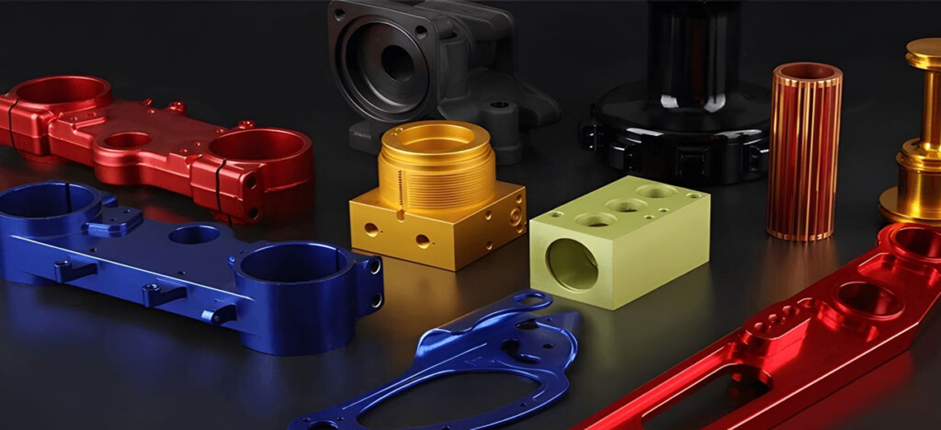
Anodized aluminum material is used mainly because it is light, strong, and corrosion-resistant. While raw aluminum does offer a certain amount of durability and scratch resistance, it is prone to oxidation, dents, and scratches, which can change it in the long term and keep it looking good. To make the aluminum stronger and more durable, it is then anodized to form a protective oxide layer on its surface. The reason for this layer is that it hardens the metal, giving it a more noncorroding and nonwear surface and a more pleasant appearance. Anodized aluminum is preferred due to these factors and is used widely across aerospace, automotive, construction, and consumer electronics industries. The anodization consists of several steps cleaning of the surface, immersion into an electrolyte bath, oxidation using electric current, and sealing. Besides making the material stronger, this treatment can be colored in different shades and finishes. Electrolytic coloring, Dip coloring, Integral coloring, and Interference coloring are different common coloring techniques.
Ordinary anodizing and hard anodizing are the two main types of anodizing. Typically there are two processes available: ordinary anodizing, used primarily for finish and low-weight applications, and hard anodizing which gives excellent durability, wearer, and strength for military, industrial, and aerospace applications. In addition to anodization, aluminum can be processed through other surface treatments such as electroplating, powder coating, chromate conversion coating, PVD coating, ceramic coatings, or hot dip galvanizing. Anodized aluminum does not possess these properties uniformly and thus is used as a versatile and reliable material in many industries, with each method providing the material with specific enhanced properties—corrosion resistance, hardness, conductivity, etc.
In this article, we’ll discuss what properties, benefits, applications, and maintenance of anodized aluminum involve, and why it is a better alternative to other metals and treatments. If we know these aspects we can understand which material to use for a particular industry and the consumer.
What is Anodized Aluminum?

Aluminum that has been anodized is an aluminum that has been run through an electrochemical process to produce a thicker, more durable oxide layer on its surface. The presence of this anodic oxide layer increases the resistance of the metal to corrosion, improves the surface hardness, and increases the ability of the metal to adhere to dyes and coatings.
The Anodization Process
In other words, the anodization process includes several key steps.
- The aluminum surface is cleaned to remove dirt, grease, or impurities from the surface before the drying, cleaning, and pre-treatment steps. The surface may also be etched for a uniform finish.
- Anodizing Bath – The aluminum is dropped right into an electrolyte solution (typically sulphuric acid) and electric present is offered. It starts oxidation and forms the thickened aluminum oxide layer.
- The porous oxide layer may be simultaneously colored (Optional) by similarly providing dyes or pigments as desired.
- Closing off the pores – Sealing of the anodized layer is done by means of hot water or steam, thus closing off the pores, further enhancing corrosion resistance.
Anodized Aluminum Material Key Properties

1. Enhanced Corrosion Resistance
Anodized aluminum is one of the most resistant to corrosion. This makes it practically useless outdoors or when submerged in water, as the oxide layer protects the metal from moisture and our environment.
2. Increased Surface Hardness
Anodization improves the hardness of aluminum significantly and aluminum becomes more resistant to scratch, dent, and wear. One such hard anodized aluminum is highly durable and is indeed used in high-performance applications.
3. Aesthetic Appeal and Color Variety
Also, anodized aluminum is offered in black, gold, bronze, silver, etc. without changing the natural texture of the metal. This is why it is a preferred choice for architectural as well as decorative applications.
4. Lightweight Yet Strong
While the oxide layer is put on top of the aluminum, this doesn’t make the aluminum significantly heavier, and it is still lighter than heavier materials such as stainless steel.
5. Electrical Insulation
Because anodized aluminum is a poor conductor of electricity as compared to untreated aluminum, it is an attractive material to use in applications where insulation is needed for electrical or electronic purposes.
6. Environmentally Friendly and Sustainable
Anodized aluminum is completely non-toxic, is recyclable, and does not out-gas dangerous and health-harming VOCs (volatile organic compounds), so it is eco-friendly.
How to Add Color to Anodized Aluminum Parts?

Anodizing aluminum is well known to be able to hold colors very vibrantly. Electrolytic coloring and dip coloring are the two of the many techniques used to color anodized aluminum.
1. Electrolytic Coloring

One popular way to beautify anodized aluminum is with electrolytic coloring whereby anodized aluminum is colored with durable and UV-resistant shades. Once the aluminum has gone through the anodizing process, it is placed in a bath with metallic salts. In the last few years metalized salts have been developed whereby, when an electric current is applied, they settle into the open pores of the anodized surface permanently creating a metal-colored surface.
Finally, the color depends on the type of metal salts involved. Copper salts ,for instance, make the solution reddish in tone, and other metals can make it in other hues. It is widely used because colors done this way last long and don’t fade, which makes it great for outdoor or high-exposure uses.
2. Dip Coloring

Another color method is ‘dip coloring’ which gives one a large variety of color choices. During this kind of processing, the porous layer is submerged in a dye solution where the anodized aluminum absorbs the pigment. Once a shade is reached, the aluminum is sealed in water to stop reactions from continuing.
Dip coloring offers much more vibrant and customizable contrasted shades, but they are not UV resistant and the colors will fade to a much lesser extent when exposed to sunlight. However, this lack of durability is the main reason why it is not commonly used in applications where the durability of parts is an important factor.
3. Integral Coloring (One-Step Process)
An integral coloring is a unique process that incorporates anodizing and coloring into one process which is more efficient than in multi-step methods. Unlike some other techniques, the electrolytes, which react with the surface of the aluminum and are quick to dry, create deep, rich metallic tones including black, gold, or bronze. The color is formed in the very oxide layer, and due to that, it is very durable and doesn’t scratch, isn’t prone to corrosion, and doesn’t fade away.
While integral coloring yields quality finishes, it is rare because of the cost and complexity. Architectural components, high-end electronics, and industrial equipment in which the parts must be able to withstand demanding conditions where an attractive appearance and longevity are required apply typically.
4. Interference Coloring
Interference coloring is a high tech advanced anodizing process where the thickness of the oxide layer of the product can be manipulated to create iridescent multi tone blues, greens and purples without dyes or pigments. Rather than absorbing color, the aluminum is reacting to the waves of light by reflecting different colors based on the point of view.
Common uses of this method in architecture, luxury products, or decorative metalwork is to achieve the desired unique visual effects. Exceptional weather resistance makes it fit for high end signage and artistic applications, as well as exterior surfaces. Although it is very complex, it is not easily made as mass production.
Alternatives to Anodized Aluminum

Aluminum surface treatment such as anodizing is widely used to improve the durability, corrosion resistance, and appearance of aluminum. The reason is that; it forms an electrochemical protective oxide layer, which makes aluminum suitable for several applications. Nevertheless, different surface treatment methods exist that can offer similar or even better results when the requirements are suitably chosen. Unlike these alternatives, they have unique advantages for instance improved protection, better adhesion properties, and decorative finishes. Some common alternatives to anodized aluminum are provided below.
1. Electroplating
Electroplating is the technique of depositing a thin layer of metal, for instance, nickel, chrome, gold…onto the surface of aluminum or other metals. One does this by an electrochemical process which helps corrosion resistance, durability and aesthetics of the item. Automotive trim, as well as jewelry and electrical components, are some of the materials that are electroplated common. The biggest advantage of this method is that manufacturers can decide on a plating material and customize the properties of aluminum. For example, it may be done for conductivity of gold plating, or increased hardness and resistance to wear of chrome plating.
2. Powder Coating
Powder coating is one of the most widely used methods for finishing metal by using dry, electrostatically charged particles of paint. The result at high temperatures is a durable and protective film over the coated part. This method is in wide application because of its good corrosion resistance, good impact resistance, and multitude of color selections. Unlike traditional liquid paint with no solvents, powder coating means no harmful solvents are used. It is widely used in architectural components, automotive parts, and consumer appliances as it can resist harsh environmental situations without chipping or fading.
3. Chromate Conversion Coating (Alodine or Chem Film)
Alodine or chem film is used as a chemical process to cover aluminum with a thin protective coating called Chromate conversion coating. It improves corrosion resistance with electrical conductivity unimpaired and is thus suitable for aerospace and electronic applications. Unlike anodizing, which creates a thick oxide layer, chromate conversion coating furnishes better paint and adhesive adhesion. Lightweight materials with reliable protective coatings are useful, especially in industries, where they are required. And while not as durable as anodizing, it may be better suited to less wear-using applications.
4. Physical Vapor Deposition (PVD) Coating
PVD coating is an aluminum surface treatment that involves the deposition of metal compounds in the form of thin layers onto aluminum in a vacuum. This greatly enhances hardness, wear resistance as well as aesthetic appearance. Among PVD coatings, durable TiN and CrN can be applied on super hard surfaces (e.g. industrial tools, firearms, luxury watches) due to their superior durability. With a variety of metallic finishes such as gold, black, and iridescent colors, PVD coatings are prime to an extensive number of finishes without modifying the shape of the part.
5. Ceramic Coatings
Ceramic coatings are excellent wear-resistant and heat-resistant surface protectors for aluminum and other metals. They are applied as a very thin and highly durable layer using thermal spraying or chemical vapor deposition (CVD). Special mention can be made to put ceramic coatings on the best, in Automotive, Aerospace, and Industrial applications where components are subjected to extreme temperatures and harsh conditions. Besides having extreme durability, ceramic coatings can be thermally insulating, which is why they are used in engine parts, exhaust systems, as well as cookware.
6. Hot-Dip Galvanizing
Hot-dip galvanizing refers to a surface coating process whereby a metal object such as steel or iron is galvanized when immersed in a molten zinc bath. It leaves a zinc coating that offers long-term corrosion resistance suitable for outdoors, on bridges, or industrial equipment. Although hot-dip galvanizing is not normally used as an aluminum protection, it still is an ideal tool for protecting ferrous metals against rusting and environmental damage. What makes this process so key is the fact that the zinc coating is allowed to self-heal so that should the surface be scratched, corrosion will never set in again and prevent the rusting of the steel surface.
Which Alternative Should You Choose?
Alternative | Best For | Key Benefits |
Electroplating | Decorative & functional metal parts | Shiny finish, corrosion resistance, customizable |
Powder Coating | Durable colored finishes | Impact-resistant, eco-friendly, available in many colors |
Chromate Conversion Coating | Aerospace & Electronics | Improves adhesion, corrosion resistance, conductive |
PVD Coating | High-performance tools & luxury goods | Extremely hard, wear-resistant, metallic finish |
Ceramic Coatings | Heat-resistant applications | Thermal barrier, high durability, anti-scratch |
Hot-Dip Galvanizing | Heavy-duty steel structures | Long-lasting corrosion protection, ideal for outdoor use |
Difference Between Hard Anodizing and Ordinary Anodizing

Anodizing is a process for improving corrosion resistance, durability, and appearance of aluminum. Two common types are ordinary anodizing and hard anodizing. Both methods generate an oxide layer, although the process conditions, properties of the oxide layer, and application are different for each.
1. Differences in the Anodizing Process
Acid Concentration
It is the concentration of acid used in the anodizing process that affects the final coating. Ordinary anodizing involves acid concentrations of 20% or so in the forming of a smooth and uniform oxide layer.
On the other hand, hard anodizing uses lower acid concentration such as a concentration about 15% or less, and the coating is denser and stronger.
Temperature Requirements
The hardness of the oxide layer is an important factor, which is wholly dependent on the temperature. Ordinary anodizing is carried out at 18 22°C (depending on the type and quantity of additives max. temperature 30°C).
In the case of high temperature, it could powder or crack off the coating. A stronger and more wear-resistant coating can only be created with hard anodizing at much lower temperatures, less than 5°C.
Current and Voltage Levels
Ordinary anodizing takes place at a current density of 1 – 1.5 A/dm² and a voltage not exceeding 18 V.
Hard anodizing, however, must be performed at much higher voltage, even up to 120 volts, to build up a much thicker oxide that is very hard as well.
2. Differences in Coating Performance
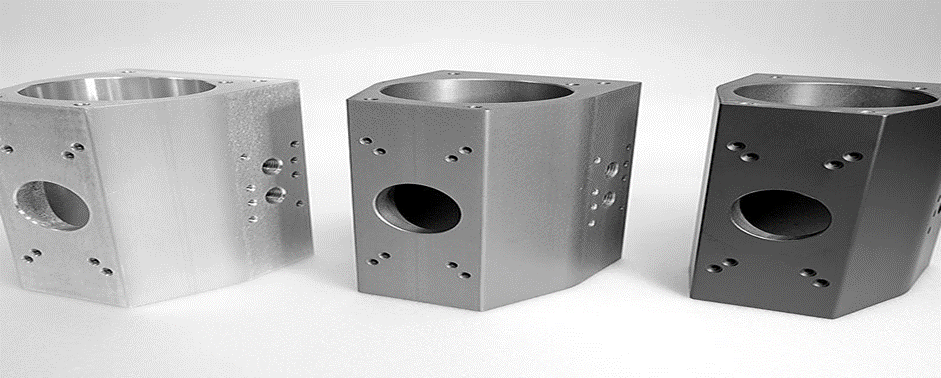
Applications and Uses
Decoration and smoothing are the main uses of ordinary anodizing as it can color an anodized surface and smooth the surface. Consumer goods, furniture, and architectural components are typical places where it is found.
However, hard anodizing is used in industrial, and military, automotive applications, for superior wear resistance and durability.
Surface Appearance
The anodizing method determines the surface texture of anodized aluminum. Anodized surfaces are ordinary smooth and uniform which are appropriate for aesthetic apps. Hard anodized surfaces are rougher to the microscopic eye, which gives them more ability to withstand wear and friction.
Porosity
Porosity refers to the number of tiny openings in the oxide layer. Highly porous ordinary anodized layers are better for dyeing and coloring, but somewhat less so in wear resistance. Hard anodized layers are less porous and hence stronger and resistant to damage.
Thickness of the Coating
Basic protection and aesthetics are provided by the oxide layer, which is usually less than 15μm, created by ordinary anodizing.
However, hard anodizing forms a much thicker layer, typically over 15μm, needed for hard and wear-resistant applications.
Transparency and Opacity
How light passes through the thickness of the oxide layer, as well as the material used. They can be easily dyed in different colors since ordinary anodized coatings are transparent.
The hard anodized coatings are opaque because of their greater thickness and hence unsuitable for decorative coloring.
Common Products Made from Anodized Aluminum
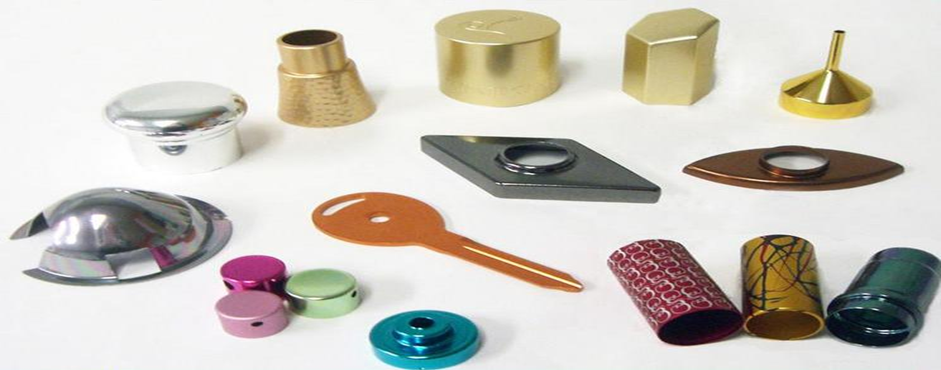
1. Smartphone and Laptop Cases
Anodized aluminum is used as the outer casings of many premium smartphones and laptops. The devices are resistant to scratches, dents, and wear because of this material. Also, they provide them with a smooth and stylish finish and at the same time they keep them lightweight and easy to carry.
2. Tablet Enclosures
Because it is lightweight and provides excellent protection, tablet enclosures are sometimes made of anodized aluminum. Manufacturers are also able to pick and choose from a wide variety of colors that won’t degrade the tablets since they are able to go through the anodizing process.
3. Window and Door Frames
Anodized aluminum is used for window and door frames in buildings because it is rust-resistant and does not fade or peel. This makes it a great option for use in home applications and commercial buildings where long life and little maintenance are required.
4. Automotive Trim and Bike Frames
The properties of anodized aluminum make it a good choice for consumers seeking high durability and lower weight in vehicles, both of which may increase fuel efficiency. Anodized aluminum bike frames are popular in the cycling industry due to their strength and lighter weight, suitable for use in regular cycling and competitive racing.
Types of Anodized Aluminum
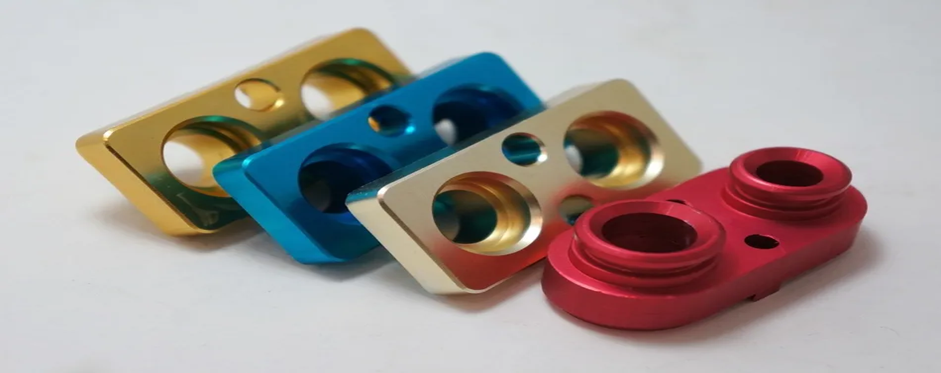
There are different types of anodized aluminum each having its unique properties and benefits based on the different characteristics and response required based on the application and performance. The type of anodization will be chosen depending on such parameters as durability, corrosion resistance, thickness and aesthetic features. The main types of anodized aluminum and their specific uses are as follows below.
1. Type I (Chromic Acid Anodizing)

In type I anodizing, chromic acid creates a thin but highly corrosion resistant oxide layer. A great method for aerospace without a significant need for weight reduction since it does not alter the normal dimensions. Type I anodized aluminum has a thickness lower than Type II, and hence is not suitable for color anodizing while it provides good adhesion of paints and primers.
Key Features
- Produces a thin, corrosion-resistant oxide layer
- Maintains aluminum’s conductivity
- Ideal for aerospace and defense applications
- Provides excellent adhesion for coatings.
2. Type II (Sulfuric Acid Anodizing)

The most common type of anodization is Type II, which uses sulfuric acid to grow a medium thickness oxide layer. This type may be anodized to give color and is used in consumer goods, architectural components and automotive parts. Because it offers good corrosion resistance, wear resistance, as well as giving improved aesthetics.
Key Features
- Standard anodization process
- Provides a moderate-thickness oxide layer
- Allows for color anodizing
- It is commonly used in electronics, furniture, and construction.
3. Type III (Hard Anodizing)
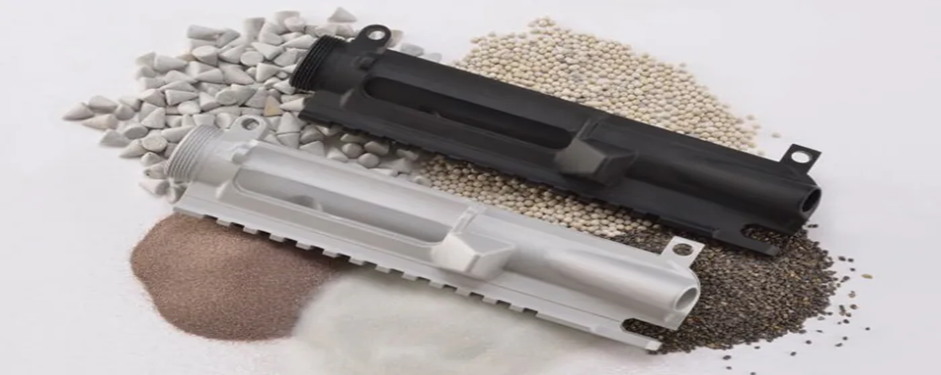
Type III anodizing, also known as hard coat anodizing, produces the thickest and hardest oxide layer and it is very wear-resistant and durable. This type is extensively applied in military, industrial, and cookware applications where high strength, superior abrasion resistance,e, and superior corrosion protection are needed. Type III anodized aluminum has high durability and is often used in machine components, firearm parts, as well as medical devices.
Key Features
- Produces a thick, wear-resistant oxide layer
- Offers maximum durability and hardness
- Used in high-performance industrial applications
- Provides superior corrosion resistance
Applications of Anodized Aluminum Material
Because of its superior properties, anodized aluminum is used in several industries and products.
1. Aerospace and Automotive Industry
- Aircraft components such as fuselage panels and wing structures
- Body panels, engine parts, and trim pieces that go into the car
- Durable due to its lightweight and corrosion-resistant properties
2. Construction and Architecture
- Window frames, curtain walls, door, etc.
- Roofing materials and railings
- Modern skyscrapers and building facades are used for aesthetic appeal.
3. Consumer Electronics and Appliances
- Apple MacBook makes use of anodized aluminum and smartphones, laptops, and tablets.
- Kitchen appliances such as coffee makers and toasters
- Anodization prevents fingerprinting, scratching, and smudges.
4. Medical and Laboratory Equipment
- Surgical instruments and medical trays
- The non-reactive nature led to the use of sterile laboratory surfaces
- Longevity in a healthcare environment relies on corrosion resistance
5. Sports and Outdoor Equipment
- Bicycle frames hiking gear and camping equipment.
- Durable and lightweight materials for extreme conditions
6. Cookware and Kitchenware
- Nonstick anodized aluminum pans or utensils
- This is resistant to scratching and high temperatures.
- It is a safer alternative to the traditional non-stick coatings.
Comparing Anodized Aluminum vs. Other Metals
Feature | Anodized Aluminum | Stainless Steel | Titanium |
Weight | Lightweight | Heavy | Moderate |
Corrosion Resistance | Excellent | Very High | Excellent |
Surface Hardness | High | Very High | Extremely High |
Electrical Conductivity | Low | Moderate | Low |
Aesthetic Options | Various Colors | Limited | Limited |
Cost | Affordable | Expensive | Very Expensive |
Maintenance and Care for Anodized Aluminum
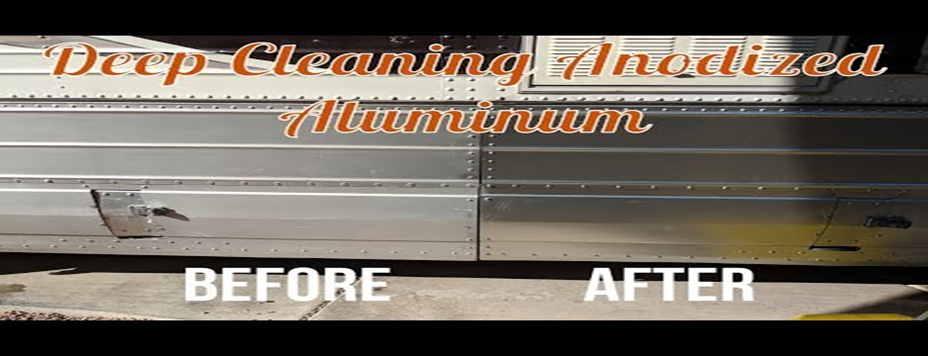
Anodized aluminum is highly durable and can withstand corrosion, however, anodizing aluminum regularly keeps it looking strong and lasting. Preventive care, such as way natural anodized aluminum to deterioration, color change, or damage to the surface, will keep the material in good form for years. The following are some tips below for the maintenance of anodized aluminum surfaces.
1. Regular Cleaning
You should keep anodized aluminum clean by using mild soap and water often. Use a soft cloth or sponge to remove dusty, dirty, and grimy grime. Abstain from utilizing rough cleaners or steel wool since they can scratch the anodized layer. A mild detergent in warm water will work wonders on troubling stains. After the cleaning rinse with clean water and dry the surface with a soft towel to prevent water spots.
2. Avoid Harsh Chemicals
Resistant also to many environmental elements, it can, however, be damaged by strong acids, alkaline solutions, or harsh industrial cleaners which affect its protective oxide layer. Do NOT use bleach, ammonia-based cleaners, or acidic substances that will fade or pit the material. If stronger cleaning agents are required, they should always use a pH-neutral solution specifically for anodized metals.
3. Polishing and Protection
To keep the anodized aluminum shiny and smooth, use a soft microfiber cloth or sponge and polish the surface only very lightly. If further protection is required, then apply a nonabrasive wax or some sort of anodized aluminum protectant. The added layer aids in the prevention of oxidation and keeping the metal’s shine and shade on most occasions.
4. Prevent Scratching and Impact Damage
Anodized aluminum has great scratch resistance but it is not scratch-proof. Do not use sharp objects, heavy tools, or rough materials directly on the surface in order not to get dents, scratches,s or chipping. Protective padding covers or even a Sharpie marker should be on hand to prevent accidental damage to anodized aluminum components.
5. Protect Against Harsh Environmental Conditions
Anodized surfaces are gradually worn by prolonged exposure to salt water, UV radiation, and extreme weathering. On the other hand, anodized aluminum should be inspected periodically if used outdoors. In marine or coastal environments fresh water rinsing of the surface may remove salt deposits that will accelerate corrosion.
Conclusion
Anodized aluminum has been found to be a very versatile and reliable material for many industries because of its light weight, durability, enhanced surface hardness and corrosion resistance. Anodizing not only hardens but also gives aluminum an option to look attractive which is why it is preferred in the construction, automotive, aerospace, electronic & cookware industries.
Anodized aluminum is one of the circuit’s principal advantages in terms of long life with minimal maintenance requirements. However, with simple cleaning with mild soap and water, avoiding harsh chemicals, and protecting from scratches and impact damage, the usability will be extended.There is excellent resistance to wear and corrosion, however, it is critical which type of anodizing (ordinary or hard anodizing) is chosen for the intended application.
Electroplating, powder coating, and PVD coatings are other types of alternative treatments that provide their own set of properties. While anodized aluminum may not be as environmentally friendly as this green coating, it is still very complimentary to this green coating as a top favorite among environmentally friendly solutions due to its affordability and superior performance in different environments.
Frequently Asked Questions (FAQs)
1. For what purpose is anodized aluminum used?
Because of its properties; lightweight, corrosion resistance and durable, anodized aluminum is used in aerospace, automotive, construction, electronics, cookware, and industrial equipment.
2. Can anodized aluminum rust?
Anodized aluminum doesn’t rust because after anodization you form an oxide layer that resists moisture and environmental damage.
3. Is anodized aluminum safe in cookware?
Anodized aluminum, yes, is non toxic and safe for cooking. Understandably, it is used in cookware because it won’t react with food and forms a scratch resistant surface.
4. What is the best way to clean an anodized aluminum surface?
In order to clean an anodized aluminum surface, only mild soap and warm water are required using a soft cloth. Use only mild and non abrasive cleaners, non harsh chemicals and never use steel wool as it can cause damage to the anodized surface.
5. What are anodized aluminum and powder-coated aluminum?
The protective oxide layer on anodized aluminum is formed through an electrochemical process, whereas the paint used on powder coated aluminum is a dry paint that is cured at high temperatures. Powder coating generally has more variety of colored paint than anodized aluminum, but is more likely to chip over time; anodized aluminum is more durable and resistant to fading.