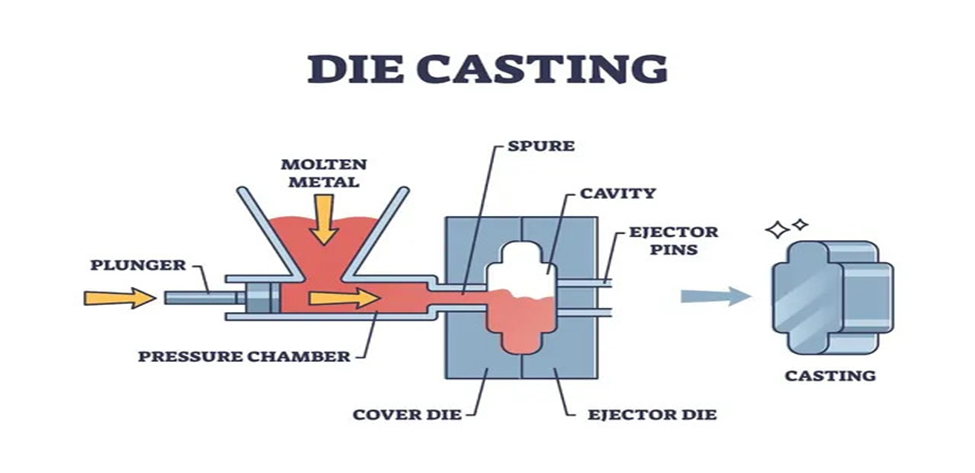
Dabei handelt es sich um ein Herstellungsverfahren, bei dem geschmolzenes Metall mit Druck in einen Formhohlraum gepresst wird, der auch als Druckguss bezeichnet wird. Die Form besteht in der Regel aus hochwertigem Stahl, so dass das Teil in großen Mengen hergestellt werden kann, der Begriff wird für die Herstellung vieler Teile verwendet. Das fertige Teil wird dann durch Öffnen der Form hergestellt, nachdem das geschmolzene Metall abgekühlt ist und eine feste Schicht bildet. Diese Art der Anwendung des Verfahrens wird meist bei der Herstellung komplizierter Metallteile eingesetzt, die eine hohe Maßgenauigkeit und polierte Oberflächen erfordern. Druckguss kann mit Aluminium, Zink und Magnesium durchgeführt werden, aber auch andere Metalle können je nach Anwendung und anderen Anforderungen für ein Gehäuse verwendet werden. Druckguss gilt als eine der besten Fertigungstechniken für die Massenproduktion von kleinen bis mittelgroßen Bauteilen aus Metall. Die Popularität des Verfahrens hat sich in der Automobilindustrie, der Luft- und Raumfahrt, der Elektronik und im Industriemaschinenbau verbreitet, da es in der Lage ist, langlebige, leichte und kompliziert zugeschnittene Teile herzustellen. Dieses Verfahren ist jedoch weithin für seine Fähigkeit bekannt, Produkte mit komplexer Geometrie herzustellen, die mit herkömmlichen Techniken nur sehr schwer zu fertigen wären.
Wie Druckguss funktioniert

Das Gießen ist der erste Teil des Druckgießverfahrens. Auf der einen Seite der Form befindet sich eine Hälfte, und zwar eine Hälfte mit einem bestimmten Design, damit die Form dem Endprodukt entspricht. Für die Formen, die in der Regel maßgeschneidert sind, werden Hohlräume und Kerne entworfen, damit das Teil so genau wie möglich nachgebildet werden kann.
1. Einspritzen von geschmolzenem Metall:
Dann wird das geschmolzene Metall unter hohem Druck in den Formhohlraum gespritzt, um die gewünschte Form zu erhalten. Das Metall wird in der Regel auf ein Grad über die Schmelztemperatur erhitzt, um es flüssig zu machen. Beim Druckguss kann der Druck, mit dem das geschmolzene Metall in die Form gepresst wird, mehrere tausend bis zehntausend psi (pounds per square inch) betragen, um sicherzustellen, dass das geschmolzene Metall in jedes Detail der Form gelangt.
2. Erstarrung:
Dies geschieht, wenn das Metall in den Gehäusehohlraum eingespritzt wird, wobei es abkühlt und das Metall aushärtet. Die Qualität des Gussteils hängt von der Abkühlungsgeschwindigkeit ab. Zusätzliche Versagensarten (Scherung, Steigen und Gleiten) kommen in diesem Fall ins Spiel und führen zu schnellerer Abkühlung, höherer Festigkeit und besserer Oberflächengüte, während eine langsamere Abkühlung zu mehr inneren Fehlern und schlechteren mechanischen Eigenschaften führen kann. Zur Unterstützung des Abkühlungsprozesses werden in der Regel in die Form eingebaute Wasserkühlsysteme verwendet.
3. Rauswurf:
Anschließend lässt man das Metall abkühlen und erstarren und kann dann die Form leicht aus dem größeren Gussteil entfernen und das Teil auswerfen. Die meiste Zeit wird dann für das Herausdrücken des Teils aus der Form mit Hilfe eines mechanischen Auswerfersystems verwendet. Dies hängt von der Komplexität des Teils ab, das weitere zusätzliche Schritte erfordert, nämlich das Beschneiden und Bearbeiten, um die endgültige Form und Abmessung zu erreichen.
4. Qualitätskontrolle:
Nach dem Auswerfen wird das Teil einer Qualitätskontrolle unterzogen. Sie kann eine Überprüfung der Abmessungen, eine Sichtprüfung und eine mechanische Prüfung umfassen, um zu bestätigen, dass das Teil den Anforderungen entspricht oder besser ist als diese. Theoretisch lassen sich beim Druckguss hohe Präzision und Wiederholbarkeit erreichen.
Arten des Druckgusses
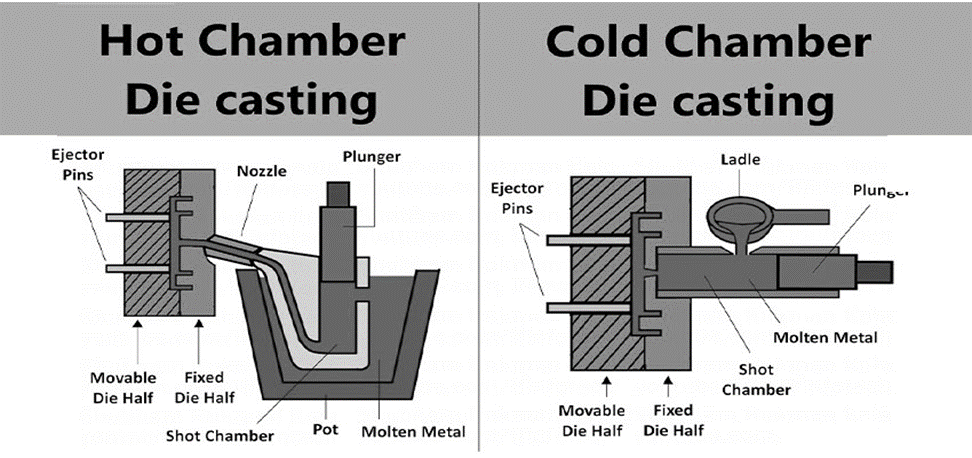
Es gibt zwei Arten von Druckguss, nämlich Warmkammer-Druckguss und Kaltkammer-Druckguss. Sie sind alle gut und haben ihre Vorteile, Einschränkungen und idealen Anwendungen.
1. Warmkammer-Druckguss
Das Verfahren, das sich am besten für Metalle wie Zink, Magnesium und Blei eignet, ist der Warmkammerdruckguss, da das Verfahren bei hohen Temperaturen und Schmelzpunkten durchgeführt wird. Das Einspritzsystem ist innerhalb des Schmelzofens installiert, so dass das Metall immer in Kontakt mit der Kammer ist.
Vorteile:
- Da die Metallschmelze in der Einspritzkammer zum Einspritzen in die Form vorbereitet ist, benötigt der Warmkammer-Druckguss weniger Zeit als der Kaltkammer-Druckguss.
- Einstufig: Es erfordert weniger Komponenten und weniger Zeit für die Einrichtung und gilt daher als wirtschaftlich, insbesondere bei hohen Stückzahlen.
- Für bestimmte Metalle: Der Warmkammer-Druckguss ist am besten geeignet, wenn die zu verwendenden Metalle niedrige Schmelztemperaturen haben, so dass die Metalle wenig oder gar nicht kontaminiert werden.
Benachteiligungen:
- Kann nicht für Metallarbeiten mit hohem Schmelzpunkt wie Aluminium und Messing verwendet werden, da die hohe Temperatur des Metalls die Kammer zum Schmelzen bringt.
- Alle Komponenten sind geschmolzenem Metall ausgesetzt, weshalb der Verschleiß im Laufe der Zeit hoch ist.
2. Kaltkammer-Druckguß
Metalle mit höherem Schmelzpunkt wie Aluminium, Messing und Kupfer werden im Kaltkammer-Druckgussverfahren gegossen. In diesem Fall wird das geschmolzene Metall aus einem zweiten Ofen abgezapft und in die Kaltkammer und dann in den Formhohlraum eingespritzt.
Vorteile:
- Was die Vielseitigkeit bei der Materialauswahl betrifft, so bietet der Kaltkammerdruckguss eine Vielseitigkeit bei der Materialverwendung, die den Einsatz von Materialien mit hohen Schmelzpunkten ermöglicht.
- Bessere Kontrolle der Metallqualität: Da der geschmolzene Metallzylinder separat in die Kammer gegossen wird, kann die Qualität des Metalls gut kontrolliert werden, um Verunreinigungen zu vermeiden.
- Erhöhte Werkzeugstandzeit: Da es während des gesamten Einspritzvorgangs nicht mehr mit dem Metall in Berührung kommt, erhöht sich die Lebensdauer des Werkzeugs.
Benachteiligungen:
- Langsamere Zykluszeit: Das manuelle Gießen des Metalls in die Kammer verlängert den Zyklus.
- Die Kosten sind höher, da es sich um ein zusätzliches Verfahren mit komplexerer Ausrüstung handelt.
Der Vergleich der Druckgussverfahren: Warmkammer vs. Kaltkammer
Hier ein Vergleich der gängigsten Arten von zwei Druckgussverfahren,
Merkmal | Warmkammer-Druckgießen | Kaltkammer-Druckgießen |
Metall-Kompatibilität | Am besten geeignet für Metalle mit niedrigem Schmelzpunkt (z. B. Zink, Blei) | Am besten für hochschmelzende Metalle (z. B. Aluminium, Messing) |
Zykluszeit | Schnellere Zykluszeiten | Langsamere Zykluszeiten |
Formverschleiß | Höherer Formenverschleiß durch direkten Kontakt mit geschmolzenem Metall | Geringerer Werkzeugverschleiß |
Kosten | Niedrigere Kosten für Großserienproduktion | Höhere Anfangskosten, aber besser für hochfeste Metalle |
Komplexität der Teile | Gut für einfachere Teile | Besser für komplexere, größere Teile |
Vorteile des Druckgusses
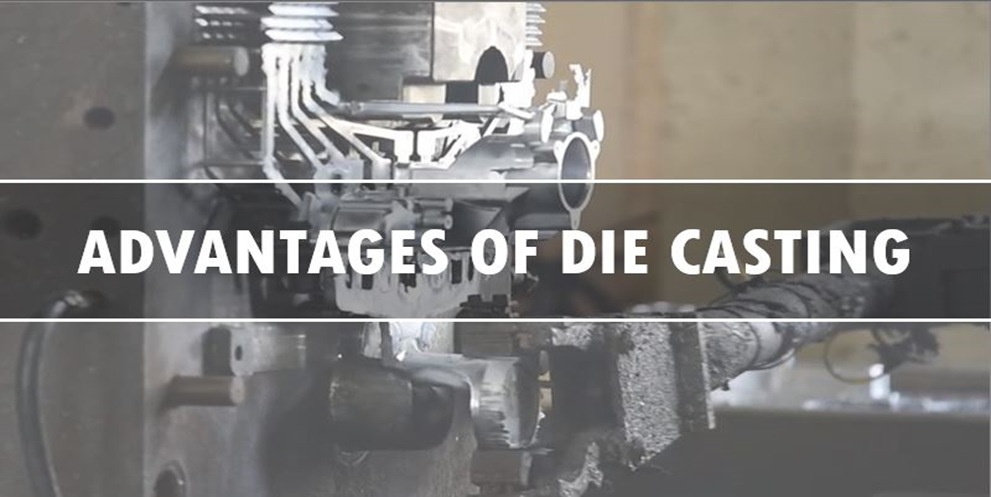
Es ist einer der größten Vorteile, dass das Druckgießen eine der bevorzugten Methoden für die Großserienproduktion von Produkten aus Metalllegierungen ist.
1. Hohe Präzision und Genauigkeit
Das Druckgießen hat viele Vorteile, denn es bietet eine hohe Präzision der Formen. Dieses Produktionsverfahren wird auch häufig für die Herstellung von Teilen verwendet, die eine gute Maßgenauigkeit erfordern, die sehr wichtig ist, da sie die für einen bestimmten Auftrag erforderlichen Toleranzwerte definiert. Es sei darauf hingewiesen, dass das Druckgussverfahren das einzige Herstellungsverfahren ist, mit dem Teile mit äußerst komplexen Geometrien hergestellt werden können.
2. Hohe Produktionsraten
In Bezug auf große Mengen ist Druckguss sehr effizient. Sobald die erste Form hergestellt ist, werden die Teile schnell und kostengünstig mit sehr geringem Arbeitsaufwand produziert. Die Nachfrage nach simulierten Pulvern ist besonders hoch in Branchen wie der Automobil- und Elektronikindustrie, wo große Mengen gleicher Teile benötigt werden.
3. Komplexe Konstruktionen und dünne Wände
Im Druckgussverfahren lassen sich komplexe Konstruktionen realisieren, die mit herkömmlichen Fertigungsmethoden nur schwer oder gar nicht möglich wären. Das Verfahren ermöglicht die Herstellung von Teilen mit dünnen Wänden und komplexen Innenstrukturen sowie Hinterschneidungen und eignet sich daher am besten für Anwendungen, bei denen der Platz begrenzt ist.
4. Materialeffizienz
Druckguss minimiert den Materialabfall. Der Druck, mit dem das geschmolzene Metall eingespritzt wird, füllt jeden Teil des Formhohlraums aus, so dass weniger Ausschuss anfällt. Außerdem können viele Druckgussteile recycelt werden, was zur Nachhaltigkeit des Prozesses beiträgt.
5. Ausgezeichnete Oberflächengüte
Die Oberflächenbeschaffenheit der im Druckgussverfahren hergestellten Teile ist glatt und ästhetisch. Es sind weniger Nachbearbeitungsprozesse wie Polieren oder Beschichten erforderlich, was Zeit und Kosten spart.
Was kann im Druckgussverfahren angewendet werden?
Nichteisenmetalle werden aufgrund ihrer guten Gießeigenschaften hauptsächlich im Druckguss verwendet. Aluminiumlegierungen sind die am häufigsten verwendeten Materialien, die im Druckgussverfahren verarbeitet werden, wie die folgenden Materialien zeigen.
1. Aluminium-Legierungen

Aufgrund seines geringen Gewichts, seiner Korrosionsbeständigkeit und seiner hervorragenden Wärme- und Elektrizitätsleitfähigkeit ist Aluminium der am häufigsten verwendete Werkstoff im Druckguss. Darüber hinaus werden spezielle Aluminiumlegierungen verwendet, wenn das Verhältnis von Festigkeit zu Gewicht eine Rolle spielt, insbesondere in der Automobil-, Luft- und Raumfahrt- und Elektroindustrie. Schließlich sind sie auch formstabil und eignen sich daher für die Herstellung hochpräziser Teile.
2. Zink-Legierungen
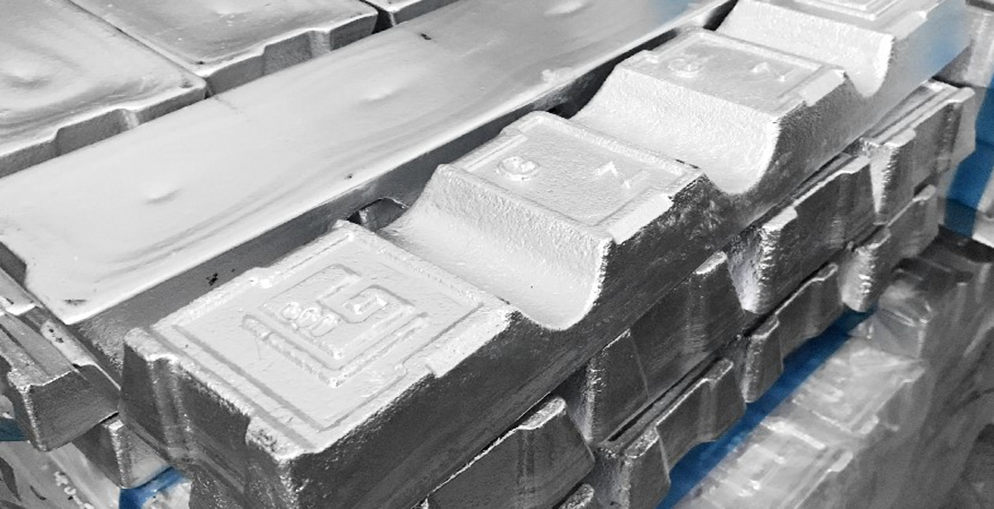
Zinkdruckgusslegierungen können aufgrund ihrer Eigenschaften wie niedriger Schmelzpunkt und hohe Fließfähigkeit bevorzugt werden, so dass komplizierte Konstruktionen mit dünnen Abschnitten und scharfen Details einfacher und effizienter hergestellt werden können. Solche Zinkteile verfügen über eine hohe Zähigkeit, sind korrosionsbeständig und weisen eine hochwertige Politur auf. Ein weiterer Anwendungsbereich von Zinklegierungen ist die Herstellung von Auto- und anderen Fahrzeugersatzteilen, Hardware und Elektronik.
3. Magnesium-Legierungen

Es ist erwähnenswert, dass Magnesium das leichteste Konstruktionsmetall ist und daher bei Teilen für Autos oder Flugzeuge ein erhebliches Gewicht aufweist. Dies liegt daran, dass Magnesiumlegierungen in Teilen verwendet werden, die stark, aber so leicht wie möglich sein müssen. Da das Metall jedoch sehr reaktionsfreudig ist, muss die Legierung während des Druckgussverfahrens gut kontrolliert werden.
4. Kupferlegierungen
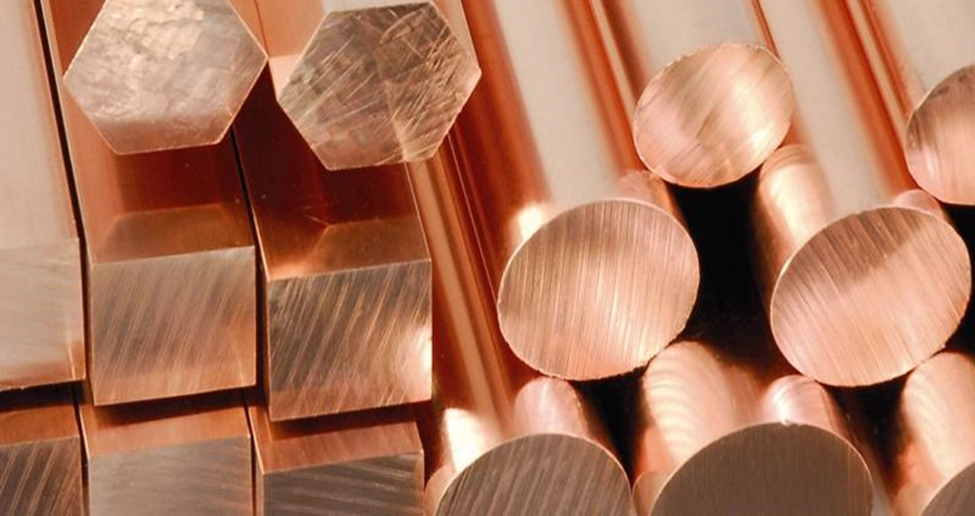
Neben Aluminium und Zink werden auch Kupferbasislegierungen, Messing und Bronze im Druckguss verwendet, allerdings nicht so häufig wie Aluminium und Zink. Sie bieten gute Festigkeitseigenschaften gegen Verschleiß und sind oft für Elektro- und Sanitäranwendungen nützlich.
Es ist sehr wichtig zu beachten, dass verschiedene Formen der Grundstoffe für verschiedene Anwendungen geeignet sind und die Kosten zwischen diesen Formen variieren und somit auch die Eigenschaften des Endprodukts.
Druckguss vs. andere Gussverfahren
Im Vergleich zu Gießverfahren wie Sandguss, Feinguss und Kokillenguss könnte dieser Abschnitt der Vergleichsteil des Druckgusses sein. Dabei ist es ratsam, die Stärken und Schwächen der einzelnen Verfahren hervorzuheben, um den Lesern zu zeigen, wann sie sich für das Druckgussverfahren gegenüber anderen Alternativen entscheiden sollten. Es könnte sich also um eine vergleichende Übersicht handeln, die bei der Bestimmung des optimalen Gießverfahrens je nach Material, Komplexität und Produktionsvolumen des Teils hilft.
Merkmal | Druckgießen | Sandgießen | Feinguss |
Präzision | Hohe Präzision mit engen Toleranzen | Geringere Präzision und grobe Oberflächengüte | Hohe Präzision und glatte Oberfläche |
Geschwindigkeit | Schneller für die Großserienproduktion | Langsamerer Produktionszyklus | Langsamer wegen der Formvorbereitung |
Materialabfall | Minimaler Abfall | Höherer Abfall durch rauere Oberfläche | Minimaler Abfall, aber komplexere Formen |
Kosten | Kostengünstig bei hohen Stückzahlen | Niedrigere Kosten für Kleinserienproduktion | Höhere Kosten aufgrund von Komplexität und Arbeitsaufwand |
Die Produktionsprozesse von Druckguss und Spritzguss werden verglichen.
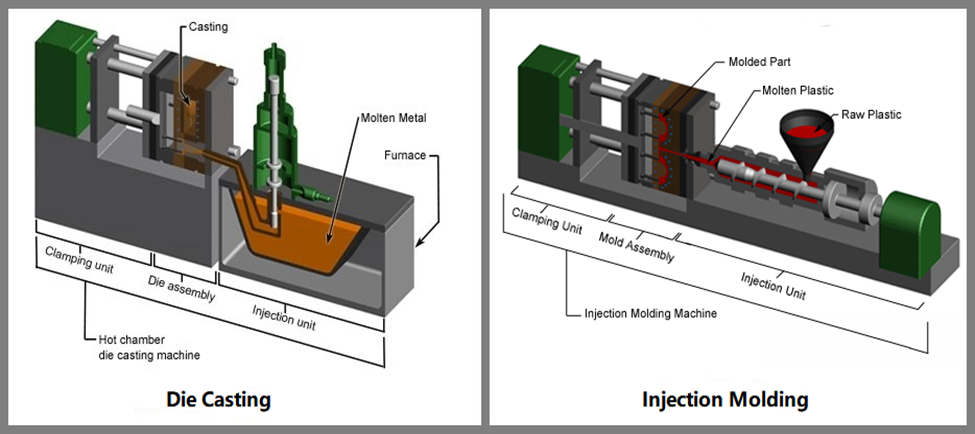
Druckguss und Spritzguss sind zwei gängige Verfahren zur Herstellung von Teilen mit feinen Details und komplizierten Formen. Obwohl beide Techniken die Verwendung von Material beinhalten, das Details formt, um Endprodukte herzustellen, gibt es Unterschiede in Bezug auf die Art des Materials, das geformte Produkt und insbesondere die Vorteile des jeweiligen Verfahrens.
1. Verwendete Materialien
Druckguss: Druckguss wird meist mit anderen Metallen als der Gruppe der Eisenmetalle bevorzugt, insbesondere mit Aluminium-, Zink-, Skill- und Kupferlegierungen. Die Metalle werden erhitzt und dann mit Hilfe von hydraulischem Druck in eine Form gegossen. Insofern ist das Druckgussverfahren die geeignetste Methode zur Herstellung von Teilen, die stark und haltbar sind und hohen Temperaturen standhalten können.
Spritzgießen: Das Spritzgießen wird in der Regel bei Kunststoffen angewendet und ist bei Metallen und Gläsern nur selten möglich. Zu den häufig verwendeten Polymeren gehören Polyethylen, Polypropylen und Polystyrol. Das Material, aus dem das Produkt hergestellt wird, ist leicht und flexibel, außerdem sind die Kosten niedrig und die Formen recht komplex, so dass sich das Spritzgießen perfekt für diese Art von Produkten eignet.
2. Prozessunterschiede
Druckgießen: Wie der Name schon sagt, wird das geschmolzene Metall mit hohem Druck in die Form gespritzt. Nach dem Abkühlen und Erstarren des Metalls bei sehr hoher Geschwindigkeit entstehen sie mit feiner Toleranz und guter Oberflächengüte, ohne dass weitere Arbeitsgänge erforderlich sind.
Spritzgießen: Da beim Spritzgießen geschmolzenes Kunststoffmaterial unter Druck in einen Formhohlraum eingespritzt wird, handelt es sich um ein Spritzgießen. Wenn die Temperatur des geschmolzenen Kunststoffs gesenkt wurde, öffnet sich die Form und das Produkt ist die Kunststoffform. Dennoch kann das Spritzgießen auch eine hohe Genauigkeit bieten, obwohl es im Vergleich zum Druckgießen häufig für die Herstellung relativ kleiner und leichterer Teile verwendet wird.
3. Anwendungen
Druckgießen: Druckguss eignet sich aufgrund seiner ausgezeichneten Hitzebeständigkeit für die Herstellung harter und starker Teile, die im Automobilbau, in der Luftfahrt und bei anderen elektronischen Produkten verwendet werden.
Spritzgießen: Kann für die Herstellung von Konsumgütern, Verpackungen, medizinischen Geräten und Spielzeug verwendet werden, da hier Flexibilität, einfaches Design und kostengünstige Produktion wichtig sind.
Anwendungen des Druckgießens

Einer der Faktoren, die das Druckgießen zu einem beliebten Fertigungsverfahren in vielen Branchen gemacht haben, ist die Tatsache, dass es die Herstellung von hochwertigen, langlebigen Teilen mit recht komplizierten Geometrien ermöglicht. Einige der Anwendungen sind:
1. Autoindustrie
Im Allgemeinen werden Motorkomponenten, Getriebegehäuse und andere wichtige Automobilteile im Druckgussverfahren hergestellt. Druckgussteile haben die Präzision und Festigkeit, um in anspruchsvollen Anwendungen in der Automobilindustrie eingesetzt zu werden.
2. Elektronikindustrie
Druckguss wird in der Elektronikbranche zur Herstellung von Gehäusen für elektronische Geräte wie Mobiltelefone, Laptops und Fernsehgeräte verwendet. Die Technik ermöglicht den Bau von leichten, aber dennoch stabilen Gehäusen, die empfindliche Komponenten schützen.
3. Luft- und Raumfahrtindustrie
Das Druckgussverfahren ist für die Luft- und Raumfahrtindustrie von großem Nutzen, da es leichte Teile mit hoher Festigkeit herstellen kann, die für Luft- und Raumfahrzeuge benötigt werden. Druckgussteile verfügen über die Präzision und die Materialeigenschaften, um in Anwendungen eingesetzt zu werden, bei denen Leistung und Sicherheit eine wichtige Rolle spielen.
4. Industrielle Ausrüstung
Auch die Teile von Maschinen, Werkzeugen und anderen Industrieanlagen werden im Druckgussverfahren hergestellt. Da es Teile mit komplizierten Geometrien und guten mechanischen Eigenschaften herstellen kann, ist es ein gutes Werkzeug für diese Anwendungen.
Schlussfolgerung
Druckguss ist ein vielseitiges, kostengünstiges und effizientes Herstellungsverfahren, das in vielen Branchen eingesetzt wird. Die produzierte Qualität ist extrem hoch in Bezug auf die Toleranzen der Teile, die Oberflächengüte und die hohen Produktionsraten, was es zu einem ausgezeichneten Fertigungswerkzeug für die modernen Fertigungsverfahren von heute macht. Der Druckguss erfüllt die Anforderungen vieler Branchen, in denen Festigkeit, Genauigkeit und Effizienz der Teile gefragt sind - von der Automobilindustrie über die Luft- und Raumfahrt bis hin zur Elektronik und Industrieausrüstung.
Obwohl die Technologie schnell wächst und wahrscheinlich auch weiterhin als Quelle für hervorragend gefertigte Metallteile in großem Umfang genutzt werden wird, ist es in Druckguss. Ein besseres Verständnis der Grundlagen des Druckgießens kann Fachleuten aus den Bereichen Technik, Fertigung und Konstruktion helfen, fundierte Entscheidungen darüber zu treffen, wie das Druckgießverfahren für das gewünschte Ergebnis eingesetzt werden kann.
FAQs über Druckguss
1. Wie lang ist der Zeitzyklus für Druckguss und Spritzguss?
Die Zykluszeit für ein bestimmtes Teil liegt zwischen 15 und 5 Minuten beim Druckguss und zwischen 10 und 60 Sekunden beim Spritzgießen.
2. Kann Druckguss auch für Kunststoffteile verwendet werden?
Druckguss wird nicht für Nicht-Metalle verwendet. Für die Herstellung von Kunststoffteilen wird üblicherweise das Spritzgussverfahren verwendet.
3. Welche Produkte eignen sich am besten für das Herstellungsverfahren des Druckgusses?
Druckguss eignet sich am besten für die Herstellung kleiner und mittelgroßer komplizierter Teile mit hoher Genauigkeit, die aus Metallen hergestellt werden. Zu den mechanischen Produkten, die hergestellt werden, gehören unter anderem Auto- und Automobilteile und -zubehör, Gehäuse für Elektrogeräte, Elektronikteile und Gerätegehäuse.
4. Der Unterschied zwischen Druckguss und Sandguss.
Dennoch, wenn man die beiden vergleicht: Das Druckgussverfahren ist genauer und weniger zeitaufwändig als das Sandgussverfahren. Während Sandguss für große und weniger komplizierte Formen bevorzugt wird, wird AL-Guss für kleine und komplexe Formen bevorzugt, da er glattere Oberflächen und engere Toleranzen ermöglicht, die für hohe Produktionsläufe typisch sind.
5. Wodurch werden die Kosten des Druckgusses bestimmt?
Einige der Überlegungen, die die Kosten des Druckgusses beeinflussen können, sind: die Art des Materials, die Komplexität des Teils, die Konstruktion der Form und die Menge der Aufträge. Die Kosten für leichte Werkzeuge hängen vom Volumen ab. Obwohl ein hohes Volumen die Stückkosten niedrig hält, sind die Anfangskosten für die Werkzeuge hoch.