
Zinkdruckguss ist ein beliebtes und effektives Fertigungsverfahren, das zur Herstellung hochwertiger Präzisionsteile für verschiedene Branchen eingesetzt wird. Kundenspezifischer Zinkdruckguss hat sich zu einem unschätzbaren Faktor für Fertigungsunternehmen entwickelt, die besondere Anforderungen an das Design erfüllen wollen. Die Anwendung von Zinkdruckguss in der Automobilindustrie, Elektronikgehäuse, Steifigkeit, kundenspezifische Extremität Leichtigkeit, Standard der höchsten, und viele andere Anwendungen gezeigt wird.
Zamak 2, Zamak 3, Zamak 5 und ZA 8 sind häufig verwendete Zinkdruckgusslegierungen, die aufgrund ihrer mechanischen und thermischen Anforderungen ausgewählt werden. Zamak 2 enthält ca. 4 % Aluminium, ca. 3 % Kupfer und etwas Magnesium, was ihm eine hohe Festigkeit und Härte mit einer Zugfestigkeit von fast 330 MPa verleiht. Zamak 3 wird bei weitem am häufigsten verwendet und ist praktisch kupferfrei (etwa 4 % Aluminium und ein ähnlicher Magnesiumgehalt) und daher hart und leicht zu gießen mit einer Zugfestigkeit von etwa 280 MPa. Eine 1% kupferhaltige Zinkbasislegierung, die die Festigkeit und Härte etwas verbessert und eine Zugfestigkeit von bis zu 310 MPa erreicht, ist als Zamak 5 bekannt, das sich gut gießen lässt. ZA-8 ist eine Legierung aus 8,5% Aluminium und etwa 1% Kupfer mit einer Zugfestigkeit von fast 390 MPa und guter Verschleißfestigkeit und Leistung unter erhöhten Temperaturbedingungen.
Benutzerdefiniert ZinkdruckgussIn diesem Artikel werden der Prozess als solcher und die Nutzung von Chinas kundenspezifischen Zinklegierungsdruckguss-Dienstleistungen untersucht.
Was ist Zinkdruckguss?

Zinkdruckguss ist ein Verfahren, bei dem geschmolzenes Zink unter hohem Druck in eine Stahlform gespritzt wird. Wenn das Metall erstarrt, nimmt es die Form der Gussform an und bildet ein besonderes und dauerhaftes Teil. Im Vergleich zu anderen Metallen verfügt Zink über eine hohe Fließfähigkeit, eine ausgezeichnete Festigkeit und die Fähigkeit, Druckgussteile mit feinen Details zu gießen.
Seine Festigkeit macht Zink unter dem Gesichtspunkt der Leistung zu einer attraktiven Option, aber es ist auch ein relativ kostengünstiges Material und eine attraktive Option für Unternehmen, die ein Gleichgewicht zwischen Leistung und Produktionskosten anstreben. Dies gilt insbesondere für jede Art von kundenspezifischem Zinkdruckguss, da dieses Verfahren es Unternehmen ermöglicht, maßgeschneiderte Komponenten für ihre individuellen Bedürfnisse zu entwerfen.
Vorteile des individuellen Zinkdruckgusses
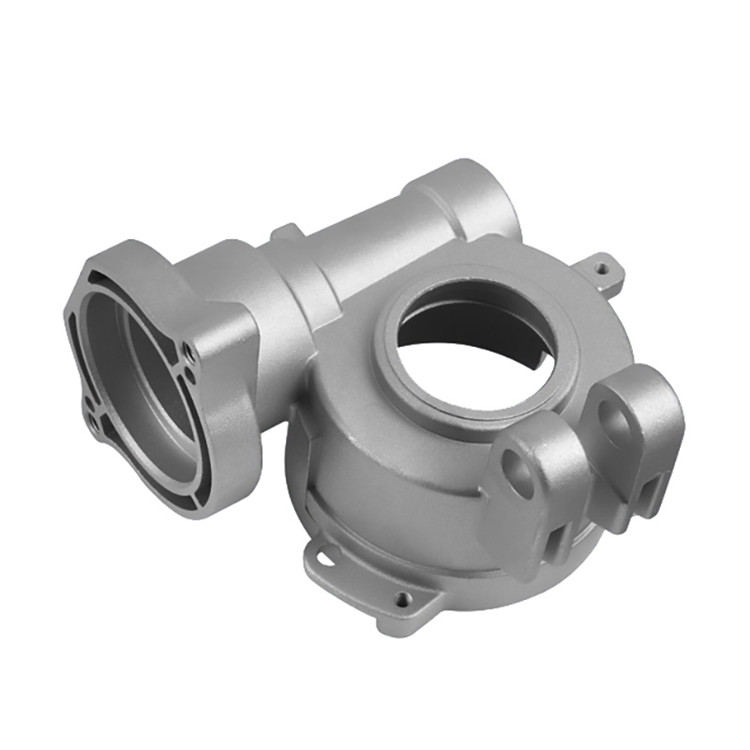
1. Präzision und Genauigkeit
Einer der wichtigsten Vorteile des Zinkdruckgusses ist die Möglichkeit, hochpräzise Teile herzustellen. Dieses Druckgussverfahren stellt sicher, dass die Abmessungen und die Oberflächenbeschaffenheit der Bauteile auch bei komplexen Konstruktionen gleich bleiben. In den Bereichen Elektronik, Automobilbau und Luft- und Raumfahrt, wo es auf Toleranz und Passgenauigkeit ankommt, wird diese Präzision sehr wichtig.
Teile mit feinen Details, die mit anderen Mitteln nicht hergestellt werden können, und Teile mit komplizierten, detaillierten Geometrien können im Zinkdruckgussverfahren hergestellt werden. Während andere Fertigungsverfahren vielleicht in der Lage sind, einige Teile mit hohen Stückzahlen identischer Teile mit minimalen Abweichungen zu produzieren, ist der Druckguss wirklich der richtige Weg für Teile, die ein hohes Maß an Konsistenz erfordern.
2. Langlebigkeit und Stärke
Es ist ein robustes Metall, das sehr haltbar und korrosionsbeständig ist. Es eignet sich daher perfekt für die Herstellung von Teilen, die abrasiven Bedingungen ausgesetzt sind. Zinkdruckguss bietet die Möglichkeit, kundenspezifische Teile herzustellen, die für eine lange Nutzungsdauer ausgelegt sind.
Druckgussteile aus Zinklegierungen bieten ein hervorragendes Verhältnis zwischen Festigkeit und Gewicht, so dass die Produkte stark, aber nicht zu schwer sind. Wie in den meisten Branchen ist dies von entscheidender Bedeutung (insbesondere im Automobilbau), wo die Verringerung der Masse des Systems für die Leistung, die Kraftstoffeffizienz usw. entscheidend ist.
3. Kosten-Wirksamkeit
Für viele Unternehmen ist Kosteneffizienz ein sehr wichtiger Aspekt. Diese Herausforderung kann sehr gut mit dem Zinkdruckgussverfahren gelöst werden, da sich damit qualitativ hochwertige Teile zu relativ niedrigen Kosten herstellen lassen. Aufgrund der relativ niedrigen Materialkosten von Zink und der Effizienz des Druckgussverfahrens spricht wenig dagegen, dass Zink eine sehr kostengünstige Wahl für Hersteller ist.
Das Druckgussverfahren ist auch sehr präzise, so dass die Kosten für die Nachbearbeitung oder die Arbeit an einer zweiten Maschine reduziert werden können. Es ermöglicht auch ein hohes Maß an identischen Teilen Produktion in einem einzigen Produktionslauf und daher weiter reduziert Kosten, so dass es die perfekte Lösung für die Massenproduktion.
4. Flexibilität bei der Gestaltung
Der Hauptvorteil des Zinkdruckgusses mit kundenspezifischem Design liegt in der Flexibilität bei der Gestaltung. Dadurch können die Hersteller Teile mit komplexen Formen, dünnen Wänden und komplizierten Merkmalen herstellen, die sonst nicht realisierbar wären. Diese Flexibilität ermöglicht es den Unternehmen, verschiedene Teile zu erfinden und herzustellen, die bestimmte Funktionen und ein bestimmtes Aussehen bieten.
Darüber hinaus können Teile mit verschiedenen Oberflächenausführungen wie glatt und poliert bis hin zu strukturiert oder matt mit dieser kundenspezifischen Zinklegierung im Druckguss hergestellt werden. Die Vielseitigkeit des Designs macht den Zinkdruckguss für viele weitere Anwendungen als die Unterhaltungselektronik geeignet - Industriemaschinen, Fahrzeugteile usw.
5. Kurze Vorlaufzeiten
In der heutigen Hochgeschwindigkeits- und Großserienfertigung ist Zeit ein entscheidender Faktor. Kundenspezifischer Zinkdruckguss hilft Unternehmen, mit kurzen Produktionsvorlaufzeiten ins Schwarze zu treffen, da sie ihre Produkte schnell auf den Markt bringen können. Der Gießprozess ist ziemlich schnell, sobald die Formen hergestellt sind, so dass der gesamte Prozess ziemlich schnell abläuft und eine schnelle Produktion einer großen Anzahl von Teilen in einem minimalen Zeitrahmen ermöglicht.
Darüber hinaus ist es in Branchen nützlich, in denen die Markteinführungszeit entscheidend ist. Der richtige Einsatz von Zinkdruckguss hilft Unternehmen, Verzögerungen und Bestandsmängel zu vermeiden, und führt zu einer hohen Qualität der Teile.
Der Prozess des individuellen Zinkdruckgusses
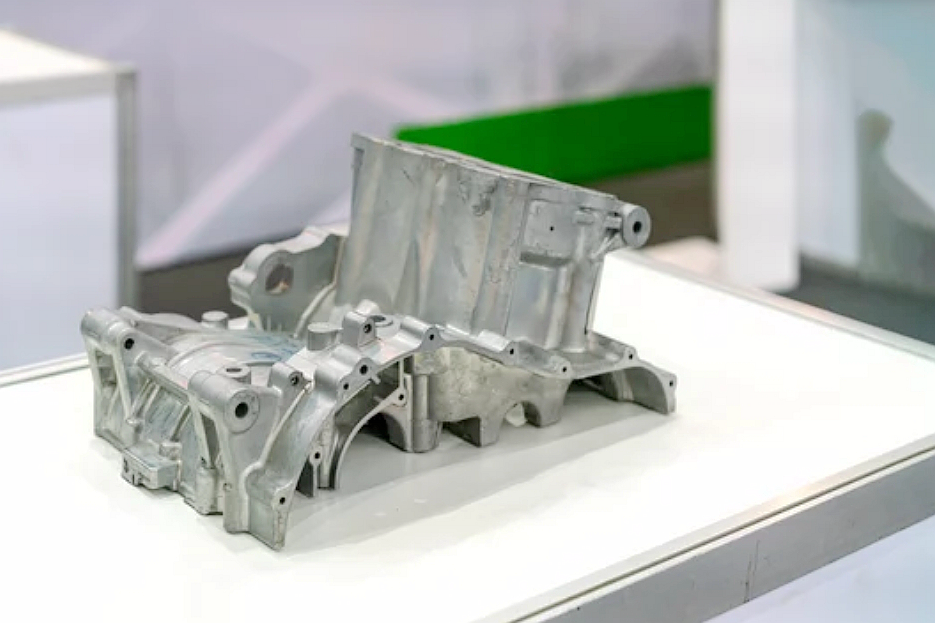
Dies ist der Fall beim kundenspezifischen Zinkdruckgussverfahren, bei dem viele wichtige Schritte durchgeführt werden müssen, um das zu erreichen, was erforderlich ist. Diese Schritte sind:
1. Entwurf und Erstellung von Formen
Bei der Herstellung einer Form wird zunächst die Form aus Stahl entworfen. Das herzustellende Teil wird in Form und Eigenschaften an das angepasst, was in der Form hergestellt werden soll, um die Form zu erstellen. In diesem Fall kann der Kunde festlegen, welche Art von Form er benötigt. Maßgeschneiderte Druckgussformen werden nach den individuellen Wünschen und Änderungen des Kunden entworfen.
2. Injektion von geschmolzenem Zink
Nachdem die Form vorbereitet wurde, wird das geschmolzene Zink unter hohem Druck in die Form gefüllt. Auf diese Weise sorgt der Druck dafür, dass jedes Detail der Form mit Zink gefüllt wird und ein präzises Teil entsteht. Es kühlt schnell ab und erstarrt in der Form der Gussform.
3. Auswurf und Nachbearbeitung
Sobald das Zink gefroren ist, wird das Teil aus der Form ausgestoßen. Das Druckgussverfahren ist jedoch noch nicht abgeschlossen. Das fertige Teil kann noch weiteren Nachbearbeitungsprozessen unterzogen werden, z. B. dem Beschneiden von überschüssigem Material oder dem Glätten rauer Kanten, und auch im Nachhinein erzeugt das Druckgussverfahren eine hochwertige Oberflächenbeschaffenheit des Teils.
4. Qualitätskontrolle
Die Teile werden dann in Qualitätskontrollen gründlich geprüft, um zu gewährleisten, dass die Teile die festgelegten Festigkeits-, Genauigkeits- und Leistungsstandards erfüllen. Dazu können Maßkontrollen, Sichtprüfungen und Belastungstests gehören.
Vergleichstabelle Zinklegierungen
Eigentum | Zamak 2 | Zamak 3 | Zamak 5 | ZA-8 | Superloy | AcuZink 5 |
Aluminium (%) | 3.8 - 4.3 | 3.8 - 4.3 | 3.8 - 4.3 | 8.2 - 8.8 | 3.5 - 4.0 | 3.5 - 4.3 |
Kupfer (%) | 2.7 - 3.3 | <0.03 | 0.7 - 1.1 | 0.9 - 1.3 | 2.2 - 2.7 | 0.5 - 1.2 |
Magnesium (%) | 0.035 - 0.06 | 0.035 - 0.06 | 0.035 - 0.06 | 0.02 - 0.035 | 0.02 - 0.05 | 0.02 - 0.05 |
Zugfestigkeit (MPa) | ~328 | ~283 | ~310 | ~386 | ~410 | ~410 |
Streckgrenze (MPa) | ~270 | ~210 | ~230 | ~315 | ~360 | ~370 |
Dehnung (%) | 3 | 7 | 6 | 1 | 2.5 | 3 |
Härte (Brinell) | 120 | 82 | 85 | 92 | 110 | 105 |
Gießbarkeit | Messe | Ausgezeichnet | Gut | Gut | Messe | Gut |
Korrosionsbeständigkeit | Mäßig | Gut | Besser als Zamak 3 | Gut | Hoch | Hoch |
Bemerkenswertes Merkmal | Hohe Festigkeit und Härte | Allzweck-Legierung | Verbesserte Festigkeit und Verschleiß | Leistung bei hohen Temperaturen | Ausgezeichnete Festigkeit und Verschleiß | Hohe Duktilität und Festigkeit |
Die Rolle von Chinas kundenspezifischen Zinklegierungsdruckgussdiensten
Chinas kundenspezifische Zinklegierungsdruckgussdienste haben sich in den letzten Jahren als ein führender Akteur im Fertigungskonglomerat etabliert. China verfügt über fortschrittliche Technologie, qualifizierte Arbeitskräfte und niedrige Produktionskosten für seine Druckgussindustrie. Daher nehmen viele Unternehmen die Dienste von Zinkdruckgießern aus China in Anspruch, um die Produktionskosten zu senken und gleichzeitig die hohe Qualität zu halten.
Chinesische Hersteller haben Geld in hochmoderne Druckgussanlagen investiert, um Präzisionsteile in großem Maßstab herzustellen. Darüber hinaus sind die Produktionsbasis und die Lieferkettennetze in China für Unternehmen, die Rohstoffe und Baumaterialien auf einer wettbewerbsfähigen Basis beschaffen, günstiger.
Zinklegierungsdruckguss mit chinesischen Herstellern bietet eine gute Gelegenheit für Unternehmen, die qualitativ hochwertigen kundenspezifischen Zinklegierungsdruckguss anbieten wollen. Als äußerst vorteilhafte Ressource für Unternehmen, die ihre Produktionsprozesse vereinfachen wollen, sind chinesische Druckgussdienste in der Lage, große Mengen von Teilen schnell und kostengünstig zu produzieren.
Materialien aus Zinkdruckguss.
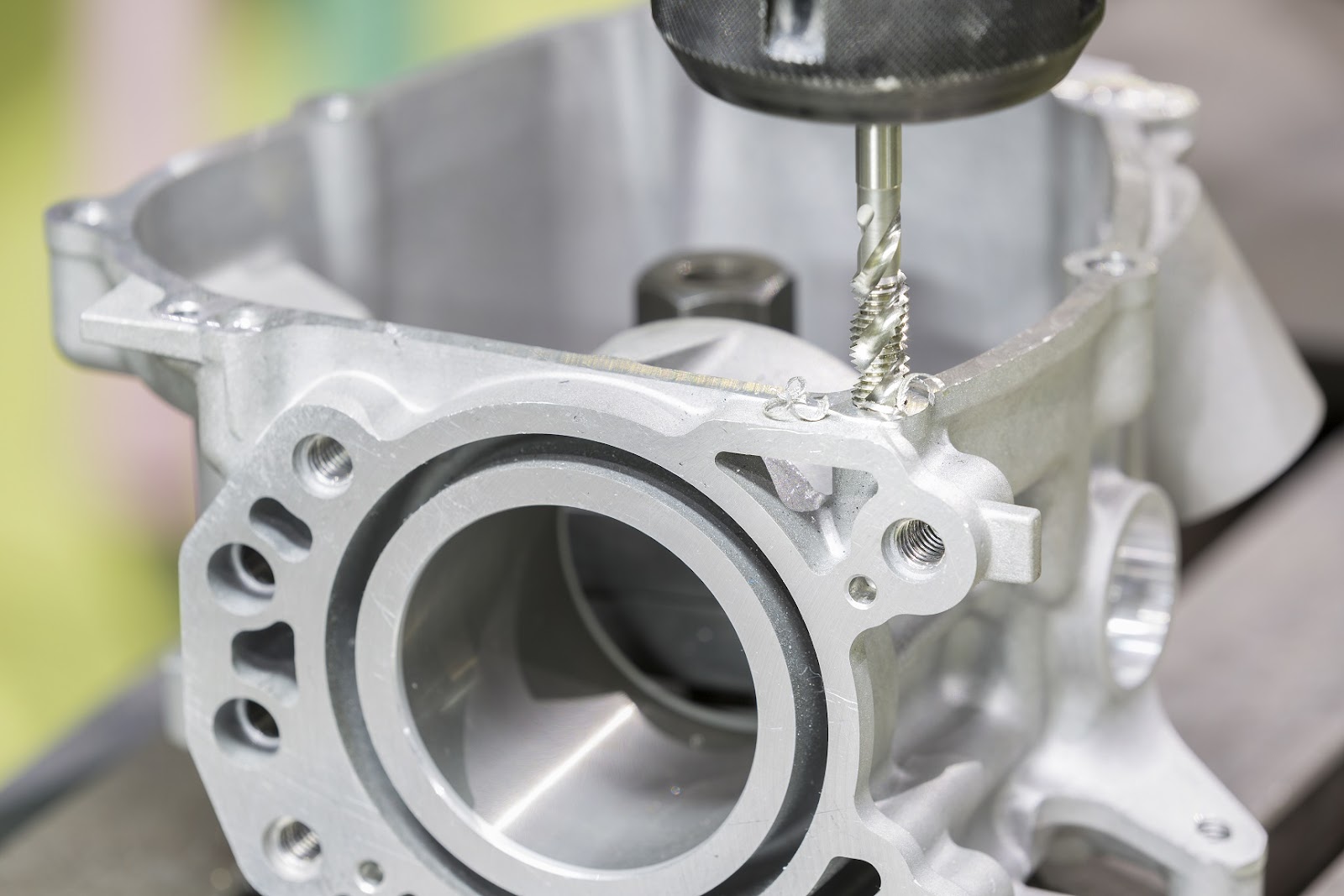
Zinkdruckguss ist ein attraktives Verfahren, das aufgrund seiner Vielseitigkeit, Langlebigkeit und Kosteneffizienz bei der Herstellung von Hochpräzisionsbauteilen eingesetzt wird. Der Werkstoff im Gießverfahren ist eines der Schlüsselelemente, die zum Erfolg dieses Verfahrens beitragen. Der Zinkdruckguss verwendet Zinklegierungen als Hauptmaterialquelle für die Eigenschaften der Legierungen wie Festigkeit, Korrosionsbeständigkeit und Fließfähigkeit. Doch nun zu den wichtigsten Materialien, die beim Zinkdruckguss verwendet werden.
1. Zink (Zn)
Die Herstellung komplizierter, komplexer und detaillierter Teile ist einer der Hauptgründe für die Verwendung von Zink als Ausgangsmaterial für das Druckgussverfahren, da Zink beim Schmelzen ein ausgezeichnetes Fließverhalten aufweist und komplizierte Formen füllen kann. Ein Metall, das im Druckgussverfahren zu präzise geformten Teilen für verschiedene Industriezweige wie die Automobilindustrie, die Elektronik und die Konsumgüterindustrie verarbeitet werden kann.
- Die Eigenschaften von Zink machen es zu einem guten Werkstoff für den Druckguss.
- Hat eine gute Fließfähigkeit: Es kann leicht Formen füllen und ausfüllen, daher kann es für komplexe Formen verwendet werden.
- Angenehmer Schmelzpunkt: Zink schmilzt bei einer niedrigen Temperatur (ca. 419°C oder 786°F), so dass weniger Energie für den Gießprozess benötigt wird.
- Korrosionsbeständigkeit: Zink ist korrosionsbeständig und eignet sich daher hervorragend für Teile, die in rauen Umgebungen oder im Freien verwendet werden.
- Festigkeit: Die Festigkeit von Produkten aus Zink ist auch stark und haltbar, besonders wenn sie mit anderen Metallen kombiniert werden.
2. Zink-Legierungen
Für den Druckguss wird reines Zink verwendet; häufig werden jedoch auch Zinklegierungen eingesetzt, um bestimmte Eigenschaften zu verbessern. Die häufigsten Zinklegierungen, die für den Druckguss verwendet werden, sind folgende:
A. ZA-8 (Zink-Aluminium-Legierung)
Zinklegierung, etwa 92% Zink und 8% Aluminium (ZA8), hat eine sehr hohe Sprengkraft und ist sehr effektiv beim Lochen und Spannen von Metallteilen. Sie zeichnet sich durch bessere mechanische Eigenschaften und gute Gießeigenschaften aus. ZA-8 hat eine hohe Festigkeit und Härte sowie eine gute Korrosionsbeständigkeit. Teile aus ZA-8-Legierungen werden häufig in hochpräzisen Anwendungen eingesetzt, z. B. in Automobilen und elektrischen Komponenten.
B. ZA-12 (Zink-Aluminium-Legierung)
ZA-12 enthält etwa 88% Zink und 12% Aluminium. Es handelt sich um eine Legierung, die in höherem Maße als Zink eine höhere Festigkeit und Härte sowie eine bessere Dimensionsstabilität bei großen Gussstücken aufweist. Diese Legierung wird unter anderem für Hochleistungsanwendungen wie Industriemaschinen, Unterhaltungselektronik und Hardware verwendet.
C. ZAMAK-Legierungen (Zink-Aluminium-Magnesium)
ZAMAK Legierungen sind Zink-Basis-Legierungen, die aus verschiedenen Aluminium-, Magnesium- und Kupferlegierungen bestehen. Die Legierung wurde ZAMAK genannt, weil sie sich aus Zink, Aluminium, Magnesium und Kupfer zusammensetzt. ZAMAK 3, ZAMAK 5 und ZAMAK 7 sind die am häufigsten verwendeten ZAMAK-Legierungen. Die Vorteile dieser Legierungen sind wie folgt.
ZAMAK 3 - stark, hart und formstabil - sind eine der am häufigsten verwendeten Zinkdruckgusslegierungen. Sie eignet sich am besten für die Herstellung von Automobilteilen, elektrischen Bauteilen und so weiter.
ZAMAK 5: Die Korrosionsbeständigkeit ist etwas besser als die von ZAMAK 3, aber der Guss ist etwas schlechter; diese Legierung ist eine bessere Wahl für raue Umgebungen, wie z.B. für Schiffs- oder Außenbauteile.
ZAMAK 7: Aufgrund seiner verbesserten Korrosionsbeständigkeit wird ZAMAK 7 vor allem im Druckguss für Teile mit hohen Anforderungen an die Detailtreue und die Oberflächengüte eingesetzt.
D. ZL-2 (Zink-Kupfer-Legierung)
Eine Zink-Kupfer-Legierung mit der Bezeichnung ZL-2 besteht überwiegend aus Zink und Kupfer. Sie bietet einen guten Kompromiss zwischen Festigkeit, Verschleißfestigkeit und Korrosionsbeständigkeit. ZL 2 wird zur Herstellung von Teilen verwendet, die großen Belastungen standhalten müssen, z. B. Maschinenteile und einige Automobilteile.
3. Kupfer (Cu)
In Zinkdruckgussstücken wird in der Regel kein Kupfer als Primärmaterial verwendet, aber Kupfer wird Zinklegierungen zugesetzt, um deren Festigkeit und Wärmeleitfähigkeit zu verbessern. Kupfer in einer Menge von nur 0,25%, das dem Zink zugesetzt wird, verbessert die mechanischen Eigenschaften der Legierung.
Stärke: Zinklegierungen sind von Natur aus fest und werden durch den Zusatz von Kupfer verstärkt, insbesondere bei höheren Temperaturen.
Abnutzungsbeständigkeit: Die Verschleißfestigkeit der Legierung wird durch Kupfer erhöht.
Korrosionsbeständigkeit: Der Zusatz von Kupfer verbessert die Korrosionsbeständigkeit der Zinklegierung, insbesondere in rauen Umgebungen, wie z. B. im Meer.
4. Aluminium (Al)
- Ein weiteres häufiges Element in Zinklegierungen ist Aluminium, zum Beispiel in ZA-8- und ZAMAK-Legierungen. Durch die Beimischung von Aluminium zu Zink werden auch mehrere wichtige Eigenschaften verbessert.
- Festigkeit: Die Zugfestigkeit der Legierung wird durch das Vorhandensein von Aluminium erhöht, wodurch die Legierung für Schwerlastanwendungen geeignet ist.
- Maßhaltigkeit - die Gussteile verziehen sich nicht, da Aluminium die Werte der Maßhaltigkeit aufrechterhält.
- Korrosionsbeständigkeit: In Bezug auf die Korrosionsbeständigkeit verbessert Aluminium die Korrosionsbeständigkeit der Zinklegierung und macht sie widerstandsfähiger gegen die Auswirkungen von Feuchtigkeit oder anderen Umwelteinflüssen.
5. Magnesium (Mg)
ZAMAK-Legierungen enthalten auch Magnesium, um die Eigenschaften der Legierung etwas zu verbessern. Magnesium verbessert die folgenden Eigenschaften:
- Magnesium hat Vorteile in Bezug auf die Festigkeit: Es erhöht das Verhältnis von Festigkeit zu Gewicht der Legierung, weshalb es für leichte Teile empfohlen wird.
- Magnesiummetall trägt dazu bei, die Legierung duktil zu machen, so dass sie Spannungen und Verformungen standhalten kann, ohne zu brechen.
- Magnesium erhöht die Korrosionsbeständigkeit der Legierung, die bevorzugt in der Schifffahrt oder bei Außenanwendungen eingesetzt wird.
6. Sonstige Zusatzstoffe und Legierungselemente
Bestimmte kleinere Mengen anderer Metalle und Elemente können je nach den Anforderungen der Anwendung in einigen Zinkdruckgusslegierungen enthalten sein. Einige dieser Elemente sind:
- Blei (Pb): Manchmal in Zinklegierungen enthalten, um die Bearbeitbarkeit zu verbessern.
- Zinn (Sn): Der Zusatz verbessert die Korrosionsbeständigkeit der Legierung und erhöht ihre Festigkeit bei hohen Temperaturen.
- Geringe Mengen Eisen können zur Verbesserung der Festigkeit, Härte und Verschleißfestigkeit zugesetzt werden.
Warum Zinklegierungen für den Druckguss bevorzugt werden
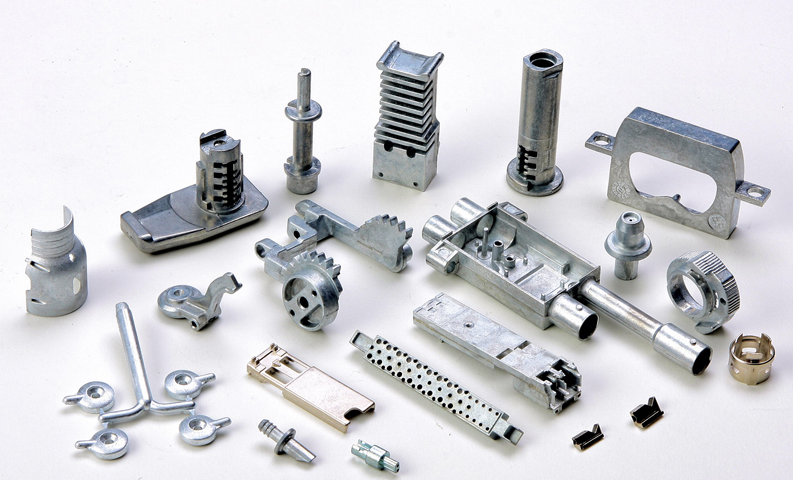
Ein Werkstoff wird hergestellt, wenn die Kombination von Zink mit anderen Legierungselementen zu einer detaillierten Kontrolle all dieser Eigenschaften führt:
- Ausgezeichnete Fließfähigkeit beim Schmelzen: Zinklegierungen haben eine hohe Fließfähigkeit beim Gießen, und das geschmolzene Metall fließt leicht in die komplexen Formhohlräume. Daher lassen sich Teile mit feinen Details und glatten Oberflächen herstellen.
- Zinklegierungen vereinen hohe Festigkeit und Härte mit hervorragender Schlagzähigkeit und eignen sich besonders für die Verwendung in Automobilteilen und neuerdings auch in der Unterhaltungselektronik.
- Es ist kostengünstig, da Zinklegierungen im Allgemeinen billiger sind als andere Metalle, und das Druckgussverfahren selbst macht es sehr effizient.
- Zink und seine Legierungen sind von Natur aus korrosionsbeständig; sie eignen sich daher für Teile, die den Elementen ausgesetzt sind.
Alternativen zum Zinkdruckguss
Aluminiumdruckguss ist ein Verfahren zur Herstellung von Präzisionsbauteilen, das die Herstellung komplexer Teile ermöglicht, wobei nur wenige Fehler auftreten können. Dies ist jedoch nicht die einzige Lösung, und je nach den Anforderungen eines bestimmten Projekts in Bezug auf Gewicht, Festigkeit, Kosten oder Umweltfaktoren stehen auch andere Optionen zur Verfügung. Jede der beschriebenen Methoden ist bis zu einem gewissen Grad nützlich, und einige von ihnen können in einem bestimmten Kontext weniger effektiv sein als andere, daher ist es äußerst wichtig, die Optionen abzuwägen.
1. Aluminium-Druckguss
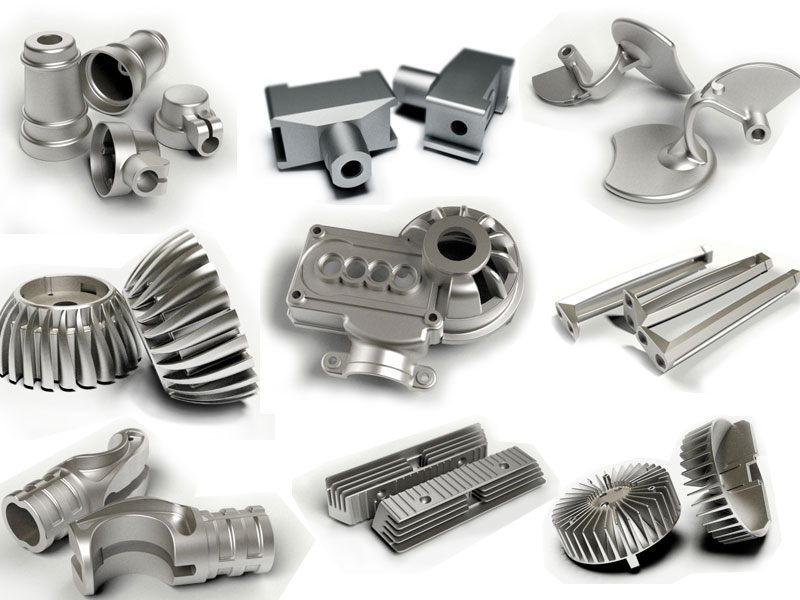
Aluminiumdruckguss gehört zu den Materialien, die bei der Herstellung als Ersatz für Zink verwendet werden. Die Beschaffenheit dieses rostfreien Stahls verleiht ihm eine hohe Festigkeit und ein geringes Gewicht, was seine umfangreiche Verwendung in der Automobilindustrie und im Flugzeugbau gewährleistet. Aluminiumteile sind relativ leicht, besitzen aber eine hohe Festigkeit und sind für den Einsatz bei hohen Temperaturen geeignet.
Außerdem ermöglicht das Verfahren die Herstellung von Teilen mit ausgezeichneten thermischen und elektrischen Leitungseigenschaften. Allerdings ist die Fließfähigkeit von Aluminium im Vergleich zu Zink relativ gering, was bei komplizierten, dünnwandigen Konstruktionen nachteilig ist. Außerdem sind die Werkzeug- und Gusskosten, die bei der Verwendung von Aluminium anfallen, bekanntermaßen etwas höher als die von Zink.
2. Magnesium-Druckguß
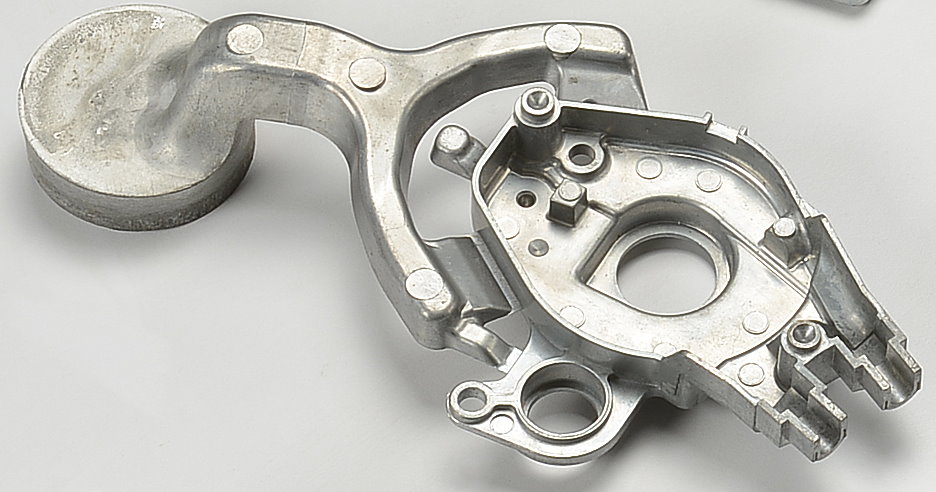
Magnesium ist das leichteste auf dem Markt erhältliche Konstruktionsmetall für Druckgusszwecke. Es eignet sich gut für Bereiche, in denen die Reduzierung des Produktgewichts von größter Bedeutung ist, z. B. in der Elektronik- und Automobilindustrie usw. Magnesium besitzt eine gute Festigkeit und Steifigkeit, und die Gussstücke aus diesem Werkstoff können sehr dünnwandig und komplex geformt sein.
Auf der anderen Seite ist es teurer als Zink, und seine Verwendung erfordert hohe Sicherheitsvorkehrungen, da geschmolzenes Magnesium leicht Feuer fängt. Es hat auch eine etwas geringere Korrosionsbeständigkeit als austenitische Stähle, was seine Verwendung in manchen Umgebungen ohne zusätzliche Beschichtung behindern kann.
3. Kunststoff-Spritzgießen
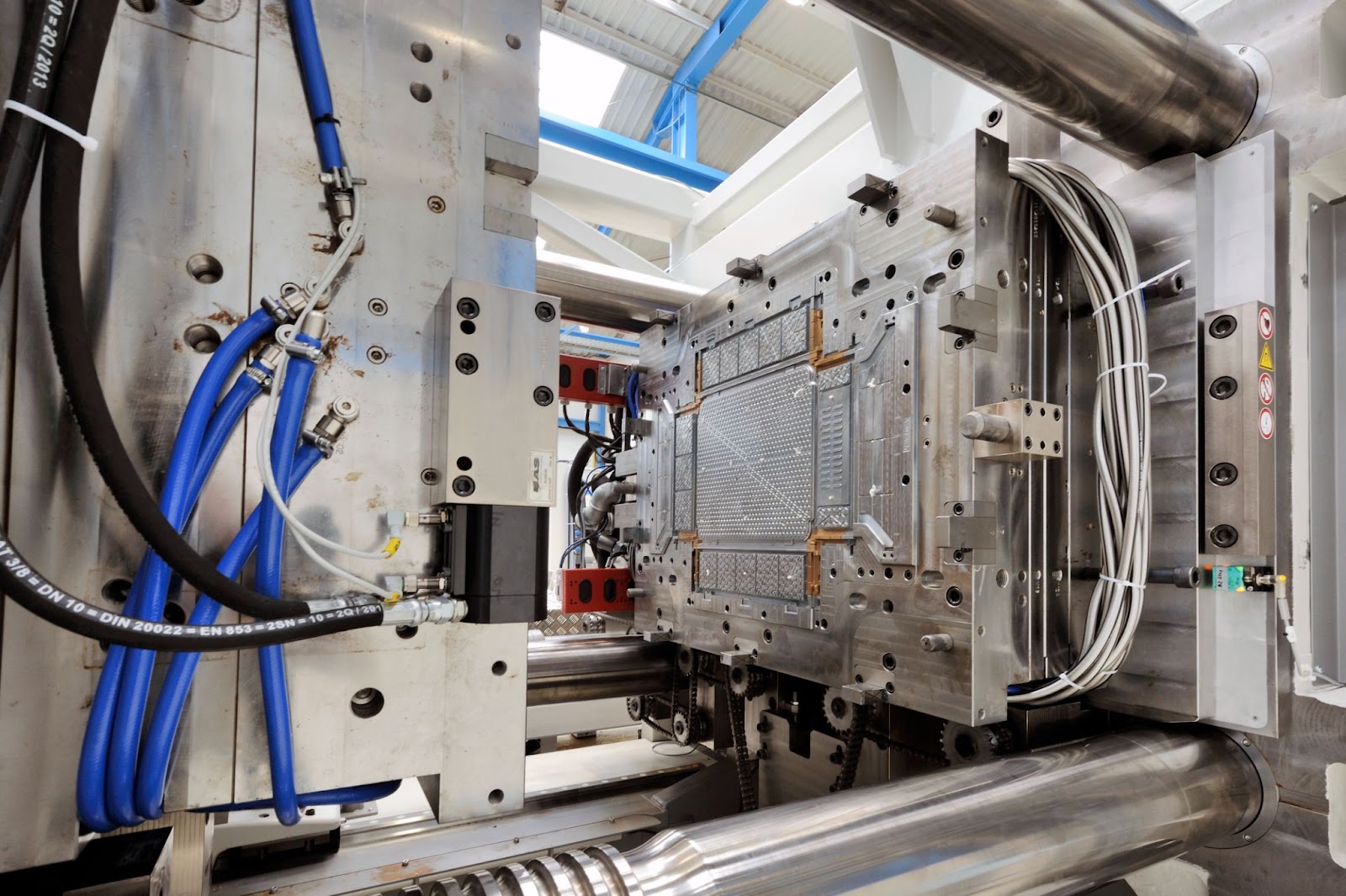
Einer der vorteilhaftesten technologischen Fortschritte bei nicht-strukturellen Komponenten ist das Kunststoffspritzgießen. Polypropylen findet breite Anwendung in Projekten wie Konsumgütern, medizinischen Geräten sowie in Elektrogehäusen.
Dank dieser Technologie erhielt man das Beste aus dem Farbspektrum, schlanke Produkte und schnelle Zykluszeiten. Allerdings sind sie nicht so stark wie Metalle und auch nicht so temperaturbeständig wie diese. Für Anwendungen, die haltbarer, hitzebeständiger oder belastbarer sein müssen, wäre Metallguss jedoch besser geeignet.
4. Stahl- oder Eisenguß
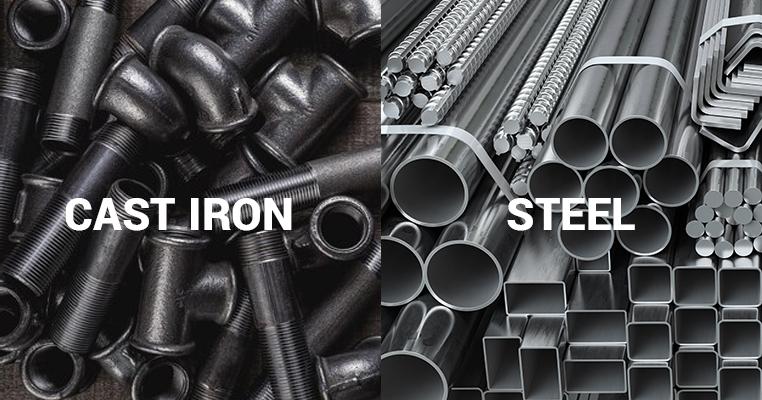
Wenn man bei extremer Festigkeit und Haltbarkeit keine Kompromisse eingehen will, dann sind Stahl- und Eisenguss die beste Wahl. Diese Materialien eignen sich für den Einsatz in Situationen, in denen sie starkem Verschleiß ausgesetzt sind, wie bei Maschinen, Werkzeugen oder Bauwerken.
Im Allgemeinen haben Stahl- und Eisengussteile eine hohe Belastbarkeit, Verschleißfestigkeit und Wärmebeständigkeit. Sie sind jedoch wesentlich dichter als Zink oder Aluminium, und aufgrund ihres höheren Schmelzpunkts ist das Gießen nicht nur energieaufwendig, sondern auch kostspielig. Aus diesem Grund sind sowohl die Bearbeitung als auch die Handhabung dieser Metalle im Vergleich zu den anderen Arten komplizierter.
5. 3D-Druck (Additive Fertigung von Metall)
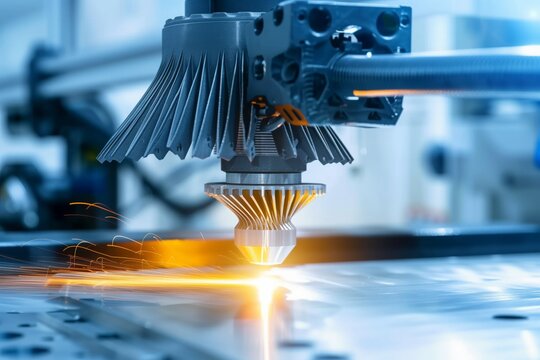
Die 3D-Metallverarbeitung, auch bekannt als Additive Fertigung, ist eine der neuen Fertigungstechnologien, die die Welt der Herstellung kleiner, aber komplexer Kleinteile umgestaltet. Sie ist heute eine große Chance für viele Branchen, in denen kundenspezifische Komponenten oder Prototypen benötigt werden, deren Herstellung durch Gießen teuer und zeitaufwändig wäre.
Es erfordert auch keine Formen zur Herstellung der Teile, ist also schnell und bietet Designvielfalt. Allerdings sind die Kosten pro Teil wesentlich höher, und im Allgemeinen hat die Technologie noch nicht ihre maximalen Fortschritte in Bezug auf die Bandbreite der verwendeten Materialien erreicht. Für die endgültigen Anpassungen in der Nachbearbeitung sind oft einige Änderungen erforderlich.
6. Feinguss
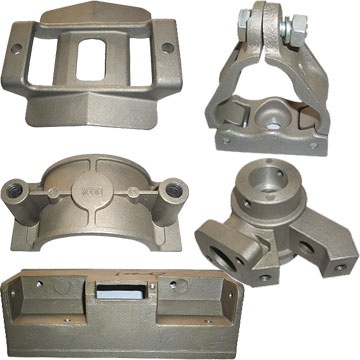
Feinguss oder Wachsausschmelzverfahren ist eine Technik, die zu einem präzisen Produkt und einer feinen Oberflächengüte führt. Es ist ideal für die Entwicklung komplexer Teile aus verschiedenen Metallen wie Edelstahl, Titan und Bronze.
Allerdings lassen sich damit Geometrien und sehr feine Details herstellen, was den Nachteil hat, dass es langsamer und kostspieliger ist als Druckguss. Es eignet sich am besten für die Produktion von Kleinserien, bei denen es auf Oberflächengüte und hohe Genauigkeit der Teile ankommt.
Die Wahl der richtigen Alternative
Bei der Auswahl des geeigneten Ersatzes für Zinkdruckguss sollten einige Faktoren wie Anwendung, Kosten, Materialeigenschaften und Kapazität berücksichtigt werden. Für kleine Teile kann es ratsam sein, Aluminium oder Magnesium zu verwenden. Bei einer großen Anzahl von Kunststoffteilen kann das Spritzgießen eine effektive Methode sein. Auch wenn die Festigkeit des Gussteils zum Schlüsselfaktor wird, kann die Verwendung von Stahl oder Feinguss sinnvoll sein.
Diese Kenntnisse ermöglichen es dem Hersteller, das am besten geeignete Verfahren im Hinblick auf Leistungsmerkmale, Kosten und einfache Herstellung auszuwählen.
Schlussfolgerung
Abschließend wird festgestellt, dass der Zinkdruckguss ein äußerst wertvolles Verfahren ist, das sich durch Präzision, Langlebigkeit, Kosteneffizienz und Designflexibilität auszeichnet. Mit diesem Verfahren können Unternehmen qualitativ hochwertige Komponenten entwickeln, ohne dass es zu Zollbeschränkungen kommt, wodurch die Produktionskosten niedrig gehalten werden. Chinas kundenspezifische Zinklegierungsdruckgussdienste tragen zu noch größeren Möglichkeiten für Unternehmen bei, die fortschrittliche Druckgusstechnologie nutzen möchten.
Kundenspezifischer Zinkdruckguss ist eine vielseitige und zuverlässige Lösung für die Herstellung von Teilen in der Automobil-, Elektronik- und Industriebranche, unabhängig davon, ob Sie ein Teil herstellen, das den höchsten Qualitätsstandards entspricht. Da sich die Technologie noch in der Entwicklung befindet, wird die Technik des Zinkdruckgusses nur noch weiter zunehmen, da sie in der modernen Fertigung von grundlegender Bedeutung sein wird.
Häufig gestellte Fragen (FAQs)
1. Der individuelle Zinkdruckguss wird erklärt und wie er funktioniert.
Zinkdruckguss ist ein Herstellungsverfahren, bei dem geschmolzene Zinklegierungen unter hohem Druck in den Formhohlraum eingespritzt werden, um hochpräzise, individuell gestaltete Zinkmetallteile herzustellen. Es wird häufig für die Herstellung komplexer Formen mit hoher Maßgenauigkeit und minimaler Bearbeitung verwendet.
2. Warum sollte ich Zinklegierungen für den Druckguss verwenden?
Einige Vorteile der Verwendung von Zinklegierungen sind ihre hohe Festigkeit, ihr niedriger Schmelzpunkt, die bessere Oberfläche und die Möglichkeit, dünnwandige, komplexe Teile herzustellen. Außerdem sind sie gut korrosionsbeständig und bei hohen Produktionsmengen sehr kostengünstig.
3. Zamak 3, ZA-8 oder AcuZinc 5: Welche Zinklegierung ist für mein Projekt am besten geeignet?
Die beste Legierung hängt von Ihrer Anwendung ab.
- Die Allzweckteile für Zamak 3 sind ideal.
- Für hochfeste und hitzebeständige Anwendungen ist ZA-8 besser geeignet.
- AcuZinc 5 ist das bevorzugte Material, wenn Duktilität und Zähigkeit erforderlich sind.
- Stimmen Sie die Legierung mit Ihrem Lieferanten auf Ihre spezifischen Bedürfnisse ab.
4. Ist es möglich, hochwertigen Zinkdruckguss aus China zu finden?
Ja. Viele chinesische Hersteller von kundenspezifischen Zinklegierungsdruckgussteilen verfügen über niedrige Preise, modernste Ausrüstung und qualifizierte technische Unterstützung. Sie sind gut für Prototypen und Massenproduktion von kundenspezifischen Teilen.
5. Welche Vorteile könnte der Zinkdruckguss haben?
Leichtbauanwendungen können mit Aluminium- oder Magnesiumdruckguss, Kunststoffspritzguss für nichtmetallische Teile, Stahlguss für hohe Festigkeit oder Feinguss für Präzisionsteile hergestellt werden. Die Wahl hängt von Design, Festigkeit, Budget und Produktionsvolumen ab.