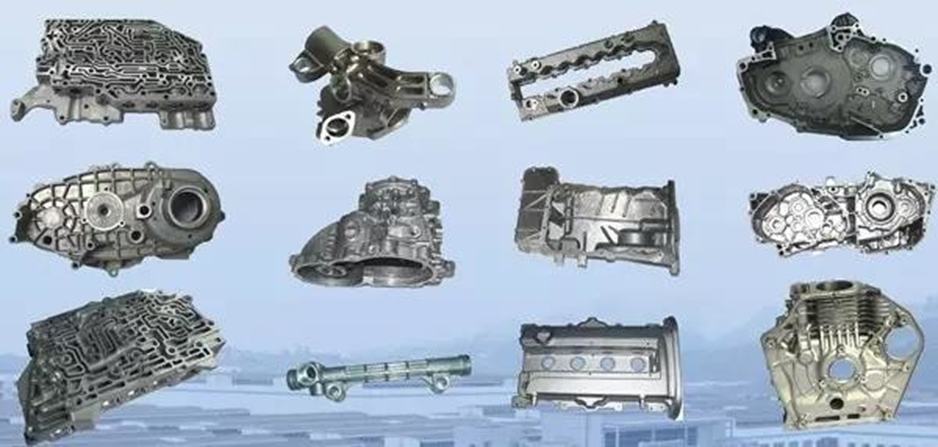
The challenges with die-cast tooling are many, although die-cast tooling does have advantages:
1. High Initial Costs
Die fabrication and design can be costly (although that may depend on the scale), and large capital investment is required for dies for small-scale manufacturers.
2. Maintenance Requirements
Maintenance for the tooling and to preserve the quality of the product is required regularly. Failing to maintain will bring about defects and delays in production.
3. Design Limitations
Emergency design is important, even critical, in some cases. Extremely intricate designs also may require advanced techniques or multi-step processes, which increase the complexity of the production costs.
4. Thermal Fatigue
Repeated high temperatures can wear out the die and worn out die will develop cracks or deformed over time.
Factors to Consider in Die Cast Tooling Design
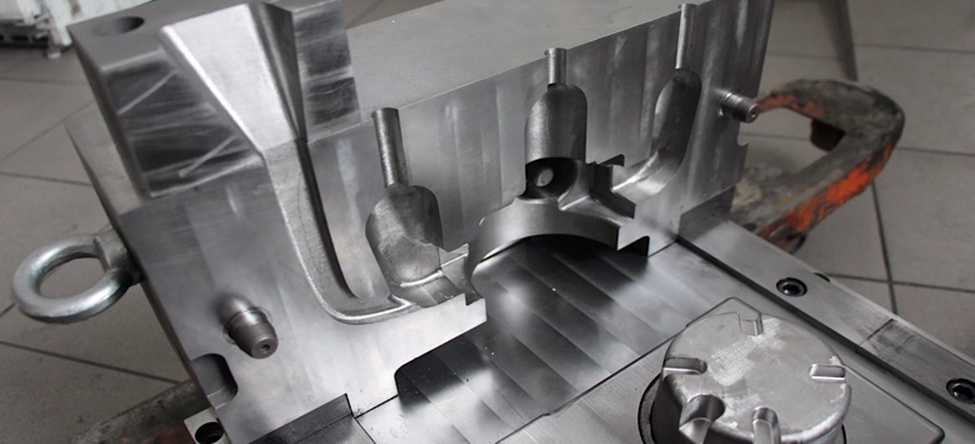
The following is specific in providing detailed planning and consideration of factors involved in the creation of efficient and reliable die-cast tooling.
1. Material Selection
Tooling design is based on the choice of metal. Commonly used are aluminium, zinc, and magnesium with properties of lightweight, strength, and corrosion resistance.
2. Thermal Management
On the other hand, proper cooling systems are necessary to prevent overheating which could lead to defects in the casting.
3. Tool Longevity
Choosing better quality materials in creating the die will lengthen its life and reduce the frequency of replacement.
4. Cost Efficiency
The initial tooling costs are high, but are, however, very low on a per unit basis for large-volume productions.
5. Product Complexity
The more complex the part design, the more intricate the tooling. A second impact can be on lead time and cost.
Applications of Die Cast Tooling
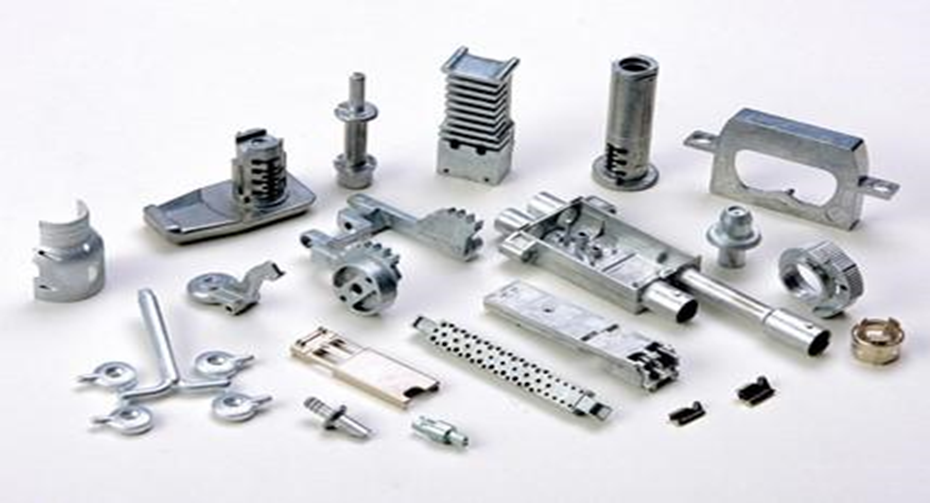
However, die-cast tooling is a critical practice for the production of complex and high-quality metal parts in many industries. It is indispensable for a wide variety of applications because of its capability to produce durable, lightweight and precise parts. Some of the main industries that make use extensively of die-cast tooling are these:
1. Automotive
In the automotive sector, the die-cast tooling is very important. Die-cast components such as engine blocks, transmission cases, brackets, steering components etc. are used which have to be cast to very tight standards of precision, toughness and strength. Of course, the process is also useful for producing lightweight parts important to further fuel efficiency in modern vehicles.
2. Consumer Electronics
In electronics manufacturing, die casting is widely used for producing the frames for smartphones, the casings of laptops, the connectors as well as heat sinks. The process’s capability of making intricate designs as the parts are also lightweight and strong also benefits these parts.
3. Aerospace
Applications for die-cast tooling exist in aerospace where components, such as housings, brackets and structural parts are used to make lightweight but robust components. For this modern industry, these components must meet stringent performance and safety requirements, and this is where die casting gives what it needs.
4. Industrial Equipment
Delivering Die die-cast pumps, Gears, Valves and Housing for Industrial Machine Parts. Die casting guarantees that such components meet stringent operational standards.
5. Medical Devices
In the medical field die castings are very important for making reliable and precise parts for devices like imaging devices, diagnostic tools and surgical tools. It is of the utmost importance that these devices can be manufactured to have tight tolerances because they are so important to the safety and effectiveness of the part itself.
6. Renewable Energy
As renewable energy expands, die-cast tooling becomes a method of creating components for wind turbines, solar panel mounts or electric vehicles to achieve both durability and efficiency.
Die-cast tooling supports innovation and production in several different sectors, as shown in these applications.
Innovations in Die Cast Tooling
Technology advancements are transforming die cast tooling: the process is becoming more of what’s possible, efficient and precise. This has been transforming the industry by cutting down on waste, improving quality and extending tooling’s lifespan. SOME OF THE NOTABLE ADVANCEMENTS HAVE BEEN WRITTEN BELOW:
Additive Fertigung: Die-cast tooling has a lot to do due to additive manufacturing, or 3D printing. The directories are being used to build prototype tooling which manufacturers use to test and refine designs quickly and at a low cost. It accelerates the development cycle and reduces the risk of errors that happen in big production. 3D printing also makes it possible to fabricate such complex geometries that cannot be made using traditional manufacturing techniques.
Fortschrittliche Beschichtungen: Die-cast tools are being surface coated, e.g., Physical Vapor Deposition (PVD) and nitriding due to a need for improved wear resistance, thermal stability, and surface hardness in the die-cast products. The addition of these coatings helps protect the dies from harsh conditions of high-pressure casting, therefore, extending the lifetime of each die and reducing maintenance costs. The coatings also improve the final product quality by reducing friction and preventing molten metal from sticking to the die.
Simulationssoftware: Engineers are using advanced simulation tools to optimally design die before any production ever starts. The result is these tools which simulate the flow of the molten metal, cooling rates, and possible defects so that manufacturers can find and fix defects before they occur during the design phase. It accomplishes this: Trial-and-error is being reduced, lead times shortened, and success in production is, in fact, higher.
Automatisierte Systeme: The die-casting process is undergoing a change brought about by automation and improved efficiency and consistency. As molten metal is injected, parts are handled, and finished components are inspected, robotic systems are being used. Automated systems eliminate human error, provide faster production speed and produce all batches with uniform quality.
Smart Monitoring and IoT Integration: Integration of Internet of Things (IoT) technology will give the real-time monitoring of die-cast tooling. Temperature, pressure and wear sensors embedded in the tools feed the data into predictive maintenance and increase the overall efficiency of the maintenance.
They are helping the die-casting industry increasingly become more precise, sustainable, and flexible, an industry that continues to be one that cannot be ignored for long.
Future Trends in Die Cast Tooling

Die-cast tooling is changing to meet the demands of new lighter, stronger, and more sustainable products as industries become more competitive. Some future trends include:
1. Sustainability Focus
The adoption of eco-friendly practices is encouraged through efforts to reduce waste and reduce energy consumption in die-casting.
2. Lightweight Materials
Magnesium as well as other lightweight alloys are being more and more used in the automotive and aerospace industries.
3. Digital Twin Technology
Real-time monitoring and predictive maintenance can be achieved through digital twins of tooling systems, and a further increase in tooling systems’ efficiency and decrease in downtime.
Schlussfolgerung
In the modern manufacturing environment, die-cast tooling is an imperative part that is used for the production of high-quality metal parts with accuracy and consistency. But it is a very complex chain of things using molds, cavity inserts, core pins and ejection systems all combining to produce parts with very tight tolerances and complex geometries. It is widely used in automotive, aerospace and electronics industries because it enables the production of durable and lightweight components. Matures, high-quality die-cast tooling made out of previously mentioned hardened steel material means you can get good long-lasting performance under extreme temperatures, and pressures. Tools of replaceable inserts, advanced cooling systems, PVD coatings, as well as innovations that bring about the above have improved tooling efficiency while minimizing waste and increasing their durability. While it does require a large initial investment in tooling, it enables faster production cycles, fewer defects and lower cost of manufacturing in high volume.
While die-cast tooling is not for the faint of heart, it is still an integral part of precision manufacturing, having maintenance and high costs associated with it. Thanks to the increasing presence of technology, the 3D printed prototypes and digital twin systems will certainly make the process even more efficient and flexible. In a nutshell, die-cast tooling is critical to building durable, elaborate components to keep the industries in stride with current manufacturing requirements with accuracy and speed.
FAQs: About Die Cast Tooling
1. What is die-cast tooling?
The die-casting process includes specialized tools that are called dies, the mold (dies) , and various cavity inserts, core pins, and ejection systems to shape the molten metal into the desired components; die-cast tooling is referred to as these specialized tools. They are a crucial part of making high-quality, consistent results in manufacturing.
2. What steels are used in die-casting tooling?
Since die-cast tooling runs through such high pressures and extreme temperatures, the die-cast tooling is usually made from hardened steel, such as H13 tool steel, 8407, H13, DIN 1.2344 etc. Generally, PVD and nitriding are added to surface coatings to increase durability and wear resistance.
3. What is the die-cast tooling cost?
Tooling cost depends upon several design aspects, die size, and material used. The cost per part is dramatically lower, but the initial investment is high in the first instance of manufacture (for example, thousands to tens of thousands of dollars).
4. How long does die-cast tooling have in its lifespan?
Die-cast tooling lifespan is greatly dictated by factors such as die-cast material, maintenance procedures and the casting process. Tooling of high quality made from hardened steel will withstand hundreds of thousands of cycles if it’s cared for and maintained properly.